Проблемы машиностроения и надежности машин, 2023, № 1, стр. 97-107
Повышение эффективности дозирующей системы в упаковочных автоматах типа “FORM-FILL-SEAL” (FFS)
Б. Л. Саламандра *
Институт машиноведения им. А.А. Благонравова РАН
Москва, Россия
* E-mail: salamandra@recuper.ru
Поступила в редакцию 23.05.2022
После доработки 06.10.2022
Принята к публикации 20.10.2022
- EDN: ATAZEJ
- DOI: 10.31857/S0235711923010108
Аннотация
Предлагается ввести в конструкцию FFS-автоматов привод смещения сопел дозатора со скоростью, равной скорости перемещения ленты с отформованными емкостями. Показано, что такой привод за счет совмещения дозирующей и транспортной операций при больших дозах выведет дозирование из состава лимитирующих операций, а на порционных автоматических линиях, где дозы малые, позволит в два раза уменьшить количество необходимых каналов дозатора, одновременно увеличив интенсивность их использования. Приводится методика выбора схемы дозирования, построенной на элементах системы “Direct filling”, и определения оптимальной рядности, которая при сохранении минимального машинного цикла линии обеспечивает максимальную загрузку дозирующей системы.
Одна из основных проблем, возникающих при проектировании автоматических линий, заключается в выравнивании и минимизации времени выполнения параллельных (выполняемых одновременно) технологических операций. Именно в случае удачного решения этой проблемы проектируемая линия будет иметь максимальную производительность. Но всегда какая-то из технологических операций становится “лимитирующей” и в конечном итоге определяет цикл работы линии. При существенном превышении времени лимитирующей операции цикл работы линии приходится увеличивать, что приводит к росту времени простоя остальных технологических станций линии, и ее эффективность падает.
Существует два способа уменьшения влияния лимитирующей операции на цикл работы линии. Это: уменьшение времени выполнения операции путем совершенствования технологии (например, распараллеливание) и изменение структуры движений элементов линии, позволяющее совместить лимитирующую операцию с очередной последовательной (как правило, транспортной) операцией. В настоящей статье оба этих способа демонстрируются на примере высокопроизводительной автоматической линии для фасовки и упаковки жидких и полужидких продуктов.
Схема линии представлена на рис. 1. За один цикл на линии одновременно “обрабатывается” матрица из m × n емкостей (рис. 1б), где n – число ручьев линии; m – число рядов. При этом над этой матрицей параллельно выполняется пять технологических операций: нагрев корпусной пленки 1 в нагревателе 2, термоформовка емкостей на силовой станции 3, заполнение их продуктом дозатором 4, сварка корпусного 1 и покровного 5 материалов (герметизация емкостей) на силовой станции 6 и вырубка готовых изделий в штампе 7. Нагрев пленки и все силовые технологические операции (формовка, сварка, вырубка) не зависят от свойств дозируемого продукта, выровнены по времени за счет подбора температурных режимов и на современных линиях типа “Form-Fill-Seal” выполняются параллельно за минимальное время tmin. В результате минимальный цикл линии, в основном, формируется из двух составляющих
(1)
$T = {{t}_{{{\text{min}}}}} + {{t}_{s}} = {{t}_{{{\text{min}}}}} + \frac{{{{S}_{1}}m}}{{{{V}_{s}}}},$Рис. 1.
Функциональная схема FFS-линии для фасовки и упаковки жидких продуктов – (а); матрица емкостей на ленте, обрабатываемых за один машинный цикл на n-ручьях, m-рядной линии – (б).
