Неорганические материалы, 2022, T. 58, № 2, стр. 209-214
Исследование механических свойств и стойкости к термоудару мелкозернистой керамики YAG:Nd/SiC
Л. С. Алексеева 1, *, А. В. Нохрин 1, К. О. Каразанов 1, А. И. Орлова 1, М. С. Болдин 1, Е. А. Ланцев 1, А. А. Мурашов 1, В. Н. Чувильдеев 1
1 Нижегородский государственный университет им. Н.И. Лобачевского
603022 Нижний Новгород, пр. Гагарина, 23, Россия
* E-mail: golovkina_lyudmila@mail.ru
Поступила в редакцию 09.09.2021
После доработки 16.11.2021
Принята к публикации 17.11.2021
- EDN: YMFUVX
- DOI: 10.31857/S0002337X22020014
Аннотация
Исследована стойкость к термоударам мелкозернистых композиционных керамик на основе иттрий-алюминиевого граната Y2.5Nd0.5Al5O12 (YAG:Nd), упрочненных частицами (10–40 об. %) α-SiC, рассматриваемых в качестве перспективных материалов для инертных топливных матриц в ядерной энергетике. Керамики с добавкой 10, 20, 30% SiC обладают высокой стойкостью к термоударам за счет сформированных при спекании сжимающих внутренних полей напряжений. В композиционной керамике YAG:Nd/40% SiC наблюдается устойчивый рост трещин при увеличении температуры термоудара, обусловленный преимущественным распространением трещин вдоль границ между частицами карбида кремния, имеющих более низкую прочность по сравнению с границами YAG:Nd/YAG:Nd и YAG:Nd/SiC.
ВВЕДЕНИЕ
В настоящее время одной из основных проблем ядерной энергетики является переработка накопленных запасов плутония и малоактивных актиноидов. Решением этой задачи является создание инертных топливных матриц (ИТМ) на основе кристаллических соединений, сходных с природными минералами, обладающих высокой термической, химической и радиационной стойкостью [1–5]. Структура иттрий-алюминиевого граната (YAG) способна вмещать малоактивные актиноиды в свою кристаллическую решетку благодаря широкому изоморфизму [6, 7], а керамика на его основе обладает высокой гидролитической и радиационной устойчивостью [6–10]. Это обуславливает интерес исследователей к возможностям применения YAG в качестве материала ИТМ.
Стойкость к тепловому удару (термоудару) является мерой способности керамических материалов выдерживать термические нагрузки и сопротивляться разрушению при резком изменении температуры [11, 12]. Для керамик сопротивление тепловому удару является одним из важных факторов, определяющих долговечность ИТМ. Поэтому в настоящее время большое внимание уделяется обеспечению стойкости керамик к термоударам для их эффективного применения при повышенных температурах [13, 14]. Отметим, что отсутствие возможности для релаксации возникающих при термоударе внутренних напряжений за счет пластической деформации, а также неблагоприятное сочетание низкой теплопроводности и высокого модуля Юнга делают термоудар наиболее опасным для керамик [15, 16].
По нашему мнению, одним из возможных путей повышения стойкости керамик к термоудару является формирование в них композиционной структуры и сжимающих внутренних полей напряжений. Добиться этого можно, вводя в состав керамики частиц с меньшим коэффициентом теплового расширения (КТР), чем у керамической матрицы. Очевидно, что в этом случае при охлаждении после спекания частицы второй фазы будут сжиматься меньше, чем керамическая матрица. Это приведет к формированию сжимающих полей внутренних напряжений вблизи частиц второй фазы. Возможность реализации на практике данного подхода была продемонстрирована нами с использованием керамик CeO2–SiC [17] и YAG:Nd–SiC [18] с содержанием частиц α-SiC до 20%.
В настоящей работе объектами исследования выступают образцы композитной керамики на основе оксида Y2.5Nd0.5Al5O12 (YAG:Nd) и α-SiC. Отличие данного исследования от работы [18] состоит в расширении объемной доли вводимых частиц α-SiC до 40%, а также в акценте на изучении стойкости получаемых керамик к термоудару.
