Проблемы машиностроения и надежности машин, 2023, № 1, стр. 86-96
Разработка способа получения алюминиевых покрытий
М. А. Марков 1, Д. А. Геращенков 1, И. Н. Кравченко 2, Ю. А. Кузнецов 3, А. Д. Быкова 1, *, А. Н. Беляков 1, С. К. Тойгамбаев 4
1 Санкт-Петербургский государственный технологический институт (технический университет)
Санкт-Петербург, Россия
2 Институт машиноведения им. А.А. Благонравова РАН
Москва, Россия
3 Орловский государственный аграрный университет им. Н.В. Парахина
Орел, Россия
4 Российский государственный аграрный университет – МСХА им. К.А. Тимирязева
Москва, Россия
* E-mail: bykova.ad@gmail.com
Поступила в редакцию 01.09.2022
После доработки 14.10.2022
Принята к публикации 20.10.2022
- EDN: ASZBJC
- DOI: 10.31857/S0235711923010091
Аннотация
В представленном исследовании разработаны практические рекомендации по получению алюминиевых покрытий методом “холодного” газодинамического напыления, а так же по способам упрочнения алюминиевых покрытий керамическим компонентом с формированием градиентной структуры. Полученные металлокерамические покрытия имеют следующие ключевые параметры оптимизации: высокие (более 70 МПа) показатели адгезионной прочности, высокий уровень твердости по Виккерсу (более 480 МПа) и низкое значение пористости (менее 0.5%). Данные функционально-градиентные покрытия можно использовать для защиты элементов и узлов машиностроительной техники от износа.
На сегодняшний день существует большое количество способов нанесения функциональных покрытий на металлическую основу, среди которых наиболее распространенными являются газоплазменные и плазменные методы [1–3].
При использовании термических методов возникает вероятность неконтролируемого изменения фазового и химического состава напыляемого материала в высокотемпературном потоке, что может привести к корректировке задаваемых свойств покрытий, к невозможности получения наноструктурных функциональных составляющих в формируемых слоях [4–7], что является негативным фактором.
В настоящей статье для получения функциональных покрытий предложен и выделен прогрессивно развивающийся метод “холодного” газодинамического напыления (ХГДН), который обладает следующими преимуществами: 1) температура частиц напыляемого материала в гетерофазном потоке не превышает 100°С, поэтому не происходит существенных фазовых и структурных превращений; 2) возможность получения покрытий заданной толщины от 50 мкм до нескольких миллиметров.
Методом ХГДН возможно наносить пластичные (металлические) порошковые материалы. Наиболее перспективно метод ХГДН применять для получения алюминиевых покрытий. В частности, такие покрытия заданной толщины от 100 мкм и более, можно использовать как прекурсоры, для формирования защитных керамических покрытий методом микродугового оксидирования [8–10].
Практика показывает, что добавление твердого керамического нанокомпонента в структуру алюминиевого покрытия позволяет существенно повысить его твердость. Поэтому получение наноструктурированных покрытий на основе алюминия с помощью метода ХГДН является весьма перспективным для защиты узлов и деталей машиностроения от механических воздействий [11].
Цель настоящей статьи – разработка практических рекомендаций по получению алюминиевых покрытий методом ХГДН, а также по способам упрочнения алюминиевых покрытий керамическим компонентом с формированием градиентной структуры.
Объект и методика исследований. Для осуществления “холодного” газодинамического напыления металлических и керамических порошков, представленных в статье, была использована установка типа “Димет-403”. На рис. 1 представлена схема работы установки.
При работе установки сжатый воздух (рабочий газ) через регулятор давления подается в камеру омического нагревателя, в которой разогревается до заданной температуры и подается в сверхзвуковое сопло. Одновременно напыляемый порошок из дозатора подается в зону сопла, захватывается проходящим воздухом, и на выходе сверхзвукового сопла формируется высокоскоростная струя смеси горячего воздуха с порошком.
Таким образом, порошок, приобретающий высокую кинетическую энергию, “набегает” на металлическую подложку. Условия взаимодействия этих составляющих определяют механизм закрепления металлической частицы на подложке, уровень адгезионной и когезионной прочности, а также условия наращивания покрытия по толщине.
Скорость частиц в гетерофазном потоке измерялась по методике, описанной в работе [12].
Исследование микротвердости покрытий проводилось на микротвердомере типа ПМТ-3М.
Измерение дисперсности порошковых материалов проводилось на лазерном дифракционном анализаторе “Malvern Mastersizer 2000” и лазерном дифракционном анализаторе наночастиц “Zetasizer Nano”. Определение адгезионной прочности покрытий осуществлялось штифтовым методом на универсальной разрывной машине Instron 1000.
