Журнал неорганической химии, 2023, T. 68, № 8, стр. 1042-1049
Получение силикофосфатов NASICON состава Na1+хZr2SiхР3–хO12 пиролизом раствора в расплаве
Д. Н. Грищенко a, *, М. А. Медков a
a Институт химии ДВО РАН
690022 Владивосток, пр-т 100-летия Владивостока, 159, Россия
* E-mail: grishchenko@ich.dvo.ru
Поступила в редакцию 06.03.2023
После доработки 12.04.2023
Принята к публикации 20.04.2023
- EDN: HXPQYD
- DOI: 10.31857/S0044457X23600366
Аннотация
Предложен новый способ синтеза Na1+xZr2SixP3–xO12 (0 < x < 3), основанный на пиролизе раствора, содержащего смесь органических компонентов в расплаве канифоли. Доказано влияние сверхстехиометрических количеств натрия и фосфора на фазовый состав продуктов синтеза. Установлено, что для получения максимально чистого фазового состава прекурсор готовится с мольным соотношением Na : Zr : Si : P = (1.15 + x) : 2 : x : (y – x), где y = 3 (1.20 + х)/(1 + х). Температура обжига прекурсора составляет 1000°С. Различные составы NASICON без кристаллических примесей получены в интервале 1.5 ≤ x ≤ 2.12. Синтезированные образцы исследованы методами рентгенофазового анализа и растровой электронной микроскопии. Представленный способ синтеза перспективен для получения NASICON как в виде объемных материалов, так и в виде тонкослойных покрытий.
ВВЕДЕНИЕ
К универсальным химическим источникам тока, которые отличаются высокой плотностью накапливаемой энергии и эффективным ее сохранением при определенных условиях эксплуатации, относятся Li-ионные проводники. Основными недостатками являются низкая устойчивость к избыточному заряду и полному разряду батареи, ухудшение работы при высоких и снижение емкости при низких температурах, взрывоопасность при нарушении герметичности корпуса. Достаточные ресурсы натриевого сырья и его относительно невысокая стоимость по сравнению с литиевым сырьем делают Na-ионные аккумуляторы перспективными кандидатами для замены Li-ионных. Их преимущество заключается в сохранении энергии как при экстремально низких температурах, так и при перепаде температур.
Натриевые суперионные проводники были открыты в 70-х гг. XX в. [1, 2]. Общая формула, предложенная авторами, выглядит следующим образом: Na1+xZr2SixP3–xO12, где 0 ≤ x ≤ 3. Интерес к изучению твердых электролитов с тех пор не снижается. Соединения NASICON перспективны для использования в качестве твердых электролитов в Na-ионной аккумуляторной батарее, в газовых сенсорах, ионоселективных электродах и прочих устройствах [3–5]. Назначение материала определяет вид синтезируемых соединений (монокристаллы, поликристаллические компакты, тонкие пленки и др.), а также способ их получения. Для создания тонких пленок NASICON для датчиков CO2 чаще используют золь-гель метод [6, 7]. Основным недостатком этого метода является трудоемкость процесса: необходимо контролировать pH растворов, их температуру, скорость добавления компонентов и прочее. Твердые электролиты чаще получают твердофазным методом [8–10]. Важное значение для получения монофазного продукта имеет тщательная гомогенизация смеси исходных компонентов, которая достигается, как правило, многостадийным истиранием в мельнице. Длительность такого синтеза иногда достигает 1 мес [11] и производится при высоких температурах спекания, поэтому процесс считается энергозатратным. Кроме того, синтез часто сопровождается как образованием новых примесных фаз, так и присутствием непрореагировавших исходных соединений [8]. В результате в конечном продукте кроме NASICON можно наблюдать наличие следующих фаз: Na3PO4, ZrO2, SiO2, ZrSiO4, Na2SiO3. Их присутствие значительно ухудшает характеристики созданных материалов: ионную проводимость [12] и химическую стабильность [13].
Указанные недостатки влияют на воспроизводимость полученного состава. В твердофазном методе прогнозировать количество непрореагировавших предшественников весьма затруднительно. В золь-гель методе невозможно воссоздать единые условия синтеза, где даже скорость добавления компонентов часто имеет принципиальное значение. Этих недостатков лишен метод пиролиза органических растворов. Использование гомогенных прекурсоров в виде истинных растворов позволяет исключить непрореагировавшие предшественники и выяснить принцип формирования NASICON в зависимости от содержания исходных компонентов.
