Поверхность. Рентгеновские, синхротронные и нейтронные исследования, 2019, № 5, стр. 62-69
Получение, структура и механические характеристики Mo–Si–B слоистого композита
В. М. Кийко 1, *, В. П. Коржов 1
1 Институт физики твердого тела РАН,
142432 Московская область, Черноголовка, Россия
* E-mail: kiiko@issp.ac.ru
Поступила в редакцию 12.06.2018
После доработки 22.06.2018
Принята к публикации 24.06.2018
Аннотация
Разработана методика получения слоистых композитных материалов из молибденовой фольги и порошков кремния и алюминия. Получены образцы материалов, структура которых представляет собой последовательное чередование слоев твердых растворов на основе молибдена и слоев интерметаллидов Mo–Si–B. Испытания при комнатной температуре на трехточечный изгиб показали прочность 400–740 МПа, трещиностойкость 9–20 МПа · м1/2, эффективную поверхностную энергию 6–10 × 103 Дж/м2, прочность 320–360 МПа при температуре 1100°C и 230–290 МПа при температуре 1300°C. Исследована микроструктура композитов до и после разрушения. На основе анализа структуры испытанных образцов выявлены различные механизмы, тормозящие процесс разрушения.
ВВЕДЕНИЕ
Разработки конструкционных материалов, предназначенных для использования при высоких температурах, на основе никеля, ниобия и молибдена с использованием последнего могут привести к получению материалов с наиболее высоким потолком рабочих температур. Высокий модуль упругости молибдена и его интерметаллидов предполагает потенциально высокую прочность и жесткость материалов, полученных на их основе [1–3]. Кроме того, высокие температуры плавления, прочность при высоких температурах и сопротивление ползучести указанных соединений, а также возможность организации повышенного сопротивления окислению (как, например, Mo–Si–B-сплавов [4]) открывают реальную перспективу получения жаропрочных материалов на их основе. Объединение в структуре композитного материала молибдена и его интерметаллидов позволяет также снизить плотность такого композита по сравнению с плотностью собственно молибдена за счет относительно низкой плотности боридов и силицидов молибдена [5]. Проблема трещиностойкости композита, которая возникает в связи с наличием в структуре материала хрупких интерметаллидов, не является непреодолимой. На одну из возможностей ее решения путем торможения трещин на слабой границе раздела хрупких компонентов структуры в четкой постановке, по-видимому, впервые было указано в работе [6]. Эта идея впоследствии использовалась при разработке различных слоистых и волокнистых композитных материалов, например работы [7, 8]. Оптимальная организация слоистой структуры с чередованием слоев интерметаллидов и относительно пластичных слоев твердых растворов бора и кремния в молибдене с соответствующими характеристиками границ раздела между фазами способна обеспечить приемлемый для конструкционного материала уровень трещиностойкости. Изготовление из композитных материалов элементов конструкций во многих случаях происходит еще на стадии формирования структуры материала, а не после его получения, из-за сложности обработки таких материалов после завершения формирования их структуры в технологическом процессе. Кроме того, совмещение технологий получения материала и элемента конструкции удешевляет весь процесс. Однако в ряде случаев придание композитному материалу формы готового изделия представляет непростую задачу. Предлагаемая технологическая схема получения слоистых Mo–Si–B-композитов дает возможность достаточно простого формования изделий из них при получении материалов на стадии, предшествующей образованию хрупких интерметаллидов, когда структура заготовки еще достаточно пластична.
ИЗГОТОВЛЕНИЕ И СТРУКТУРА КОМПОЗИТА
Слоистые композиты Mo–Si–B–1 и Mo–Si–B–2 изготавливались из заготовок, представлявших пакеты листов молибденовой фольги толщиной 50 мкм каждый с Si–B-покрытием. Лист фольги имел размер 30 × 40 мм с направлением прокатки вдоль листа. Покрытие в виде суспензии из смеси порошков кремния и бора в полиэтиленгликоле наносилось на фольгу методом “окрашивания”. Пакеты Mo–Si–B–1 имели двухстороннее покрытие фольги, а Mo–Si–B–2 – одностороннее. Структура заготовок детально представлена в работе [9]. Диффузионная сварка пакетов проводилась при высокой температуре в вакууме не ниже 10–4 мм рт. ст. под давлением в режиме: температура 1500°C, время сварки 0.5 ч, давление 10 МПа, кроме того, проводили дополнительную сварку в режиме 1500°C – 0.5 ч – 14 МПа.