Морфологию покрытий исследовали методами сканирующей электронной микроскопии и микрорентгеноспектрального анализа на исследовательском комплексе TTSCAN Vega. Фазовый состав покрытий определяли на рентгеновском дифрактометре D8 Advance фирмы Bruker (Германия) с использованием Cu Kα-излучения в гониометрии Брегга–Брентано, открытую пористость покрытий – на оптическом микроскопе Axio Observer А1m (Carl Zeiss) в сертифицированной программе AxioVision Rel. 4.8.
Результаты исследований. “Холодное” газодинамическое напыление алюминиевых порошков и их композиций на металлической подложке позволяет сформировать функциональные покрытия, которые в том числе можно использовать и как прекурсоры в качестве подслоя для осуществления микродугового оксидирования. Для реализации технологии ХГДН необходимо использовать полезный фракционный состав порошков в диапазоне 10–60 мкм. Практические эксперименты показывают, что легкие металлические частицы диаметром менее 10 мкм не обладают достаточной кинетической энергией для закрепления на твердой поверхности. В то время как тяжелые частицы диаметром более 60 мкм ухудшают прочность сцепления.
Технология ХГДН позволяет варьировать температуру рабочего газа 0–600°С. Если в качестве рабочего газа используется воздушная среда, то можно наблюдать следующую зависимость, а именно изменение его скорости под действием термического расширения (рис. 2).
При холодном напылении алюминиевых (и прочих металлических) порошков рационально использовать технологическую добавку – крупнозернистый корунд. В процессе напыления технологическая добавка повышает когезию формируемого покрытия за счет удаления природной оксидной пленки и прочих примесей с поверхности закрепленных алюминиевых частиц.
Практические результаты экспериментов показывают, что на прочность сцепления формируемых покрытий помимо фракционного состава влияют основные технологические характеристики процесса – температура и давление воздуха (рис. 3). Для напыления в данном случае был использован алюминиевый порошок А-80-13 с технологической корундовой связкой.
Рис. 3.
Изменение прочности сцепления алюминиевых покрытий от режимов ХГДН: (а) – от фракции порошкового материала; (б) – от давления воздуха; (в) – от температуры нагрева воздуха; 1 – алюминиевая основа; 2 – стальная основа.

Из представленных графиков видно, что повышение давления воздуха при понижении его температуры, приводит к улучшению адгезии формируемых алюминиевых покрытий.
В рамках исследования рассмотрим результаты по ХГДН алюминиевого порошка с технологической добавкой крупнозернистого корунда, и без нее (табл. 1).
Таблица 1.
Порошки для ХГДН
Порошок | Содержание алюминия фракцией 20–60 мкм, % мас. | Содержание корунда фракцией 50–100 мкм, % мас. |
---|---|---|
АСД-1 | 100 | 0 |
Композиция (АСД-1 + корунд) | 70 | 30 |
Для осуществления напыления порошкового материала газовый поток оснащен регулятором подачи. В табл. 2 представлены результаты определения расхода порошка в зависимости от положения регулятора установки стандарта “Димет”.
Таблица 2.
Осуществление расхода порошка
Порошок | Положение регулятора, у.ед. | Расход порошка, г/с |
---|---|---|
АСД-1 | 3.0 | 0.26 |
3.5 | 0.29 | |
4.0 | 0.38 | |
5.0 | 0.71 | |
5.5 | 0.93 | |
6.0 | 1.05 | |
6.5 | 1.05 | |
Композиция | 3.0 | 0.17 |
3.5 | 0.31 | |
4.0 | 0.40 | |
4.5 | 0.44 | |
5.0 | 0.52 | |
5.5 | 0.67 | |
6.0 | 0.97 | |
6.5 | 1.03 |
Данные в табл. 2 показывают, что расход порошков является индивидуальным параметром, привязанным к конкретному типу порошкового материала и его геометрической форме.
Принимая во внимание тот факт, что при расходе порошка свыше 1 г/с существенным образом повышается его коэффициент использования, рационально ограничить диапазон работы регулятора до указанных значений в диапазоне 3–6.5 у.ед.
Для осуществления эксперимента на плоские подложки из стали марки Ст3 были нанесены ХГДН-дорожки (рис. 4) по следующим технологическим режимам: скорость перемещения газового потока (или сопла) изменялась в диапазоне 10–90 мм/с; путь газового потока (или расстояние между соплом и подложкой) составило 10 мм; скорость газового потока составила 550 мм/с.
