Поверхность. Рентгеновские, синхротронные и нейтронные исследования, 2020, № 11, стр. 17-23
Слоисто-волокнистый композит с матрицей на основе ниобия, армированный монокристаллическими сапфировыми волокнами
В. М. Кийко a, *, В. П. Коржов a, В. Н. Курлов a, К. А. Хвостунков b, **
a Институт физики твердого тела РАН
142432 Московская область, Черноголовка, Россия
b Московский государственный университет им. М.В. Ломоносова
119991 Москва, Россия
* E-mail: kiiko@issp.ac.ru
** E-mail: khvostunkov@gmail.com
Поступила в редакцию 28.01.2020
После доработки 30.03.2020
Принята к публикации 08.04.2020
Аннотация
Твердофазным методом диффузионной сварки получены образцы композитных материалов со слоистой матрицей на основе ниобия, однонаправленно армированные монокристаллическими волокнами сапфира. Волокна сапфира получены методом Степанова (EFG). В результате испытаний впервые получены зависимости прочности таких волокон от длины. Величины прочности отвечают мировому уровню. Проведен рентгеноспектральный микроанализ полученных материалов. Установлено образование твердых растворов и интерметаллидов системы Nb–Al в процессе формирования композитной структуры. Проведены испытания на прочность (500–700 МПа) и определена эффективная поверхностная энергия разрушения композитов ((9–49) × 103 Дж/м2), установлена их корреляция с режимами изготовления. Изучены особенности структуры разрушения таких материалов и процессы, тормозящие ее разрушение под нагрузкой.
ВВЕДЕНИЕ
Разработка высокотемпературных конструкционных материалов является одной из основных проблем современного материаловедения. Повышение рабочих температур элементов конструкций ведет к расширению диапазона их применения, в особенности в летательных аппаратах в атмосфере и космосе, повышению их эксплуатационных характеристик, увеличению коэффициента полезного действия разного рода тепловых машин, что приводит к более эффективному использованию топлива и уменьшению экологических нагрузок. Особенно остро эта проблема стоит при разработке материалов для элементов конструкций газотурбинных двигателей. Возможности традиционных сплавов сегодня практически исчерпаны, что определяется или ограниченностью потолка рабочих температур в связи с близостью температур плавления сплавов, например, на основе никеля, приводящей к низкому сопротивлению ползучести [1, 2], или низкой трещиностойкостью сильно легированных сплавов, например, на основе ниобия [3], или сложностями получения и использования тугоплавких конструкционных материалов на основе, например, молибдена из-за высокой плотности [4], а также проблем, связанных с газовой коррозией [5]. Последние два фактора особенно важны при применении материалов для роторных лопаток газотурбинных двигателей. Продвижение разработок конструкционных материалов в область все более высоких температур требует использования новых, обычно ранее не применяемых соединений и организации новых структур. Примером такой новой структуры является представленная в работе слоисто-волокнистая структура композита с матрицей на основе ниобия и его интерметаллидов cистемы Nb–Al, армированной монокристаллическими волокнами сапфира, полученными методом Степанова. Результаты, представленные в этой работе, открывают новое направление разработок и исследований композитных материалов такого рода, соединяющих в иерархически организованной структуре высокопрочные оксидные волокна и трещиностойкую, потенциально крипостойкую слоистую композитную матрицу, содержащую высокотемпературные сплавы, твердые растворы и интерметаллидные соединения. Представленный композитный материала на основе ниобия является частью результатов проводящихся авторами работ по разработке и исследованию высокотемпературных слоистых и слоисто-волокнистых композитов [6–12]. Твердофазный метод позволяет не только сохранить достоинства исходных компонентов (высокопрочных армирующих оксидных волокон и композитных матриц), но и образовать новые фазы в виде интерметаллидов и твердых растворов. Интерметаллиды повышают прочность и модуль упругости композита, а твердые растворы совместно с границами раздела между компонентами – трещиностойкость [13, 14]. При этом оптимально организованные неоднородные композитные структуры за счет синергетического эффекта позволяет достигнуть еще более высоких характеристик в сравнении с оцененными по “правилу смесей” [15]. Кроме того, наличие относительно легких оксидных волокон и интерметаллидных слоев в этих структурах снижают общую плотность материалов (что существенно для многих применений) в сравнении с базовыми металлами, на основе которых они изготовлены. Это снижение дополнительно повышает удельные механические характеристики композитов в целом [16]. Представляемые результаты можно считать начальными с дальнейшей перспективой получения слоисто-волокнистых композитов на базе ниобиевых сплавов различного состава с рабочими температурами не менее 1350°C, более чем на 200°C превышающих соответствующую температуру используемых в настоящее время монокристаллов никелевых сплавов [17, 18].
