Неорганические материалы, 2022, T. 58, № 7, стр. 801-806
Электроимпульсное плазменное спекание керамики на основе Si2N2O
Л. С. Алексеева 1, *, П. В. Андреев 1, П. Д. Дрожилкин 1, М. С. Болдин 1, К. Е. Сметанина 1, А. А. Мурашов 1, К. О. Каразанов 1, Г. В. Щербак 1
1 Нижегородский государственный университет им. Н.И. Лобачевского
603022 Нижний Новгород, пр. Гагарина, 23, Россия
* E-mail: golovkina_lyudmila@mail.ru
Поступила в редакцию 29.12.2021
После доработки 05.04.2022
Принята к публикации 08.04.2022
- EDN: RKSVBP
- DOI: 10.31857/S0002337X22070028
Аннотация
Изготовлены порошковые смеси на основе нано-Si3N4 и оксидов иттрия и алюминия. Методом электроимпульсного плазменного спекания при давлении 80 МПа и скорости нагрева 50°C/мин получены образцы керамики с относительной плотностью 95–96%. Микроструктура образцов представляет собой зерна Si2N2O размером ~0.7 мкм c распределенной между ними аморфной оксидной фазой. Наибольшая твердость (13.3 ГПа) наблюдалась у образца с мольным соотношением оксидов Y2O3 и Al2O3 (2 : 1), полученного при температуре спекания 1770°C.
ВВЕДЕНИЕ
В последние годы популярность набирают керамические материалы на основе ковалентных кремниевых соединений в качестве термоустойчивых конструкционных материалов [1]. В частности, оксинитрид кремния (Si2N2O) и сиалоны (Si–Al–O–N) благодаря высокой стойкости к тепловому удару, жаропрочности, коррозионной стойкости, стойкости к окислению, износостойкости и низкому коэффициенту температурного расширения являются перспективными материалами для высокоответственных изделий, работающих при повышенных температурах [2–4].
Получение керамики из чистого оксинитрида кремния традиционным спеканием затруднено, так как в исходных порошках Si2N2O содержится много примесных фаз, таких как Si3N4, SiO2, остаточный кремний и т.д. [5]. В связи с этим в настоящее время предлагаются новые способы получения оксинитридных керамик [5, 6]. Известны способы получения плотной керамики из оксинитрида кремния методом горячего прессования порошковых смесей Si3N4 и SiO2 с различными добавками (Y2O3, Al2O3, MgO, Li2O и др.) [7–9].
В последние годы популярностью исследователей пользуется технология электроимпульсного (“искрового”) плазменного спекания (ЭИПС) [10], представляющая собой способ высокоскоростного горячего прессования. При ЭИПС спекание порошков, предварительно помещенных в графитовую пресс-форму, происходит в вакууме или в инертной среде в условиях приложения одноосного давления. Нагрев (до 750°С/мин) создается постоянным током, протекающим между пуансонами в импульсном режиме. Высокие скорости спекания обеспечивают незначительный рост зерен, что позволяет создавать ультрамелкозернистые керамики, для чего используют исходное сырье в виде нанопорошков [11].
Ранее методом ЭИПС из нанопорошковой смеси на основе нитрида кремния с добавкой Y2O3–Al2O3 нами была получена керамика Si2N2O [12]. Был сделан вывод, что аморфный нанопорошок (<15 нм) Si3N4 в процессе изготовления шихтовых смесей взаимодействует с атмосферой и адсорбирует на своей поверхности кислород. В процессе ЭИПС происходит взаимодействие наночастиц Si3N4 с кислородом, которое обеспечивает условия для образования и роста зерен оксинитрида кремния, а растворение Si3N4 при жидкофазном спекании в оксидной спекающей добавке могло привести к появлению твердого раствора замещения, изоструктурного Si2N2O, называемого O'-сиалон [13].
