Поверхность. Рентгеновские, синхротронные и нейтронные исследования, 2019, № 5, стр. 49-57
Роль топографических дефектов поверхности в формировании слоев углеродных нанотрубок на поверхности массивного никеля
С. Г. Львов 1, *, **, Е. Ф. Куковицкий 1, В. А. Шустов 1, Н. М. Лядов 1
1 Казанский физико-технический институт им. Е.К. Завойского –
обособленное подразделение ФИЦ КазНЦ РАН
420029 Казань, Россия
* E-mail: lvov@kfti.knc.ru
** E-mail: sglvov@yandex.ru
Поступила в редакцию 23.07.2018
После доработки 10.08.2018
Принята к публикации 10.08.2018
Аннотация
Методами оптической, растровой электронной и атомно-силовой микроскопии, рентгеноструктурного анализа, профилометрии исследованы начальные стадии процесса химического осаждения углерода из газовой фазы на поверхность никеля, предварительно подвергнутую различной абразивной обработке. Выявлено, что локальное ускоренное формирование слоев углерода с сильно разупорядоченной структурой уже на начальной стадии осаждения является причиной неоднородностей слоев углеродных нанотрубок, синтезируемых непосредственно на поверхности металла. Наблюдается увеличение скорости осаждения на топографических поверхностных дефектах, включая микрополости с большим отношением площадь−объем. Негерметичные микрополости в подповерхностном слое, сформированные в процессе абразивной обработки, также являются центрами ускоренного образования углеродных слоев. Природа ускорения – особая химия пиролиза углеводородов в условиях продолжительного нахождения в микрополостях. Высокая скорость осаждения углерода ведет к образованию внутри таких дефектов углеродных форм с сильно разупорядоченной структурой. Происходит интенсивное углеводородное распыление металла на микроразмерных шероховатостях, микровыступах, сформировавшихся в ходе абразивной обработки. Образование многочисленных микротрещин на этих дефектах из-за коррозионного распыления, в свою очередь, стимулирует появление центров ускоренного образования в ограниченных объемах углерода с неупорядоченной структурой.
ВВЕДЕНИЕ
Среди многочисленных практических приложений углеродных нанотрубок (УНТ) использование их в качестве полевых эмиттеров электронов наиболее перспективно. Высокая электропроводность контакта между слоем УНТ и подложкой и высокая адгезия слоя к подложке – критически важные критерии получения стабильной полевой эмиссии и высоких величин эмиссионного тока. Для практической реализации также необходима совместимость методов получения автоэмиттеров с существующими технологиями вакуумной электроники. Формирование слоя УНТ непосредственно на подложке каталитически активных металлов удовлетворяет этим требованиям. Слои УНТ на фольге из массивного никеля с достаточно хорошими электронно-эмиссионными характеристиками были получены ранее [1, 2]. Несмотря на большую плотность эмиссионного тока и высокий уровень стабильности, достигнутые ранее в подобных эмиттерах [1], сформированные слои УНТ демонстрируют очевидные морфологические неоднородности. Важно выявить причины их образования для повышения эмиссионных характеристик.
Для подготовки поверхности к формированию слоя нанотрубок применяются различные способы, в том числе методы механической обработки. Экспериментально установлено, что осаждение углерода на массивный каталитически активный металл зависит не только от состояния поверхности, но и от микроструктуры подповерхностных слоев металла [3]. Было обнаружено, что скорость образования нанотрубок углерода на поверхности переходных металлов существенно возрастает, если поверхность подвергнуть интенсивной пластической деформации, в результате которой образуется тонкий слой наноструктурированного металла [4–7]. Влияние обработки поверхности на количество и морфологию осаждаемых слоев углерода объяснялось исключительно его ускоренной межзеренной диффузией в наноструктурированном металле и создаваемыми каталитически активными центрами, т.е. специфической конфигурацией атомов металла, локализованных в кристаллографических или топографических дефектах поверхности – нарушениях структуры решетки металла (например, на границах зерен) [4, 8, 9]. Работы, посвященные исследованию осаждения слоя углерода на поверхности металла и его морфологии [10–12], ограничивались простой констатацией факта быстрого локального осаждения на топографических дефектах поверхности.
