Журнал неорганической химии, 2019, T. 64, № 7, стр. 774-781
Получение керамики на основе системы Y2O3–ZrO2–HfO2 для литейных форм
Ю. И. Фоломейкин 1, Ф. Н. Карачевцев 2, В. Л. Столярова 3, *
1 Центральный институт авиационного моторостроения им. П.И. Баранова
111116 Москва, ул. Авиамоторная, 2, Россия
2 Всероссийский научно-исследовательский институт авиационных материалов
105005 Москва, ул. Радио, Россия
3 Санкт-Петербургский государственный университет
199034 Санкт-Петербург, Университетская наб., 7/9, Россия
* E-mail: v.stolyarova@spbu.ru
Поступила в редакцию 14.12.2018
После доработки 20.12.2018
Принята к публикации 26.12.2018
Аннотация
Изучены потенциальные возможности системы Y2O3–ZrO2–HfO2 для синтеза керамики для литейных форм, содержащей 15 мол. % Y2O3 : 60 мол. % ZrO2 : 25 мол. % HfO2. Исследовано влияние технологических параметров на морфологию и основные свойства керамических форм, получаемых по удаляемым моделям на основе керамики указанного выше состава, а также рассмотрены основные рекомендации для дальнейшей разработки технологии их получения. Установлено, что высокоогнеупорную литейную форму, стабильную вплоть до температуры 2773 K, удается получить традиционным методом по удаляемым моделям, при этом твердофазное спекание керамики не исключает возможности одновременного совмещения с синтезом выбранного трехкомпонентного твердого раствора, содержащего 15 мол. % Y2O3 : 60 мол. % ZrO : 25 мол. % HfO2, выступающего в качестве высокотемпературной связки.
ВВЕДЕНИЕ
В последние годы значительно увеличилось число публикаций как в нашей стране, так и за рубежом, относящихся к использованию керамики на основе оксидов гафния и редкоземельных элементов:
− при выборе материалов керамических форм для литья лопаток газотурбинных двигателей (ГТД) нового поколения с использованием перспективных жаропрочных сплавов [1–5],
− для термобарьерных покрытий нового поколения [6–12],
− в различных областях атомной техники и технологии, в частности для длительного ядерно-безопасного хранения плутония, включая отходы [13, 14],
− в микроэлектронике в качестве альтернативного диэлектрика для замены диоксида кремния [15].
Установлено [16], что диоксид гафния в комбинации с оксидами редкоземельных элементов позволяет получать перспективную высокотемпературную керамику для новой техники, значительно превосходящую материалы на основе ZrO2 по температурам плавления (на ∼473 K) и термостабильности благодаря значительно повышенной (на ∼873–973 K) температуре моноклинно-тетрагонального превращения HfO2. Это превращение у HfO2 находится в такой области, где связанные с ним объемные изменения не вызывают такой опасности растрескивания изделий, как у диоксида циркония, так как возникающие напряжения легче релаксируют в более подвижном при высоких температурах материале. Следует также отметить, что само объемное изменение у HfO2 (3–4%) существенно меньше, чем у ZrO2 (7%). Однако информация о синтезе керамики, в частности для литейных форм на основе трехкомпонентных систем, содержащих оксид гафния, носит отрывочный и эпизодический характер.
В перспективных газотурбинных двигателях предполагается увеличение степени сжатия и рост температуры перед турбиной, что позволит повысить их экономичность [17]. Одно из направлений, позволяющих решить эту задачу, – использование для получения литых лопаток ГТД сплавов на основе тугоплавких металлов, таких как ниобий, титан, гафний и цирконий, с температурой плавления до 2373 K [4].
Известно, что наиболее исследованные NbSi-композиционные сплавы с направленно-ориентированной структурой по уровню кратковременной и длительной прочности при 1473 K более чем в 2 раза превосходят никелевые монокристаллические сплавы и сохраняют свойства при температурах до 1623 K [18, 19].
Для реализации процесса литья деталей из композиционных сплавов на основе тугоплавких металлов с интерметаллидным упрочнением на установках направленной кристаллизации необходимо использовать формы из керамики высшей огнеупорности. В настоящее время предельная рабочая температура общепринятых керамических форм на основе оксида алюминия не превышает 1873–1923 K, что является недостаточным [1].
