Неорганические материалы, 2022, T. 58, № 7, стр. 733-741
Синтез нитридов ниобия и тантала азотированием порошков в процессе восстановления их оксидных соединений кальцием
В. М. Орлов 1, *, Р. Н. Осауленко 2, В. Я. Кузнецов 1, Д. В. Лобов 2
1 Институт химии и технологии редких элементов и минерального сырья им. И.В. Тананаева – обособленное подразделение Федерального исследовательского центра “Кольский научный центр Российской академии наук”
184209 Мурманская обл., Апатиты, Академгородок, 26а, Россия
2 Петрозаводский государственный университет
185910 Петрозаводск, пр. Ленина, 33, Республика Карелия, Россия
* E-mail: v.orlov@ksc.ru
Поступила в редакцию 17.01.2022
После доработки 15.03.2022
Принята к публикации 17.03.2022
- EDN: SCLSQT
- DOI: 10.31857/S0002337X22060070
Аннотация
Исследованы характеристики порошков, полученных азотированием продуктов восстановления Та2O5, Nb2O5, Mg4Та2O9 и Mg4Nb2O9 парами кальция. Процесс вели в две стадии: 1 – восстановление оксидных соединений при 750, 800, 850 и 900°С в течение 1–6 ч; 2 – выдержка продуктов восстановления в атмосфере азота при тех же температурах в течение 1–5 ч. При использовании в качестве прекурсора Та2O5 получены продукты, содержащие помимо тантала нитриды θ-TaN и Ta2N. Синтез нитридов тантала из продуктов восстановления Mg4Та2O9 затруднен. При использовании в качестве прекурсора Nb2О5 продукты помимо ниобия содержат нитриды NbN и Nb2N с гексагональными плотноупакованными решетками. При азотировании продуктов восстановления Mg4Nb2O9 содержание нитридов в 6–10 раз меньше, чем при восстановлении и азотировании пентаоксида ниобия, что объясняется особенностями пористой структуры порошков. При повышении температуры восстановления с 750 до 850°С удельная поверхность азотированных порошков уменьшилась с 26.2 до 11.6–14.5 м2/г. Порошки характеризуются мезопористой структурой.
ВВЕДЕНИЕ
Нитриды ниобия и тантала благодаря специфическим свойствам нашли применение в различных областях техники [1, 2]. В системе ниобий-азот имеются α-фаза, представляющая собой твердый раствор азота в ниобии, гексагональная β-фаза с широкой областью гомогенности (от NbN0.4 до NbN0.5), тетрагональная γ-фаза с более узкой областью гомогенности (NbN0.75–NbN0.79), кубическая δ-фаза (NbN0.88–NbN1.0) и гексагональная ε-фаза (NbN1.0–NbN1.06) [3, 4]. При взаимодействии тантала с азотом образуются твердый раствор азота в тантале – β-фаза, кубическая решетка которой несколько отличается от решетки чистого металла, гексагональные фазы: γ (ТаN0.4–ТаN0.5), δ (ТаN0.8–ТаN0.9), ε и θ (ТаN), а также нитрид состава Та3N5 с ромбической решеткой [4]. Имеет место и высокотемпературная кубическая модификация нитрида ТаN [5].
Существует несколько способов получения нитридов ниобия и тантала, отличающихся используемыми прекурсорами и температурными режимами. Синтез нитридов с большой удельной поверхностью, применяемых, в частности, в качестве катализаторов различных реакций, осуществляют обычно аммонолизом порошков пентаоксидов ниобия [3, 6–8] и тантала [9–13] в токе NH3 при высокой температуре. В работе [14] предложено получать нитрид тантала взаимодействием смеси гептафторотанталата калия (K2TaF7) с азидом натрия (NaN3) в режиме горения. Температура процесса в зависимости от условий синтеза составляла 700–1200°С. Продукт реакции представлял смесь гексагональных фаз ε-TaN, TaN0.8 и Ta2N. При температуре 1200°С преобладала фаза TaN. Взаимодействием в атмосфере азота смеси K2TaF7 + (5 + k) NaN3 + kNH4F, где k – количество молей вещества (в режиме горения k = 4), при температуре 850–950°С был получен порошок кубического нитрида δ-TaN с удельной поверхностью 30.59 м2/г [15].
Различные варианты синтеза нитридов ниобия и тантала с использованием в качестве прекурсора пентахлоридов NbCl5 и TaCl5 рассматриваются в работах [16–18]. Нитриды ниобия состава NbNx (x = 1.64–1.33) получали аммонолизом NbCl5 в хлороформе при комнатной температуре с последующей термообработкой при 600°С [16]. Нанокристаллические NbN и ТаN со средним размером частиц 28 нм синтезировали взаимодействием пентахлоридов с азидом натрия при температуре 300°С и аутогенном давлении [17]. Нитриды тантала различного фазового состава и морфологии с удельной поверхностью 9.87–11.64 м2/г получали восстановлением TaCl5 натрием при низкой температуре с последующей термообработкой в высоком вакууме [18].
