Проблемы машиностроения и надежности машин, 2021, № 6, стр. 88-95
Управление процессами формообразования заготовок из титановых сплавов (на примере сплава от4-1) с использованием моделирования реологии и режимов деформирования
П. А. Петров 1, Нгуен Хань Тоан 1, И. А. Бурлаков 2, Р. Ю. Сухоруков 3, *
1 Московский политехнический университет
Москва, Россия
2 Производственный комплекс “Салют” АО “ОДК”
Москва, Россия
3 Институт машиноведения им. А.А. Благонравова РАН
Москва, Россия
* E-mail: ryusukhorukov@gmail.com
Поступила в редакцию 19.07.2021
После доработки 11.08.2021
Принята к публикации 24.08.2021
Аннотация
В статье представлены результаты определения реологической модели титанового сплава ОТ4-1 путем осадки образцов со скоростями деформации $\dot {\varepsilon }$ = 10–1, 10–2 и 10–3 с–1 на воздухе при постоянной температуре в изотермических условиях в температурном интервале 20–800°С с применением эмпирической модели, предложенной Хензелем–Шпиттелем. Показана корректность найденной зависимости по результатам ее применения для моделирования программой QForm 9.0.8 процессов осадки с кручением и без кручения цилиндрических образцов из сплава ОТ4-1.
Особенности свойств титана и его сплавов определяют его широкое применение в машиностроении. Однако более широкое использование во многих отраслях промышленности сдерживается необходимостью более систематизированной информации, касающейся процессов изготовления заготовок пластической деформацией. Весьма ограничены возможности холодной деформации титановых сплавов [1]. Даже малолегированные сплавы имеют пластичность в 2–3 раза меньшую, чем нержавеющие стали. Вместе с тем даже незначительный нагрев существенно снижает сопротивление деформированию и повышает пластичность. Кроме того, титановые сплавы чувствительны к скорости деформирования. Высокие скорости заметно сокращают их деформируемость и снижают качество получаемых полуфабрикатов. Ошибки, допущенные при их горячей деформации невозможно исправить термической обработкой, т.к. титановые сплавы нельзя закалить и отпустить с кардинальной переработкой структуры и свойств [2]. Поэтому при разработке технологических процессов для назначения корректных режимов пластического формообразования необходимы реологические модели материалов, позволяющие максимально точно моделировать процессы, например, программой QForm. Настоящая статья посвящена созданию реологической модели титанового α-сплава ОТ4-1, широко применяемого для изготовления узлов и деталей, длительно работающих при температурах до 300°С.
Целью настоящей статьи является определение кривых текучести титанового сплава ОТ4-1 деформацией сжатием при комнатной и повышенных температурах, необходимых для моделирования методом конечных элементов формообразующих операций.
В процессе исследования необходимо было решить следующие задачи: 1) изготовить и осуществить осадку образцов при комнатной и повышенных температурах; 2) построить эмпирическую модель сопротивления титанового сплава ОТ4-1 деформации; 3) выполнить моделирование процесса осадки заготовок с кручением и без кручения с учетом найденной эмпирической модели; 4) осуществить осадку заготовок с кручением и без кручения из сплава ОТ4-1; 5) выполнить анализ полученных данных и осуществить корректировку кривой текучести.
Материалы и методы исследования. В качестве исследуемого материала был выбран титановый сплав ОТ4-1, химический состав которого, % (мас.): Al – 1.0–2.5; Mn – 0.7–2.0; C – 0.10; Fe – 0.30; Si – 0.15; Zr – 0.30; O2 – 0.15.
Для получения реологической модели с применением электроэрозии были изготовлены цилиндрические образцы диаметром и высотой 10 мм (рис. 1а).
Структура исходного сплава представляет собой равноосные зерна величиной 5‒10 мкм (рис. 2). Температура полиморфного превращения tпп = 930°С, температура начала и конца рекристаллизации равна 720 и 840°С соответственно [2].
Испытания провели на универсальных испытательных машинах моделей LFM250 при температуре 20°С и LFM50 при температурах 300, 400, 600 и 800°С. Испытания проводились со скоростями деформации $\dot {\varepsilon }$ = 10–1, 10–2 и 10–3 с–1 на воздухе при постоянной температуре в изотермических условиях без применения смазки. Образцы после осадки показаны на рис. 1. Скорость деформации поддерживалась постоянной за счет перемещения траверсы по рассчитанным в соответствии с формулой (1) значениям [3], которые задавались контроллеру испытательной машины.