Цель настоящей работы – получение и изучение механизма ЭИПС керамики Si2N2O из смеси, синтезированной методом Печини из нанопорошка Si3N4 и нитратов иттрия и алюминия в качестве прекурсоров спекающих добавок состава Al2O3–Y2O3 в количестве не более 5 мас. % (в пересчете на оксидную фазу). Соотношение нитратов иттрия и алюминия было выбрано из расчета существующих стехиометрических фаз, характерных для системы Al2O3–Y2O3, чтобы проследить их возможное влияние на процесс спекания и фазовый состав.
ЭКСПЕРИМЕНТАЛЬНАЯ ЧАСТЬ
Объектами исследования являлись смеси на основе Si3N4 с добавками 5 мас. % оксидов иттрия и алюминия в различных стехиометрических соотношениях, соответствующих иттрий-алюминиевому перовскиту YAlO3, иттрий-алюминиевому оксиду в моноклинной модификации Y4Al2O9 и иттрий-алюминиевому гранату Y3Al5O12. В качестве исходного материала использовался порошок Si3N4 (производитель ABCR Gmbh, Германия) с размером частиц 15–30 нм и содержанием не менее 98.5 мас. % Si3N4.
Керамику получали методом ЭИПС на установке Dr. Sinter model-625 в вакууме. Порошки помещали в графитовую пресс-форму внутренним диаметром 10.8 мм и нагревали за счет пропускания миллисекундных импульсов электрического тока большой мощности (до 3 кА). ЭИПС проводили при давлении 80 МПа до окончания процесса усадки. Давление к образцу прикладывалось одновременно с началом нагрева. Скорость нагрева до 600°С составляла 100°С/мин, нагрев до температуры окончания усадки проводили со скоростью 50°С/мин. Изотермическая выдержка при температуре спекания не применялась. Температура в процессе спекания измерялась оптическим пирометром, сфокусированным на поверхности пресс-формы. Охлаждение образцов проводилось в свободном режиме, вместе с установкой. Для удаления с поверхности образца остатков графита их отжигали в печи ЭКПС-10 на воздухе при температуре 750°С (2 ч).
В процессе ЭИПС с помощью дилатометра установки Dr. Sinter model SPS-625 фиксировалась зависимость усадки порошков от температуры нагрева L(t), которая пересчитывалась в температурную зависимость уплотнения ρ/ρth(t) в соответствии с процедурой, описанной в работе [14].
Плотность полученных керамик (ρ) измеряли методом гидростатического взвешивания в дистиллированной воде на весах Sartorius CPA 225D. Теоретическая плотность оценивалась из соотношения Si2N2O : YxAlyOz = 95 : 5 мас. %. При расчете теоретической плотности (ρth) керамики плотность Si2N2O принималась равной 2.81, YAlO3 – 5.51, Y4Al2O9 – 4.41, Y3Al5O12 – 4.55 г/см3.
Рентгенофазовый анализ (РФА) образцов проводили на дифрактометре Shimadzu LabX XRD-7000 (излучение CuKα, λ = 1.54 Å). Размер областей когерентного рассеяния (ОКР) рассчитывали по методу Галдера–Вагнера [15]. Микроструктуру керамических образцов изучали с использованием растрового электронного микроскопа (РЭМ) JEOL JSM-6490.
Твердость по Виккерсу (HV) определяли с помощью микротвердомера Qness 60A+ при нагрузке 20 H. Минимальный коэффициент трещиностойкости (KIc) определяли методом Палмквиста на основе измерения максимальных длин трещин от углов отпечатка индентора. При расчете KIc величина модуля упругости принималась равной 240 ГПа.
