Поверхность. Рентгеновские, синхротронные и нейтронные исследования, 2019, № 10, стр. 74-81
Пористые пленки анодного оксида алюминия на поверхности монокристаллов Al(111)
И. В. Росляков 1, 2, *, Д. С. Кошкодаев 2, В. А. Лебедев 1, К. С. Напольский 1, 2
1 Московский государственный университет им. М.В. Ломоносова,
Химический факультет
119991 Москва, Россия
2 Московский государственный университет им. М.В. Ломоносова,
Факультет наук о материалах
119991 Москва, Россия
* E-mail: ilya.roslyakov@gmail.com
Поступила в редакцию 02.02.2019
После доработки 15.03.2019
Принята к публикации 04.04.2019
Аннотация
Микроструктура и кристаллографическая ориентация алюминия оказывают существенное влияние на морфологию пористых оксидных пленок, формируемых путем анодирования на его поверхности. В большинстве существующих работ по поиску закономерностей анодного окисления алюминия металлические фольги рассматривают как изотропную среду. Новизна настоящего исследования заключается в аттестации пористых оксидных покрытий, сформированных на монокристаллах алюминия одной и той же ориентации – Al(111). Эксперименты проводили в растворе щавелевой кислоты концентрацией 0.3 М в широком диапазоне напряжений анодирования 20–140 В. Методами растровой электронной и атомно-силовой микроскопии установлена зависимость от приложенного напряжения степени упорядочения пор с формированием гексагонального массива, а также высоты профиля границы раздела металл–оксид. Установлен коэффициент пропорциональности между толщиной пористого слоя и удельным электрическим зарядом анодирования.
ВВЕДЕНИЕ
Анодное окисление алюминия в растворах кислых электролитов приводит к формированию на поверхности металла пористых оксидных пленок, в структуре которых присутствуют однородные по размеру каналы, равноудаленные друг от друга и ориентированные вдоль нормали к подложке. В 1995 г. японские ученые впервые показали, что при определенных условиях анодирования происходит самоорганизация пор в двумерный гексагональный массив [1]. Следует отметить, что образующиеся в результате пористые оксидные пленки состоят из доменов – областей с малодефектной гексагональной упаковкой каналов. Соседние домены разориентированы друг относительно друга на некоторый угол в плоскости образца, а их латеральные размеры не превышают нескольких микрон.
Первые свидетельства влияния кристаллической структуры подложки на морфологию анодного оксида алюминия получены в 2007 г. [2]. Установлено, что лишь при использовании металла с большим размером зерна возможно формирование пористых пленок с дальнодействующими (более 1 см) ориентационными корреляциями в их структуре. Позднее показана взаимосвязь между размером доменов в анодном оксиде алюминия и симметрией Al подложки на примере текстурированных поликристаллических фольг [3] и монокристаллов [4, 5]: средний размер доменов максимален при использовании алюминия, ориентированного в плоскости (100). По результатам численного моделирования данный феномен связан с различным соотношением скоростей реакции ионизации алюминия и его взаимодействия с кислородсодержащими анионами на различных гранях монокристаллов [6].
Альтернативная версия влияния кристаллографической ориентации металла на упорядочение каналов в аморфной оксидной пленке связана с анизотропией скоростей электрохимического окисления алюминия, приводящей к дальнодействующему ориентационному порядку системы пор в плоскости оксидной пленки [7, 8]. В случае Al(111) с гексагональным мотивом упаковки атомов наблюдается наибольшее количество доменов макроскопического размера. Напротив, ось симметрии четвертого порядка в случае Al(100) приводит к преобладанию в структуре анодного оксида алюминия доменов малого размера, разориентированных друг относительно друга в плоскости пленки.
Влияние микроструктуры алюминиевых фольг на структуру анодного оксида алюминия в направлении роста каналов было изучено методом малоугловой дифракции рентгеновского излучения и нейтронов. Показано увеличение извилистости пор в пленке оксида с уменьшением размера зерна металла [9], что объясняется различным направлением роста каналов в соседних зернах [10]. Данный факт вызван отклонением направления роста каналов от нормали к плоскости образца при наличии в структуре металла устойчивых к растворению кристаллографических плоскостей, пересекающих его поверхность под углом, близким к нормальному [11].
