Неорганические материалы, 2022, T. 58, № 5, стр. 554-561
Структурные превращения керамики, образующейся в процессе высокотемпературной нитридизации сплава Zr–Nb
И. А. Ковалев 1, *, С. В. Шевцов 1, Г. П. Кочанов 1, С. В. Федоров 1, С. В. Канныкин 1, 2, А. И. Ситников 1, А. И. Огарков 1, А. В. Шокодько 1, С. С. Стрельникова 1, А. С. Чернявский 1, К. А. Солнцев 1
1 Институт металлургии и материаловедения им. А.А. Байкова Российской академии наук
119334 Москва, Ленинский пр., 49, Россия
2 Воронежский государственный университет
394018 Воронеж, Университетская пл., 1, Россия
* E-mail: vankovalskij@mail.ru
Поступила в редакцию 13.12.2021
После доработки 28.01.2022
Принята к публикации 29.01.2022
- EDN: CCVGEM
- DOI: 10.31857/S0002337X22050062
Аннотация
Представлена последовательность структурных превращений, характеризующих высокотемпературную нитридизацию цирконий-ниобиевых сплавов с содержанием ниобия 0.1—10 мас. %. В ходе высокотемпературного насыщения твердых растворов ниобия в цирконии азотом для каждого состава происходит распад твердого раствора Zr〈Nb〉 с образованием композитных структур Zr1 –хNbхN – (ZrN1 –n/β-тв. раствор Zr в Nb) – Zr1 –хNbхN. При нитридизации гетероструктур происходит взаимодействие нитрида циркония с β-ниобием, что завершает нитридизацию исходного твердого раствора Zr〈Nb〉 . Для полученной керамики характерна приповерхностная пористость, которая наследует поверхностную пористость исходного проката.
ВВЕДЕНИЕ
Конструкционные материалы, характеризующиеся высокими электро- и теплопроводностью, износостойкостью, химической инертностью, биосовместимостью и радиационной стойкостью, широко востребованы в микроэлектронике, медицине, при изготовлении обрабатывающего инструмента, в аэрокосмической индустрии и атомной энергетике. Этим требованиям соответствует керамика на основе нитридов металлов подгруппы титана и подгруппы ванадия, сочетающая свойства, характерные для металлов, жаропрочных сплавов и керамических материалов. Керамика на основе нитридов металлов подгруппы титана может выполнять функцию матрицы, в состав которой вводят активные добавки нитридов урана и трансуранидов [1–6] либо добавки в виде фаз, изменяющих ее характеристики [4, 7, 8].
Вследствие сложности компактирования порошков тугоплавких нитридов разработка одностадийного синтеза керамики, изучение свойств, общих закономерностей формирования структуры, субструктуры и кинетики роста представляют значительный научный интерес. В работе [9] композитную керамику создавали прямой нитридизацией двухкомпонентных твердых растворов металлов. Развитие технологии специальных материалов на основе бинарных нитридов ZrN–NbN позволит решить важную научно-техническую задачу – разработать способ одностадийного синтеза керамики с упрочняющими или функциональными добавками, повышающими ее эксплуатационные свойства.
Синтез композитной керамики на основе нитрида циркония–нитрида ниобия с сохранением заданной формы исходной заготовки может быть осуществлен прямой нитридизацией металлического проката на основе твердого раствора ниобия в цирконии [10, 11]. Сплавы Zr〈Nb〉 широко используются в качестве конструкционных материалов [12–15]. Влияние содержания ниобия в сплаве на способ его прокатки, свойства и субструктуру описаны в работах [12, 15–18]. Авторы [16, 19] рассматривают насыщение азотом поверхности сплава Zr〈Nb〉 как способ его упрочнения. В работах [16, 19] определены механические свойства упрочненного сплава, показана структура приповерхностного слоя. В доступной литературе отсутствует описание структурных превращений, протекающих при формировании керамики во время высокотемпературной нитридизации твердого раствора Zr〈Nb〉.
Цель настоящей работы – установление структурных превращений в процессе синтеза нитрида твердого раствора ниобия в цирконии при термическом отжиге.