Рис. 4.
Формирование покрытий из порошковых материалов: (а) – формирование покрытий на плоских образцах; (б) – применение роботизированной системы; (в) – покрытие в поперечном сечении, композиция алюминия с корундом (расход порошка 0.52 г/с, скорость 10 мм/с).
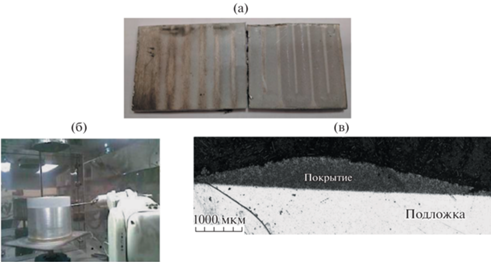
На рис. 5 для сравнения приведены профили дорожек напыления в зависимости от скорости перемещения газового потока при сопоставимом расходе алюминиевых порошков двух составов.
Рис. 5.
Сравнение толщин дорожек ХГДН: (а) – АСД-1 (расход порошка 0.29 г/с); (б) – композиция (расход порошка 0.32 г/с); (в) – АСД-1 (расход порошка 0.71 г/с); (г) – композиция (расход порошка 0.67 г/с); (д) – АСД-1 (расход порошка 1.05 г/с); (е) – композиция (расход порошка 1.03 г/с). 1 – 90 мм/с; 2 – 70 мм/с; 3 – 50 мм/с; 4 – 30 мм/с; 5 – 10 мм/с.
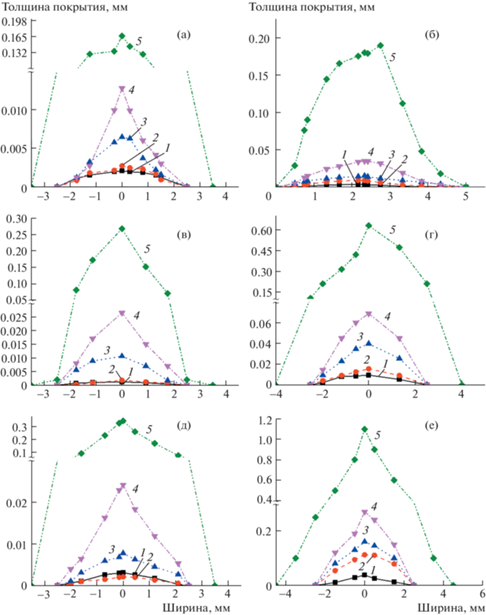
Представленные рисунки демонстрируют положительный вклад введения корундовой связки, которая приводит к повышению толщины формируемого покрытия, что оптимизирует технологию ХГДН алюминиевых порошков в части коэффициента использования. Однако из-за различной скорости движения керамических и металлических частиц для соответствующих профилей дорожек наблюдается отклонение от симметричности.
Серия экспериментов позволяет говорить о том, что толщину ХГДН алюминиевых покрытий можно регулировать, используя такие параметры, как: расход порошка; скорость движения или сканирования газового потока; температура среды.
При использовании роботизированного комплекса, на основании анализа ширины профилей дорожек, можно осуществлять смещение шага сканирования, оптимизируя тем самым возможность понижения пористости формируемого покрытия.
В качестве примера варьирования технологического решения по выбору конкретных оптимальных режимов ХГДН алюминиевых покрытий на основе экспериментальных результатов приведены следующие режимы: 1) задаваемая толщина покрытия 500 мкм по первому варианту: исходные порошки АСД-1+электрокорунд; расход дозатора 5 (рис. 1), что соответствует расходу композиционного порошка 0.52 г/с; скорость перемещения газового потока (сопла) 10 мм/с, шаг сканирования 3 мм, количество проходов в один слой; температурный режим 300°С, что соответствует скорости газового потока 550 г/с; расстояние от подложки до сопла – 10 мм; 2) задаваемая толщина покрытия 500 мкм по второму варианту: исходные порошки АСД-1+электрокорунд; расход дозатора 6 (рис. 1), что соответствует расходу композиционного порошка 0.97 г/с; скорость перемещения газового потока (сопла) 30 мм/с, шаг сканирования 2 мм; количество проходов в два слоя; температурный режим 300°С, что соответствует скорости газового потока 550 г/с; расстояние от подложки до сопла – 10 мм.
На следующем этапе работы продемонстрированы результаты по упрочнению алюминиевых покрытий за счет модифицирования ультрадисперсными частицами корунда фракцией 0.1–1.0 мкм с использованием системы раздельных дозаторов с параллельной подачей порошка (рис. 6). Выбор корунда в качестве упрочняющей компоненты дополнительно обоснован тем фактом, что это наиболее нейтральный компонент к алюминию для осуществления финишной обработки покрытия методом микродугового оксидирования.