Существует несколько подходов к получению нитридов ниобия и тантала с использованием в качестве прекурсора порошков этих металлов. Кубический нитрид δ-NbNх (х = 0.87–1.015) был синтезирован азотированием в режиме горения. Значение х определялось давлением азота в реакторе, которое изменяли в интервале 48–230 МПа [19]. Возможен синтез нитридов в процессе измельчения порошков ниобия и тантала в атмосфере азота [20–24]. Однако традиционным способом следует считать азотирование при нагреве компактного металла или его порошка в атмосфере азота [3, 25–27].
В работе [25] осуществляли азотирование порошков ниобия и тантала со средним размером частиц от 2 до 7 мкм в токе азота. Оптимальный режим получения Nb2N – выдержка 30–60 мин при температуре 900°С, NbN – выдержка 60–120 мин при 1200°С. Заметная диффузия азота в тантал при выдержке 10–15 мин начинается только с температуры 700°С. Оптимальный режим получения Ta2N – температура 800–900°С, выдержка 60–120 мин. Для получения TaN необходимы нагрев до 1200°С и выдержка в течение 60 мин. Наблюдавшееся незначительное отклонение параметров кристаллической решетки нитридов, полученных азотированием натриетермического порошка ниобия, от литературных данных объясняется присутствием небольших количеств кислорода [26]. Взаимодействие компактного ниобия с азотом при давлении 150 кПа в интервале 1100–1900°С исследовали в работе [27]. Авторы установили, что образующаяся фаза δ-NbN при охлаждении превращается в γ-NbN и ε-NbN. Скорость роста толщины слоя нитрида определяется в основном диффузией азота через нитриды. Следовательно, уменьшение размеров частиц порошка металла позволит значительно ускорить процесс образования нитридов при взаимодействии с азотом. В этом плане большой интерес представляет использование в качестве прекурсора наноразмерных порошков ниобия и тантала, получаемых металлотермическим восстановлением их оксидных соединений [28, 29]. К сожалению, на поверхности металлических ниобия и тантала всегда присутствует слой естественного оксида толщиной около 2 нм [30, 31].
После отмывки металла от побочных продуктов реакции содержание кислорода в порошках с удельной поверхностью 50 м2/г составляет около 15 мас. %. Азотирование мезопористых порошков ниобия и тантала с большой удельной поверхностью в токе аммиака может быть осуществлено уже при температуре 700–800°С [32, 33]. При этом в случае аммонолиза порошка тантала вплоть до температуры 870°С получали только оксинитрид TaON, а удельная поверхность порошка снижалась с 56 до 18 м2/г [32]. Еще более значительное сокращение поверхности наблюдалось при аммонолизе порошка ниобия с удельной поверхностью 123 м2/г, которая уменьшалась в 6 раз [33].
Цель работы – исследование возможности получения порошков нитридов ниобия и тантала с большой удельной поверхностью непосредственно в процессе восстановления, когда на образовавшихся частичках металла отсутствует поверхностный оксид, а коагуляция частиц металла затруднена присутствующим оксидом кальция. Порошки получали при азотировании непосредственно продуктов восстановления пентаоксидов ниобия и тантала, а также ниобата и танталата магния парами кальция.
ЭКСПЕРИМЕНТАЛЬНАЯ ЧАСТЬ
В качестве исходных материалов использовали пентаоксиды тантала и ниобия производства АО “Соликамский магниевый завод”, а также танталат Mg4Та2O9 и ниобат магния Mg4Nb2O9, синтезированные спеканием стехиометрической смеси исходных оксидов при температуре 1300°С в течение 2 ч. В этих же условиях термообрабатывали пентаоксиды для уменьшения их удельной поверхности. Продукты после термообработки измельчали в порошок крупностью менее 800 мкм. Процесс восстановления с последующим азотированием вели в реакторе, представляющем собой реторту из нержавеющей стали. Контейнер с кальцием помещали в нижней части реакционного стакана, выше располагали поддон с 4 контейнерами, в которые загружали по 10 г оксидных соединений. Стакан закрывали крышкой и устанавливали в реактор. Реактор герметизировали, вакуумировали и нагревали до требуемой температуры. Процесс осуществляли в 2 этапа [32]. Вначале вели восстановление при температуре 750–850°С в вакууме (10 Па) в течение 1–6 ч или при температуре 900°С и остаточном давлении аргона в реакторе 1 кПа. После завершения стадии восстановления реактор заполняли азотом до избыточного давления 30–100 кПа и осуществляли выдержку в течение 1–5 ч при заданной температуре, поддерживая избыточное давление азота. Азот высокой чистоты подавали в реактор непосредственно из баллона, без дополнительной очистки.