Таким образом, кристаллическая структура алюминия во многом предопределяет морфологию формируемых на его поверхности оксидных пленок. Отметим, однако, что в большинстве существующих теоретических работ по моделированию процесса анодирования [12, 13] и экспериментальных исследований оптимизации условий электрохимической обработки (в частности, напряжения анодирования [14] и скорости его развертки на начальной стадии [15], а также температуры [16], состава [14, 17, 18] и концентрации [19] электролита) с целью достижения максимальной степени упорядочения пор металлические фольги рассматривают как изотропную среду. Новизна настоящей работы заключается в аттестации морфологии оксидных покрытий, сформированных на монокристаллах алюминия с одинаковой ориентацией – Al(111). Варьирование напряжения анодирования в широком диапазоне позволило проследить зависимость упорядочения и высоты профиля структурированной в результате анодного окисления поверхности металла в кинетическом и в диффузионном режимах роста пленки анодного оксида алюминия. На поликристаллических фольгах экспериментально установлено отношение толщины пористого слоя к удельному электрическому заряду, прошедшему за время электрохимического эксперимента, которое в дальнейшем было использовано для кулонометрического контроля продолжительности анодного окисления.
ЭКСПЕРИМЕНТАЛЬНАЯ ЧАСТЬ
В качестве исходного материала для получения пористых пленок анодного оксида алюминия использован алюминий двух видов: поликристаллические фольги (чистота 99.999%, толщина 0.5 мм) для предварительных экспериментов по уточнению параметров электрохимического эксперимента; монокристаллы (чистота 99.9998%, толщина ~2 мм) с кристаллографической ориентацией, близкой к (111).
Перед проведением анодного окисления поверхность металла выравнивали с помощью механической шлифовки (наждачная бумага Smirdex на основе карбида кремния с зернистостью 400, 800, 1500, 2500 и 4000 ед.) и последующей полировки с применением алмазной суспензии Struers DiaDuo-2 с размером зерна абразива 3 мкм. На финальной стадии проводили электрохимическую полировку алюминия в растворе, содержащем 1.8 М хромового ангидрида и 15.1 М ортофосфорной кислоты при температуре 80°С и интенсивном перемешивании. В качестве анода выступал монокристалл алюминия, катодом служила Al пластина, значительно превосходящая анод по площади, расстояние между электродами составляло ~1 см. Процесс проводили в гальваностатическом режиме при плотности тока ~500 мА/см2 с использованием источника постоянного тока Agilent N8740A в импульсном режиме: время импульса 3 с, интервал между импульсами 40 с, продолжительность 40 циклов.
Анодирование алюминия проводили в растворе щавелевой кислоты концентрацией 0.3 М при температуре ~1°С в двухэлектродной электрохимической ячейке. Площадь монокристаллов при анодировании была ограничена витоновым кольцом с внутренним диаметром 12 мм. Катодом, удаленным от анода на расстояние ~10 см, выступала платиновая проволока, свернутая в виде кольца. Напряжение между электродами в диапазоне 20–140 В задавали с помощью источника постоянного тока Agilent N5751A. В случае анодного окисления при напряжениях выше 60 В осуществляли его плавную развертку на начальной стадии со скоростью 0.5 В/с. Продолжительность эксперимента определяли in situ путем подсчета величины электрического заряда, прошедшего в процессе анодирования. Для этого с помощью цифрового мультиметра Agilent Truevolt 34461A регистрировали зависимости тока от времени. Анодирование прекращали при достижении заданной плотности заряда: в случае поликристаллических фольг ~100 Кл/см2; в случае монокристаллов Al(111) ~200 Кл/см2 при напряжениях от 20 до 60 В и ~250 Кл/см2 при напряжениях выше 60 В.
Кристаллическая структура используемых монокристаллов алюминия была аттестована методом дифракции обратно рассеянных электронов. Эксперименты проводили с использованием растрового электронного микроскопа Carl Zeiss NVision 40, оборудованного детектором обратно рассеянных электронов на базе CCD-камеры Nordlys II (Oxford Instruments).