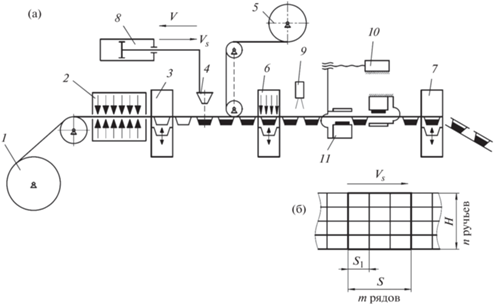
Дозирование продукта при неподвижных соплах может осуществляться только в период tmin выстоя ленты с емкостями. Однако время td выдачи дозы никак не связано с tmin, поскольку зависит от объема дозы и свойств дозируемого продукта. При дозировании жидких продуктов (например, соевого соуса) скорость истечения продукта из сопла ограничена возникновением брызг при ударе струи в донышко емкости, а при дозировании полужидких продуктов (например, меда, сливочного масла) минимальное время дозирования будет зависеть от текучести, вязкости продукта, проходных сечений каналов дозатора и выходных сопел. В результате время ${{t}_{d}}$ дозирования, как правило, существенно отличается от времени tmin выполнения основных технологических операций и никак с ним не согласовано. Для того чтобы гарантировать заполнение всех n × m емкостей, формуемых за один минимальный цикл, в настоящее время на линиях FFS “платят достаточно большую цену”: создают и используют дозатор, содержащий n × m параллельных каналов и выходных сопел. Каждый канал выдает дозу продукта в одну соответствующую емкость, которая поступит под неподвижное сопло после выполнения очередного шага S. Когда дозы большие или дозируется трудно текучий продукт, т.е. когда операция дозирования является лимитирующей, поскольку время выдачи дозы ${{t}_{d}} > {{t}_{{{\text{min}}}}}$, приходится увеличивать ${{t}_{{{\text{min}}}}}$ и время цикла T, что занижает производительность линии. При ${{t}_{d}} < {{t}_{{{\text{min}}}}}$, что характерно для порционных автоматических линий (масло, мед, соусы по 10, 15, 20 г), весь этот достаточно сложный и дорогой массив каналов дозатора простаивает значительный период времени: $\left( {{{t}_{s}} + {{t}_{{{\text{min}}}}} - {{t}_{d}}} \right)$, часто превышающий 0.5T.
Очевидно, что время работы дозатора, допускаемое в пределах минимального цикла, можно увеличить, если организовать перемещение столика с соплами11, синхронное с движением ленты с емкостями. Синхронность означает движение с одинаковой скоростью и одновременную остановку после отработки шага S. При таком совместном движении сопла будут находиться над соответствующими емкостями, и можно проводить дозирование непосредственно в процессе движения.
Для реализации синхронного движения столик с соплами можно оснастить пневмоприводом 8 (рис. 1а), который включается по сигналу от фотодатчика 9 при протягивании электроприводом 10 ленты с емкостями, зажатой захватом 11. Равенство скоростей столика и ленты достигается регулировкой дросселя, установленного на пневмоприводе 8.
Выигрыш во времени, полученный в результате совмещения операции дозирования с транспортной операцией, позволяет в случае больших доз или трудно текучих продуктов вывести дозирование из состава лимитирующих операций, а на порционных линиях, где дозы малые, смещение сопел относительно ленты с емкостями позволяет одним и тем же каналом дозатора заполнять две емкости, вдвое уменьшив количество необходимых каналов, но увеличив при этом интенсивность их использования.
Эффективность совмещения транспортной и дозирующей операций в настоящей статье определяется для двух вариантов алгоритма синхронного движения ленты с емкостями и столика с соплами.
Ι. Смещение столика на шаг S. Исходное положение: сопла расположены над пустыми емкостями.
Включение дозирования, движений ленты и столика проводится одновременно (рис. 2а, б). Скорости Vs ленты и V столика равны. После отработки шага S столик останавливается, но дозирование продолжается. После завершения дозирования и заполнения емкостей столик возвращается в исходное положение со скоростью V $ \gg $ Vs. Цикл отработан: сопла находятся над очередными пустыми емкостями.
Рис. 2.
(а) + (б) – циклограмма работы линии при смещении сопел на шаг S; (а) + (в) – то же, но при смещении на S/2.
