Проблемы машиностроения и надежности машин, 2021, № 2, стр. 63-68
Особенности сварки и пайки сплавов, обладающих эффектом памяти формы
Д. У. Хасьянова *
Институт машиноведения им. А.А. Благонравова РАН
Москва, Россия
* E-mail: dinara.khasyanova@mail.ru
Поступила в редакцию 17.12.2018
После доработки 19.11.2020
Принята к публикации 18.12.2020
Аннотация
В статье представлены особенности конструирования сварных или паяных соединений деталей, в которых используются материалы обладающие эффектом памяти формы. Показано влияние процессов сварки и пайки на характеристики сплава с эффектом памяти формы и “работу эффекта памяти формы”.
Обеспечение высокого качества машин на весь срок эксплуатации за счет повышения надежности и герметичности комплектующих элементов, является одной из важнейших задач машиностроения и долговременных целей промышленности [1]. Одним из основных факторов обеспечения надежности является применение новых материалов, обладающих специфическими свойствами (сверхупругость (СУ), эффект памяти формы (ЭПФ), жаропрочность, постоянство модуля упругости, физические и прочностные свойства в зависимости от анизотропии материала и т.д).
При использовании таких материалов, качество изделий коренным образом зависит от уровня технологии, повышение которого можно достичь благодаря разработке и внедрению процессов, в которых участие человека ограничено и сводится главным образом к их управлению.
Сущность ЭПФ материала заключается в явлении сохранять долгое время деформированное состояние в одном температурном интервале, а при незначительном нагреве возвращаться в исходное состояние. Восстановление исходных размеров ведет к созданию внутри материала напряжений, значительно превосходящих напряжения, приложенные в процессе деформирования. На основании данного явления, разработаны высокотехнологичные процессы, позволяющие самому материалу осуществлять исполнительные действия [2].
По отношению к нормальной температуре, сплав может находиться в аустенитном (В2) или мартенситном (В19) состоянии. В промышленности принято маркировать сплавы, находящиеся в аустенитном состоянии – ТН1, а мартенситном – ТН1К.
Мартенситные превращения характеризуются температурами фазовых превращений: Мн, Мк – температуры начала и конца мартенситного превращения соответственно, Ан, Ак – температуры начала и конца аустенитного превращения. В зависимости от соотношения компонентов Ti, Ni и легирующих элементов, фазовые превращения в сплавах могут происходить при температурах от –20° до +100°С [3].
При сочетании определенных условий, превращения аустенита (А) в мартенсит (М) приобретает некую особенность – “термоупругость”. Процесс превращения можно инициировать изменением температур, напряжений или сочетанием и того, и другого. Следовательно, если в какой-то момент прекратить охлаждение, то превращение прекратится на той стадии, на которой его застала “температура остановки”.
Подъем температуры от этого состояния приводит к обратному М → А превращению, все сдвиговые смещения атомов идут в обратном направлении, а сами атомы возвращаются в исходные позиции, соответствующие аустенитной фазе материала.
На рис. 1 схематически представлены температуры мартенситной и аустенитной области существования материала. Заданная деформация проходит при температурах, ниже интервала прямого мартенситного превращения (МП).
Рис. 1.
Зависимость реактивных напряжений, возникающих в материале при термическом формовосстановлении в условиях противодействия от температуры.
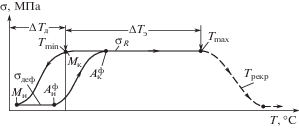
Если процессу термического формовосстановления создать препятствие, то в материале генерируются реактивные напряжения, которые превышают деформационные [4]. Температуры формовосстановления $А_{{\text{н}}}^{{\text{ф}}}$, $А_{{\text{к}}}^{{\text{ф}}}$ в отличие от Ан, Ак имеют сдвиг в область повышенных температур. На рис. 1: $А_{{\text{н}}}^{{\text{ф}}}$, $А_{{\text{к}}}^{{\text{ф}}}$ – температуры термического формовосстановления; Ан, Ак – точки начала и конца обратного мартенситного превращения; Мн, Мк – температуры начала и конца прямого мартенситного превращения; σдеф, – напряжения деформирования мартенсита неупругости; σR – напряжения термомеханического возврата; ΔТЭ – интервал температур эксплуатации; ΔТд – интервал температур деформации в зоне мартенситной неупругости. Величина реактивных напряжений зависит от степени недовосстановления и жесткости противодействия. Верхняя граница температур эксплуатации для деталей из TiNi составляет Тмах = = ~280°C, которая определяется началом развития в материале процесса релаксирования, приводящего к необратимой пластичности [5].