ЭКСПЕРИМЕНТАЛЬНАЯ ЧАСТЬ
Объекты исследования – образцы нитридной керамики, полученной нитридизацией лент из иодидного циркония, ниобия марки Нб-1Пл (ГОСТ 16099-80), твердого раствора ниобия в цирконии с содержанием 0.1, 2.5, 5.0, 7.5 и 10.0 мас. % Nb длиной 60 мм, сечением 3.0 × 0.3 мм. Фольгу перечисленных составов изготавливали способом прокатки.
Элементный состав сплавов определяли на рентгенофлуоресцентном волнодисперсионном спектрометре последовательного типа BRUKER S8 Tiger (серия 2) в вакууме по бесстандартной методике с применением ПО QUANT-EXPRESSTM. При выборе содержания Nb в твердом растворе исходили из литературных данных о свойствах и применении твердых растворов цирконий-ниобий, в том числе упрочненных азотированием, и о введении в состав нитридной керамики допирующих добавок, улучшающих ее свойства.
Нитридизацию образцов проводили резистивным нагревом в атмосфере азота особой чистоты марки “6.0” (ГОСТ 10157-79) в течение 180 мин при температуре 1700, 1900 и 2400°С. Выбранная для синтеза температура расположена ниже, вблизи и выше температуры перитектической реакции [20]. Температуру реакции контролировали пирометром LumaSense IMPAC ISR 50-LO (Германия) (погрешность 0.1% в рассматриваемом диапазоне температур).
Исследование морфологии поверхности поперечных сколов и локальный элементный анализ проводили на растровом электронном микроскопе (РЭМ) LEO 1420, Carl Zeiss c системой энергодисперсионного микроанализа INCA Energy 300, Oxford. Элементный состав определяли на поверхностях поперечных сколов образцов.
Микроструктуру шлифов керамики и исходных сплавов исследовали на оптическом инвертированном микроскопе Carl Zeiss Axio Observer 3 в дифференциально-интерференционном рельефном контрасте и в светлом поле на металлографическом инвертированном микроскопе Olympus GX51.
Рентгенофазовый анализ (РФА) проводили на вертикальном рентгеновском θ–2θ-дифрактометре XRD–6000 (Shimadzu), а также на θ–θ-дифрактометре ARL X`TRA в геометрии Брэгга-Брентанно. В качестве источника использовали рентгеновскую трубку с медным анодом (CuKα). Приборы были откалиброваны по стандартному образцу NIST SRM-1976a, средняя погрешность положения рефлексов на оси 2θ относительно эталона не превышала 0.005°. Кристаллические фазы идентифицировали по банку данных [21].
РЕЗУЛЬТАТЫ И ОБСУЖДЕНИЕ
Морфология поверхности исходных циркониевых сплавов после селективного травления в разбавленном водном растворе HF–NH4HF2 представлена на рис. 1. Для твердого раствора состава Zr–0.1% Nb (рис. 1а) характерна равноосная форма зерен α-Zr размером 30–100 мкм. В твердом растворе с содержанием 2.5–7.5% Nb (рис. 1б) наблюдается однородная субмикронная зеренная структура, состоящая из зерен α-Zr (размер менее 0.2 мкм) [18, 22]. Для сплава Zr–10% Nb (рис. 1в) можно выделить чередующиеся составляющие: “темная” – мелкозернистый α-Zr, “светлая” – вытянутые зерна β-Zr [14, 23], объемная доля которого, определенная с помощью программы анализа микрофотографий РЭМ и расчета площадей включений и пористости керамических материалов ImageJ [24], составляет ~35%. Наличие пор (3–5%) на шлифах объясняется технологией изготовления сплава.
Рис. 1.
Морфология поверхности травленых шлифов исходных сплавов: а – 0.1% Nb, б – 5% Nb, в – 10% Nb.
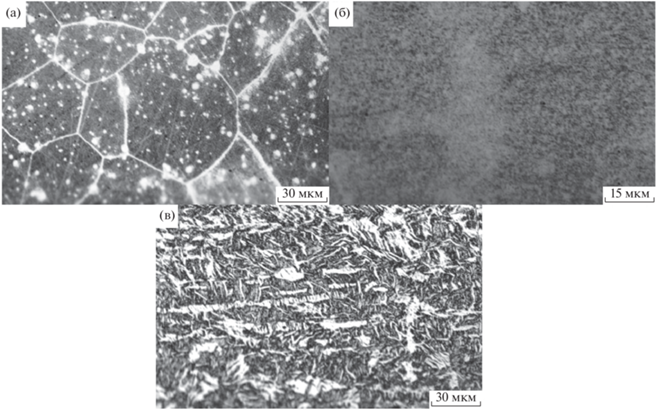
На рис. 2 приведены рентгеновские дифрактограммы исходных сплавов и нитридной керамики Zr–Nb (2.5 и 7.5%).