В настоящей работе исследован принцип получения материалов семейства Na1+xZr2SixP3–xO12, а также влияние сверхстехиометрических количеств натрия и фосфора на фазовый состав синтезированных продуктов.
ЭКСПЕРИМЕНТАЛЬНАЯ ЧАСТЬ
В качестве растворителя в данном методе использовали этиловый спирт (C2H5OH, ч., “Идеал-Фарм”, Киргизия). Для получения прекурсора в расплаве применяли канифоль (сосновая, марка “А”, ГОСТ 19113-84, “Спецтехнохим”, Россия). Исходными компонентами служили: ацетилацетонат циркония (Zr(C5H7O2)4, ч., “Реахим”, Россия), олеат натрия (C18H33O2Na, ч. д. а., “Sigma Aldrich”, Германия), трибутилфосфат (C12H27O4P, х. ч., “Acros Organics”, США), тетраэтоксисилан (C8H20O4Si, х. ч., “Реахим”, Россия).
Процесс получения прекурсора происходил при постоянном перемешивании с помощью магнитной мешалки (300 об/мин) при начальной температуре растворителя 40–50°С. В этиловом спирте последовательно растворяли ацетилацетонат циркония(IV), тетраэтоксисилан, трибутилфосфат, затем добавляли растворенный в этиловом спирте олеат натрия, полученный раствор нагревали до 60–70°С и добавляли канифоль. При температуре 80°С удаляли растворитель. Полученный прекурсор, представлявший собой прозрачный раствор, подвергали термической обработке при 500°С в течение 30 мин для формирования аморфного порошка. Смесь компонентов измельчали ручным сухим способом и подвергали пиролизу при 1000°С в течение 30 мин. Получены порошки состава Na1+xZr2SixP3–xO12, где х = 1, 1.5, 2, 2.12, 2.35.
Материал исследовали методом рентгенофазового анализа (РФА) на дифрактометре Stoe STADI P. Использовали программу поиска EVA и базу порошковых данных ICDD PDF-2. Идентификацию проводили с помощью PDF-файлов: 01-084-1197, 00-047-0515, 01-084-1200, 01-084-1317, 01-078-1240. Составы дополнительно контролировали методом Ритвельда, расчеты выполнены в программе FULLPROF. Морфология образцов изучена методом растровой электронной микроскопии. Микрофотографии поверхности образцов получены на электронном сканирующем микроскопе Hitachi S5500.
РЕЗУЛЬТАТЫ И ОБСУЖДЕНИЕ
Нами исследована возможность получения различных материалов линейки Na1+xZr2SixP3–xO12 в диапазоне 0 < x < 3 пиролизом растворов в расплаве канифоли. Использование канифоли позволяет избежать дробной кристаллизации или дробного выделения аморфного осадка из смеси компонентов при испарении растворителя, поскольку все составляющие растворяются в расплаве канифоли. В отсутствие канифоли прекурсор после отгонки растворителя представляет собой аморфный осадок, а основным продуктом обжига прекурсора при 1000°С является паракелдышит (Na2ZrSi2O7) с примесями NASICON и ZrO2.
Пиролиз органических растворов в расплаве канифоли исходных компонентов, взятых в стехиометрических количествах, приводит к получению составов, отличных от заданных, и присутствию примесных фаз (табл. 1). Однофазный продукт получить не удалось. Все образцы имели двухфазный или трехфазный состав. Причиной мог быть недостаток элементов Na и P в системе.
Таблица 1.
