Неорганические материалы, 2022, T. 58, № 7, стр. 792-800
Получение керамики гидроксиапатита методом высокоскоростного микроволнового послойного спекания
С. С. Балабанов 1, С. В. Егоров 2, А. Г. Еремеев 2, И. В. Плотников 2, Е. Е. Ростокина 1, *, К. И. Рыбаков 2, А. А. Сорокин 2, В. В. Холопцев 2
1 Институт химии высокочистых веществ им. Г.Г. Девятых Российской академии наук
603137 Нижний Новгород, ул. Тропинина, 49, Россия
2 Федеральный исследовательский центр Институт прикладной физики Российской академии наук
603950 Нижний Новгород, ул. Ульянова, 46, Россия
* E-mail: rostokina@ihps-nnov.ru
Поступила в редакцию 16.02.2022
После доработки 24.03.2022
Принята к публикации 25.03.2022
- EDN: EPMJSS
- DOI: 10.31857/S0002337X2206001X
Аннотация
На примере гидроксиапатита представлены первые результаты исследования нового аддитивного метода изготовления керамических изделий, заключающегося в многократном последовательном нанесении слоев суспензии с высоким содержанием порошкового материала и их высокоскоростном микроволновом спекании на частоте 24 ГГц. Исследована устойчивость водных суспензий порошка гидроксиапатита с субмикронным размером частиц в зависимости от pH дисперсионной среды и используемых диспергаторов. Получены суспензии с высоким значением массы твердой загрузки и текучестью, достаточной для обеспечения сплошности слоев, наносимых методом дозирующего лезвия. Методом послойного микроволнового спекания со скоростью нагрева до 30°C/мин и максимальной температурой до 1330°C получены образцы керамики с плотностью до 92% от теоретического значения с замкнутой системой пор микронных размеров.
ВВЕДЕНИЕ
Известные методы аддитивного формирования основаны на изготовлении изделий по компьютерной 3D-модели путем последовательного добавления материала и его сплавления с использованием лазерного излучения [1, 2]. Однако для создания керамических и композиционных изделий, в отличие от металлических, применение лазерного нагрева связано с принципиальными трудностями, обусловленными высокой температурой спекания и низкой теплопроводностью материалов. Для аддитивного изготовления керамических изделий разрабатываются специальные методы (см., например, [3]).
В последние годы активно внедряются новые подходы в 3D-технологиях, заключающиеся в послойном формировании порошковой заготовки с последующей консолидацией слоев спеканием в печах резистивного типа. Одним из таких методов является метод стереолитографии (SLA- или LCM-технология), основанный на отверждении контролируемой засветкой ультрафиолетовым излучением суспензии порошка в жидком мономере [4]. В этом случае трехмерный объект, как правило, формируется послойно под воздействием УФ-излучения на подвижной платформе, погружаемой или извлекаемой из ванны, после чего изделие проходит термическую обработку для выжигания органического связующего с последующим спеканием оставшегося порошкового материала. Высокотемпературная стадия уплотнения материала является необходимой процедурой практически всех процессов изготовления керамических изделий методом аддитивной технологии, независимо от способа создания “сырого” прототипа.
Использование микроволнового нагрева позволяет значительно сокращать время спекания керамических изделий и улучшать их качество (получать более тонкую и однородную микроструктуру, повышенные физико-механические свойства, обеспечивать точное формообразование) [5, 6]. СВЧ-гиротронные комплексы 24 и 263 ГГц [7, 8], используемые в наших работах, позволяют направлять интенсивное излучение миллиметрового или субмиллиметрового диапазона в технологическую камеру в виде однородного (рассеянного) или сфокусированного волнового пучка. Излучение высокой интенсивности обеспечивает необходимый темп нагрева керамических изделий и позволяет спекать объекты больших размеров. Несомненными преимуществами применения миллиметрового излучения для изготовления керамических изделий по сравнению с лазерным являются объемный характер нагрева, увеличенный размер области эффективного энерговыделения, возможность нагрева материалов с низкой теплопроводностью, высокой температурой спекания и малой устойчивостью к термическим ударам.
В ряде публикаций, в том числе и авторами настоящей работы, показана возможность реализации процесса сверхбыстрой консолидации многих оксидных керамик в поле интенсивного микроволнового излучения [9–12]. Основной причиной перехода в режим ускоренного спекания является развитие тепловой неустойчивости, возникающей в результате роста эффективной электрической проводимости материала и, соответственно, коэффициентов поглощения микроволнового излучения при увеличении температуры. Развитие тепловой неустойчивости в этом случае может сопровождаться образованием на поверхности частиц высокопоглощающей фазы с повышенными транспортными свойствами [12–14].