На первой стадии предварительно вводят в сверхзвуковой поток воздуха армирующие ультрадисперсные частицы Al2O3, фракцией 0.1–1.0 мкм из дозатора 1, и проводят обработку поверхности напыляемого изделия до образования ювенильной поверхности, скорость гетерофазного потока составляет 300–400 м/с. На второй стадии, при скоростях гетерофазного потока 400–650 м/с, на ювенильную поверхность напыляемого изделия наносят порошок аллюминия для получения промежуточного слоя из дозатора 2. На третьей стадии проводят нанесение функционально-градиентного покрытия из одновременно работающих дозаторов 1 и 2, при увеличении содержания Al2O3 в покрытии от промежуточного слоя к поверхности в пределах 0.1–30 мас. % по линейной зависимости, скорость при этом составляет 400–650 м/с (рис. 7а).
Рис. 7.
Схемы реализации ХГДН: (а) – использование двух дозаторов; (б) – использование трех дозаторов; 1 – дозатор 1; 2 – дозатор 2; 3 – дозатор 3.
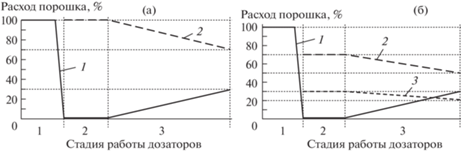
Для понижения пористости формируемого упрочненного покрытия рационально вводить наноразмерные или микроразмерные алюминиевые частицы с использованием третьего параллельно работающего дозатора. Напыление проходит по следующей схеме. На первой стадии дозатором 1 проводится обработка подложки до образования ювенильной поверхности. Затем дозатором 2 и 3 напыляется монослой чистого материала основы при скорости потока 400–650 м/с (рис. 7б).
Фактически предложенный вариант напыления схематично можно представить на рис. 8.
Общий вид формируемого упрочненного металлокерамического покрытия на основе алюминия в поперечном сечении, с использованием элементной тепловой карты (применение EBSD-анализа) представлен на рис. 9а. Можно наблюдать фактически задаваемую градиентную структуру с постепенным повышением содержания керамического компонента от металлической основы к поверхности покрытия. Для идентификации фазового состава керамики приведены результаты рентгенофазового анализа поверхностного слоя покрытия (рис. 9б).
Рис. 9.
Покрытие Al-Al2O3: (а) – поперечное сечение покрытия, цветовое распределение элементов по кислороду и алюминию; (б) – рентгенограмма поверхности.
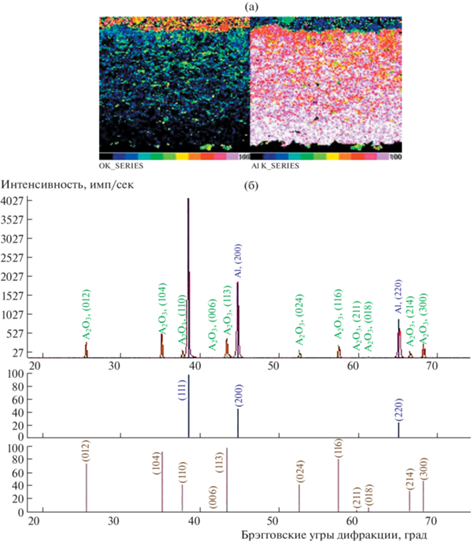
Предлагаемый способ создания функционально-градиентного покрытия обладает признаками научной новизны по следующим двум параметрам: 1) химический и фазовый состав может быть изменен по заданному закону; 2) модифицирование мелкодисперсными частицами приводит к формированию наиболее плотной упаковки.
При использовании в качестве порошка основы материала, соответствующего химическому составу подложки, обеспечивается минимальное изменение коэффициента термического расширения в полученных слоях градиентного покрытия, что обеспечивает высокую адгезионную прочность наносимого дисперсного материала. Полученные результаты сведены в табл. 3.
Таблица 3.