Исследование структуры композитов проводилось на цифровых электронных сканирующих микроскопах Tescan VEGA-II XMU и CamScan MV230 (VEGA TS 5130MM), оснащенных энергодисперсионными рентгеновскими микроанализаторами. Анализ микроструктуры шлифов композита Mo–Si–B–1 [10] в поперечном сечении показал наличие отдельных многофазных участков слоев в зонах исходных покрытий, местами пористых и неоднородных по толщине. Учет этого обстоятельства привел к организации структуры композита Mo–Si–B–2 более плотной, однородной и упорядоченной. Участок поперечного сечения такой структуры представлен на рис. 1а, а распределение по участкам анализа концентраций элементов Mo, Si и B показано на рис. 1б. Затем соединения Mo–Si–B идентифицировались по диаграммам состояния систем Mo–В и Mo–Si. Состав слоев на основе молибдена приходился на доэвтектический участок диаграммы состояния Mo–B (светло-серые участки, раcположенные слева и справа на микрофотографии рис. 1а: 5–11 ат. % бора и не более 0.2 ат. % кремния). Однако в слое, образовавшемся при диффузионной сварке молибдена с Si–B-покрытием (темно-серая вертикальная полоса в центре микрофотографии рис. 1а), где концентрация кремния была больше, чем бора, образовались соединения Mo5Si3–Mo4.32(Si2.47B1.21)3.68. Этот слой окружают две прослойки (серого цвета на микрофотографии рис. 1а) твердого раствора бора в Mo3Si–Mo2.77(Si0.82B0.41)1.23.
Рис. 1.
(а) – микроструктура поперечного сечения композита Mo–Si–B–2 после диффузионной сварки: области светло-серого цвета слева и справа на микрофотографии – Mo(B) + Mo2B, где – Mo(B) – твердый раствор бора в молибдене; области серого цвета – зона Mo3(Si,B); центральная область темно-серого цвета – Mo5(Si,B)3; (б) – концентрационные зависимости молибдена, бора и кремния по данным рентгеноспектрального микроанализа. 1–8 – пронумерованные области проведения рентгеноспектрального анализа.
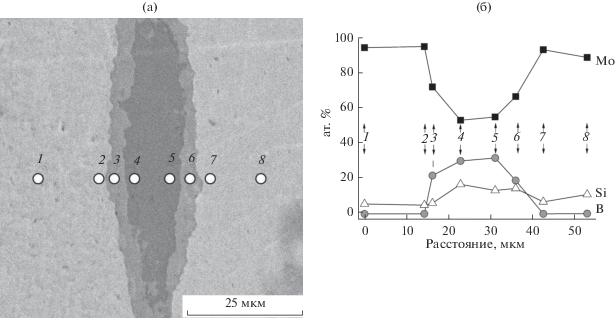
ИСПЫТАНИЯ И ОСОБЕННОСТИ РАЗРУШЕНИЯ СЛОИСТОЙ СТРУКТУРЫ КОМПОЗИТОВ
Из пластин изготовленного композитного материала на электроэрозионном станке вырезались образцы в форме стержней прямоугольного сечения ~1 × 2 мм и длиной от 10 до 40 мм в зависимости от вида экспериментов. Кроме того, если предполагались испытания на трещиностойкость, то в средней части образцов делались боковые надрезы примерно до середины сечения. На полученных образцах определялись следующие физические параметры: плотность, модуль упругости, прочность, трещиностойкость, эффективная поверхностная энергия.