Настоящие исследования – продолжение изучения микроструктуры приповерхностных слоев никелевых подложек [4]. Цель работы – идентифицировать поверхностные и подповерхностные явления, связанные с присутствием топографических микродефектов и вызывающие неоднородное осаждение углерода из газовой фазы на никелевую подложку на ранней стадии процесса, а также прояснить роль абразивной обработки поверхности в создании дефектов, влияющих на кинетику осаждения и морфологию углеродного слоя.
ЭКСПЕРИМЕНТ
Подготовка образцов. Эксперименты проводили для оценки влияния абразивной обработки поверхности на осаждение углерода из газовой фазы. Процедуры механической и химической обработки, примененные к никелевым фольгам, представлены в табл. 1. Одна сторона круглых поликристаллических (со средним размером кристаллитов ~40 мкм) никелевых подложек диаметром 12 мм и толщиной 0.2 мм была подвергнута шлифованию и в двух случаях дополнительному полированию. Использовали однонаправленное шлифование (без вращения образца), чтобы упростить анализ результатов экспериментов. Типичные условия шлифовки и полировки на вращающемся диске: давление ~10–1 МН/м, линейная скорость ~2–3 м/с. Обратная сторона никелевых образцов была предварительно деактивирована для предотвращения осаждения углерода.
Таблица 1.
Обозначения процедур и способы обработки образцов
Обозначение | Процедура |
---|---|
A1 | Ni-фольга толщиной 0.2 мм, шлифованная абразивной бумагой SiC с зерном 100 мкм |
A2 | Ni-фольга толщиной 0.2 мм, шлифованная абразивной бумагой SiC с зерном 36 мкм |
A3 | Ni-фольга толщиной 0.2 мм, шлифованная абразивной бумагой SiC с зерном 15 мкм |
A3 + P | Ni-фольга толщиной 0.2 мм, шлифованная абразивной бумагой SiC с зерном 15 мкм, а затем полированная алмазной пастой с частицами размером 6 мкм |
P | Ni-фольга толщиной 0.2 мм, шлифованная абразивной бумагой SiC с зерном 15 мкм для сглаживания поверхности, затем химически полированная для удаления деформированного слоя и полированная алмазной пастой с частицами размером 6 мкм |
Процесс химического осаждения из газовой фазы (ХОГФ) и кинетические измерения. В экспериментах по ХОГФ был использован описанный ранее [2] реактор с горячими стенками. В качестве углеродсодержащего прекурсора применяли гранулированный полиэтилен. Обычно при пиролизе расходуется до 0.5 г полиэтилена. Пиролиз происходил при температуре ~700°С в атмосфере гелия при давлении 1.2 атм. Продуктом термического разложения полиэтилена является сложная смесь углеводородов, состав которой в закрытом реакторе не контролируется. В реализованном процессе ХОГФ эта смесь доставляется в зону расположения подложек путем естественной конвекции в газовом столбе, нагреваемом снизу [2]. Одинаково обработанные образцы укладывали в стопки попарно направленными друг к другу обработанными поверхностями. Зазор между ними, существующий из-за не параллельности поверхностей, был оценен в ~30 мкм. Высота стопки из 10 подложек не превышала 2 мм. Такое расположение подложек позволяет реализовать диффузионный механизм газового транспорта в узком зазоре между подложками в отличие от неконтролируемого конвекционного транспорта в объеме реактора. Каждая пара подложек, разделенных узкой щелью, представляет собой микрореактор с каталитически активными стенками. Диффузионный характер газового транспорта в таком микрореакторе обеспечивает длительное время нахождения в сравнении со временем на открытой поверхности и, как следствие, возможность протекания цепочек химических реакций, специфичных для ограниченных объемов. Если конечным продуктом таких реакций является углерод, то наблюдаемая скорость образования углеродного слоя в таких объемах может быть больше скорости его осаждения во внешнем пространстве [2]. Использованная геометрия сделала возможным одновременное проведение экспериментов со многими подложками в идентичных условиях, обеспечив корректное сравнительное исследование различных поверхностей. Углеродный слой осаждался на обработанные поверхности в процессах ХОГФ различной длительности (1–15 мин). Скорости осаждения углерода на начальных стадиях определены в прерываемых кратковременных процессах ХОГФ (1–2 мин) при температурах подложек 600 и 650°С. Эти условия были выбраны, чтобы минимизировать образование углерода в газовой фазе. Оценочные данные о кинетике осаждения были получены в результате взвешивания металлических образцов до и после процесса осаждения. Слои углеродных нанотрубок выращивали при более длительных процессах (12–15 мин) при 800°С.
