Проблемы машиностроения и надежности машин, 2022, № 1, стр. 68-77
Перенос материала абразивного инструмента на поверхность титанового сплава в различные периоды шлифования кругом из карбида кремния
В. А. Носенко 1, *, Н. Д. Сердюков 1, А. В. Фетисов 1
1 Волгоградский государственный технический университет
Волжский, Россия
* E-mail: vladim.nosenko2014@yandex.ru
Поступила в редакцию 08.04.2021
После доработки 11.10.2021
Принята к публикации 20.10.2021
- EDN: PUIGDX
- DOI: 10.31857/S0235711922010072
Аннотация
Морфологию и химический состав поверхности титанового сплава исследовали на различных этапах шлифования абразивным инструментом из карбида кремния на керамической связке. Установлено, что шлифование сопровождается переносом продуктов износа шлифовального круга на обработанную поверхность. Продукты, внедренные в обработанную поверхность, являются кристаллами карбида кремния и керамической связки. Интенсивность переноса оценивали по концентрации кремния. Установлено, что наибольший перенос происходит на первом этапе шлифования непосредственно после правки абразивного инструмента.
Титановые сплавы являются наиболее востребованными конструкционными металлами для изделий, работающих в экстремальных условиях эксплуатации [1, 2]. Поэтому качеству поверхности при обработке титановых сплавов на финишных операциях, в частности, при шлифовании уделяется особое внимание [3, 4].
В процессе шлифования титановый сплав налипает на вершины зерен абразивного инструмента, что увеличивает силу резания и износ инструмента. Налипание металла обусловлено высокой адгезионной активностью титана к абразивному материалу [4–6]. Из классических абразивных материалов меньшей адгезионной активностью во взаимодействии с титановыми сплавами имеет карбид кремния. Инструмент из карбида кремния по сравнению, например, с корундом обеспечивает бесприжоговое шлифование, износостойкость карбида кремния почти на порядок больше. Поэтому карбид кремния рекомендован к использованию на операциях шлифования титановых сплавов [7–9].
В наших первых работах (1983–1984 гг.) на основе результатов микрорентгеноспектрального анализа показана возможность переноса химических элементов абразивного материала на поверхность титанового сплава при шлифовании без охлаждения кругами из карбида кремния на бакелитовой связке. На основе результатов анализа предложен критерий оценки интенсивности адгезионного взаимодействия обрабатываемого материала с абразивным инструментом в условиях шлифования по содержанию химических элементов абразивного материала, перенесенных на обработанную поверхность. Дана классификация d-переходных металлов по интенсивности адгезионного взаимодействия с инструментом из карбида кремния [9–11].
Кристаллы абразивного инструмента, внедренные в обработанную поверхность, являются концентраторами напряжений, снижающие усталостную прочность материала [12, 13]. Поэтому исследованию переноса материала абразивного инструмента на обрабатываемую поверхность при шлифовании в последнее время уделяется особое внимание. Перенос абразивного материала в процессе шлифования возможен при обработке различных сталей и сплавов [14–16].
Перенос продуктов износа абразивного инструмента происходит в результате скалывания микро- и макрообъемов абразивного материала и связки, вырывания зерна из связки круга. Одним из факторов, который оказывает существенное влияние на перенос материала абразивного инструмента и шаржирование обработанной поверхности кристаллическими продуктами износа, является правка шлифовального круга. Убедительным доказательством существенного влияния правки на перенос продуктов износа абразивного инструмента является шлифование с постоянной правкой [4, 17]. Cледует ожидать, что при маятниковом шлифовании с периодической правкой перенос материала абразивного инструмента на обработанную поверхность титанового сплава в начальный период обработки будет более интенсивным.
Цель работы – исследование переноса материала абразивного инструмента на поверхность титанового сплава в различные периоды шлифования.
