Проблемы машиностроения и надежности машин, 2021, № 6, стр. 79-87
Управление ресурсом работы пильного блока с плоским вращательно-поступательным движением пильных полотен
М. А. Блохин 1, *, Э. Ю. Грачёва 1, И. И. Павлова 1
1 Московский государственный технический университет им. Н.Э. Баумана
Москва, Россия
* E-mail: hornet10@yandex.ru
Поступила в редакцию 01.04.2021
После доработки 07.06.2021
Принята к публикации 24.08.2021
Аннотация
Статья посвящена проектированию и инженерному расчету надежности и долговечности (выносливости) нового вида распиловочного оборудования с плоским вращательно-поступательным движением пильных полотен. Представленное принципиальное конструкторско-технологическое решение является особенно актуальным при переработке древесины (заготовок) в местах временного складирования кругляка или непосредственно на лесосеке. В статье представлен современный инженерный подход с использованием программного обеспечения Solid Works, ANSYS, NX Siemens, а также конструкторские решения вариантов основных деталей пильного блока с расчетом их долговечности и надежности.
В настоящее время существует несколько принципиальных схем оборудования, предназначенного для распиловки бревен или брусьев на доски, паркет, ламель. Это – лесорамы различных модификаций с возвратно-поступательным движением пильной рамки; круглопильное оборудование с дисковыми пилами; ленточнопильное оборудование с пильным полотном в виде замкнутой ленты. Они характеризуются как отдельными преимуществами друг перед другом, так и присущими им недостатками.
В процессе эволюции и совершенствования лесопильного оборудования разработчиками и изобретателями рассматривалась схема, так называемой “коленчатой” пилы [1–9], поскольку концы полотен предполагалось размещать на шейках коленчатых валов. Пространственное расположение шести шеек коленчатого вала (рис. 1) отличалось углом 60° последовательно и относительно друг друга, что предполагало начало пиления каждым полотном сразу же после выхода предыдущего из рабочего процесса.
Рис. 1.
Принципиальная схема многопильного блока с плоским вращательно-поступательным движением пильных полотен.
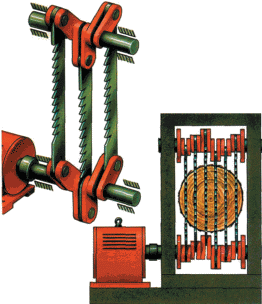
При этом обеспечивался динамический баланс всего многопильного блока (далее – блок) с отсутствием инерционных сил в его опорных узлах, плавностью самого процесса пиления. При этом сила резания, в любой момент времени, была направлена вниз, обеспечивая прижим заготовки к подающему вальцу.
Представленная схема (рис. 1) привлекала компактностью, малой металлоемкостью, отсутствием фундамента, а также короткими полотнами, обладающими повышенной жесткостью (устойчивостью) в плоскости их наибольшей жесткости [10, 11].
Главным сборочным узлом оборудования является многопильный блок, состоящий из шести многопильных узлов (модулей), обеспечивающих его динамический баланс без дополнительных корректирующих элементов. При этом количество и номенклатура выпускаемого пиломатериала соответствует принятым стандартам. Повышенная жесткость полотен позволяет получать пиломатериал с малой разнотолщинностью, что обеспечивается отрицательной обратной связью сил подачи узла резания и сил противодействия пилению. При этом процесс распиловки характеризуется малым энергопотреблением, поскольку в любой момент времени распиловка ведется одним пильным узлом (пильным модулем), каждый из которых может быть снабжен одним, двумя или тремя полотнами. Батарейный способ (метод) получения пиломатериала практически исключает его крыловатость, т.е. его продольное спиральное искривление. Упомянутый положительный эффект является результатом практического отсутствия внутренних напряжений в полученном пиломатериале.
Специалисты по деревопереработке древесины смогут найти еще достаточно много позитивных отличительных черт и свойств разработанного оборудования при сравнении с оборудованием аналогичного функционального назначения [12–17].
По совокупности технико-экономических показателей созданный станок, в котором устанавливается указанный многопильный блок, стоит первым в линейке лесоперерабатывающего оборудования аналогичного функционального назначения.