Получение NASICON из стехиометрических количеств компонентов
№ п/п | Заданный состав | Состав прекурсора, Na : Zr : Si : P, мол. |
Состав продукта синтеза |
---|---|---|---|
1 | Na2Zr2SiP2O12 | 2 : 2 : 1 : 2 | Na2Zr2SiP2O12** + ZrO2(т) + ZrO2(м) |
2 | Na2.5Zr2Si1.5P1.5O12 | 2.5 : 2 : 1.5 : 1.5 | Na3Zr1.833Si1.333Р1.667O12 + ZrO2(т) |
3 | Na3Zr2Si2PO12 | 3 : 2 : 2 : 1 | Na3Zr2Si2PO12 + ZrO2(т)* + Na2ZrSi2O7 |
4 | Na3.12Zr2Si2.12Р0.88O12 | 3.12 : 2 : 2.12 : 0.88 | Na3Zr2Si2РO12 + Na2ZrSi2O7 |
5 | Na3.35Zr2Si2.35P0.65O12 | 3.35 : 2 : 2.35 : 0.65 | Na3.12Zr2Si2.12Р0.88O12 + Na2ZrSi2O7 |
Считается, что Na и P испаряются в процессе высокотемпературной обработки прекурсора. Для сокращения потерь этих элементов предлагают разные стратегии: обжиг в закрытой системе [14], компенсация путем введения дополнительных количеств этих компонентов [15], ступенчатый процесс спекания с понижением температуры обжига [16]. Испарение натрия маловероятно, он не образует летучих соединений. Дефицит тех или иных компонентов возникает, скорее всего, вследствие появления примесей либо участия в образовании рентгеноаморфной фазы. Так, в работе [16] в образцах обнаружен недостаток кремния в образовавшемся NASICON и доказано, что Si является компонентом стеклофазы, образующейся на границах зерен материала. В случае недостатка натрия при твердофазном синтезе в конечных продуктах нередко встречаются непрореагировавшие предшественники [8].
В настоящей работе используется компенсация недостающих количеств компонентов. Предварительные исследования для состава Na3Zr2Si2PO12 показали, что для компенсации недостатка элементов в системе достаточно дополнительно использовать 5 мол. % Na и 20 мол. % P. Эти же мольные проценты избыточных количеств Na и P использовали для получения остальных NASICON. В табл. 2 представлены составы продукта синтеза при изменении концентраций компонентов прекурсора. Единственный состав, полученный без примесей, – это Na3Zr2Si2PO12 (№ 3 в табл. 2), остальные содержат паракелдышит или тетрагональный ZrO2. Естественно, чем больше примесной фазы находится в продукте синтеза, тем сильнее его дифракционная картина не совпадает с ожидаемым результатом. Получение NASICON желаемого состава требует изменения концентраций компонентов в органической смеси. Известно [17], что содержание примеси ZrO2 можно минимизировать путем увеличения количества Na в составе прекурсора. Присутствие паракелдышита является следствием нехватки Р-содержащего компонента в составе смеси [18].
Таблица 2.
Влияние избытка Na и P на состав продукта синтеза NASICON
№ п/п | Состав прекурсора, Na : Zr : Si : P, мол. |
Ожидаемый состав | Состав продукта синтеза |
---|---|---|---|
1 | 2.1 : 2 : 1 : 2.4 | Na2Zr2Si P2O12 | Na2Zr2Si P2O12** + ZrO2(т) |
2 | 2.63 : 2 : 1.5 : 1.8 | Na2.5Zr2Si1.5P1.5O12 | Na2.5Zr2Si1.5P1.5O12 + ZrO2(т)* |
3 | 3.15 : 2 : 2 : 1.2 | Na3Zr2Si2PO12 | Na3Zr2Si2PO12 |
4 | 3.28 : 2 : 2.12 : 1.056 | Na3.12Zr2Si2.12Р0.88O12 | Na3.12Zr2Si2.12Р0.88O12 + Na2ZrSi2O7* |
5 | 3.52 : 2 : 2.35 : 0.78 | Na3.35Zr2Si2.35P0.65O12 | Na3.35Zr2Si2.35P0.65O12** + Na2ZrSi2O7 |
С учетом этих сведений проведена коррекция дополнительных количеств Na и Р для минимизации примесных фаз в составе синтезируемых материалов. Получены следующие результаты. Состав Na2Zr2SiP2O12 (х = 1) не удалось получить без примеси ZrO2. Минимальное содержание ZrO2 получено при дополнительных количествах Na 11 мол. %, P 20 мол. %. Состав Na2.5Zr2Si1.5P1.5O12 (х = 1.5) получен без примеси ZrO2 при сверхстехиометрических количествах Na (8 мол. %) и P (20 мол. %). Состав Na3Zr2Si2PO12 (х = 2), как уже было указано, получен без примесей при добавлении 5 мол. % Na и 20 мол. % Р. Для получения Na3.12Zr2Si2.12P0.88O12 (х = 2.12) необходимо дополнительно 5 мол. % Na и 23 мол. % P. Состав Na3.35Zr2Si2.35P0.65O12 (х = 2.35) без примеси паракелдышита не получен. Минимального количества Na2ZrSi2O7 можно добиться при содержании сверхстехиометрических количеств Na (5 мол. %) и Р (27 мол. %). Составы с х = 1; 1.5; 2.35 имеют ромбоэдрическую сингонию с пр. гр. R$\bar {3}$c, составы с х = 2; 2.12 – моноклинную сингонию с пр. гр. C2/c. Из всего вышесказанного следует, что пиролизом смеси органических растворов при температуре обжига 1000°С можно получить различные составы NASICON без примесей в интервале 1.5 ≤ x ≤ 2.12. Диапазон ограничен данными используемой базы ICDD. Указанные дополнительные количества Na и Р компенсируют нехватку элементов и позволяют получить желаемый состав. Результаты отражены на рис. 1.