где Si – перемещение траверсы испытательной машины; $\dot {\varepsilon }$ – скорость деформации; t – время; h0 – исходная высота образца исследуемого материала.Моделирование. Для моделирования процесса осадки с кручением был применен программный комплекс QForm 9.0.8 [4] со следующими исходными данными: обрабатываемый материал – титановый сплав ОТ4-1 с использованием найденной реологической модели; материал инструмента – сталь 5ХНМ; температура заготовки – 300°С; температура инструмента – 300°С; фактор трения – 0.8; скорость перемещения инструмента – 2 мм/сек.; угол поворота пуансона – 0 и 360°.
Обсуждение результатов. Полученные испытанием на сжатие зависимости напряжения текучести от величины и скорости деформации при различных температурах показаны на рис. 3: 1, 2, 3 – при температуре 20°С и скоростях деформаций 0.1; 0.01; 0.001 (сек–1); 4, 5, 6 – при температуре 400°С и скоростях деформаций 0.1; 0.01; 0.001 (сек–1); 7, 8, 9 – при температуре 600°С и скоростях деформаций 0.1; 0.01; 0.001 (сек–1); 10, 11, 12 – при температуре 800°С и скоростях деформаций 0.1; 0.01; 0.001 (сек–1).
При холодной осадке образцов деформация свыше ε = 0.30–0.35 приводила к трещинообразованию. Поэтому, вследствие необходимости создания реологической модели материала, зависимости “напряжение–деформация” были экстраполированы до ε = 0.5.
Полученные экспериментальные зависимости корректировались методом постановки обратной задачи [5].
При построении математической модели сопротивления сплава ОТ4-1 деформации была применена эмпирическая модель, предложенная Хензелем–Шпиттелем [6], которая устанавливает связь между напряжением текучести и термомеханическими параметрами
(2)
${{\sigma }_{i}} = A\exp \left( {{{m}_{1}}T} \right){{T}^{{{{m}_{9}}}}}\varepsilon _{i}^{{{{m}_{2}}}}\exp \left( {\frac{{{{m}_{4}}}}{{{{\varepsilon }_{i}}}}} \right){{\left( {1 + {{\varepsilon }_{i}}} \right)}^{{{{m}_{5}}T}}}\exp \left( {{{m}_{7}}{{\varepsilon }_{i}}} \right)\dot {\varepsilon }_{i}^{{{{m}_{3}}}}\dot {\varepsilon }_{i}^{{{{m}_{8}}T}},$Неизвестные коэффициенты модели находили методом Левенберга–Маркардта [7] с применением программы MatLab.
Оптимизация для нахождения неизвестных коэффициентов модели выполнялась с применением модифицированного метода наименьших квадратов – метода Левенберга–Маркардта [7] – в программе MatLab.
Найденные коэффициенты для температурных интервалов 20–400°С и 600–800°С приведены в табл. 1 и в виде эмпирических моделей (рис. 4).
Таблица 1.
Коэффициенты модели Хензеля–Шпиттеля для титанового сплава ОТ4-1
Тип деформации | A | m1 | m2 | m3 | m4 | m5 | m7 | m8 | m9 |
---|---|---|---|---|---|---|---|---|---|
20 и 400°С | 8.0995 | –0.0171 | 0.2039 | 0.0316 | –0.0088 | –0.0048 | 0.6978 | –0.0007 | 1.6027 |
600 и 800°С | 10.0104 | –0.0004 | –0.2874 | –0.5733 | –0.0625 | –0.0035 | 1.9078 | 0.0011 | 0.5600 |
Рис. 4.
Сравнение экспериментальных и расчетных напряжений текучести при осадке образцов с различными скоростями деформации при различных температурах: I – 20°С ; II – 400°С; III – 600°С; IV – 800°С градусов (- - - данные эксперимента; $\rlap{--} $ расчетная кривая (2)).