Свойства покрытий
Стадии процесса напыления | Скорость гетерофазного потока, м/с | Свойства покрытия | ||
---|---|---|---|---|
адгезионная прочность, σ ± 5, МПа | твердость по Виккерсу, HV ± 10, МПа | пористость, П ± 0.1, % | ||
1 стадия (нано Al2O3) | 300–400 | достижение ювенильной поверхности подложки | ||
2 стадия (микро Al) | 400 | 45 | 60 | 4.0 |
500 | 50 | 85 | 4.2 | |
600 | 55 | 120 | 4.0 | |
650 | 65 | 125 | 3.8 | |
3 стадия (микро Al, нано Al, нано Al2O3) | 400 | 72 | 410 | 0.5 |
500 | 74 | 435 | 0.4 | |
600 | 72 | 490 | 0.2 | |
650 | 70 | 480 | 0.1 |
Полученные покрытия (табл. 3) имеют следующие ключевые параметры оптимизации: высокие (более 70 МПа) показатели адгезионной прочности, высокий уровень твердости по Виккерсу (более 480 МПа) и низкое значение пористости (менее 0.5%). Разработанные функционально-градиентные покрытия могут быть использованы для защиты элементов и узлов машиностроительной техники от износа.
Выводы. 1. Экспериментально показано, что на прочность сцепления алюминиевых покрытий, полученных методом “холодного” газодинамического напыления, влияют следующие параметры: фракционный состав порошков, температура и давление рабочего газового потока. 2. Экспериментально показано, что толщину алюминиевых покрытий, полученных методом “холодного” газодинамического напыления, можно задавать, регулируя следующие параметры: расход порошка, скорость движения или сканирования газового потока, температура среды. 3. Продемонстрированы практические результаты по упрочнению алюминиевых покрытий, полученных методом “холодного” газодинамического напыления, за счет введения в газовый поток мелкодисперсных частиц алюминия (повышение адгезионной прочности и понижение пористости) и оксида алюминия (повышение твердости).
Список литературы
Алхимов А.П., Клинков С.В., Косарев В.Ф., Фомин В.М. Холодное газодинамическое напыление. Теория и практика. М.: Физматлит, 2010, 536 p.
Irissou E., Legoux J.-G., Arsenault B., Moreau C. Investigation of Al-Al2O3 Cold Spray Coating // Thermal Spray Technol. 2007. T. 16. № 5–6. P. 661.
Кравченко И.Н., Пузряков А.Ф., Бобряшов Е.М., Пузряков А.А. Плазменные методы упрочнения и восстановления рабочих органов дорожно-строительных и почвообрабатывающих машин. М.: Эко-Пресс, 2013. 328 с.
Meydanoglu O., Jodoin B., Kayali E.S. Microstructure, mechanical properties and corrosion performance of 7075 Al matrix ceramic particle reinforced composite coatings produced by the cold gas dynamic spraying process // Surface and Coatings Technology. 2013. V. 235. P. 108.
Guo X., Zhang G., Li W.Y., Dembinski L., Gao Y., Liao H., Coddet C. Microstructure, microhardness and dry friction behavior of cold-sprayed tin bronze coatings // Applied Surface Science. 2007. T. 254. № 5. P. 1482.
Li W.-Y., Li C.-J., Liao H., Coddet C. Effect of heat treatment on the microstructure and microhardness of cold-sprayed tin bronze coating // Applied Surface Science. 2007. T. 253. № 14. P. 5967.
Кудинов В.В., Бобров Г.В. Нанесение покрытий напылением. Теория, технология и оборудование. М.: Металлургия, 1992. 432 p.
Gerashchenkov D.A., Askinazi A.Y., Fedoseev M.L., Gerashchenkova E.Y., Makarov A.M. Formation of Intermetallic Phases in Functional Coatings Prepared by Cold Gas-Dynamic Spraying // Metal Science and Heat Treatment. 2020. V. 62 (1–2). P. 90.
Geraschenkov D.A., Makarov A.M., Geraschenkova E.Y., Vasiliev A.F. Obtaining Functional Intermetallic Ni–Ti Coatings by Heterophase Transfer Combined with Laser Treatment // Inorganic Materials: Applied Research. 2019. V. 10 (6). P. 1378.
Геращенков Д.А., Васильев А.Ф., Фармаковский Б.В., Машек А.Ч. Исследование температуры потока в процессе холодного газодинамического напыления функциональных покрытий // Вопросы материаловедения. 2014. № 1 (77). С. 87.
Markov M.A., Bykova A.D., Krasikov A.V., Farmakovskii B.V., Gerashchenkov D.A. Formation of Wear- and Corrosion-Resistant Coatings by the Microarc Oxidation of Aluminum // Refractories and Industrial Ceramics. 2018. V. 59. № 2. P. 207.
Фармаковский Б.В., Быстров Р.Ю., Васильев А.Ф. и др. РФ Патент 2362839, 2009.
Дополнительные материалы отсутствуют.
Инструменты
Проблемы машиностроения и надежности машин