Характер и особенности плоского вращательно-поступательного движения полотен в составе многопильного модуля выдвигают определенные требования к его габаритно-массовым характеристикам, что, в свою очередь, вызывает необходимость проведения инженерного расчета, обеспечивающего повышенную производительность оборудования, гарантированную надежность и долговечность (ресурс), а также безопасность его эксплуатации.
Рабочая схема конструкции блока (рис. 2) явилась результатом работ по изучению динамических характеристик полотен, резонансов собственных и параметрических колебаний самих пильных модулей, особенностей проектирования подшипниковых узлов многопильных модулей (далее – модулей), а также результатом решения других сопрягаемых задач [18–25].
Конструкция блока (рис. 2) имитирует принципиальную схему “коленчатой” пилы, где 1 – пильные полотна, 2 – верхний шарнирный узел с элементами подвижной фиксации 3 пильного полотна и корректирующей массой, 3 – упругие элементы узла подвижной фиксации, 4 – нижний шарнирный узел с элементами крепления пильного полотна и корректирующей массой, 5 – боковая стойка, 6 – шкив нижнего вала, 7 – верхний вал, 8 – нижний вал, 9 – подшипниковые опоры валов, 10 – эксцентрик, 11 – болт регулировочный, 12 – элементы фиксации эксцентриков на валах 7, 8.
Модули, состоящие из основных деталей 1, 2, 3, 4 устанавливаются на шлицевые валы 7, 8, которые своими концами входят в подшипниковые опоры 9. Натяжение полотен осуществляется в результате подъема верхнего вала. Верхний вал вместе с верхними шарнирами модулей поднимается болтами 11, расположенными на стойках 5, обеспечивая необходимое усилие натяжения Fн полотен. Стойки 5 крепятся к основанию (не показано).
Перепозиционирование модулей на валах блока осуществляется винтовыми механизмами 12 с их фиксацией относительно подшипниковых опор. При этом между эксцентриками модулей устанавливаются распорные кольца (не показано) необходимого размера.
Подача крутящего момента от шкива 6 нижнему валу также обеспечивает вращение верхнего вала с частотой ω, поскольку осуществляется передача крутящего момента от нижнего вала полотнами модулей, отличающихся друг от друга на 60° по их угловому расположению на валах.
Общая величина силы натяжения трех полотен Fн одного модуля находится в пределах 750–2000 Н, а их суммарная сила резания Fр = 400–700 Н. Разброс величины сил резания объясняется различной твердостью обрабатываемого материала, количеством установленных в модуле полотен, выбранной величиной подачи полотен на один оборот, связанной с величиной шероховатости обработанной поверхности, и иными особенностями.
Определение предела выносливости. Известно, что прочность (выносливость) при напряжениях, переменных во времени, существенно зависит от числа циклов, но мало зависит от частоты изменения напряжений во времени [25].
Расчет напряженно-деформированного состояния нижнего вала (рис. 3), как самого нагруженного, проводился эмпирически и с использованием программных комплексов ANSYS и NX Siemens.
Рис. 3.
Расчетная схема нагрузки нижнего вала пильного блока, закрепленного по шарнирной схеме. Эпюры силовых факторов: Fн – максимальная сила натяжения полотен; Мкр – крутящий момент на шкиве нижнего вала; Fп – сила натяжения ременной передачи.
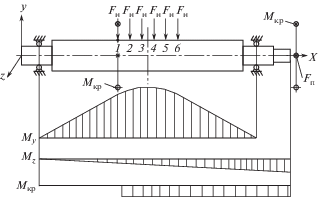
По результатам расчетов определялись значения эквивалентных напряжений в зонах максимальных моментов сил. В качестве целевой функции максимизировалась выносливость вала (число циклов), определяемая по стандартным формулам расчета на выносливость. При этом в точках 1 и 6 углы прогибов вала, под действием сил натяжения полотен Fн, выходили за пределы допустимых величин и тогда разворот шарниров в плоскости валов приводил к появлению колебаний полотен в плоскости их наименьшей жесткости.
С целью снижения прогибов валов и повышения предела их выносливости была предложена схема закрепления концов валов пильного блока, представленная на рис. 4.
Рис. 4.
Расчетная схема нагрузки нижнего вала пильного блока с концовиками, закрепленными по схеме заделки. Эпюры силовых факторов: Fн – максимальная сила натяжения полотен, Мкр – крутящий момент на шкиве нижнего вала; Fп – сила натяжения ременной передачи.
