Поверхность. Рентгеновские, синхротронные и нейтронные исследования, 2020, № 10, стр. 46-54
Оценка однородности механических свойств покрытия AlCrN триботехнического назначения с применением зондовых методов
Т. А. Кузнецова a, *, В. А. Лапицкая a, С. А. Чижик a, Б. Вархолинский b, А. Гилевич b, С. М. Айзикович c, Б. И. Митрин c, Л. И. Кренев c
a Институт тепло- и массообмена имени А.В. Лыкова НАН Беларуси
220072 Минск, Республика Беларусь
b Кошалинский Технологический университет
75-453 Кошалин, Польша
c Донской государственный технический университет
1344000 Ростов-на-Дону, Россия
* E-mail: kuzn06@mail.ru
Поступила в редакцию 12.01.2020
После доработки 22.02.2020
Принята к публикации 25.02.2020
Аннотация
Представлены результаты исследования микроструктуры, фазового состава и механических свойств покрытия Al–Cr–N, полученного методом катодного дугового испарения катода из сплава марки Al70Cr30. Методом наноиндентирования определены значения модуля упругости (Е) и микротвердости (Н) покрытия. Методом атомно-силовой микроскопии получены контрасты адгезионных сил в покрытии Al–Cr–N, установлены коэффициенты трения и удельный объемный износ.
ВВЕДЕНИЕ
Требования промышленности, связанные с увеличением эффективности и скорости обработки, делают проблему долговечности и надежности режущих инструментов чрезвычайно важной. Покрытия из нитридов переходных металлов, применяемые для этих целей, обладают хорошими механическими свойствами, высокой твердостью и модулем упругости, хорошей адгезией, высокой износо- и коррозионной стойкостью [1–4]. В настоящее время предпочтение отдается составам, которые могут сочетать несколько свойств. Последние десятилетия покрытия триботехнического назначения, как правило, являются многокомпонентными системами [5, 6]. Добавление нового элемента или модификатора позволяет существенно изменить поверхностные свойства традиционного состава и расширить область его применения [7, 8].
Покрытия из CrN широко используются в металлообработке благодаря хорошим трибологическим свойствам и коррозионной стойкости [9, 10], но их твердость и стойкость к окислению не всегда достаточны для удовлетворения требований современной механической обработки. Добавление металлических или неметаллических элементов (Ti, Si, Al, C, B) к CrN позволяет улучшить характеристики покрытий. Одной из наиболее перспективных тройных систем является Al–Cr–N благодаря своей превосходной стойкости к окислению и высоким механическим свойствам [11]. Al–Cr–N обладает лучшей износостойкостью благодаря образованию оксидных слоев на изношенных поверхностях в процессе работы. Добавление алюминия к CrN повышает его износостойкость при высоких температурах. Покрытия Al–Cr–N по сравнению с CrN, TiN и TiAlN характеризуются стойкостью к окислению до 850–900°С и почти постоянной твердостью до 800°С.
Свойства Al–Cr–N покрытия зависят от концентрации в нем алюминия. При содержании Al ниже 75% в Al–Cr–N образуется кубическая фаза c-AlN [12]. Увеличение концентрации алюминия способствует образованию гексагональной фазы h-AlN и снижению твердости покрытий [12]. Гексагональная фаза h-AlN является более стабильной, чем кубическая. Превращение кубической c-AlN фазы в гексагональную h-AlN фазу под действием механической нагрузки и температуры происходит самопроизвольно. Покрытия Al–Cr–N могут быть получены магнетронным распылением и испарением катодной дуги. В зависимости от применяемого метода нанесения и технологических параметров, различного фазового состава и микроструктуры их механические свойства могут существенно отличаться. Отсюда механические и трибологические свойства фаз AlN при разработке покрытий A–Cr–N представляют интерес.
У покрытий Al–Cr–N, полученных распылением сплава Al70Cr30, ожидаются более низкие механические свойства по сравнению с покрытиями из сплава Al80Cr20 из-за возможного присутствия кубической с-AlN фазы. Кроме того, обилие микрочастиц в покрытии может также влиять на снижение его механических свойств. Неоднородность фазового состава, большое количество микрочастиц делает актуальной задачу исследования однородности механических свойств покрытия и оценки износа на участках матрицы и капельной фазы.