Рис. 2.
Рентгеновские дифрактограммы керамики Zr–2.5% Nb (а), Zr–7.5% Nb (б): нитриды синтезированы при 1700 (1), 1900 (2), 2400°С (3); исходные сплавы (4).
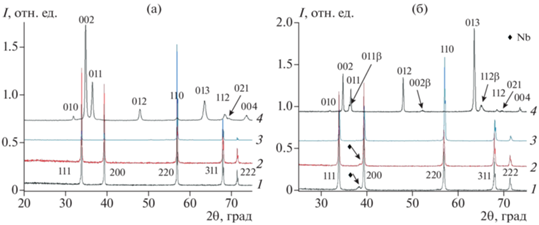
Из данных РФА следует, что при концентрации ниобия ≤2.5% Nb исходный сплав однофазный: α-твердый раствор Zr〈Nb〉 (ГПУ, пр. гр. P/63mmc (194)). Сплав с содержанием Nb ≥ 5% двухфазный, наряду α-твердым раствором Zr〈Nb〉 определяется фаза β-твердого раствора циркония (ОЦК, пр. гр.Im$\bar {3}$m (229)). Доля β-фазы увеличивается с повышением содержания ниобия, что следует из увеличения относительной интенсивности соответствующих отражений. Данные РФА и оптической микроскопии согласуются с приведенными в работах [14, 18, 22], где наличие метастабильной фазы β-Zr объяснено стабилизирующим влиянием ниобия, образующего с β-Zr неограниченную область твердых растворов. Авторы отмечают, что повышение содержания ниобия в сплаве увеличивает долю β-Zr.
На рис. 3 приведены РЭМ-изображения поверхности сколов нитридов ZrN (а), NbN (б) и твердых растворов (в, г), синтезированных при температуре 1900°С в течение 180 мин.
Рис. 3.
РЭМ-изображения поверхности сколов керамики, синтезированной при 1900°С в течение 180 мин: нитрид циркония (а), нитрид ниобия (б), нитрид твердого раствора Zr–2.5% Nb (в), нитрид твердого раствора Zr–7.5% Nb (г).
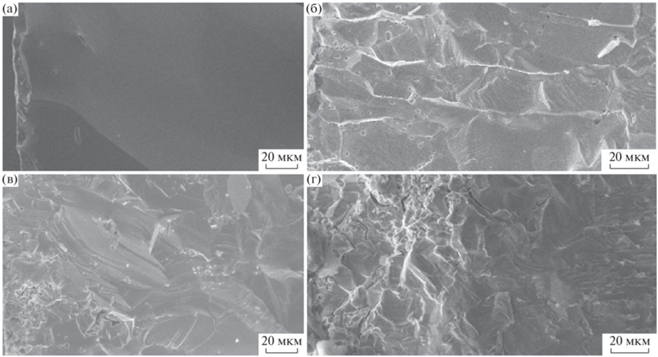
Нитрид иодидного циркония однородный, не содержит пор (рис. 3а), размер зерен равен ширине образца (~300 мкм). Морфология поверхности скола нитрида ниобия характеризуется крупными зернами вытянутой формы, ориентированными перпендикулярно свободной поверхности (рис. 3б). В нитридах твердых растворов Zr〈Nb〉 проявляется пористость, наследующая пористость поверхностных слоев исходной фольги. Морфология поверхности скола в приповерхностном объеме мелкозернистая с размером зерен до 10 мкм и крупными кристаллитами 20–40 мкм, широкая неоднородная по толщине (30–80 мкм) приповерхностная область характеризуется кристаллитами с более мелким зерном (4–20 мкм) (рис. 3в, 3г). Морфологические особенности приповерхностной области предположительно связаны с воспроизведением керамикой исходной микроструктуры проката и с отторжением ниобия из приповерхностного слоя к центру образца в ходе процесса нитридизации. На рис. 4–6 приведены микрофотографии, характеризующие морфологию поверхности шлифа керамики Zr1 – хNbхN, синтезированной при разных температурах.
