Проблемы машиностроения и надежности машин, 2022, № 5, стр. 93-98
Определение температуры нагрева смазочного слоя при трении
А. Ю. Албагачиев 1, А. Н. Михеев 1, М. А. Тананов 1, А. Б. Тохметова 1, *
1 Институт машиноведения им. А.А. Благонравова РАН
Москва, Россия
* E-mail: aygerim.tokhmetova@mail.ru
Поступила в редакцию 04.02.2022
После доработки 15.05.2022
Принята к публикации 21.06.2022
- EDN: RZWYYJ
- DOI: 10.31857/S0235711922050029
Аннотация
В статье рассмотрены экспериментальные и теоретические исследования температуры нагрева смазочного слоя между трущимися поверхностями. Экспериментальное исследование определения температуры смазочного слоя выполнялось на универсальной машине трения УМТ-1.
Проблема повышения надежности и долговечности узлов трения в машинах всегда была серьезной проблемой в современной инженерии [1–6]. При трении 85–90% механической энергии превращается в теплоту [7–9]. Главным фактором для оценки работоспособности узлов трения является температурное состояние фрикционного контакта. Теплота, генерируемая в зоне контакта, распределяется между сопряженными телами и окружающей средой [10]. Целью исследования является определение температуры нагрева зоны контакта твердых тел при трении.
Материалы и методы. Трибологические испытания проводились на универсальной машине трения УМТ-1 (рис. 1) [11]. Объектом исследования является моторное масло Mobil Ultra 10W-40. В качестве образцов в виде колец с наружным диаметром 28 мм, внутренним диаметром 20 мм, высотой 15 мм (рис. 2) использовались латунь и нержавеющая сталь 12Х18Н10Т.
Рис. 2.
Схема расположения образцов и датчиков: 1 – вращающийся патрон УМТ; 2 – вращающийся образец, нержавеющая сталь; 3 – инфракрасный датчик температуры MLX90614; 4 – неподвижный образец, латунь; 5 – неподвижный патрон УМТ; 6 – трубка для измерения давления смазки; 7 – датчик давления смазки.
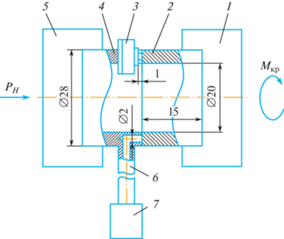
В торце неподвижного образца были просверлены два отверстия диаметром 2 мм для датчиков температуры и давления. Нормальная сила, приложенная к неподвижному образцу, составляла 200–500 Н. Полость, между образцами, была заполнена смазкой.
Регистрация и обработка экспериментальных данных проводилась с использованием измерительной системы, состоящей из датчика температуры, датчика частоты вращения шпинделя и микроконтроллера, данные которых отражались в персональном компьютере (ПЭВМ) (рис. 3).
Вычисления действительного значения температуры проводили при помощи микроконтроллера с использованием данных от инфракрасного датчика, датчика температуры корпуса измерителя и тарировочных таблиц, записанных в постоянной памяти (ПЗУ). Значения температуры и частоты вращения с метками времени передаются на компьютер, где обрабатываются программой составленной в среде LabView.
Для измерения температуры слоя смазки, независимо от температур образцов, применен инфракрасный бесконтактный измеритель температуры на основе датчика MLX90614 с оптической системой. Блок-схема измерителя температуры приведена на рис. 4.
Рис. 4.
Блок-схема измерителя температуры: МШУ – малошумящий усилитель; ПУ – усилитель с программируемым коэффициентом усиления; АЦП – аналого-цифровой преобразователь; ППЗУ – перепрограммируемое постоянное запоминающее устройство; ОЗУ – оперативное запоминающее устройство.
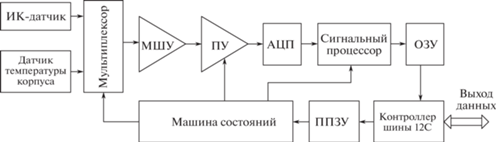
Бесконтактный измеритель температуры содержит два датчика: инфракрасный датчик теплового излучения (полупроводниковый болометр) и датчик температуры корпуса (терморезистор).