Целью работы является экспериментальное исследование методами наноиндентирования (НИ) и атомно-силовой спектроскопии (АСМ) локальных механических свойств покрытия Al–Cr–N, полученного катодно-дуговым распылением мишени из сплава Al70Cr30 на стальную подложку, после механической полировки поверхности покрытия, после испытаний на трение и на поперечном шлифе покрытия.
МЕТОДИКА ЭКСПЕРИМЕНТА
Покрытия Al–Cr–N наносили катодно-дуговым испарением на подложки из стали марки HS6-5-2 (аналог стали марки Р6М5) с использованием установки TINA-900 М [13]. Применяли катоды из сплава AlCr (70 : 30) с чистотой 99.99% и диаметром 100 мм. Подложки диаметром 32 мм и толщиной 3 мм шлифовали и полировали до параметра шероховатости Ra = 0.02 мкм, а затем промывали в щелочной среде в ультразвуковой ванне, ополаскивали в деионизированной воде и высушивали теплым воздухом. Подложки устанавливали на вращающемся держателе, параллельном поверхности испаряемого катода, в рабочей камере на расстоянии 18 см от источников. Камеру вакуумировали до базового давления 1 мПа, подложки нагревали до температуры около 350°С. Процессу нанесения покрытия предшествовало травление поверхности подложек ионами аргона и хрома при U = 600 В, PAr = 0.5 Па в течение 10 минут при токе хромовой дуги 80 А. Тонкий слой хрома толщиной около 100 нм улучшал адгезию покрытия к подложке. Покрытия Al–Cr–N наносили при напряжении смещения подложки – 50 В, токе дуги 80 А, давлении азота 2 Па. Толщина покрытий составляла около 3 мкм.
Фазовый состав покрытий определяли рентгенофазовым анализом (РФА) на дифрактометре модели X’Pert PANalytical с использованием CuKα-излучения при напряжении 40 кВ, токе 35 мА, скорости сканирования 20 c/шаг, шаге 0.05 в диапазоне углов дифракции от 20° до 90°.
Измерения микротвердости Н и модуля упругости Е проводились на наноинденторе Hysitron 750 Ubi (США) с предварительным сканированием поверхности путем внедрения алмазного индентора Берковича с радиусом закругления 200 нм с непрерывной регистрацией деформационных кривых зависимости глубины внедрения от приложенной нагрузки. Калибровку радиуса острия выполняли внедрением в калибровочный образец плавленого кварца. Определение величин Н и Е выполняли как с поверхности образца с удаленной микрокапельной фазой, так и на шлифе поперечного сечения покрытий. Выполняли по 35 кривых с поверхности образца и по 10 на поперечном шлифе. Кроме исходной полированной поверхности покрытия измерение Е и Н проводили на участках дорожки трения, полученной при нагрузке 20 Н на контртело из Al2O3 диаметром 10 мм при скорости 0.2 м/c и длине пути 2000 м. Контроль шероховатости поверхности осуществляли с использованием профилографа Hommel Tester T8000.
Исследования морфологии и неоднородности распределения фаз на поверхности полированного образца проводили с использованием сканирующего электронного микроскопа (СЭМ) Mira (Tescan, Чехия) с микрорентгеноспектральным анализатором “INCA Energy 350” фирмы “Oxford Instruments Analytical” (Великобритания) и на атомно-силовом микроскопе Dimension FastScan (Bruker, США). Атомно-силовой микроскоп применяли в режиме PeakForce Tapping QNM с использованием стандартных кремниевых кантилеверов типа MPP-12 120-10 (производство Bruker, США) и распределение различных фаз выявляли за счет контраста адгезионных сил.