Морфология и толщина пористых пленок анодного оксида алюминия, а также алюминиевые подложки, полученные после селективного растворения оксида, были аттестованы с помощью растрового электронного микроскопа (РЭМ) LEO Supra 50 VP. Перед проведением исследования на непроводящие образцы наносили слой хрома толщиной 5 нм с использованием установки магнетронного напыления Q150T ES (Quorum Technologies). Толщину полученных пористых пленок, сформированных на поверхности поликристаллических Al фольг, определяли путем анализа скола образца. Предварительно алюминиевую подложку селективно растворяли в растворе 10 об. % брома в метаноле.
Морфологию поверхности алюминиевой подложки изучали после селективного удаления оксидной пленки в растворе 0.2 М CrO3 и 0.6 М H3PO4 при 70°С. Для количественного анализа степени упорядочения структуры анодного оксида алюминия проводили статистическую обработку РЭМ-изображений [20]. Для аттестации шероховатости исходных монокристаллов и высоты профиля алюминия после анодирования и селективного удаления пористой оксидной пленки использовали атомно-силовой микроскоп NT-MDT NTEGRA Aura в полуконтактном режиме. В качестве зонда применяли алмазные кантилеверы SCD 15/Albs с радиусом кривизны острия ~7 нм. Для воссоздания реального профиля поверхности осуществляли процедуру деконволюции с использованием подхода слепого восстановления формы иглы в программном пакете Gwyddion.
РЕЗУЛЬТАТЫ И ИХ ОБСУЖДЕНИЕ
Качество подготовки поверхности и кристаллографическая ориентация алюминия были аттестованы, соответственно, методами атомно-силовой микроскопии (АСМ) и дифракции обратно рассеянных электронов. Средняя шероховатость (Sa) монокристаллов Al(111) не превышает 1.96 ± ± 0.28 нм на площади 20 × 20 мкм2 (рис. 1а). Отметим, что использование электрохимической полировки на заключительной стадии приводит к удалению поверхностного аморфизированного слоя, формирующегося при механическом выравнивании поверхности. Таким образом, для проведения дифракционных исследований дополнительная пробоподготовка не требуется. По данным дифракции обратно рассеянных электронов (рис. 1б) отклонение поверхности образца от плоскости {111} составляет ~3.7°. На анализируемой площади ~4 × 10 мм2 мозаичность монокристалла не превышает 2.5°.
Рис. 1.
Аттестация монокристаллов алюминия, используемых в качестве исходного материала: а – морфология поверхности по данным АСМ; б – полюсная фигура для кристаллографических плоскостей семейства {111} монокристалла алюминия, полученная с помощью дифракции обратно рассеянных электронов.
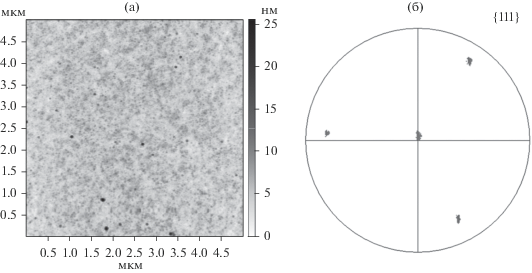
В связи с тем, что степень упорядочения пористой структуры изменяется в процессе роста слоя анодного оксида алюминия [15, 21], возможность получения пленок заданной толщины чрезвычайно важна для количественного сравнения их структурных параметров. Перед анодированием монокристаллов алюминия была получена серия образцов на поликристаллических Al фольгах. Согласно закону Фарадея толщина пористого оксидного слоя (H) линейно увеличивается с плотностью заряда анодирования (q) с коэффициентом пропорциональности (x), определяемым условиями электрохимической обработки:
Экспериментальные значения параметра x для различных напряжений анодирования (U) в щавелевой кислоте концентрацией 0.3 М при температуре ~1°С представлены на рис. 2. Согласно полученным данным коэффициент пропорциональности монотонно увеличивается с ростом напряжения. Наблюдаемая тенденция коррелирует с увеличением эффективности формирования слоя оксида (доли окисленных атомов алюминия, формирующих оксидную пленку на поверхности металла) при бо́льших напряжениях анодирования [14]. Аналогичное изменение параметра x с ростом напряжения ранее было показано для ограниченного числа режимов анодирования в порообразующих электролитах на основе серной, щавелевой и селеновой кислот [8, 17, 22].Рис. 2.