После охлаждения реактора до комнатной температуры продукты реакции взвешивали и определяли степень восстановления как разницу в массах полученных продуктов и прекурсора по отношению к теоретическому изменению массы по реакции. Следует отметить, что, если процесс восстановления парами кальция был недостаточно стабилен, продукты реакции вновь загружали в реактор и реакцию восстановления-азотирования повторяли. Отмывку порошка от побочных продуктов реакции осуществляли двукратной в течение 0.5 ч обработкой 18%-ным раствором азотной кислоты. Затем порошок промывали дистиллированной водой до нейтральной реакции раствора и сушили при температуре 85°С.
Фазовый состав продуктов реакции определяли на дифрактометре ДРФ-2 с CuKα-излучением и графитовым монохроматором. Идентификацию фаз осуществляли по базе дифрактометрических данных PDF-2 ICPDS-ICCD, 2002. Для уточнения параметров кристаллической решетки использовали автоматизированный рентгеновский дифрактометр ДРОН-4, метод Ритвельда и базу данных структур неорганических кристаллов ICSD, Карлсруе, 2013. На приборе Micromeritics TriStar II 3020 измеряли удельную поверхность адсорбционным статическим методом БЭТ и параметры пористости методом BJH. Содержание азота и кислорода определяли методом газоадсорбционной хроматографии в сочетании с импульсным нагревом на анализаторе К-671.
РЕЗУЛЬТАТЫ И ОБСУЖДЕНИЕ
В табл. 1 и 2 приведены удельная поверхность (S), содержания азота (СN), кислорода (СО) и фазовый состав порошков, полученных азотированием продуктов восстановления оксидных соединений ниобия и тантала в зависимости от температуры восстановления (tв), азотирования (tаз) и длительности выдержек на стадии восстановления (τв) и азотирования (τаз). Ориентировочное содержание фаз определено по соотношению высот соответствующих рефлексов на рентгенограммах. Анализ данных табл. 1 и 2 показывает, что содержание азота в продуктах восстановления-азотирования пентаоксидов коррелирует с величиной удельной поверхности полученных порошков (опыты 1–4, табл. 1 и 2) и температурой на стадии восстановления. С повышением температуры в реакторе скорость испарения кальция увеличивается. Это приводит к дополнительному росту локальной температуры в зоне реакции и, соответственно, уменьшению удельной поверхности порошка. Остаточное давление аргона в реакторе 1 кПа позволило значительно снизить скорость испарения кальция при температуре восстановления 900°С (опыты 5, табл. 1 и 2), что привело к увеличению удельной поверхности по сравнению с порошками, полученными при температуре 850°С в вакууме (опыты 3, 4, табл. 1 и 2). Аналогичная зависимость удельной поверхности порошков от скорости поступления паров магния в зону реакции наблюдалась нами ранее [28]. Содержание азота в продуктах, рассчитанное на основе фазового состава, согласуется с результатами газового анализа (СN). Несмотря на большую величину удельной поверхности порошков, полученных восстановлением Mg4Nb2O9 и Mg4Ta2O9, содержание азота в них не превышало 1.5 и 0.7% соответственно.
Таблица 1.
Характеристики азотированных продуктов, полученных после восстановления Nb2О5 и Mg4Nb2O9
Опыт | tв, °С | τв, ч | tаз, °С | τаз, ч | СN, % | СО, % | S, м2/г | Содержание фаз, % | ||
---|---|---|---|---|---|---|---|---|---|---|
NbN | Nb2N | Nb | ||||||||
Nb2О5 | ||||||||||
1 | 750 | 6 | 750 | 5 | 6.9 | 7.3 | 26.2 | 25 | 50 | 25 |
2 | 800 | 4 | 800 | 1 | 3.9 | 8.1 | 15.7 | 20 | 19 | 61 |
3 | 850 | 1 | 850 | 2 | 4.1 | 6.2 | 16.2 | 15 | 15 | 60** |
4 | 850 | 4 | 850 | 2 | 3.4 | 4.9 | 14.5 | 18 | 20 | 62 |
5 | 900* | 6 | 900 | 3 | 7.2 | 4.1 | 18.4 | 35 | 35 | 30 |
Mg4Nb2O9 | ||||||||||
6 | 750 | 6 | 750 | 5 | 1.5 | >12 | 50.6 | сл. | сл. | 99 |
7 | 800 | 4 | 800 | 1 | 1.0 | >12 | 52.8 | сл. | сл. | 99 |
8 | 850 | 1 | 850 | 2 | 0.6 | >12 | 60.1 | – | – | 100 |
9 | 850 | 4 | 850 | 2 | 0.52 | 9.9 | 56.4 | – | – | 100 |
10 | 900* | 6 | 900 | 3 | 1.0 | 9.6 | 51.4 | сл. | сл. | 99 |
Таблица 2.