Износ покрытия и коэффициент трения на участках различных фаз определяли в режиме Contact Mode с использованием кантилеверов с алмазным острием на кремниевой консоли типа D300 (производство SCDprobes, Эстония) с радиусом закругления острия 40 нм, с жесткостью консоли 73.67 Н/м. Испытания выполняли при нормальной нагрузке 8, 18 и 22 мкН в течение 40 циклов при скорости 8.1 мкм/с (4 Гц). Удельный объемный износ ${{k}_{{v}}}$ определяли, как отношение объема материала V, удаленного во время испытания на трение АСМ, к величине нормальной нагрузки L и расстоянию скольжения s [14]:
Объем износа оценивали по площади профиля сечения дорожки износа S и периметру дорожки износа.РЕЗУЛЬТАТЫ И ИХ ОБСУЖДЕНИЕ
Поверхность покрытия Al–Cr–N практически полностью покрыта микрочастицами (в некоторых работах микрокаплями) (рис. 1). Как видно на изображении, полученном в СЭМ, на поверхности покрытия Al–Cr–N в исходном состоянии, микрочастицы различной формы и контраста, плоские и округлые, при среднем размере 3 мкм и диапазоне размеров 0.5–10 мкм покрывают поверхность сплошным узором и даже сложно найти участок диаметром 0.5–1 мкм без микрочастиц. Это типичные дефекты, связанные с технологией нанесения покрытий – катодно-дуговым испарением [15]. Микрокапли катодного материала обычно диаметром несколько микрометров испускаются из катодных пятен. Столкновения между атомами или ионами в результате высокого давления способствуют образованию агломератов еще до осаждения на подложку [16]. Чем ниже температура катода, тем больше линейные размеры и тем больше количество осажденных частиц. В случае катодов из Al и Cr максимальные размеры осажденных частиц составляют 10–20 мкм и 1 мкм соответственно. Согласно рентгенофазовому анализу (рис. 2), в покрытии приблизительно в равных количествах содержатся следующие фазы: гексагональная AlN (h-AlN), Cr, CrN и Cr2N. В несколько меньших количествах, чем h-AlN присутствует кубическая фаза AlN (c-AlN). Практически все пики на дифрактограмме находятся в характерных для них угловых положениях. Постоянные решеток выявленных фаз совпадают со своими табличными значениями, что позволяет заключить, что в покрытии нет существенных механических напряжений.
Из-за микрочастиц исходная поверхность покрытий Al–Cr–N, полученных катодно-дуговым испарением, характеризуется относительно большим параметром шероховатости Ra, равным примерно 0.3 мкм. После механического полирования шероховатость поверхности покрытия значительно уменьшается (примерно до 0.05 мкм) и локальные механические характеристики можно определить с гораздо меньшей погрешностью измерения. При выполнении шлифов более твердые фазы получаются выступающими над остальной поверхностью, а более мягкие – углубленными [17]. У покрытий Al–Cr–N основная фаза – матрица – более твердая, а отдельные углубления могут быть образованы скоплением дефектов, микрочастицами чистого металла, границами микрочастиц (рис. 3). Полированная поверхность покрытия представляет собой карту локальных участков с пониженными механическими свойствами. По количеству и расположению углублений в полированном покрытии Al–Cr–N можно предположить, что это контуры бывших микрочастиц, по количеству – что это фазы, содержащие Cr и CrN. В среднем, после полирования поверхности покрытия одно углубление приходится на площадь диаметром 5 мкм. Таким образом, полировка поверхности покрытия помогает визуально разделить исходное многообразие фаз микрочастиц покрытия на двухфазную систему: основную более твердую матрицу и более мягкую фазу в углублениях. При подробном рассмотрении материала в углублениях выявляется его однородная структура, состоящая из плоских зерен диаметром менее 100 нм, что может быть тонким слоем материала, снятого в результате полировки тонкими слоями, многократно деформируемого и перемещенного в углубления.
Рис. 3.
АСМ-топография поверхности покрытия Al–Cr–N после полировки: a – 20 × 20 мкм, б – 7 × 7 мкм.
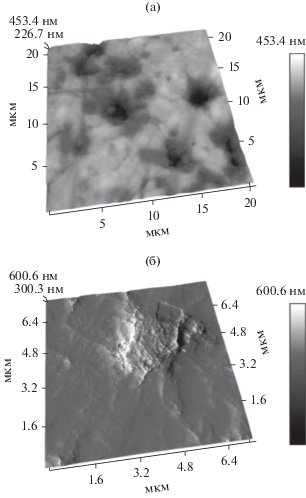
Согласно СЭМ- и АСМ-изображениям, полированное покрытие Al–Cr–N представляет собой достаточно гладкую поверхность, на которой равномерно распределены округлые углубления диаметром от 1 до 3 мкм. На СЭМ-изображениях они более темного контраста (рис. 4а). Использование режима обратно отраженных электронов (BSE) позволяет выявить светлые округлые частицы, нередко закрытые в углублениях под тонким слоем перенесенного материала на изображении в режиме вторичных электронов и темные углубления (рис. 4в). Микрорентгеноспектральный анализ (МРСА) данных элементов структуры показывает, что округлые светлые частицы не содержат азота, а только металлы Cr и Al приблизительно пополам. Темные углубления являются нитридными фазами, обогащенными хромом по сравнению с остальной матрицей. Используя режим обратно отраженных электронов, можно наблюдать распределенные по поверхности округлые светлые частицы, состоящие, согласно МРСА, из Cr и Al и темные фазы, обогащенные Cr нитридные фазы (рис. 4в). По СЭМ изображению излома покрытия (рис. 4б) видно, что темные фазы проходят вглубь покрытия. Таким образом, микрочастицы локализуются не только на поверхности покрытия, а по всей его толщине.