ЭКСПЕРИМЕНТАЛЬНАЯ ЧАСТЬ
Порошок граната состава YAG:Nd получали методом соосаждения. Водный раствор, содержащий Y(NO3)3, Nd(NO3)3 и Al(NO3)3, смешивали с 5%-ным раствором аммиака. Полученную смесь нагревали для дегидратации при 90°C. Сухой остаток выдерживали при 300, 500, 800 и 1000°C в течение 10 ч на каждой стадии, диспергируя после каждого этапа термостатирования. Полученную порошковую смесь YAG:Nd и частицы α-SiC размером 0.8–1 мкм смешивали друг с другом в планетарной мельнице Pulverisette 6 в течение 2 ч со скоростью 300 об./мин.
Керамику получали методом электроимпульсного (искрового) плазменного спекания (ЭИПС) [19] на установке Dr. Sinter model-625. Порошки помещали в графитовую пресс-форму с внутренним диаметром 12 мм и нагревали за счет пропускания миллисекундных импульсов электрического тока большой мощности (до 3 кА). Спекание проводили до окончания процесса усадки. Условия спекания (скорость нагрева vh, величина приложенного одноосного давления P, температура спекания ts и время изотермической выдержки τs при ts) представлены в табл. 1. Охлаждение образцов проводилось вместе с установкой.
Таблица 1.
Параметры спекания и механические свойства керамических образцов
SiC, % | vh, oC/мин | P, MПa | ts, °C | τs, мин | ρ, г/см3 | ρ/ρth, % | HV, ГПa | KIс, MПa м1/2 |
2θmax, град | β, град |
---|---|---|---|---|---|---|---|---|---|---|
параметры спекания | характеристики керамики | |||||||||
0 [18] | 100 | 80 | 1390 | 8 | 4.67 | 98.6 | 12.5 | 1.5 | 33.068 | 0.140 |
10 | 1320 | 0 | 4.53 | 99.1 | 15.7 | 2.2 | 33.230 | 0.142 | ||
20 | 1350 | 4.49 | 99.0 | 15.8 | 1.8 | 33.241 | 0.138 | |||
30 | 1390 | 4.35 | 99.0 | 15.9 | 1.8 | 33.222 | 0.147 | |||
40 | 1380 | 4.25 | 99.2 | 16.7 | 1.8 | 33.215 | 0.152 |
Фазовый состав порошков и керамик изучали методом рентгенофазового анализа (РФА) на дифрактометре Shimadzu LabX XRD-6000. Плотность полученных образцов (ρ) измеряли методом гидростатического взвешивания в дистиллированной воде на весах Sartorius CPA 225D. При расчете относительной плотности (ρ/ρth) теоретическая плотность (ρth) граната YAG:Nd принималась равной 4.76 г/см3, карбида кремния α-SiC – 3.21 г/см3.
Микроструктуру образцов изучали с использованием растрового электронного микроскопа (РЭМ) JEOL JSM-6495 с энергодисперсионным микроанализатором Oxford Instruments INCA 350. Микротвердость HV измерялась с использованием твердомера Duramin Struers-5. Минимальный коэффициент трещиностойкости (KIc) рассчитывался по методу Палмквиста по длине максимальной радиальной трещины.
Для изучения стойкости к термоудару на шлифованную поверхность образцов предварительно наносили трещину с помощью пирамиды Виккерса на твердомере HVS-1000 при нагрузке 5 H. Образцы с трещиной нагревали в воздушной муфельной печи ЭКПС-10 в интервале температур от 200 до 800°C с шагом в 50–100°C, выдерживали в течение 20 мин на каждой стадии и охлаждали на воздухе. Максимальная температура испытаний на термоудар (800°С) была выбрана исходя из условий применения данной керамики в качестве топливных материалов, а также с учетом интенсивного окисления карбида кремния при более высоких температурах нагрева. Изменение длины трещины фиксировали с использованием металлографического микроскопа Leica DR IRM и с помощью программного комплекса GoodGrains.