Методы характеризации и исследования. Для характеризации образцов применяли оптическую микроскопию (микроскоп Olympus DX51), растровую электронную микроскопию (РЭМ) и энергодисперсионный элементный анализ, атомную силовую микроскопию (АСМ). Использовали растровый электронный микроскоп Carl-Zeiss EVO 50XVP с микроанализатором INCA Energy 350 (Oxford Instruments). Уровень шероховатости обработанных поверхностей определялся с помощью профилометра TR-200 (Time Group Inc.). Прибор имеет разрешение по вертикали не менее 10 нм. Определяемые параметры шероховатости соответствовали ISO 4287–1997. Микроскопические исследования взаимодействия никель–углерод наиболее информативны на ранней стадии осаждения углерода, когда еще нет значительного покрытия поверхности разупорядоченными формами углерода. Образцы с более толстым углеродным слоем исследовали методом дифракции рентгеновских лучей, падающих под углом к поверхности подложки α = 2°. Полный дифракционный спектр был получен на дифрактометре ДРОН-7 в диапазоне углов 2θ = 15°–58° при использовании CuKα-излучения. Для проведения полнопрофильного анализа дифракционного спектра была использована программа MAUD 2.33 [13].
РЕЗУЛЬТАТЫ И ИХ ОБСУЖДЕНИЕ
Изменение шероховатости подложек после обработки показано на рис. 1 (Rq – среднеквадратичное отклонение профиля поверхности). Кинетические данные осаждения углерода на никелевые подложки приведены на рис. 2. Эти данные были получены в процессах длительностью 1–2 мин с использованием пиролизованного полиэтилена массой 0.2 г. Скорости осаждения были рассчитаны с учетом увеличения площади поверхности шлифованных подложек A1–A3 по отношению к плоской поверхности полированных образцов [14].
Рис. 2.
Зависимость скорости осаждения углерода от процедуры обработки поверхности и температуры процесса ХОГФ.
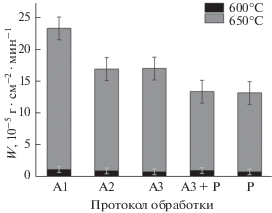
Ниже описаны результаты исследования методом оптической микроскопии никелевых подложек после процедур механической обработки в соответствии с табл. 1, а также после кратковременных процессов химического осаждения углерода при температурахе 600 и 650°С. Детектируемые особенности ограничиваются размером несколько микрометров.
Шлифованные подложки, серия А1–А3. Основными особенностями шлифованных поверхностей А1–А3 являются выраженные бороздки от частиц абразива с гребнями пластически деформированного металла по обе стороны бороздок. Глубина и ширина борозд уменьшается в этой серии, что подтверждается уменьшением параметра Rq (рис. 1). Другая особенность – это наличие отдельных скрепленных с поверхностью кусочков (чешуек) металла, имеющих вид “смазанного” металла. Наибольшее количество подобных фрагментов имеется в образце А1, а наименьшее – в образце А3. То же относится к их размерам (толщина по измерениям АСМ ~0.5–1.5 мкм).
После процесса ХОГФ, проведенного при температуре 600°С, на поверхности подложки образуется углеродный слой в основном в виде коричневатой пленки, которая покрывает почти всю подложку, повторяя ее морфологию (рис. 3а). Этот слой имеет графитоподобную структуру. Также наблюдаются приподнятые над уровнем поверхности на ~1 мкм упомянутые выше чешуйки металла (рис. 3а, вставка).