На рис. 2 представлены штрихрентгенограммы различных типов NASICON в интервале углов 17° < 2θ < 40°. Как показывает рисунок, чем больше переменное значение х в NASICON, тем меньший угол отражения имеет дифракционный максимум в определенном интервале 2θ. Эта информация будет использована далее для разъяснения полученных результатов.
Рис. 2.
Штрихрентгенограммы: PDF 01-078-1240, х = = 2.35 (а); PDF 01-084-1317, х = 2.12 (б); PDF 01-084-1200, х = 2 (в); PDF 00-047-0515, х = 1.5 (г); PDF 01-084-1197, х = 1 (д).
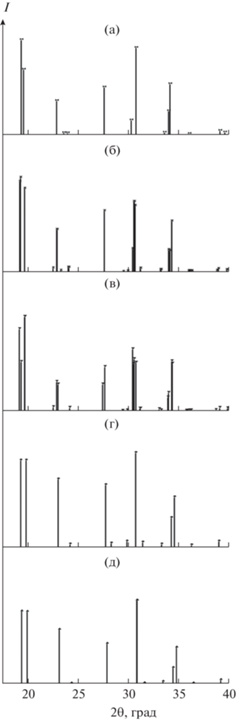
Известно, что свойства NASICON изменяются при увеличении содержания Na или Na + P в исходной смеси [16, 19–21]. В связи с этим изучено влияние дополнительных количеств этих элементов на состав продукта синтеза. В прекурсоры каждого образца к компенсирующим количествам было добавлено дополнительно 5 мол. % Р-содержащего компонента. Обнаружено образование фаз NASICON с близкими кристаллическими структурами. В качестве примера на рис. 3 приведены дифрактограммы состава Na2.5Zr2Si1.5P1.5O12 с дополнительными количествами Na и P, мол. %: 8 и 20, 8 и 25 соответственно. Рис. 3 (кривая 1) демонстрирует классический вариант – образование одной фазы NASICON ромбоэдрической сингонии. При повышении концентрации Р образуется вторая фаза NASICON (рис. 3, кривая 2), причем новая фаза (отмечена стрелками на увеличенном изображении) имеет углы отражения с бóльшими значениями, а NASICON – с меньшим х. Возможно, при дальнейшем увеличении Р образовавшаяся фаза будет преобладать над первой, таким образом, происходит структурное изменение продукта синтеза.
Рис. 3.
Дифрактограммы состава Na2.5Zr2Si1.5P1.5O12 с избыточными количествами Na и P, мол. %: 8 и 20 (1), 8 и 25 (2) соответственно.
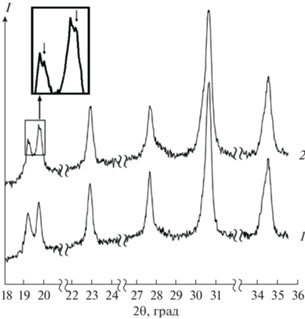
В прекурсоры к компенсирующим количествам было добавлено дополнительно 5 мол. % Na-содержащего компонента. Обнаружено, что дополнительные количества Na способствуют получению NASICON с более высоким значением х. Основную роль в этом случае играет, скорее всего, способность Si и P к взаимозамещению в синтезируемых материалах. На рис. 4 представлены дифрактограммы ожидаемого состава Na3Zr2Si2PO12 с дополнительным количеством Na и P: 5 и 20, 10 и 20, 10 и 30 мол. % соответственно. NASICON на рис. 4 (кривая 1) идентифицирован как Na3Zr2Si2PO12. Дифрактограмма (рис. 4, кривая 2) имеет профиль, типичный для состава Na3.12Zr2Si2.12P0.88O12, что подтверждает увеличенное изображение. Дифракционные пики на рис. 4 (кривые 1 и 3) идентичны, дифрактограммы соответствуют Na3Zr2Si2PO12, т.е. дополнительные количества одновременно Na и P позволяют получить продукт с составом кристаллической фазы, практически не отличающимся от состава с компенсирующими количествами.