Описанные ниже эксперименты проводились на образцах композитов Mo–Si–B–1 и Mo–Si–B–2, дополнительно механические испытания при высокой температуре проводились на образцах Mo–Si–B–2. Результаты испытаний показали нeзначительную разницу в прочности указанных композитов в отличие от заметных различий в структурах. Прочность определялась в диапазоне температур 20–1300°C, остальные измерения проводились при комнатной температуре. Поскольку материал является анизотропным, испытания на прочность, трещиностойкость и эффективную поверхностную энергию проводились с приложением нагрузок в двух направлениях: перпендикулярно и параллельно слоям структуры в условиях “трехточечного изгиба”. В табл. 1 сведены основные результаты указанных измерений. Для сравнения в табл. 1 приведены не только характеристики композита Mo–Si–B–1, но и данные для слоистых композитов Ni–Al и Nb–Si–B, полученных ранее также твердофазным методом. Плотность определяли методом гидростатического взвешивания в дистиллированной воде (табл. 1). Наличие в структуре композитов интерметаллидов приводит к понижению плотности композитных материалов в сравнении с базовыми металлами: никелем (плотность 8900 кг/м3), ниобием (8570 кг/м3), молибденом (10 200 кг/м3) [11]. Модули упругости материалов образцов (модули Юнга) определялись путем измерения резонансных частот поперечных колебаний образцов в форме балок постоянного по длине прямоугольного поперечного сечения. При колебаниях образцы изгибались в плоскости, перпендикулярной плоскости слоев композита. Методической особенностью данных измерений является закрепление в оснастке вибростенда образца в середине длины последнего, что обеспечивает достаточную точность измерений модуля упругости, которая вычисляласьпо формуле [12]:
где $f$ – частота резонанса поперечных колебаний образца, $l$ – половина длины образца, $h$ – высота образца, ${\rho }$ – плотность материала образца. В табл. приведен результат измерения модуля упругости для слоистого композитного материала Mo–Si–B–1, а также (для сравнения) других слоистых композитов [11]. Образование интерметаллидов в структуре композитов привело к повышению модуля упругости композитов Ni–Al (модуль упругости никеля 200 ГПа) и Nb–Si–B (ниобия – 110 ГПа) и к понижению модуля упругости Mo–Si–B (модуль упругости молибдена 320 ГПа). Однако модуль упругости Mo–Si–B–1-композита остается достаточно высоким, существенно превышая, например, модуль упругости стали (около 210 ГПа).Таблица 1.
Характеристики композитных материалов при комнатной температуре (приведены средние значения). Нагрузки при испытаниях прикладывались перпендикулярно плоскости слоев структуры
Материал | Ni–Al | Nb–Si–B | Mo–Si–B |
---|---|---|---|
Плотность, кг/м3 | 7500 | 7200 | 8600 |
Модуль упругости, ГПа | 220 | 130 | 270 |
Прочность, МПа | 870 | 600 | 620 |
Трещиностойкость, МПа · м1/2 | 20.0 | 13.0 | 12.0 |
Эффективная поверхностная энергия, Дж/м2 | 3500 | 8000 | 10 000 |
Значения прочности при изгибе определялись по формулам сопротивления материалов [14]. Прочность при комнатной температуре в случае нагружения образцов перпендикулярно слоям структуры составила 620 ± 90, а при нагружении параллельно слоям – 590 ± 130 МПа.
Трещиностойкость в величинах критического коэффициента интенсивности напряжений $K{\text{*}}$ вычислялась по формуле [15]:
Таким образом, трещиностойкость составила 12 ± 6 и 14 ± 2.3 МПа · м1/2 при приложениях нагрузки перпендикулярно и параллельно слоям структуры, соответственно.
Для случая нагружения нагрузкой, перпендикулярной плоскости слоев, данные по прочности и трещиностойкости Mo–Si–B–1-композита, а также (для сравнения) Ni–Al- и Nb–Si–B-композитов [11] приведены в табл. 1.