Зависимость отношения толщины пористых пленок анодного оксида алюминия к плотности заряда от напряжения анодирования. Данные получены в щавелевой кислоте концентрацией 0.3 М при температуре ~1°С. Точками отмечены экспериментальные данные, пунктирная кривая – математическое описание согласно уравнению (2).
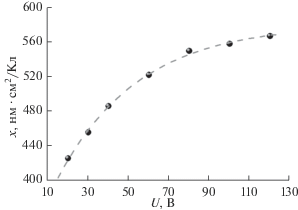
Экспериментальные точки хорошо аппроксимируются экспоненциальной зависимостью вида:
Представленные данные, впервые полученные для широкого диапазона напряжений, позволяют воспроизводимо получать пленки анодного оксида алюминия заданной толщины в щавелевой кислоте концентрацией 0.3 М in situ с использованием кулонометрического контроля анодного окисления. Отметим, что полученные значения параметра x рассчитаны для поликристаллических Al фольг, однако могут быть использованы и при анодном окислении монокристаллов ввиду слабого влияния кристаллографической ориентации алюминия на данный параметр [8].Для анализа морфологии пленок анодного оксида алюминия, полученных анодированием монокристаллов Al(111) в диапазоне напряжений 20–140 В, были использованы изображения поверхности алюминия после удаления оксидного слоя, которая является точной репликой нижней части пленки оксида (рис. 3). Отчетливо видно, что увеличение напряжения анодирования приводит к росту среднего расстояния между порами. Степень упорядочения структуры анодного оксида алюминия изменяется немонотонно: поры образуют высокоупорядоченный двумерный гексагональный массив около 40 и 140 В (рис. 3а, в); при промежуточных значениях структура разупорядочена (рис. 3б).
Рис. 3.
РЭМ-изображения поверхности монокристаллов Al(111) после формирования и последующего селективного растворения пористого оксидного слоя. Анодирование проводили в щавелевой кислоте концентрацией 0.3 М при температуре ~1°С и напряжении: 40 (а); 80 (б); 140 В (в).
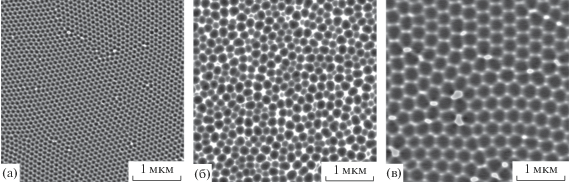
Количественное сравнение полученных изображений проведено на основе результатов их статистического анализа с использованием разработанного коллективом авторов программного обеспечения [20]. В качестве одного из параметров порядка определена доля пор в гексагональном окружении при помощи построения диаграмм Вороного [23]. Отметим, что несмотря на существенные различия в морфологии (рис. 3), для всех полученных структур среднее число соседей каждой отдельной поры равно шести. Данный факт позволяет описывать структуру анодного оксида алюминия в терминах гексагональной упаковки независимо от степени упорядочения. По полученным данным (рис. 4а) доля пор в гексагональном окружении максимальна (более 90%) для образца, полученного при 40 В, и лежит в диапазоне 70–80% при напряжениях анодирования 120 и 140 В. Указанные значения напряжений попадают на верхнюю границу кинетического режима и в диффузионный режим анодирования соответственно [19]. Для других образцов доля пор в гексагональном окружении не превышает 60%.
Рис. 4.
Результаты статистического анализа РЭМ-изображений: доля пор в гексагональном окружении (а) и параметр локального порядка 〈ψ〉 (б) в зависимости от напряжения анодирования для пористых пленок анодного оксида алюминия, полученных окислением монокристаллов Al(111) в щавелевой кислоте концентрацией 0.3 М при температуре ~1°С.
