Проблемы машиностроения и надежности машин, 2023, № 1, стр. 75-85
Комбинация сдвиговой и ротационной деформаций – эффективный процесс получения ультрамелкозернистых полуфабрикатов из жаропрочных сплавов
Ф. З. Утяшев 1, Р. Ю. Сухоруков 2, **, А. К. Галимов 3, Л. В. Гаврилина 2, *
1 Институт проблем сверхпластичности металлов РАН
Уфа, Россия
2 Институт машиноведения им. А.А. Благонравова РАН
Москва, Россия
3 Уфимский государственный авиационный технический университет
Уфа, Россия
** E-mail: labutps@yandex.ru
* E-mail: griboedova04@mail.ru
Поступила в редакцию 29.07.2022
После доработки 11.10.2022
Принята к публикации 20.10.2022
- EDN: ASRWIS
- DOI: 10.31857/S0235711923010133
Аннотация
При изготовлении дисков газотурбинных двигателей из жаропрочных суперсплавов на основе никеля, железа и титана используют сверхпластическую деформацию ультрамелкозернистых полуфабрикатов. Эта технология основана на “гаторайзинг-процессе”, которую реализуют, используя мощные горизонтальные гидропресса для изготовления ультрамелкозернистых прутков и вакуумно-штамповочные комплексы для изготовления из прутков дисков в безокислительной атмосфере. В настоящей статье рассматриваются теоретические и практические предпосылки разработки эффективного деформационного процесса получения ультрамелкозернистой структуры в жаропрочных сплавах. Показаны технологические преимущества использования комбинированных методов, сочетающие сдвиговую и ротационную компоненты деформации для формирования ультрамелкозернистой структуры в крупногабаритных заготовках. На примере осадки (или растяжения) с кручением определено напряженно-деформированное состояние материала и энергосиловые параметры деформирования, а также конструкционно-технологические особенности оснастки, обеспечивающие измельчение структуры в прутках и дисках.
В “гаторайзинг-процессе” для получения сверхпластичных ультрамелкозернистых (УМЗ) полуфабрикатов слитки или порошковые заготовки подвергают горячему прессованию с большими степенями деформации [1]. В России был разработан менее дорогостоящий метод изготовления таких изделий, названный деформационно-термической обработкой (ДТО) [2]. Этот метод включает осадку цилиндрической заготовки в режиме сверхпластичности с целью получения УМЗ-шайбы диаметром 450–550 мм, из которой затем в состоянии сверхпластичности раскатывали диск газотурбинного двигателя (ГТД) диаметром 600–800 мм. При изготовлении шайбы штамп нагревают на 100–150°C ниже температуры деформации. Исходную цилиндрическую заготовку для предотвращения охлаждения оборачивают коалиновым полотном и помещают в теплоизолирующий контейнер из нержавеющей стали. Штамповку заготовки выполняют за несколько переходов с промежуточными рекристаллизационными отжигами. Большое количество операций и невысокий коэффициент использования металла из-за образования поверхностных трещин, а также ограниченная стойкость изотермического штампа, выполненного из жаропрочного сплава ЖС6У, стали причиной поиска новых технических решений, позволяющих повысить эффективность метода ДТО [3–6].
Для получения УМЗ-структуры (вплоть до нанометрических размеров зерен) в металлах и сплавах применяют методы интенсивной пластической деформации (ИПД), позволяющие накапливать чрезвычайно большие деформации в заготовках. Исследования последних лет [7, 8] показали, что для измельчения структуры при ИПД важное значение имеет немонотонное деформирование, при котором активно изменяют ориентацию осей тензора деформации. Максимальные размеры заготовок с УМЗ-структурой субмикрокристаллического диапазона на примере титанового сплава ВТ6, полученные таким методом ИПД как всесторонняя ковка не превышают 150–200 мм. При этом потребовались десятки переходов и промежуточные подогревы сплава. Очевидно, что с увеличением размеров заготовок, из которых можно изготавливать диски, валы и кольца ГТД больших диаметров, потребуется увеличение числа переходов и автоматизация процесса всесторонней ковки [9].
В то же время известен менее трудоемкий и автоматизируемый метод ИПД – кручение под давлением (КД). Этот метод позволяет измельчать структуру во многих материалах, включая высокопрочные и труднодеформируемые жаропрочные сплавы. Измельчение зерен происходит вследствие относительно небольшой величины осадки диска и существенно большей ротационной деформации. Аналогичную комбинированную деформацию используют и для изготовления осесимметричных деталей посредством штамповки с кручением, но в этом случае заготовку подвергают в большей мере осадке, чем пластическому кручению. Технологически важным результатом при этом является снижение осевой силы деформации, что необходимо для повышения стойкости инструмента при изотермической деформации жаропрочных сплавов [4, 10].