Рис. 3.
Оптические микрофотографии поверхности образца А1 после процессов ХОГФ: а − при 600°С, стрелки указывают на возникающие области коксоподобного углерода; б − при 650°С. Вставки показывают приподнятые над поверхностью фрагменты металла.
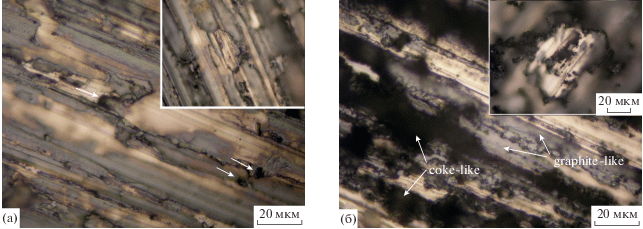
Температура 650°С значительно ускоряет процесс осаждения углерода (рис. 2). Скорость осаждения на подложку А1 при этой температуре наибольшая. На поверхности образуются слои углерода двух видов: графитоподобного и коксоподобного. Если первый имеет прежнюю морфологию, то второй появляется в виде черных бесформенных пятен и областей (рис. 3б). Фрагменты металла на поверхности исчезают за выростами коксоподобного углерода или оказываются приподнятыми над поверхностью на высоту до 10 мкм (рис. 3б, вставка).
Скорость осаждения углерода при температуре 600°С не зависит от вида абразивной обработки и практически одинакова для всех подложек (рис. 2). Скорость осаждения при температуре 650°С, при которой формируется коксоподобный углерод, наивысшая в случае наиболее шероховатых подложек А1 и спадает в случае подложек А3 и полированных подложек, на которых образование коксоподобного углерода почти не наблюдается.
Для определения структурных характеристик углеродного слоя были проведены дифракционные исследования подложек А1 после процессов ХОГФ при 600 и 650°С (рис. 4, табл. 2). Основная фракция углерода при 600-градусном процессе подобна турбостратному графиту (как это было определено в [2]). Коксоподобный углерод оказался графитом с большей степенью разупорядочения. Известно, что чем выше скорость осаждения углерода, тем больше степень разупорядочения его структуры. Выявленное относительное массовое содержание углеродных фаз для процесса при Т = 650°С находится в удовлетворительном соответствии с результатами измерений массы (рис. 2) и исследований методами микроскопии.
Рис. 4.
Определение вкладов графитоподобной (1) и коксоподобной (2) углеродных фаз в рефлекс 002 после процессов ХОГФ при: а – 600; б – 650°C. Точки – эксперимент, приведены также результирующие кривые.
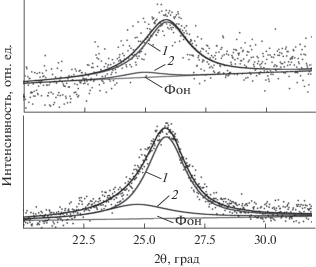
Таблица 2.
Результаты рентгеноструктурного анализа углеродных слоев на подложке А1
Вид углерода | Содержание (мас. %) и постоянная решетки (Å) | |||
---|---|---|---|---|
600°C | 650°C | |||
Графитоподобный | 94 | d002 = 3.39 ± 0.02 | 75 | d002 = 3.39 ± 0.02 |
Коксоподобный | 6 | d002 = 3.52 ± 0.10 | 25 | d002 = 3.55 ± 0.1 |
Поскольку образование двух фаз углерода происходит одновременно и в одинаковых экспериментальных условиях на одной и той же поверхности, следует допустить, что образование коксоподобного углерода обусловлено топографическими особенностями поверхности. Наблюдения подтверждают, что он формируется на границах упомянутых выше дефектов поверхностей – чешуек “смазанного” шлифовкой металла, гребней, выступов и (в редких случаях) на дне глубоких борозд. Коксоподобный углерод образуется также и после процесса при температуре 600°С (рис. 3а, стрелки). В результате наблюдений с помощью оптической микроскопии обнаружено, что разупорядоченный углерод образуется в основном на дне бороздок, для которых отношение глубина/ширина не меньше чем 0.5.