Рис. 4.
Морфология поверхности шлифов керамики Zr–0.1% Nb (а), Zr–5% Nb (б), Zr–10% Nb (в) после нитридизации при 1700°С в течение 180 мин (цифры характеризуют содержание Nb (ат. %)).
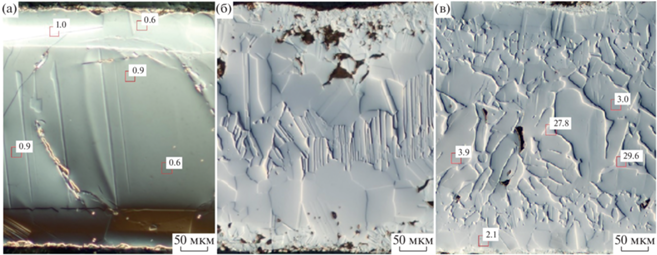
В нитриде твердого раствора с 0.1 мас. % Nb, по данным элементного анализа, количество ниобия, однородно распределенного в объеме материала, составляет ~1 ат. %. На поверхности скола керамики после нитридизации при 1700°С (рис. 4а) и 1900°С (рис. 5а) проявляется двухслойная структура с четкой границей между фазами нитрида циркония, содержащими разное количество азота. Керамика, полученная при 2400°С (рис. 6а), однородная с равномерным распределением азота в объеме. В приповерхностной области образца на глубине ~10–20 мкм содержатся полости, пористость в объеме низкая (1–2%).
Рис. 5.
Морфология поверхности шлифов твердых растворов Zr–0.1% Nb (а), Zr–5% Nb (б), Zr–10% Nb (в) после нитридизации при 1900°С в течение 180 мин (цифры характеризуют содержание Nb (ат. %)).
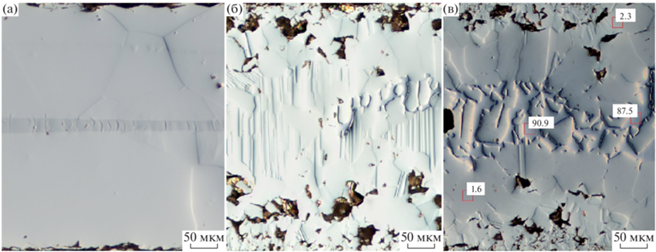
Рис. 6.
Морфология поверхности шлифов твердых растворов Zr–0.1% Nb (а), Zr–5% Nb (б), Zr–10% Nb (в) после нитридизации при 2400°С в течение 180 мин (цифры характеризуют содержание Nb (ат. %)).
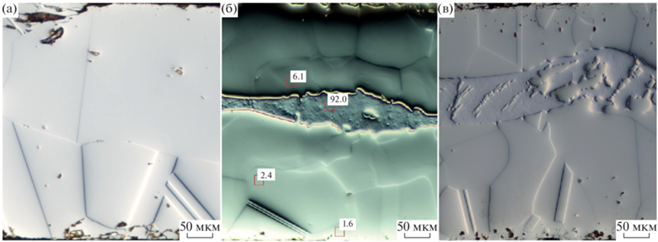
Сопоставление микрофотографий поперечных сколов керамики, синтезированной из сплавов, содержащих 2.5 и 5 мас. %. Nb, подтверждает сходство морфологии поверхностей для каждой исследуемой температуры. В ходе реакции формируется мелкозернистый нитрид с размером зерен до 10 мкм и порами до 3–5 мкм в количестве 5–15% по площади шлифа, в основном расположенными в виде скоплений по границам слоев. В центральной области образца обнаружена фаза с повышенным содержанием Nb, которая при 1700°С сегрегирована между кристаллитами нитрида циркония, а при 1900 и 2400°С ниобий однородно распределен в объеме керамики.
При температуре ниже температуры плавления ниобий однородно распределен в объеме материала за исключением приповерхностного слоя.
В нитриде твердого раствора Zr–5 мас. % Nb при 1700 и 1900°С фаза, содержащая ниобий, сегрегирована между кристаллитами основной фазы (рис. 4б, 5б), при 2400°С она образует слой в центре образца (рис. 6б).