Целью настоящей статьи является изучение условий осуществления комбинированной деформации кручения с осевой деформацией осадкой или растяжением, обеспечивающих подготовку УМЗ-структуры в жаропрочных сплавах. Основное внимание при этом уделено определению рациональных вкладов осевой и ротационной составляющих, а также расчету энергосиловых параметров, обеспечивающих формирование УМЗ-структуры в жаропрочных сплавах за одну операцию. Результаты исследований необходимы при разработке эффективных новых технологий и оборудования для изготовления УМЗ-полуфабрикатов в виде диска или прутка больших размеров, которые целесообразно использовать в технологиях формообразования различных изделий в условиях сверхпластичности.
Условия измельчения зерен в жаропрочных сплавах в процессе горячей деформации. Исследования деформационного измельчения зерен были выполнены в отношении широкой гаммы никелевых и титановых жаропрочных сплавов, отличающихся химическим, фазовым, зеренным строением. Для сплавов, полученных различными методами (горячедеформированные и порошковые) установлено, что наиболее оптимальной УМЗ-структурой для последующей сверхпластической деформации является микродуплексная структура для сплавов на основе никеля и глобулярная структура для сплавов на основе титана. В сплавах на никелевой основе такая структура формируется, при содержании в них интерметаллидной γ'-фазы свыше 30–35%. Такие сплавы сначала предварительно подвергают гетерогенизирующей термообработке, а затем деформируют методом дробной осадки с суммарной степенью 70–80% в температурно-скоростных условиях сверхпластичности в (γ + γ')-области. В результате зерна γ'-матрицы приобретают размеры 2–5 мкм, а частицы γ'-фазы укрупняются до размера 1–3 мкм. Внутрифазные γ/γ' границы при этом приобретают большеугловые разориентировки, а межфазные γ/γ' – некогерентность. В титановых сплавах измельчение α и β зерен до размера 2–3 мкм достигается при таких же степенях деформации, как и для никелевых сплавов после деформации в режиме сверхпластичности в (γ + γ')-области [11–13].
Особенности измельчения зерен в жаропрочных сплавах в температурно-скоростном режиме сверхпластической деформации. Для прохождения динамической рекристаллизации структуры в условиях горячей изотермической деформации необходимо, чтобы во всем объеме заготовки была накоплена достаточно большая степень деформации (0.7–0.8), требуемая для возникновения большого количества центров рекристаллизации и одновременной тотальной миграции их границ. Такая степень деформации в диски обеспечивается, если для осадки используется цилиндрическая заготовка с отношением высоты к диаметру <2. Вследствие относительно невысокой температуры прохождения динамической рекристаллизации в режиме сверхпластической деформации, заготовки из жаропрочных титановых сплавов, (например, ВТ9, ВТ25) деформируют в изотермическом штампе, нагретом на 20–40 градусов ниже температуры полиморфного превращения, при этом для обеспечения удовлетворительной стойкости штампа его нагревают не выше 950°С. Динамическая рекристаллизация в современных жаропрочных никелевых сплавах (ЖНС) происходит при более высоких температурах деформации, более 1000°С. Для предотвращения охлаждения заготовки при осадке в открытом штампе, бойки которого нагреты до 950°С, ее оборачивают каолиновым полотном и помещают в теплоизолирующий контейнер из нержавеющей стали. Осадку осуществляют с конечной степенью 70–80% дробно за 2–3 перехода. Между переходами заготовку подвергают длительным рекристаллизационным отжигам. Нередко такая технология приводит к подстуживанию сплава и к образованию поверхностных трещин, которые приходится удалять механической обработкой. В целом процесс осадки заготовок из ЖНС в отрытом штампе отличается большой трудоемкостью и низким коэффициентом использования материала КИМ 50–60% [14, 15].
Негативные особенности подготовки УМЗ-структуры в ЖНС полностью устраняются, если процесс осадки заготовки выполнять одновременно с ее кручением. В таком комбинированном процессе необходимая для прохождения динамической рекристаллизации степень деформации накапливается за счет вклада сдвиговой компоненты, создаваемой при осадке, и ротационной компоненты, вследствие пластического кручения заготовки. Технологически целесообразно уменьшить вклад сдвиговой составляющей и увеличить вклад ротационной составляющей деформации. Это позволяет уменьшить исходную высоту заготовки и штампа, обеспечить однородность температурного поля в его закрытой полости и соответственно в объеме заготовки. В таком случае можно деформировать заготовку без применения теплозащитного контейнера и осуществлять процесс за одну операцию. Существенное значение при этом имеет рациональное распределение вкладов между осевой и ротационной компонентами деформаций.