Эти материалы, после начальной деформации способны самопроизвольно принимать исходную форму, которой они обладали до деформации, при незначительном нагреве, например, на 2 ± 50°С в зависимости от вида превращений и состава сплава [6, 7].
Высокие характеристики параметров сплавов с ЭПФ на основе TiNi, такие как степень восстановления, развиваемые усилия, величина накопленной обратимой деформации при повышенной пластичности, высокая коррозионная стойкость, определяют перспективу его широкого применения в технике. Обеспечение высоких и стабильных термомеханических характеристик никелида титана в конкретных устройствах во всем интервале температур эксплуатации требует умения варьировать параметрами ЭПФ и сверхупругости в широких пределах [8]. Научный подход к решению таких задач заключается в выяснении природы и механизмов проявления ЭПФ на основе глубоких исследований свойств материала.
Основными критериями оценки работоспособности гидро- и пневмосистем является надежность трубопроводов и их соединений [1].
Было установлено [9], что основную массу неисправностей и отказов в работе гидросистем составляют монтажные работы.
Трубопроводы в процессе эксплуатации подвергаются различным нагрузкам (статические, температурно-циклические, динамические, вибрационные и т.д.). Кроме того, они должны быть герметичны. Наиболее нагруженными являются трубопроводы в летальных аппаратах, на которые эти нагрузки действуют в комплексе [10–13].
Давление рабочей жидкости в современных гидросистемах [14] постоянно возрастает. Увеличение давления в гидросистемах вызвано стремлением уменьшить массу трубопроводов и исполнительных механизмов, т.к. с увеличением давления уменьшаются размеры силового привода и требующиеся расходы рабочей жидкости.
В конструкциях гидро- и пневмосистем летательного аппарата получили широкое распространение разъемные и неразъемные виды соединений трубопроводов. Наиболее распространены разъемные соединения по наружному конусу (ГОСТ 13954-68 – ГОСТ 13977-68) для трубопроводов из стали 12Х18Н10Т.
Разъемные соединения трубопроводов в настоящее время все в большей степени заменяют на более надежные неразъемные соединения.
Неразъемные соединения – это наиболее перспективный вид соединений (рис. 2). Неразъемные соединения трубопроводов обеспечивают не только высокую герметичность и надежность, но и обладают сравнительно низкой трудоемкостью их изготовления. В отечественной промышленности изготовление неразъемных соединений трубопроводов осуществляется в основном сваркой и пайкой (рис. 2), поэтому материалы труб подбираются с близкими по химическому составу свойствами.
Рис. 2.
Способы сварки и пайки для соединений трубопроводов: (а) – сварное встык; (б) – сварное внахлестку: (в) – паяные соединения.
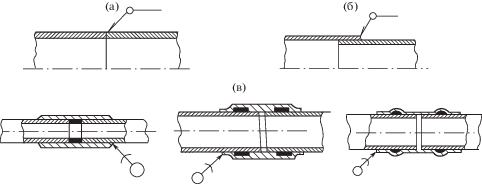
Эти соединения в настоящее время не допускают многократного демонтажа и последующего монтажа соединяемых элементов, а ремонтные работы, как правило, выполняются путем вырезки дефектного участка с заменой отдельных элементов [1].
Степень надежности, при прочих равных условиях, определяется качеством и совершенством технологии их изготовления.
Сварка – наиболее распространенный способ соединений, который осуществляется как на специализированных участках, так и на изделии.
Сварка. Известно, что в современном машиностроении, для обеспечения высокой технологичности деталей и узлов, широко применяются сварные соединения. Сварка титана, никеля и сплавов на их основе, при соблюдении специальных технологических режимов, обеспечивают достаточную прочность и надежность соединений.
Бинарное соединение никелид титана, являющееся интерметаллидом, обладает относительно невысокой температурой плавления (Тпл = ~1200°С) и легко поддается для формирования ванны расплавленного металла. Эффектами памяти формы и свойствами проявления термоупругих мартенситных превращений в основном обладает марица TiNi.
На рис. 3 представлена диаграмма соотношений Ti↔Ni в матрице, которая определяет области существования TiNi и температуры фазовых превращений. Превышение в составе сплава Ti или Ni сверх области существования TiNi, приводит к выделению фаз Ti2Ni или Ti2Ni3, которые не только загрязняют сплав, но и являются концентраторами разрушения при силовых воздействиях. Кроме того, эти соединения имеют температуры эвтектики и перетектической реакции ниже, чем температура плавления TiNi [15].