РЕЗУЛЬТАТЫ И ОБСУЖДЕНИЕ
Для получения смесей составов 95 мас. % Si3N4 + + 5 мас. % (Al2O3 + Y2O3) к смеси растворов нитратов иттрия (Y(NO3)3 · 6H2O, “х. ч.”) и алюминия (Al(NO3)3 · 9H2O, “ч.”), взятых в стехиометрических соотношениях YAlO3 (серия 1), Y4Al2O9 (серия 2) и Y3Al5O12 (серия 3), добавляли раствор лимонной кислоты (C6H8O7 · H2O, “х. ч.”) и перемешивали при 80°C. Мольное соотношение лимонной кислоты к суммарному содержанию нитрат-ионов составляло 1 : 1. К полученной смеси добавляли нанопорошок Si3N4 в количестве 95 мас. % (в пересчете на состав Si3N4–Al2O3–Y2O3) и высушивали при постоянном перемешивании при температуре 120°C до состояния густого геля. Полученный гель отжигали при температуре 300°C в течение 1 ч.
Результаты РФА порошковой смеси показывают, что пики, соответствующие оксидной фазе и Si3N4, отсутствуют, что позволяет сделать вывод об их аморфном состоянии.
В процессе ЭИПС были получены образцы керамики серий 1, 2, 3 с плотностью 94.8% (2.73 г/см3), 95.5% (2.73 г/см3) и 96.4% (2.76 г/см3) соответственно. Образцы не имели видимых макродефектов.
Как видно из представленных на рис. 1 диаграмм ЭИПС “время (τ, c)–температура (t, °C)–приложенное давление (P, МПа)–давление вакуума (Vac, Па)”, при нагреве порошков наблюдается резкое снижение уровня вакуума, что свидетельствует о протекании химических реакций и диссоциации с поверхности образцов элементов, входящих в состав спекаемых керамик. Для образца серии 1 наблюдается резкое снижение уровня вакуума до величины, близкой к нулю в интервале температур 500–800°С (время процесса τ = 300–600 c), и затем незначительное снижение уровня вакуума в интервале температур 1100–1200°C (τ = = 1000–1080 c) (рис. 1а). Первый минимум связан с разложением промежуточных продуктов синтеза оксидной добавки. Аналогичный двухстадийный характер уменьшения уровня вакуума наблюдается при ЭИПС образцов серий 2 и 3, но температурные интервалы протекания реакций диссоциации смещены в область бóльших температур нагрева, а интенсивность снижения вакуума в области низкотемпературного отжига оказывается меньше, чем для образца серии 1.
Рис. 1.
Диаграммы зависимости температуры (t), давления пресса (P) и уровня вакуума (Vac) от времени процесса ЭИПС образцов керамики серий 1 (а), 2 (б) и 3 (в).
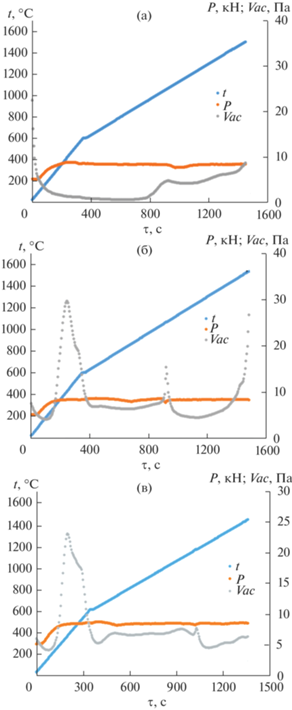
Анализ представленных на рис. 2 кривых уплотнения ρ/ρth(t) показывает, что кинетика спекания схожа для всех образцов. Зависимости ρ/ρth(t) имеют немонотонный характер с ярко выраженной стадией скачкообразной (“лавинообразной”) усадки при пониженных температурах нагрева. Стадия интенсивной усадки нанопорошков начинается при температурах ~1200, 1240 и 1350°С для образцов серий 1, 2 и 3, а завершается при температурах 1755, 1730 и 1610°С соответственно. Предельная величина уплотнения для всех образцов составляет 0.95–0.96, но достигается при различных температурах. Для образцов серий 1 и 2 температуры, при которых достигается максимальное уплотнение, составляют примерно 1740 и 1770°С соответственно. Керамика серии 3 достигает максимального уплотнения при температуре 1640°С. Таким образом, скорость уплотнения керамического образца серии 3 является самой высокой, а температура спекания – самой низкой.
