Проблемы машиностроения и надежности машин, 2022, № 2, стр. 47-56
Свойства износостойких композиционных покрытий, полученных скоростным борированием
В. П. Лялякин 1, *, В. Ф. Аулов 1, А. В. Ишков 2, И. Н. Кравченко 3, **, Ю. А. Кузнецов 4
1 Федеральный научный агроинженерный центр ВИМ
Москва, Россия
2 Алтайский государственный аграрный университет
Барнаул, Россия
3 Институт машиноведения им. А.А. Благонравова РАН
Москва, Россия
4 Орловский государственный аграрный университет им. Н.В. Парахина
Орел, Россия
* E-mail: valpal-1938@mail.ru
** E-mail: kravchenko-in71@yandex.ru
Поступила в редакцию 14.09.2021
После доработки 10.12.2021
Принята к публикации 20.12.2021
- EDN: UHADCT
- DOI: 10.31857/S0235711922020080
Аннотация
С помощью ТВЧ-нагрева образцов из стали 65Г под слоем шихты на основе плавленого боратного флюса П-066, содержащей карбид бора получены износостойкие композиционные боридные покрытия FeB толщиной до 800 нкм в течение 1–2 мин. Используя метод рентгенофазного анализа и металлографии, установлены состав и структура покрытий. Исследовано распределение микротвердости по глубине и определена их относительная износостойкость.
Для улучшения физико-механических характеристик поверхности различных деталей, их упрочнения и повышения срока службы в технологии машиностроения широко применяются методы химико-термической обработки (ХТО), заключающиеся в воздействии на стальные поверхности температурой и веществами, химически реагирующими с материалом детали [1]. При ХТО на поверхности металла образуются различные функциональные покрытия, преимущественно диффузионной природы, содержащие как неметаллические (С, N, S, Si, P, B), так и металлические (Cr, Ti, Al, Ni и др.) элементы в различных фазовых состояниях, а также продукты их взаимодействия с основным материалом детали (карбиды, нитриды, карбонитриды, интерметаллиды и пр.).
Среди современных процессов ХТО особое место занимают технологии насыщения поверхностного слоя конструкционных и легированных сталей бором – борирование. При борировании на поверхности стальной детали удается получать протяженные слои, отличающиеся высокой твердостью и прочностью к коррозии, абразивной стойкостью и высоким сопротивлением к изнашиванию [2]. Большинство процессов борирования длительны, энергоемки и трудно встраиваются в технологические схемы современных производств.
Интенсификация процессов ХТО, в частности борирования, может осуществляться с применением технологий высокоскоростного нагрева поверхности стальной детали с нанесением на нее борирующего состава токами высокой частоты (ТВЧ) до температур образования новых фаз и эвтектик (1370–1620 К) в системах Fe-B, Fe-B-C и Fe-Me-B-C, где Ме – это легирующий элемент из группы Cr, Mn, Ni и т.п. [3–5].
Для разработки промышленной технологии скоростного борирования требуется исследования структуры и свойств покрытий.
Целью исследования являлось изучение состава структуры и свойств износостойких композиционных покрытий, полученных скоростным борированием.
В качестве борирующих агентов использовали технический карбид бора В4С по ГОСТ 5744-85 и аморфный бор. Флюс состоял из прокаленной буры, борного ангидрида силикокальция и сварочного флюса АН 348 (П-0.66). Он соответствует по химическому составу тому, что применяется для индукционной наплавки [2]. Флюс вводился для раскисления, удаления окисных пленок и перевода твердофазного процесса в квазижидкостное борирование. Активаторами борирования служили СаF2 (фтористый кальций) и NH4Cl (хлористый аммоний).
Смеси для создания боридных покрытий наносились на подготовленные поверхности и закреплялись на них с помощью жидкого стекла, казеинового клея или эпоксидной смолы, вводимого в их состав за счет уменьшения количества флюса.
Нагрев подготовленных образцов производили в петлевом индукторе, подключенном к высокочастотному ламповому генератору ВЧГЗ – 160/0.066. Геометрия индуктора обеспечивала нагрев исследуемых образцов. В процессе нагрева генератор был настроен на средние режимы работы (анодный ток 5.1 А, сеточный ток 0.78 А, анодное напряжение 7.2 кВ).
В индукторе одновременно нагревалось 18 образцов до температуры 1470–1570 К в течение 1.0–2.5 мин, температуру измеряли ренеевой термопарой (диаметром 0.2 мм), приваренной конденсаторной сваркой к поверхности образца. После выдержки при указанной температуре нагрев прекращался, и образцы вынимались из индуктора и остывали на воздухе до комнатной температуры.