В нитридах твердых растворов с 7.5 и 10 мас. % Nb при 1700 и 1900°С, содержание ниобия, сегрегированного между кристаллитами основной фазы, увеличивается. Ниобий однородно распределен в объеме материала, кроме внешнего слоя толщиной ~30 мкм (рис. 4в). В некоторых областях в центре образца содержание Nb составляет 91 ат. % (рис. 5в), что коррелирует с данными РФА. В образцах, синтезированных при 2400°С, фаза с повышенным содержанием ниобия практически не выделяется, при этом в центре образца обнаружен нитрид циркония с повышенным за счет сегрегации содержанием ниобия ~10–25 ат. %. На сколах отмечено повышенное на ~1 ат. % содержание ниобия в центральной части образца по границам зерен основной фазы. В центре изображения представлено зерно с межкристаллитным расколом. За счет сегрегации ниобия присутствует значительное количество включений с фазой, обогащенной по ниобию (рис. 7).
Рис. 7.
РЭМ-изображение поверхности скола по границам зерна за счет межкристаллитного растрескивания (цифры характеризуют содержание Nb (ат. %)).
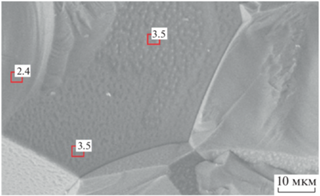
Образование нитридов твердых растворов, содержащих более 2.5 мас. % ниобия, протекает с распадом твердого раствора вследствие связывания циркония, имеющего более высокое химическое сродство к азоту, в тугоплавкий нитрид и выделения ниобия в виде фазы β-Nb. Нитридизация β-Nb начинается только после того, как прореагирует основная часть циркония.
Таким образом, при создании керамики высокотемпературной нитридизацией твердых растворов ниобия в цирконии прослеживается последовательность структурных превращений: на начальной стадии происходит образование гетероструктур, которые при дальнейшем взаимодействии с азотом превращаются в Zr1 – хNbхN. Для чистых металлов и сплавов Zr〈Nb〉 с низким (~0.1%) содержанием ниобия характерно образование трехслойных гетероструктур на основе нитрида соответствующего металла и твердого раствора азота в нем. При нитридизации сплавов составов Zr–(2.5–10 мас. %) Nb формирование керамики происходит через стадию образования композитов Zr1 – хNbхN–(ZrN1 – n/β-твердый раствор Zr в Nb)– Zr1 – хNbхN.
Анализ поперечных сколов подтверждает, что микроструктура синтезированного композитного материала определяется содержанием ниобия в исходном твердом растворе и температурой синтеза. Гетероструктуры, образовавшиеся при нитридизации сплавов с содержанием ниобия до 5 мас. %, во всем температурном интервале характеризуются сосредоточением твердого раствора на основе β-ниобия между кристаллитами основной фазы нитрида циркония. Нитридизация сплавов, содержащих 7.5 и 10 мас. % Nb, при температуре ниже температуры плавления также сопровождается сосредоточением твердого раствора β-ниобия между кристаллитами ZrN. При температуре выше перитектической реакции в случае сплавов с высоким содержанием ниобия формируются трехслойные гетероструктуры, в центре которых расположен твердый раствор β-ниобия. В ходе дальнейшей нитридизации гетероструктур формируется мелкозернистая керамика с размером зерен до 10 мкм и крупными кристаллитами 20–40 мкм. При повышении концентрации Nb в исходном твердом растворе протяженность мелкозернистой структуры в направлении центра керамики увеличивается. При увеличении времени синтеза ниобий полностью растворяется в ZrN1 –n с образованием керамики Zr1 –хNbхN. Морфологические особенности приповерхностной области, в частности низкое содержание ниобия, связаны с отторжением ниобия из приповерхностного слоя в ходе нитридизации. Анализ изображений внешней поверхности и поверхности поперечного скола показывает, что для керамики Zr1 –хNbхN характерна приповерхностная пористость, повторяющая пористость проката.
