Журнал неорганической химии, 2023, T. 68, № 7, стр. 965-974
Синтез и свойства магнитных углеродных нанокомпозитов из целлюлозы методом химической активации FeCl3
А. Н. Прусов a, *, С. М. Прусова a, М. В. Радугин a
a Институт химии растворов им. Г.А. Крестова РАН
153045 Иваново, ул. Академическая, 1, Россия
* E-mail: anp@isc-ras.ru
Поступила в редакцию 15.12.2022
После доработки 13.03.2023
Принята к публикации 14.03.2023
- EDN: RHOMBK
- DOI: 10.31857/S0044457X22602206
Аннотация
Исследовано получение графитизированных магнитных углеродных композитов, сочетающих адсорбционные свойства активированного угля с магнитными, а также свойствами, присущими графиту. Показана эффективность метода, включающего модификацию целлюлозы костры льна лимонной кислотой для усиления хелатирующей способности целлюлозной матрицы костры льна, пропитку модифицированной целлюлозы хлоридом железа, пиролиз в инертной среде для контролирования состава, морфологии, удельной поверхности и пористости гибридных углеродных материалов. Методом термогравиметрии установлен возможный механизм пиролиза целлюлозной матрицы. Характеристики графитизированных композитов исследованы с помощью рентгеноструктурного анализа. Установлено, что модификация целлюлозы лимонной кислотой позволяет получить углеродный композит с высоким содержанием графита (74%) со степенью графитизации графитовой структуры, близкой к степени графитизации коммерческого графита при 700°С. Методами низкотемпературной адсорбции–десорбции N2 и ζ-потенциала установлен возможный механизм адсорбции экологически опасных красителей. Показано, что наибольшая равновесная величина адсорбции красителей метиленового синего и метилового оранжевого составила 127.4 и 23.7 мг/г соответственно. Полученные композиты могут использоваться в качестве адсорбентов и наполнителей в полимерных композиционных материалах.
ВВЕДЕНИЕ
Активированный уголь (АУ) широко применяется в качестве эффективного адсорбента для очистки воды и воздуха благодаря его большой площади поверхности и развитой микро- и мезопористой структуре [1–5]. Кроме того, АУ способен адсорбировать полярные и неполярные соединения из газовой и жидкой фазы [6–11].
Как правило, коммерческий АУ получают путем карбонизации и активации материалов с высоким содержанием углерода, таких как уголь и смола [12, 13]. Однако эти прекурсоры углерода относительно дорогие и не возобновляются, что побудило к развитию научных исследований по использованию отходов сельского хозяйства и промышленности в качестве прекурсоров АУ [14–18].
При производстве волокнистых продуктов из тресты у производителей возникает большая проблема по утилизации отходов в виде костры, количество которой достигает 65–75% от объема исходного сырья. В настоящее время основную массу таких отходов просто сжигают в топках котельных, т.е. используют в качестве топлива. В то же время эти отходы на ~60% состоят из чистой целлюлозы, потребности в которой увеличиваются год за годом, из-за чего растут вырубки лесов. Поэтому простое сжигание костры крайне неэффективно экономически и наносит вред экологии. Гораздо эффективнее использовать костру для получения активированного угля и других материалов [19–23].
Химическая активация считается высокоэффективным методом получения АУ благодаря высокому выходу, низкой температуре и короткому времени активации [11]. В качестве нового активирующего агента FeCl3 обладает уникальными свойствами, такими как низкая стоимость и низкая токсичность, по сравнению с типичными активирующими агентами (ZnCl2, H3PO4, KOH) [24, 25]. Кроме того, активированные углеродные матрицы, содержащие Fe3O4, предпочтительнее обычного АУ в системах очистки воды и сточных вод, поскольку они значительно облегчают проблематичную стадию выделения сорбента из очищенных сточных вод за счет использования внешнего магнита [26, 27].
Усиление хелатирующей способности целлюлозы за счет карбоксильных групп, обеспечивающих высокий отрицательный поверхностный заряд, позволяет осуществлять контроль хелатирующего связывания ионов металлов. Связывание ионов металлов уменьшает их подвижность в набухшей целлюлозе, что обеспечивает их равномерное распределение в целлюлозной матрице. При пиролизе углеродная матрица сохраняет морфологию исходной целлюлозы и равномерное распределение наночастиц металлов и их оксидов.
Целью работы является получение магнитного графитового нанокомпозита, изучение механизма пиролиза микрокристаллической целлюлозы (МКЦ), модифицированной лимонной кислотой (МКЦЛ), исследование морфологии нанокомпозитов и их свойств, определение адсорбционной емкости углеродных нанокомпозитов относительно красителей метиленового синего (МС) и метилового оранжевого (МО).
ЭКПЕРИМЕНТАЛЬНАЯ ЧАСТЬ
В работе использовали гексагидрат хлорида железа (FeCl3 · 6H2O) аналитической чистоты (Sigma-Aldrich); моногидрат лимонной кислоты аналитической чистоты; MС (C16H18ClN3S ⋅ 3H2O) и МО (C14H14O3N3SNa) производства Sigma-Aldrich. Все растворы были приготовлены на деионизированной воде. Чистота N2 составляла 99.999%.