Смачивание поверхности заготовок при расплавлении шихты определяли содержанием в ней компонентов флюса и временем выдержки в индукторе.
Смачивание расплавленной шихты на поверхности заготовок происходит полностью (рис. 1а–е) и частично растекается от первоначальных геометрических размеров нанесенных порошковых материалов, независимо от того, какой активатор (NH4Cl, CaF2) находится в шихте, содержащей карбид бора или аморфный бор.
Рис. 1.
Поверхность затвердевшего боридного расплава на образцах из стали 65Г: В90% + CaF2 5% + + Фл 5% В 90% + CaF2 5% + Фл 5% В 90% + CaF2 5% + Фл 5%.

Для того чтобы поверхность, подвергаемая упрочнению, полностью покрылась борирующим расплавом, достаточно 1.16 мин. Время полного смачивания определяется составом шихты.
В предварительных экспериментах при нанесении на очищенную стальную поверхность борирующего компонента В4С и последующем индукционном нагреве до температуры 1470–1570 К, которую измеряли термопарой с различным временем выдержки были получены островковые двухфазные (FeB + Fe2B) боридные покрытия толщиной 0.02–0.03 мм, что не удовлетворяет требованиям, предъявляемым к почвообрабатывающим рабочим органам из-за незначительной толщины [6].
Состав исследуемых смесей приведен в табл. 1.
Таблица 1.
Состав борирующих смесей, масс. %
Смесь | Борирующий агент | Активатор | Флюс |
---|---|---|---|
I | В4С (90) | – | П-0.66 (10) |
Iа | В4С (84) | NH4Cl (6) | П-0.66 (10) |
II | В4С (84) | – | П-0.66 (16) |
IIа | В4С (90) | CaF2 (5) | П-0.66 (5) |
III | В (90) | – | П-0.66 (10) |
IIIа | В (90) | CaF2 (5) | П-0.66 (5) |
Установлено, что при ТВЧ-нагреве сталей Ст3, 50, 50ХГА, 65Г, покрытых борирующими составами, при выбранных параметрах процесса (Т = 1470–1570 К, выдержка 1–2 мин) на всех образцах образуются покрытия, по внешнему виду напоминающие наплавленный сплав. Их рентгенофазовый анализ показал присутствие фаз: б-Fe, FeB и Fe2B, Fe3(C, B), Fe23(C,B)6, мета- и ортоборатов железа (Fe3BO3,Fe3BO6, Fe3BO5), следы вюстита FeO и шпинели FeO·Fe2O3, то есть при ТВЧ-нагреве легированных углеродистых сталей под слоем флюса П-0.66, содержащего от 84 до 90% борирующих агентов, на их поверхности образуются сложные боридные покрытия. Для выяснения характеристик и структуры полученных слоев, а также состояния боридов в них были изучены микрофотографии шлифов (рис. 2).
Рис. 2.
Структура боридного подслоя на стали 65Г, сформированного за 1 мин из различных смесей (×250): (а) – Iа; (б) – II; (в) – IIIа.
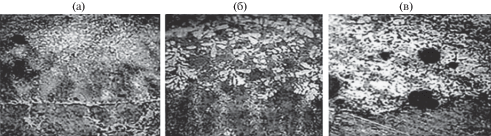
Из рис. 2 следует, что при выбранных температурных значениях времени борирования структура и состояние границы полученных подслоев отличаются. Однако, в отличие от классических боридных иглообразных двухфазных слоев, на поверхности заготовок формируется более стойкая, предпочтительная в условиях тяжелого абразивного, знакопеременного и ударного износа пластичная боридная эвтектика с выраженной или диффузионной границей. Изменений структуры основного металла из-за перегрева практически не наблюдается. Создаются боридные покрытия трех типов [7].
Так для смесей, содержащих в качестве борирующего агента одинаковое количество карбида бора, флюса и отличающихся только наличием активатора (NH4Cl, CaF2), способствующего усилению обратимых диффузионных процессов, особенно при низких температурах, в начале процесса борирования наблюдается образование мелкозернистой эвтектической структуры с включениями фазы Fe2B. Микротвердость такого упрочнения не выше 700–750 HV при толщине слоя до 100 мкм, просматривается четко различимая граница раздела покрытия с основным металлом (рис. 2а).