Для получения качественных отливок деталей методом литья по выплавляемым моделям из сплавов на основе тугоплавких металлов наряду с высокой огнеупорностью материала керамических форм необходимо обеспечить низкую химическую активность и летучесть лицевого слоя такой керамической формы в процессе высокоградиентной направленной кристаллизации сплавов на основе тугоплавких металлов при температурах >1923 K в условиях инертной атмосферы при пониженном давлении. В работах [20, 21] показано, что экспериментальный сплав на основе системы Nb–Ti–Hf–Cr–Al–Si в атмосфере инертного газа при максимальной температуре литья 2123 K взаимодействует с керамической формой на основе высокоогнеупорного оксида иттрия с образованием на поверхности отливки сплошного слоя оксида гафния.
В настоящем исследовании рассмотрены потенциальные возможности системы Y2O3–ZrO2–HfO2 для синтеза керамики для литейных форм, содержащей 15 мол. % Y2O3 : 60 мол. % ZrO2 : 25 мол. % HfO2. Этот выбор обусловлен имеющимися данными о фазовых равновесиях в рассматриваемой системе [22–26], а также недавними результатами об особенностях испарения этой системы [27–29]. Необходимо отметить, что керамика выбранного состава на основе системы Y2O3–ZrO2–HfO2 при температурах до 2773 K испаряется конгруэнтно (практически без селективного испарения компонентов). Это позволяет при длительной высокотемпературной эксплуатации материалов на ее основе сохранить заданные физико-химические свойства.
Основная цель настоящей работы – изучение влияния технологических параметров на морфологию и основные свойства керамических форм, получаемых по удаляемым моделям на основе керамики указанного выше состава, а также рассмотрение основных рекомендаций для дальнейшей разработки технологии их получения.
ЭКСПЕРИМЕНТАЛЬНАЯ ЧАСТЬ
Керамические образцы и формы были изготовлены методом послойного нанесения керамической суспензии на удаляемые модели с последующей обсыпкой плавленым крупнозернистым ZrO2, стабилизированным Y2O3, с дальнейшей промежуточной сушкой каждого слоя, удалением модельной массы и последующей термообработкой и высокотемпературным обжигом. Следует отметить, что в этом случае наблюдалось совмещение твердофазного спекания керамики с синтезом трехкомпонентного твердого раствора на основе керамики, содержащей 15 мол. % Y2O3 : : 60 мол. % ZrO2 : 25 мол. % HfO2, выступающего в качестве высокотемпературной связки в высокоогнеупорном керамическом материале [30].
В качестве исходных оксидных материалов керамической суспензии был выбран гранулированный порошок ZrO2, стабилизированный 4 мол. % Y2O3 (ТУ-У 48-0502-01-89), и порошки HfO2 (х. ч.) и Y2O3 (х. ч.). Изучение микроструктуры материалов и образцов проводили на растровом электронном микроскопе Hitachi SU 8010. Изображения получали в режиме вторичных электронов при ускоряющем напряжении 2 кВ. На рис. 1 и 2 приведена микроструктура плавленого крупнозернистого ZrO2, стабилизированного Y2O3, и исходных оксидных порошков.
Рис. 1.
Микроструктура крупнозернистого ZrO2, стабилизированного Y2O3 (увеличение ×200). Материал обсыпки представлен зернами неправильной осколочной формы с максимальным размером 250 мкм.
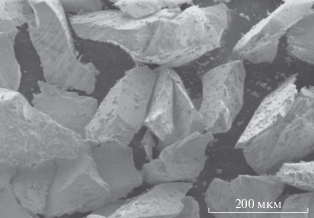
Рис. 2.
Микроструктура исходных порошков оксидов (увеличение ×200): а – ZrO2, стабилизированный 4 мол. % Y2O3; б – HfO2; в – Y2O3.
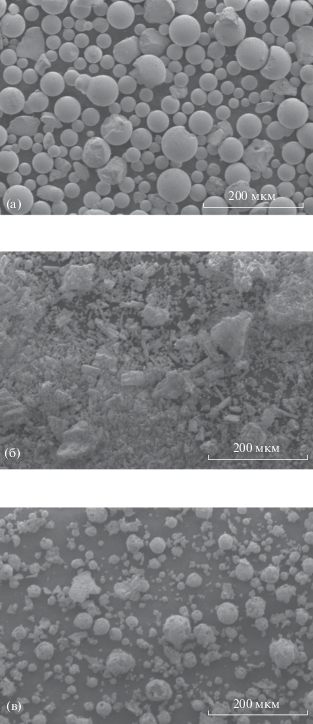
Отметим, что частицы исследованных порошков ZrO2, стабилизированного 4 мол. % Y2O3, и HfO2 имеют правильную сферическую форму независимо от размеров, причем диаметр сфер не превышает 50 мкм. Полидисперсный порошок HfO2 представлен частицами неправильной осколочной формы с максимальным размером 100–110 мкм. Дисперсные частицы порошка Y2O3 состоят из рыхлых агломератов сферической формы.