В образце А3 коксоподобный углерод почти отсутствует. Этот позволяет наблюдать особенности и дефекты поверхности после процесса ХОГФ. На рис. 5 представлена растрескавшаяся поверхность гребней металла, разделенных соседствующими бороздками. Эти растрескавшиеся области – результат высокотемпературной углеводородной коррозии поверхности металла. Рис. 5 демонстрирует, что коксоподобный углерод зарождается и растет в трещинах поверхности. Индивидуальные углеродные волокна уже появляются как часть этой углеродной фазы. Элементный микроанализ был проведен в областях 1–3. Никель отсутствует в графитоподобном углероде (область 3), коксоподобный углерод в областях 1 и 2 содержит 3–4 ат. % никеля.
Рис. 5.
РЭМ-изображение поверхности образца A3: а – после процесса ХОГФ при 650°C; б – увеличенное изображение. В областях 1–3 проведен энергодисперсионный анализ, белые области в правом нижнем углу – образования коксоподобного углерода.
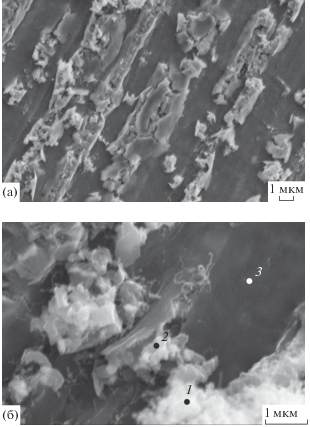
Полированные подложки А3 + Р и Р. Оптическая микроскопия показывает, что до процессов осаждения полированные подложки А3 + Р и Р имели идентичную гладкую поверхность без выраженных особенностей. Поверхности полированных подложек после процессов ХОГФ при температуре 600°С также идентичны и не имеют видимых особенностей, характерных для шлифованных образцов. Однако после осаждения при 650°С точечные образования коксоподобного углерода на подложке A3 + P более многочисленны по сравнению с подложкой Р (рис. 6). Для прояснения причин такого отличия был проведен дополнительный процесс ХОГФ такой же длительности при Т = 650°С, но при увеличенной концентрации реактивных газов. В случае подложки Р не выявлено качественного изменения, за исключением увеличения массы осажденного углерода. Состояние поверхности подложки А3 + Р до и после 650°C процесса ХОГФ показано на рис. 7. Наблюдаемую эволюцию поверхности можно объяснить следующими процессами. После шлифования вся поверхность покрыта перекрывающимися царапинами, образовавшимися в результате воздействия режущих точек абразива (рис. 7a). Все царапины исчезают после алмазной полировки, и микрофотография демонстрирует гладкую поверхность с некоторыми микроскопическими дефектами (рис. 7б). После осаждения углерода при температуре 650°С поверхность вновь становится негладкой (рис. 7в). РЭМ-изображение демонстрирует испещренную бороздками поверхность подложки (рис. 8). Внутри бороздок наблюдаются малые частицы, предположительно, углеродной природы. Отогнутые металлические лепестки (указаны стрелками) по обеим сторонам бороздок, вероятно, ранее перекрывали бороздки сверху. Такие же лепестки часто видны вокруг маленьких ямок в гладких областях между бороздками. Углеродный материал, предположительно, растет из-под этих лепестков металла.
Рис. 6.
Оптические микрофотографии полированных подложек после процесса ХОГФ при 650°С: a − подложка A3 + P, стрелки указывают на образования коксоподобного углерода; б − подложка Р.
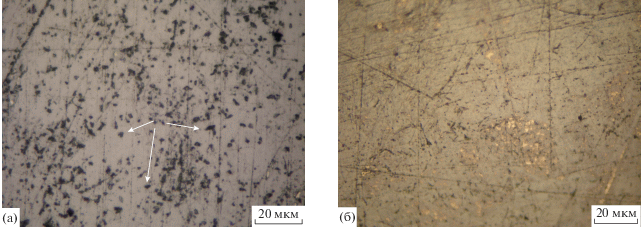
Рис. 7.