Получение металл-углеродных композитов. Измельченную сухую костру гидролизовали 10%-ным водным раствором азотной кислоты, затем ее промывали и отбеливали щелочным раствором, содержащим Н2О2. Полученную МКЦ модифицировали лимонной кислотой, образующей сложноэфирную связь с макромолекулой целлюлозы [28]. Модификацию MКЦ раствором лимонной кислоты проводили следующим образом. МКЦ (50 г) смешивали с раствором лимонной кислоты (200 г/л) в соотношении 1 : 3, перемешивали в течение 30 мин при 20°C и сушили при 50°C в сушильном шкафу с принудительной подачей воздуха. Через 24 ч реакцию между кислотой и МКЦ продолжали путем повышения температуры печи до 120°С на 12 ч. После охлаждения продукт реакции заливали 0.6 л дистиллированной воды и перемешивали. Избыток воды, содержащей непрореагировавшую лимонную кислоту, удаляли фильтрацией. МКЦЛ промывали дистиллированной водой до нейтральной реакции, центрифугировали при 3000 об/мин и сушили на воздухе.
Затем 50.0 г MКЦЛ смешивали с 125 мл 0.6 M раствора FeCl3 и выдерживали в течение 12 ч. Пропитанный раствором FeCl3 образец MКЦЛ (Fe@MКЦЛ) сушили при температуре 105°С до постоянной массы [29]. Далее образцы Fe@MКЦЛ массой по 3 г подвергали пиролизу при разных температурах в горизонтальном реакторе непрерывного действия в среде чистого азота согласно работе [30]. Перед пиролизом реакционную камеру продували азотом в течение 30 мин. Процесс пиролиза образцов проводили со скоростью нагрева 10 град/мин в потоке азота, подаваемого со скоростью 30 см3/мин. Образцы охлаждали в воздушной атмосфере.
В результате пиролиза получены графитовые углеродные композиты при разных температурах: Fe@С-500, Fe@С-600, Fe@С-700, Fe@С-800, Fe@С-900 и Fe@С-1000.
Методы анализа. Адсорбционные свойства графитовых углеродных материалов изучали с использованием красителей MС и МО. Готовили исходный раствор, содержащий 1 г МС в 1 л дистиллированной воды. Готовый раствор хранили в темном месте при комнатной температуре.
Адсорбционные эксперименты проводили в наборе колб Эрленмейера объемом 100 мл. Фиксированную массу углеродного композита (15 мг) взвешивали на электронных лабораторных весах CAUW 120D и помещали в конические колбы, содержащие растворы красителя MС (рН 7.0) различной концентрации (20, 100, 150, 200, 300, 400 мг/л).
Герметичные колбы помещали в термостат и встряхивали при 120 об/мин при 25°С до достижения равновесия. После достижения равновесия адсорбент отделяли от водной фазы центрифугированием при 5000 об/мин в течение 30 мин. Равновесное количество МС и МО (мг/г), поглощенное композитом, определяли с использованием спектрофотометра Specord при максимальной длине волны λ = 668 и 464 нм соответственно.
Равновесное количество красителей qр (мг/г), поглощенное углеродными нанокомпозитами, определяли по уравнению [31]:
где C0 и Cр (мг/л) – концентрация красителя в жидкой фазе в исходном и равновесном состоянии соответственно, V (л) – объем раствора, W (г) – масса использованного адсорбента.Все исследования проводили методом рентгеновской дифракции на дифрактометре Bruker D8 Advance, оборудованном германиевым монохроматором и системой щелей для монохроматизации и фокусировки (λCuKα1 = 1.5406 Å), а также позиционно-чувствительном детектором LynxEye, в угловом диапазоне 5°–80° с шагом 0.02° по углу 2θ.
Расчеты выполнены с помощью программы EVA [Bruker AXS GmbH, DIFFRAC.EVA, Karlsruhe, Германия, 2011] и TOPAS 4.2 [Coelho, A. TOPAS 4.2, Bruker AXS GmbH, Karlsruhe, Германия, 2009].
Поиск кристаллических фаз осуществляли по величинам d(hkl) с помощью открытой кристаллографической базы структурных данных, порошковых баз данных PDF-2 и PDF-4, а также открытых литературных источников. Количественное определение фазового состава проводили с использованием полнопрофильного уточнения (метод Ритвельда) и данных об атомных координатах и тепловых параметрах индивидуальных фаз, содержащихся в Кембриджской базе данных (ccdc.cam.ac.uk). Фон учитывали при помощи линейных полиномов до 19 порядка. Инструментальный вклад в уширение дифракционных максимумов описан с помощью предварительных измерений стандарта (LaB6). Для определения размера кристаллита использовали метод расчета высоты колонок из данных интегрального уширения дифракционных максимумов.