Целью настоящей работы является разработка структуры слоисто-волокнистого композита, получение и испытания монокристаллических волокон сапфира, выбор исходных компонентов композита, определение базовых режимов их изготовления, исследование структуры и испытания композитов и установление корреляции механических характеристик с режимами изготовления.
ПОЛУЧЕНИЕ И СТРУКТУРА КОМПОЗИТОВ
Композиты изготавливались твердофазным методом диффузионной сварки исходных компонентов под нагрузкой. Монокристаллические волокна сапфира выращивались методом Степанова из расплава оксида алюминия [19], а фольги алюминия, ниобиевого сплава Nb–0.1C и порошок ниобия использовались в готовом виде промышленного изготовления. Температуры, при которых использовался метод, позволяют сохранить, (в основном) структуру и механические свойства исходных материалов. А соответствующий подбор этих материалов при определенных температурах предоставляет возможность получить и новые соединения, в частности, интерметаллиды, повышающие механические свойства композита [6, 9, 20]. Кроме того, твердые растворы, образующиеся в процессах диффузии, обладают определенной пластичностью, тормозящей развитие трещин. При технологических процедурах формируются также границы разделов между компонентами композитной структуры, представляющие особый вид неоднородности, играющей важную роль в процессах диссипации энергии при нагружении материала, определяющей сопротивление разрушению [21].
Многослойная структура заготовки представляла собой плоский пакет, набранный из повторяющихся отдельных элементов. Элемент собирался последовательной укладкой исходных компонентов следующим образом. На плоскую поверхность помещали лист фольги из ниобиевого сплава (основы материала матрицы). Затем – лист фольги из алюминия, относительно низкая температура плавления, которого при нагреве приводит к его пластической деформации и первоначального связывания компонентов структуры, имеющих более высокую температуру плавления. Основная же задача этой пары фольг состояла в образовании твердого раствора алюминия в ниобии и интерметаллидов системы Nb–Al, существенно определяющих свойства матрицы (трещиностойкость, модуль упругости, сопротивление ползучести). Далее на алюминиевую фольгу однонаправленно с заданным шагом укладывались волокна Al2O3, в значительной мере определяющие прочность, жесткость, сопротивление ползучести композита. Промежутки между волокнами заполнялись суспензией порошка технически чистого ниобия в полиэтиленгликоле. Затем сверху снова укладывался лист фольги из алюминия, завершающий сборку единичного элемента. Необходимое количество элементов собиралось в полную заготовку многослойного композитного материала. Далее собранный пакет помещался в вакуумную камеру (вакуум не ниже 10–4 мм рт. ст.) установки для горячего прессования, и осуществлялась диффузионная сварка в режиме первого этапа. Подобные процедуры и высокотемпературная вакуумная технологическая установка подробно описаны в работах [16, 22]. С целью приближения к общему оптимальному технологическому режиму получения композитного материала диффузионная сварка проводилась в три этапа. Причем по техническим причинам второй и третий этап выполнялись в другой технологической установке в атмосфере аргона. После каждого этапа от полученной плитки из композитного материала отрезались образцы вдоль волокон примерно квадратного поперечного сечения, проводились механические испытания (на этой начальной стадии работы испытания проводились при комнатной температуре), и исследовалась их структура, далее по результатам определялись дальнейшие шаги. Оставшаяся часть композитного материала от предыдущего этапа могла быть подвергнута диффузионной сварке в режиме следующего этапа. Режимы изготовления композита характеризуются тремя основными параметрами: температурой, временем, удельной нагрузкой на исходную заготовку. На первом этапе температура составляла 1400°C, время – 0.5 ч, удельная нагрузка –12 МПа, на втором – дополнительно к первому – 1750°С – 2 ч – 0.16 МПа, на третьем – дополнительно ко второму – 1950°С – 2 ч – 0.28 МПа. Примером результата такой технологической процедуры может служить поперечное сечение композита, полученного после первого этапа, показанное на рис. 1а.