Для смеси II без активаторов в покрытии наблюдается выраженный рост дендритов, островов и друз фазы FeB в матрице Fe2B, микротвердость покрытия достигает 1100–1250 HV, толщина слоя – до 200 мкм. Покрытие характеризуется диффузной границей раздела с основным металлом (рис. 2б).
Экспериментально установлено, самыми реакционноспособными оказались смеси на основе аморфного бора (рис. 2в). Так, в смеси IIIa, содержащей дополнительно 5% активатора CaF2 и 5% флюса, за 1 мин толщина слоя составила 600 мкм при микротвердости 2200–2300 HV. Основная структура представляет собой переплавленную гомогенизированную железо-боридную эвтектику с включением фазы FeB, образовавшуюся с такой скоростью, что из расплава при его затвердевании не успели выделиться частицы шлака, кроме того, формируется граница раздела покрытие–основной металл.
Исследование распределения микротвердости полученных подслоев по глубине показало наличие в них, как правило, двух зон – более твердого поверхностного слоя и менее твердого слоя, лежащего под ним, протяженность и характеристики которых различаются (рис. 2).
Существование такой слоистой структуры в полученных покрытиях в данном случае объясняется не наличием двух фаз FeB и Fe2B, расположенных в материале друг за другом, а различающимся содержанием одной упрочняющей фазы по глубине покрытия. Вид упрочняющей фазы в нашем случае определяется природой борирующего агента и составом смеси. Об этом свидетельствуют как структура полученных покрытий, так и зависимость толщины, твердости и износостойкости покрытий, образующихся на сталях 65Г и 50ХГА за различное время из обмазки на основе В4С, а также данные их рентгенофазового анализа [8].
Боридные подслои, полученные при ТВЧ-нагреве этих же образцов в течение 1.5‒2 мин, имеют иную структуру (рис. 3). При таких условиях борирования (рис. 3) образуются структуры двух типов. В покрытии, полученном при ТВЧ-нагреве из смеси, содержащей карбид бора и флюс П-0.66 без активаторов, наблюдается разрастание ледебуритоподобной железо-боридной эвтектики, которая имеет мелкозернистую структуру на образцах, выдержанных при температуре 1200–1570 К в течение одной минуты, причем состав эвтектики изменяется в более светлых и темных участках.
Рис. 3.
Структура боридных подслоев на стали 65Г, полученных за 1.5 мин из различных смесей (×300): (а) – I; (б) – IIа; (в) – IIIа.
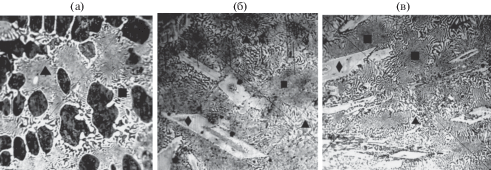
В эвтектической матрице наблюдаются равномерно распределенные замкнутые карбидные области (рис. 3а). Микротвердость образующегося покрытия 1450–1600 HV, толщина до 300–350 мкм.
На рис. 4а, б приведены типичные структуры наплавленных сплавов (ПГ-УС-25 и ПС-14-60) с толщиной боридных подслоев 0.1–0.15 мм, полученных при ТВЧ-нагреве стали 65Г под борирующей обмазкой на основе В4С и флюса П-0.66 без активатора (рис. 4а) и в присутствии 5% фторида кальция (рис. 4б).
Рис. 4.
Структура износостойкого покрытия в боридном подслое, полученном за 2 мин для материала: (а) – ПГ-УС25 на стали 65Г; (б) – ПС-14-60 на стали 50 (×400).
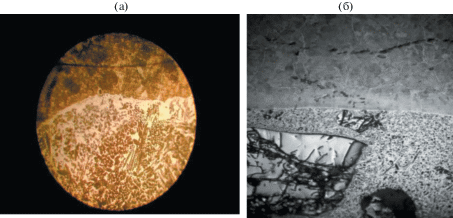
Основой (матрицей) износостойкого покрытия в обоих случаях является железо-боридная эвтектика, однако для этой стали доля более твердых светлых областей в ее объеме значительно меньше, чем на образцах стали 65Г, борированных в течение 1.0 и 1.5 мин.
