Проблемы машиностроения и надежности машин, 2022, № 6, стр. 56-64
Оценка шероховатости поверхностей деталей машин с износостойкими газотермическими покрытиями при токарной обработке
А. А. Ковалев 1, *, А. С. Краско 1, Н. В. Рогов 1
1 Московский государственный технический университет им. Н.Э. Баумана
Москва, Россия
* E-mail: kovalevarta@gmail.com
Поступила в редакцию 08.10.2021
После доработки 17.05.2022
Принята к публикации 21.06.2022
- EDN: KURZZN
- DOI: 10.31857/S023571192205008X
Аннотация
В настоящей статье рассматриваются модели оценки шероховатости поверхностей деталей машин с износостойкими покрытиями при токарной обработке. Была предложена модель оценки шероховатости, позволяющая установить взаимосвязь между получаемой при токарной обработке величиной шероховатости поверхности газотермического покрытия с режимами резания, геометрическими параметрами резца и свойствами материалов заготовки и инструмента.
Обеспечение эксплуатационных свойств ответственных деталей машин и технологической оснастки, работающих в условиях многофакторных воздействий, в современном машиностроении реализуется, в частности, посредством нанесения функциональных покрытий, в том числе газотермическими методами [1–6].
На сегодняшний день наиболее перспективными способами газотермического напыления являются плазменное (APS) и высокоскоростное газопламенное (HVOF, HVAF) напыление, позволяющие в условиях мелкой серии заменить химико-термическую обработку и нанесение гальванических покрытий, что потенциально даст возможность повысить гибкость производства [2, 7–11].
Покрытия, полученные такими способами, обладают высокой износостойкостью, однако в процессе их формирования не обеспечивается заданная разменная точность и шероховатость поверхности детали, что приводит к необходимости их дальнейшей механической обработки.
Износостойкость покрытий, обусловленная их высокой твердостью и хрупкостью, вызывает трудности при последующей механической обработке, а наличие переходной зоны между покрытием и основным материалом является ограничением по назначению технологических режимов [12–17].
В настоящее время для обработки износостойких покрытий широко применяются методы абразивной обработки, однако для пар трения, вследствие шаржирования, требуется дополнительная ультразвуковая очистка поверхности. Помимо этого, в условиях мелкосерийного производства абразивные методы не обладают требуемой гибкостью. Исходя из этого, наиболее рациональным методом обработки покрытий является лезвийная обработка – точение и фрезерование.
В связи с этим, актуальной задачей является оценка параметров качества поверхностей деталей с износостойкими покрытиями при токарной обработке с учетом труднообрабатываемости материалов и наличием переходной зоны между покрытием и основным материалом детали.
Разработка модели оценки шероховатости поверхности покрытия. В работах А.М. Дальского и А.Г. Суслова [18–20] изложены методики оценки шероховатости поверхности, полученной при обработке заготовок точением. Рассмотренная модель шероховатости учитывает составляющие профиля шероховатости, обусловленные: геометрией и кинематикой перемещения рабочей части инструмента; колебаниями инструмента относительно обрабатываемой поверхности; пластическими деформациями в зоне контакта инструмента и заготовки; шероховатостью рабочих поверхностей инструмента.
На первом этапе рассматривается геометрически-кинематическая составляющая профиля шероховатости. Исходными данными являются следующие параметры: φ – главный угол резца в плане, град; φ1 – вспомогательный угол в плане, град; So – подача инструмента, мм/об; re – радиус при вершине резца, мм.
При расчете составляющей шероховатости, обусловленной геометрией и кинематикой перемещения рабочей части инструмента, возможны четыре случая соотношений исходных данных между собой. При этом, сравниваются величины углов φ и φ1 со значением arcsin(So/2re) и, исходя из этого, возможны следующие случаи: 1) φ > arcsin(So/2re), φ1 > > arcsin(So/2re); 2) φ ≤ arcsin(So/2re), φ1 ≤ arcsin(So/2re); 3) φ > arcsin(So/2re), φ1 ≤ ≤ arcsin(So/2re); 4) φ ≤ arcsin(So/2re), φ1 > arcsin(So/2re).
Кинематическая составляющая профиля шероховатости поверхности при точении обусловлена геометрическими параметрами режущей пластины резца и величиной подачи инструмента [18]. Таким образом, под кинематической составляющей профиля понимается след, который оставляет инструмент на поверхности заготовки в процессе резания, перемещаясь вдоль ее оси.