Методика расчета степени деформации при изотермической комбинированной деформации заготовки. Процесс комбинированной деформации в случае кручения и осевой деформации можно реализовать в двух вариантах: как кручение с осадкой и как кручение с растяжением. Отличие между этими схемами деформации заключается в направлении осевой силы, приводящей в случае осадки к получению диска, а в случае растяжения – прутка. В том и другом случаях заготовку необходимо подвергать большой деформации. Для анализа деформированного состояния при большой деформации используют так называемые тензоры конечной деформации. Такие тензоры являются нелинейными, поскольку их компоненты включают не только первые производные, но и их произведения, что существенно осложняет анализ деформированного состояния. Задача упрощается, если деформированное состояние оценить не по указанному тензору, а по скалярной величине – степени накопленной деформации. При этом использовать не тензор конечной деформации, а его производную по времени, т.е. тензор скорости деформации [14]. В этом случае по второму инварианту тензора скорости деформации можно определить интенсивность скорости деформации, построить траекторию деформации, характеризующую накопленную степень деформации и по ней рационально задать вклады сдвиговой и ротационной компонент.
Тензор конечной деформации, со смешанными компонентами скорости деформации для осадки с кручением имеет вид [14–16]
(1)
${{\xi }}_{j}^{i} = \left( {\begin{array}{*{20}{c}} { - {v}{\text{/}}2L}&0&0 \\ 0&{ - {v}{\text{/}}2L}&{r{{\omega /}}2L} \\ 0&{r{{\omega /}}2L}&{{v}{\text{/}}L} \end{array}} \right),$(2)
${{\xi }_{e}} = \sqrt {\frac{2}{3}\xi _{j}^{i}\xi _{j}^{i}} = \frac{1}{{L\sqrt 3 }}\sqrt {3{{{v}}^{2}} + {{r}^{2}}{{\omega }^{2}}} .$К такой же формуле можно прийти, используя тензор скорости деформаций, применяемый для описания кинематики малых деформаций. Степень накопленной деформации определим путем интегрирования интенсивности скорости деформации по времени
где e = ${v}t$/L0. Параметр e – это относительная деформация от действия осевой силы.После подстановки (1) в (2) и интегрирования при условии, что ${v}$ = const, ω = const, получим
(4)
${{\varepsilon }} = 2\sqrt {1 + \frac{{{{{{\theta }}}^{2}}}}{3}} - 2\sqrt {1 + \frac{{{{{{\theta }}}^{2}}}}{{3\left( {1 + {{{{\varepsilon }}}_{{\text{а}}}}} \right)}}} + \ln \left( {1 + {{{{\varepsilon }}}_{а}}} \right) + {\text{ln}}\frac{{1 + \frac{{{{{{\theta }}}^{2}}}}{{6\left( {1 + {{{{\varepsilon }}}_{{\text{а}}}}} \right)}} + \sqrt 1 + \frac{{{{{{\theta }}}^{2}}}}{{3\left( {1 + {{{{\varepsilon }}}_{{\text{а}}}}} \right)}}}}{{1 + \frac{{{{{{\theta }}}^{2}}}}{6} + \sqrt {1 + \frac{{{{{{\theta }}}^{2}}}}{3}} }},$Для оценки вкладов удобно рассмотреть диаграмму деформирования. Для этого введем плоскую систему координат: с абсциссой e1, показывающую степень осевой деформации, с ординатой e2 – показывающей степень ротационной деформации. Принимая во внимание, что линейная скорость движения активного инструмента ${v}$ = dL/dt, а угловая скорость вращения ω = dω/dt, получим (de)2 = (de1)2 + (de2)2, где de1 = d(L/L0), de2 = rdφ/L$\sqrt 3 $. Далее введем вектор деформации e = e1i + e2j, где e1 = = ln(L/L0), e2 = $\int {r{\text{/}}L\sqrt 3 ~d\varphi } $. Кривая перемещения конца вектора e в плоскости (e1, e2) определит траекторию деформации. На рис. 1 приведены варианты траекторий, полученные при различных соотношениях e2/e1 = k.
Рис. 1.
Траектория деформации при кручении с осадкой или с растяжением при k = 1 (верхняя), k = 2 (средняя), k = 3 (нижняя).
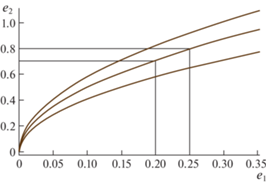
Видно, что при k = 2 даже после небольшой деформации e1 = 0.2–0.25 ротационная составляющая достигает значения 0.65–0.8. В изотермических условиях деформирования в режиме сверхпластичности, как показали многие исследования, такая степень деформации достаточна для измельчения зерен в результате прохождения динамической рекристаллизации [4–6]. При такой степени деформации возникает множество границ деформационного происхождения (ГДП) с большой кривизной и, соответственно, множество центров рекристаллизации, требуемых для формирования однородной УМЗ-структуры [16, 17].