Эффективность использования микроволнового излучения в задачах спекания и быстрого трехмерного формирования керамических объектов в значительной мере определяется морфологией и микроструктурой исходных материалов. Естественно, применение ультрадисперсных и наноразмерных порошковых материалов позволяет значительно сокращать время спекания изделий и улучшать их механические свойства.
Для реализации процесса высокоскоростного микроволнового спекания слоистых порошковых структур и получения в итоге однородных керамических материалов с требуемыми физико-химическими характеристиками неотъемлемой и важной стадией является приготовление суспензий порошков для послойного нанесения. Такие суспензии должны быть устойчивы к агрегации, обладать вязкостью, достаточной для обеспечения сплошности наносимых слоев заданной толщины, а также иметь высокое содержание дисперсной фазы. Как правило, коллоидные водные суспензии порошков термодинамически неустойчивы из-за большой свободной поверхностной энергии, в связи с чем проводят их стабилизацию различными диспергаторами. В качестве таких добавок обычно используются неионогенные или ионогенные вещества/полимеры, которые адсорбируются на поверхности частиц и обеспечивают повышенную стабильность суспензии за счет электростатических, стерических или электростерических сил (последнее наиболее применимо к высококонцентрированным дисперсиям). В литературе имеется значительное количество работ по применению лимонной, полиакриловой и полиметакриловой кислот, их солей и др. в качестве диспергаторов для керамических порошков [15–19].
В качестве объекта исследований в данной работе был использован гидроксиапатит (Ca10(PO4)6(OH)2, ГАП), представляющий большой интерес как биосовместимый материал. В силу сходства химического состава ГАП с минеральной составляющей костной ткани материалы на его основе находят широчайшее применение в различных областях медицины (стоматологии, ортопедии, хирургии) в виде керамики, цементов, композитов и т. д. [1, 20, 21]. Вопрос получения водных суспензий ГАП, особенно высококонцентрированных, и их стабилизации к настоящему времени остается открытым, поскольку большинство работ, тем или иным образом касающихся этого направления, фокусируются лишь на изучении реологических свойств дисперсий [20, 22, 23]. Для реализации аддитивной технологии керамических материалов из ГАП весьма актуально более подробное изучение данного вопроса.
Целью данной работы являлось получение суспензий порошков ГАП с характеристиками, достаточными для обеспечения сплошности наносимых слоев, и последующее высокоскоростное послойное спекание изготовленных структур в поле интенсивного микроволнового излучения.
ЭКСПЕРИМЕНТАЛЬНАЯ ЧАСТЬ
В качестве исходного порошка использовали гидроксиапатит марки ГАП-85д (НПО “Полистом”, Россия). Суспензии получали смешением порошка ГАП с бидистиллированной водой с последующей обработкой в планетарной мельнице в течение 1 ч и ультразвуковой ванне в течение 20 мин. На первоначальном этапе были приготовлены суспензии порошка с концентрацией 10 мас. % твердой фазы, из которых впоследствии отбирались аликвоты для коллоидно-химических измерений. Аликвоты разбавлялись бидистиллированной водой до нужной концентрации. Для стабилизации суспензий применялось несколько диспергаторов, обеспечивающих электростатический тип стабилизации (цитрат этаноламмония (Dolapix CE64) и цитрат аммония) и отвечающих за электростерическую стабилизацию (полиакрилат аммония и полиакрилат натрия (Акремон D-1 AA)). Высококонцентрированные дисперсии (с концентрацией твердой фазы 40–60 мас. %) получали аналогичным образом на основании проведенных коллоидно-химических исследований.
Определение размеров и электрокинетического потенциала частиц дисперсной фазы суспензий проводили методами динамического и электрофоретического рассеяния света соответственно на анализаторе частиц и дзета-потенциала NanoBrook 90 Plus Zeta (Brookhaven Instruments, США). Значения pH суспензий определяли с помощью портативного pH-метра HI 991300 (Hanna Instruments, США). Калибровку прибора осуществляли, используя буферные растворы с pH 6.86, 4.00 и 9.18. Относительная погрешность измерений составляла ±0.1 единиц pH. С использованием водного раствора аммиака (ОСЧ 25–5) и азотной кислоты (ОСЧ 27–4) варьировали pH дисперсионной среды.
Для изучения седиментационной устойчивости 20%-ную дисперсию ГАП помещали в несколько пробирок, в каждую из которых добавляли различное количество диспергатора. Пробирки периодически встряхивали в течение 12 ч для полной сорбции диспергатора, затем оставляли отстаиваться на 3 сут после чего измеряли высоту седиментационного слоя.