Методика исследований. Методика шлифования. В качестве обрабатываемого материала использовали двухфазный α + β титановый сплав марки ВТ9. Образцы для исследований получены из проката круглого профиля методом ковки с последующим двойным отжигом. Содержание β-фазы после двойного отжига около 10%. Размер α‑колоний 25–30 мкм, толщина α-пластин около 3 мкм. Окончательный размер заготовки 100 × 50 × 10 мм, в целях исключения переноса на обработанную поверхность кристаллов карбида кремния, получали шлифованием с выхаживанием алмазным инструментом. Размер обрабатываемой поверхности 100 × 10 мм, допуск по длине 60 мкм, по ширине – 20 мкм, параметр шероховатости Ra не более 0.75 мкм. Исследования проводили на станке с ЧПУ модели CHEVALIER Smart–B1224 III. Режим обработки: скорость шлифования ${v}$ = 30 м/с, скорость подачи стола станка ${{{v}}_{{\text{s}}}}$ = 12 м/мин, радиальная подача (подача на глубину) St = 0.005 мм/ход, припуск на обработку – 0.5 мм. Тип, размер и характеристика шлифовального круга согласно ГОСТ Р 52781-2007 – 1 350 × 20 × 127 64CF80L7V. Образцы из титанового сплава шлифовали с охлаждением СОЖ Волтес-151, расход жидкости – 14 л/мин. Рабочую поверхность шлифовального круга правили алмазной иглой марки 3908–0031, ГОСТ 607-80. Режим правки: ${v}$ = 30 м/с, St = 0.01 мм/ход; припуск на радиус – 0.1 мм (10 проходов); осевая подача So = 0.12 мм/об. Составляющие силы резания плоского врезного шлифования Pz и Py измеряли силоизмерительным комплексом Amti. Составляющая Pz параллельна направлению скорости подачи стола, Py – перпендикулярна.
Исследования морфологии и химического состава обработанной поверхности. Электронно-микроскопические исследования проводили на растровом электронном микроскопе Versa 3D DualBeam. Для исследования подготавливали образцы из титанового сплава ВТ9, размер обрабатываемой поверхности 10 × 8 мм. Образцы для микроскопа вырезали из основного образца с последующим шлифованием выхаживанием алмазным кругом. Непосредственно перед опытом основной образец и образцы для исследований морфологии и химического состава закрепляли в тисках и выравнивали до обеспечения полного контакта обрабатываемых поверхностей с рабочей поверхностью шлифовального круга по всей длине образца. После этого с образцов дополнительно снимали припуск 0.02 мм с последующим выхаживанием.
При проведении опыта заданную величину припуска снимали с основного образца (обрабатываемая поверхность 100 × 10 мм). Затем шлифовали образец для исследований на микроскопе. Образец 1 обрабатывали непосредственно после правки абразивного инструмента, остальные образцы 2–5 – после заданного количества проходов. Основной образец и образцы для исследования на микроскопе шлифовали на одном режиме. Припуск, снимаемый с образцов – 0.02 мм, количество проходов на образце – 4, что соответствует приведенной наработке – 0.2 мм2.
Химический состав объектов определяли методом рентгеноспектрального микроанализа. Размер площадки сканирования 800 × 1200 мкм, количество площадок на одном образце – не менее девяти, количество точечных измерений на одной площадке – 400, диаметр электронного зонда – 50 нм.
Фотографии поверхности получали во вторичных и обратно рассеянных электронах. Метод получения изображения во вторичных электронах обеспечивает наибольшее пространственное разрешение. Изображение в обратно рассеянных электронах дают информацию о распределении электронной плотности атомов и позволяют сделать качественную оценку химического состава.
Результаты исследования и обсуждение. Периоды времени, в привязке к которым исследовали морфологию и химический состав обработанной поверхности, определяли по характерным участкам работы абразивного инструмента. В общем случае за период стойкости абразивного инструмента в производственных условиях выделяют этап приработки инструмента после правки и этап стабильного (относительно стабильного) шлифования. Этап приработки во многом определяется методом правки, правящим инструментом, режимом правки и характеристикой шлифовального круга. Этап стабильной работы и его протяженность определяются требованиями к качеству обработанной поверхности. В процессе правки, в результате контакта с правящим инструментом, формируется рельеф рабочей поверхности абразивного инструмента. В процессе шлифования происходит формирование нового рельефа, отвечающего условиям взаимодействия рабочей поверхности абразивного инструмента с обрабатываемым материалом.
Одним из наиболее востребованных динамических показателей шлифования, используемых для оценки состояния процесса, является мощность или сила резания (составляющие силы резания).
Исследование составляющих силы резания. Закономерности изменения составляющих силы резания за период шлифования одинаковы. Поэтому в качестве примера на рис. 1 приведена только составляющая Py. На этапе приработки составляющая силы резания Py (вертикальная составляющая) возрастает, затем, снижается (рис. 1). Значительный рост составляющей силы резания наблюдается на 1–5 проходах.