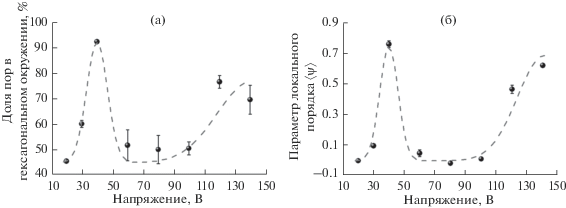
В качестве альтернативы в [24] предложен параметр локального порядка (ψi), который для i-й поры можно рассчитать следующим образом:
где θijk – угол между тремя соседними порами, ni – число соседей вокруг i-й поры. Отметим, что в случае бездефектной гексагональной упаковки среднее значение этой величины 〈ψ〉 = 1, а в случае стохастического расположения каналов 〈ψ〉 = 0. Для исследованных структур значение параметра локального порядка меняется в широких пределах в зависимости от напряжения анодирования (рис. 4б). Для U = 40 В значение 〈ψ〉 превышает 0.75, при напряжении 120–140 В лежит в диапазоне 0.45–0.65, а для остальных образцов с разупорядоченной структурой не превышает 0.1. Следует отметить полное согласие результатов, полученных с помощью двух независимых подходов.Таким образом, на качественном уровне морфология слоя анодного оксида алюминия, сформированного на поверхности монокристаллов Al(111), существенно не отличается от структуры оксидных пленок, полученных на подложках из поликристаллических Al фольг. Упорядочение пор с формированием гексагонального массива наблюдается в двух узких диапазонах на шкале напряжений: при U = 40 В (соответствует верхней границе кинетического режима анодирования) и при U выше 120 В (диффузионный режим анодирования) [19].
По данным АСМ поверхность монокристаллов Al(111) после анодирования и селективного удаления оксидной пленки представляет собой набор полусферических углублений и выступов между ними. Каждое углубление соответствует основанию поры и окружено шестью выступами. В случае упорядоченных структур ямки формируют гексагональный массив, а выступы имеют форму правильных трехгранных пирамид (рис. 5а).
Рис. 5.
Морфология поверхности монокристалла Al(111) после селективного растворения пористой пленки анодного оксида алюминия толщиной ~50 мкм, полученной в щавелевой кислоте концентрацией 0.3 М при напряжении 40 В и температуре ~1°С: а – АСМ-изображение поверхности металла; б – профиль вдоль линии, указанной на АСМ-изображении; в – зависимость угла наклона боковых граней выступов от напряжения анодирования. Горизонтальная пунктирная линия при 54.7° соответствует углу между плоскостями {111} и {100} в структуре алюминия.
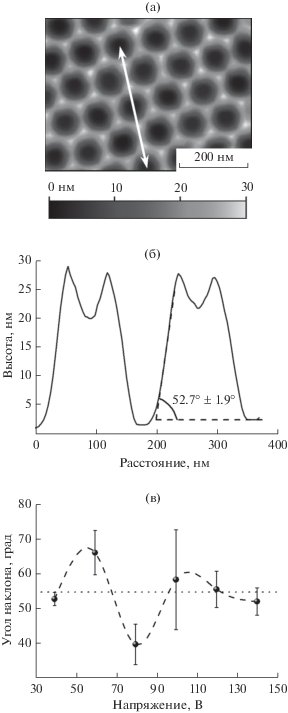
Согласно профилю поверхности монокристалла Al(111) после анодного окисления при 40 В (рис. 5б) средний угол наклона грани пирамидального выступа к горизонтальной плоскости образца составляет 52.7° ± 1.9°. Это значение близко к углу между высокосимметричными плоскостями {111} и {100} в структуре алюминия, который равен 54.7°. Ранее в [7] было выдвинуто предположение, что формирование пирамидальных выступов на поверхности металла стабильными плоскостями с высокой плотностью упаковки атомов наиболее выгодно с энергетической точки зрения. В этом случае ряды пор оказываются параллельны кристаллографическим направлениям семейства 〈110〉 элементарной ячейки алюминия, что подтверждается согласующимися между собой данными РЭМ и дифракции обратно рассеянных электронов. Таким образом, указанные структуры на границе металл–оксид являются переходными элементами, которые связывают морфологию пористой пленки с кристаллографической ориентацией подложки.