Рис. 4.
Дифрактограммы состава Na3Zr2Si2PO12 с избыточными количествами Na и P, мол. %: 5 и 20 (1); 10 и 20 (2); 10 и 30 (3) соответственно.
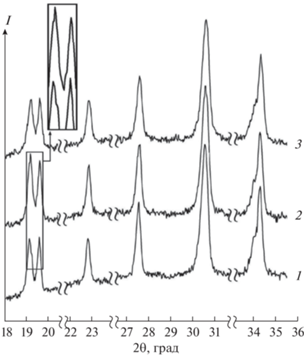
Для всех исследованных материалов установлены количества дополнительных компонентов Na и P, при которых формируется заданный состав. В табл. 3 указаны две различные комбинации сверхстехиометрических значений добавляемых элементов для каждого из исследуемых составов. По данным РФА, повышение концентрации Na и P сверх указанных максимальных количеств приводит к значительному увеличению рентгеноаморфной фазы в материале. Результаты исследования указывают на необходимость одновременного непропорционального увеличения содержания Na и P в прекурсоре для сохранения состава, полученного при минимальных дополнительных количествах. Отношение Na/(Si + P) для NASICON с различными х, где Zr имеет постоянное значение, определяет состав полученного материала. Можно сделать вывод, что для получения желаемого состава требуется соблюдение следующего условия: отношение мольных количеств компонентов образца Na/(Si + P) должно соответствовать определенному значению для каждого конкретного х. Для всех составов NASICON проведен расчет значений указанного отношения. Расчеты параметров элементарных ячеек кристаллических решеток экспериментальных образцов с минимальными дополнительными количествами Na и P, выполненные по методу Ритвельда, отражены в табл. 4. Для максимальных дополнительных количеств параметры аналогичны.
Таблица 3.
Варианты получения заданного состава NASICON при сверхстехиометрических количествах Na- и P-содержащих компонентов
№ п/п | Состав продукта синтеза | Минимальные дополнительные количества Na и P, мол. % | Максимальные дополнительные количества Na и P, мол. % | ||||
---|---|---|---|---|---|---|---|
Na | P | Na/(Si + P) | Na | P | Na/(Si + P) | ||
1 | Na2Zr2SiP2O12 + ZrO2 (т) | 8 | 15 | 0.654 | 11 | 20 | 0.653 |
2 | Na2.5Zr2Si1.5P1.5O12 | 6 | 16 | 0.818 | 10 | 25 | 0.815 |
3 | Na3Zr2Si2PO12 | 5 | 20 | 0.984 | 10 | 30 | 1.00 |
4 | Na3.12Zr2Si2.12P0.88O12 | 5 | 23 | 1.023 | 10 | 35 | 1.037 |
5 | Na3.35Zr2Si2.35P0.65O12 + Na2ZrSi2O7 | 5 | 27 | 1.108 | 10 | 45 | 1.119 |
Таблица 4.