Максимальное значение Py на пятом проходе превышает 80 Н. В интервале проходов 5–25 составляющие силы резания снижаются в среднем на 25%, на проходах 25‒37 – практически не изменяются, затем, начинают возрастать. К проходам 75–81 Py возрастает на 5–9% относительно участка стабильных сил резания. Рост силы резания свидетельствует о работе шлифовального круга в режиме преимущественного затупления. На последних 20-ти проходах составляющие силы резания изменяются незначимо. Работа абразивного инструмента осуществляется в смешанном режиме равновероятного затупления–самозатачивания. На встречной подаче Pу на 9–12% больше, чем на попутной. Возможными причинами различных значений составляющих силы резания на встречной и попутной подачах являются кинематика резания и условия транспортировки СОЖ в зону резания, зависящие от направления подачи.
Исследование морфологии обработанной поверхности. Морфологию и химический состав поверхности титанового сплава исследовали для наиболее характерных периодов работы шлифовального круга. В соответствии с рис. 1 выделены следующие проходы: 1, 5, 25, 51, 99. Морфология обработанной поверхности после прохода 1 свидетельствует о достаточно высоком адгезионном взаимодействии титанового сплава с абразивным инструментом (рис. 2а).
Рис. 2.
Морфология обработанной поверхности в различные периоды шлифования: (а) – проход 1; (б) – проход 5; (в) – проход 25.
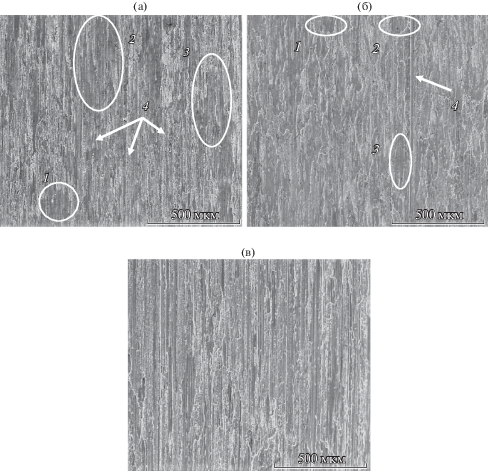
Тем не менее, на поверхности можно выделить более чистые участки, например 1, 2, 3 и др. Достаточно много царапин, оставленных относительно чистыми вершинами зерен, например, царапины, выделенные стрелками 4. Проход 5 выбран также на этапе приработки и соответствует максимальному значению силы резания, после которого наступает существенное снижение. Инструмент переходит в другой режим работы с преимущественным самозатачиванием. Состояние обработанной поверхности на проходе 5 (рис. 2б) свидетельствует о более высокой интенсивности взаимодействия пары титановый сплав–абразивный инструмент по сравнению проходом 1. Практически вся поверхность образца на проходе 5 покрыта размазанным металлом с единичными царапинами, оставленными более чистыми вершинами зерен. Более чистые участки поверхности уменьшены в размерах, например, 1–3. Редко встречаются различимые царапины, оставленные относительно чистыми вершинами зерен, например, 4.
На проходе 25 получена минимальная сила резания (рис. 1). Морфология обработанной поверхности свидетельствует о снижении интенсивности адгезионного взаимодействия металла с абразивным инструментом (рис. 2в). На поверхности возрастает число царапин, оставленных более чистыми вершинами зерен и участков обработанной поверхности без налипшего металла.
Начиная с проходов 41–43, составляющие силы резания возрастают (рис. 1), что свидетельствует о переходе инструмента из режима равновероятного затупления-самозатачивания в режим более выраженного затупления. Проход 51 находится в середине этапа затупления, где наблюдается небольшой рост силы резания. Состояния обработанных поверхностей, сформированных на проходах 51 и 25, отличаются не столь существенно. Тем не менее, можно говорить о тенденции к увеличению адгезионного взаимодействия, что сопровождается увеличением налипания металла на вершины зерен рабочей поверхности круга и более выраженным переносом металла с вершин зерен на обработанную поверхность.
После прохода 70 начинается вторая стабилизация силы резания, продолжающаяся вплоть до завершения обработки. В связи с тем, что исследования морфологии проведены для поверхностей, полученных на нечетных проходах, поверхность последнего образца также сформирована на предпоследнем 99 проходе стола при относительно стабильных значениях составляющих силы резания. Существенных отличий в морфологии поверхностей, полученных на проходах 51 и 99 не установлено.