Среднее значение угла наклона граней пирамидальных выступов в зависимости от напряжения анодирования представлены на рис. 5в. В случае упорядоченных структур (U = 40, 120 и 140 В) угол между поверхностью образца и боковыми гранями пирамид близок к 55°. Таким образом, пирамидальные выступы для указанного диапазона напряжений образованы наиболее устойчивыми к окислению атомными плоскостями в структуре алюминия. В случае стохастического расположения каналов величина угла наклона далека от указанного значения, что свидетельствует о образовании граней пирамид плоскостями низкой симметрии и делает процесс формирования анодного оксида алюминия менее стабильным.
ЗАКЛЮЧЕНИЕ
Впервые проведено количественное сравнение морфологии пористых пленок анодного оксида алюминия на поверхности монокристаллов алюминия Al(111), полученных в растворе щавелевой кислоты концентрацией 0.3 М в диапазоне напряжений 20–140 В при температуре ~1°С. Упорядочение пор с образованием гексагонального массива наблюдается в двух узких диапазонах по шкале напряжения (при 40 В и выше 120 В), что согласуется с результатами, полученными ранее на поликристаллических Al подложках. Максимальная степень упорядочения достигнута при анодном окислении алюминия при 40 В: доля пор в гексагональном окружении равна 92%, параметр локального порядка составляет 0.76. По данным АСМ поверхность Al(111) после анодного окисления и селективного удаления пористого оксидного слоя представляет собой массив полусферических углублений, окруженных выступами в форме трехгранных пирамид. При формировании анодного оксида алюминия с упорядоченной структурой грани выступающих пирамид образованы устойчивыми к растворению плоскостями {100} с углом наклона относительно поверхности образца, близким к 55°. При образовании пленок с разупорядоченной структурой угол наклона боковых граней пирамид существенно отличается от указанного значения, что свидетельствует о нестабильной конфигурации границы раздела металл–оксид.
Экспериментально установлены значения коэффициента, связывающего толщину анодного оксида алюминия с плотностью электрического заряда, прошедшего за время электрохимического эксперимента. Наблюдается монотонное увеличение данного параметра с ростом напряжения анодирования от 426 нм · см2/Кл при 20 В до 567 нм · см2/Кл при 120 В. Аппроксимация экспериментальных точек экспоненциальной зависимостью позволяет с высокой точностью определить отношение толщины к плотности заряда для напряжений вплоть до 160 В. Полученные результаты дают возможность воспроизводимо получать пористые оксидные пленки заданной толщины в электролите на основе 0.3 М щавелевой кислоты с использованием in situ кулонометрического контроля электрохимического процесса.
Список литературы
Masuda H., Fukuda K. // Science. 1995. V. 268. P. 1466. https://doi.org/10.1126/science.268.5216.1466
Григорьев С.В., Григорьева Н.А., Сыромятников А.В., Напольский К.С., Елисеев А.А., Лукашин А.В., Третьяков Ю.Д., Эккерлебе Х. // Письма в ЖЭТФ. 2007. Т. 85. № 9. С. 549. https://doi.org/10.1134/S0021364007090081
Beck G., Petrikowski K. // Surf. Coat. Technol. 2008. V. 202. P. 5084. https://doi.org/10.1016/j.surfcoat.2008.04.089
Beck G., Bretzler R. // Mater. Chem. Phys. 2011. V. 128. P. 383. https://doi.org/10.1016/j.matchemphys.2011.03.022