Расчет энергосиловых параметров осадки с кручением. Приведем аналитическое решение задачи по оценке необходимой осевой силы, момента кручения и мощности при комбинированной деформации. Используем для этого подходы и методику, разработанные в публикациях [14–16].
Пусть сплошной круговой цилиндр с исходным диаметром D0 и высотой 2h0 подвергается осадке плоскими бойками вдоль оси z со скоростью перемещения верхнего торца v и с угловой скоростью вращения бойка ω. Введем следующие обозначения: r0 = D0/2; t – время; а = ωt/ω – параметр проскальзывания (ωt – угловая скорость вращения торца заготовки). Отметим, что 0 < a < 1; h = h0 – ${v}$t текущая высота заготовки; е = ${v}t$/h0 – относительная осевая деформация, примем во внимание, что степень деформации при осадке ограничена неравенством е ≥ 0.2–0.3; θ = r0ω/${v}$ – относительная скорость вращения бойка; ${{\Gamma }^{2}} = 1 + 4{{\left( {1 - \varepsilon } \right)}^{2}}{{\left( {1 - a} \right)}^{2}}{{\theta }^{2}}{\text{/}}{{w}^{2}}$, w = r0/h0, ${{\zeta }} = {{\mu }}{v}{\text{/}}{{{{\tau }}}_{0}}{{h}_{0}}$ – безразмерные параметры, вводимые для сокращения выкладок.
Реологическое поведение материала можно описать подходящей для деформации крупнозернистого сплава моделью линейного вязкопластического тела Шведова–Бингама в виде
где τs – предел текучести на сдвиг; Н – интенсивность скорости деформации сдвига; τ0 и μ – постоянные материала.Сделаем предположения, аналогичные приведенным в работе [6]: бочкообразование при осадке отсутствует, величина полного напряжения трения на контактной поверхности τf = ψτs, где ψ – параметр трения. Поле скоростей, удовлетворяющее граничным условиям и условиям несжимаемости среды, примем в виде
(6)
${{u}_{r}} = --r{v}{\text{/}}2L,\quad {{u}_{\varphi }} = \omega rz{\text{/}}L,\quad {{u}_{z}} = z{v}{\text{/}}L,$По известным соотношениям находим интенсивность скоростей деформации сдвига
Для определения энергосиловых параметров используем метод верхней оценки. В качестве варьируемого параметра возьмем параметр проскальзывания “α”. В соответствии с этим методом определим кинематически возможное поле скоростей, которое обеспечит минимум полной мощности N
где Nin и Nf – мощность внутренних сил трения и контактного трения соответственно.Мощность внутренних сил определим из выражения
(9)
${{N}_{{{\text{in}}}}} = \iiint\limits_{v} {{{\sigma }_{e}}{{\xi }_{e}}dV} = \iiint\limits_{v} {{{\tau }_{e}}HdV} = \mathop \smallint \limits_0^{2\pi } d\varphi \mathop \smallint \limits_0^h dz\mathop \smallint \limits_0^{{{r}_{k}}} \left( {{{\tau }_{0}} + \mu H} \right)Hrdr.$Здесь σе – интенсивность напряжений; ξе – интенсивность скорости деформации; τе – интенсивность напряжений сдвига; Н – интенсивность скорости деформации сдвига ${{r}_{k}} = {{r}_{0}}{\text{/}}\sqrt {1 - {{\varepsilon }}} $ – текущий радиус.
Интегрируя (8) с учетом h = h0 – ${v}t$ = h0(1 – ε) получим
(10)
${{N}_{{{\text{in}}}}} = {{{{\tau }}}_{0}}{{\pi }}r_{0}^{2}{v}\sqrt 3 \left\{ {\frac{2}{{{{\alpha }^{2}}{{\theta }^{2}}}}~\left[ {{{{\left( {1 + \frac{{{{\alpha }^{2}}{{\theta }^{2}}}}{{3\left( {1 - \varepsilon } \right)}}} \right)}}^{{3/2}}} - 1} \right] + \frac{{\zeta \sqrt 3 }}{{1 - \varepsilon }}\left[ {1 + \frac{{{{\alpha }^{2}}{{\theta }^{2}}}}{{6\left( {1 - \varepsilon } \right)}}} \right]} \right\}.$Здесь θ = r0ω/${v}$ – относительная скорость вращения бойка; ζ = μ${v}$τ0h0.