Оптические микрофотографии поверхности подложек: a − исходной A3; б − A3 + P; в – A3 + P после процесса ХОГФ при 650°С при увеличенной концентрации реакционных газов.
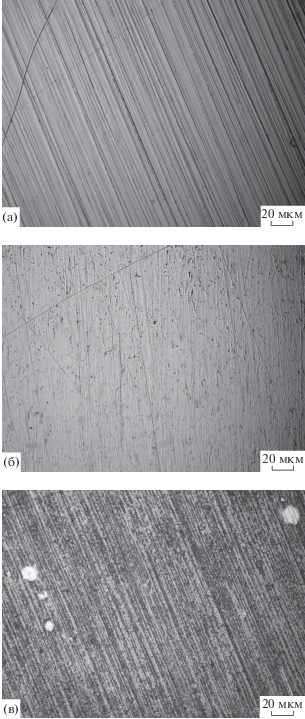
Рис. 8.
РЭМ-изображения поверхности, показанной на рис. 7в. Стрелки указывают на отогнутые лепестки металла.
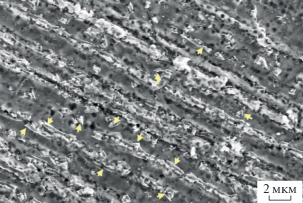
Обобщая наблюдения, можно сделать вывод, что местами ускоренного осаждения углерода являются поверхностные дефекты, возникающие вследствие образования негерметичных микрополостей в ходе шлифовки и полировки, а также неровностей микронного размера при абразивной обработке, подверженных быстрому насыщению углеродом и приводящих к процессу растрескивания металла. Схематически эти дефекты приведены на рис. 9.
Рис. 9.
Схематическое изображение топографических особенностей поверхности, способствующих быстрому осаждению углерода: a – гребни и щели, образовавшиеся в процессе бокового сдвига металла; б – обломки металла, скрепленные с поверхностью; в – гребни и долины поверхности, обработанной абразивом; г – предполагаемое формирование приповерхностных полостей различной формы при полировке поверхности. Серые стрелки – микрополости и микрощели. Черные стрелки – микровыступы.
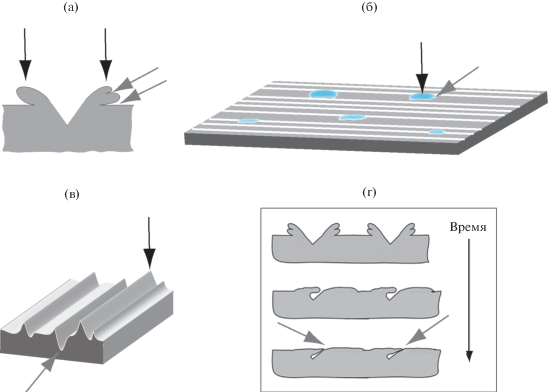
Получение слоев УНТ на обработанных подложках. Углеродные нанотрубки были выращены в процессе ХОГФ длительностью 12 мин при Т = = 800°С. Описанная ранее геометрия использовалась для подложек А3 + Р и Р. Слои углеродных нанотрубок, выращенных на подложках А3 + Р и Р, показаны на рис. 10а, 10б соответственно. Внешняя морфология и внутренняя микроструктура углеродных волокон, полученных в процессах ХОГФ, подробно изучены в [15].
Выше было показано, что рост слоев углерода с неупорядоченной структурой начинается раньше (и возможен при более низкой температуре), чем процесс фрагментации поверхностных слоев металла, приводящий к зарождению углеродных нанотрубок. Большие углеродные выросты, быстро сформировавшиеся в начале осаждения углерода, включаются затем в слой углеродных нанотрубок, образующийся в продолжительном процессе ХОГФ. Такие включения ухудшают структуру и поверхностную топографию слоя нанотрубок. Светлые пятна на рис. 10а – это бугры, сформировавшиеся благодаря углеродным выростам, возникшим на ранней стадии процесса ХОГФ из-за быстрого локального образования коксоподобного углерода на поверхностных и подповерхностных дефектах. Такие бугры почти отсутствуют на подложке, обработанной по процедуре Р (рис. 10б).