Механическую смесь указанного выше состава, полученную с учетом содержания в исходном порошке ZrO2 в качестве стабилизатора 4 мол. % Y2O3, измельчали в агатовой ступке как в сухом состоянии, так и с добавлением воды. Полученные смеси сушили в электрическом шкафу СНОЛ 220/300 при температуре 393 K. Микроструктура смеси порошков после сухого и мокрого измельчения приведена на рис. 3.
Рис. 3.
Микроструктура исходной смеси порошков после сухого (а – увеличение ×1000) и мокрого измельчения (б – увеличение ×2000).
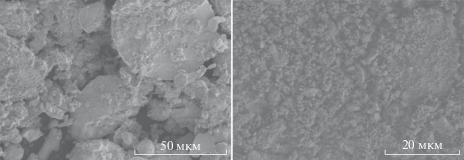
Как следует из рис. 3, мокрое измельчение позволяет получить более дисперсную и однородную по составу смесь оксидных порошков, что облегчает процесс твердофазного спекания керамики, совмещенного с синтезом трехкомпонентного твердого раствора исследуемой керамики.
Затем полученные смеси вводили в предварительно приготовленный раствор эпоксидной смолы ЭД-20 в органическом растворителе (эпоксидное связующее) следующего состава, мас. %:
– смола ЭД-20 (временная технологическая связка) – 15.0;
– полиэтиленполиамин (отвердитель) – 5.0;
– диэтилкетон (органический растворитель) – 80.0.
Были приготовлены две керамические суспензии: F-1, состоящая из смеси порошков ZrO2, HfO2, Y2O3 после сухого измельчения и эпоксидного связующего, и F-2, включающая смесь порошков ZrO2, HfO2, Y2O3 после мокрого измельчения и эпоксидное связующее, содержащие 50–60 мас. % смеси высокоогнеупорных порошков и 40–50 мас. % эпоксидного связующего с использованием мешалки передвижной с пневмодвигателем ЭТНА.
На модельные блоки демонстрационных лопаток и образцов-свидетелей из водорастворимой модельной массы на основе мочевины наносили 5–7 слоев керамической суспензии методом погружения в суспензию с последующей обсыпкой каждого слоя крупнозернистым огнеупорным материалом. В качестве обсыпки использовали узко-фракционированный плавленый ZrO2, стабилизированный Y2O3, имеющий размер зерен 212–250 мкм. Каждый полученный таким образом слой подвергали сушке на воздухе при комнатной температуре в течение 2 ч и затем при температуре 353 K в течение 3–5 ч в сушильном шкафу с парообогревом.
После формирования многослойного керамического покрытия модельную массу удаляли струей воды с температурой 303–308 K. Затем керамические формы и образцы-свидетели сушили на воздухе в течение 3–5 ч. Предварительную термообработку при температуре 473–523 K в течение 2 ч проводили в электрическом сушильном шкафу СНОЛ 220/300. Высокотемпературный обжиг, при котором происходило полное удаление остатков эпоксидного связующего и твердофазное спекание керамики, совмещенное с синтезом трехкомпонентного твердого раствора, выполняли в электрической печи Nabertherm LHT 04/17 SW при температуре 1973 K в течение 4–10 ч в воздушной среде.
На обожженных образцах-свидетелях были проведены измерения линейной усадки по ГОСТ 5402.2-2000 при помощи штангенциркуля ШЦ-II 160-0.05, открытой пористости методом гидростатического взвешивания по ГОСТ 2409-95 с использованием весов ВЛР 200 и предела прочности при статическом изгибе ГОСТ 473.8-81 (скорость приложения нагрузки 6 мм/мин) на разрывной машине МР-005.
Исследована микроструктура полученной таким образом керамики методом сканирующей электронной микроскопии при помощи растрового электронного микроскопа Hitachi SU 8010, оснащенного энергодисперсионным спектрометром Oxford Instruments X-Max (80 мм2). Микрорентгеноспектральный анализ проводили по ГОСТ 22309-2015 при ускоряющем напряжении 25 кВ. Локальность микрорентгеноспектрального анализа составляла 1 мкм2, глубина анализа 1 мкм. Изображения получали в режиме отраженных электронов на микрошлифе образца керамической формы с напылением золотом.