Мощность сил контактного трения найдем по формуле
где интегрирование ведется по контактной поверхности (круг радиуса rk), а вектор $u_{S}^{'}$ – это относительная скорость движения точки торца заготовки относительно бойка, площадь s-торца(12)
$u_{s}^{'} = \sqrt {{{{(u_{r}^{'})}}^{2}} + {{{(u_{\varphi }^{'})}}^{2}}} = \sqrt {{{{\left( {r{v}{\text{/}}2h} \right)}}^{2}} + {{{\left[ {\left( {1 - \alpha } \right)\omega r} \right]}}^{2}}} .$Подставляя в (10) $u_{S}^{'}$ из (11) и τfr = ψτs получим
(13)
${{N}_{{{\text{fr}}}}} = {{\tau }_{0}}\pi r_{0}^{2}\frac{{{v}\sqrt 3 }}{{1 - \varepsilon }}\Gamma \psi \left[ {\frac{w}{{3\sqrt 3 {{{\left( {1 - \varepsilon } \right)}}^{{3/2}}}}} + \frac{{\zeta I}}{{1 - \varepsilon }}} \right],$(14)
$I = \frac{1}{{r_{0}^{2}{{h}_{0}}}}\mathop \smallint \limits_0^{\frac{{{{f}_{0}}}}{{\sqrt {1 - \varepsilon } }}} \sqrt {1 + \frac{{{{\alpha }^{2}}{{\omega }^{2}}{{r}^{2}}}}{{3{{{v}}^{2}}}}} {{r}^{2}}dr.$Вычисляя стандартным способом интеграл в правой части (13), получим
(15)
$\begin{gathered} I = \frac{w}{8}{{\left( {\frac{3}{{{{\alpha }^{2}}{{\theta }^{2}}}}} \right)}^{{3/2}}}\left\{ {\left[ {1 + \frac{{2{{\alpha }^{2}}{{\theta }^{2}}}}{{3\left( {1 - \varepsilon } \right)}}} \right]\frac{{\alpha \theta }}{{\sqrt 3 \sqrt {1 - \varepsilon } }}} \right. \times \\ \times \;\left. {\sqrt {1 + \frac{{{{\alpha }^{2}}{{\theta }^{2}}}}{{3\left( {1 - \varepsilon } \right)}} - \frac{1}{2}} {\kern 1pt} {\text{1}}n\left| {1 + \frac{{2{{\alpha }^{2}}{{\theta }^{2}}}}{{3\left( {1 - \varepsilon } \right)}} + \frac{{2\alpha \theta }}{{\sqrt 3 \sqrt {1 - \varepsilon } }}\sqrt {1 + \frac{{{{\alpha }^{2}}{{\theta }^{2}}}}{{3\left( {1 - \varepsilon } \right)}}} } \right|} \right\}. \\ \end{gathered} $Параметр “α” можно получить из условия минимума полной мощности. Однако применение стандартного условия dN/dt приводит к весьма громоздкому трансцендентному уравнению. Поэтому этот параметр целесообразно определить численным методом путем минимизации выражения для полной мощности
Величина крутящего момента, передаваемого заготовке тангенциальными напряжениями трения будет равна
(17)
$\vec {M} = \iint\limits_s {\overrightarrow {{{{{\tau }}}_{{{\text{fr}}}}}} \times \vec {r}dS}{\text{\;}}.$Интегрируя (13) с учетом того, что вектор полного напряжения трения противонаправлен вектору относительной скорости движения частиц торца по бойку, получим
(18)
$M = 2\pi r_{0}^{2}{{h}_{0}}{{\tau }_{0}}\sqrt 3 \psi \frac{{\sqrt {{{\Gamma }^{2}} - 1} }}{\Gamma }\left\{ {\frac{w}{{3\sqrt {3{{{\left( {1 - \varepsilon } \right)}}^{{3/2}}}~} }} + \frac{{\zeta I}}{{1 - \varepsilon }}} \right\}.$Для того чтобы найти силу осадки с кручением Pk, запишем баланс мощности
Подставляя в (19) Nin из (10), Nfr из (13) и M из (18) получим Pk
(20)
$\begin{gathered} {{P}_{k}} = \frac{{\sqrt 3 {{\tau }_{0}}\pi r_{0}^{2}}}{{1 - \varepsilon }}\left\{ {\frac{{2\left( {1 - \varepsilon } \right)}}{{{{\alpha }^{2}}{{\theta }^{2}}}}\left[ {{{{\left( {1 + \frac{{{{\alpha }^{2}}{{\theta }^{2}}}}{{3\left( {1 - \varepsilon } \right)}}} \right)}}^{{3/2}}} - 1} \right] + \frac{{\zeta \sqrt 3 }}{{1 - \varepsilon }}\left[ {1 + \frac{{{{\alpha }^{2}}{{\theta }^{2}}}}{{6\left( {1 - \varepsilon } \right)}}} \right] + } \right. \\ \left. { + \;\left[ {\Gamma \psi - \left( {1 - ~\varepsilon } \right)\psi \theta \frac{{2\sqrt {{{\Gamma }^{2}} - 1} }}{{\Gamma w}}} \right]\left[ {\frac{w}{{3\sqrt 3 ~{{{\left( {1 - \varepsilon } \right)}}^{{3/2}}}}} + \frac{{\zeta I}}{{1 - \varepsilon }}} \right]} \right\}. \\ \end{gathered} $Выражение для величины силы осадки без кручения P0 получаем из (20) предельным переходом θ → 0
(21)