Работа измерителя контролируется внутренней машиной состояния реализованной по принципу конечного автомата, которая управляет процессом измерения и расчетами температуры объекта и корпуса, а также выполняет постобработку температур для вывода их через цифровой интерфейс I2C. Выходной сигнал ИК-датчика усиливается малошумящим усилителем и усилителем с программируемым коэффициентом усиления, преобразуется в сигма-дельта аналого-цифровым преобразователем и подается на сигнальный процессор для дальнейшей обработки. Сигнал обрабатывается программируемыми фильтрами нижних и верхних частот для дальнейшего уменьшения ширины полосы входного сигнала для достижения минимального уровня шума и заданной частоты обновления. На основании результатов измерений рассчитываются соответствующая температура корпуса прибора и температура объекта.
Оптическая система измерителя температуры показана на рис. 5 и состоит из линзы 1, фокусирующей тепловое излучение на инфракрасном датчике 3, и диафрагмы 2, формирующей диаграмму направленности. На одном основании с инфракрасным датчиком размещен датчик температуры корпуса 4.
Рис. 5.
Оптическая система измерителя температуры. Обозначения на рисунке: 1 – линза; 2 – диафрагма; 3 – инфракрасный датчик; 4 – датчик температуры корпуса.
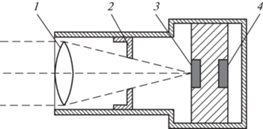
Испытание смазочного материала проводилось при нагрузках 200 и 500 Н, с частотой вращения 100, 500, 1000 об/мин. Показания считывались и записывались в память с периодом 0.01 с.
Для каждого режима длительность испытания составляла 5 минут. Измерения проводились в интервале 1 мин в конце испытания (табл. 1). Частота вращения образца n составляла 100, 500, 1000 об/мин.
Таблица 1.
Экспериментальные данные измерения температуры смазочного слоя
№ | Нагрузка, Н | Частота вращения, об/мин | Момент трения по динамометру, Н ⋅ м | Температура по ИК-датчику, °С |
---|---|---|---|---|
1 | 200 | 100 | 0.60 | 30.5 |
2 | 200 | 500 | 0.36 | 38.6 |
3 | 200 | 1000 | 0.32 | 59.0 |
4 | 500 | 100 | 0.73 | 48.0 |
5 | 500 | 500 | 0.41 | 138.0 |
6 | 500 | 1000 | 0.28 | 210.0 |
Коэффициент трения определялся по измеренному моменту трения и приложенной нагрузке. Силу трения рассчитывали по среднему диаметру образца 24 мм. Таким образом, коэффициент трения равен: $k = \frac{{M \times 2 \times 1000}}{{24N}}$, где М – момент трения, Н ⋅ м; N – нагрузка, Н. Площадь кольцевого образца A с наружным диаметром 28 мм и внутренним диаметром 20 мм составляет 3 × 10–4 м3.
Теплофизические свойства неподвижного образца, изготовленного из латуни ЛС-59 составляют [12]: теплопроводность ${{{{\lambda }}}_{1}} = 22.68$ $\frac{{{\text{Вт}}}}{{{\text{м}}\;^\circ {\text{С}}}}$, произведение теплоемкости и плотности ${{с}_{1}}{{\rho }_{1}} = 4.536 \times {{10}^{6}}$ $\frac{{{\text{Дж}}}}{{{{{\text{м}}}^{{\text{3}}}}\;^\circ {\text{С}}}}$, вращающегося образца изготовленного из коррозионно-стойкой стали 12Х18Н10Т: ${{{{\lambda }}}_{2}} = 126.84$ $\frac{{{\text{Вт}}}}{{{\text{м}}\;^\circ {\text{С}}}}$, ${{с}_{2}}{{\rho }_{2}} = 4.074 \times {{10}^{6}}$ $\frac{{{\text{Дж}}}}{{{{{\text{м}}}^{{\text{3}}}}\;^\circ {\text{С}}}}$.
Для вычисления температуры нагрева смазочного слоя выведена формула
(1)
$\theta = \frac{{fNV\sqrt t }}{{1.73A\left( {\sqrt {{{\lambda }_{1}}{{C}_{1}}{{\rho }_{1}}} + \sqrt {{{\lambda }_{2}}{{C}_{2}}{{\rho }_{2}}} } \right)}},$В табл. 2 показано изменение температуры смазочного слоя между сопряженными поверхностями в зависимости от коэффициента трения и теплофизических свойств металлов при линейной скорости вращения (0.125; 0.628 и 1.25 м/с).
Таблица 2.