Рис. 4.
СЭМ-изображения изломов (а. б) и поверхности полированного образца (в) покрытия Al–Cr–N: a – ×3000; б – ×25 000; б – ×20 000, режим BSE.
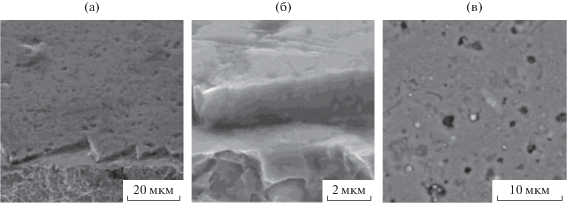
Для определения значений Е и Н покрытия индентирование проводили на двух различных участках покрытия по 35 кривых на каждом участке. Один из массивов кривых показан на рис. 5а. Среднее значение E составило 234 ± 13 ГПа, Н – 24.2 ± 1.7 ГПа. Для того, чтобы количественно сравнить значения E и H на основной матрице и углубленных фазах, индентирование осуществляли отдельно по основной матричной фазе и по углубленным фазам (рис. 5б, 5в), выполняя по 14 индентирований. Обобщенные кривые наноиндентирования, представленные на рис. 5в позволили разделить фазы на две группы со средними значениями: E = 248 ± 16 ГПа и Н = 26.2 ± 3.3 ГПа для матрицы и E = 232 ± 48 ГПа и Н = 17.6 ± 3.3 ГПа для фаз бывших микрочастиц. Большие значения стандартных отклонений при индентировании по отдельным фазам по сравнению с приведенными выше значениями для всего покрытия, объясняются влиянием рельефа при использовании меньшей нагрузки в 5000 мкН. Матрица и углубленные фазы имеют равные значения Е и близкие значения H. Некоторое снижение значений Н объясняется присутствием в углублениях более мягкого тонкого слоя, образовавшегося при полировке. Более низкие значения Е и Н для некоторых площадок бывших микрочастиц объясняются тем, что в их состав входят металлы Cr и Al более мягкие, чем нитридные фазы. В контрасте адгезионных сил режима PeakForce Tapping QNM для основной фазы cилы адгезии составляли 18.2 нН, а для фаз бывших микрочастиц – 33.3 нН. Повышенное значение сил адгезии часто характерно для более мягких фаз.
Рис. 5.
Результаты наноиндентирования: вид всего массива кривых, (а) вид поверхности покрытия Al–Cr–N 10 × 10 мкм с точками индентирования (б), пример вида кривых наноиндентирования от матрицы (1) и более мягкой фазы углублений (2).
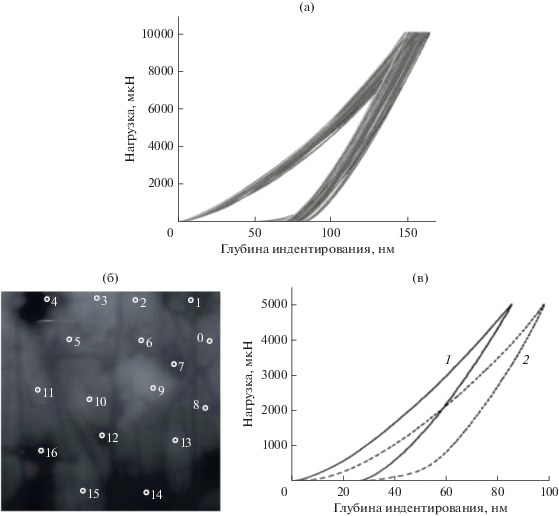
Таким образом, несмотря на многообразие фазового состава, покрытие Al–Cr–N является однородным по механическим свойствам, так как выявленные ранее полировкой области пониженных механических свойств показали различие по Е с остальным покрытием в пределах ошибки метода наноиндентирования, а снижение в этих областях Н на 10% объясняется присутствием на их поверхности тонкого мягкого слоя, образовавшегося при полировке (рис. 6).