Для оценки шероховатости используют соотношение (1) [19], определяющее высоту неровности Rz', образованной при прохождении резца (рис. 1).
Рис. 1.
Формирование кинематической составляющей шероховатости поверхностного слоя при малых подачах.
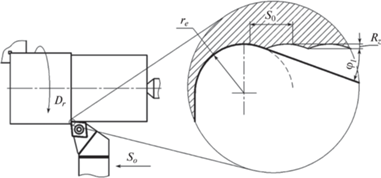
При более высоких значениях подачи в процессе резания помимо главной режущей кромки и криволинейного участка режущей кромки резца участвует также вспомогательная режущая кромка. Таким образом, представленная на рис. 1 модель формирования шероховатости становится некорректной.
Очевидно, что профиль шероховатости при точении с участием вспомогательной режущей кромки будет формироваться из следов криволинейного участка режущей кромки и вспомогательной режущей кромки резца, что графически представлено на рис. 2.
Рис. 2.
Формирование кинематической составляющей шероховатости поверхностного слоя при высоких подачах.
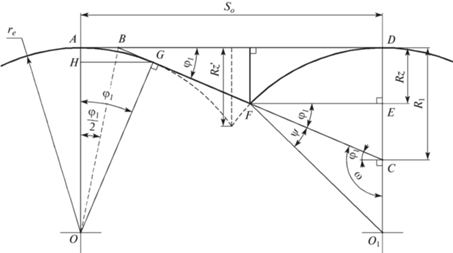
Оценка шероховатости проводится на основании геометрических построений (рис. 2), согласно которым, кинематическая составляющая профиля шероховатости Rz определяется в соответствии с равенством
Для удобства дальнейшей записи вводятся следующие параметры: ω – угол, определяемый из ΔO1FC по формуле (2); ψ – угол, определяемый из ΔO1FC в соответствии с теоремой синусов по формуле (3).
(3)
$\begin{gathered} \sin \psi = \frac{{F{{O}_{1}}\sin \omega }}{{C{{O}_{1}}}} = \frac{{{{r}_{e}}\sin \omega }}{{{{r}_{e}} - DC}}; \\ \psi = \arcsin \left( {\frac{{\sin \omega \left( {{{r}_{e}} - DC} \right)}}{{{{r}_{e}}}}} \right). \\ \end{gathered} $На основании геометрических построений (рис. 2) получено равенство (4)
(4)
${{R}_{1}} = DC = \operatorname{tg} {{\varphi }_{1}}\left( {{{S}_{o}} - {{r}_{e}}\operatorname{tg} \left( {\frac{{{{\varphi }_{1}}}}{2}} \right)} \right).$Окончательно, с учетом введенных соотношений, получена следующая система уравнений (5), по которой рассчитывается геометрически-кинематическая составляющая шероховатости поверхности:
(5)
$Rz = \left\{ \begin{gathered} \frac{{125S_{o}^{2}}}{{{{r}_{e}}}},\quad {\text{если}}\quad {{S}_{o}} \leqslant 2{{r}_{e}}\sin {{\varphi }_{1}}, \hfill \\ {{R}_{1}} - \sin {{\varphi }_{1}}\sqrt {{{{({{r}_{e}} - {{R}_{1}})}}^{2}} + r_{e}^{2} - 2{{r}_{e}}\left( {{{r}_{e}} - {{R}_{1}}} \right)\cos \left( {90^\circ - {{\varphi }_{1}} - \psi } \right)} , \hfill \\ {\text{если}}\quad 2{{r}_{e}}\sin {{\varphi }_{1}} < {{S}_{o}} \leqslant \frac{{2{{r}_{e}}}}{{\sin {{\varphi }_{1}}}}. \hfill \\ \end{gathered} \right.$При пересчете параметра Rz в параметр Ra принимается соотношение Ra = 0.2Rz [19].
Составляющая профиля шероховатости, обусловленная колебаниями инструмента относительно обрабатываемой поверхности, определяется способом, предложенным в [18], по формуле (6)
где Pz – сила резания, Н; j – жесткость технологической системы, кН/мм.В источнике [18] для расчета силы резания предлагается использовать эмпирические зависимости, приведенные в [21]. Недостатком такого подхода является отсутствие справочных данных при обработке труднообрабатывемых материалов, например, титановых сплавов.
В настоящей статье, при определении составляющей профиля шероховатости h2 используется аналитическая зависимость для расчета силы резания, приведенная в [22], которая позволяет получить данные для любых материалов с известными физическими свойствами.