Характеристики азотированных продуктов, полученных после восстановления Та2О5 и Mg4Ta2O9
Опыт | tв, °С | τв, ч | tаз, °С | τаз, ч | СN, % | СО, % | S, м2/г | Содержание фаз, % | ||
---|---|---|---|---|---|---|---|---|---|---|
TaN | Ta2N | Та | ||||||||
Та2О5 | ||||||||||
1 | 750 | 6 | 750 | 5 | 4.6 | 4.0 | 26.2 | 35 | 60 | 5 |
2 | 800 | 4 | 800 | 1 | 3.1 | 3.5 | 16.4 | 40 | 10 | 50 |
3 | 850 | 1 | 850 | 2 | 3.0 | 3.1 | 13.3 | 32 | 20 | 48 |
4 | 850 | 4 | 850 | 2 | 2.7 | 2.5 | 11.6 | 30 | 20 | 50 |
5 | 900* | 6 | 900 | 3 | 4.3 | 2.9 | 14.5 | 40 | 35 | 25 |
Mg4Ta2O9 | ||||||||||
6 | 750 | 6 | 750 | 5 | 0.7 | 5.7 | 36.6 | – | 4 | 86** |
7 | 800 | 4 | 800 | 1 | 0.6 | 7.9 | 29.8 | – | – | 100 |
8 | 850 | 1 | 850 | 2 | 0.43 | 5.7 | 33.7 | – | 5 | 85*** |
9 | 850 | 4 | 850 | 2 | 0.52 | 4.4 | 26.4 | сл. | – | 99 |
10 | 900* | 6 | 900 | 3 | 0.5 | 3.2 | 17.3 | сл. | сл. | 99 |
На рис. 1 представлены дифрактограммы продуктов, полученных азотированием восстановленных оксидных соединений Nb2O5 и Mg4Nb2O9 при 750 и 900°С (образцы 1, 5 и 6, 10, табл. 1). Уточненный методом Ритвельда фазовый состав и параметры кристаллической структуры этих образцов приведены в табл. 3. Аналогичные данные для образцов, полученных азотированием продуктов восстановления оксидных соединений тантала, приведены на рис. 2 (образцы 1, 5 и 6, 10, табл. 2) и в табл. 4. По уточненным данным, азотированные продукты восстановления пентаоксида ниобия представлены гексагональными фазами: ε-NbN (ICSD № 76384, пр. гр. P63/mmc) и β-Nb2N (ICSD № 31165, пр. гр. P63/mmc). Азотированные продукты восстановления пентаоксида тантала представлены фазами: θ-TaN (ICSD № 76455, пр. гр. P$\bar {6}$m2) и Ta2N (ICSD № 76015, пр. гр. P$\bar {3}$m1). Фаза TaN может иметь разные кристаллические модификации: θ-TaN (ICSD № 76455) и δ‑TaN (ICSD № 76016). Обе имеют группу симметрии P$\bar {6}$m2. При уточнении структуры методом Ритвельда установлено, что лучший вариант реализуется для θ-TaN. В этом случае фактор недостоверности Rwp(%) = 10.25, тогда как в варианте с δ-TaN он не опускается ниже 13.21. Присутствие гидрида тантала объясняется взаимодействием металлического тантала с выделяющимся в процессе кислотной обработки водородом.
Таблица 3.
Фазовый состав и параметры решетки продуктов восстановления-азотирования Nb2О5 и Mg4Nb2O9
Фаза | № ICSD | Пр. гр. | a, Å | c, Å | Содержание фазы, % |
||
---|---|---|---|---|---|---|---|
ICSD | эксп. | ICSD | эксп. | ||||
Образец 1, табл. 1 | |||||||
NbN | 76 384 | $P{{{\text{6}}}_{{\text{3}}}}{\text{/}}mmc$ | 2.968 | 2.9696(8) | 5.549 | 5.5365(9) | 25 |
Nb2N | 31 165 | $P{{{\text{6}}}_{{\text{3}}}}{\text{/}}mmc$ | 3.064 | 3.0530(0) | 4.971 | 4.9767(8) | 59 |
Nb | 645 059 | $Im\bar {3}m$ | 3.3063 | 3.3034(4) | c = a | 16 | |
Образец 6, табл. 1 | |||||||
Nb* | 645 059 | $Im\bar {3}m$ | 3.3063 | 3.3010(9) | c = a | ∼100 | |
Образец 5, табл. 1 | |||||||
NbN | 76 384 | $P{{{\text{6}}}_{{\text{3}}}}{\text{/}}mmc$ | 2.968 | 2.96794 | 5.549 | 5.5459(2) | 35 |
Nb2N | 31 165 | $P{{{\text{6}}}_{{\text{3}}}}{\text{/}}mmc$ | 3.064 | 3.0524(6) | 4.971 | 4.9853(2) | 39 |
Nb | 645 059 | $Im\bar {3}m$ | 3.3063 | 3.3018(1) | c = a | 26 | |
Образец 10, табл. 1 | |||||||
NbN | 76 384 | $P{{{\text{6}}}_{{\text{3}}}}{\text{/}}mmc$ | 2.968 | 2.9677(7) | 5.549 | 5.54587 | 2 |
Nb2N | 31 165 | $P{{{\text{6}}}_{{\text{3}}}}{\text{/}}mmc$ | 3.064 | 3.0526(6) | 4.971 | 4.9873(5) | 10 |
Nb | 645 059 | $Im\bar {3}m$ | 3.3063 | 3.3004(7) | c = a | 88 |
Таблица 4.