Рис. 3.
Зависимость температур мартенситного превращения от соотношения компонентов: Мн – температура начала мартенситного превращения, Ак – температура конца аустенитного превращения.
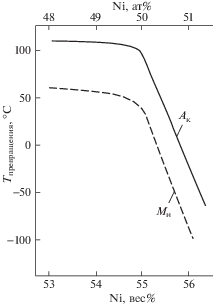
Для практической оценки свариваемости материала [16] с технологической точки зрения необходимо обеспечивать, следующие основные требования: химический состав, структура и свойства металла шва должны соответствовать основному материалу; структура и механические характеристики металла в околошовной зоне не должны отличаться; отсутствие склонности основного материала к образованию трещин.
Для исследования свариваемости сплава ТН1 применялись заготовки с температурой прямого МП + (40–60)°С в виде листов толщиной 2 мм и использовалась аргоно-дуговая (АрДС) без присадка или с присадком из того же сплава, электронно-лучевая (ЭЛС) или точечная (ТЭС) сварка.
Сварные соединения (АрДС) осуществленные по режиму I = 120 А, Vсв = 20–40 м/час показали, что сварочных трещин не наблюдается. Характер формирования шва с усадкой в центре сходно с формированием шва для тугоплавких сплавов. Усадочный подрез, как концентратор напряжений, ведет к разрушению сварного соединения.
Электронно-лучевая сварка осуществлялась в вакууме по режиму U = 30 кВ, I = 50 мА, Vсв = 40 м/час и показала возникновение трещины по всей длине шва.
При высоких температурах в вакууме Ni испаряется примерно в два раза интенсивнее, чем Ti. Данное явление приводит к тому, что сплав в зоне шва имеет повышенное содержание Ti. Изменение соотношения компонентов химического состава шва по отношению к основному материалу на 0.1% приводит к смещению температур МП примерно на 20°С. Это способствует резкому снижению температур МП шва в область низких температур (вплоть до криогенных температур) и снижению его пластичности. Локальный нагрев приводит к выделению вторичных фаз Ti2Ni обладающих низкой пластичностью не только в сварном шве, но и околошовной зоне [17]. Применение высокотемпературных методов сварки, особенно в вакууме, приводит к резкому изменению характеристик фазового состава материала в зоне сварного шва от мартенситного к аустенитному, что при эксплуатации сплавов с ЭПФ нецелесообразно.
Для получения надежных видов соединений, с образованием ванны сварного шва, необходимо использовать механические методы. Соединение отдельных элементов из материалов для никелида титана в настоящее время нет.
Точечная и роликовая сварка применяется для соединения деталей толщиной от 0.3 + 0.3 до 7.0 + 7.0 мм. Свариваемость никелида титана методом ТЭС определяется технологически – на отрыв. Вследствие низкой тепло- и электропроводности никелида титана, для сварки используются режимы, как в случае с титановым и жаропрочным материалами. Происходящее в процессе ТЭС плотное сжатие между собой свариваемых деталей и кратковременность теплового воздействия препятствует доступу воздуха в зону сварки, следовательно, не требует специальной защиты [18].
Установлено, что оптимальными режимами для листовых полуфабрикатов толщиной 2.0 + 2.0 являются: I = 10 мкА; Р = 375 кг; τ = 0.04 сек.
При испытаниях на отрыв разрушения наблюдаются по основному материалу, а не по точке сварки.
На основании контроля микрошлифов в зоне шва или околошовной зоне, значительных изменений температуры фазовых превращений, по образованию термического мартенсита при охлаждении, не установлено. В связи с кратковременностью процесса сварки и замкнутостью объема при ТЭС, процессов преимущественного испарения одного из элементов, приводящего к изменению соотношений компонентов состава матрицы TiNi не происходит. Термомеханические характеристики материала шва, по сравнению с основным материалом аналогичны, значительных выделений вторичных фаз (TiNi2 и Ti2Ni3), не наблюдается.
Пайка. Пайка осуществляется токами высокой частоты как непосредственно на изделии, так и на специализированных участках.
На основании диаграммы состояния Ti ↔ Ni (рис. 3) между сплавом TiNi и титаном находится интерметаллидное соединение Ti2Ni, имеющее с β-твердым раствором титана эвтектику с температурой 955°С. Соединение Ti2Ni имеет перетектическую реакцию при 1015°C.
Наиболее подходящим припоем для пайки никелида титана между собой, а также с титаном и титановыми сплавами является припой на титановой основе с температурой плавления 910–920°С ВПр16 (Zr – 0.3%; Cu – 23%; Ni – 9%; ост. – Ti).