${{P}_{0}} = \mathop {\lim }\limits_{0 \to 0} {{P}_{k}} = \frac{{\sqrt 3 {{\tau }_{0}}\pi r_{0}^{2}}}{{1 - \varepsilon }}\left[ {1 + \frac{{\zeta \sqrt 3 }}{{1 - \varepsilon }}} \right]\left[ {1 + \frac{{\psi w}}{{3\sqrt 3 {{{\left( {1 - \varepsilon } \right)}}^{{3/2}}}}}} \right].$Для конкретного расчета выберем цилиндрическую заготовку диаметром D0 = 200 мм, высотой h0 = 320 мм. Уравнение состояния, соответствующее реологическому поведению жаропрочного титанового сплава ВТ9 при температуре 950°C имеет вид τ = (23.1 + + 133 Н) MПa. При расчетах варьировали величину параметра трения от 0.05 до 0.8, скорость перемещения бойка и скорость его вращения 0.008–0.8 мм/с и 0–50 об/мин соответственно. Расчеты показывают, что осадка с кручением приводит к снижению величины осевой силы Pk по сравнению с силой, возникающей при осадке без кручения P0, причем уменьшение отношения Pk/P0 особенно заметно с ростом n, ψ, ε (рис. 2). При больших значениях отмеченных параметров заметно возрастает величина крутящего момента (рис. 3). С другой стороны, при весьма больших степенях деформации на величину Pk/P0 влияет эффект скоростного упрочнения материала заготовки, приводящий к снижению эффективности процесса осадки с кручением. Энергосиловые показатели можно улучшить, путем рационального выбора конструктивно-технологических приемов осуществления процесса.
Рис. 2.
Влияние степени деформации и линейной скорости сжатия на относительную силу при осадке с кручением: (а) – при ψ = 0.2 и при значениях ${v}$ = 0.008–0.8 мм/с; (б) – для сплава ВТ9 (диск h0 = 320 мм, D = 200 мм) расчетные зависимости отношения Pk/P0 от скорости вращения бойка n при ${v}$ = 0.008 мм/с, T = 950°C.
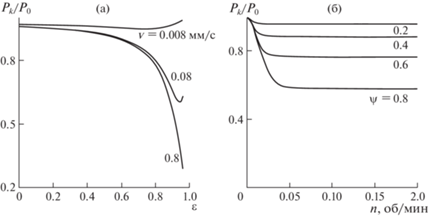
Рис. 3.
Влияние скорости кручения на крутящий момент при осадке для значений линейной скорости ${v}$: 0.008 мм/с; 0.08 мм/с; 0.8 мм/с при коэффициенте ψ = 0.2.
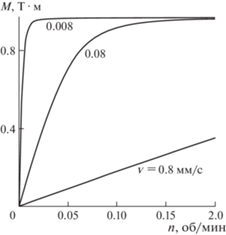
Конструктивно-технологические особенности реализации комбинированной деформации. Снижение осевой силы является важным результатом для практической технологии изготовления УМЗ-полуфабрикатов из жаропрочных сплавов, создает возможность уменьшения исходной высоты заготовки при сохранении ее объема за счет соответствующего увеличения ее диаметра. Необходимую для рекристаллизации степень деформации сплава в этом случае можно обеспечить не столько за счет вклада сдвиговой деформации (степени осадки), сколько за счет ротационной деформации, т.е. пластического кручения [18]. Такой выбор позволяет существенно снизить высоту изотермического штампа, обеспечить теплоизоляцию его рабочей зоны от окружающего пространства посредством введения в конструкцию штампа керамического кожуха. Конструктивно такой кожух можно выполнить из нескольких частей, снабженных нагревательными элементами. Например, в виде двух полых керамических цилиндров, коаксиально расположенных относительно друг друга. При этом верхнюю часть кожуха связать с верхним подвижным бойком, а нижнюю – с неподвижным нижним бойком. Во время деформации и нагрева заготовки обе части кожуха образуют закрытую от внешнего воздействия среды теплоизолированную рабочую зону штампа, а после деформации заготовки в результате подъема верхнего бойка с кожухом обеспечивается возможность снятия диска и установка новой заготовки для последующей операции. Такая конструкция штампа позволяет создать однородную температуру деформации, необходимую для реализации однопереходного процесса подготовки УМЗ-структуры в заготовках из жаропрочных сплавов без использования теплозащитного контейнера. Перераспределение вкладов в деформации в пользу ротационной компоненты создает также условия для управления силами трения и предотвращения проскальзывания. Решается эта задача путем создания на поверхности бойков ориентированных в радиальном направлении неглубоких пазов, достаточных для передачи момента трения и не затрудняющих снятие заготовки с бойка. Под воздействием осевой силы торцевой материал заготовки заполняет такие пазы, что обеспечит передачу заготовке момента кручения без проскальзывания. Для снижения трения в радиальном направлении и предотвращения адгезионного схватывания заготовки с инструментом на поверхность бойков целесообразно нанести защитно-смазочное покрытие, например, на основе жидкого стекла. Съем заготовки с бойков в таком штампе можно выполнить с помощью выталкивателя гидропресса и робота. Формирование однородной УМЗ-структуры во всем объеме заготовки обеспечит осадка со степенью 0.2–0.3, необходимая для