На основе полученных данных можно предложить механизм нитридизации твердых растворов ниобия в цирконии. Вследствие более высокого химического сродства циркония к азоту на начальной стадии нитридизации сплава Zr〈Nb〉 происходит образование преимущественно нитрида циркония. Рост фазы нитрида циркония до температуры перитектической реакции идет по хемоэпитаксиальному механизму в пределах зерна металла и сопровождается образованием фазы β‑ниобия в результате ее сегрегации на границах формирующихся зерен ZrN. При температуре выше температуры перитектической реакции образуется жидкая фаза, которая “удерживается” в объеме образца слоем тугоплавкого нитрида циркония, содержащего 1–3 ат. % нитрида ниобия. С появлением расплава внутри керамической оболочки образование нитрида происходит как в жидкой фазе, так и на внутренней поверхности внешнего слоя нитрида, что приводит к непрерывному уменьшению количества циркония, образованию β-ниобия, которому свойственна более высокая температура плавления, и его сосредоточению в центральной области образца. По мере расходования циркония твердый раствор β‑ниобия [17, 18, 23] в центральной области образца вступает в реакцию с азотом, растворяясь в ZrN1 –n с образованием керамики Zr1 –хNbхN.
ЗАКЛЮЧЕНИЕ
Процесс нитридизации твердых растворов ниобия в цирконии Zr〈Nb〉 с разным содержанием ниобия характеризуется последовательностью структурных изменений, отражающих этапы образования фаз разного состава – от металлокерамических композитов до нитрида Zr1 –хNbхN.
В ходе высокотемпературного насыщения твердых растворов ниобия в цирконии азотом образуются композиты типа Zr1 –хNbхN–(ZrN1 –n/β-твердый раствор циркония в ниобии)–Zr1 –хNbхN или керамика на основе стехиометрических нитридов циркония и ниобия Zr1 –хNbхN.
Список литературы
Arai Y., Nakajima K. Preparation and Characterization of PuN Pellets Containing ZrN and TiN // J. Nucl. Mater. 2000. V. 281. № 2–3. P. 244–247. https://doi.org/10.1016/S0022-3115(00)00393-7
Streit M., Ingold F., Pouchon M., Gauckler L.J., Ottaviani J.P. Zirconium Nitride as Inert Matrix for Fast Systems // J. Nucl. Mater. 2003. V. 319. P. 51–58. https://doi.org/10.1016/S0022-3115(03)00133-8
Wheeler K., Peralta P., Parra M., McClellan K., Dunwoody J., Egeland G. Effect of Sintering Conditions on the Microstructure and Mechanical Properties of ZrN as a Surrogate for Actinide Nitride Fuels // J. Nucl. Mater. 2007. V. 366. № 3. P. 306–316. https://doi.org/10.1016/j.jnucmat.2007.03.023
Деменюк В.Д., Юрлова М.С., Лебедева Л.Ю., Григорьев Е.Г., Олевский Е.А. Методы электроимпульсной консолидации: альтернатива спарк-плазменному спеканию (обзор литературы) // Ядерная физика и инжиниринг. 2013. Т. 4. № 3. С. 195–239. https://doi.org/10.1134/S2079562913030019
Hollmer T. Manufacturing Methods for (U–Zr)N-Fuels: Student Thesis. Stockholm: AlbaNova University Centre, 2011. P. 80.
Башлыков С.С., Деменюк В.Д., Григорьев Е.Г., Олевский Е.А., Юрлова М.С. Электроимпульсный метод компактирования порошка мононитрида урана // Физика и xимия обработки материалов. 2013. № 5. С. 77–83.
Graziani T., Bellosi A. Densification and Characteristics of TiN Ceramics // J. Mater. Sci. Lett. 1995. V. 14. № 15. P. 1078–1081. https://doi.org/10.1007/BF00258170
Song J., Jiang L., Liang G., Gao J., An J., Cao L., Xie J., Wang S., Lv M. Strengthening and Toughening of TiN-Based and TiB2-Based Ceramic Tool Materials with HfC Additive // Ceram. Int. 2017. V. 43. № 11. P. 8202–8207. https://doi.org/10.1016/j.ceramint.2017.03.147
Kovalev I.A., Shokodko A.V., Shevtsov S.V., Ogarkov A.I., Ashmarin A.A., Tenishev A.V., Kolomiets T.Yu., Shokodko E.A., Chesnokov A.A., Shornikov D.P., Kochanov G.P., Chernyavskii A.S., Solntsev K.A. Development of a Fuel Element on the Basis of the Composition (Zr,U)N for a High-Temperature Reactor // J. Phys.: Conf. Ser. 2018. V. 1134. № 1. P. 012075. https://doi.org/10.1088/1742-6596/1134/1/012075
Solntsev K.A., Shustorovich E.M., Buslaev Y.A. Oxidative Constructing of Thin-Walled ceramics (OCTWC) // Dokl. Chem. 2001. V. 378. № 4–6. P. 143–149.