РЕЗУЛЬТАТЫ И ОБСУЖДЕНИЕ
Полученные поликристаллические порошки YAG:Nd имеют бледно-фиолетовый цвет; средний размер частиц составляет 0.1–0.2 мкм. Субмикронные частицы YAG:Nd после перемешивания с частицами SiC образуют агломераты размером 30–50 мкм. Анализ результатов РФА показывает, что синтезированный порошок Y2.5Nd0.5Al5O12 (ICDD № 79-1891, пр. гр. Ia3d) является однофазным (дифрактограмма 0 на рис. 1).
Рис. 1.
Рентгеновские дифрактограммы порошков YAG:Nd (0) и керамических образцов с добавкой 10 (1), 20 (2), 30 (3) и 40% SiC (4).
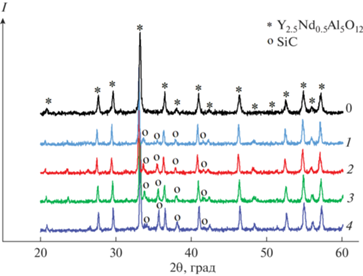
Зависимости усадки (L) и скорости усадки (S) от температуры нагрева (t) порошков показывают, что интенсивная усадка начинается при 1000°С, практически полностью завершается при температуре 1350°С и почти не зависит от содержания SiC (рис. 2а). Зависимости S(t) имеют традиционный двухступенчатый характер (рис. 2б). Температура нагрева t1, при которой наблюдаются максимальные значения скорости усадки Smax, для керамики YAG:Nd + 10% SiC составляет 1250–1280°C, а для образцов с 20, 30 и 40% SiC t1 = 1280–1310°C. Максимальная скорость усадки в пределах точности измерения не зависит от содержания карбида кремния. Таким образом, можно сделать вывод, что увеличение объемной доли частиц SiC не оказывает влияния на кинетику спекания керамики YAG:Nd/SiC.
Результаты РФА показывают, что полученные образцы являются двухфазными: на рентгенограммах присутствуют пики, соответствующие фазе граната (ICDD, № 79-1891, пр.гр. Ia3d) и гексагональной фазе α-SiC (ICDD, № 74-1302, пр. гр. P63mc) (рис. 1). Другие фазы на рентгенограммах отсутствуют.
Относительная плотность композитов YAG/SiC составила ~99% от теоретической (табл. 1). Заметного влияния объемной доли частиц SiC на плотность керамики не выявлено.
Представленные на рис. 3 результаты РЭМ показывают, что микроструктура спеченных образцов состоит из светло-серых зерен граната размером 1–3 мкм, образующих области размером до ~10 мкм. Между областями граната располагаются темные частицы карбида кремния размером ~0.5–1 мкм. В структуре спеченных композитов наблюдается остаточная нано- и микропористость. Средний размер пор не превышает 0.1 мкм. В качестве примера на рис. 3г единичные крупные поры указаны желтыми стрелочками, а их скопления выделены желтой пунктирной линией.
Результаты механических испытаний, представленные в табл. 1, показывают, что введение частиц α-SiC в гранат приводит к повышению микротвердости HV и коэффициента трещиностойкости KIc по сравнению с чистым гранатом YAG:Nd, полученным в аналогичных условиях (HV = 12.5 ГПа, KIc = 1.5 МПа м1/2 [18]).
По данным РФА, в спеченных образцах наблюдаются увеличение ширины максимума 420 на полувысоте (β) и его смещение (2θmax) в сторону больших углов (табл. 1). Это, в соответствии с уравнением Вульфа–Брэгга, свидетельствует об уменьшении межплоскостного расстояния и формировании сжимающих полей внутренних напряжений. Как видно из табл. 1, с увеличением содержания SiC происходит повышение сжимающих внутренних напряжений в керамике.
Причиной возникновения внутренних напряжений в композитах YAG/SiC является, очевидно, различие в КТР граната YAG ((7.8–8.2) × 10–6°С–1) и α-SiC (4.7 × 10–6°С–1). При охлаждении спеченной керамики YAG/SiC линейные размеры частиц α-SiC сокращаются в ~2 раза меньше, чем средний размер зерен граната, что приводит к формированию сжимающих полей внутренних напряжений вокруг частиц α-SiC.