На рис. 2 показаны типичные кривые деформирования при испытаниях образцов на прочность. Видно качественное различие поведения образцов под нагрузкой при приложении нагрузок перпендикулярно и параллельно слоям структуры. При приложении нагрузки перпендикулярно слоям структуры нелинейный ступенчатый характер зависимости нагрузка–прогиб с локальными подъемами нагрузки (рис. 2а) свидетельствует о нехрупком характере разрушения (рис. 3а) со сменой доминирующих видов микроразрушения в процессе продвижения макротрещины (рис. 4а, 5). На микрофотографиях видна извилистость траектории макротрещины (рис. 3а, 4а) с расслоениями по границе раздела между слоями различных фаз, причем, поверхности расслоений имеют негладкий вид, вызванный нехрупким разрушением (вставка на рис. 3а). Расслоения вызывают изменения траектории конца макротрещины. В процессе разрушения кроме расслоений возникает множественное растрескивание достаточно хрупких фаз интерметаллидов и “шейкообразование” относительно пластичных твердых растворов (рис. 4а, 5). Особо следует отметить торможение микротрещин на границах слоев интерметаллидов и твердых растворов (рис. 5). Эти виды микроразрушений вносят существенный вклад в энергию, поглощаемую материалом при его разрушении. При приложении нагрузки параллельно слоям также наблюдается нелинейность зависимости нагрузка–прогиб, но эта зависимость сглажена и имеет более крутой подъем и спад (рис. 2б), чем в первом случае, что определяется более простыми механизмами процесса разрушения при прохождении макротрещины вдоль плоскости слоев структуры. Однако некоторые расслоения наблюдаются и в этом случае (рис. 3б), как и незначительное образование микротрещин в слоях интерметаллидов (рис. 4б). Основной же вклад в трещиностойкость, по-видимому, вносит пластическая деформация твердых растворов на основе молибдена. Подобные процессы разрушения наблюдались, например, в случае испытаний слоистых образцов Ni–Al с боковыми надрезами (испытания на трещиностойкость) [16]. Примеры зависимостей нагрузка–прогиб для Mo–Si–B–1-материала приведены на рис. 6. Качественно они согласуются с результатами испытаний слоистых Ni–Al-образцов.
Рис. 2.
Зависимости нагрузка–прогиб образцов при испытаниях на прочность: (а) – при приложении нагрузки перпендикулярно слоям структуры, (б) – параллельно слоям.
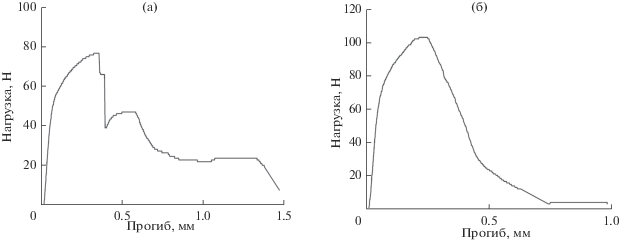
Рис. 3.
Поверхности разрушения образцов при испытаниях на прочность: (а) – при приложении нагрузки перпендикулярно слоям структуры, (б) – параллельно слоям. Представлено по две половины разрушенных образцов на каждом снимке.
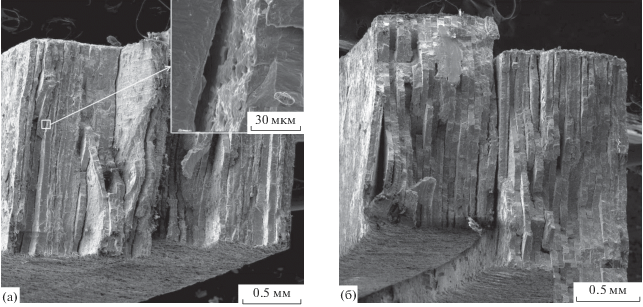
Рис. 4.
Сечения образцов после разрушения; стрелками показаны направления приложения нагрузок; (а) – нагрузка прикладывалась перпендикулярно слоям, (б) – параллельно.