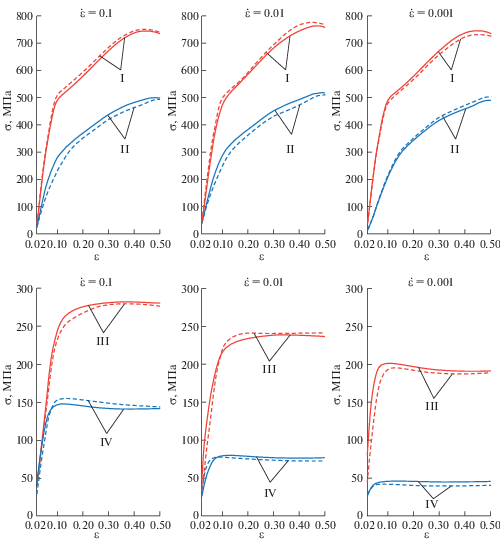
Итоговая зависимость для холодной и теплой осадки для температурного интервала 20–800°С в графическом виде показана на рис. 4. Сравнение экспериментальных и расчетных кривых показывает, что средняя ошибка не превышает 5%.
Корректность найденной реологической модели сплава ОТ4-1 была проверена путем моделирования двухступенчатой осадки цилиндрического образца диаметром и высотой 10 мм. Первая ступень осадки до высоты 8.2 мм была осуществлена согласно методике без вращения пуансона, а вторая – с вращением. Результаты моделирования и эксперимента представлены на рис. 5. В обоих случаях диаметр 14 мм и высота 5.4 мм практически совпадают, что подтверждает адекватность найденной модели исследуемого сплава.
Рис. 5.
Результаты моделирования и испытания осадки с кручением титановой заготовки при температуре 800°С.
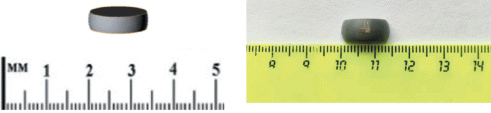
Анализ структур показывает, что наибольшее влияние на их изменение оказывает температура. Деформация на величину ε = 0.342–0.386 при комнатной температуре со скоростями $\dot {\varepsilon }$ = 0.001, 0.01 и 0.1 формирует практически одинаковую несколько измельченную микроструктуру, характеризующуюся удлиненными зернами. В результате зависимости напряжения от деформации для различных скоростей практически совпадают. Аналогичная картина наблюдается при осадке образцов с нагревом заготовок до 400°С. Изотермическая осадка при температуре 600°С приводит к существенным изменениям структуры. На границе зерен выделяются дисперсные частицы диаметром 1–2 мкм, количество которых увеличивается со снижением скорости. Это облегчает протекание деформации, что отражается на характере кривой “напряжение–деформация” (рис. 3). При температуре образцов 800°С начинают протекать процессы, связанные с рекристаллизацией, дисперсные частицы на границах зерен увеличиваются в размерах и напряжение течения резко падает, причем возрастает роль скорости деформации. Сочетание осевой деформации с кручением позволяет существенно снизить нагрузку на инструмент и повышает однородность ультрамелкозернистой структуры [8–10]. Выбор температурно-скоростного режима деформирования обеспечивает благоприятные условия для формоизменения исследуемого материала (табл. 2, образцы 10, 11, 12).
Таблица 2.
Влияние термомеханических режимов осадки на структуру титанового сплава ОТ4-1
№ образца | Фото образца с высотой | Температура образца, °C | Величина деформации, ε | Скорость деформации, $\dot {\varepsilon }$ | Структура, ×1000 |
---|---|---|---|---|---|
1 | ![]() |
20 | 0.357 | 0.1 | ![]() |
2 | ![]() |
20 | 0.86 | 0.01 | ![]() |
3 | ![]() |
20 | 0.342 | 0.001 | ![]() |
4 | ![]() |
400 | 0.105 | 0.1 | ![]() |
5 | ![]() |
400 | 0.105 | 0.01 | ![]() |
6 | ![]() |
400 | 0.090 | 0.001 | ![]() |
7 | ![]() |
600 | 0.431 | 0.1 | ![]() |
8 | ![]() |
600 | 0.478 | 0.01 | ![]() |
9 | ![]() |
600 | 0.580 | 0.001 | ![]() |
10 | ![]() |
800 | 0.494 | 0.1 | ![]() |
11 | ![]() |
800 | 0.544 | 0.01 | ![]() |
12 | ![]() |
800 | 0.616 | 0.001 | ![]() |
В области температур 600–800°С преимущественное влияние на формирование микроструктуры оказывает скорость деформации (табл. 2, образцы 7–12). Выбор оптимального режима изотермического деформирования заготовки при осадке с кручением упрощает управление технологией получения заготовок с ультрамелкозернистой структурой [11]. Например, при осадке образцов с деформацией около ε = 0.5 при температуре 600°С уменьшение скорости деформации на два порядка (с $\dot {\varepsilon }$ = 0.1 до 0.001 с–1) снижает напряжение текучести на 37%, а при температуре 800°С – уже на 215%.