Условную вязкость керамической суспензии измеряли с использованием вискозиметра ВЗ-246 с диаметром сопла 4 мм по ГОСТ 8420-74.
РЕЗУЛЬТАТЫ И ОБСУЖДЕНИЕ
Установлено, что для формирования оптимальной структуры многослойного материала керамической формы необходимы условия, при которых частицы крупнозернистого материала будут внедряться в суспензионный слой на глубину, равную примерно половине его толщины при нанесении первого слоя, и практически на всю глубину при нанесении последующих слоев за счет использования керамических суспензий различной вязкости. Для первого слоя условная вязкость керамической суспензии составляла 30–35 с, для последующих слоев – 20–25 с.
Исследовано влияние температуры на скорость сушки образцов экспериментального состава. В процессе сушки при температурах 313–373 K наблюдалось испарение органического растворителя и последующее отверждение эпоксидной смолы с образованием пространственного полимера. Показано, что при снижении температуры сушки ниже 313 K ее скорость уменьшается примерно в 2 раза по сравнению с сушкой при 373 K, что технологически не оправдано. Повышение температуры сушки более 373 K может приводить к деформации модели. Сформированные на моделях керамическая форма и образцы-свидетели после сушки при 353 K и удаления модельной массы приведены на рис. 4.
Структура полученного керамического материала слоистой морфологии приведена на рис. 5. Обжиг керамических образцов-свидетелей проводили при нагревании со скоростью 300–350 град/ч до температуры 1973 K и выдержке при конечной температуре в течение 2 ч. Внешний вид спеченных керамических образов показан на рис. 6.
Рис. 5.
Микроструктура сформированного материала керамической формы после удаления модельной массы (увеличение ×60).
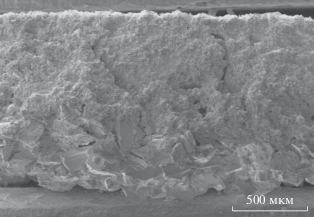
После высокотемпературного обжига на лицевой поверхности керамических образцов наблюдалось отслаивание тонких слоев поверхности в виде чешуек, что, вероятно, связано с высокой скоростью процесса термической деструкции эпоксидного связующего, сопровождаемого интенсивным газообразованием.
Известно, что основная масса эпоксидной смолы ЭД-20 разлагается при температурах 523–723 K с выделением следующих летучих продуктов деструкции: фрагментов ОН, Н2О, СО, Н2СО, С2Н2О, СН3ССН3, а также фенола. При этом температура максимума десорбционных пиков находится в интервале Тm = 579–603 K [31].
Изучено влияние температуры термообработки на прочность экспериментального керамического материала формы в области температур, близкой к температуре разложения основной массы эпоксидной смолы ЭД-20. Результаты исследований, приведенные в табл. 1, свидетельствуют о том, что с увеличением температуры термообработки от 473 до 523 K прочность образцов-свидетелей постепенно уменьшается независимо от вида использованной керамической суспензии, однако остается достаточной для проведения дальнейших технологических операций. Отметим, что наблюдаемое снижение прочности связано с частичным разложением смолы ЭД-20, при этом состояние лицевой поверхности не изменяется.
Таблица 1.
Значения предела прочности при статическом изгибе керамических образцов-свидетелей по ГОСТ 473.8-81 (скорость приложения нагрузки 6 мм/мин)
Шифр керамической суспензии | Прочность σизг, МПа | |||
---|---|---|---|---|
после удаления модельной массы | после термообработки в течение 1 ч | |||
Т = 473 K | Т = 498 K | Т = 523 K | ||
F-1 (смесь порошков ZrO2, HfO2, Y2O3 после сухого измельчения, эпоксидное связующее) | 15.3 | 13.2 | 12.4 | 7.2 |
F-2 (смесь порошков ZrO2, HfO2, Y2O3 после мокрого измельчения, эпоксидное связующее) | 18.6 | 16.6 | 15.3 | 8.9 |
Керамические формы и образцы-свидетели после термообработки при 523 K обожжены при быстром нагреве до 1973 K и выдержке при конечной температуре в течение 2 ч. На рис. 7 приведены изображения керамических образцов-свидетелей и формы, полученные с использованием керамической суспензии F-2.