Шаржирование обработанной поверхности продуктами износа абразивного инструмента. В процессе исследования морфологии шлифованной поверхности титанового сплава обнаружены посторонние включения, внедренные в металл, например, рис. 3а. Химический состав включений определяли методом рентгеноспектрального анализа в точке 1.
На спектрограмме получены пики линий рентгеновского характеристического излучения шести химических элементов: C, Al, Si, Zr, Mo, Ti (рис. 3б). По оси ординат дана интенсивность спектра характеристического рентгеновского излучения N, по оси абсцисс – энергия активации E. Для определения химической формулы объекта внедрения химический состав представлен в атомных процентах (рис. 3в). Наибольшую долю имеют атомы углерода и кремния, соответственно, 39.2 ± 4.5 атом. % и 39.7 ± 1.3 атом. %. С учетом доверительных интервалов средние атомные доли углерода и кремния можно считать одинаковыми (различие незначимо), что соответствует химической формуле абразивного материала шлифовального круга – SiC (карбид кремния).
Третьим элементом по содержанию атомов является титан: 2.0 ± 0.4 атом. %. В небольших количествах присутствуют атомы Al, Zr и Mo, относящихся к числу основных легирующих элементов титанового сплава ВТ9 (ГОСТ 19807-91). Присутствие титана и основных легирующих элементов на кристалле карбида кремния свидетельствует о переносе титанового сплава на поверхность абразивного материала, что в данном случае вполне обосновано.
Изображение объектов на рис. 4а получено в обратно рассеянных электронах. Коэффициент отражения электронов прямо пропорционален среднему атомному номеру матрицы, поэтому более светлые области на изображении соответствуют фазам с большим средним атомным номером. На светлом фоне титанового сплава (основной элемент титан, атомный номер 22) выделятся группа объектов темно-серого и почти черного цветов. Фотография свидетельствует о существенной разнице атомных номеров титанового сплава и продуктов внедрения, состоящих из химических элементов с меньшим атомным номером.
Рис. 4.
Внедренный фрагмент связки шлифовального круга (а), спектрограмма (б) и диаграммы химических составов в точках 1 (в) и 2 (г).
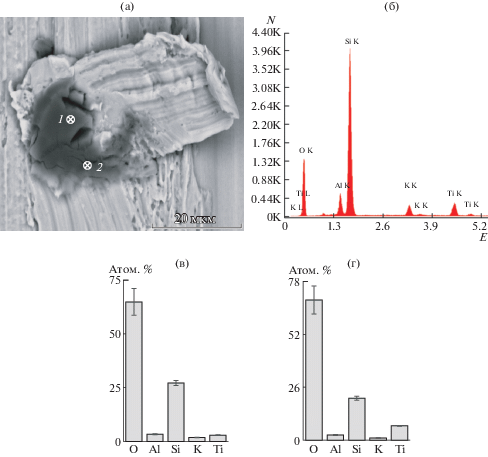
Основными продуктами износа рассматриваемого абразивного инструмента являются карбид кремния, керамическая связка и их сочетание. Атомные номера химических элементов карбида кремния: Si – 14 и С – 6; средний атомный номер – 10. Атомные номера основных химических элементов керамической связки К10: O – 8; Si – 14; Al – 13; K – 19. Средний атомный номер связки с учетом атомной доли основных химических элементов – 11. Темный цвет объектов внедрения согласуется со средними атомными номерами предполагаемых объектов внедрения (рис. 4а).
Химический состав объектов определяли в точках 1 и 2. Спектрограммы свидетельствуют о наличии в составе объектов кислорода, кремния, алюминия и калия (на рис. 4б в качестве примера приведена одна спектрограмма). Концентрация атомов O, Si и K в точках 1 и 2 соответствует их содержанию в связке. В табл. 1 приведен химический состав по основным химическим элементам компонентов связки [18], представленный в атомных долях.
Таблица 1.