Выводы. 1. Проведены экспериментальные работы по осадке в изотермических условиях образцов из титанового сплава ОТ4-1 при комнатной (20°С и повышенных (400, 600 и 800°С) температурах с различными ($\dot {\varepsilon }$ = 0.1; 0.01 и 0.001 с–1) скоростями деформации. 2. Получена реологическая модель титанового сплава ОТ4-1 (с использованием эмпирической модели Хензеля–Шпиттеля), которая устанавливает зависимость между напряжением текучести и термомеханическими параметрами формоизменения. 3. Использование реологической модели (формула (2), табл. 1) для моделирования процессов осадки и осадки с кручением с использованием программы QForm 9.0.8 продемонстрировало хорошую сходимость между результатами эксперимента и расчета.
Список литературы
Александров В.К., Аношкин Н.Ф. и др. Полуфабрикаты из титановых сплавов. М.: Металлургия, 1979. 512 с.
Горынин И.В., Чечулин Б.Б. Титан в машиностроении. М.: Машиностроение, 1990. 400 с.
Петров П.А., Перфилов В.И. Исследование упрочнения алюминиевого сплава АМг6 на начальном участке кривой текучести при повышенных температурах // Моделирование, программное обеспечение и наукоемкие технологии в металлургии. Труды 2-й Всероссийской научно-практической конференции / Под общей редакцией С.П. Мочалова. Новокузнецк: СибГИУ. 2006. С. 205.
Руководство пользователя системы QFORM. (в электронном виде) ООО “КванторФорм”, 2019.
Петров П.А. и др. Определение модели сопротивления деформации по найденным изотермическим кривым текучести с применением современных компьютерных программ // Заготовительные производства в машиностроении. 2013. № 8. С. 32.
Хензель А., Шпиттель Т. Расчет энергосиловых параметров в процессах обработки давлением: Справочник. М.: Металлургия, 1982. 360 с.
Marquardt D.W. An algorithm for least-squares estimation of nonlinear parameters An algorithm for least-squares estimation of nonlinear parameters // Journal of the Society for Industrial and Applied Mathematics. 1963. V. 11. № 2. P. 431.
Гейкин В.А., Бурлаков И.А., Гаврилина Л.В., Македонов А.В., Морозов В.В., Морозов С.В., Сухоруков Р.Ю., Утяшев Ф.З. Автоматизированное оборудование для формообразования осесимметричных деталей из жаропрочных сплавов методом раскатки в изотермических и сверхпластических условиях // Проблемы машиностроения и автоматизации. 2019. № 2. С. 132.
Sukhorukov R.Y. Simulation of technology for the production of axisymmetric parts for gas turbine engines made of heat resistant alloys by means of reeling under superplastic conditions // Journal of Machinery Manufacture and Reliability. 2020. V. 49. № 2. C. 150.
Сухоруков Р.Ю., Кощавцев Н.Ф., Утяшев Ф.З., Колесник А.В., Кощавцев А.Н., Гаврилина Л.В., РФ Патент 2725455, 2020.
Nagimov M.I., Mukhtarov S.K., Utyashev F.Z., Raab G.I., Sukhorukov R.Y. Constructive-technological features of a rotary drawing of geometrically complex hollow shafts for gas turbine engines // Journal of Machinery Manufacture and Reliability. 2017. V. 46. № 6. C. 596.
Дополнительные материалы отсутствуют.
Инструменты
Проблемы машиностроения и надежности машин