Фазовый состав и параметры решетки продуктов восстановления-азотирования Ta2О5 и Mg4Ta2O9
Фаза | № ICSD | Пр. гр. | a {b}, Å | c, Å | Содержание фазы, % |
||
---|---|---|---|---|---|---|---|
ICSD | эксп. | ICSD | эксп. | ||||
Образец 1, табл. 2 | |||||||
θ-TaN | 76 455 | $P{{\bar {6}}}m2$ | 2.931 | 2.9325(8) | 2.879 | 2.8750(1) | 24 |
Ta2N | 76 015 | $P{{\bar {3}}}m1$ | 3.0476 | 3.0466(1) | 4.9187 | 4.9294(6) | 72 |
Ta2H | 41 774 | С222 | 4.738 {3.398} | 4.7855(3) {3.3727(2)} | 4.763 | 4.6961(4) | 2 |
Ta | 167 903 | $Im\bar {3}m$ | 3.24842(8) | 3.3139(5) | c = a | 2 | |
Образец 6, табл. 2 | |||||||
Ta2H | 41 774 | С222 | 4.738 {3.398} | 4.7786(2) {3.3768(1)} | 4.763 | 4.6912(3) | 10 |
Ta | 167 903 | $Im\bar {3}m$ | 3.24842(8) | 3.3066(5) | c = a | 74 | |
Mg4Ta2O9 | 65 301 | $P{{\bar {3}}}С1$ | 5.1654(1) | 5.1579(2) | 14.0463(6) | 14.0331(3) | 16 |
Образец 5, табл. 2 | |||||||
θ-TaN | 76 455 | $P{{\bar {6}}}m2$ | 2.931 | 2.9322(3) | 2.879 | 2.8766(2) | 26 |
Ta2N | 76 015 | $P{{\bar {3}}}m1$ | 3.0476 | 3.0471(6) | 4.9187 | 4.9263(4) | 57 |
Ta2H | 41 774 | С222 | 4.738 {3.398} | 4.7663(1) {3.3711(2)} | 4.763 | 4.7047(6) | 4 |
Ta | 167 903 | $Im\bar {3}m$ | 3.24842(8) | 3.3078(4) | c = a | 13 | |
Образец 10, табл. 2 | |||||||
β-Ta2N | 1456 | $P{{\bar {3}}}1m$ | 5.285(5) | 5.28178 | 4.919(3) | 4.9162(2) | 4 |
Ta2H | 41 774 | С222 | 4.738 {3.398} | 4.7974(1) {3.3725(5)} | 4.763 | 4.7065(1) | 13 |
Ta | 167 903 | $Im\bar {3}m$ | 3.24842(8) | 3.3065(2) | c = a | 83 |
Обращает на себя внимание отсутствие в азотированных продуктах фазы ε-ТаN и кубической модификации NbN, которые наблюдались в азотированных продуктах магниетермического восстановления [34]. Пиков, соответствующих этим фазам, на рентгенограммах нет. С другой стороны, наблюдается некоторое количество нитридов NbN и Nb2N в азотированных продуктах восстановления ниобата магния, которые отсутствовали в азотированных продуктах магниетермического восстановления [34]. В случае азотирования продукта восстановления танталата магния при 900°С также образовалось небольшое количество фазы β‑Ta2N, имеющей пр. гр. P$\bar {3}$1m и ромбоэдрическую сингонию. Отличие этой модификаций нитрида в том, что при практически одинаковом с Ta2N параметре c параметры a и b увеличены в 1.7 раза. На одну элементарную ячейку β-Ta2N приходится 9 атомов, тогда как в Ta2N их число 3. Как следствие, объем элементарной ячейки β-Ta2N практически в 3 раза больше и составляет 119 Å3. Периоды кристаллической решетки для одинаковых модификаций полученных нитридов практически не зависят от температуры процесса и находятся в хорошем согласии с данными базы ICSD. Рассчитанные по формуле Шеррера размеры кристаллитов фаз приведены в табл. 5. Размер металлических фаз практически не зависит от температуры реакции. Что касается нитридных фаз, то с ростом температуры наблюдается увеличение размеров кристаллитов.
Таблица 5.