Пайка образцов из TiNi, а также с образцами из титановых сплавов ВТ3-1, ВТ6С, ВТ15 и ВТ20 проводилась в вакууме 10–4 тор припоем ВПр16. Перед пайкой поверхности подвергаются процедуре зачистки и травления.
В ходе исследования установлено, что применение высокотемпературных методов сварки, особенно в вакууме приводит к резкому изменению характеристик фазового состава материала в зоне сварного шва от мартенситного к аустенитному. Что при эксплуатации сплавов с ЭПФ нецелесообразно.
Формирование паяных соединений проходит удовлетворительно.
Выводы. При конструировании сварных или паяных соединений деталей в которых используются материалы обладающие ЭПФ, необходимо учитывать следующее обстоятельство. Сплав является “живым” материалом, в котором при МП генерируются не только значительные напряжения, но и перемещения связанные с обратимостью деформации в пределах до 8%. При МП смещение поверхности, исследуемого материала, относительно конструкционного, допускающего деформацию не более 0.5% приводит к разрушениям из-за несовместимости значительных перемещений на поверхности раздела.
Надежное соединение элементов из конструкционных материалов и сплавов с ЭПФ может быть обеспечено механическим способом или созданием условий предотвращающих мартенситные превращения в зоне контакта.
Список литературы
Батурин А.Т. Детали машин. М.: Машиностроение, 1958. 423 с.
Хасьянова Д.У. Технологическое обеспечение качества изготовления муфт ТМС и сборки трубопроводов. Дис. … канд. наук. МГУПИ, Москва, 2012. 115 с.
Лотков А.И. Фазовые превращения в системе вблизи эквиатомного состава. Сверхупругость, эффект памяти формы и их применение в новой технике. Тез. докл. всесоюз. науч. конф. Томск, изд-во Том. ун-та, 1985. С. 87.
Шишкин С.В., Махутов Н.А. Расчет и проектирование силовых конструкций на сплавах с эффектом памяти формы // Регулярная и хаотическая динамика. М.: НИЦ, 2007. 412 с.
Hust J.G., Weitzel D.H., Rowell R.L. Thermal conductivity, electrical resistivity and Thermopower of aerospace alloys from 4 to 300 K // J. Nat. But. Standards 75 A. № 4. P. 269.
Хисаси Токэути, Тосио Хомма, Кэндзо Судзуки. Сборник докладов на 58 симпозиуме общества металлистов Японии, 1966. 46 с.
Хисаси Токэути, Тосио Хомма, Кэндзо Судзуки, Сигэру Ямадзаки. Сборник докладов на 60 симпозиуме общества металлистов Японии, 1967. 197 с.
Khasyanova D.U. Conditions for Operational Reliability and Tightness of Thermomechanical Joining Pipelines Using Couplers // J. Mach. Manuf. Reliab. 2020. V. 49. № 2. https://doi.org/10.3103/S1052618820020089
Сапожников В.М., Лагосюк Г.С. Прочность и испытания трубопроводов гидросистем самолетов и вертолетов. М.: Машиностроение, 1973. 274 с.
Евстигнеев М.И., Морозов И.А., Подзей А.В. и др. Изготовление основных деталей авиадвигателей. М.: Машиностроение, 1972. 166 с.
Запунный А.И. Контроль герметичности конструкций. Киев: Техника, 1976. 152 с.
Камерштейн А.Г., Рождественский В.В., Ручинский М.Н. Расчет трубопроводов на прочность. М.: Гостехиздат, 1969. 440 с.
Поздней А.В. Изготовление основных деталей авиадвигателей. М.: Машиностроение, 1972. 152 с.
Сапожников В.М. Монтаж и испытания гидравлических и пневматических систем ЛА. М.: Машиностроение, 1979. 158 с.
Корнилов И.И., Белоусов О.К., Качур Е.В. Никелид титана и другие сплавы с памятью формы. М.: Наука, 1977. 178 с.
Рыкалин Н.Н. Расчеты тепловых процессов при сварке. “Справочник по сварке”. Машгиз, 1961. Т. 1. Гл. 11.
Шоршоров М.Х., Назаров Г.В. Сварка титановых сплавов. Справочник “Конструкционные материалы”. “Советская энциклопедия”, 1963. Т. 3.
Поплавко В.М. и др. Сварка титановых сплавов. Сб. “Сварка цветных металлов и сплавов”, Оборонгиз, 1961.
Дополнительные материалы отсутствуют.
Инструменты
Проблемы машиностроения и надежности машин