ЗАКЛЮЧЕНИЕ
Изучено химическое осаждение углерода из газовой фазы на механически обработанные поверхности массивного никеля с использованием полиэтилена в качестве прекурсора. При последовательном переходе от грубых к более гладким поверхностям шлифованных подложек (А1–А3) в процессе осаждения образуются слои углерода двух типов: коксоподобного и графитоподобного. Слои, формирующиеся на поверхностных дефектах с высоким отношением площадь/объем, характеризуются высокой скоростью осаждения и разупорядоченной структурой. Такие дефекты могут иметь место как на поверхности (царапины, щели), так и в подповерхностном слое в виде негерметичных микропустот. Формирующиеся при абразивной обработке микровыступы склонны к быстрому насыщению углеродом и приводят к коррозионному растрескиванию металла, ускоряющему образование коксоподобного углерода.
Целью абразивной подготовки металлических подложек к синтезу на них слоев УНТ является создание условий для однородной по площади и синхронной фрагментации поверхности в результате проникновения углерода в подложку в процессе ХОГФ. Полученные данные позволяют сделать вывод о влиянии на фрагментацию не только поверхностной топографии, но и скрытых подповерхностных микроскопических дефектов. Именно такие дефекты приводят к образованию локально неоднородных слоев УНТ даже в случае тщательно полированной и визуально качественной поверхности.
Неоднородность слоев углеродных нанотрубок, полученных непосредственно на металлических подложках, оказывает сильное влияние на функциональность устройств, например, на характеристики полевых эмиттеров на базе углеродных нанотрубок. Метод подготовки поверхности, включающий последовательные процессы механической шлифовки, химического полирования и тонкой механической полировки (процедура Р), обеспечивает высокую гладкость поверхности и предотвращает образование скрытых подповерхностных дефектов, что позволяет формировать более однородные слои углеродных нанотрубок на массивной никелевой фольге в используемом процессе ХОГФ.
Список литературы
Куковицкий Е.Ф., Львов С.Г. // Нано- и микросистемная техника. 2010. Т. 6. С. 2.
Kukovitsky E.F., Lvov S.G. // ECS J. Solid State Sci. Tech. 2013. V. 2. P. M51.
Куковицкий Е.Ф., Львов С.Г., Саинов Н.А. и др. // Нано- и микросистемная техника. 2002. Т. 7. С. 28.
Kukovitsky E.F., L’vov S.G., Sainov N.A. et al. // Appl. Surf. Sci. 2003. V. 215. P. 201.
Reddy N.K., Meunier J.L., Coulombe S. // Mater. Lett. 2006. V. 60. P. 3761.
Yang X.F., Lu J. // Appl. Surf. Sci. 2013. V. 264. P. 191.
Xu J.Y., Lei X.C., Yang R. et al. // J. Nanomater. 2014. P. 690630.
Presland A.E.B., Walker P.L. // Carbon. 1969. V. 7. P. 1.
Baird T., Fryer J.R., Grant B. // Carbon. 1974. V. 12. P. 591.
Du C.S., Pan N. // Mater. Lett. 2005. V. 59. P. 1678.
Quah E.B.H., Li C.Z. // Appl. Catalysis. A. 2003. V. 250. P. 83.
Bernardo C., Trimm D.L. // Carbon. 1976. V. 14. P. 225.
Lutterotti L. // Nucl. Instrum. Methods Phys. Res. B. 2010. V. 268 P. 334.
Lam W.P.W., Kerr C., Chaudhary A.J. et al. // Struers J. Materialography. 2004. V. 1. P. 1.
Kiselev N.A., Sloan J., Zakharov D.N. et al. // Carbon. 1998. V. 36. P. 1149.
Дополнительные материалы отсутствуют.
Инструменты
Поверхность. Рентгеновские, синхротронные и нейтронные исследования