Поверхность. Рентгеновские, синхротронные и нейтронные исследования, 2020, № 10, стр. 101-104
Исследование качества поверхности усталостных образцов из сплава Ti–6Al–4V методами рентгеноструктурного анализа
М. С. Калиенко a, b, *, А. В. Желнина a, А. В. Волков a
a ПАО “Корпорация ВСМПО-АВИСМА”
624760 Верхняя Салда, Россия
b Уральский федеральный университет им. первого Президента России Б.Н. Ельцина
620002 Екатеринбург, Россия
* E-mail: kamak@yandex.ru
Поступила в редакцию 11.12.2019
После доработки 22.01.2020
Принята к публикации 24.01.2020
Аннотация
Усталостная прочность материала при испытании зависит от большого числа параметров, в частности от состояния поверхности. В представленной работе были исследованы образцы из титанового сплава Ti–6Al–4V после механической обработки. Проведена оценка распределения плотности дислокаций и остаточных напряжений методами рентгеноструктурного анализа. Установлено, что поверхностный пластически деформированный слой после точения новым инструментом составляет 30 мкм и увеличивается до 40 мкм при использовании инструмента, имеющего износ. Остаточные напряжения на поверхности составляют –190 МПа и достигают максимального значения –220 МПа в подповерхностном слое после точения усталостного образца изношенным инструментом. Данное распределение остаточных напряжений с пиком на некотором расстоянии от поверхности и дальнейшем снижении до нуля характерно для точеных образцов.
ВВЕДЕНИЕ
Титановый сплав Ti–6Al–4V имеет высокую удельную прочность, хорошее сопротивление коррозии, высокую вязкость разрушения и обладает совместимостью с композитами. Благодаря данным свойствам он широко используется в авиастроении для изготовления различных деталей – от компонентов фюзеляжа до лопаток турбореактивного двигателя. [1]. Большое количество деталей работает при циклических нагрузках, поэтому усталостное разрушение может быть наиболее вероятным. В связи с этим всестороннее изучение вопросов, связанных с усталостным разрушением и испытаниями является важной научно-технической задачей.
Patric J. Golden и др. [2] провели исследование с целью определить влияние подготовки поверхности на вариабельность усталостной жизни сплава Ti–6Al–4V. Усталостная прочность металла была исследована на 122 круглых образцах с различным качеством поверхности при четырех фиксированных нагрузках. Образцы были изготовленные по двум схемам: 1) образцы со сжимающими остаточными напряжениями на поверхности (–200…–250 МПа) после точения и механической продольной полировки камнем; 2) часть образцов изготовленных по первой схеме были термически обработаны в вакууме при температуре 704°С в течение 1 ч, после чего была проведена электрополировка со съемом 50 мкм с поверхности (образцы без остаточных напряжений на поверхности). В результате работы были сделаны следующие выводы: в ходе повторных испытаний материала в одном структурном состоянии при одной нагрузке наблюдается разброс полученного количества циклов, которой не имеет ни нормального не логнормального распределения вероятности; наблюдается сложная зависимость вероятности разрушения от приложенного напряжения – двойное распределение; разброс значений у образцов после электрополировки в области малоцикловой усталости менее чувствителен к прикладываемому напряжению и на количество циклов при испытании, прежде всего, оказывает период до зарождения трещины, который из-за наличия остаточных напряжений больше у механически полированных образцов. В дальнейшем продолжении данной работы [3], было показано, что образование и ориентация усталостной фасетки разрушения влияет на зарождение трещины в исследованном двухфазном сплаве. Данное исследование показывает, что на вариативность усталостной жизни сплава Ti–6Al–4V оказывает влияние структура металла и качество поверхности усталостных образцов.
В литературе имеется большое количество работ по исследованию взаимосвязей между механической обработкой и целостностью поверхности [4–8], но работ касающихся вопросов механической обработки при изготовлении усталостных образцов крайне мало. Поэтому целью представленной работы было исследовать качество поверхности усталостных образцов после точения. Эта информация необходима для разработки технологии изготовления усталостных образцов, а именно для определения глубины снимаемого материала при финишной полировке, которая проводится с целью получения требуемой шероховатости поверхности и удаления пластически деформированного слоя, образующегося при точении.
ЭКСПЕРИМЕНТАЛЬНАЯ ЧАСТЬ
Исследование проведено на материале прутка из сплава Ti–6Al–4V производства ПАО “Корпорация ВСМПО-АВИСМА”. Круглые усталостные образцы были изготовлены из прутка при использовании новой и изношенной токарной пластины при одинаковых параметрах резания. Механическая обточка образцов проводилась на машине TRAUB model TNA300 с использованием охлаждающей жидкости.