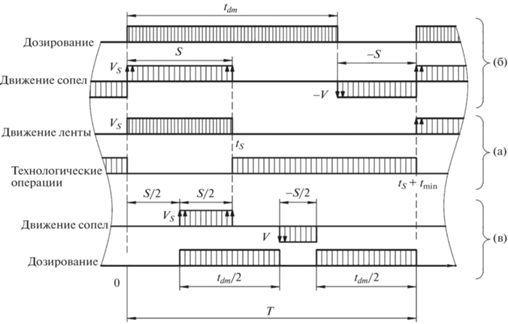
ΙΙ. Смещение столика на шаг S/2. Исходное положение: сопла расположены над заполненными емкостями.
Включается движение ленты (рис. 2а+в). После смещения емкостей на S/2 (под сопла подойдут пустые емкости) одновременно включается дозирование и синхронное (со скоростью Vs) движение сопел. Остановка ленты и столика происходит одновременно. После выполнения первого такта дозирования – емкости заполнены – столик перемещается на –S/2 со скоростью V $ \gg $ Vs в исходное положение – сопла встали над следующей группой пустых емкостей – включается второй такт дозирования, по завершении которого – цикл отработан: сопла находятся над заполненными емкостями.
Выбор смещения сопел на S/2 не случаен. При четных m все множество m × n емкостей, формируемых за один машинный цикл, разделяется на два равных подмножества, причем, в двух крайних положениях столика сопла будут располагаться над центрами емкостей каждого из подмножеств. В дальнейшем эта особенность позволит производить два такта дозирования за один машинный цикл.
При варианте Ι время ${{t}_{{dm}}}$ для выполнения дозирования максимален
а при варианте ΙΙ несколько меньше но в варианте ΙΙ уже в структуру движений столика и ленты вложено смещение сопел относительно емкостей, что позволяет при двух тактах дозирования за один цикл заполнять из каждого сопла по две емкости. Используя (1), выражения (2) и (3) можно привести к виду(4)
${\text{для варианта}}\;{\text{I}}{\kern 1pt} :\quad {{t}_{{dm}}} = {{t}_{{{\text{min}}}}} + {{S}_{1}}m\left( {\frac{1}{{{{V}_{s}}}} - \frac{1}{V}} \right);$(5)
${\text{для варианта}}\;{\text{II}}{\kern 1pt} :\quad {{t}_{{dm}}} = {{t}_{{{\text{min}}}}} + \frac{{{{S}_{1}}m}}{2}\left( {\frac{1}{{{{V}_{s}}}} - \frac{1}{V}} \right),$Значение ${{t}_{{dm}}}$ определяет максимальное время, которое за счет совмещения операций можно выделить из минимального машинного цикла T для выполнения операции дозирования. Если это время будет кратно времени ${{t}_{d}}$ излива дозы, т.е. если ${{t}_{{dm}}} = k{{t}_{d}}$, где k – число тактов дозирования, необходимых для заполнения всех n × m емкостей, то простои дозирующей системы будут минимальны, а линия будет иметь максимальную производительность. Это означает, что при любом конкретном значении ${{t}_{d}}$, зависящем от свойств дозируемого продукта, для каждого из рассматриваемых вариантов организации синхронного движения существует оптимальная рядность ${{m}_{{{\text{opt}}}}}$ линии, при которой достигается максимальная интенсивность работы дозирующей системы.
Возможности многоканальных дозаторов по быстродействию. Если время ${{t}_{{{\text{min}}}}}$ определяется только свойствами корпусного и покровного материалов, составляющих упаковку, и технологией их обработки для получения герметичной емкости, то значение ${{t}_{d}}$ зависит только от возможностей дозатора, точнее, от того, насколько быстро он может выдать требуемую дозу продукта. Наиболее быстродействующими являются дозаторы “Direct filling” [1], которые не содержат приводных цилиндров и работают от давления дозируемого продукта в напорном продуктопроводе. В отличие от традиционных дозаторов [2, 3], где в зависимости от положения 3-ходового крана последовательно выполняются этапы набора дозы из промежуточного бака и ее выдачи в выходное сопло, дозаторы “Direct filling” могут выдавать дозы практически непрерывно без задержки на набор дозы, поскольку в них каждый этап выдачи дозы всегда сопровождается набором и фиксацией дозы для следующего цикла дозирования.