Рис. 6.
Схема сечения покрытия с подложкой с матрицей, мягкой фазой и тонким слоем мягкого материала, образовавшегося при полировке.
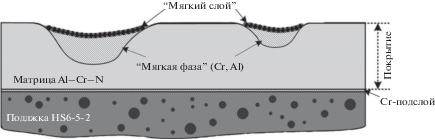
Измерение Е и Н проводили в двух участках дорожки трения, отмеченных стрелками на рис. 7 и отличающихся цветом: более светлом, имеющем металлический блеск на оптическом изображении, и представляющем очищенную поверхность, и темном, представляющем собой окисный слой из деформированных микрочастиц. Для светлой поверхности в дорожке трения величина E составила 233 ± 10 ГПа, Н – 24.2 ± 1.7 ГПа. Для темного слоя величина E составила 232 ± 13 ГПа, Н – 24.0 ± 2.0 ГПа. Значения на разных участках дорожки трения совпали как между собой, так и со значениями покрытия до испытаний. Контроль Е и Н покрытия Al–Cr –N в дорожке трения, в свою очередь, показывает перспективность данных покрытий для трибологических приложений. В то время как некоторые покрытия при трибоиспытаниях частично разрушаются и отслаиваются от подложки, значительно снижают свои механические характеристики из-за пластического деформирования, исследуемые покрытия после испытаний сохраняют исходный уровень значений Е и Н.
Рис. 7.
Участки на поверхности дорожки трения (указаны стрелками), в которых выполнялось по 35 кривых наноиндентирования (а) и вид поперечного шлифа подложки с покрытием Al–Cr–N 10 × 10 мкм с указанием точек индентирования (б) и карты Е (в).
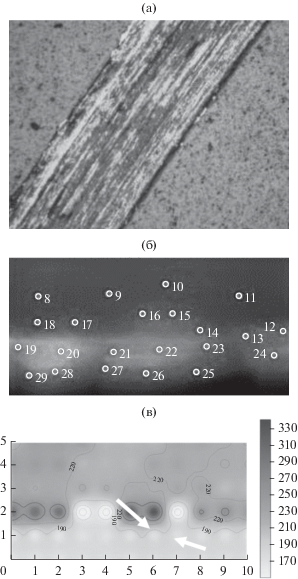
Величины Е и Н, определенные по шлифу поперечного сечения покрытия Al–CrN в точках, указанных на рис. 7б, дают существенный разброс значений, но при этом несколько выше значений, полученных по шлифу поверхности. В целом у подложки при значениях Е = 226 ГПа, Н = 11 ГПа в переходной зоне значения Е и Н немного снижаются до Е = 219 ГПа, Н = 11 ГПа из-за присутствия мягкого тонкого подслоя хрома. Покрытию соответствуют величины Е = 250 ГПа, Н = 16 ГПа, а на поверхности покрытия наблюдается снижение свойств до Е = 150 ГПа, Н = 14 ГПа. Снижение свойств на поверхности при определении их на поперечном шлифе можно объяснить погрешностью препарирования уже полированного с поверхности образца. При всей относительности метода наблюдается снижение свойств в переходной зоне подложка–покрытие по сравнению со свойствами покрытия. Отклонения в значениях в центральной части покрытия объясняется присутствием на поперечном шлифе областей с границами микрочастиц. В целом, значения модуля упругости покрытия при определении на поперечном сечении оказались несколько завышенными, а микротвердость – заниженной по сравнению со значениями, полученными с поверхности, что может быть связано с анизотропией механических свойств в покрытии в перпендикулярных направлениях.