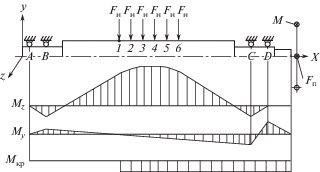
Управление величиной выносливости. В качестве управляющих параметров выносливости нижнего вала блока были приняты варьируемые расстояния между внутренними опорными подшипниками в точках В и С (рис. 4), где “а” – расстояние между опорами В и С.
Результаты расчета представлены в табл. 1 и на рис. 5.
Таблица 1.
Зависимость предела выносливости N вала от изменения расстояния между внутренними опорными подшипниками (рис. 4)
Вариант | Расстояние между В и C, мм | Расстояние между А и В, мм | RA, H | RB, H | RC, H | RD, H | Ресурс (N – число циклов) |
---|---|---|---|---|---|---|---|
1 | 646 | 132 | 6731 | 12 731 | 12 737 | 6803 | 9.163 × 107 |
2 | 596 | 132 | 4664 | 10 665 | 10 670 | 4755 | 1.722 × 109 |
3 | 546 | 132 | 3292 | 9293 | 9297 | 3407 | 4.75 × 1010 |
Рис. 5.
Зависимости ресурса нижнего вала от изменения расстояния между точками В и С опорных узлов нижнего вала пильного блока.
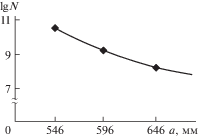
Отметим, что прогибы валов в точках 2 и 5, выполненных по схеме на рис. 4, в 2.5–3 раза меньше прогибов валов, выполненных по схеме на рис. 3. Расчетный диаметр вала составляет величину 55 мм, а диаметр концовиков равен 45 мм.
Параметры вала (рис. 4), приняты и использованы в конструкции модернизированного блока, представленного на рис. 6.
Необходимо отметить, что условный предел выносливости определяют, как значение максимального напряжения, которое может выдержать образец при заданном заранее количестве циклов. Для легированных сталей N = 108 [25].
На рис. 6 представлен блок, который по своим характеристикам позволяет вести распиловку заготовок с максимальными размерами пиломатериала в соответствии с ГОСТ 24454-80, где ширина доски не превышает 275 мм.
Дополнительным фактором повышения выносливости валов пильного блока является снижение силы натяжения полотен Fн в самом модуле (рис. 7), что автоматически ведет к снижению напряжений в обоих валах. При этом сохраняется условие устойчивости плоской формы полотна [25], зависящей от изгибающего момента сил, действующего во фронтальной плоскости пильного полотна (рис. 7)
где Z – величина, которая определяется положением многопильного модуля в пространстве.Рис. 7.
Многопильный модуль с плоским вращательно-поступательным движением пильных полотен: 1 – верхний корпус, 2 – эксцентрик, 3 – подшипник, 4 – пильное полотно, 5 – линия межзубовых впадин, 6 – линия натяжения полотна, 7 – крепеж, 8 – нижний корпус, 9 – нижний вал, 10 – пальцы, 11 – упругие элементы, 12 – верхний вал, 13 – заготовка, ${v}$ – скорость подачи заготовки в зону резания; (a) – режим холостого хода; (б) – режим резания; (в) – вид сбоку.
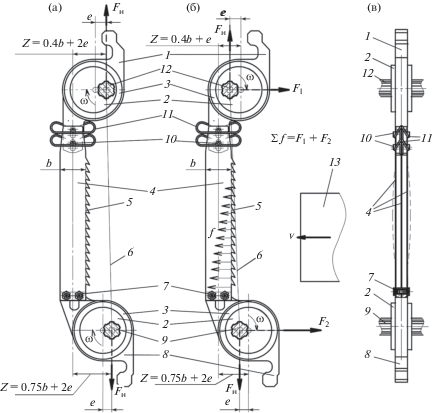
Границу потери устойчивости полотна при его внецентренном растяжении можно найти из соотношения
где Е – модуль упругости, при этом G = 0.5Е(1 + μ), где μ = 0.3; GJ2= = [0.5Е(1 + + μ)]βh3b – жесткость на кручение, где β = b/h = 0.33 (b и h – ширина и толщина полотна); EJ1= $E\left[ {{{h}^{3}}b\frac{1}{{12}}} \right]$ – жесткость полотна на изгиб в направлении, перпендикулярном к плоскости внешних моментов; $\ell $ – длина полотна.Устойчивый процесс резания (рис. 7б) достигается созданием отрицательной обратной связи суммарных сил подачи $\sum {{{F}_{{1,2}}}} $ и сил противодействия $\sum f $, когда силы противодействия располагаются за линией 6, соединяющей точки приложения сил подачи F1 и F2, т.е. оси верхнего 12 и нижнего 9 валов.