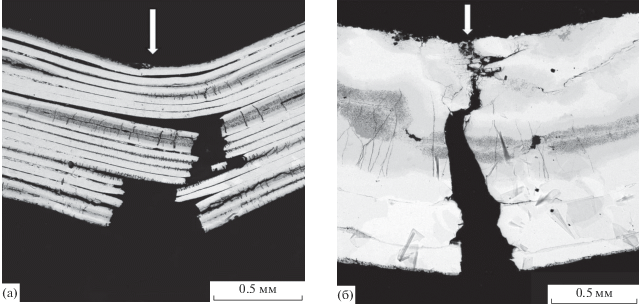
Рис. 5.
Сечение, перпендикулярное плоскости слоев структуры образца после разрушения, в области макротрещины: I – слои твердых растворов на основе молибдена, II – слои интерметаллидов. Белой стрелкой показано направление распространения макротрещины, черными стрелками – микротрещины в слоях интерметаллидов, белыми пунктирными стрелками – образования “шеек” в слоях твердых растворов при прохождении макротрещины.
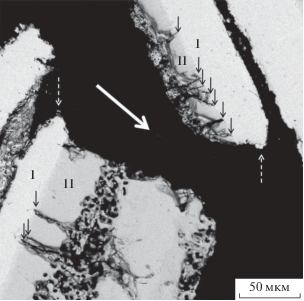
Рис. 6.
Зависимости нагрузка–прогиб образцов с надрезами при испытаниях на трещиностойкость: (а) – при приложении нагрузки перпендикулярно слоям структуры, (б) – параллельно слоям.
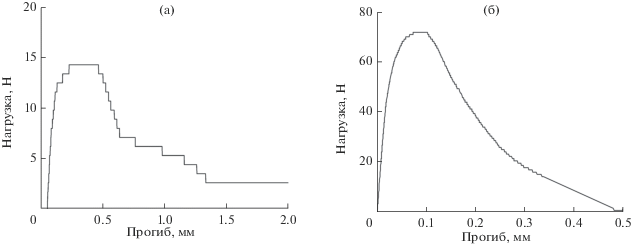
Разрушение образцов в проведенных экспериментах можно рассматривать как разделение их на две части прошедшей в поперечном направлении через образец макроскопической трещиной с образованием двух новых поверхностей (поверхностей разрушения). Оценку эффективной поверхностной энергии разрушения g в этом случае можно определить как отношение работы внешних сил по разрушению образца к удвоенной площади его поперечного сечения: $g = ({1 \mathord{\left/ {\vphantom {1 {2F}}} \right. \kern-0em} {2F}})\int_x {Q(x)dx} ,$ где $Q$ – нагрузка на образец, $x$ – перемещение точки приложения нагрузки к образцу (прогиб образца), $F$ – площадь поперечного сечения образца. Вычисленное значение g для случая приложения нагрузки в направлении, перпендикулярном слоям структуры (рис. 6а), составило 10 × 103, а для случая приложения нагрузки в направлении, параллельном слоям структуры (рис. 6б), составило 6.3 × 103 Дж/м2. Вклад в работу разрушения вносят: эффективная поверхностная энергия компонентов структуры (твердых растворов, интерметаллидов) при прохождении макротрещины, поверхностная энергия микротрещин, пластическая деформация нехрупких слоев твердых растворов, расслоения по границам раздела компонентов, трение по образовавшимся поверхностям микроразрушений (рис. 4, 5). Различие в значениях эффективной поверхностной энергии при приложениях нагрузки перпендикулярно и вдоль плоскости слоев структуры образца объясняется вовлечением различных видов микроразрушений в общее разрушение: их количеством при прохождении макротрещины перпендикулярно и параллельно слоям, соответственно.
При высоких температурах испытания проводились в стальной вакуумной камере с танталовыми нагревателями и молибденовой оснасткой. Нагружение осуществлялось при приложении нагрузки перпендикулярно плоскости слоев композита с целью включения большего количества микромеханизмов сопротивления разрушению, которое наблюдается в сравнении с нагружением вдоль плоскости слоев структуры. Зависимость прочности от температуры приведена на рис. 7. Следует отметить, что прочность слоистых комопзитов Mo–Si–B при температурах 1100–300°C превосходит прочность композитов Ni–Al и Nb–Si–B примерно на 50–100 МПа [17, 18].