В порционных FFS-линиях наиболее часто используются линейные модульные дозаторы, объединенные в пакет общим продуктопроводом и общей системой управления. В результате такой пакет из N модулей представляет собой насадку на напорный продуктопровод, преобразующую один непрерывный поток жидкости в последовательность фиксированных доз, распределенных по N или 2N каналам.
N каналов образуется в том случае, если пакет сформирован из N однотактных модулей. Каждый такой модуль (рис. 3а) имеет входной канал 1, соединенный с напорным продуктопроводом 2, и выходной канал 3, по которому продукт поступает к соплу 4. Входной канал 1 можно перекрыть управляемыми пневмоклапанами 5 и 6, а выходной канал 3 – клапанами 7 и 8. Каналы соединены между собой мерной гильзой 9, в которой между упорами 10 и 11 (один из них является микрометрическим винтом для регулирования дозы) размещен плавающий поршень 12. В исходном состоянии все клапаны 5, 6, 7, 8 закрыты, а поршень 12 находится на одном из упоров, например, на упоре 10. При открытии клапанов 5 и 7 поршень 12 под давлением продукта переместится до упора 11, выдавив соответствующую дозу продукта в выходной канал 3 и сопло 4. Закрыв клапаны 5, 7 и открыв 6, 8, получим обратное фиксированное перемещение поршня 12 и соответствующую дозу на выходе 4 модуля. Таким образом, за счет чередования закрытия и открытия клапанов на различных диагоналях устройства на одном его выходном канале формируется последовательность фиксированных доз. При этом для выдачи одной дозы и заполнения одной емкости достаточно одного такта дозирования независимо от того, на каком упоре находится поршень 12. Условное обозначение однотактного модуля, используемое на последующих рисунках, приведено на рис. 3а справа.
2N каналов получим, если пакет сформируем из двухтактных модулей. В отличие от однотактного такой модуль (рис. 3б) имеет два выходных канала 3а и 3б и соответственно два сопла 4а и 4б. В результате при последовательном закрытии и открытии клапанов на различных диагоналях модуля дозы будут выдаваться в каждый канал поочередно, и на выходе каждого канала будет формироваться последовательность доз, отделенных друг от друга одним “пустым” тактом дозирования. Это означает, что для заполнения одной емкости по любому из двух каналов модуля в общем случае необходимо затратить время, равное двум тактам дозирования. Условное обозначение двухтактного модуля показано на рис. 3б справа. В один пакет могут собираться как одно-, так и двухтактные модули.
Как видно из представленных схем, одно- и двухтактные модули почти одинаковы и мало чем отличаются по трудоемкости своего изготовления. Поэтому при создании многоканальных систем дозирования для FFS-автоматов всегда появляется желание упростить и удешевить систему за счет уменьшения числа N модулей в пакете путем замены двух однотактных модулей одним двухтактным. Однако такая замена не является эквивалентной: для заполнения двух емкостей двумя однотактными модулями достаточно одного такта дозирования (модули работают параллельно), а при использовании двухтактного модуля заполнение тех же емкостей происходит последовательно, что требует двух тактов дозирования. Поэтому замену можно проводить, если это допускает машинный цикл, т.е. если ${{t}_{d}} \leqslant {{t}_{{dm}}}{\text{/}}2$.
Существенное влияние на быстродействие выдачи дозы оказывает конструкция выходного сопла. Для дозирующей системы “Direct filling” разработаны сопла одинарного (рис. 4а) и двойного (рис. 4б) истечения, используемые для дозирования жидких продуктов (соевого соуса, растительного масла и т.п.). Сопла оснащены пневмоуправляемым клапаном 1, перекрывающим канал после завершения дозирования. Такой клапан при “схлопывании” сбрасывает последнюю каплю продукта в емкость и исключает возможность возникновения капели при быстром перемещении столика.
