Проблемы машиностроения и надежности машин, 2023, № 1, стр. 108-112
Повышение эффективности материалорежущих станков за счет когерентной работы источника и потребителя механической мощности
А. В. Егоров 1, В. Г. Шрам 2, *, Ю. Ф. Кайзер 2, 4, А. В. Лысянников 2, 4, Ю. Н. Безбородов 2, К. С. Степанова 3, А. В. Кузнецов 2, 4, В. Л. Тюканов 2
1 Саровский физико-технический институт, филиал НИЯУ МИФИ
Саров, Россия
2 Сибирский федеральный университет
Красноярск, Россия
3 Поволжский государственный технологический университет
Йошкар-Ола, Россия
4 Красноярский государственный аграрный университет
Красноярск, Россия
* E-mail: Shram18rus@mail.ru
Поступила в редакцию 14.10.2021
После доработки 10.10.2022
Принята к публикации 20.10.2022
- EDN: ATEZVY
- DOI: 10.31857/S0235711923010030
Аннотация
Одним из возможных путей повышения эффективности функционирования сложных систем является метод когерентной работы отдельных элементов системы. Повышение эффективности работы материалорежущего оборудования возможно путем обеспечения оптимального положения между валом приводного электродвигателя и жестко связанного с ним напрямую режущего инструмента. Оптимальное взаимное положение вала приводного электродвигателя и режущего инструмента можно достичь при совмещении максимумов генерируемого и потребляемого крутящего момента. Любое отклонение взаимного положения максимума генерируемого и минимума потребляемого крутящего момента приводит к знакопеременным колебаниям крутящего момента в системе вращающихся масс “вал приводного электродвигателя–режущий инструмент”. Недостаток генерируемого крутящего момента для преодоления потребного крутящего момента ведет к увеличению скольжения приводного электродвигателя и локальному снижению коэффициента полезного действия в течение примерно 180 градусов угла поворота вала приводного электродвигателя.
Одним из возможных путей повышения эффективности функционирования сложных систем является метод когерентной работы отдельных элементов системы. В настоящее время основные работы по обеспечению когерентной работы компонентов сложных систем сосредоточены в области электроэнергетических систем [1–7].
На основе сравнения работы отдельных компонентов сложных систем и определения их когерентности разрабатываются методы контроля технического состояния механических систем [8, 9].
Когерентная работа компонентов оборудования добывающих и обрабатывающих систем практически не рассматривается.
Вопросы когерентной работы машиностроительного оборудования рассмотрены лишь компанией Форд в части когерентной работы металлообрабатывающих центров, оснащенных большим количеством режущего инструмента [10].
Основу механического обрабатывающего оборудования составляют станки, содержащие в своем составе генераторы и потребители механической мощности. Синхронизация их работы в части выработки и потребления механической мощности является одним из путей повышения эффективности материалообрабатывающего оборудования.
Настоящая статья содержит научно-техническое обоснование повышения эффективности материалорежущих станков за счет когерентной работы источника и потребителя механической мощности.
В качестве источника механической мощности в механическом материалообрабатывающем оборудовании применяются асинхронные и синхронные электрические машины. Вал электрического двигателя посредством механической передачи или напрямую соединяется с режущим инструментом. Далее в настоящей статье будем исходить из условия прямого соединения вала приводного электродвигателя с механическим режущим инструментом.
Из курса электротехники хорошо известна угловая характеристика синхронного двигателя (рис. 1).
Рис. 1.
Угловая характеристика синхронного электродвигателя: М – крутящий момент, развиваемый на валу электродвигателя; Мн – номинальный крутящий момент; Ммакс – максимальный крутящий момент; Θ – угол поворота вала двигателя.
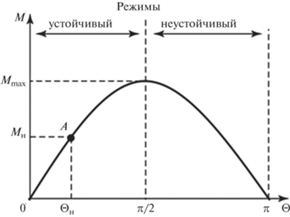
В монографии Ю.Н. Внукова [11] представлена форма колебаний силы резания (потребного крутящего момента) для условия неравномерного фрезерования с выходом соседних зубьев фрезы из зацепления с деталью (рис. 2).
Рис. 2.
График колебаний силы резания при неравномерном фрезеровании: Р – усилие резания; Тz – период зубцовой частоты фрезы; tрез – время резания; tх.х. – время холостого хода.
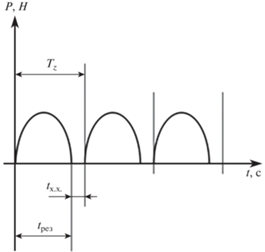
Для случая, когда один зуб фрезы выходит из зацепления, а второй сразу входит, время холостого хода будет стремиться к нулю, а колебания силы резания будут стремиться к положительному синусоидальному закону.
Сравнивая графики, представленные на рис. 1, 2 можно заметить, что генерация крутящего момента электродвигателем и потребление крутящего момента фрезой совпадают по форме. При полном совпадении по фазе колебаний генерируемого и потребляемого крутящего момента при прямом приводе режущего инструмента металлорежущего станка можно достигнуть его когерентной работы. Естественным условием работоспособности механизма является превышение или равенство по амплитуде генерируемого крутящего момента и затрачиваемого на резание материала. Также важным условием является равенство количества полюсов приводного электродвигателя количеству режущих зубьев фрезы.