Размеры кристаллитов фаз в порошках, полученных азотированием при 750 и 900°С
Прекурсор | tаз, °С | Размеры кристаллитов, Å | |||||
---|---|---|---|---|---|---|---|
Ta | Ta2N | TaN | Nb | Nb2N | NbN | ||
Та2О5 | 750 | 258 | 100 | 137 | – | – | – |
900 | 257 | 124 | 168 | – | – | – | |
Mg4Ta2O9 | 750 | 250 | – | – | – | – | – |
900 | 321 | 174 | – | – | – | – | |
Nb2О5 | 750 | – | – | – | 345 | 200 | 178 |
900 | – | – | – | 394 | 277 | 208 | |
Mg4Nb2O9 | 750 | – | – | – | 362 | – | – |
900 | – | – | – | 367 | 278 | 205 |
Известно, что частица оксида тантала после восстановления парами магния характеризуется полосчатой структурой, представленной перемежающимися пластинчатыми частицами оксида магния и металлического тантала. Между ними имеется свободное пространство (зазор), размеры которого позволяют атомам магния или кальция проникать вглубь частицы к фронту реакции [35]. Размеры зазора между частицами образовавшегося оксида восстановителя и тантала зависят от толщины пластинок оксида восстановителя. Чем они тоньше, тем меньше зазор. После выщелачивания оксида магния или кальция частица металла характеризуется губчатой мезопористой структурой, и по размерам пор можно косвенно судить о размерах зазоров между частицами оксида и металла. Диаметр молекулы азота (3.18 Å) значительно больше диаметров атомов Mg и Са (1.6 и 1.97 Å соответственно) [36]. Поэтому для проникновения азота к поверхности частичек тантала необходим зазор больших размеров. Это объясняет неполное азотирование продуктов восстановления.
Форма кривых сорбции (рис. 3) полученных продуктов азотирования соответствует IV типу по классификации IUPAC, что свидетельствует о сохранении мезопористой структуры. Представляет интерес сравнение пористой структуры порошков, полученных в настоящей работе и при азотировании продуктов магниетермического восстановления [34]. Удельная поверхность порошков нитридов при использовании в качестве прекурсора пентаоксидов ниобия и тантала находится на одном уровне. При этом средний размер пор кальциетермических продуктов меньше на 13 и 21% соответственно. С другой стороны, удельная поверхность порошков, полученных в кальциетермическом процессе с использованием в качестве прекурсора ниобата или танталата магния, меньше в 2–3 раза, а средний размер пор больше на 50 и 75% соответственно. Этими особенностями пористой структуры можно объяснить меньшее содержание азота в порошках, полученных азотированием продуктов кальциетермического восстановления пентаоксидов, и появление некоторого количества нитридов при использовании в качестве прекурсора танталата и ниобата магния. В первом случае уменьшение размера пор, образовавшихся после выщелачивания оксида кальция, приводит к уменьшению зазора между прослойками оксида и металла. Во втором, наоборот, происходит некоторое увеличение зазора, вероятно, в поверхностных слоях восстанавливаемой частицы.
Рис. 3.
Кривые адсорбции-десорбции азота порошками, полученными азотированием продуктов восстановления Та2О5 при 750 (а), 900°C (б).
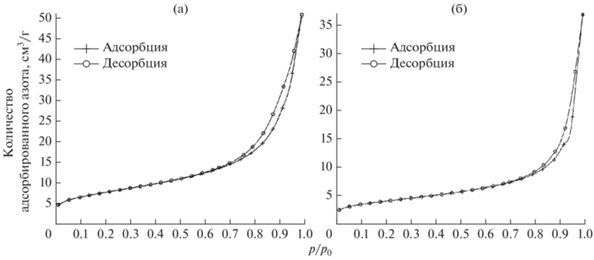
Полученные результаты подтверждают высказанное ранее предположение, что степень азотирования продуктов восстановления определяется величиной зазоров между пластинками оксида и металла в структуре восстановленной частицы оксида, а размер зазоров определяется толщиной пластинок оксида [34].
ЗАКЛЮЧЕНИЕ
Исследована возможность получения порошков нитридов ниобия и тантала с большой удельной поверхностью непосредственным азотированием продуктов кальциетермического восстановления оксидных соединений (Nb2О5 и Mg4Nb2O9; Та2О5 и Mg4Та2O9). Процесс вели при температуре 750–900°С в две стадии: 1 – восстановление парами кальция; 2 – выдержка продуктов реакции восстановления в атмосфере азота. В этих условиях при использовании в качестве прекурсора Nb2О5 образуются нитриды NbN с ГПУ-решеткой (ICSD № 76384, пр. гр. P63/mmc) и Nb2N (ICSD № 31165, пр. гр. P63/mmc). При использовании в качестве прекурсора Та2О5 фазовый состав представлен нитридами θ-TaN (ICSD № 76455, пр. гр. P$\bar {6}$m2) и Ta2N (ICSD № 76015, пр. гр. P$\bar {3}$m1). При азотировании продуктов восстановления ниобата Mg4Nb2O9 или танталата Mg4Та2O9 в полученных порошках наблюдалось незначительное количество нитридов NbN, Nb2N и β-Ta2N (ICSD № 1456, пр. гр. P$\bar {3}$1m).
Максимальная величина удельной поверхности порошков нитридов, полученных с использованием в качестве прекурсора пентаоксидов, находится на уровне 26 м2/г. Она определялась условиями стадии восстановления и уменьшалась с повышением температуры от 750 до 850°С, что объясняется увеличением скорости испарения кальция. Пропорционально уменьшалось и содержание азота в полученных продуктах.