Микроволновое спекание образцов проводили послойно в однородном электромагнитном поле в рабочей камере специализированного гиротронного комплекса, работающего в непрерывном режиме на частоте 24 ГГц с автоматически регулируемой выходной мощностью до 6 кВт [7]. В каждом опыте послойное спекание проводили одновременно на нескольких (4 или 5) образцах. Для повышения однородности температуры в теплоизоляцию из пористого оксида алюминия встраивался внутренний керамический тигель из диоксида циркония (рис. 1). Теплоизоляционная сборка с образцами располагалась в средней части рабочей камеры (характерный размер камеры L ≈ 50λ, где λ = 1.25 см – длина волны излучения). Температуру измеряли двумя неизолированными платиново-родиевыми термопарами (В-типа), контактирующими с образцами в разных частях тигля (рис. 1), что позволяло контролировать однородность температуры в теплоизоляционной сборке.
Рис. 1.
Фотография четырех образцов ГАП, загруженных в тигель из диоксида циркония для проведения микроволнового спекания.
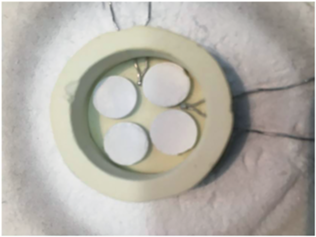
В качестве подложки для нанесения слоев использовалась керамика ГАП, изготовленная прессованием в металлической форме исходного порошка с последующим микроволновым спеканием до плотности порядка 80% от теоретической. Слои суспензии на подложку наносили методом дозирующего лезвия (doctor blade). Процессы микроволнового спекания проводили в форвакууме при давлении остаточного воздуха порядка 1 Па. На начальном этапе образцы нагревали до 800°C с относительно медленной скоростью 10°C/мин с целью удаления ПАВ и воды. Затем скорость нагрева увеличивали до 20–30°C/мин, и образцы нагревали до температуры 1150–1180°C без изотермической выдержки так, чтобы плотность образцов не превышала 80%. Формирование многослойных систем проводилось по следующей схеме. Первый слой наносили на все подложки. После микроволнового спекания наносили следующий слой на все образцы, за исключением одного, и повторяли процесс спекания всех образцов в том же режиме. По такому же сценарию спекали образцы с последующими нанесенными слоями. В заключительном процессе нагрева максимальная температура составляла 1300 или 1330°C; в последнем случае использовалась изотермическая выдержка в течение 20 мин.
Плотность образцов после спекания измеряли методом гидростатического взвешивания в дистиллированной воде с точностью 0.01 г/см3.
Исследование порошков и микроструктуры слоев (на поперечных сколах спеченных образцов) проводили при помощи сканирующего электронного микроскопа JSM-6390LA (JEOL, Япония).
Образцы с последовательно нанесенными и спеченными слоями ГАП подвергали испытаниям на микротвердость по Виккерсу ${{H}_{v}}$ на механическом тестере Struers Duramin-5 (Struers, Дания) при нагрузке 9.8 Н.
РЕЗУЛЬТАТЫ И ОБСУЖДЕНИЕ
Характеристики порошка ГАП. Как свидетельствуют многочисленные экспериментальные результаты, гранулометрический состав исходных порошков оказывает существенное влияние на процесс консолидации, микроструктуру и свойства конечного керамического материала. В данной работе использовался коммерческий порошок ГАП с заявленным производителем размером частиц 0.7–2 мкм и удельной площадью поверхности 3–10 м2/г. Микрофотографии порошка приведены на рис. 2. Видно, что первичные субмикронные частицы имеют вытянутую форму, иногда разветвлeнную, и объединены в агломераты, достигающие размеров около 10 мкм. Измеренная удельная площадь поверхности составила SБЭТ = 4.1 м2/г, что соответствует эквивалентному диаметру частиц dБЭТ = 460 нм.
На рис. 3 приведены гистограммы распределения частиц суспензии порошка ГАП по размерам до и после ультразвуковой (УЗ) обработки в течение 5 и 20 мин. Проведенные измерения хорошо согласуются с данными электронной микроскопии. Видно двухмодовое распределение частиц по размерам. Практически все первичные частицы исходного порошка ГАП объединены в агломераты с максимумами мод на 2 и 9 мкм. УЗ-обработка суспензии приводит к повышению дисперсности порошка. Увеличение доли микронных частиц после 5 мин УЗ-обработки по сравнению с исходным порошком, вероятно, произошло из-за разрушения более крупных агломератов, размер которых превышает рабочий диапазон прибора. Более продолжительная УЗ-обработка способствует более эффективному разрушению агломератов частиц и уменьшению среднего размера последних. Как видно из гистограммы, после УЗ-обработки суспензии в течение 20 мин бόльшая доля частиц имеет субмикронный размер, доля частиц микронного размера не превышает 10%. В связи с этим для обеспечения наилучшего покрытия поверхности порошка диспергаторами введение последних проводили в процессе УЗ-диспергирования.