Результаты триботехнических испытаний на АСМ показали существенное различие значений износа и коэффициентов трения для матрицы покрытия и для равномерно распределенных углублений от “мягких фаз” бывших микрочастиц (рис. 8, 9). У матрицы глубина износа при нормальной нагрузке 18 мкH составила 3.5 нм, а у мягких фаз бывших микрочастиц – 92 нм, значение удельного объемного износа как 1.9 × 10–14 м3/H · м в первом случае и 5.0 × 10–13 м3/H · м во втором. Завышенные значения удельного объемного износа для мягкой фазы объясняются наличием в углублениях тонких слоев мягкого материала, образовавшегося при полировке и заполнившего углубления (рис. 6). Значение удельного объемного износа для основной матричной фазы (1.9 × 10–14 м3/H · м) практически совпало со значением, определенным в работе [18] для покрытия Al–Cr–N. Зависимости коэффициента трения от количества циклов износа, определенные для основной фазы (светлые точки) и более мягкой фазы (темные точки) АСМ представлены на рис. 9б. Коэффициенты трения, определенные в процессе износа АСМ, составили 0.14 для основной и 0.45 для мягких фаз (рис. 9б). При этом значение коэффициента трения для твердой фазы совпало со значением коэффициента трения (0.14), определенного в макрорежиме для покрытия Al–Cr–N при нагрузке 0.2 Н и возвратно-поступательном перемещении индентора из WC с той же частотой (4 Гц), что и при испытании АСМ. Значения Ктр для мягкой фазы при определении АСМ, также, как и удельный объемный износ указывают на мягкий материал, который не может быть нитридными фазами. Однако в обычном режиме скольжения и взаимодействия контртела с поверхность покрытия такие углубления, аналогичные образующимся при полировке, и равномерно распределенные по поверхности, будут служить “карманами” для материала пластически измененного слоя – “третьего тела” – улучшающего условия контакта при трении.
Рис. 8.
Вид фрагментов поверхности покрытия Al–Cr–N со следами износа, 3 × 3 мкм: а – основная фаза, б – более мягкая фаза бывших микрочастиц.
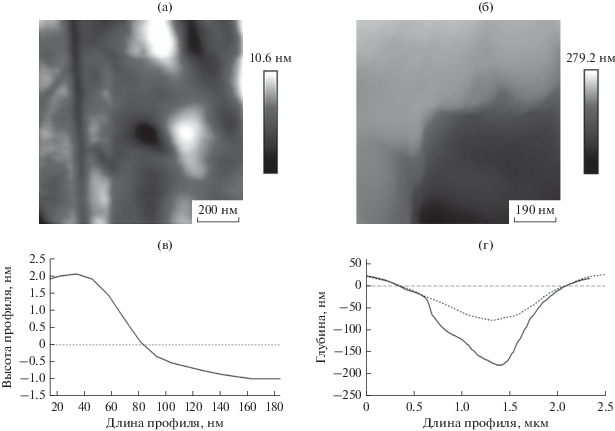
Рис. 9.
Результаты триботехнических испытаний на АСМ: а – зависимости глубины износа и удельного объемного износа от нагрузки для основной фазы AlN; б – зависимости коэффициента трения от количества циклов износа, определенные для основной фазы h-AlN (светлые точки) и более мягкой фазы (темные точки).
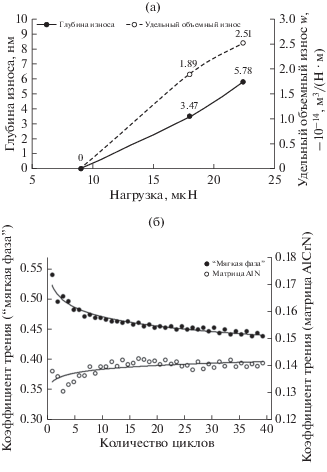
ЗАКЛЮЧЕНИЕ
Представлены результаты исследований микроструктуры, фазового состава, локальных механических и трибологических свойств покрытий Al–Cr–N, полученных катодно-дуговым испарением катода из сплава Al70Cr30. Фазовый состав, согласно РФА, приблизительно в равных количествах представлен фазами h-AlN + c-AlN, Cr, CrN и Cr2N. При этом МРСА выявляет однородное распределение Al, Cr и N по полированной поверхности покрытия за исключением углубленных локальных областей, содержащих Al и Cr, либо нитридные фазы, обогащенные Cr. Установлена близость микротвердости и идентичность модулей упругости основного покрытия и участков с предполагаемыми пониженными механическими свойствами.