Размеры кристаллитов рассчитывали по формуле Шеррера:
где λ – длина волны CuKα-излучения, нм; β – полная ширина дифракционного пика, измеренная на его полувысоте, рад; θ – угловое положение рефлекса, град.Уравнение Брэгга использовали для расчета межплоскостного расстояния d002:
где d002 – межплоскостное расстояние, λ – длина волны CuKα-излучения, θ – угол Брэгга.Степень графитизации, являющуюся структурным параметром, использовали для количественной характеристики степени сходства между углеродным материалом и идеальным монокристаллом графита. Для расчета степени графитизации применяли уравнение [32]:
Gp – степень графитизации в процентах, 0.3440 и 0.3354 нм – расстояние между слоями полностью турбостратного и гексагонального графита соответственно.Долю плоскостей (р), находящихся в турбостратном состоянии, рассчитывали по уравнению Бейкона [33]:
Доля плоскостей, находящихся в турбостратном состоянии, рассчитанная по уравнению Бейкона, р = 0.13.
Для моноатомного слоя атомов углерода в графите определяли число графенов:
Термогравиметрический анализ проводили на термомикровесах TG 209 F1 Iris фирмы Netzsch (Германия).
Морфология поверхности композитов изучена с использованием сканирующих электронных микроскопов Carl Zeiss NVision 40 и Vega3 Tescan.
Измерение удельных площадей поверхности АС проводили путем адсорбции N2 при 77 K с использованием анализатора удельной поверхности и пористости NOVAtouch NT LX. Перед измерением образцы дегазировали в течение 1 ч при 523 K.
Модель Брунауэра–Эммета–Теллера (ВЕT) была применена для определения площади поверхности (SBET, м2/г), распределение пор по размерам определяли с помощью метода функционала плотности (DFT) [34, 35], метод t-plot был применен для расчета объема микропор и площади внешней поверхности (площадь мезопористой поверхности). Общий объем пор (Vобщ) рассчитывали при Р/P0 = 0.99, средний диаметр пор – по уравнению: 4Vобщ/SBET [35], объем мезопор (Vмезо) – вычитанием Vмикро из Vобщ : Vмезо = Vобщ – Vмикро [35].
ζ-Потенциал поверхности частиц АС определяли при pH 7 (20°C) в одноразовых кюветах из полистирола (λ = 633 нм, С = 0.1 мг/мл, Zetasizer Nano ZS).
РЕЗУЛЬТАТЫ И ОБСУЖДЕНИЕ
Рентгеноструктурный анализ
Рентгенограмма Fe@С-500 без промывки кислотой представлена на рис. 1. На рентгенограмме обнаружены дифракционные пики при 2θ = = 30.35°, 35.75°, 43.46°, 57.49° и 63.14°, которые возникли в результате карботермического восстановления Fe2O3 аморфным углеродом до магнетита [34].
При повышении температуры пиролиза до 600°C часть наночастиц Fe3O4 в результате карботермического восстановления превращается в Fe0, проявляя пики при 2θ = 44.67° и 65.02° (рис. 2).
Рис. 2.
Рентгенограммы образцов Fe@MКЦЛ после пиролиза при 600 (1), 700 (2), 800 (3), 900 (4) и 1000°С (5).
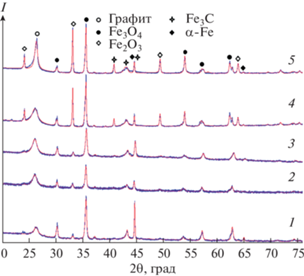
Дифракционные пики с низкой интенсивностью в интервале 2θ = 43°–45° свидетельствуют о поглощении углерода наночастицами железа и появлении метастабильных наночастиц Fe3C, разлагающихся с образованием жидкой фазы аморфный углерод–железо. При этом происходит процесс образования графитовых наноструктур, который идет до тех пор, пока образующийся графит не изолирует расплав железа от аморфного углерода. Хорошо упорядоченные графитовые наноструктуры появляются в результате перекристаллизации растворенного в наночастицах железа аморфного углерода. Появление упорядоченных структур проявляется в виде хорошо выраженного дифракционного пика при 2θ = 26.52°. Авторы многих работ объясняют образование графитовых структур с помощью механизма растворения-осаждения [32, 36]. Примечателен тот факт, что процесс графитизации протекает интенсивно при 600°С, а не при 800°С [37, 38].
Средний размер кристаллитов Fe3O4 при 600, 700, 800, 900 и 1000°C равен 27 ± 3, 22 ± 7, 26 ± 10, 23 ± 5 и 29 ± 9 нм соответственно. Содержание магнетита в углеродном композите при 600, 700, 800, 900 и 1000°C равно 37 ± 5, 21 ± 11, 21 ± 13, 14.0 ± 15 и 18 ± 12% соответственно, т.е. с увеличением температуры наблюдается уменьшение содержания Fe3O4.
Кроме магнетита углеродный композит содержит гематит (Fe2O3) (2θ = 24.32° и 33.42°), содержание которого при 600, 700, 800, 900 и 1000°C равно 4 ± 17, 6 ± 18, 7 ± 16, 12 ± 16 и 9 ± 12% соответственно. Средний размер кристаллитов Fe2O3 при 600, 700, 800, 900 и 1000°C равен 31 ± 6, 28 ± 4, 31 ± 7, 40 ± 5 и 52 ± 14 нм соответственно.