Анализ пористой структуры порошков подтверждает высказанное ранее предположение, что степень азотирования продуктов восстановления определяется величиной зазоров между пластинками оксида восстановителя и металла в структуре восстановленной частицы оксида, а размер зазоров определяется толщиной пластинок оксида восстановителя [34].
Список литературы
Тот Л. Карбиды и нитриды переходных металлов: пер. с англ.; под ред. Гельда П.В. М.: Мир, 1974. 296 с.
Ningthoujam R.S., Gajbhiye N.S. Synthesis, Electron Transport Properties of Transition Metal Nitrides and Applications // Prog. Mater. Sci. 2015. V. 70. P. 50–154. https://doi.org/10.1016/j.pmatsci.2014.11.004
Brauer G. Nitrides, Carbonitrides and Oxynitrides of Niobium // J. Less-Common Met. 1960. V. 2. № 2–4. P. 131–137.
Самсонов Г.В., Кулик О.П., Полищук В.С. Получение и методы анализа нитридов. Киев: Наук. Думка, 1978. 318 с.
Zhizhun Yu., Zaulichny Ya.V., Zhurakovskii E.A. Features of the Electronic Structure of Different Modifications of Tantalum Mononitrides // Powder Metall. Met. Ceram. 1998. V. 37. № 7–8. P. 425–431. https://doi.org/10.1007/BF02676030
Guidotti R.A., Kesterke D.G. The Use of Nitride Intermediates in the Preparation of Metals. A Study of the Reduction of Nb2O5 with NH3 // Metallurg. Trans. 1973. V. 4. № 5. P. 1233–1237.
Kim H.S., Shin Ch.H., Bugli G. et al. Catalytic Activity of Niobium Oxynitride and Carbide I. Preparation, Characterization and Thermal Stability of Finely Divided Niobium Oxynitrides // Appl. Catal., A. 1994. V. 119. № 2. P. 223–240.
Wang P., Wang R., Lang J. et al. Porous Niobium Nitride as a Capacitive Anode Material for Advanced Li-Ion Hybrid Capacitor with Superior Cycling Stability // J. Mater. Chem. A. 2016. V. 4. № 25. P. 9760–9766. https://doi.org/10.1039/C6TA02971J
Brauer G., Weldlein J., Strahle J. Uber das Tantalnitrid Ta3N5 und das Tantaloxidnitrid TaON // Z. Anorg. Allg. Chem. 1966. B. 348. № 5–6. S. 298–309.
Swisher J.H., Read M.H. Thermodynamic Properties and Electrical Conductivity of Ta3N5 and TaON // Metall. Trans. 1972. V. 3. № 2. P. 489–494.
Zhang Q., Gao L. Ta3N5 Nanoparticles with Enhanced Photocatalytic Efficiency under Visible Light Irradiation // Langmuir. 2004. V. 20. № 22. P. 9821–9827. https://doi.org/10.1021/la048807i
Fu B., Gao L. Synthesis of Nanocrystalline Cubic Tantalum(iii) Nitride Powders by Nitridation–Thermal Decomposition // J. Am. Ceram. Soc. 2005. V. 88. № 12. P. 3519–3521. https://doi.org/10.1111/j.1551-2916.2005.00617.x
Henderson S.J., Hector A.L. Structural and Compositional Variations in Ta3N5 Produced by High-Temperature Ammonolysis of Tantalum Oxide // J. Solid State Chem. 2006. V. 179. № 18. P. 3518–3524. https://doi.org/10.1016/j.jssc.2006.07.021
Lee Y.-J., Kim D.-Y., Nersisyan H.H. et al. Rapid Solid-Phase Synthesis for Tantalum Nitride Nanoparticles and Coatings // Int. J. Refract. Met. Hard Mater. 2013. V. 41. P. 162–168. https://doi.org/10.1016/j.ijrmhm.2013.03.006
Lee Y.-J., Kim D.-Y., Lee K.-H. et al. Ammonium Fluoride-Activated Synthesis of Cubic δ-TaN Nanoparticles at Low Temperatures // Nanoscale Res.Lett. 2013. V. 8. № 1. Article.126. https://doi.org/10.1186/1556-276X-8-126
Choi D. Synthesis and Characterization of Nanostructured Niobium and Molybdenum Nitrides by a Two-Step Transition Metal Halide Approach // J. Am. Ceram. Soc. 2011. V. 94. № 8. P. 2371–2378. https://doi.org/10.1111/j.1551-2916.2011.04412.x
George P. P., Gedanken A., Makhlouf S. B.-D. et al. Synthesis and Characterization of Titanium Nitride, Niobium Nitride, and Tantalum Nitride Nanocrystals Via the RAPET (Reaction under Autogenic Pressure at Elevated Temperature) Technique // J. Nanopart. Res. 2009. V. 11. № 4. P. 995–1003. https://doi.org/10.1007/s11051-008-9550-5