Профиль распределения плотности дислокаций и остаточных напряжений исследован при послойном химическом травлении образцов с последующим исследованием методами рентгеноструктурного анализа [9]. Оценку остаточных напряжений проводили вдоль оси образцов на дифрактометре Bruker D8 Advance методом sin2ψ, используя дифракционный пик α-фазы титана (21.3), программный пакет Leptos 5.04. Распределение остаточных напряжений представлено без коррекции на релаксацию напряжений и градиент. Рентгеноструктурный анализ профиля дифракционных линий проводили, используя программный пакет TOPAS [10]. Распределение дислокаций на поверхности образцов после точения оценивали посредством измерения ширины на половине высоты (FWHM) дифракционного пика α-фазы титана (21.3).
Исследование поверхности образцов проводили на электронном сканирующем микроскопе FEI Quanta 3D FEG и на оптическом бинокулярном микроскопе Leica MZ12.5.
РЕЗУЛЬТАТЫ И ИХ ОБСУЖДЕНИЕ
Новая и использованная ранее токарные пластины представлены на рис. 1. На режущих кромках использованной ранее пластины наблюдается формирование кратеров и характерный налип металла. При точении заготовки происходит изменение геометрии режущих кромок токарной пластины вследствие чего изменяется качество поверхности. На износ инструмента оказывают влияние различные параметры, такие как, геометрия инструмента, материал инструмента и заготовки, их физические, механические и химические свойства, а также параметры среды и резания [11].
Рис. 1.
Снимки токарных пластин с оптического бинокулярного микроскопа (a, б) и снимки, полученные на растровом электронном микроскопе (в, г).
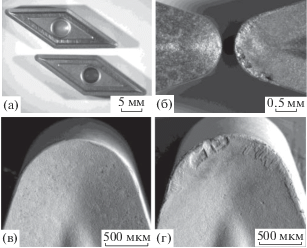
Микроструктура исследованных образцов глобулярно-пластинчатого типа, представлена на рис. 2а. На рис. 2б представлены усталостные образцы и их рабочая поверхность, очевидно, что износ инструмента повлиял на топографию поверхности. На точеной поверхности можно видеть регулярные пики и углубления, которые при небольшом увеличении схожи у обоих образцов, рис. 2б, 2г. Период расстояния между протяженными линиями на снимках образцов приблизительно одинаковый и характеризует подачу инструмента. Поперечные риски более выражены на образце точеном новой пластиной, чем после пластины с износом, рис. 2в, 2д. После точения новой пластиной продольная шероховатость Ra составила 0.46 мкм, а после пластины с износом 0.56 мкм, что свидетельствует, что шероховатость увеличилась с износом инструмента. Perez J.I. и др. [12] исследовали влияние износа инструмента на шероховатость и обнаружили, что при увеличении скорости резания шероховатость поверхности сначала растет, а затем снижается с износом инструмента при использовании твердосплавных фрез. Che-Haron и Jawaid [13] наблюдали похожее поведение, что с износом инструмента поверхность становиться более гладкой при точении образцов сплава Ti–6Al–4V.
Рис. 2.
Точеные усталостные образцы (a) и поверхность после точения: б, в – новой токарной пластиной; г, д – токарной пластиной с износом.
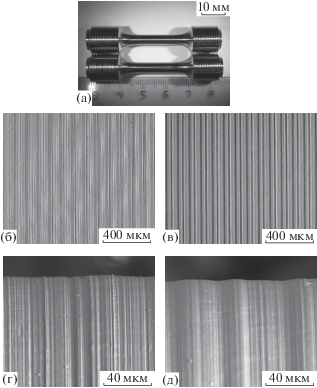
На поверхности точеных усталостных образцов наблюдается повышенная плотность дислокаций, с максимумом на поверхности и снижающаяся вглубь металла, рис. 3а. Плотность дислокаций на поверхности исследованных образцов существенно не отличается, однако, как можно видеть глубина наклепанного слоя на образце возрастает с 30 мкм после точения новой пластиной до 40 мкм на образце, изготовленном токарной пластиной с износом.
Рис. 3.
Распределение плотности дислокаций (а) и остаточных напряжений (б) на поверхности точеных усталостных образцов.
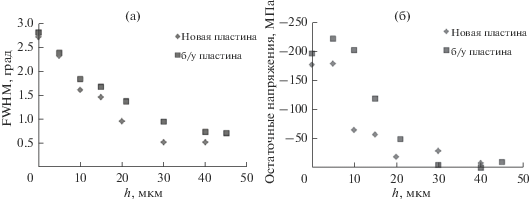
При точении усталостных образцов на их поверхности формируются остаточные сжимающие напряжения, уровень напряжений зависит от режима резания и износа инструмента. Для корректной оценки усталостной прочности уровень остаточных напряжений на поверхности усталостных образцов перед испытанием регламентируется в соответствии с требованиями стандартов, предъявляемых заказчиками к материалу. В связи с этим необходимо оценивать распределение остаточных напряжений и профиль плотности дислокаций, формирующихся в поверхностном наклепанном слое для установления толщины снимаемого слоя при финишной полировке. В настоящее время для этих целей широко используется метод рентгеновской дифракции. Однако необходимо правильно интерпретировать полученные результаты и учитывать влияние различных факторов для корректной оценки напряжений [14].