Возможность окисления в инертной среде Fe0 обусловлена тем, что целлюлоза в процессе пиролиза обеспечивает необходимое количество кислорода, а образующийся углерод обладает способностью восстанавливать Fe3+ до Fe2+(Fe0). Совместное присутствие Fe3O4, Fe2O3 и Fe0 в графитизированных композитах может быть вызвано большим (объемным) размером частиц, содержащих железо (замедляет процесс восстановления), и воздействием окружающей атмосферы [37], а отсутствие FeO указывает на наличие окислительно-восстановительного диспропорционирования: 3Fe2+ ↔ 2Fe3+ + Fe [39].
При повышении температуры от 600 до 1000°С изменяется интенсивность пика при 2θ = 26.52°, что означает изменение отношения графитовый углерод/аморфный углерод.
Структурные характеристики d002, Gp не изменяются по мере повышения температуры (табл. 1). Минимальный размер у кристаллитов графита наблюдается при температуре пиролиза 800°С, максимальный – при 1000°С. Следует отметить, что содержание графита значительно уже при 600°С (52 ± 6%).
Таблица 1.
Результаты рентгенофазового анализа углеродных композитов
Образец | 2θ, град | d002 (межплоскостное расстояние), нм | L (размер кристаллитов), нм | Gp (уровень графитизации), % | N = L/d002 + 1 (число графенов) |
---|---|---|---|---|---|
Fe@C-600 Fe@C-700 Fe@C-800 Fe@C-900 Fe@С-1000 |
26.52 26.52 26.52 26.52 26.52 |
0.3358 0.3358 0.3358 0.3358 0.3358 |
7 ± 2 4 ± 5 4 ± 6 5 ± 7 11 ± 14 |
95 95 95 95 95 |
22 13 13 16 34 |
Содержание графита возрастает от 52 ± 6% до 74 ± 3, 72 ± 4, 73 ± 3 и 71 ± 2% с повышением температуры пиролиза от 600 до 700, 800, 900 и 1000°С соответственно, т.е. можно констатировать, что процесс графитизации заканчивается уже при 700°С.
Небольшие различия в содержании графита при температурах выше 700°С вызваны изменением фазового состава углеродного композита. Степень графитизации графитовой структуры, равная 95%, близка к степени графитизации коммерческого графита [40].
Термогравиметрический анализ
Кривая ТГ МКЦЛ характеризуется потерей массы 2.18% из-за испарения воды, оставшейся в предварительно высушенном образце (пик при 63.3°C, ДТГ, рис. 3а). Вторая стадия потери массы МКЦЛ, протекающая с высокой скоростью в интервале температур 317.1–358.0°C, обусловлена деградацией гемицеллюлозы и целлюлозы (пик при 343.7°C, ДТГ). Начиная с температуры 360°C кривая ДТГ характеризуется низкой скоростью потери массы, обусловленной деградацией лигнина.
Кривые ТГ и ДТГ процесса пиролиза Fe@МКЦЛ представлены на рис. 3б. Потеря адсорбционной воды при пиролизе Fe@МКЦЛ (пик при 56.4°C, ДТГ) осложняется тем, что уже выше 79.3°C начинается процесс гидролиза целлюлозы, катализируемый FeCl3. Второй этап потери массы (55.99%) начинается при 186.1°C (пик при 225.3°C), а заканчивается при 303.9°C, он вызван разложением гемицеллюлозы, целлюлозы и FeCl3 · 6H2O согласно реакции (1) [41]:
(1)
$\begin{gathered} {\text{FeC}}{{{\text{l}}}_{3}} + 2{{{\text{H}}}_{{\text{2}}}}{\text{O}} \to {\text{FeOCl }}\cdot{\text{ }}{{{\text{H}}}_{{\text{2}}}}{\text{O}} + 2{\text{HCl}} \to \\ \to {\text{FeOOH}} + {\text{2HCl}}{\text{.}}~~~~~~~~~~~~ \\ \end{gathered} $Потеря массы в диапазоне 303.9–671.2°C соответствует дальнейшему разложению целлюлозы и лигнина, а также протеканию реакций (2) и (3) [42]:
(2)
$2{\text{FeOOH}} \to {\text{F}}{{{\text{e}}}_{{\text{2}}}}{{{\text{O}}}_{3}} + {{{\text{H}}}_{{\text{2}}}}{\text{O}},$(3)
$3{\text{F}}{{{\text{e}}}_{{\text{2}}}}{{{\text{O}}}_{3}} + {\text{C}} \to 2{\text{F}}{{{\text{e}}}_{{\text{3}}}}{{{\text{O}}}_{4}} + {\text{CO}}.~$Кроме того, при температуре ~600°C и выше начинается реакция между Fe3O4 и аморфным углеродом (см. уравнение (4)), а также образование графита:
(4)
${\text{F}}{{{\text{e}}}_{{\text{3}}}}{{{\text{O}}}_{4}} + 4{\text{C}} = 3{\text{F}}{{{\text{e}}}^{0}} + 4{\text{CO}}.$Наличие ярко выраженной ступени в интервале температур 671.2–741.1°C (пик при 701.9°C, ДТГ) на графике TГ свидетельствует о высокой скорости протекания карботермического восстановления по уравнению (4). В этом интервале температур наиболее интенсивно начинают протекать процессы восстановления оксидов железа углеродом до наночастиц Fe0, образующих метастабильные карбиды металла (Fe3С). Стадия потери массы (10.1%) при температуре выше 700°C обусловлена процессами дальнейшей карбонизации и графитизации.