С целью выявления влияния разницы положения по углу поворота максимумов кривой генерации и потребления крутящего момента на величину суммарного доступного крутящего момента в жестко сцепленной системе вращающихся масс “вал приводного двигателя–фреза” выполним математическое моделирование. Для целей моделирования будем считать, что закон изменения генерируемого и потребного крутящего момента осуществляется по синусоидальному закону. А генерируемый крутящий момент полностью расходуется на компенсацию потребного крутящего момента в режиме когерентности. Результаты моделирования представлены на рис. 3.
Рис. 3.
Влияние разницы положения по углу поворота максимумов кривой генерации и потребления крутящего момента на величину суммарного доступного крутящего момента: 1 – при угле 0°; 2 – при угле 45°; 3 – при угле 90°; 4 – при угле 135°.
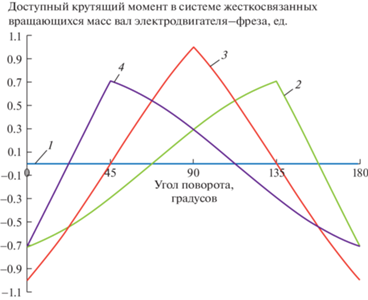
При совпадении максимума генерации и потребления крутящего момента (рис. 3) достигается наиболее стабильный режим работы с колебаниями доступного крутящего момента близкого к минимуму. Наиболее неравномерный режим работы приводного электродвигателя достигается, когда максимум генерации и максимум потребления крутящего момента сдвинуты по отношению друг к другу на угол 90°.
Любое отклонение максимума генерируемого крутящего момента приводит к знакопеременности доступного крутящего момента в смоделированной системе.
Уход в минус доступного крутящего момента для приводного электродвигателя будет означать увеличение скольжения и, как следствие, потерю коэффициента полезного действия в течение примерно 180° угла поворота ротора приводного электродвигателя.
Выводы. 1. Повышение эффективности работы материалорежущего оборудования возможно путем обеспечения оптимального положения между валом приводного электродвигателя и жестко связанного с ним напрямую режущего инструмента. 2. Оптимальное взаимное положение вала приводного электродвигателя и режущего инструмента можно достигнуть при совмещении максимумов генерируемого и потребляемого крутящего момента. 3. Любое отклонение взаимного положения максимума генерируемого и минимума потребляемого крутящего момента приводит к знакопеременным колебаниям крутящего момента в системе вращающихся масс “вал приводного электродвигателя–режущий инструмент”. 4. Недостаток генерируемого крутящего момента для преодоления потребного крутящего момента ведет к увеличению скольжения приводного электродвигателя и локальному снижению коэффициента полезного действия в течение примерно 180 градусов угла поворота вала приводного электродвигателя.
Список литературы
Benmiloud O., Arif S. Identification of Coherent Generators in Multi-Machine Power Systems // Int. Conf. on Advanced Electrical Engineering, ICAEE-2019. 2019. 9015067.
Gupta A.K., Verma K., Niazi K.R. Power system low frequency oscillations monitoring and generator coherency determination in real time // Int. Conf. on Innovative Smart Grid Technologies, ISGT Asia-2018. 2018. P. 752.
Khan S., Shariff S., Ahmad A., Saad Alam M. A Comprehensive Review on Level 2 Charging System for Electric Vehicles // Smart Science. 2018. V. 6. Iss. 3. P. 271.
Widl E., Jacobs T., Schwabeneder D., Schuelke A., Auer H. Studying the potential of multi-carrier energy distribution grids: A holistic approach // Energy. 2018. V. 153. P. 519.
Soni B.P., Saxena A., Gupta V. Online identification of coherent generators in power system by using SVM // 2017 4th Int. Conf. on Power, Control and Embedded Systems, ICPCES-2017. 2017. P. 1.
Li C., Xu J., Zhao C., Liu W. Coherency equivalence method for voltage source converter based on virtual synchronous generator. Diangong Jishu Xuebao // Transactions of China Electrotechnical Society. 2016. V. 31. Iss. 13. P. 111.
Zhang H.-B., Zheng Z.-Q., Li Z.-N., Xun G., Sun Y.-W. An analytic hierarchy process based method for identifying coherent generator groups // China Int. Conf. on Electricity Distribution, CICED, 2014. P. 490.
Pavlov A.I., Egorov A.V., Polyanin I.A., Kozlov K.E. A method for functional diagnosis of hydraulic drives of forest machinery // Int. J. of Environmental and Science Education. 2016. V. 11. Iss. 18. P. 11331.
Pavlov A.I., Tarbeev A.A., Egorov A.V., Kaizer Y.F., Matkerimov T.Y. Oscillating method for monitoring the technical condition of the hydraulic cylinders of manipulator machines // J. of Physics: Conference Series. 2020. V. 1515. Iss. 4. 042053.
Hamidieh Y.A., Seth B.B. Drill breakage detection in two spindles station in a dial machine // SAE Transactions Section 5: J. of Materials & Manufacturing. 1996. V. 105. P. 950.
Внуков Ю.Н. Автоколебания при фрезеровании тонкостенных элементов детали. Монография. Электронное издание. Запорожье: ЗНТУ, 2017. 208 с.
Дополнительные материалы отсутствуют.
Инструменты
Проблемы машиностроения и надежности машин