Рис. 1.
Структура поперечного сечения композита: крупные круглые объекты черного цвета – волокна сапфира, серого – ниобий и его соединения с углеродом и алюминием, а также твердый раствор алюминия в ниобии (а); участок поперечного сечения композита с волокном и примыкающими областями матрицы различного состава, обозначенными I, II, III, IV (б). Оси координат – линии, вдоль которых был проведен рентгеноспектральный микроанализ, результаты которого показаны на рис. 2.
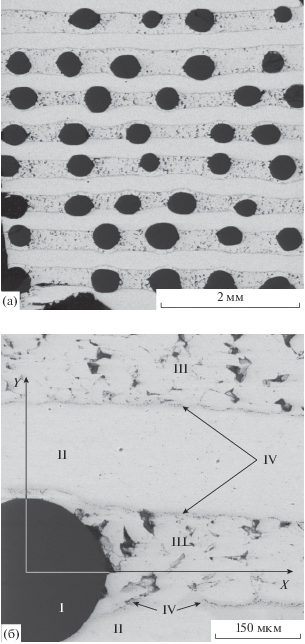
На поперечном сечении (шлифе) композитного материла (рис. 1б) можно выделить сапфировое волокно черного цвета (I) с четкими границами между волокном и матрицей, а также области матрицы серого цвета различных оттенков, представляющих разный состав, не имеющими столь резко выраженных границ между собою (II, III, IV). Результаты проведенного рентгеноспектрального микроанализа в областях с характерными размерами около 5–7 мкм вдоль осей X и Y (рис. 1б и рис. 2) позволяют полуколичественно определить состав композитного материала. Область I – волокно сапфира Al2O3. Область II – наследие фольги из исходного сплава Nb–0.1C, представляющего вблизи горизонтальных границ (рис. 1) с областями–прослойками IV твердые растворы алюминия в ниобии. Анализ по углероду по техническим причинам не проводился. Области IV являются слоями, занимающими положение между областями I и II или II и III, которые образовались на месте прокладок из исходных алюминиевых фольг. Они представляют собой твердые растворы алюминия в ниобии и интерметаллидные соединения, идентифицированные по диаграмме состояния системы Nb–Al как Nb2Al и Nb3Al. Мелкие черные “точки” областей IV (рис. 1б), микроанализ которых из-за их размера, меньшего размера электронного зонда, не проводился, вероятно, состоят из Al2O3, образовавшегося на поверхности исходной алюминиевой фольги. Слой III изначально представлял порошок технически чистого ниобия, а незначительное количество алюминия, обнаруженное в некоторых участках этого слоя, по-видимому, является материалом, содержащим соединения алюминия, занесенного в поры при шлифовании.
Рис. 2.
Концентрационные зависимости ниобия и алюминия по данным рентгеноспектрального микроанализа в отдельных областях вдоль осей X (а) и Y (б), показанных на рис. 1б. Области различных составов композита, обозначенные I, II, III, IV, разделены вертикальными пунктирными линиями.
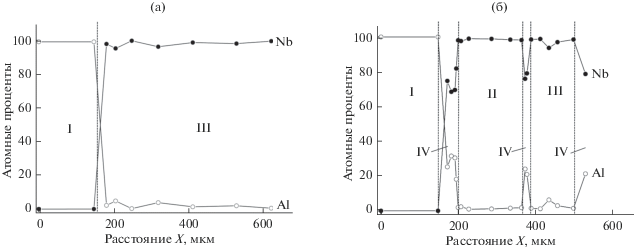
Таким образом, в результате горячего прессования из исходных компонентов сформировалась структура волокнистого композитного материала, обладающего достаточной сплошностью. При этом в матрице образовались интерметаллиды и твердые растворы.
Структура и состав композитов и их компонентов изучалась с применением растровых электронных микроскопов Tescan VEGA-II XMU и CamScan MV230 (VEGA TS 5130MM). Микроскопы были оснащены детекторами вторичных и отраженных электронов и энергодисперсионными рентгеновскими микроанализаторами.