Для расчета жесткости технологической системы используется зависимость, представленная в [23] (соотношение (7))
где E – модуль упругости материала резцедержателя, МПа; J – момент инерции сечения резцедержателя, мм4; H – размер резцедержателя в плоскости y0z, мм; L – вылет резца, мм.При оценке шероховатости в предлагаемой модели не учитывается пластическая деформация, т.к. она вносит несущественный вклад в общую величину шероховатости. Помимо этого, данное допущение справедливо при оценке шероховатости после токарной обработки материалов с низкой пластичностью, в частности, износостойких покрытий.
На основании полученных ранее зависимостей (5) и (6) разработана обобщенная модель оценки шероховатости Rz0 (8), которая также учитывает величину шероховатости вершины резца (в соответствии с рекомендациями в [18–20])
где Rz1 – шероховатость поверхности вершины резца, мкм.В процессе точения шероховатость вершины резца изменяется, поэтому в предлагаемой модели Rz1 принимается равным среднему арифметическому значений шероховатости поверхности вершины резца до и после обработки.
Сравнительный анализ моделей оценки шероховатости поверхностей деталей с износостойкими покрытиями. Сравнение существующей модели [18–20] и предложенной в настоящей статье обобщенной модели оценки величины шероховатости в зависимости от параметров механической обработки точением проводится в программе Matlab с использованием генератора случайных чисел. В табл. 1 представлены диапазоны исходных данных, принятые для выполнения машинного эксперимента. Для оценки возможных вариантов сочетаний “обрабатываемый материал–материал режущего инструмента” были использованы данные для обрабатываемых материалов в диапазоне от высоколегированных сталей (например, 20Х23Н18) до цветных металлов и сплавов (таких как, например, бронза БрАЖ9-4). Свойства материала режущего инструмента также были взяты в широком диапазоне – от инструментальных сталей (У8, У12 и др.) до твердых сплавов (таких как Т5К10, Т15К6 и др.).
Таблица 1.
Исходные данные для машинного эксперимента
Коэффициент теплопроводности материала резца, λр, Вт/(м °C) | 20–50 | |
Главный угол резца в плане, φ, град | 45–95 | |
Вспомогательный угол резца в плане, φ1, град | 10–40 | |
Радиус при вершине резца, r, мм | 0.05–0.80 | |
Коэффициент теплопроводности обрабатываемого материала, λ, Вт/(м °C) | 20–100 | |
Объемная теплоемкость обрабатываемого материала, cρ, МДж/(м3 °C) | 2.5–5.0 | |
Передний угол резца, γ, град. | –5–5 | |
Коэффициент трения по напряжению текучести, μ | 0.2–0.5 | |
Коэффициент трения между стружкой и передней поверхностью резца, μ1 | ||
Коэффициент трения между обработанной поверхностью заготовки и задней поверхностью резца на длине контакта, μ2 | ||
Длина контакта задней поверхности резца и обработанной поверхности заготовки, l3, мм | 0.1–0.3 | |
Напряжение текучести обрабатываемого материала, σs, МПа | 1100–1800 | |
Задний угол резца, α, град. | –15–15 | |
Температура плавления обрабатываемого материала, tплав, °C | 1300–1700 | |
Модуль упругости материала резца, Eр × 105, МПа | 1.9–2.1 | |
Размеры поперечного сечения резца | Hр, мм | 20–25 |
Bр, мм | ||
Вылет резца, Lр, мм | 30–60 | |
Предел прочности обрабатываемого материала, σв, МПа | 800–1000 | |
Шероховатость поверхности вершины резца, Rz1, мкм | 0.8–1.6 | |
Скорость резания, ${v}$, м/мин | 50–500 | |
Подача резца, s, мм/об | 0.05–0.50 | |
Глубина резания, t, мм | 0.05–1.50 |
Для большого числа машинных экспериментов целесообразно провести корреляционный анализ, согласно которому наибольшее влияние на величину шероховатости оказывают параметры φ1, r и s, причем увеличение величины вспомогательного угла в плане и подачи вызывает ухудшение шероховатости обрабатываемой поверхности, в то время как увеличение радиуса режущей кромки улучшает шероховатость.
Таким образом, предложенная в настоящей статье обобщенная модель (8) для оценки составляющей шероховатости, обусловленной геометрией и кинематикой перемещения рабочей части инструмента, имеет более рациональный вид, чем предложенная в источнике [19], т.к. в (8) в качестве исходных данных входят φ1, r и s, оказывающие наибольшее влияние на значение величины шероховатости. При этом в [18–20] к вышеуказанным параметрам добавляется также главный угол в плане, φ, который, как показал корреляционный анализ, слабо влияет на результирующее значение величины шероховатости [18–20].