Химический состав связки марки К10 (фрагмент), Атом. %
O | Si | Al | K | B | Na | Остальные |
---|---|---|---|---|---|---|
56.2–68.5 | 20.4–22.2 | 6.2–10.0 | 2.0–3.8 | 1.8–2.8 | 1.2–2.2 | 1.1–1.5 |
Количественная оценка интенсивности переноса материала абразивного инструмента на обработанную поверхность. Учитывая возможность влияния переноса продуктов износа абразивного инструмента на свойства поверхности титанового сплава в результате различных форм взаимодействия (адгезионное, химическое, диффузионное, механическое), дана оценка суммарному переносу. Суммарный перенос оценивали по содержанию наиболее значимого и удобного с методической точки зрения химического элемента. При шлифовании инструментом из SiC в качестве такого элемента целесообразно использовать кремний [11, 17]. Массовая доля атомов кремния в абразивном материале (карбид кремния) около 70%, в связке абразивного инструмента – около 28%. В титановом сплаве массовая доля кремния не более 0.35% (ГОСТ 19807-91).
Массовую долю атомов кремния на обработанной поверхности определяли в различные периоды шлифования в зависимости от числа проходов (рис. 5). Наибольшая концентрация кремния получена на первом проходе – 1.3 масс. %, по мере увеличения числа проходов стола массовая доля атомов кремния снижается. В диапазоне проходов 1–5 концентрация снизилась в 1.8 раза, от 5 к 25 проходу – еще на 25%. Массовые доли кремния на 25 и 51 проходах отличаются незначимо. Незначимо различие средних концентраций массовых долей кремния на 51 и 99 проходах.
Основная причина наиболее существенного роста массовой доли кремния на первом проходе обусловлена влиянием правки шлифовального круга. При механическом воздействии алмазной иглы на вершины зерен шлифовального круга происходит скалывание части кристалла карбида кремния. В оставшейся части возможно образование трещин, снижающих прочность абразивного материала. Образование трещин возможно и в материале связки, соединяющей зерно с абразивным инструментом. При последующем контакте такого зерна с обрабатываемым материалом происходит скалывание поврежденных фрагментов кристаллов абразивного инструмента и связки, или вырывание зерна из связки. Подобная закономерность наблюдается на операции глубинного шлифования с непрерывной правкой шлифовального круга алмазным роликом [4, 17]. Сколовшиеся части абразивных зерен или вырванные зерна внедряются в обрабатываемую поверхность заготовки. В результате контакта отделившегося абразивного материала и связки с другими вершинами зерен шлифовального круга возможно вдавливание кристаллов в обрабатываемый металл и дополнительное их дробление.
После начального этапа приработки инструмента, на котором происходит отделение поврежденных зерен, перенос материала абразивного инструмента снижается, достигая минимальных значений на этапе относительно стабильной работы абразивного инструмента в режиме затупления или частичного самозатачивания. Минимальная концентрация кремния в рассмотренном примере на 30% выше максимальной концентрации, установленной ГОСТ 19807-91.
Учитывая, что кристаллы абразивного материала и стекловидной связки, внедренные в обработанную поверхность, являются концентраторами напряжений, снижающими усталостную прочность материала, особенно, при эксплуатации изделий в условиях знакопеременных нагрузок [12], результаты исследований необходимо учитывать при разработке технологического процесса шлифования ответственных деталей из титановых сплавов.
Выводы. 1. Морфология обработанной поверхности после первого прохода свидетельствует об интенсивном адгезионном взаимодействии титанового сплава с абразивным инструментом. На проходе 5 при максимальном значении составляющих силы резания интенсивность адгезионного взаимодействия возрастает. На проходе 25, где составляющие силы резания по сравнению с проходом 5 снижаются на 25%, и инструмент начинает работать в режиме равновероятного затупления–самозатачивания, интенсивность адгезионного взаимодействия титанового сплава с абразивным инструментом снижается. Увеличение составляющих силы резания на 5–9% в интервале до 80 прохода и последующая вторая стабилизация силы резания не оказали значимого влияния на морфологию обработанной поверхности. 2. На поверхности титанового сплава после шлифования кругом из карбида кремния на керамической связке обнаружены посторонние включения. Методом точечного рентгеноспектрального анализа установлено, что посторонние включения являются продуктами износа абразивного инструмента – кристаллами карбида кремния и керамической связкой. Продукты износа абразивного инструмента частично или полностью вдавлены в обработанную поверхность. 3. Наибольший перенос материала абразивного инструмента происходит непосредственно после правки на первом проходе. Средняя массовая доля атомов кремния достигает 1.3%. На проходе 5, где сила резания максимальна, содержание кремния снижается почти в 1.8 раза, на проходе 25 – еще на 25%. Концентрации кремния на последующих проходах не отличаются от концентрации, полученной на 25-м проходе.