Морфология поверхности композитов
СЭМ-изображения показывают только внешнюю морфологию и не могут предоставить информацию о внутренней структуре частиц. Детали морфологии поверхности образцов были представлены на микрофотографиях СЭМ (рис. 4). Графитизированные магнитные углеродные композиты демонстрируют неровную, шероховатую и агломерированную зернистую структуру поверхности из-за содержания железосодержащих агломератов. На СЭМ-изображениях видны кристаллы магнетита и гематита кубической и тригональной сингонии. Поверхность композита Fe@С-600 покрыта частицами размером ⁓30 нм. При этом на поверхности углеродного материала имеются и более крупные частицы (~60–120 нм). С увеличением температуры выше 600°C размер железосодержащих частиц увеличивается. При температуре пиролиза 1000°C размер железосодержащих агрегатов достигает 800–900 нм (рис. 4д). Наличие элементов углерода, железа, кислорода и незначительного количества хлора (0.09%) в углеродных композитах подтверждается методом энергодисперсионной рентгеновской спектроскопии на примере Fe@C-700 (рис. 4е).
Адсорбционные характеристики
На рис. 5 представлены изотермы адсорбции-десорбции N2 при 600, 700, 800, 900 и 1000°С для углеродных композитов. Изотермы относятся к типу IV по классификации UIPAC [43] и обусловлены капиллярной конденсацией азота. В изотерме типа IV капиллярная конденсация происходит в мезопорах (>2 нм), что приводит к появлению петли гистерезиса Н2, демонстрирующей эффект блокирования десорбционных пор [44]. Появление петли гистерезиса Н2 характерно для материалов, содержащих сложные системы пор, такие как сеть пор в форме чернильницы, для которых характерен эффект блокирования десорбционных пор. Данный тип гистерезиса обусловлен узким распределением поровых тел с широким распределением размера шейки и не сопровождается кавитацией. Петли гистерезиса, резко закрывающиеся при Р0/Р = 0.42, обычно объясняются наличием пор “чернильницы” с узким входом и большей внутренней полостью, которая опорожняется за счет кавитации, а критическая ширина диаметра шейки поры составляет 5–6 нм [44]. В этом случае десорбция происходит посредством кавитации, т.е. спонтанного зарождения пузырька в поре, вызывающего опорожнение полости поры, в то время как шейка поры остается заполненной.
Отсутствие плато адсорбции при относительном давлении, близком к единице, предполагает распределение пор по размерам, простирающееся в диапазон крупных мезопор, а также наличие макропор (>50 нм).
Площадь поверхности композитов, согласно теории БЭТ (табл. 2), уменьшается с повышением температуры пиролиза от 347.0 до 233.5 м2/г, что, возможно, связано с изменением отношения графитовый углерод/аморфный углерод. Общий объем пор композитов уменьшается в ряду: Fe@С-700 > Fe@С-600 ~ Fe@С-900 > Fe@С-1000 ~ Fe@С-800. При этом максимальный объем микропор имеет Fe@С-600, а минимальный – Fe@С-700. Композит Fe@С-700 имеет максимальный объем мезоропор, а Fe@С-600 – минимальный.
Таблица 2.
Пористая структура активированных углеродных композитов, величины равновесной адсорбции МС и МО
Образец | SBET | Sмикро | Sмезо | Vобщ | Vмикро | Vмезо | Средний размер пор, нм | qа(МС) | qа(МО) | S(МС) | S(МО) | ζ-Потен-циал |
---|---|---|---|---|---|---|---|---|---|---|---|---|
м2/г | см3/г | мг/г | м2/г | |||||||||
Fe@С-600 | 347.0 | 287.4 | 59.6 | 0.24 | 0.12 | 0.12 | 2.76 | 37.1 | 9.6 | 137.6 | 16.5 | –15.6 |
Fe@С-700 | 292.1 | 108.7 | 183.4 | 0.34 | 0.049 | 0.291 | 4.65 | 127.4 | 23.7 | 472.6 | 40.8 | +4.11 |
Fe@С-800 | 252.8 | 120.4 | 132.4 | 0.191 | 0.054 | 0.137 | 3.03 | 67.1 | 19.9 | 248.9 | 34.2 | +7.24 |
Fe@С-900 | 258.5 | 120.7 | 137.8 | 0.22 | 0.053 | 0.167 | 3.40 | 109.7 | 20.6 | 406.9 | 35.4 | –3.61 |
Fe@С-1000 | 233.5 | 127.8 | 105.7 | 0.20 | 0.056 | 0.144 | 3.43 | 74.6 | 8.1 | 276.7 | 13.9 | +7.84 |
Размер микропор для Fe@С-700, Fe@С-900, Fe@С-1000, Fe@С-800 и Fe@С-600 в основном равен 1.8, 1.7, 1.6–1.7, 1.5–1.6 и 1.5 нм соответственно (рис. 6). Полученные композиты характеризуются хорошо развитой мезопористой структурой. Композиты Fe@С-600, Fe@С-800, Fe@С-1000, Fe@С-900 и Fe@С-700 имеют средний размер мезопор 3.6–4.5, 2.6–4.3, 2.7–4.3, 2.6–4 и 2.6–4 нм соответственно. Fe@С-900 и Fe@С-700 показали более узкое распределение пор по размерам. При этом Fe@С-600 показал высокие значения микропористости (83%, Smi/SBET) и низкие – мезопористости (17%, Sme/SBET). Композиты Fe@С-700 и Fe@С-900 соответственно имеют низкие значения микропористости (37 и 47%) и высокие значения мезопористости (63 и 53%).