По данным РФА, состав керамики представлен преимущественно кристаллической фазой Si2N2O (PDF № 01-075-5608) и фазой β-Si3N4 (PDF № 01-071-0623) (рис. 3). Содержание фазы β-Si3N4 по оценкам, выполненным методом корундовых чисел, не превышает 2% в образцах серий 1 и 3 и 5% в керамике серии 2. Пики фазы β-Si3N4 имеют небольшую интенсивность и уширены, что говорит о малом размере ОКР. Параметры элементарной ячейки фазы Si2N2O имеют равные в пределах погрешности значения около a = 8.87(1) Å, b = 5.49(1) Å, c = 4.85(1) Å для всех образцов, что соответствует Si2N2O по базе данных ICSD (№ 34 025) и заметно ниже характерных параметров для O'-сиалона, имеющего ту же кристаллическую модификацию.
По нашему мнению, очень быстрая усадка порошковой смеси на начальной стадии ЭИПС может быть связана с лавинообразной кристаллизацией оксинитрида кремния из наноструктурированного нитрида кремния с адсорбированным на поверхности частиц кислородом. Различие температур, при которых этот процесс запускается, вероятно, связано с составом спекающей оксидной добавки. Аналогичные различия характерны и для спекания Si3N4 [16].
Параметры элементарной ячейки фазы β-Si3N4 установить не удалось ввиду малости ее объемной доли и размеров ОКР, поэтому не исключено, что в ней содержатся примесные катионы Al3+ и Y3+. В этом случае, по нашему мнению, корректнее говорить о фазе β-сиалона, изоморфной β-Si3N4. Дифракционные пики, соответствующие оксидам, не выявлены, что позволяет говорить об их аморфном состоянии. Размеры ОКР для всех образцов составляют 0.71–0.73 мкм.
Микроструктура спеченных образцов состоит из темно-серых зерен Si2N2O размером менее 1 мкм (рис. 4), что коррелирует с оценкой ОКР. Между зернами Si2N2O располагаются светлые частицы оксидов размером менее 0.5 мкм. В микроструктуре наблюдается остаточная нано- и микропористость; средний размер пор не превышает 0.3 мкм. В качестве примера на рис. 4в единичные крупные поры указаны желтыми стрелками.
Микротвердость Hv образцов серий 1, 2, 3 составила 12.2 ± 0.7, 13.3 ± 0.5, 10.9 ± 0.6 ГПа соответственно. Минимальный коэффициент трещиностойкости KIc, рассчитанный по длине максимальной радиальной трещины, для образцов данных серий составил 1.5 ± 0.1, 1.6 ± 0.2 и 1.2 ± ± 0.1 МПа м1/2 соответственно. Низкие значения коэффициента трещиностойкости обусловлены, очевидно, наличием нано- и микропор в структуре, которые могут являться областями зарождения микротрещин при нагружении.
Для анализа механизмов высокоскоростного спекания использовали две взаимно дополняющих друг друга модели: модель Янга–Катлера [17] и модель диффузионного растворения пор вблизи границ зерен в мелкозернистых материалах [14].
Модель Янга–Катлера описывает начальную стадию неизотермического спекания сферических частиц в условиях одновременного протекания процессов объемной и зернограничной диффузии, а также вязкого течения материала [17]. В соответствии с [17], угол наклона зависимости усадки от температуры в координатах ln(T∂ε/∂T)–Tm/T соответствует эффективной энергии активации спекания mQs1, где m – коэффициент, зависящий от доминирующего механизма спекания (m = 1/3 для случая зернограничной диффузии, m = 1/2 для объемной диффузии, m = 1 для вязкого течения), Tm – температура плавления (Tm = 1970 K).