Солнцев К.А., Шусторович Е.М., Чернявский А.С., Дуденков И.В. Окислительное конструирование тонкостенной керамики (ОКТК) выше температуры плавления металла: получение оксидных волокон из волокон Al и его сплава // Докл. Академии наук. 2002. T. 385. № 3. С. 372–377.
Кононов А.Г., Кукареко В.А., Белый А.В., Шаркеев Ю.П. Ионно-модифицированные субмикрокристаллические титановые и циркониевые сплавы для медицины и техники. // Механика машин, механизмов и материалов. 2013. T. 1. № 22. P. 47–53.
Zhaoa Y., Lib H., Huanga Yu. The Structure, Mechanical, Electronic and Thermodynamic Properties of bcc Zr–Nb Alloy: A First Principles Study // Journal Alloys Compd. 2021. V. 862. P. 158029.
Daniel C.S., Honniball P.D., Bradley L., Preuss M., Fonseca J.Q. Texture Development During Rolling of α + β Dual-Phase ZrNb Alloys/Zirconium in the Nuclear Industry: 18th Int. Symp. STP 1597. 2018. https://doi.org/10.1520/STP159720160070
Соколенко В.И., Мац А.В., Мац В.А. Механические характеристики наноструктурированных циркония и цирконий-ниобиевых сплавов // Физика и техника высоких давлений. 2013. Т. 23. № 2. С. 96–102.
Белый А.В., Кононов А.Г., Кукареко В.А. Влияние ионно-лучевого азотирования на структурнофазовое состояние и триботехнические характеристики поверхностных слоев сплава Zr–2.5% Nb // Тр. БГТУ. 2016. № 2. С. 87–99.
Тихончев М.Ю., Светухин В.В. Расчет пороговых энергий атомных смещений вблизи протяженной границы раздела фаз ГПУ-Zr и ОЦК-Nb методом молекулярной динамики // Изв. Самарского науч. центра Российской академии наук. 2012. Т. 14. № 4 (4). С. 1143–1148.
Неклюдов И.М., Ажажа В.М., Воеводин В.Н., Бородин О.В., Петельгузов И.А., Василенко Р.Л., Рыбальченко Н.Д., Роенко Н.М. Исследование микроструктуры ТВЭЛьных труб из кальциетермического сплава Zr1Nb (КТЦ-110) // Вопросы атомной науки и техники. 2002. № 6 (82). С. 106–111.
Liu Y.Y., Yang Y., Dong D., Wang J., Zhou L. Improving Wear Resistance of Zr–2.5Nb Alloy by Formation of Microtextured Nitride Layer Produced via Laser Surface Texturing/Plasma Nitriding Technology // Surf. Interfac. 2020. V. 20. P. 100638–100644.
Ushakov S.V., Navrotsky A., Hong Q.-J., Walle A. Carbides and Nitrides of Zirconium and Hafnium // Materials. 2019. V. 12. № 17. P. 2728. https://doi.org/10.3390/ma12172728
Powder Diffraction File. Alphabetical Index Inorganic Compounds. Pensilvania: ICPDS. 1997.
Kondo R., Nomura N., Suyalatu, Tsutsumi Yu., Doi H., Hanawa T. Microstructure and Mechanical Properties of As-Cast Zr–Nb Alloys // Acta Biomater. 2011. V. 7. P. 4278–4284.
Abriata J.P., Bolcich J.C. The Nb−Zr (Niobium−Zirconium) System // J. Phase Equilib. 1982. № 3(1). P. 34–44.
Collins T.J. Images for Microscopy // BioTechniques. 2007. V. 43. P. 25–30.
Дополнительные материалы отсутствуют.
Инструменты
Неорганические материалы