Стабилизация водных суспензий порошка ГАП. Одной из важнейших коллоидно-химических характеристик дисперсных систем является их устойчивость к агрегации. Агрегативная устойчивость суспензий зависит от многих факторов, среди которых одним из определяющих является pH дисперсионной среды.
Для оценки стабильности рассматриваемой системы были проведены измерения электрокинетического потенциала (дзета(ζ)-потенциала) частиц суспензий ГАП при различных значениях pH дисперсионной среды, но постоянной величине концентрации дисперсной фазы. Измерения проводились при концентрации дисперсной фазы 0.05 мас. %. Полученные зависимости приведены на рис. 4.
Рис. 4.
Зависимость ζ-потенциала частиц ГАП от pH для водных суспензий с концентрацией дисперсной фазы 0.05 мас. %.
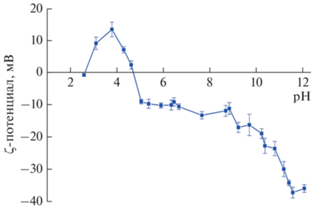
Исходная водная суспензия ГАП характеризуется слабощелочной средой (pH ~ 7.8) и имеет отрицательное значение ζ-потенциала, равное –13 мВ, что недостаточно для хорошей устойчивости системы только за счет электростатической составляющей. При pH ~ 4.7 ζ-потенциал достигает нулевого значения (изоэлектрическая точка (ИЭТ)), при котором адсорбция положительно и отрицательно заряженных ионов на поверхности частиц эквивалентна; система в таком состоянии максимально неустойчива. С повышением кислотности среды после ИЭТ ζ-потенциал возрастает и приобретает положительное значение за счет преобладания адсорбции на поверхности частиц положительно заряженных H+-ионов. В области pH > 11 количество гидроксилов, адсорбированных на поверхности частиц, достигает максимума и наблюдается минимум (максимум по абсолютной величине) значений ζ-потенциала суспензий (~−37 мВ при pH 11.5). В сильнокислой (pH < 3) и сильнощелочной средах (pH > 11.5) ζ-потенциал имеет тенденцию к снижению, что можно объяснить теорией ДЛФО. Как в сильнокислой, так и в щелочной средах требуется больше HNO3 и NH4OH для регулирования значений pH, в результате чего повышается ионная сила суспензии, что приводит к сжатию двойного электрического слоя на частицах и, как следствие, снижению их ζ‑потенциала. Агрегативно устойчивая суспензия может быть получена при высоком абсолютном значении ζ-потенциала частиц (>|30| мВ), что обусловлено высокой плотностью поверхностного заряда для создания достаточной отталкивающей силы двойного электрического слоя. Данный вид стабилизации хорошо подходит для низкоконцентрированных дисперсий субмикронных порошков, но не очень эффективен в случае высококонцентрированных суспензий, в связи с чем требуется дополнительное введение диспергаторов.
На рис. 5 приведены результаты измерений ζ‑потенциала частиц ГАП в зависимости от концентрации анионных диспергаторов: Dolapix CE64, Акремона D-1 AA, полиакрилата аммония и цитрата аммония. Исследования проводили при pH > 8.5 ввиду наибольшей степени диссоциации диспергаторов и устойчивости суспензий в этом диапазоне значений pH. Как видно из рис. 5, введение в суспензию цитрата аммония и Dolapix CE64 приводит к повышению значения ζ-потенциала частиц от |20| до |37| мВ. Кривые имеют схожий характер ввиду близости свойств рассматриваемых диспергаторов. Использование данных добавок также способствует смещению ИЭТ в область меньших pH (на рис. 6 приведены данные по Dolapix CE64, для цитрата аммония наблюдается аналогичная картина) по сравнению с суспензией без добавок (рис. 4). Сдвиг ИЭТ является результатом адсорбции отрицательно заряженных цитрат-ионов на поверхности частиц ГАП. Наиболее высокие абсолютные значения электрокинетического потенциала, требуемые для получения относительно стабильной суспензии, достигаются при концентрации 2 мас. % Dolapix CE64 и 2–2.5 мас. % цитрата аммония. Дальнейшее увеличение количества рассматриваемых диспергаторов практически не изменяет ζ-потенциал. Тем не менее, избыточное количество диспергатора может неблагоприятным образом сказываться на стабильности суспензии. Неадсорбированные молекулы диспергатора действуют как свободный электролит, снижая электростатическое отталкивание между частицами за счет сильного экранирования эффективного заряда на частицах. Этот эффект становится более очевидным с увеличением концентрации таких добавок, что приводит к постепенному повышению вязкости дисперсий за счет агрегации частиц.