Основная задача, возникающая при проектировании одинарного сопла (рис. 4а) – это обеспечение максимального расхода для достижения минимального времени ${{t}_{d}}$ выдачи дозы. Здесь ограничивающим фактором является скорость истечения. При большой скорости истечения наблюдается разбрызгивание продукта при ударе струи о донышко емкости. Для устранения такого дефекта в выходной канал дозатора обычно встраивают регулируемый продуктовый дроссель, а сечение выходной насадки 2 на сопло делают максимально возможным, что ограничено силой поверхностного натяжения, удерживающей запертый клапаном 1 столб дозируемой жидкости. Поскольку эта сила, как правило, неизвестна, сопло оснащают насадками различного диаметра 6–12 мм, выбор из которых осуществляют на основе экспериментальных результатов при пробных фасовках конкретного продукта.
Задача достижения минимального времени ${{t}_{d}}$ излива дозы D кардинально решается при использовании сопла двойного истечения (рис. 4б). Здесь в одном сопле организовано два канала и при поступлении дозы D от дозатора она разделится на две части α и β. Если проходные сечения обоих каналов одинаковы и равны проходному сечению одинарного сопла, то при равной скорости истечения время ${{t}_{d}}$ излива дозы через сопло двойного истечения уменьшится в 2 раза. Однако при этом необходимо учитывать два важных обстоятельства: 1. Получение полной дозы D в одной емкости требует двух тактов дозирования; 2. Поскольку D = α + β, но α ≠ β, в силу различного сопротивления истечению в этих двух каналах, следует организовывать смещение емкостей относительно выходных насадок сопла так, чтобы объемы α и β, составляющие дозу D, попадали в одну емкость.
Разнообразие элементов системы “Direct filling” позволяет создавать различные многоканальные схемы дозирования для FFS-автоматов, отличающиеся как составом и количеством необходимых модулей, так и временем (количеством тактов) выполнения операции дозирования за один минимальный рабочий цикл. В табл. 1 приведены возможные схемы дозирования для двухрядной (m = 2, левый ряд схем) и четырехрядной (m = 4, правый ряд) автоматической линии. Каждая схема иллюстрирует процесс заполнения m емкостей, расположенных в одном ручье по рядам многорядной линии и образующим шаг S протяжки ленты за один цикл. Предполагается, что для остальных ручьев линии схема не изменяется. В двух верхних строках табл. 1 показаны схемы дозирования, в которых осуществляется синхронное смещение столика с соплами на шаг S в соответствии с вариантом Ι. Этим схемам соответствует циклограмма работы линии, представленная на рис. 2а+б. В трех нижних строках представлены схемы со смещением столика на S/2 по варианту ΙΙ – им соответствует циклограмма на рис. 2а+в. В каждой ячейке табл. 1 для представленной в ней схемы указаны: количество k тактов дозирования, которое необходимо выполнить за один машинный цикл; общее число K каналов дозатора, равное числу одинарных сопел для заполнения n × m емкостей; количество M задействованных в схеме модулей, при этом не делается различия между одно- и двухтактными модулями, поскольку их габариты и трудоемкость изготовления примерно одинаковы, а при проектировании линии важны габариты пакета модулей и его общая стоимость. При расчете численных значений M и K предполагается, что линия 4-ручьевая, т.е. n = 4.
Таблица 1
Двухрядная линия (m = 2) | Четырехрядная линия (m = 4) | |
---|---|---|
Смещение сопел на S (вариант I) | ![]() |
![]() |
![]() |
![]() |
|
Смещение сопел на S/2 (вариант II) | ![]() |
![]() |
![]() |
![]() |
|
![]() |
![]() |
Схемы в верхней строке табл. 1 по количеству используемых каналов полностью соответствуют традиционному построению дозирующих систем для FFS-линий. В них заполнение всех n × m емкостей проводится за один такт. Поэтому увеличенное время ${{t}_{{dm}}} \approx {{t}_{d}}$, полученное по (4) за счет совмещения операций, позволяет на существующих линиях расширить диапазон дозируемых объемов при сохранении минимального машинного цикла. Если ${{t}_{d}} \approx {{t}_{{dm}}}{\text{/}}2$, то при использовании двухтактных модулей системы “Direct filling” (k = 2 – вторая строка табл. 1), кроме расширения диапазона доз, достигается двухкратное уменьшение числа M модулей в пакете.