Параметры элементарных ячеек кристаллических решеток экспериментальных образцов NASICON
Состав прекурсора, Na : Zr : Si : P, мол. |
Образец | Параметры элементарной ячейки | |||||
---|---|---|---|---|---|---|---|
a | b | c | α | β | γ | ||
Å | град | ||||||
2.16 : 2 : 1 : 2.3 | PDF: 01-084-1197 | 8.9348 | 8.9348 | 22.8486 | 90 | 90 | 120 |
Na2Zr2SiP2O12 | 8.947(1) | 8.947(1) | 22.998(2) | 90 | 90 | 120 | |
2.65 : 2 : 1.5 : 1.74 | PDF: 00-047-0515 | 8.980 | 8.980 | 22.930 | 90 | 90 | 120 |
Na2.5Zr2Si1.5Р1.5O12 | 8.994(1) | 8.994(1) | 23.015(1) | 90 | 90 | 120 | |
3.15 : 2 : 2 : 1.2 | PDF: 01-084-1200 | 15.6513 | 9.055 | 9.2198 | 90 | 123.742 | 90 |
Na3Zr2Si2РO12 | 15.660(2) | 9.058(1) | 9.229(1) | 90 | 123.840(5) | 90 | |
3.27 : 2 : 2.12 : 1.08 | PDF: 01-084-1317 | 15.669 | 9.246 | 9.055 | 90 | 90 | 124.12 |
Na3.12Zr2Si2.12Р0.88O12 | 15.674(2) | 9.240(1) | 9.061(1) | 90 | 90 | 124.160(4) | |
3.52 : 2 : 2.35 : 0.82 | PDF: 01-078-1240 | 9.097 | 9.097 | 22.680 | 90 | 90 | 120 |
Na3.35Zr2Si2.35Р0.65O12 | 9.087(1) | 9.087(1) | 22.793(2) | 90 | 90 | 120 |
Доказана возможность получения заданного состава NASICON при различных количествах Na и P в составе прекурсора. Однако излишне добавленные компоненты входят, скорее всего, в состав рентгеноаморфной фазы, поскольку иных кристаллических структур, кроме NASICON, с помощью РФА не выявлено. Микроскопия подтверждает наличие незначительного дополнительного количества стеклофазы в образцах с повышенным содержанием указанных элементов. На рис. 5 приведен пример для состава Na3Zr2Si2PO12. Средний размер зерна всех исследуемых материалов составляет 0.3 мкм.
Рис. 5.
Микрофотографии образцов состава Na3Zr2Si2PO12 с избыточными количествами Na и P, мол. %: 5 и 20 (а), 10 и 30 (б) соответственно.
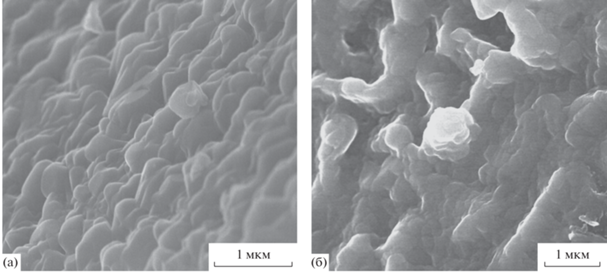
Анализ полученных данных позволяет предложить формулу для расчета мольного соотношения компонентов прекурсора, необходимого для формирования заданного состава:
(1)
${\text{Na}}:{\text{Zr}}:{\text{Si}}:{\text{P}} = \left( {1.15{\text{ }} + x} \right):2:x:\left( {y--x} \right),$Таблица 5.
Расчет мольного соотношения компонентов прекурсора по формуле (1)
№ п/п | Состав продукта синтеза | Состав прекурсора, Na : Zr : Si : P, моль |
Отношение Na/(Si + P) |
---|---|---|---|
1 | Na2Zr2SiP2O12 + ZrO2 (т) | 2.15 : 2 : 1 : 2.3 | 0.652 |
2 | Na2.5Zr2Si1.5P1.5O12 | 2.65 : 2 : 1.5 : 1.74 | 0.818 |
3 | Na3Zr2Si2PO12 | 3.15 : 2 : 2 : 1.2 | 0.984 |
4 | Na3.12Zr2Si2.12P0.88O12 | 3.27 : 2 : 2.12 : 1.07 | 1.025 |
5 | Na3.35Zr2Si2.35P0.65O12 + Na2ZrSi2O7 | 3.5 : 2 : 2.35 : 0.82 | 1.104 |
ЗАКЛЮЧЕНИЕ
Исследованы условия процесса получения Na1+xZr2SixP3–xO12 (0 < x < 3), основанного на пиролизе растворов исходных компонентов в расплаве канифоли. Установлена прямая зависимость фазового состава продукта синтеза от сверхстехиометрических количеств натрия и/или фосфора в прекурсорах. Образование NASICON состава Na1+xZr2SixP3–xO12 происходит из прекурсора, полученного в соответствии с формулой Na : Zr : Si : P = = (1.15 + x) : 2 : x : (y – x), где y = 3(1.20 + х)/(1 + х). Формула справедлива для системы олеат натрия–ацетилацетонат циркония–трибутилфосфат–тетраэтоксисилан–спирт–канифоль при температуре обжига прекурсора 1000°С. Однофазный состав продукта можно получить в диапазоне 1.5 ≤ x ≤ 2.12. Мелкодисперсный материал имеет средний размер зерна 0.3 мкм.