Рис. 5.
Зависимости ζ-потенциала частиц ГАП от концентрации диспергаторов при pH дисперсионной среды 10.7.
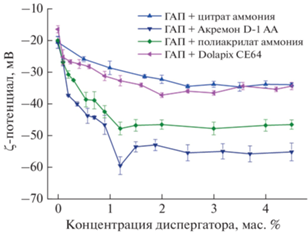
Несколько иное поведение суспензий ГАП наблюдается при введении в состав Акремона D-1 AA и полиакрилата аммония (рис. 5). Добавление указанных диспергаторов приводит к существенно большему росту электрокинетического потенциала и, как следствие, большей устойчивости суспензий ГАП. Повышение устойчивости дисперсной системы в данном случае происходит за счет комбинации электростатического и стерического факторов, что наиболее эффективно для стабилизации суспензий субмикронных порошков. Наибольшее абсолютное значение ζ-потенциала (|60| мВ для суспензии с Акремоном D-1 AA и |48| мВ – с полиакрилатом аммония) соответствует концентрации добавок 1.2 мас. %. Дальнейшее повышение концентрации диспергаторов нецелесообразно ввиду отсутствия их влияния на ζ-потенциал и возможности повторной агрегации частиц при их избытке. ИЭТ не была достигнута в исследуемом диапазоне значений pH в присутствии рассматриваемых диспергаторов (на рис. 6 приведены данные по Акремону D-1 AA, для полиакрилата аммония наблюдается аналогичная картина).
На рис. 7 показаны результаты исследования седиментационной устойчивости суспензий ГАП (20 мас. %) в присутствии полиакрилата аммония. Поскольку наибольшая стабильность разбавленных (0.05 мас. %) суспензий наблюдалась в щелочной среде, pH концентрированных суспензий также поддерживали на уровне 10.8. Оценку выполняли путем измерения отношения текущей высоты мутного слоя после отстаивания в течение 3 сут (H) к максимальной высоте (Hmax).
Рис. 7.
Зависимость относительной высоты седиментационного слоя от концентрации полиакрилата аммония для суспензий ГАП с концентрацией дисперсной фазы 20 мас. % при pH 10.8.
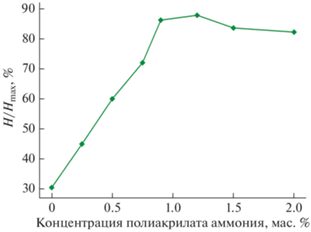
Суспензия ГАП без диспергатора спустя несколько минут после начала эксперимента начинает расслаиваться на два четко различимых слоя: слой осадка и слой прозрачного надосадочного раствора. Относительная высота седиментационного слоя H/Hmax составляет ~30%. Введение в суспензию диспергатора приводит к увеличению H/Hmax (соответственно, увеличению агрегативной устойчивости). Наиболее устойчивой (наименее седиментирующей) является суспензия ГАП, содержащая 1.2 мас. % полиакрилата аммония. Полученные данные находятся в хорошем соответствии с результатами измерений электрокинетического потенциала.
Высококонцентрированные суспензии ГАП были получены при pH дисперсионной среды 10.8 и концентрации полиакрилата аммония 1.2 мас. %. Введение диспергатора позволяет увеличить массу твердой загрузки до 60% при сохранении достаточной текучести суспензии.
Микроволновое послойное спекание. Для нанесения слоев ГАП использовали суспензию с содержанием порошка 60 мас. %. Вследствие нанесения суспензии вручную существовала некоторая погрешность в толщине наносимого слоя, но в целом она соответствовала высоте используемого шаблона дозирующего лезвия 150 мкм. Толщина наносимого слоя была достаточно малой для быстрого высыхания воды (пока осуществлялась загрузка образца в камеру для спекания). Длительность цикла спекания составляла около 100 мин, а с учетом ручного нанесения суспензии, загрузки-выгрузки образца и остывания требуемое время на нанесение одного слоя составляло около 2.5–3 ч. Конечная толщина слоя после спекания была около 100 мкм.