При синхронном движении сопел на длине S/2 перемещения ленты (схемы в третьей строке таблицы) число тактов k = 2, а увеличенное время ${{t}_{{dm}}} \approx 2{{t}_{d}}$, полученное по (5) в результате совмещения операций, позволяет в два раза уменьшить число необходимых каналов K и модулей M. Переход с однотактных модулей на двухтактные (четвертая строка табл. 1) увеличивает число необходимых тактов до k = 4 и, если допустимо условие ${{t}_{d}} \approx {{t}_{{dm}}}{\text{/}}4$, то число модулей в пакете уменьшается в четыре раза. Если же ${{t}_{d}} > {{t}_{{dm}}}{\text{/}}2$ для двухрядной линии или ${{t}_{d}} > {{t}_{{dm}}}{\text{/}}4$ для четырехрядной, то можно сохранить все эти преимущества, существенно уменьшив время ${{t}_{d}}$ излива дозы за счет распараллеливания операции дозирования путем замены одинарных сопел на сопла двойного истечения (схемы в нижней строке табл. 1).
Из приведенного описания понятно, что схемы, показанные в верхней части таблицы, целесообразно применять при больших дозах D > 50 мл. При анализе схем, расположенных ниже, видно, что растет число k тактов дозирования, необходимое для заполнения n ⋅ m емкостей, что ограничивает допустимое время ${{t}_{d}}$ излива дозы. Поэтому схемы, представленные в нижней части таблицы, целесообразно использовать в порционных линиях FFS, которые, в основном, производят продукцию с малой дозировкой по 10–40 мл. Именно на порционных линиях достигается максимальный эффект от введения синхронного смещения сопел на S/2: увеличение производительности линии при одновременном уменьшении числа K необходимых каналов дозатора. Тем не менее нет ясности в том, какую схему дозирования следует реализовывать на автоматической линии, когда задана конкретная доза конкретного продукта.
Методика выбора схемы дозирования и определения оптимальной рядности ${{m}_{{{\text{opt}}}}}$ автоматической линии демонстрируется на конкретном примере адаптации линии мод. АЛБ165 производства фирмы “Рекупер” [4] для изготовления порционных упаковок соевого соуса. Заказчиком линии заданы объем дозы продукта в упаковке D = 40 мл и ее размеры: длина S1 = 70 мм и ширина H = 60 мм. По опыту и экспериментальным данным, накопленным фирмой “Рекупер” при работе с соевым соусом, известны следующие параметры, зависящие от свойств дозируемого продукта: Vs = 100 мм/с – максимальная скорость ленты с емкостями, при которой отсутствует выплескивание продукта из емкости на этапах разгона и торможения; Q = 30 мл/с – максимальная скорость спокойного (без разбрызгивания) истечения соуса из сопла Ø 8 мм. Этих данных достаточно для определения: числа ручьев линии n = 240/H = 4, где 240 – ширина ленты, применяемой в линиях АЛБ165 для формовки емкостей; времени выдачи дозы ${{t}_{d}} = D{\text{/}}Q$ = 1.33 с; при использовании сопел двойного истечения ${{t}_{d}}$ уменьшается до 0.66 с. Для серийной линии АЛБ165 известно минимальное время выполнения технологических операций ${{t}_{{{\text{min}}}}} = 2.0$ с.
Выбор схемы дозирования и определения ${{m}_{{{\text{opt}}}}}$ базируется на сравнении времени выдачи дозы ${{t}_{d}}$ со временем дозирования [${{t}_{d}}$], которое допускается минимальным машинным циклом при различной рядности m и возможных количествах k тактов дозирования. В табл. 2 для приведенных выше данных показаны результаты расчетов T по формуле (1), соответствующие им значения проектной производительности линии P = 3600 × n × m/T и допускаемые времена дозирования $\left[ {{{t}_{d}}} \right] = {{t}_{{dm}}}{\text{/}}k$, вычисленные по (4) для варианта Ι и по (5) для варианта ΙΙ организации синхронного движения. При этом было принято, что скорость возвратного движения столика с соплами V = 2Vs.