формирования большеугловых границ деформационного происхождения (ГДП) и погонная на каждый миллиметр высоты ротационная деформации со степенью 0.6–0.8 [16–18]. Приведенный анализ энергосиловых параметров деформации и конструктивно-технологические особенности процесса деформации указывают на снижение осевой силы деформации, что важно для повышения стойкости изотермического штампа и реализации однооперационного процесса получения дисков с однородной УМЗ-структурой. Температурно-скоростные условия сверхпластичности обеспечивают динамическое равновесие между деформационным разогревом и рассеянием тепла, которые формируют УМЗ-структуру. Невысокая скорость деформации в этих условиях (10–2–10–3) с–1, в том числе осадки и кручения способствует снижению мощности, затрачиваемой на осуществления процесса и создания требуемого момента сил.
Метод кручения с наложением осевой силы растяжения можно использовать и для подготовки УМЗ-структуры в прутках большого диаметра, но в этом случае необходимо силу сжатия заменить растягивающей силой.
Обсуждение результатов. При кручении с осадкой снижение осевой силы достигается за счет “разворота” вектора сил контактного трения между бойком и торцом заготовки. Величина сил контактного трения, возникающих на поверхности между инструментом и заготовкой, ограничена по величине соотношением
где f – вектор сил контактного трения; fmax – эмпирическая постоянная. Во время осадки без кручения вектор f имеет единственную отличную от нуля компоненту fr, т.е. он направлен вдоль радиуса контактной зоны. При осадке с кручением вектор f имеет две компоненты: радиальную $f_{r}^{'}$ и тангенциальную $f_{\tau }^{'}$. Абсолютная величина вектора f ограничена по модулю, радиальная компонента в этом случае становится меньше, чем при осадке без кручения: $f_{r}^{'}$ < fr. В то же время тангенциальная сила трения носит активный полезный характер и в отсутствие проскальзывания равна нулю. Отсюда следует, что суммарное сопротивление “растеканию” материала по поверхности инструмента снижается до малых значений, особенно в случае применения смазки. Поэтому роль трения в снижении осевой силы может быть незначительна. При кручении с растяжением контактное трение вовсе отсутствует. Тем не менее, энергосиловой расчет и экспериментальные данные показывают, что и в этом случае осевая сила снижается. Следовательно, это снижение связано не только с уменьшением сил внешнего контактного трения, но также с особой ролью ротационной составляющей деформации в снижении напряжения внутреннего трения (сил Пайерлса–Наборро), оказывающее сопротивление скольжению дислокаций. Хотя эта ротационная составляющая не приводит к формоизменению заготовки, но она важна для обеспечения совместности деформации и для активизации процесса рекристаллизации. Распределенный по всему объему заготовки V момент кручения M = τcV, где τс – напряжение сдвига способствует активизации множества источников подвижных решеточных дислокаций и частичных дисклинаций. Поэтому на долю осевой силы приходится лишь обеспечение заданного схемой деформации формоизменение заготовки (осадки или растяжения), т.е. работа, затрачиваемая на преодоление внутреннего трения. Кроме того, кручение порождает множество большеугловых границ деформационного происхождения вследствие перемещений частичных дисклинаций. Пересечение и миграция таких границ, собственно, и приводит к образованию мелких рекристаллизованных зерен [6, 14–16].Осадка c кручением – это процесс, который позволяет сформировать УМЗ-структуру в цилиндрических заготовках, высота которых по отношению к диаметру меньше единицы. Такая возможность обусловлена тем, что накопленная при осадке с кручением степень деформации является результатом суммарного вклада компонент сжатия и кручения. При этом бόльший вклад в деформацию целесообразно внести за счет кручения, которое хотя и не приводит к формоизменению заготовки, но способно обеспечить значительное измельчение зерен в жаропрочных сплавах до размеров, обеспечивающих им сверхпластичность при деформации в определенных температурно-скоростных условиях.