Список литературы
Каширин В.В., Бурханова А.А., Филатов А.А. Опыт и перспективы применения титановых сплавов в инновационных разработках ОАО “ОКБ Сухого” // Титан. 2012. № 1 (35). С. 42.
Gialanella S., Malandruccolo A. Aerospace Alloys. Topics in Mining, Metallurgy and Materials Engineering. Cham, Switzerland, 2020. 570 p.
Клауч Д.Н., Овсеенко А.Н., Овумян Г.Г. и др. Технологические методы повышения качества изготовления и ресурса работы турбинных лопаток // Вестник МГТУ им. Г.И. Носова. Магнитогорск. 2008. № 4. С. 49.
Носенко С.В., Носенко В.А., Кременецкий Л.Л. Влияние правки абразивного инструмента на состояние рельефа обработанной поверхности титанового сплава при встречном глубинном шлифовании // Вестник машиностроения. 2014. № 7. С. 64.
Garbacz H., Wieciński P., Kuczyńska D., Kubacka D., Kurzydłowski K.J. The effect of grain size on the surface properties of titanium grade 2 after different treatments // Surface and Coatings Technology. 2018. V. 335. P. 13.
Zhao T., Yaoyao S., Laakso S., Jinming Z. Investigation of the Effect of Grinding Parameters on Surface Quality in Grinding of TC4 Titanium Alloy // Procedia Manufacturing. 2017. V. 11. P. 2131.
Справочник технолога / Под общ. ред. А.Г. Суслова. М.: Инновационное машиностроение, 2019. 800 с.
Biao Z., Wenfeng D., Yi Z., Honghua S., Jiuhua X. Effect of grain wear on material removal behaviour during grinding of Ti-6Al-4V titanium alloy with single aggregated cBN grain // Ceramics International. 2019. V. 45. P. 14842.
Klocke F., Soo S., Karpuschewski B.D., Elfizy A., Tönissen S. Abrasive machining of advanced aerospace alloys and composites // CIRP Annals. 2018. V. 64 (2). P. 581.
Носенко В.А. К вопросу об интенсивности контактного взаимодействия d-переходных металлов с карбидом кремния при шлифовании // Проблемы машиностроения и надежности машин. 2002. № 5. С. 78.
Носенко В.А., Фетисов А.В., Сердюков Н.Д. Морфология и химический состав поверхности титанового сплава после шлифования кругом из карбида кремния // Наукоемкие технологии в машиностроении. 2019. № 12 (102). С. 22.
Dwyer-Joyce R.S. The life cycle of a debris particle // Tribol. Lett. 2005. V. 307. P. 681.
Fowler G., Shipway P.H., Pashby I.R. A technical note on grit embedment following abrasive water-jet milling of a titanium alloy // Journal of Materials Processing Technology. 2005. V. 159. P. 356.
Niranjan C.A., Srinivas S., Ramachandra M. Experimental investigations on depth of penetration and surface integrity in AZ91/Al2O3 nano-composites cut by abrasive water jet // Int. J. Adv. Manuf. Technol. 2020. V. 107. P. 747.
Quing M., Wenfeng D., Yulong G., Jiuhua X. Comparative investigation on wear behavior of brown alumina and microcrystalline alumina abrasive wheels during creep feed grinding of different nickel-based superalloys // Wear. 2019. V. 426–427. P. 1624.
Novovic D., Aspinwall D.K., Dewes R.C., Bowen P., Griffiths B. The effect of surface and subsurface condition on the fatigue life of Ti–25V–15Cr–2Al–0.2C %wt alloy // CIRP Annals-Manufacturing Technology. 2016. V. 65. P. 523.
Nosenko S.V., Nosenko V.A., Koryazhkin A.A. The effect of the operating speed and wheel characteristics on the surface quality at creep-feed grinding titanium alloys // Solid State Phenomena. 2018. V. 284. P. 369.
Гаршин А.П., Федотова С.М. Абразивные материалы и инструменты. Технология производства / Под общ. ред. А.П. Гаршина. СПб.: Изд-во Политехнического ун-та, 2008. 1009 с.
Дополнительные материалы отсутствуют.
Инструменты
Проблемы машиностроения и надежности машин