Рост мезопористости с увеличением температуры обусловлен графитизацией, в результате которой микропоры расширяются и превращаются в мезопоры [37].
Гетероциклическое ароматическое соединение широко используется для оценки структуры и адсорбционной способности активированного угля, поскольку доступность поверхности адсорбента для больших молекул, таких как красители, ограничена. Для исследования адсорбционной способности магнитных графитизированных композитов были использованы красители катионного (МС) и анионного (МО) типа. Выбор красителей обусловлен тем, что ионы МС и МО имеют в водном растворе при pH 7 положительные и отрицательные заряды соответственно. Молекулы МО существуют в отрицательно заряженной форме при растворении в воде при pH 7, а в кислой среде H+ присоединяется к атому азота азогруппы МО, и молекула становится заряженной как положительно, так и отрицательно. В основной форме МО (щелочная среда) ион водорода теряется из мостика –N=N– между кольцами, а электроны, используемые для связывания водорода, нейтрализуют положительный заряд на концевом азоте, и он не может образовывать π-связь [30]. Поскольку поверхность магнитных углеродных композитов имеет отрицательный или положительный ζ-потенциал, очевидно влияние электростатического взаимодействия на адсорбцию красителей (табл. 2). Наличие влияния электростатического взаимодействия между адсорбентом и ионами отмечают авторы [45, 46]. При этом отсутствует явная зависимость между величинами адсорбции красителей и знаком ζ-потенциала углеродных адсорбентов.
Это обусловлено тем, что МС и МО представляют собой плоские молекулы, которые легко адсорбируются на углеродных композитах за счет межмолекулярного взаимодействия между делокализованными π-электронами на поверхности нанокомпозита и свободными электронами в ароматических кольцах молекул красителей [47, 48]. На π–π-взаимодействие графитовой структуры с ароматическими кольцами молекул красителей оказывает влияние изменение отношения графитовый углерод/аморфный углерод. При этом наибольшей интенсивностью характеризуются пики (θ = 26.52°) при температуре пиролиза 700 и 900°C. Как следует из табл. 2, композиты Fe@С-700 и Fe@С-900 имеют наибольшую адсорбцию МС и МО.
Наличие адсорбционных сил взаимодействия также влияет на адсорбционную способность адсорбентов [48, 49].
Таким образом, механизм поглощения MС и МО включает гидрофобные, электростатические и адсорбционные взаимодействия. При этом соотношения вкладов разных взаимодействий, влияющих на равновесную адсорбционную емкость композитов по отношению к МС и МО, изменяются с повышением температуры пиролиза. Вероятно, π–π-взаимодействие графитовой структуры с ароматическими кольцами молекул красителей больше для МС, чем для МО. Об этом свидетельствует строение молекул красителей (рис. 7). Кроме того, возможно влияние на адсорбцию конфигурации молекул красителей, влияющей на доступность пор адсорбента.
Исходя из того, что молекулы МС и МО адсорбируются на поверхности углеродного материала в мономерной форме, рассчитана площадь и степень покрытия поверхности углеродных композитов [50].
Величины поверхности полученных композитов рассчитаны с использованием величин адсорбции красителей МС и МО по уравнениям:
Как видно из данных табл. 2, только композиты Fe@С-600 и Fe@С-800 имеют степень покрытия 40 и 99% (S/SBET). Такое покрытие, вероятно, можно считать монослойным. При этом площадь поверхности Fe@С-800, рассчитанная по BET, совпадает с площадью поверхности, рассчитанной с использованием величины адсорбции МС. Степень покрытия поверхности композитов Fe@С-700, Fe@С-900 и Fe@С-1000 составляет 162, 157 и 118%, что свидетельствует о многослойном покрытии поверхности молекулами МС [27]. Степень покрытия углеродных композитов МО находится в пределах 5–14%, что свидетельствует о монослойном покрытии поверхности адсорбентов.