Несмотря на то что послойное спекание требует больше времени для создания объемных изделий, чем метод стереолитографии, на наш взгляд, оно имеет ряд преимуществ. Близость плотности каждого слоя после спекания к конечной плотности изделия не требует сложного моделирования процессов усадки. Контроль размеров каждого слоя и, при необходимости, их коррекция – простой и легко автоматизируемый процесс. Моделирование усадки при спекании заготовки, полученной методом стереолитографии, основано на прецизионной воспроизводимости характеристик суспензии, что обусловливает очень высокие эксплуатационные расходы данной технологии. Изготовление суспензии для микроволнового послойного спекания возможно в лабораторных условиях из коммерчески производимых порошков ГАП.
В настоящей работе были получены две серии керамических образцов ГАП методом послойного микроволнового спекания. В каждой серии образцы, отличающиеся количеством нанесенных слоев, спекались одновременно, т.е. имели одинаковую историю нагревов. Первая серия образцов спекалась при максимальной температуре 1300°С без изотермической выдержки, вторая – при 1330°C с изотермической выдержкой 20 мин. Для осуществления указанных режимов нагрева величина микроволновой мощности не превышала 700 Вт в пике и 400 Вт в среднем.
Измеренная плотность пятислойного образца, спеченного при максимальной температуре 1300°С без изотермической выдержки, после сошлифовки подложки составила 70% от теоретической величины плотности ГАП (ƍтеор = 3.156 г/см3). Плотность четырехслойного образца, спеченного при максимальной температуре 1330°C с изотермической выдержкой, составила 92%.
На рис. 8 представлены микрофотографии поперечных разломов пятислойного и четырехслойного образцов керамики ГАП. Наружная часть образцов толщиной порядка 100 мкм имеет более плотную структуру вследствие большей вероятности миграции вакансий к поверхности и их разрядки на ней. Это обусловливает практически нулевую открытую пористость и, соответственно, низкое водопоглощение полученной керамики. Более глубокие слои имеют однородную пористую структуру, граница раздела слоев часто неразличима или проявляется тонкой прослойкой материала повышенной плотности, который формируется за счет частичного попадания суспензии в поры предыдущего слоя.
Рис. 8.
Микрофотографии поперечных разломов пятислойной (a) и четырехслойной (б) керамики ГАП (подложка сверху).
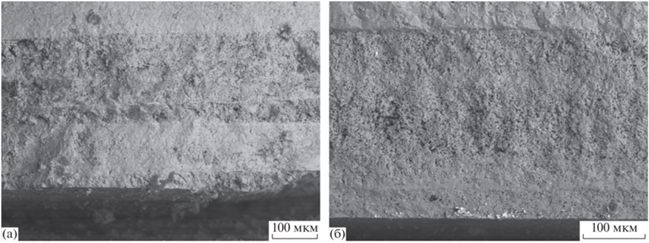
На рис. 9 представлена микрофотография границы раздела подложки и первого нанесенного слоя керамики ГАП. Видно, что, несмотря на высокую скорость нагрева и отсутствие выдержки при максимальной температуре, произошло спекание частиц порошка друг с другом и с подложкой с формированием хорошо закристаллизованных зерен. Средний размер зерна во внутренних слоях составляет около 6 мкм для пятислойного образца (спеченного при 1300°С без выдержки), а в случае более плотного четырехслойного образца (спеченного при 1330°С с изотермической выдержкой 20 мин) – около 8 мкм.
Рис. 9.
Микрофотография границы раздела подложки (сверху) и первого слоя (снизу) пятислойной керамики ГАП.
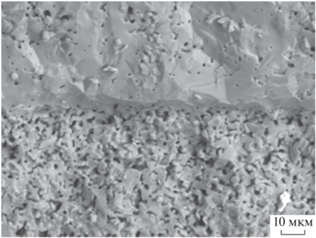
Для качественного прорастания керамического импланта костной тканью необходимо бимодальное распределение пор по размерам. Структура и объем микронных пор определяют скорость биорезорбции керамики, тогда как соответствующие характеристики пор размером 50–500 мкм отвечают за эффективность остеоинтеграции в живые ткани керамики ГАП. В зависимости от места установки импланта различаются и требования к пористой структуре. В полученных из суспензии слоях наблюдаются поры размером 1–5 мкм (рис. 8). Важной особенностью полученной структуры является то, что поры не изолированы (как, например, в подложке), а образуют большей частью связанные каналы. Можно предположить высокую скорость резорбции такой керамики. Для уменьшения скорости резорбции можно использовать спекание при более высокой температуре (например, как во второй серии образцов) и, соответственно, снизить микронную пористость. Крупные поры можно формировать на стадии нанесения слоев удалением ненужного материала. В отличие от методов приготовления шихты с выгорающими добавками, послойное спекание позволяет формировать регулярную структуру пор для обеспечения большей механической прочности керамики ГАП.