В структурах первого типа (рис. 4а) в покрытии хорошо видны острова и друзы упрочняющей фазы FeB. Подобные структуры приведены на рис. 4б. Микротвердость этих участков достигает 2100–2200 HV, а твердость матрицы, образующейся при ТВЧ-борировании стали 50ХГА, составляет 1700–1800 HV, что на 100–200 единиц выше, чем для стали 65Г, толщина же образующегося покрытия, наоборот, несколько меньше, и составляет 450–600 мкм. Введение активатора CaF2 ускоряет процесс, за две минуты в покрытии не успевают образовываться включения боридов железа, а в железо-боридной матрице видны карбидные области, подобные тем, которые показаны на рис. 3а, однако их площадь и общая доля в структуре заметно меньше (рис. 3б). Микротвердость такого покрытия 1300–1400 HV, толщина 450–600 мкм.
Создание износостойкого боридного покрытия на рабочих органах сельскохозяйственных машин производилась не только на лаповых генераторах, но и на преобразователе “Элист 120 ПЗ” фирмы ООО Элист, г. Томск. Боридный состав наносился непосредственно на лезвийную поверхность заготовки.
На рис. 4 показана стрельчатая лапа “Алтай”, установленная в индуктор с двумя параллельными ветвями, подключенный к высокочастотному преобразователю “Элист 120 ПЗ”, с насыпанной шихтой, содержащей карбид бора до 8%.
Смесь наносилась на лезвийную поверхность высотой 1.0–1.2 мм специальным дозатором, помещалась в индуктор (рис. 4) и выдерживалась в нем в течение 1.1–1.2 мин при температуре 1200–1250 К. Затем заготовка остывала, образовавшийся шлак снимался металлической щеткой, и повторно на это же место насыпался порошок хромистого чугуна марки ПГ-УС25 80% и 20% – флюса, высотой 1.0–1.2 мм, и в этом же индукторе осуществляли наплавку износостойкого чугуна в течение 0.58–1.0 мин. Глубина борированного подслоя составляла 250–300 мкм. Далее из наплавочного образца вырезались темплеты, изготавливались шалфы для металлографических исследований на микроскопе CarllZeissAxioObzerverz 1m, и определялась микротвердость NetronMH-6 при нагрузке 100 г.
Рис. 5.
Заготовка стрельчатой лапы “Алтай”, установленная в индуктор с двумя параллельными ветвями. Состав для создания борирующего покрытия на стали 65Г содержал 80% карбида бора и 20% – флюса.
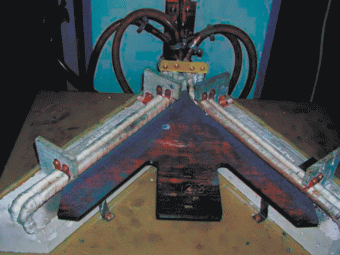
Характерная структура наплавленного хромистого чугуна на подслой боридного покрытия показана на рис. 6.
Рис. 6.
Характерная структура наплавленного сплава марки ПГ-УС25 на боридном покрытии стали 65Г (толщина подслоя 100–150 мкм): 1 – линия раздела наплавленного сплава и основного металла; 2 – тонко дифференцированная пластинчатая эвтектика; 3 – сложные карбороиды.
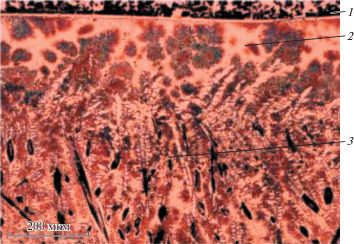
В результате диффузионных процессов и механического перемешивания основного металла (подслоя) наплавляемым сплавом не образуется характерных структурных зон, которые создаются при наплавке порошковых материалов типа сормайта.
Вследствие высокой термодинамической активности бора он вытесняет углерод из фазовых составляющих структур наплавляемого сплава (рис. 6).
Вследствие активного действия бора полностью подавляется образование доэвтектической структуры, и его величина настолько значительна в боридном подслое упрочняемого металла, что его достаточно, чтобы сформировать новые структуры в наплавленном сплаве по линии соединения с основным металлом. Микротвердость наплавленного сплава на боридный подслой показана на рис. 7.
Рис. 7.
Микротвердость наплавленного сплава марки ПГ-УС25 и основного металла 65Г: 1 – наибольшее значение микротвердости; 2 – среднее значение микротвердости; 3 – нижнее значение микротвердости.
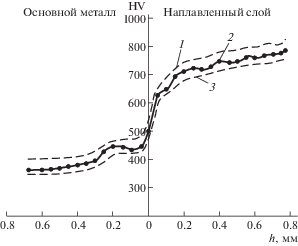
Проведенный микрорентгеноспектральный анализ позволил установить состав основных фаз боридных подслоев, получающихся при ТВЧ-борировании исследованных сталей (табл. 2).