ЗАКЛЮЧЕНИЕ
Усиление хелатирующей способности целлюлозы за счет карбоксильных групп, обеспечивающих отрицательный поверхностный заряд, позволяет осуществлять контроль хелатирующего связывания ионов металлов и обеспечивает их равномерное распределение в целлюлозной матрице. При пиролизе углеродная матрица сохраняет морфологию исходной целлюлозы и равномерное распределение наночастиц металлов и их оксидов. Механизм поглощения MС и МО включает гидрофобные, электростатические и адсорбционные взаимодействия. На адсорбционную способность МС и МО, возможно, влияет конфигурация молекул красителей, от которой зависит доступность пор адсорбента. Использование хлорида железа в качестве катализатора графитизации позволяет получить графитизированный магнитный углеродный композит со степенью графитизации 95%. Самую высокую адсорбционную способность по отношению к МС (127.4 мг/г) и МО (23.7 мг/г) имеет углеродный композит Fe@С-700. Монослойное или многослойное покрытие площади адсорбентов молекулами МС зависит от температуры пиролиза. Одностадийность метода синтеза магнитных адсорбентов, высокая адсорбционная способность молекул МС и МО, возможность удаления адсорбентов из водной среды с использованием магнитов свидетельствуют о перспективности использования углеродных композитов для борьбы с загрязнением водной среды.
Список литературы
Niazi L., Lashanizadegan A., Sharififard H. // J. Clean. Prod. 2018. V. 185. P. 554. https://doi.org/10.1016/j.jclepro.2018.03.026
Zhang B., Zeng X., Xu P. et al. // Environ. Sci. Technol. 2016. V. 50. P. 11837. https://doi.org/10.1021/acs.est.6b01919
Erdem H., Erdem M. // Biomass Conv. Bioref. 2022. V. 12. P. 3513. https://doi.org/10.1007/s13399-020-00963-z
Bekhoukh A., Moulefera I., Zeggai F.Z. et al. // J. Polym. Environ. 2022. V. 30. P. 886. https://doi.org/10.1007/s10924-021-02248-6
Rashidi N.A., Yusup S. // Chem. Eng. J. 2017. V. 314. P. 277. https://doi.org/10.1016/j.cej.2016.11.059
Klasson K.T., Wartelle L.H., Lima I.M. et al. // Bioresour. Technol. 2009. V. 100. P. 5045. https://doi.org/10.1016/j.biortech.2009.02.068
Ogungbenro A.E., Quang D.V., Al-Ali K.A. et al. // J. Environ. Chem. Eng. 2020. V. 8. P. 104257. https://doi.org/10.1016/j.jece.2020.104257
Somasundaram S.K., Sekar Gupta V.K., Ganesan S. // J. Mol. Liq. 2013. V. 177. P. 416. https://doi.org/10.1016/j.molliq.2012.09.022
Ahmed M.J. // J. Environ. Chem. Eng. 2016. V. 4. P. 89. https://doi.org/10.1016/j.jece.2015.10.027
Prusov A.N., Prusova S.M., Radugin M.V. et al. // Fuller. Nanotub. Car. N. 2021. V. 29. P. 685. https://doi.org/10.1080/1536383X.2021.188106
Ahmed M.J., Theydan S.K. // Powder Technol. 2012. V. 229. P. 237. https://doi.org/10.1016/j.powtec.2012.06.043
Ma J., Zhou L., Dan W. et al. // J. Colloid Interface Sci. 2015. V. 446. P. 298. https://doi.org/10.1016/j.jcis.2015.01.036
Teng H.S., Yeh T.S., Hsu L.Y. // Carbon. 1998. V. 36. P. 1387. https://doi.org/10.1016/S0008-6223(98)00127-4
Hamouda H.A., Cui S., Dai X. et al. // RSC Adv. 2021. V. 11. P. 354. https://doi.org/10.1039/D0RA09509E
Xu Z., Sun Z., Zhou Y. et al. // Colloids Surf., A. 2019. V. 582. P. 123934. https://doi.org/10.1016/j.colsurfa.2019.123934
Khiari B., Ferjani A.I., Azzaz A.A. et al. // Biomass Conv. Bioref. 2021. V. 11. P. 325. https://doi.org/10.1007/s13399-020-00641-0
Rodríguez-Sánchez S., Díaz P., Ruiz B. et al. // J. Environ. Manage. 2022. V. 312. P. 114897. https://doi.org/10.1016/j.jenvman.2022.114897
Прусов А.Н., Прусова С.М., Базанов А.В. и др. // Журн. неорган. химии. 2019. Т. 64. С. 431.
Feng H., Li J., Wang L. // BioRes. 2010. V. 5. № 3. P. 1484. https://doi.org/10.15376/biores.5.3.1484-1495.