Обожженные керамические образцы-свидетели и формы, изготовленные с использованием керамической суспензии F-1, в дальнейшей работе не использовали из-за низкой механической прочности.
Микроструктура материала обожженной керамической формы, полученного с использованием керамической суспензии F-2, показана на рис. 8.
Как видно из рис. 8, при высоких температурах спекания наблюдается слияние отдельных дисперсных частиц и зарастание пор.
Распределение элементов в материале обожженной керамической формы представлено на рис. 9, из которого видно, что в материале керамической формы присутствуют частицы с повышенным содержанием гафния размером до 50 мкм, а также с повышенным содержанием циркония размером до 50 мкм. Наблюдаются области равномерного распределения гафния, циркония и иттрия между частицами с повышенным содержание гафния.
Рис. 9.
Картины распределения элементов в материале обожженной керамической формы ×500 (а – изображение в режиме отраженных электронов, б – распределение гафния, в – распределения циркония, г – распределения иттрия).
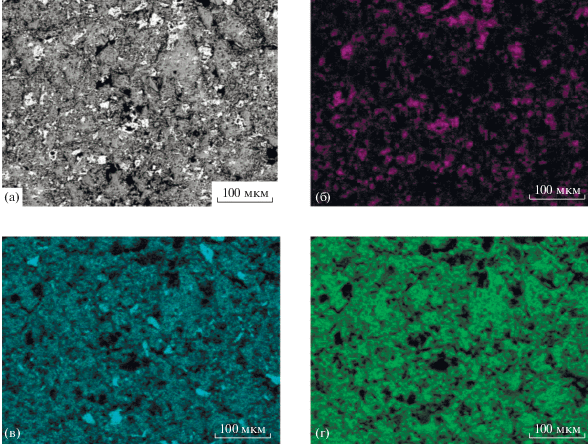
Определены основные структурно-механические свойства полученного высокотемпературного керамического материала формы:
– линейная усадка при обжиге 0.9%;
– открытая пористость 27.2%;
– предел прочности при изгибе при комнатной температуре 6.1 МПа.
Таким образом, полученные значения основных свойств разработанной керамической формы соответствуют требованиям, предъявляемым к литейным формам [20].
На основании проведенного исследования можно сделать вывод, что высокоогнеупорную литейную форму, стабильную при температурах существенно выше 2273 K, удается получить традиционным методом по удаляемым моделям, при этом твердофазное спекание керамики не исключает возможности одновременного совмещения с синтезом выбранного трехкомпонентного твердого раствора, содержащего 15 мол. % Y2O3 : 60 мол. % ZrO2 : 25 мол. % HfO2, выступающего в качестве высокотемпературной связки.
ЗАКЛЮЧЕНИЕ
В результате проведенного исследования проиллюстрирована перспективность использования керамики на основе системы Y2O3–ZrO2–HfO2, содержащей 15 мол. % Y2O3 : 60 мол. % ZrO2 : 25 мол. % HfO2, для дальнейшего синтеза высокотемпературной керамики для литейных форм. Разработаны методические особенности получения указанной керамики и определены ее физико-химические характеристики, подтверждающие целесообразность работ в данном направлении.
Список литературы
Литые лопатки газотурбинных двигателей: сплавы, технология, покрытия / Под ред. Каблова Е.Н. М.: Наука, 2006. 632 с.
Каблов Е.Н., Бондаренко Ю.А., Ечин А.Б. // Авиационные материалы и технологии. 2017. № S. С. 24.https://doi.org/10.18577/2071-9140-2017-0-S-24-38
Bewlay B.P., Cretegny L., Francis M. et al. Shell mold for casting niobium-silicide alloys, and related compositions and processes. Patent № US 7 296 616 B2. Date of Patent: Nov. 20, 2007.
Bancheri S.F., Klug F.J., Bewlay B.P. Hafnia-modified rare-earth metal-based ceramic bodies and casting processes performed therewith. Patent US № 7 845 390 B2. Date of Patent: Dec. 7, 2010.
Bewlay B.P., Klug F.J. Rare earth-based core constructions for casting refractory metal composites, and related processes. Patent № US 7 610 945 B2. Date of Patent: Nov. 3, 2009.
Zhu D., Bansal N.P., Miller R.A. Thermal conductivity and stability of HfO2–Y2O3 and La2Zr2O7 evaluated for 1650°C thermal/environmental barrier coating applications. NASA/TM-2002-212544, 2003.