Таблица 2.
Результаты микрорентгеноспектрального анализа основных фаз в боридных подслоях на стали 65Г и 50ХГА
Обозначение фазы, элементы | Описание фазы, морфология | Состав, элемент, % | Химическая формула | |
---|---|---|---|---|
весовой | атомный | |||
$\blacksquare $ – Fe, C, B | матрица – серое поле в ледебуритоподобной эвтектике | Fe – 57.25 | 21.72 | FeC2.3B1.3 |
C – 28.02 | 49.42 | |||
B – 14.73 | 28.86 | |||
$\blacksquare $* – Fe, C, B | то же | Fe – 64.31 | 27.12 | FeC1.6B1.1 |
C – 22.30 | 43.73 | |||
B – 13.38 | 29.15 | |||
$\square $ – Fe, C, B | упрочняющая фаза – светлые области эвтектики | Fe – 50.63 | 17.24 | FeC2.1B2.7 |
C – 23.11 | 36.59 | |||
B – 26.25 | 46.17 | |||
![]() |
упрочняющая фаза – пластинчатые кристаллы или иглы | Fe – 64.70 | 28.11 | Fe58MnC96B51 |
Mn(Cr) – 1.21(1.35) | 0.54(0.62) | Fe58CrC96B51 | ||
C – 23.01 | 46.49 | |||
B – 11.08 | 24.87 | |||
![]() |
упрочняющая фаза – темные замкнутые области | Fe – 86.60 | 58.15 | Fe1.4C |
C – 13.40 | 41.85 |
Как следует из данных табл. 2, в состав основной матричной и упрочняющих фаз всех исследованных покрытий помимо железа и бора входит углерод, причем его доля колеблется от 13.4 до 28 мас. %, что отвечает углеродным фазам от цементита и карбоборидов Fe до специальных карбидов и специальных карбоборидов Fe, Mn и Cr. Такой состав фаз в полученных покрытиях хорошо согласуется с известной диаграммой состояния тройной системы Fe–C–B, изотермические сечения которой при 900, 1000 и 1080 К приведены в работах [6, 9]. Основными равновесными фазами в системе Fe‒C–B при содержании углерода до 25, а бора до 35 мас. %, по данным настоящей статьи, являются диборид железа FeB2, цементит Fe3C, борированный цементит Fe3(C,B) и специальный борированный карбид Fe23(C,B)6. В случае же осуществления высокоскоростного процесса ТВЧ-борирования создаются условия для образования метастабильных фаз, фаз переменного состава и твердых растворов бора и углерода в железе (табл. 2). В пользу этого свидетельствуют и данные рентгенофазового анализа (идентификация по картотеке JCPDS), объективно подтверждающие существование во всех полученных покрытиях только фазы FeB2 и ее кристаллохимического димера Fe2B4 (рис. 8).
Исследование распределения микротвердости полученных покрытий по глубине показало наличие в них, как правило, двух зон более твердого поверхностного слоя и менее твердого слоя, лежащего под ним, протяженность и характеристики которых различаются (рис. 9).
Рис. 9.
Распределение микротвердости по глубине покрытий, полученных из различных борирующих смесей на стали 65Г за 1 мин.
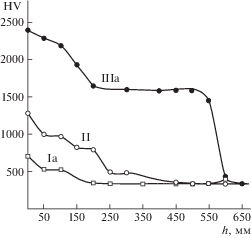
Существование такой слоистой структуры в полученных покрытиях в нашем случае объясняется не наличием двух фаз FeB и Fe2B, расположенных в металле друг за другом [5], различающемся содержанием основной упрочняющей фазы по глубине покрытия. Об этом свидетельствуют как структура полученных покрытий (рис. 2, 8), так и зависимость толщины, твердости и износостойкости покрытий, образующихся на почвообрабатывающих органах, выполненных в промышленных условиях из сталей 65Г и 50ХГА за различное время из обмазки на основе B4C без активаторов (табл. 3).
Таблица 3.