Cox M., Pichugin A.A., El-Shafey E.I. et al. // Hydrometallurgy. 2005. V. 78. P. 137. https://doi.org/10.1016/j.hydromet.2004.12.006
Wang C., Yang Q., Ren N. et al. // Chem. Eng. Commun. 2020. https://doi.org/10.1080/00986445.2020.1826940
Hu W., Zhang M., Ton-That M.-T. et al. // Fiber. Polym. 2014. V. 15. P. 1722. https://doi.org/10.1007/s12221-014-1722-6
Prusov A.N., Prusova S.M., Radugin M.V. et al. // Fuller. Nanotub. Car. N. 2021. V. 29. P. 232. https://doi.org/10.1080/1536383X.2020.1832994
Bedia J., Monsalvo V.M., Rodriguez J.J. et al. // Chem. Eng. J. 2017. V. 318. P. 224. https://doi.org/10.1016/j.cej.2016.06.096
Bedia J., Belver C., Ponce S. et al. // Chem. Eng. J. 2018. V. 333. P. 58. https://doi.org/10.1016/j.cej.2017.09.161
Vasu A.E., Archana A.P.M.S., Sagayaraj A.C. et al. // Chem. Commun. 2022. V. 141. P. 109541. https://doi.org/10.1016/j.inoche.2022.109541
Hermosa G.C., Liao C.-S., Wan. S.-F. et al. // J. Nanosci. Nanotechnol. 2021. V. 21. P. 5756. https://doi.org/10.1166/jnn.2021.19494
Vaughana T., Seoa C.W., Marshall W.E. // Bioresour. Technol. 2001. P. 78. P. 133. https://doi.org/10.1016/S0960-8524(01)00007-4
Prusov A.N., Prusova S.M., Zakharov A.G. et al. // Fuller. Nanotub. Car. N. 2019. V. 27. P. 967. https://doi.org/10.1080/1536383X.2019.1679780
Prusov A.N., Prusova S.M., Radugin M.V. et al. // Fuller. Nanotub. Car. N. 2022. V. 30. P. 1019. https://doi.org/10.1080/1536383X.2022.2057965
Kuang Y., Zhang X., Zhou S. // Water. 2020. V. 12. P. 587. https://doi.org/10.3390/w12020587
Destyorini F., Irmawati Y., Hardiansyah A. et al. // Eng. Sci. Technol. Int. J. 2021. V. 24. P. 514. https://doi.org/10.1016/j.jestch.2020.06.011
Bacon BY G.E. // Acta Cryst. 1951. V. 4. P. 558. https://doi.org/10.1107/s0365110x51001781
Dai C., Wan J., Yang S. et al. // Appl. Surf. Sci. 2018. V. 444. P. 105. https://doi.org/10.1016/j.apsusc.2018.02.261
Dizbay-Onat M., Vaidya U.K., Balanay J.A.G. et al. // Adsorpt. Sci. Technol. 2018. V. 36. № 1–2. P. 441. https://doi.org/10.1177/0263617417700635
Krivoruchko O.P., Zaikovskii V.I. // Mendeleev Commun. 1998. V. 8. № 3. P. 97. https://doi.org/10.1070/MC1998v008n03ABEH000944
Hoekstra J., Beale M., Soulimani F. et al. // Carbon. 2016. V. 197. P. 248. https://doi.org/10.1016/j.carbon.2016.05.065
Xu Z., Zhou Y., Sun Z. et al. // Chemosphere. 2020. V. 241. P. 125120. https://doi.org/10.1016/j.chemosphere.2019.125120
Jozwiak W.K., Kaczmarek E., Maniecki T.P. et al. // Appl. Catal. A: General. 2007. V. 326. P. 17. https://doi.org/10.1016/j.apcata.2007.03.021
Li H., Zhang H., Li K. et al. // Fuel. 2020. V. 279. https://doi.org/10.1016/j.fuel.2020.118531
Rufford. T.E., Hulicova-Jurcakova D., Zhu. Z. // J. Mater. Res. 2011. V. 25. P. 1451. https://doi.org/10.1557/JMR.2010.0186
Zhu X., Liu Y., Luo G. et al. // Environ. Sci. Technol. 2014. V. 48. P. 5840. https://doi.org/10.1021/es500531c
Thommes M., Kaneko K., Neimark A.V. et al. // Pure Appl. Chem. 2015. V. 87. P. 1051. https://doi.org/10.1515/pac-2014-1117
Cychosz K.A., Thommes M. // Engineering. 2018. V. 4. P. 559. https://doi.org/10.1016/j.eng.2018.06.001
Udayakumar M., Mrabate B.E., Koós T. et al. // Arabian J. Chem. 2021. V. 14. P. 103214. https://doi.org/10.1016/j.arabjc.2021.103214
Janani B., Mohaimeed A.M.A., Raju L.L. et al. // J. Environ. Health Sci. Engineer. 2021. V. 19. P. 389. https://doi.org/10.1007/s40201-021-00612-1
Istratie R., Stoia M., Păcurariu C. et al. // Arabian J. Chem. 2019. V. 12. P. 3704. http://dx.doi.org/10.1016/j.arabjc.2015.12.012
Fan W., Gao W., Zhang C. et al. // J. Mater. Chem. 2012. V. 22. P. 25108. https://doi.org/10.1039/C2JM35609K
Karagöza S., Tay T., Ucar S. et al. // Bioresour. Technol. 2008. V. 99. P. 6214. https://doi.org/10.1016/j.biortech.2007.12.019
Pittman C.U., He G.R., Wu B. et al. // Carbon. 1997. V. 35. № 3. P. 317. https://doi.org/10.1016/S0008-6223(97)89608-X
Дополнительные материалы отсутствуют.
Инструменты
Журнал неорганической химии