ЗАКЛЮЧЕНИЕ
Показана возможность формирования слоистой структуры, состоящей из последовательного чередования слоев твердых растворов и интерметаллидов, из листов молибденовой фольги, покрытой суспензией смеси порошков кремния и бора, методом диффузионной сварки под давлением в вакууме.
Установлено, что представленные в исходном составе элементы Mo, Si и B легко вступают в диффузионное взаимодействие, образуя твердые растворы и интерметаллиды, идентифицируемые по результатам локального спектрального микроанализа с использованием диаграмм состояния указанных элементов.
Вариациями толщины и способов нанесения на молибденовую фольгу суспезии возможно управление структурой интерметаллидных слоев.
Определены характеристики слоистых композитов Mo–Si–B: плотность, модуль упругости, прочность, трещиностойкость, эффективная поверхностная энергия.
Прочность полученных композитных материалов не уступает лучшим конструкционным сплавам аналогичного назначения в широком диапазоне температур, а жесткость превосходит многих из них.
Значение трещиностойкости полученных материалов занимает промежуточное положение между соответствующими значениями для керамик и высокопрочных сплавов, однако не является вполне достаточным для их широкого применения в качестве конструкционных. В этой части композитная структура нуждается в дальнейшей оптимизации путем выбора исходных составов и технологических режимов.
Полученные результаты по формированию структуры, механическим испытаниям и анализу процессов разрушения носят достаточно общий характер и могут служить основой для разработки иных слоистых конструкционных материалов на основе тугоплавких металлов, упрочненных интерметаллидами.
Список литературы
Свойства, получение и применение тугоплавких соединений / Ред. Косолапова Т.Я. М.: Металлургия, 1986. 928 с.
Schneibel J.H. // Intermetallics. 2003. № 11. P. 625.
Sharif A.A., Misra A., Mitchell T.E. // Scripta Materialia. 2005. № 52. P. 399.
Jain P., Kumaru K.S. // Acta Materialia. 2010. V. 58. № 6. P. 2124.
Гороновский И.Т., Назаренко Ю.П., Некряч Е.Ф. Краткий справочник по химии. Киев: Наукова думка, 1987. 929 с.
Cook J., Gordon J.E. // Proceedings of the Royal Society. 1964. V. 282. № 8. P. 508.
Анищенков В.М., Милейко С.Т. // ДАН СССР. 1978. V. 241. № 5. С. 1068.
Kolchin A.A., Kiiko V.M., Sarkissyan N.S., Mileiko S.T. // Composite Science and Technology. 2001. V. 61. P. 1070.
Коржов В.П., Кийко В.М., Прохоров Д.В. // Перспективные материалы и технологии. Т. 1. Витебск, 2017. С. 373.
Kiiko V., Prokhorov D., Stroganova T., Zheltyakova I., Ershov A., Korzhov V. // Machines, Technologies, Materials. 2017. V. 8. P. 422.
Коржов В.П., Кийко В.М., Прохоров Д.В. // Перспективные материалы и технологии. Материалы международного симпозиума. Витебск, 2017. С. 10.
Кийко В.М. // LVIII Международная конференция Актуальные проблемы прочности. Пермь, 2017. С. 194.
Феодосьев В.И. // Сопротивление материалов. Москва: Наука, 1979. 560 с.
Рудицин М.Н., Артемов П.Я., Любошиц М.И. Справочное пособие по сопротивлению материалов. Минск: Высшая школа, 1970. 632 с.
Броек Д. Основы механики разрушения. М: Высшая школа, 1980. 368 с.
Кийко В.М., В.П. Коржов В.П. // Поверхность. Рентген., синхротр. и нейтрон. исслед. 2017. № 11. С. 47.
Коржов В.П., Кийко В.М. // Деформация и разрушение материалов. 2015. № 6. С. 11.
Kiiko V.M., Korzhov V.P. // Materials, Methods & Technologies. 2017. V. 11. P. 35.
Дополнительные материалы отсутствуют.
Инструменты
Поверхность. Рентгеновские, синхротронные и нейтронные исследования