В табл. 1 приведены данные микротвердости образцов ГАП из разных серий, содержащих разное количество нанесенных слоев. После вдавливания алмазного индентора не наблюдалось расслоения образцов, что указывает на достаточно высокую изотропность структуры. Достаточно высокая погрешность измерения ${{H}_{v}}$ связана с невозможностью выполнения более качественной пробоподготовки слоистого образца и невозможностью проведения достаточного количества измерений на одном образце. Микротвердость первого слоя минимальна, а у последующих выше и примерно одинакова. На наш взгляд, это может быть связано с различным распределением пор по размерам. Перед окончательным уплотнением подложка, полученная одноосным прессованием, имела более однородные субмикронные поры, тогда как слои, сформированные из высококонцентрированной суспензии, вероятно, обладали бимодальным распределением пор: субмикронными, образовавшимися вследствие агрегации частиц, и микронными – между агломератами. На стадии спекания в первую очередь удалялись субмикронные поры, а микронные служили центрами стока вакансий. Если во всех слоях на микронных порах разряжались только собственные вакансии, то в первом слое добавлялись также вакансии подложки. В связи с этим первый слой обладал большей пористостью и, соответственно, меньшей прочностью. Этот механизм хорошо выражен для образцов, полученных при tmax = 1300°С без выдержки, и менее выражен в случае более плотных образцов, спеченных при tmax = 1330°С с выдержкой 20 мин, где микронная пористость распределилась на большее количество слоев и в значительной степени снизилась.
Таблица 1.
Микротвердость по Виккерсу (${{H}_{v}}$) образцов керамики ГАП с различным количеством слоев в зависимости от условий спекания
Количество слоев | ${{H}_{v}}$, ГПа (tmax = 1300°С, без выдержки) | ${{H}_{v}}$, ГПа (tmax = 1330°С, выдержка 20 мин) |
---|---|---|
0 | 2.5 ± 0.1 | 2.5 ± 0.1 |
1 | 0.2 ± 0.1 | 1.8 ± 0.3 |
2 | 0.3 ± 0.1 | 1.7 ± 0.4 |
3 | 0.4 ± 0.1 | 1.9 ± 0.3 |
4 | 0.4 ± 0.1 | 2.0 ± 0.5 |
5 | 0.4 ± 0.1 |
ЗАКЛЮЧЕНИЕ
Исследована устойчивость водных суспензий субмикронного порошка ГАП в зависимости от pH дисперсионной среды и используемых диспергаторов. При значении pH 10.8 и концентрации полиакрилата аммония 1.2 мас. % получены суспензии с массой твердой загрузки 60% и текучестью, достаточной для обеспечения сплошности наносимых слоев методом дозирующего лезвия.
Последующим микроволновым спеканием многослойной заготовки со скоростью нагрева 30°C/мин при 1300°С без изотермической выдержки получена керамика ГАП плотностью 70% от теоретической. Повышение температуры спекания до 1330°С и применение изотермической выдержки 20 мин позволили увеличить плотность керамики до 92%. Полученная керамика ГАП характеризуется сообщающейся системой внутренних пор размером 1–5 мкм и плотной внешней оболочкой, обеспечивающей практически полное отсутствие водопоглощения. Повышение плотности керамики привело к существенному увеличению микротвердости слоев: с ~0.4 ГПа до значений, близких к микротвердости керамики, спеченной из заготовок, полученных одноосным прессованием (~2 ГПа). Данные результаты показывают перспективность дальнейшей разработки аддитивных методов микроволнового послойного спекания для создания керамических изделий.
Список литературы
Zocca A., Colombo P., Gomes C.M., Günster J. Additive Manufacturing of Ceramics: Issues, Potentialities, and Opportunities // J. Am. Ceram. Soc. 2015. V. 98. P. 1983–2001.
Gao W., Zhang Y., Ramanujan D. et al. The Status, Challenges, and Future of Additive Manufacturing in Engineering // Comput. Des. 2015. V. 69. P. 65–89.
Travitzky N., Bonet A., Dermeik B. et al. Additive Manufacturing of Ceramic-Based Materials // Adv. Eng. Mater. 2014. V. 16. P. 729–754.
Nguyen A.K., Goering P.L., Skoog S.A., Narayan R.J. Physical Characterization and in vitro Evaluation of 3D Printed Hydroxyapatite, Tricalcium Phosphate, Zirconia, Alumina, and SiAlON Structures Made by Lithographic Ceramic Manufacturing // MRS Adv. 2020. V. 5. P. 2419–2428.