Сравнение моделей шероховатости поверхностей деталей с экспериментальными данными. Был проведен сравнительный анализ предложенной обобщенной модели (8) с экспериментальными данными, приведенными в работе [24], в которой исследовалось влияние режимов обработки титанового сплава Ti-6Al-4V точением на величину шероховатости с использованием резца с пластиной из твердого сплава и углами φ = 90°, φ1 = 30°, γ = 0° и α = 15°. Данная работа была выбрана для верификации полученной зависимости, т.к. часто на основе твердых соединений титана формируют износостойкие покрытия, применяемые в различных областях машиностроения.
С целью упрощения графического представления результатов эксперимента [24] с использованием программы Matlab была проведена аппроксимация данных квадратичным полиномом. Независимыми переменными в полученном выражении (9) являются ${v}$ (м/мин), s (мм/об) и t (мм), а зависимой – шероховатость Ra (мкм).
(9)
$\begin{gathered} Ra = 0.28 - 0.0018{v} + 23.12s + 33.83t + 0.0000033{{{v}}^{2}} - 64.64{{s}^{2}} - \\ - \;1295.45{{t}^{2}} - 0.0017{v}s + 0.0125{v}t - 391.67st, \\ {{R}^{2}} = 0.9803,\quad F = 264.90 > {{F}_{0}} = 3.24, \\ \end{gathered} $Средняя относительная погрешность значений, рассчитаных на основании регрессионного уравнения, составила 3.14%.
Диапазоны изменения режимов точения приведены в табл. 2.
Таблица 2.
Диапазоны изменения независимых переменных, принятые в исследовании [24]
${v}$, м/мин | s, мм/об | t, мм | |
---|---|---|---|
min | 100 | 0.01 | 0.005 |
max | 400 | 0.04 | 0.025 |
На рис. 3–5 графически представлено сравнение результатов оценки шероховатости по зависимостям, предложенным в [18–20], разработанной обобщенной модели (8), а также эмпирической зависимости (9).
Обобщенная модель (8) и зависимость из [18–20] дают хорошую сходимость с экспериментальными данными из [24]. В предложенной обобщенной зависимости средняя погрешность результатов расчета шероховатости составила 17.81%, в зависимости из [18–20] – 22.28%, при этом среднее расхождение результатов расчета по ним составило 9.63%.
Выводы. Предложенная в настоящей статье обобщенная модель (8), используемая для оценки шероховатости поверхностей деталей с износостойкими покрытиями при токарной обработке, учитывает характеристики материала, влияющие на величину силы резания, которая, в свою очередь, оказывает влияние на величину шероховатости поверхностного слоя после точения, в то время как зависимость, предложенная в [18–20], основывается только на эмпирических данных силы резания, которые отсутствуют для современных материалов, в том числе, различных функциональных покрытий, используемых в машиностроении.
Машинный эксперимент по сравнению с существующей и вновь разработанной зависимостью показал, что в широком диапазоне исходных данных (табл. 1) результаты расчета существенно не различаются.
В обобщенной модели оценки шероховатости (8) не учитывается составляющая шероховатости, обусловленная пластическими деформациями в зоне контакта инструмента и заготовки, т.к. в процессе исследования зависимости из [18–20] было установлено, что она не оказывает существенного влияния на величину шероховатости, рассчитываемую по обобщенной модели. Как было отмечено ранее, это справедливо для хрупких материалов, к которым, в частности, относятся износостойкие покрытия.
Необходимо отметить, что предложенная модель не учитывает эксплуатационные характеристики системы деталь–покрытие, в частности, прочности сцепления, что требует дальнейших исследований в данном направлении.
Список литературы
Ковалев А.А., Краско А.С. Перспективы сокращения трудоемкости изготовления деталей машин за счет применения функциональных покрытий // Механика и машиностроение. Наука и практика. 2020. Т. 3. С. 27.
Ковалев А.А., Краско А.С. Перспективы и проблемы применения сверхзвукового плазменного напыления в условиях мелкосерийного производства // Современные материалы, техника и технология. 2020. С. 174.
Tokarev D.I., Drozdov A.A., Gulyaev M.N., Sirotenko L.D., Muratov K.R., Ablyaz T.R., Islamov V.F. Surface roughness in the machining of F-4K20 composite // Russian engineering research. 2019. V. 39. № 2. P. 167.