Выводы. 1. Теоретически обоснована комбинированная деформация (КД) для формирования УМЗ-структуры в полуфабрикатах из суперсплавов для изготовления деталей ГТД. 2. Получены аналитические зависимости напряженного и деформированного состояния полуфабрикатов из жаропрочных сплавов при кручении под давлением в режиме сверхпластичности, приведена оценка необходимых энергосиловых параметров для этого процесса. 3. Использование в технологии изготовления из жаропрочных сплавов деталей ГТД-процесса кручения под давлением в режиме сверхпластичности, позволит существенно упростить технологию, оборудование и инструмент за счет уменьшения силы деформации, повышения стойкости штампового инструмента, реализации однопереходной операции без промежуточных рекристаллизационных отжигов.
Список литературы
Athey R.L., Moore J.B. Progress Report on the GatorisingTM Forging Process // National Aerospase Engineering and Manufacturing meeting. Los Angeles. 1975. P. 1.
Kaibyshev O.A., Utyashev F.Z. Superplasticity: Microstructural Refinement and Superplastic Roll Forming, Futurepast: Inc., Arlington, Virginia USA, ISTC Science & technology Series. 2005. V. 3. 386 p.
Tan L., Li Y., Liu F. et al. Superplastic behavior of a powder metallurgy superalloy during isothermal compression // J. of Materials Science & Technology, 2019. V. 35. № 11. P. 2591.
Смирнов О.М. и др. Влияние комбинированного нагружения на параметры штамповки плоских дисков в состоянии сверхпластичности // Кузнечно-штамповочное производство. Обработка материалов давлением. 1997. № 1. С. 7.
Pandey K.K., Levitas V.I. In situ quantitative study of plastic strain-induced phase transformations under high pressure: Example for ultra-pure Zr // Acta Materialia. 2020. V. 196. P. 338.
Utyashev F.Z., Valiev R.Z., Raab G.I., Galimov A.K. Strain Accumulated during Equal-Channel Angular Pressing and Its Components // Russian Metallurgy (Metally). 2019. № 4. P. 281.
Shuitcev A., Gunderov D.V., Sun B. et al. Nanostructured Ti29.7Ni50.3Hf20 high temperature shape memory alloy processed by high-pressure torsion // J. Materials Science and Technology. 2020. V. 52. № 7–8. P. 218.
Korznikova G., Kabirov R., Nazarov K. et al. Influence of constrained high-pressure torsion on microstructure and mechanical properties of an aluminum-based metal matrix composite // J. of the Minerals Metals & Materials Society (JOM). 2020. V. 72. № 8. P. 2898.
Valiev R.Z., Zhilyaev A.P., Langdon T.G. Bulk Nanosructured Materials: Fundamentals and Applications. John Wiley & Sons, Inc., 2013. 456 p.
Kawasaki M., Han J.K., Jung S.H. et al. Mechanical bonding of aluminum hybrid alloy systems through high-pressure torsion // Advanced Engineering Materials. 2020. V. 22. № 1. P. 1900483.
Horita Z., Tang Y., Masuda T. et al. Severe plastic deformation under high pressure: Upsizing sample dimensions // Materials Transactions. 2020. V. 61. Iss. 7. P. 1177.
Lv Sh., Jia Ch., He X. et al. Superplastic Deformation and Dynamic Recrystallization of a Novel Disc Superalloy GH4151 // Materials. 2019. V. 12. Iss. 22. P. 3667.
Asghari-Rad P., Sathiyamoorthi P., Nguyen N.T.-C. et al. Fine-tuning of mechanical properties in V10Cr15Mn5Fe35Co10Ni25 high-entropy alloy through high-pressure torsion and annealing // Materials Science and Engineering A. 2020. V. 771. P. 138604.
Утяшев Ф.З., Сухоруков Р.Ю., Валитов В.А. Теоретические основы использования интенсивной пластической деформации для формирования ультрамелкозернистой структуры в суперсплавах // Проблемы машиностроения и автоматизации. 2021. № 3. С. 72.
Еникеев Ф.У., Рыжков В.Г., Утяшев Ф.З. Аналитическое исследование энергосиловых параметров осадки с кручением цилиндрических заготовок из вязкопластического материала // Проблемы прочности. 1994. № 6. С. 68.
Утяшев Ф.З., Сухоруков Р.Ю. Механика интенсивной пластической деформации в процессах измельчения зерен в суперсплавах // Доклады Российской академии наук. Физика, технические науки. 2022. Т. 504. С. 66.
Hughes D.A., Hansen N. Microstructure and strength of nickel at large strains // Acta Materialia. 2000. V. 48. № 11. P. 2985.
Афонин В.Л. и др. Исследования и разработка инновационных технологических процессов и интеллектуальных систем управления для изготовления деталей газотурбинных двигателей (ГТД). М.: ИМАШ РАН, 2019. 137 с.
Дополнительные материалы отсутствуют.
Инструменты
Проблемы машиностроения и надежности машин