Bykov Y.V., Rybakov K.I., Semenov V.E. High-temperature Microwave Processing of Materials // J. Phys. D: Appl. Phys. 2001. V. 34. P. R55–R75.
Curto H., Thuault A., Jean F. et al. Coupling Additive Manufacturing and Microwave Sintering: A Fast Processing Route of Alumina Ceramics // J. Eur. Ceram. Soc. 2020. V. 40. P. 2548–2554.
Быков Ю.В., Еремеев А.Г., Глявин М.Ю. и др. Исследовательский гиротронный комплекс миллиметрового диапазона длин волн. I. Описание комплекса. // Изв. вузов. Радиофизика. 2018. Т. 61. С. 843–855.
Глявин М.Ю., Морозкин М.В., Цветков А.И. и др. Автоматизированный микроволновый комплекс на основе работающего в непрерывном режиме гиротрона с рабочей частотой 263 ГГц и выходной мощностью 1 кВт // Изв. вузов. Радиофизика. 2015. Т. 58. С. 709–719.
Bykov Y., Egorov S., Eremeev A. et al. On the Mechanism of Microwave Flash Sintering of Ceramics // Materials (Basel). 2016. V. 9. P. 684.
Быков Ю.В., Егоров С.В., Еремеев А.Г. и др. Сверхбыстрое спекание оксидных керамических материалов при микроволновом нагреве // Журн. техн. физики. 2018. Т. 88. С. 402.
Egorov S.V., Eremeev A.G., Kholoptsev V.V. et al. Rapid Microwave Sintering of Zinc Oxide-Based Varistor Ceramics // J. Eur. Ceram. Soc. 2021. V. 41. P. 6508–6515.
Bykov Y.V., Egorov S.V., Eremeev A.G. et al. Ultra-Rapid Microwave Sintering of Pure and Y2O3-doped MgAl2O4 // J. Am. Ceram. Soc. 2018. V. 102. № 2. P. 559–568.
Egorov S.V., Eremeev A.G., Kholoptsev V.V. et al. On the Correlation Between the Thermal Instability Onset and the Flash Sintering Event // Scr. Mater. 2020. V. 174. P. 68–71.
Bykov Y.V., Egorov S.V., Eremeev A.G. et al. Flash Microwave Sintering of Transparent Yb:(LaY)2O3 Ceramics // J. Am. Ceram. Soc. 2015. V. 98. P. 3518–3524.
Puzyrev I.S., Lipilin A.S., Ivanov V.V., Yatluk Y.G. Stabilization of Isopropanol Dispersions of Nanosized Powders of Yttrium Oxide-Stabilized Zirconium Dioxide // Colloid J. 2011. V. 73. P. 97–103.
Cesarano J., Aksay I.A., Bleier A. Stability of Aqueous alpha-Al2O3 Suspensions with Poly(methacrylic acid) Polyelectrolyte // J. Am. Ceram. Soc. 1988. V. 71. P. 250–255.
Hackley V.A. Colloidal Processing of Silicon Nitride with Poly(acrylic acid): I, Adsorption and Electrostatic Interactions // J. Am. Ceram. Soc. 2005. V. 80. P. 2315–2325.
Pina A., Nakache E., Feret B., Depraetere P. Copolymer Polyelectrolyte Adsorption onto Titanium Dioxide // Colloids Surf., A. 1999. V. 158. P. 375–384.
Kamiya H., Fukuda Y., Suzuki Y. et al. Effect of Polymer Dispersant Structure on Electrosteric Interaction and Dense Alumina Suspension Behavior // J. Am. Ceram. Soc. 2004. V. 82. P. 3407–3412.
Ahmed Y., Ewais E., El-Sheikh S. Effect of Dispersion Parameters on the Consolidation of Starch-Loaded Hydroxyapatite Slurry // Process Appl. Ceram. 2014. V. 8. P. 127–135.
Tripathi G., Basu B. A Porous Hydroxyapatite Scaffold for Bone Tissue Engineering: Physico-Mechanical and Biological Evaluations // Ceram. Int. 2012. V. 38. P. 341–349.
Knowles J. Characterisation of the Rheological Properties and Zeta Potential of a Range of Hydroxyapatite Powders // Biomaterials. 2000. V. 21. P. 1387–1392.
Gardini D., Galassi C., Lapasin R. Rheology of Hydroxyapatite Dispersions // J. Am. Ceram. Soc. 2005. V. 88. P. 271–276.
Дополнительные материалы отсутствуют.
Инструменты
Неорганические материалы