Ng C.K.Y., Ngan A.H.W. // Chem. Mater. 2011. V. 23. P. 5264. https://doi.org/10.1021/cm202461z
Cheng C., Ng K.Y., Aluru N.R., Ngan A.H.W. // J. Appl. Phys. 2013. V. 113. P. 204903. https://doi.org/10.1063/1.4807295
Napolskii K.S., Roslyakov I.V., Romanchuk A.Y., Kapitanova O.O., Mankevich A.S., Lebedev V.A., Eliseev A.A. // J. Mater. Chem. 2012. V. 22. P. 11922. https://doi.org/10.1039/C2JM31710A
Roslyakov I.V., Koshkodaev D.S., Eliseev A.A., Hermida-Merino D., Ivanov V.K., Petukhov A.V., Napolskii K.S. // J. Phys. Chem. C. 2017. V. 121. P. 27 511. https://doi.org/10.1021/acs.jpcc.7b09998
Чумаков А.П., Росляков И.В., Напольский К.С., Елисеев А.А., Лукашин А.В., Eckerlebe H., Bouwman W.G., Белов Д.В., Окороков А.И., Григорьев С.В. // Российские нанотехнологии. 2013. Т. 8. № 9−10. С. 34. https://doi.org/10.1134/S1995078013050029
Roslyakov I.V., Eliseev A.A., Yakovenko E.V., Zabelin A.V., Napolskii K.S. // J. Appl. Crystallogr. 2013. V. 46. P. 1705. https://doi.org/10.1107/S002188981302579X
Roslyakov I.V., Koshkodaev D.S., Eliseev A.A., Hermida-Merino D., Petukhov A.V., Napolskii K.S. // J. Phys. Chem. C. 2016. V. 120. P. 19698. https://doi.org/10.1021/acs.jpcc.6b05268
Mirzoev R.A., Davydov A.D., Zarubenko E.S., Vystupov S.I., Panteleev E.S. // Electrochim. Acta. 2016. V. 218. P. 74. https://doi.org/10.1016/j.electacta.2016.09.115
Mirzoev R.A., Davydov A.D., Vystupov S.I., Kabanova T.B. // Electrochim. Acta. 2019. V. 294. P. 276. https://doi.org/10.1016/j.electacta.2018.10.041
Гордеева Е.О., Росляков И.В., Садыков А.И., Сучкова Т.А., Петухов Д.И., Шаталова Т.Б., Напольский К.С. // Электрохимия. 2018. Т. 54. № 11. С. 999. https://doi.org/10.1134/S0424857018130194
Росляков И.В., Куратова Н.С., Кошкодаев Д.С., Hermida-Merino D., Лукашин А.В., Напольский К.С. // Поверхность. Рентген., синхротр. и нейтрон. исслед. 2016. № 2. С. 39. https://doi.org/10.7868/S0207352816020098
Zaraska L., Stepniowski W.J., Ciepiela E., Sulka G.D. // Thin Solid Films. 2013. V. 534. P. 155. https://doi.org/10.1016/j.tsf.2013.02.056
Gordeeva E.O., Roslyakov I.V., Napolskii K.S. // Electrochim. Acta. 2019. V. 307. P. 13. https://doi.org/10.1016/j.electacta.2019.03.098
Knornschild G., Poznyak A.A., Karoza A.G., Mozalev A. // Surf. Coat. Technol. 2015. V. 275. P. 17. https://doi.org/10.1016/j.surfcoat.2015.04.030
Roslyakov I.V., Gordeeva E.O., Napolskii K.S. // Electrochim. Acta. 2017. V. 241. P. 362. https://doi.org/10.1016/j.electacta.2017.04.140
http://www.eng.fnm.msu.ru/software/
Napolskii K.S., Roslyakov I.V., Eliseev A.A., Byelov D.V., Petukhov A.V., Grigoryeva N.A., Bouwman W.G., Lukashin A.V., Chumakov A.P., Grigoriev S.V. // J. Phys. Chem. C. 2011. V. 115. P. 23726. https://doi.org/10.1021/jp207753v
Kushnir S.E., Pchelyakova T.Y., Napolskii K.S. // J. Mater. Chem. C. 2018. V. 6. P. 12192. https://doi.org/10.1039/C8TC04246B
Sack J.-R., Urrutia J. Handbook of Computational Geometry. Amsterdam: North-Holland, 2000.
Borba J.R., Brito C., Migowski P., Vale T.B., Stariolo D.A., Teixeira S.R., Feil A.F. // J. Phys. Chem. C. 2013. V. 117. P. 246. https://doi.org/10.1021/jp308542d
Дополнительные материалы отсутствуют.
Инструменты
Поверхность. Рентгеновские, синхротронные и нейтронные исследования