Механические свойства покрытия Al–Cr–N оказались достаточно высокие для систем, содержащих кубическую фазу c-AlN: E = 234 ± 13 ГПа, Н = 24.2 ± 1.7 ГПа c низким удельным износом 1.9 × 10–14 м3/H · м.
Была выявлена однородность механических свойств при определении их в направлении поверхности и некоторая неоднородность при определении по поперечному сечению со снижением значений в переходной зоне покрытие–подложка. Однородность свойств покрытия Al–Cr–N с при определении их с поверхности объясняется гомогенным распределением фаз в основной части покрытия, что подтверждается МРСА, и близкими значениями Е и Н в областях пониженных свойств. Неоднородность свойств покрытия Al–Cr–N при определении по поперечному сечению связана со столбчатым строением покрытия, что выявляется микроструктурой излома, приводящим к образованию пор на поперечном сечении и со снижением значений в переходной зоне покрытие–подложка.
Список литературы
Hogmark S., Jacobson S., Larsson M. // Wear. 2000. V. 246. P. 20.
Holmberg K., Matthews A., Ronkainen H. // Tribology International. 1998. V. 31. P. 107.
Andreyev M., Markova L., Kuznetsova T., Anishchik V.M. // Vacuum. 2005. V. 78. № 2–4. P. 451.
Barata A., Cunha L., Moura C. // Thin Solid Films. 2001. V. 398–399. P. 501.
Kuznetsova T.A., Andreev M.A., Markova L.V., Chekan V.A. // J. Frict. Wear. 2001. V. 22(4). P. 423.
Kuznetsova T.A., Lapitskaya V.A., Chizhik S.A. et al. // IOP Conference Series: Materials Science and Engineering. 2018. V. 443. https://doi.org/10.1088/1757-899X/443/1/012017
Warcholinski B., Kuznetsova T.A., Gilewicz A. et al. // J. of Mater. Eng. and Perform. 2018. V. 27. P. 3940. https://doi.org/10.1007/s11665-018-3483-7
Kuznetsova T.A., Lapitskaya V.A., Chizhik S.A. et al. // IOP Conference Series: Materials Science and Engineering. 2018. V. 443. https://doi.org/10.1088/1757-899X/443/1/012018
Lousa A., Romero J., Martínez E., Esteve J., Montala F., Carreras L.// Surf. Coat. Technol. 2001. V. 146–147. P. 268.
Вархолински Б., Гилевич А., Куприн А.C и др. // Трение и износ. 2019. Т. 40. № 2. С. 209. (Warcholinski B., Gilewicz A., Kuprin A. et al. // Journal of Friction and Wear 2019. Т. 40. № 2. P. 163).https://doi.org/10.3103/S1068366619020156
Long Y., Zeng J., Yu D., Wu S. // Ceram. Int. 2014. V. 40. P. 9889.
Wang L., Zhang S., Chen Z., Li J., Li M. // Appl. Surf. Sci. 2012. V. 258. P. 3629.
Ovcharenko V.D., Kuprin A.S., Tolmachova G.N. et al. // Vacuum. 2015. V. 117. P. 27.
Кузнецова Т.А., Андреев М.А., Маркова Л.В. // Трение и износ. 2005. Т. 26. № 5. С. 521.
Warcholinski B., Gilewicz A., Ratajski J., Kuklinski Z., Rochowicz J. // Vacuum. 2012. V. 86. P. 1235.
Wan X.S., Zhao S.S., Yang Y., Gong J., Sun C. // Surf. Coat. Technol. 2010. V. 204. P. 1800.
Чижик С.А., Кузнецова Т.А., Худолей А.Л. и др. // Инженерно-физический журнал. 2013. Т. 86. № 5. С. 949–959. (Chizhik S.A., Kuznetsova T.A., Khudolei A.L. et al. // Journal of Engineering Physics and Thermophysics. 2013. Т. 86. № 5. P. 1008).https://doi.org/10.1007/s10891-013-0922-z
Gilewicz A., Jedrzejewski R., Myslinski P. et al. // J. of Mater. Eng. and Perform. 2019. V. 28. Is. 3. P. 1522. https://doi.org/10.1007/s11665-019-03934-2
Дополнительные материалы отсутствуют.
Инструменты
Поверхность. Рентгеновские, синхротронные и нейтронные исследования