Расчетные данные изменения температуры смазочного слоя
№ | Нагрузка, Н | Частота вращения, об/мин | Линейная скорость вращающейся поверхности, м/с | Коэффициент трения | Температура смазочного слоя с учетом комнатной температуры, °С |
---|---|---|---|---|---|
1 | 200 | 100 | 0.125 | 0.250 | 26.345 |
2 | 200 | 500 | 0.628 | 0.150 | 39.125 |
3 | 200 | 1000 | 1.250 | 0.133 | 53.754 |
4 | 500 | 100 | 0.125 | 0.122 | 27.741 |
5 | 500 | 500 | 0.628 | 0.068 | 41.675 |
6 | 500 | 1000 | 1.250 | 0.047 | 49.820 |
По результатам исследования (рис. 6, 7) с увеличением частоты вращения от 100 до 1000 об/мин температура смазочного слоя возрастает от 30 до 210°С (является закономерным).
Рис. 6.
Зависимость температуры смазочного слоя от частоты вращения при постоянной нагрузке 200 Н: 1 – экспериментальные исследования; 2 – теоретические исследования.
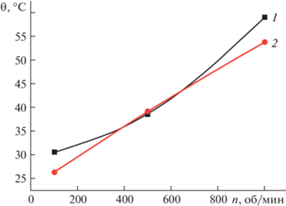
Рис. 7.
Зависимость температуры смазочного слоя от частоты вращения при постоянной нагрузке 500 Н: 1 – экспериментальные исследования; 2 – теоретические исследования.
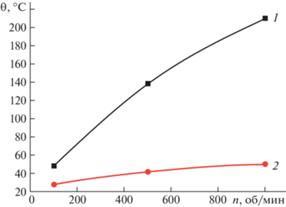
Как видно из полученных данных (рис. 7), при нагрузке 500 Н экспериментальные значения сильно отличаются от теоретических.
Корреляция экспериментальных и расчетных данных наблюдается при нормальной нагрузке 200 Н и нарушается при нагрузке 500 Н. Из этого следует, что данная формула применима для расчета при нагрузке 200 Н, а при нагрузке 500 Н она нуждается в дальнейшей корректировке, связанной с учетом температуры смазочного слоя во времени и распределением тепловых потоков между смазкой и металлическими образцами.
Выводы. Из анализа экспериментальных данных следует, что температура нагрева смазочного слоя между трущимися поверхностями увеличивается с ростом нормальной нагрузки и частоты вращения образца. Предложен аналитический метод расчета температуры смазочного слоя между трущимися поверхностями. В результате сравнения теоретических и экспериментальных данных температуры нагрева смазочного слоя установлено их соответствие при нагрузке 200 Н.
Список литературы
Трение, изнашивание и смазка: Справочник / Под общ. ред. И.В. Крагельского, В.В. Алисина. В 2 т. Т. 1. М.: Машиностроение, 1978.
Чичинадзе А.В. Трение, износ и смазка (трибология и триботехника). М.: Машиностроение, 2003. 576 с.
Persson B.N.J., Tosatti E. Physics of Sliding friction. Kluwer, Dordrecht 1996, 460 p.
Чичинадзе А.В., Берлинер Э.М., Браун Э.Д. Трение, износ и смазка. Трибология и триботехника / Под ред. А.В. Чичинадзе. М.: Машиностроение, 2003. 576 с.
Bowden F.P., Tabor D. The Friction and Lubrication of Solids. Oxford: Clarendon Press, 2001.
Persson B.N.J. Sliding Friction. Physical Principles and Applications. Springer, 2002.
Rabinowicz E. Friction and wear of materials. 2nd ed. John Wiley & Sons, inc., 1995. 315 p.
Мышкин Н.К., Петроковец М.И. Трение, износ, смазка. Физические основы и технические приложения трибологии. М.: ФИЗМАТЛИТ, 2007. 368 с.
Попов В.А., Попов В.Л. Механика контактного взаимодействия и физика трения: от нанотрибологии до динамики землетрясений. М.: ФИЗМАТЛИТ, 2013. 350 с.
Резников А.Н. Тепловые процессы в технологических системах. М.: Машиностроение, 1990. 288 с.
Справочник по триботехнике / Под общ. ред. М. Хедбы, А.В. Чичинадзе. В 3 т. Т. 1. Теоретическиеосновы. М.: Машиностроение, 1989.
Albagachiev A.Yu., Novikova N.N., Tokhmetova A.B. Tribotechnical Characteristics of Nanomodifier 1 // J. of Machinery Manufacture and Reliability. 2020. V. 49 (5). P. 457.
Дополнительные материалы отсутствуют.
Инструменты
Проблемы машиностроения и надежности машин