Отрицательная обратная связь делает систему самокорректирующейся в случае, когда внецентренное растяжение полотен Z = 0.5b + hз увеличено на эксцентриситет вращения е модуля, что соответствует расстоянию между осью вала 12 и осью подшипника 3, установленного на эксцентрике 2, а также расстоянию между осью вала 9 и осью соответствующего подшипника 3. Таким образом, внецентренное растяжение полотен Z ≥ 0.5b + hз + е (рис. 7б) обеспечивает устойчивый процесс с наименьшей разнотолщинностью получаемого пиломатериала.
Однако сохранение формы полотна в плоскости его наибольшей жесткости (рис. 7в) также определяется зависимостью, возникающей в положении холостого хода многопильного модуля (рис. 7а) при Z = 0.5b + h + 2е.
Принимая во внимание специфику процесса пиления и выноса продуктов резания из пропила необходимо учесть особенности внецентренного растяжения пильных полотен. Продукты резания в межзубовых впадинах при “вращении” пильного полотна перемещаются от верхних впадин в нижние. Наибольшее их количество сосредотачивается в межзубовых впадинах нижней части полотен, что повышает сопротивление продвижению полотна в рабочем режиме.
Для сохранения частоты собственных колебаний полотен (резонанса), обусловленных их внецентренным растяжением, целесообразно уменьшить величину их внецентренного растяжения в верхней части и увеличить в нижней [26]. Внецентренные растяжения верхней Zв и нижней Zн частей полотен определяются выражениями: Zв = 4b + + hз + е и Zн = 0.75b + hз + 2е, соответственно, с учетом распределенных сил противодействия процессу пиления вдоль полотна.
Учитывая соотношения (1) и (2) возникает возможность определения минимальной силы Fmin внецентренного натяжения пильного полотна
(3)
${{F}_{{{\text{min}}}}} = \frac{\pi }{{\ell (0.5b + {{h}_{{\text{з}}}} + 2e)}}\sqrt {E{{J}_{1}}G{{J}_{2}}} .$Варьируя параметрами пильного полотна (b, h, $\ell $, hз, – ширина, толщина, длина полотна, высота зуба полотна соответственно) достигается приемлемое значение величины натяжения полотен. При этом учитывается и радиус вращения любой точки модуля: е – эксцентриситет вращения.
Результатом настоящего исследования является факт возможности варьировать величиной выносливости валов схематично аналогичных конструкций с концовиками, закрепленными по схеме заделки (рис. 6).
Величина выносливости валов, при найденном рациональном расстоянии между внутренними опорными подшипниками валов пильной рамки, для представленной конструкции, увеличилась в 30 раз по сравнению с традиционной схемой закрепления концовиков валов по шарнирной схеме.
Предложенное решение снижения сил натяжения полотен обеспечивает одновременное повышение ресурса (выносливости) модуля (рис. 7) на 25–35% с соответствующим увеличением ресурса подшипников модулей и подшипников опорных узлов блока.
Конструктивные особенности усовершенствованного блока [26] позволяют вести распиловку заготовок в автоматизированном режиме перепозиционирования пильных модулей на его валах с организацией выпуска пиломатериала заданной номенклатуры без предварительной сортировки заготовок по диаметрам (характерным размерам).
Уменьшение силы натяжения полотна: 1) снижает в 2–3 раза энергопотребление модуля при его холостом “вращении”; 2) снижает общую потребляемую мощность блока на 15–25%.
Список литературы
Андрианов В.В., Журиков В.Ф., Кучкина Н.П., Матвеева М.В. СССР Свидетельство на изобретение 288278, В27В 3/10, 1969.
John W. McGehee. США Патент 3929048, reciprocating gang saw, В27В 3/00. 1975.