Некоторые характеристики покрытий
Состав обмазки (В4С: флюс П-0.66), масс.% | Материал основы | ф, мин | h, мкм | MKT | W, мг | Фазовый состав покрытия |
---|---|---|---|---|---|---|
84 : 16 | 65Г | 1 | 260 | 2300 | 100 | FeB, Fe2B |
2 | 280 | 1060 | 150 | Fe2B | ||
90 : 10 | 50ХГА | 1 | 160 | 1000 | 200 | б-Fe, FeB, Fe3(C,B) |
2 | 190 | 1100 | 300 | FeB | ||
84 : 16 | 50ХГА | 1 | 100 | 950 | 600 | б-Fe, FeB, Fe2B |
2 | 150 | 1100 | 300 | Fe2B | ||
90 : 10 | 65Г | 1 | 280 | 2150 | 150 | FeB, Fe2B |
2 | 350 | 2200 | 250 | FeB, Fe2B |
Примечание. ф – время выдержки детали в индукторе при 1250 ч 1300°С, мин; h – толщина упрочняющего боридного покрытия, мкм; МКТ – микротвердость рабочей поверхности, измеренная на ПМТ-3 при нагрузке 100 г, НV; W – износ образца на 10000 м пути при трении о нежестко закрепленные абразивные частицы, мг.
Выводы. 1. Введение в состав борирующих обмазок, содержащих В4С, В аморфн., активаторы NH4CI, CаF2 плавленого флюса для индукционной наплавки П-0.66 позволяет значительно увеличить скорость процесса борирования из твердой в квазижидкую фазу. 2. Установлено, что на поверхности сталей 65Г и 50ХГА образуются износостойкие покрытия, состоящие из упрочняющих фаз (цементит, диборид, Fe2B и Fe2B4, карбобориды и специальные карбиды Fe, Mn и Cr), распределенных в матрице железоборидной эвтектики, с толщиной от 100 до 800 мкм, микротвердостью от 700 до 2350 HV, износ которых при трении о незакрепленный абразив составляет от 100 до 600 мг на 10 000 м пути в зависимости от природы борирующего агента, состава обмазки, времени выдержки и вида стали. 3. Одновременное борирование упрочняемой поверхности и твердого сплава осуществляли с карбидом бора, при содержании его во флюсе от 4 до 8%.
Список литературы
Затуловский С.С. Литье с применением инокуляторов. Достижения и перспективы // Литейное производство. 1989. № 2. С. 4.
Иванайский В.В., Шанчуров С.М., Ишков А.В. и др. Тепловая модель индукционной наплавки // Алдамджаровские чтения: материалы междунар. научн.-практ. конф. Костанай: Изд-во КСТУ им. акад. З. Алдамжар, 2011. С. 105.
Боль А.А. Регулирование режима работы высококачественного генератора при индукционной наплавке. М.: ЦНИИТЭ-Итракторосельхозмаш, 1984. ВЖП 1. С. 13.
Мишустин Н.М., Иванайский В.В., Ишков А.В. Скоростное борирование сталей 65Г и 50ХГА // Современные проблемы машиностроения: Сб. докладов V-й Межуднар. Научн. техн. конф. Томск: Изд-во ТПУ, 2010. С. 250.
Мишустин Н.М., Ишков А.В., Иванайский В.В., Кривочуров Н.Т. Образование боридных покрытий постструктуированных сталях при ТВЧ-нагреве. Матер. XXII Междунар. инновац.-ориент. конф. молодых ученых и студентов (26–29 октября). М.: Микмус, 2010. 30 с.
Черноиванов В.И., Лялякин В.П., Аулов В.Ф., Ишков А.В., Кривочуров Н.Т., Иванайский В.В., Коваль Д.В., Соколов А.В. Особенности изнашивания деталей сельхозмашин, упрочненных композиционными боридными покрытиями FE NB-FE-B // Трение и износ. 2015. Т. 36. № 2. С. 174.
Ишков А.В., Мишустин Н.М., Иванайский В.В. Структура и свойства износостойких слоев, полученных на стали 65Г высокоскоростным борированием [Комп.] // Горизонты образования: электронный научный журнал. 2010. Вып 12. http: // www/edu/secna.ru/main/review/
Junji M., Taisure O., Toshifumi K., Shintaro M. and oth. Some properties, of boronized layerers on steels with direct diode laser // Vacuum. 2008. V. 83. № l. P. 185.
Аулов В.Ф., Ишков А.В., Иванайский В.В., Кривочуров Н.Т., Лялякин В.П. Влияния легирования бором на структуру сварочных швов для стали 65Г // Сварочное производство. 2018. № 5. С. 38.
Дополнительные материалы отсутствуют.
Инструменты
Проблемы машиностроения и надежности машин