Схема испытаний керамических образцов на термоудар представлена на рис. 4а, а зависимость максимальной длины трещины от температуры – на рис. 4б.
Рис. 4.
Схема испытаний керамик на термоудар (а) и зависимость максимальной длины трещины lmax от температуры нагрева (б).
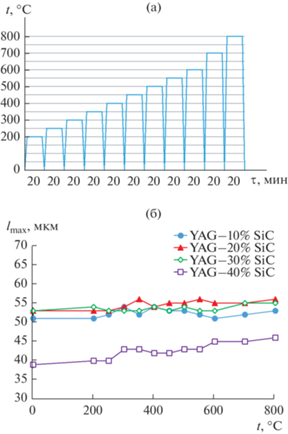
Образцы чистого граната YAG:Nd, имеющие низкие твердость и трещиностойкость, разрушились после второго цикла термоудара. Образцы YAG:Nd/SiC выдержали полный цикл испытаний (11 циклов нагрев–охлаждение) без разрушения. Исследования поверхности керамики показали, что в образцах YAG:Nd + 10(20, 30)% SiC с увеличением температуры нагрева (термоудара) средний размер трещин не изменился и составил lmax ~ ~ 52–54 мкм (рис. 4б). Начальный размер трещины в образце YAG:Nd + 40% SiC оказывается на 10% меньше (lmax ~ 39 мкм), чем в образцах с 10–30% SiC, но при увеличении температуры нагрева наблюдается рост трещины и после 11 циклов нагрева–охлаждения lmax достигает ~43–44 мкм (рис. 4б).
Рост трещины в керамике YAG:Nd + 40% SiC с повышенным уровнем сжимающих внутренних напряжений является неожиданным результатом. По нашему мнению, это связано с тем, что объемная доля частиц α-SiC в данной керамике уже достаточно велика для того, чтобы образовать непрерывную систему “границ” из карбида кремния вокруг крупных (~10 мкм) областей YAG:Nd (рис. 3г). Отметим, что карбид кремния методом ЭИПС спекается при существенно более высоких температурах: например, для β-SiC оптимальная температура ЭИПС составляет ts = 2000°C [19]. Это означает, что после спекания керамики YAG:Nd–40% SiC при ts = 1380°C прочность границ между частицами карбида кремния (SiC/SiC) оказывается меньше, чем прочность границ YAG:Nd/YAG:Nd и YAG:Nd/SiC. Это облегчает распространение трещин по границам SiC/SiC и, как следствие, снижает стойкость керамики к термоударам.
ЗАКЛЮЧЕНИЕ
Методом высокоскоростного (100°С/мин) ЭИПС получены керамические образцы на основе YAG:Nd, упрочненные частицами α-SiC. Образцы имеют высокую относительную плотность (~99%), твердость (15.8–16.8 ГПа) и удовлетворительную трещиностойкость (1.8–2.2 МПа м1/2).
Образцы с добавкой 10, 20 и 30% частиц SiC обладают высокой стойкостью к термоударам, моделируемым путем циклического нагрева и охлаждения на воздухе. В керамике YAG:Nd–40% SiC наблюдается устойчивый рост трещин при увеличении температуры нагрева. Это обусловлено более низкой прочностью границ между частицами карбида кремния по сравнению с границами YAG:Nd/YAG:Nd и YAG:Nd/SiC.
Для дальнейшего обеспечения более высокой стойкости керамики YAG:Nd/SiC к термоударам необходимо добиться более равномерного распределения частиц карбида кремния в объеме керамики и, тем самым, минимизировать число “хрупких” границ SiC/SiC.
Список литературы
Orlova A.I., Ojovan M.I. Ceramic Mineral Waste-Forms for Nuclear Waste Immobilization // Materials. 2019. V. 12. № 16. 2638.