Зависимости ln(T∂ε/∂T)–Tm/T на стадии интенсивной усадки для исследуемых образцов имеют традиционный двухстадийный характер (рис. 5а). Анализ полученных результатов показывает, что эффективная энергия активации ЭИПС (mQs1) на стадии интенсивной усадки составляет ~(7.7–9.5)kTm. В области высоких температур спекания угол наклона зависимости ln(T∂ε/∂T)–Tm/T становится отрицательным (рис. 5а) и для анализа кривых уплотнения корректнее использовать модель диффузионного растворения пор [17].
Рис. 5.
Иллюстрация к расчету энергии активации ЭИПС в рамках модели Янга–Катлера (а), в рамках модели диффузного растворения пор (б).
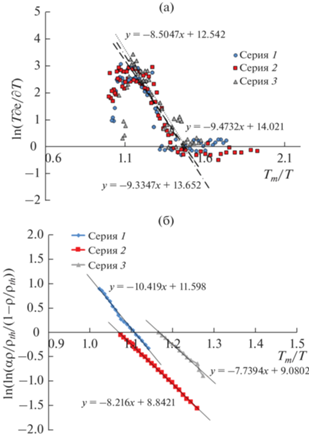
В рамках модели диффузионного растворения пор энергия активации спекания Qs2 может быть определена по углу наклона зависимости ln(ln(αρ/ρth/(1–ρ/ρth))–Tm/T, где α = 0.5–0.62 – коэффициент уплотнения прессовки, пропорциональный насыпной плотности порошков (рис. 5б). Проведенный анализ показал, что энергия активации Qs2 для образцов серий 1–3 составляет ~(7.7–10.4)kTm.
Таким образом, значения эффективной энергии активации mQs1, рассчитанной в рамках модели Янга–Катлера [17], и значения энергии активации Qs2, рассчитанной в рамках модели диффузионного растворения пор, оказываются близки друг к другу. Это означает, что величина коэффициента m близка к единице (m ~ 1), что соответствует случаю вязкого течения материала в условиях горячего прессования.
ЗАКЛЮЧЕНИЕ
Методом Печини получены порошковые смеси на основе нанесенных на поверхность частиц Si3N4 оксидов иттрия и алюминия в роли спекающей добавки состава Al2O3–Y2O3 в количестве 5 мас. % (в пересчете на оксидную фазу). Соотношение ионов Y3+ и Al3+ выбрано из расчета существующих стехиометрических фаз иттрий-алюминиевого перовскита YAlO3, иттрий-алюминиевого оксида в моноклинной модификации Y4Al2O9 и иттрий-алюминиевоого граната Y3Al5O12.
Методом ЭИПС получены образцы керамики, состоящие из кристаллических частиц Si2N2O размером около 0.7 мкм. Наибольшая твердость (13.3 ГПа) наблюдалась у образца с добавкой оксидов иттрия и алюминия в мольном соотношении Y3+ : Al3+ = 2 : 1, спеченного при температуре 1770°C.
С использованием модели Янга–Катлера и модели диффузионного растворения пор показано, что основным механизмом уплотнения порошков на стадии интенсивной усадки является процесс вязкого течения материала в условиях горячего прессования.