Время синтеза NASICON составляет ⁓6 ч, что является минимальным из всех известных методов изготовления материала. Альтернативные способы уступают представленному по длительности процесса, энергоемкости и трудозатратам.
Список литературы
Hong H.Y.-P. // Mater. Res. Bull. 1976. V. 11. № 2. P. 173. https://doi.org/10.1016/0025-5408(76)90073-8
Goodenough J.B., Hong H.Y.-P., Kafalas J.A. // Mater. Res. Bull. 1976. V. 11. № 2. P. 203. https://doi.org/10.1016/0025-5408(76)90077-5
Miyachi Y., Sakai G., Shimanoe K., Yamazoe N. // Sens. Actuators, B. 2003. V. 93. № 1–3. P. 250. https://doi.org/10.1016/S0925-4005(03)00174-6
Paściak G., Mielcarek W., Prociów K., Warycha J. // Ceram. Int. 2014. V. 40. № 8. P. 12783. https://doi.org/10.1016/j.ceramint.2014.04.132
Meunier M., Izquierdo R., Hasnaoui L. et al. // Appl. Surf. Sci. 1998. V. 127–129. P. 466. https://doi.org/10.1016/S0169-4332(97)00674-0
Tetsuya K., Miyachi Y., Shimanoe K., Yamazoe N. // Sens. Actuators, B. 2001. V. 80. № 1. P. 28. https://doi.org/10.1016/S0925-4005(01)00878-4
Kim H.J., Choi J.W., Kim S.D., Yoo K.S. // Mater. Sci. Forum. 2007. V. 544–545. P. 925. https://doi.org/10.4028/www.scientific.net/MSF.544-545.925
Jalalian-Khakshour A., Phillips Ch., Jackson L. et al. // J. Mater. Sci. 2020. V. 55. P. 2291. https://doi.org/10.1007/s10853-019-04162-8
Naqash S., Sebold D., Tietz F., Guillon O. // J. Am. Ceram. Soc. 2019. V. 102. № 3. P. 1057. https://doi.org/10.1111/jace.15988
Yang G., Zhai Y., Yao J. et al. // Chem. Commun. 2021. V. 57. P. 4023. https://doi.org/10.1039/d0cc07261c
Noguchi Y., Kobayashi E., Plashnitsa L.-S. et al. // Electrochim. Acta. 2013. V.101. P. 59. https://doi.org/10.1016/j.electacta.2012.11.038
Fuentes R.O., Marques F.M.B., Franco J.I. // Bol. Soc. Esp. Ceram. Vidrio. 1999. V. 38. № 6. P. 631.
Fuentes R.O., Figueiredo F., Marques F.-M.B., Franco J.I. // Solid State Ionics. 2001. V. 139. № 3–4. P. 309. https://doi.org/10.1016/S0167-2738(01)00683-X
Fuentes R.O., Figueiredo F.M., Marques F.M.B., Franco J.I. // Solid State Ionics. 2001. V. 140. № 1–2. P. 173. https://doi.org/10.1016/S0167-2738(01)00701-9
Shimizu Y., Azuma Y., Michishita S. // J. Mater. Chem. 1997. V. 7. P. 1487.
Naqash S., Tietz F., Yazhenskikh E. et al. // Solid State Ionics. 2019. V. 336. P. 57. https://doi.org/10.1016/j.ssi.2019.03.017
Грищенко Д.Н., Курявый В.Г., Подгорбунский А.Б., Медков М.А. // Журн. неорган. химии. 2023. № 1. С. 17. https://doi.org/10.31857/S0044457X22601043
Грищенко Д.Н., Дмитриева Е.Э., Медков М.А. // Хим. технология. 2022. Т. 23. № 10. С. 418. https://doi.org/10.31044/1684-5811-2022-23-10-418-423
Narayanan S., Reid S., Butler S., Thangadurai V. // Solid State Ionics. 2019. V. 331. P. 22. https://doi.org/10.1016/j.ssi.2018.12.003
Rao Y.B., Bharathi K.K., Patro L.N. // Solid State Ionics. 2021. V. 366–377. P. 115671. https://doi.org/10.1016/j.ssi.2021.115671
Wang H., Zhao G., Wang S. et al. // Nanoscale. 2022. V. 14. № 3. P. 823. https://doi.org/10.1039/d1nr06959d
Дополнительные материалы отсутствуют.
Инструменты
Журнал неорганической химии