Zhu D., Miller R.A. Thermal conductivity of advanced ceramic thermal barrier coatings determined by a steady-state laser heat-flux approach. NASA/TM-2004-213040, 2004.
Acosta W.A., Bhatt R.T., Brewer D.N., Zhu D. // The Amptiac Quarterly. 2004. V. 8. № 4. P. 126.
Cao X. // J. Mater. Sci. Technol. 2007. V. 23. № 1. P. 15.
Chong Wang. Experimental and computational phase studies of the ZrO2-based systems for thermal barrier coatings. Dissertation. Universitat Stuttgart. Bericht Nr. 189. September 2006.
Kuznetsov S.A // Chemical Papers. 2012. V. 66. № 5. P. 511.
Чубаров Д.А., Матвеев П.В. // Авиационные материалы и технологии. 2013. № 4. С. 43.
Способ получения изделий из композиционного материала на основе диоксида гафния: Пат. 2176281C2 РФ. Заявл. 09.11.1999; опубл. 27.11.2001 // Бюл. изобр. № 36.
Алешин Д.К. Технология получения гафнийсодержащих оксидных систем для поглощающих стержней управления и защиты. Автореф. дис. … канд. хим. наук. Екатеринбург, 2011. 16 с.
Kumar B.R., Rao T.S. // Int. J. Pure Appl. Sci. Technol. 2011. V. 4. № 2. P. 105.
Глушкова В.Б., Кравчинская М.В., Кузнецов А.К., Тихонов П.А. Диоксид гафния и его соединения с оксидами редкоземельных элементов. Л.: Наука, 1984. 176 с.
Новиков А.С., Харьковский С.В., Мухин А.А. // Двигатель. 2017. № 1. С. 2.
Оспенникова О.Г., Рассохина Л.И., Битюцкая О.Н. и др. // Тр. ВИАМ: электрон. научно-техн. журн. 2017. Т. 52. № 4. С. 3. https://doi.org/10.18577/2307-6046-2017-0-4-1-1
Бондаренко Ю.А., Колодяжный М.Ю., Ечин А.Б. и др. // Тр. ВИАМ: электрон. научно-техн. журн. 2018. Т. 61. № 1. С. 3. https://doi.org/10.18577/2307-6046-2018-0-1-1-1
Фоломейкин Ю.И., Светлов И.Л., Кузьмина И.Г. // Огнеупоры и техническая керамика. 2016. № 4–5. С. 15.
Зайцев А.К., Светлов И.Л., Фоломейкин Ю.И. и др.// Изв. вузов. Цветная металлургия. 2013. № 6. С. 14.
Trubeja M.F., Stubican V.S. // J. Am. Ceram. Soc. 1988. V. 71. № 8. P. 662.
Шевченко А.В., Лопато Л.М., Оболончик Т.В. // Изв. АН СССР. Неорган. материалы. 1987. Т. 23. № 3. С. 452.
Оболончик Т.В., Лопато Л.М., Герасимюк Г.И., Шевченко А.В. // Неорган. материалы. 1991. Т. 27. № 11. С. 2345.
Нипан Г.Д. // Неорган. материалы. 1999. Т. 35. № 10. С. 1252.
Dudnik E.V., Lakiza S.N., Tishchenko Ya.S. et al. // Powder Metall. Met. Ceram. 2014. V. 53. № 5–6. P. 303.
Sevast'yanov V.G., Simonenko E.P., Simonenko N.P. et al. // Russ. J. Inorg. Chem. 2012. Т. 57. № 3. P. 307. [Cевастьянов В.Г., Симоненко Е.П., Симоненко Н.П. и др. // Журн. неорган. химии. 2012. Т. 57. № 3. С. 355.]
Sevastyanov V.G., Simonenko E.P., Simonenko N.P. et al. // Mater. Chem. Phys. 2015. V. 153. P. 78. https://doi.org/10.1016/j.matchemphys.2014.12.037
Столярова В.Л. // Тр. Кольского научного центра РАН. 2015. Т. 31. № 5. С. 47.
Способ изготовления бескремнеземной керамической формы для литья по выплавляемым моделям. Пат. 2502578С1 РФ. Опубл. 27.12.2013.
Сигарева Н.В., Горелов Б.М., Старокадомский Д.Л. // Поверхность. 2013. Т. 20. № 5. С. 206.
Дополнительные материалы отсутствуют.
Инструменты
Журнал неорганической химии