Распределение остаточных напряжений на исследованных образцах представлено на рис. 3б. В поверхностном слое исследованных образцов остаточные напряжения сжимающие. Средний уровень остаточных сжимающих напряжений существенно выше после точения пластиной с износом и имеет значение в пике –220 МПа на расстоянии 5 мкм от поверхности. На глубине порядка 30 мкм остаточные напряжения снижаются до уровня основного металла на обоих образцах. Данная глубина совпадает с глубиной наклепанного слоя на образце, изготовленном новой пластиной и несколько ниже глубины наклепанного слоя после точения пластиной с износом.
Как было установлено в работе [2] средняя продолжительность усталостной жизни меньше у образцов с элетрополированной поверхностью, чем у образцов после механической полировки и наличием сжимающих напряжений. Наблюдаемое отличие максимально в области малоцикловой усталости. Однако, в одном из ранних исследований, проведенных L. Wagner и др. [15] было получены результаты свидетельствующие, что усталостная прочность образцов с наклепанным слоем и остаточными сжимающими напряжениями значительно больше, чем у электрополированных образцов, прежде всего, в области многоцикловой усталости, что является предметом для научной дискуссии в данной области. Так или иначе, полученные в настоящей работе результаты позволяют обоснованно подойти к выбору технологии изготовления усталостных образцов с требуемым качеством поверхности (целевым уровнем остаточных напряжений и шероховатости поверхности), что обеспечивает получение корректных данных при усталостных испытаниях.
ЗАКЛЮЧЕНИЕ
Проведено исследование качества поверхности усталостных образцов из сплава Ti–6Al–4V после механической обработки точением методом рентгеноструктурного анализа. После обточки новой токарной пластиной и с износом на поверхности образцов обнаружен наклепанный слой с различным распределением плотности дислокаций и остаточных напряжений. Наблюдается увеличение величины остаточных сжимающих напряжений вблизи поверхности при использовании токарной пластины с износом в сравнении с новой пластиной, соответственно ‒220 и –190 МПа. Установлено, что поверхностный пластически деформированный слой на образце после точения новым инструментом составляет 30 мкм и увеличивается до 40 мкм при использовании изношенного инструмента. В связи с этим установление взаимосвязи износа инструмента при механической обработке с целостностью поверхности является необходимым для правильной оценки глубины снимаемого слоя при финишном механическом полировании усталостных образцов.
Для рассмотренной в работе технологической схемы изготовления усталостных образцов, рекомендованный режим полировки после точения включает съем металла 40 мкм с поверхности образца.
Список литературы
Колачев Б.А., Полькин И.С., Талалаев В.Д. Титановые сплавы разных стран. М.: ВИЛС, 2000. 316 с.
Golden P.J., Reji J., Porter W.J. // Procedia Eng. 2010. V. 2. P. 1839.
Jha S.K., Szczepanski C.J., Golden P.J. et al. // Int. J. Fatigue. 2012. V. 42. P. 248.
Machado A.R., Wallbank J.J. // J. Eng. Manuf. 1990. № 204. P. 53.
Nabhani F. // Rob. Comput. Integr. Manuf. 2001. V. 17. P. 99.
Astakhov V. P. // Int. J. Mach. Tools Manuf. 2004. V. 44. P. 637.
Klocke F., Soo S., Karpuschewski B. et al. // CIRP Ann. 2015. V. 64. P. 581.
Wang B., Liu Z. // Int. J. Adv. Manuf. Technol. 2018. V. 98. P. 1925.
Cullity B.D., Stuart R. Elements of X-Ray Diffraction. New Jersey: Prentice Hall. 2001. 664 p.
TOPAS V4.2, General Profile and Structure Analysis Software for Powder Diffraction Data – User’s Manual. Karlsruhe, Germany: Bruker AXS. 2008. 68 p.
Ezugwu E.O., Da Silva R.B., Sales W.F. et al. // Encyclopedia of Sustainable Technologies. 2017. V. 2. P. 487.
Perez J.I., Llorente J.I., Sanchez J.A. et al. // J. Mater. Process. Technol. 2000. V. 100. P. 1.
Che-Haron C.H., Jawaid A.J. // J. Mater. Process. Technol. 2005. V. 166. P. 188.
Moussaoui K., Segonds S., Rubio W. et al. // Mat. Sci. Eng. A. 2016. V. 667. P. 340.
Wagner L., Luetjering G., Gerdes C. // Proceedings of Titanium: Science and Technology. 1985. P. 2147.
Дополнительные материалы отсутствуют.
Инструменты
Поверхность. Рентгеновские, синхротронные и нейтронные исследования