Список литературы
Wang Y., Hou Q., Tian L. et al. Effect of in situ Synthesis of Si2N2O on Microstructure and the Mechanical Properties of Fused Quartz Ceramic // Ceram. Int. 2020. V. 46. № 7. P. 8725–8729. https://doi.org/10.1016/j.ceramint.2019.12.111
Riley F.L. Silicon Nitride and Related Materials // J. Am. Ceram. Soc. 2000. V. 83. P. 245–265. https://doi.org/10.1111/J.1151-2916.2000.TB01182.X
Ohashi M., Kanzaki S., Tabata H. Processing, Mechanical Properties, and Oxidation Behavior of Silicon Oxynitride Ceramics // J. Am. Ceram. Soc. 1991. V. 74. P. 109–114. https://doi.org/10.1016/0272-8842(95)00136-0
Radwan M., Kashiwagi T., Miyamoto Y. New Synthesis Route for Si2N2O Ceramics Based on Desert Sand // J. Eur. Ceram. Soc. 2003. V. 23. P. 2337–2341. https://doi.org/10.1016/S0955-2219(03)00040-2
Inagaki Y., Ohji T., Kanzaki S., Shigegaki Y. Fracture Energy of an Aligned Porous Silicon Nitride // J. Am. Ceram. Soc. 2000. V. 83. P. 1807–1809. https://doi.org/10.1111/J.1151-2916.2000.TB01468.X
Kawai C., Yamakawa A. Effect of Porosity and Microstructure on the Strength of Si3N4: Designed Microstructure for High Strength, High Thermal Shock Resistance, and Facile Machining // J. Am. Ceram. Soc. 1997. V. 80. P. 2705–2708. https://doi.org/10.1111/j.1151-2916.1997.tb03179.x
Billy M., Boch P., Dumazeau C. et al. Preparation and Properties of New Silicon Oxynitride Based Ceramics // Ceram. Int. 1981. V. 7. № 1. P. 13–18. https://doi.org/10.1016/0272-8842(81)90033-X
Fruhstorfer J., Kerber F., Weigelt C. et al. Activated Reaction Synthesis of Silicon Oxynitride from Silica and Silicon Nitride // Ceram. Int. 2018. V. 44. № 7. P. 8467–8475. https://doi.org/10.1016/j.ceramint.2018.02.044
Tong Q., Wang J., Li Z., Zhou Y. Low-Temperature Synthesis/Densification and Properties of Si2N2O Prepared with Li2O Additive // J. Eur. Ceram. Soc. 2007. V. 27. № 16. P. 4767–4772. https://doi.org/10.1016/j.jeurceramsoc.2007.04.004
Tokita M. Pulse Electric Current Synthesis and Processing of Materials // Development of Advanced Spark Plasma Sintering (SPS) Systems and Its Industrial Applications / Eds. Munir Z.A. et al. 2006. New Jersey: Wiley. P. 314.
Nishimura T., Xu X., Kimoto K., Hirosaki N., Tanaka H. Fabrication of Silicon Nitride Nanoceramics – Powder Preparation and Sintering: A Review // Sci. Technol. Adv. Mater. 2007. V. 8. P. 635–643. https://doi.org/10.1016/j.stam.2007.08.006
Andreev P., Rostokina E., Alekseeva L. et al. Spark Plasma Sintering of Si3N4-YAG Nanocomposite // IOP Conf. Ser.: Mater. Sci. Eng. 2021. V. 1014. P. 1–4. https://doi.org/10.1088/1757-899X/1014/1/012002
Trigg M.B., Jack K.H. The fabrication of O'-Sialon Ceramics by Pressureless Sintering // J. Mater. Sci. 1988. V. 23. P. 481–487. https://doi.org/10.1007/bf01174673
Чувильдеев В.Н., Болдин М.С., Дятлова Я.Г. и др. Сравнительное исследование горячего прессования и высокоскоростного электроимпульсного плазменного спекания порошков Al2O3/ZrO2/Ti(C,N) // Журн. неорган. химии. 2015. Т. 60. № 8. С. 1088–1094.
Halder N.C., Wagner C.N.J. Separation of Particle Size and Lattice Strain in Integral Breadth Measurements // Acta Crystallogr. 1966. V. 20. P. 312–313. https://doi.org/10.1107/S0365110X66000628
Petzow G., Herrmann M. Silicon Nitride Ceramics // High Performance Non-Oxide Ceramics II. Structure and Bonding / Ed. Jansen M. V. 102. Berlin: Springer, 2002. https://doi.org/10.1007/3-540-45623-6_2
Young W.S., Cutler I.B. Initial Sintering with Constant Rates of Heating // J. Am. Ceram. Soc. 1970. V. 53. № 12. P. 659–663. https://doi.org/10.1111/j.1151-2916.1970.tb12036.x
Дополнительные материалы отсутствуют.
Инструменты
Неорганические материалы