Philip Selvaraj D. Optimization of Surface Roughness of Duplex Stainless Steel in Dry Turning Operation Using Taguchi Technique // Materials Physics and Mechanics. 2018. V. 40. № 1. P. 63.
Alajmi M.S., Almeshal A.M. Prediction and Optimization of Surface Roughness in A Turning Process Using the ANFIS-QPSO Method // Materials. 2020. V. 13. № 13. P. 1.
Nabil K., Zahia H., Yalles M.A., Ouelaa N. Statistical analysis of surface roughness by design of experiments in hard turning // Mechanika. 2012. V. 18. № 5. P. 605.
Албагачиев А.Ю., Ковалев А.А., Краско А.С. Выбор метода упрочняющей обработки деталей машин в условиях автоматизированного мелкосерийного производства // Проблемы машиностроения и автоматизации. 2021. № 2. С. 4.
Макаров Р.В., Осколкова Е.Р. Влияние вибраций на шероховатость поверхности при точении со смазочно-охлаждающими жидкостями // Вестник Иркутского государственного технического университета. 2006. № 4–3 (28). С. 76.
Ротаренко О.Ю., Любомудров С.А. Исследование зависимости шероховатости поверхности от скорости резания при точении титановых сплавов // Неделя науки СПбГПУ (материалы научно-практической конференции). 2014. С. 228.
Некрасов В.Н., Черданцев А.О., Черданцев П.О. Исследование процесса формирования шероховатости обработанной поверхности при точении // Ползуновский вестник. 2016. № 3. С. 71.
Жуков Э.Л., Ларионова Т.А., Плавник С.Л. Методы обеспечения заданной шероховатости обрабатываемой поверхности на операциях чистового точения // Современное машиностроение. Наука и образование. 2016. № 5. С. 924.
Ярославцев В.М. Обработка газотермических покрытий резанием: учеб. пособие для вузов. М.: Изд-во МГТУ им. Н.Э. Баумана, 2013. 89 с.
Саклакова А.Е., Селина Ю.Н., Симаков М.А., Филиппов Ю.А. Экспериментальное исследование шероховатости поверхности детали из теплостойкой стали после точения режущими пластинами из твердого сплава // Решетневские чтения. 2016. Т. 1. С. 577.
Сергеев А.С., Плотников А.Л., Зайцева Н.Г. Уточненная математическая модель расчета параметра шероховатости поверхности при точении углеродистых сталей на станках с ЧПУ // Металлообработка. 2012. № 5–6 (71–72). С. 64.
Вожжов А.А. Оценка влияния относительных колебаний детали и инструмента на шероховатость поверхности в процессе фасонного точения канавок колец коллекторов // Вестник современных технологий, 2017. № 3 (7). С. 24.
Рогов В.А., Горбани С. Исследование рабочих параметров резцов для чистовой обработки // Фундаментальные исследования. 2013. № 11–3. С. 435.
Чигиринский Ю.Л., Ингеманссон А.Р., Юдкин А.Ю., Головков В.В. Анализ влияния технологических условий точения на высоту микропрофиля обработанной поверхности // Известия Волгоградского государственного технического университета. 2019. № 1 (224). С. 44.
Суслов А.Г., Горленко О.А. Экспериментально-статистический метод обеспечения качества поверхности деталей машин. М.: Машиностроение, 2003. 302 с.
Суслов А.Г. Качество поверхностного слоя деталей машин. М.: Машиностроение, 2000. 320 с.
Суслов А.Г., Дальский А.М. Научные основы технологии машиностроения. М.: Машиностроение, 2002. 684 с.
Справочник технолога-машиностроителя. В 2 т. Т. 2 / Под ред. А.С. Васильева, А.А. Кутина. 6-е изд., перераб. и доп. М.: Инновационное машиностроение, 2018. 818 с.
Воронцов А.Л., Албагачиев А.Ю., Султан-заде Н.М. Теоретические основы обработки металлов в машиностроении: монография. Старый Оскол: ТНТ, 2014. 552 с.
Безъязычный В.Ф. Основы технологии машиностроения: учебник для вузов. М.: Машиностроение, 2013. 568 с.
Aslantas K., Danish M., Hasçelik A., Mia M., Gupta M., Ginta T., Ijaz H. Investigations on Surface Roughness and ToolWear Characteristics in Micro-Turning of Ti-6Al-4V Alloy // Materials. 2020. V. 13. № 13. P. 1.
Дополнительные материалы отсутствуют.
Инструменты
Проблемы машиностроения и надежности машин