Бартошевич Ю.К. СССР Свидетельство на изобретение 146019, В27В 15/04, 1962.
Буйнов Р.И. РФ Патент 1771443, В27В 3/00, 1992.
Шабалин Н.Ф. РФ Патент 2058884, В27В 3/10, 1996.
Гузиков В.А., Митюшин А.В., Страхов А.В. РФ Патент 2060873, В27В 3/00, 1996.
Huvi R., Heikki V. Финляндия Патент 3,929,048. В27В 3/00, 1975.
Акпанбетов С.Б. РФ Патент 2058884, В27В 3/26, 1993.
Фонкин В.Ф. CCCР Свидетельство на изобретение 1068283: В27В 3/12, 1982.
Белкин А.Е., Гаврюшин С.С. Расчет пластин методом конечных элементов. М.: МГТУ им. Н.Э. Баумана, 2003. 151 с.
Гаврюшин С.С., Барышникова О.О., Борискин О.Ф. Численный анализ элементов конструкций машин и приборов. М.: МГТУ им. Н.Э. Баумана, 2014. 479 с.
Гаврюшин С.С., Прокопов В.С., Блохин М.А. Разработка методики численного анализа динамических характеристик многопильного станка с круговым поступательным движением дереворежущих полотен // Вестник МГТУ. Машиностроение. 2010. № 4 (81). С. 108.
Гаврюшин С.С., Блохин М.А., Фунг В.Б. Анализ лесопильного станка с использованием виртуальной математической модели // Наука и образование. 2014. № 12. С. 128.
Фунг В.Б., Данг М.Х., Гаврюшин С.С. Разработка математической модели для процесса управления жизненным циклом многопильного станка нового типа // Наука и образование. 2017. № 2. С. 87.
Фунг В.Б. Автоматизация и управление процессом принятия решений при многокритериальном проектировании пильного блока лесопильного станка: Дис. … канд. техн. наук. М.: МГТУ им. Н.Э. Баумана. 2017. 157 с.
Прокопов В.С. Разработка методики численного анализа динамических характеристик многопильного станка с круговым поступательным движением дереворежущих полотен [Текст]: Дисс. … канд. техн. наук: М., 2013. 206 с.
Блохин М.А. Мехатроника и робототехника в лесопильном оборудовании // Вестник машиностроения. 2019. № 8. С. 33.
Phuong B.V., Gavriushin S.S., Minh D.H., Binh P.V., Duc N.V. Application of a novel model “Requirement–Object–Parameter” for design automation of complex mechanical system // Advances in Intelligent Systems and Computing. 2020. T. 1127 AISC. C. 375.
Гаврюшин С.С., Николаева А.С. Метод смены подпространства управляющих параметров и его применение к задачам синтеза нелинейных деформируемых осесимметричных тонкостенных конструкций // Известия Российской академии наук. Механика твердого тела. 2016. № 3. С. 120.
Eremeykin P.A., Zhargalova A.D., Gavriushin S.S. A software system for thin-walled parts deformation analysis // Advances in Intelligent Systems and Computing. 2018. T. 658. C. 259.
Гаврюшин С.С. Элементы управляемой упругой деформации для функциональных устройств робототехнического оборудования // Мехатроника. 2000. № 5. С. 16.
Gavriushin S.S. Nonlinear analysis of elastic thin-walled shell structures // Communications in Nonlinear Science and Numerical Simulation. 2002. T. 7. № 4. C. 223.
Еремейкин П.А., Жаргалова А.Д., Гаврюшин С.С. Расчетно-экспериментальная оценка технологических деформаций при “мягких” режимах токарной обработки тонкостенных деталей // Обработка металлов (технология, оборудование, инструменты). 2018. Т. 20. № 1. С. 22.
Galakhar A.S., Gavryushin S.S. Defining the assigned useful life of operational facilities taking into account the safe operation index // Journal of Machinery Manufacture and Reliability. 2018. V. 47. № 4. C. 345.
Валиашвили Н.В., Гаврюшин С.С. Сопротивление материалов и конструкций: учебник для академического бакалавриата. М.: Издательство Юрайт, 2017. 429 с.
Блохин М.А., Гаврюшин С.С. РФ Патент 2647274, 2016.
Дополнительные материалы отсутствуют.
Инструменты
Проблемы машиностроения и надежности машин