Liu L., Huang K., Hou J., Zhu H. Structure Refinement for Tantalum Nitrides Nanocrystals with Various Morphologies // Mater. Res. Bull. 2012. V. 47. P. 1630–1635. https://doi.org/10.1016/j.materresbull.2012.03.050
Lindea A.V., Grachev V.V., Marin-Ayral R.-M. Self-Propagating High-Temperature Synthesis of Cubic Niobium Nitride Under High Pressures of Nitrogen // Chem. Eng. J. 2009. V. 155. № 1–2. P. 542–547. https://doi.org/10.1016/j.cej.2009.08.014
Sherif El-Es. M., Sumiyama K., Aoki K., Masumoto T. Mechanism of Solid-Gas Reaction for Formation of Metastable Niobium-Nitride Alloy Powders by Reactive Ball Milling // J. Mater. Res. 1994. V. 9. № 11. P. 2891–2898. https://doi.org/10.1557/JMR.1994.2891
Qin Y., Liu L., Chen L. Characterization of Nanocrystalline Tantalum Nitride Formed by Solid–Gas Reaction During Mechanical Alloying // J. Alloys Compd. 1998. V.269. № 1–2. P. 238–240. https://doi.org/10.1016/S0925-8388(98)00136-4
Liu L., Lu L., Chen L., Qin Y., Zhang L.D. Solid-Gas Reactions Driven by Mechanical Alloying of Niobium and Tantalum in Nitrogen // Metall. Trans. A. 1999. V. 30. № 4. P. 1097–1100. https://doi.org/10.1007/s11661-999-0161-2
Linde A.V., Marin-Ayral R.-M., Granier D. et al. Synthesis of Cubic Niobium Nitride by Reactive Diffusion under Nitrogen Pressure // Mater. Res. Bull. 2009. V. 44. № 5. P. 1025–1030. https://doi.org/10.1016/j.materresbull.2008.11
Garcia-Mendoza T., Martinez-Garciab A., Becerril-Juarezd I.G. et al. Mechanosynthesis of Metastable Cubic δ-Ta1 − xN // Ceram. Int. 2020. V. 46. № 14. P. 23049–23058. https://doi.org/10.1016/j.ceramint.2020.06.082
Верхоглядова Т.С., Дубовик Г.Д., Самсонов Г.В. Азотирование порошков переходных металлов // Порошковая металлургия. 1961. № 4. С. 9–20.
Самсонов Г.В., Верхоглядова Т.С. Азотирование порошкообраз-ного ниобия и некоторые свойства образующихся фаз //Журн. неорган. химии. 1961. Т. 6. Вып. 12. С. 2732–2736.
Musenich R., Fabbricatore P., Gemme et al. Growth of Niobium Nitrides by Nitrogen-Niobium Reaction at High Temperature // J. Alloys Compd. 1994. V. 209. № 1–2. P. 319–328. https://doi.org/10.1016/0925-8388(94)91120-7Get rights and content
Орлов В.М., Крыжанов М.В. Получение нанопорошков тантала магниетермическим восстановлением танталатов // Металлы. 2015. № 4. С. 93–97.
Орлов В.М., Крыжанов М.В., Калинников В.Т. Восстановление оксидных соединений ниобия парами магния // ДАН. 2015. Т. 465. № 2. С. 182–185.https://doi.org/10.7868/S0869565215320146
Розенберг Л.А., Штельман С.В. Состояние кислорода в танталовых порошках // Извест. АН СССР. Металлы. 1985. № 4. С. 163–164.
Delheusy M., Stierle A., Kasper N. et al. X-ray Investigation of Subsurface Interstitial Oxygen at Nb/oxide Interfaces // Appl. Phys. Lett. 2008. V. 92. Art. 101911. https://doi.org/10.1063/1.2889474
Орлов В.М., Кузнецов В.Я., Осауленко Р.Н. Аммонолиз магниетермических порошков тантала // Журн. неорган. химии. 2017. Т. 62. № 1. С. 38–43. https://doi.org/10.7868/S0044457X17010135
Орлов В.М., Осауленко Р.Н. Свойства нитридов, полученных аммонолизом магниетермических порошков ниобия // Неорган. материалы. 2018. Т. 54. № 7. С. 675–680. https://doi.org/10.7868/S0002337X18070047
Орлов В.М., Осауленко Р.Н., Кузнецов В.Я. Синтез нитридов в процессе магниетермического восстановления оксидных соединений тантала и ниобия // Неорган. материалы. 2019. Т. 55. № 11. С. 1183–1189. https://doi.org/10.1134/S0002337X19110101
Müller R., Bobeth M., Brumm H. et al. Kinetics of Nanoscale Structure Development during Mg-Vapour Reduction of Tantalum Oxide // Int. J. Mater. Res. 2007. V. 98. № 11. P. 1138–1145.
Перельман В.И. Краткий справочник химика. М.: Химия, 1964. 624 с.
Дополнительные материалы отсутствуют.
Инструменты
Неорганические материалы