Burakov B.E., Ojovan M.I., Lee W.E. Crystalline Materials for Actinide Immobilisation. L.: Imperial College Press, 2010. 198 p.
Chauvin N., Konings R.J., Matzke H. Optimization of Inert Matrix Fuel Concepts for Americium Transmutation // J. Nucl. Mater. 1999. V. 274. P. 105–111.
Neeft E.A.C., Konings R.J.M., Bakkera K. et al. Neutron Irradiation of Pollycristalline Yttrium Aluminate Garnet, Magnesium Aluminate Spinel and α-Alumina // J. Nucl. Mater. 1999. V. 274. P. 78–83.
Neeft E.A.C., Bakker K., Schram R.P.C. et al. The EFTTRA-T3 Irradiation Experiment on Inert Matrix Fuels // J. Nucl. Mater. 2003. V. 320. P. 106–116.
Лившиц Т.С. Изоморфизм актиноидов и РЗЭ в синтетических ферритных гранатах // Геология рудных месторождений. 2010. Т. 52. № 1. С. 54–64.
Potanina E., Golovkina L., Orlova A. et al. Lanthanide (Nd, Gd) Compounds with Garnet and Monazite Structures. Powders Synthesis by “wet” Chemistry to Sintering Ceramics by Spark Plasma Sintering // J. Nucl. Mater. 2016. V. 473. P. 93–98.
Томилин С.В., Лизин А.А., Лукиных А.Н., Лившиц Т.С. Радиационная и химическая устойчивость алюмитриевого граната // Радиохимия. 2011. Т. 53. № 2. С. 162–165.
Лившиц Т.С. Устойчивость искусственных ферритовых гранатов с актиноидами и лантаноидами в водных растворах // Геология рудных месторождений. 2008. Т. 50. № 6. С. 535–547.
Алексеева Л.С., Нохрин А.В., Болдин М.С. и др. Гидролитическая устойчивость керамики на основе Y2.5Nd0.5Al5O12 со структурой граната в гидротермальных условиях // Неорган. материалы. 2021. Т. 58. № 8. С. 918–922.
Kingery W.D., Bowen H.K., Uhlmann D.R. Introduction to Ceramics, 2nd ed. N.Y.: Wiley, 1976. P. 817–830.
Tite M.S., Kilikoglou V., Vekinis G. Strength, Toughness and Thermal Shock Resistance of Ancient Ceramics, and Their Influence of Technological Choice // Archaeometry. 2001. V. 43. P. 301–324.
Schneider G.A. Thermal Shock Criteria for Ceramics // Ceram. Int. 1991. V. 17. P. 325–333.
Bao Y.W., Wang X.H., Zhang H.B. et al. Thermal Shock Behavior of Ti3AlC2 between 200°C and 1300°C // J. Eur. Ceram. Soc. 2005. V. 25. P. 3367–3374.
Gupta T.K. Strength Degradation and Crack Propagation in Thermal Shocked Al2O3 // J. Am. Ceram. Soc. 1972. V. 55. P. 249–253.
Hasselman D.P.H. Strength Behavior of Polycrystalline Alumina Subjected to Thermal Shock // J. Am. Ceram. Soc. 1970. V. 53. P. 490–495.
Алексеева Л.С., Нохрин А.В., Болдин М.С. и др. Получение мелкозернистых керамик CeO2–SiC для инертных топливных матриц методом электроимпульсного плазменного спекания // Неорган. материалы. 2020. Т. 56. № 12. С. 1380–1387.
Golovkina L.S., Orlova A.I., Chuvil’deev V.N. et al. Spark Plasma Sintering of High-Density Fine-Grained Y2.5Nd0.5Al5O12 + SiC Composite Ceramics // Mater. Res. Bull. 2018. V. 103. P. 211–215.
Chuvil’deev V.N., Boldin M.S., Nokhrin A.V., Popov A.A. Advanced Materials Obtained by Spark Plasma Sintering // Acta Astronaut. 2016. V. 135. P. 192–197.
Дополнительные материалы отсутствуют.
Инструменты
Неорганические материалы