Таблица 2
Число рядов m | Минимальное время цикла T, с | Производи-тельность линии P, шт./ч | Допускаемое время [${{t}_{d}}$] дозирования | ||||
---|---|---|---|---|---|---|---|
для варианта Ι | для варианта ΙΙ | ||||||
k = 1 | k = 2 | k = 4 | k = 2 | k = 4 | |||
1 | 2.7 | 5330 | 2.35 | 1.175 | 0.5875 | – | – |
2 | 3.4 | 8470 | 2.70 | 1.350 | 0.675 | 1.175 | 0.5875 |
4 | 4.8 | 12 000 | 3.40 | 1.70 | 0.850 | 1.350 | 0.6750 |
6 | 6.2 | 13 935 | 4.10 | 2.05 | 1.025 | 1.525 | 0.7625 |
8 | 7.6 | 15 155 | 4.80 | 2.40 | 1.20 | 1.70 | 0.850 |
При синхронном смещении сопел (табл. 2) на шаг S (вариант Ι) оптимальной для производства упаковок соевого соуса по 40 мл является двухрядная линия $\left( {{{m}_{{{\text{opt}}}}} = 2} \right)$ с двумя тактами дозирования (k = 2). Этим параметрам соответствует схема, показанная в табл. 1 во второй строке слева. Здесь под оптимальностью понимается максимальная загруженность дозатора ([${{t}_{d}}$] = 1.35 ≈ ${{t}_{d}}$ = 1.33) при минимальном машинном цикле T = 3.4 с, что обеспечивает производительность P = 8470 уп./ч. Линия должна быть оснащена пакетом из n × m/2 = 4 двухтактных модулей.
При варианте ΙΙ (смещение столика на S/2) оптимальной $\left( {\left[ {{{t}_{d}}} \right] \approx {{t}_{d}}} \right)$ является 4-рядная линия с k = 2, схема дозирования для которой представлена в табл. 1 в третьей строке справа. Линия имеет минимальный цикл T = 4.8 с, производительность P = 12 000 уп./ч и дозатор, состоящий из n × m/2 = 8 однотактных модулей. При необходимости уменьшить пакет можно воспользоваться соплами двойного истечения. Тогда для рассматриваемой задачи время ${{t}_{d}}$ станет равным 0.66 с, для которого, как следует из табл. 2, ${{m}_{{{\text{opt}}}}} = 4$ при k = 4. Как следует из схемы табл. 1 (нижняя строка справа), удовлетворяющей этим условиям, для обеспечения производительности линии в 12 000 уп./ч достаточно пакета из n × m/4 = 4 двухтактных модулей.
Найденная оптимальная схема линии с ${{m}_{{{\text{opt}}}}} = 4$ и k = 2, имеющая производительность P = 12 000 уп./ч, по количеству и номенклатуре используемых элементов дозатора полностью совпадает с традиционной схемой построения FFS-линий (сравните со схемой в верхней строке табл. 1, слева: m = 2, k = 1). В обоих случаях необходим пакет из 8-ми однотактных модулей. Однако для традиционной схемы P = 8470 уп./ч. Такое существенное увеличение производительности линии на 42% при равном инструментальном обеспечении обусловлено только повышенной интенсивностью использования дозирующей системы.
Список литературы
Саламандра Б.Л., Тывес Л.И., Саламандра К.Б., Корендясев Г.К. Direct filling – технология порционного дозирования вязких продуктов от напорного продуктопровода // Проблемы машиностроения и надежности машин. 2013. № 6. С. 71.
Крайнев А.Ф. Машиноведение на языке схем, рисунков и чертежей. Книга 1. Технология, машины и оборудование. М.: Издательский дом “Спектр”, 2010.
Финкельштейн С.М. Автоматические дозаторы для жидкостей // Автоматизация производственных процессов. Вып. IV. М.: Наука, 1964. С. 68.
Рекупер – Производство фасовочно-упаковочного оборудования URL: http://Recuper.ru/
Дополнительные материалы отсутствуют.
Инструменты
Проблемы машиностроения и надежности машин