МЕХАНИЧЕСКИЕ ИСПЫТАНИЯ И ХАРАКТЕРИСТИКИ РАЗРУШЕНИЯ КОМПОЗИТА
Важнейшей компонентой композитного материала являются монокристаллические волокна сапфира. Волокна были испытаны на прочность по методике [23], позволяющей определить зависимость прочности волокон от длины. Методика вкратце состоит в том, что волокно наматывается последовательно на серию жестких цилиндров уменьшающихся диаметров, на каждом диаметре подсчитывается деформация в волокне и средняя длина между изломами. В результате получается зависимость деформации разрушения волокна от длины. Поскольку материал волокна является достаточно хрупким и имеет практически линейную деформационную зависимость вплоть до разрушения, то прочность волокна может быть определена умножением величины предельной деформации на модуль Юнга материала волокна, для сапфира модуль известен и принимается равным 400 ГПа. На рис. 3 представлены результаты испытаний партии волокон. На рис. 3а показаны зависимости деформаций и прочности при разрушении волокон от длины в логарифмических координатах. Практически линейные зависимости свидетельствуют о степенной зависимости прочности (деформации при разрушении) от длины. Убывающая зависимость прочности волокон характеризует распределение дефектов разного вида по длине и является типичной для хрупких материалов такого рода, в частности, для волокон, изготовленных другими методами [23]. Полученные результаты важны не только для характеризации собственно волокон, но могут быть использованы в качестве исходных данных при построении моделей разрушения композита. Поверхность разрушения одного из волокон, показанная на рис. 3б, имеет развитую топологию со сколами по относительно слабым плоскостям, что увеличивает эффективную поверхность разрушения, способную внести свой вклад в общее сопротивление разрушению композита.
Рис. 3.
Результаты испытаний группы сапфировых волокон: a – зависимости деформации разрушения и прочности волокон от длины (каждое волокно отмечено своим значком на графике), б – поверхность разрушения волокна после испытаний.
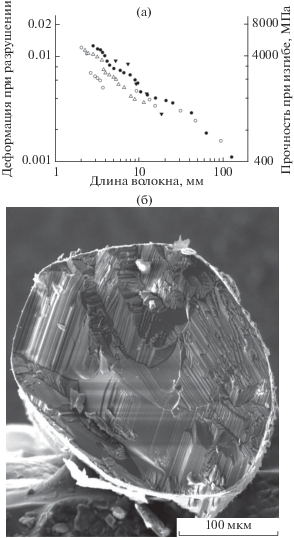
Учитывая исследовательский характер работы и сложность изготовления композитных образцов на растяжение, в основном для сравнительной оценки механических свойств испытания проводились в условиях трехточечного изгиба. В процессе испытаний велась запись нагрузка–прогиб образца, позволяющая качественно судить о деформационных характеристиках композита. Значения прочности определялись по известным соотношениям сопротивления материалов [24]. На рис. 4 показаны типичные примеры результатов таких испытаний с приложением нагрузки перпендикулярно плоскостям структуры, как показано на рис. 5. Сравнение кривых деформирования, представленных на рис. 4а, 4б, указывает на то, что композитный образец материала, изготовленного в режиме первого этапа (рис. 5а), под нагрузкой более пластичен (квазипластичен), чем материал, изготовленный в режиме третьего этапа (рис. 4б). В то же время прочность последнего существенно выше при очевидно более хрупком поведении. Очевидно также, что эти отличия связаны с различием в структуре, определяемой режимами термообработки. Форма кривых деформирования образцов материала, изготовленного в режиме второго промежуточного этапа, занимает промежуточное положение в сравнении с приведенными кривыми. Прочность же типичного образца, изготовленного в режиме второго этапа, составляет 570 МПа. Величины эффективной поверхностной энергии разрушения образцов $g$ определялись по формуле g = = $({1 \mathord{\left/ {\vphantom {1 {2S}}} \right. \kern-0em} {2S}})\int_x {P(x)dx} ,$ где $P$ – нагрузка на образец, $x$ – перемещение точки приложения нагрузки к образцу (прогиб образца), $S$ – площадь поперечного сечения образца [25]. Для образца, кривая деформирования которого показана на рис. 4а, изготовленного в режиме первого этапа, величина $g$ составила 49 × 103 Дж/м2, для образца (рис. 4б) – 8.8 × 103 Дж/м2, а для типичного образца, изготовленного в промежуточном режиме второго этапа, 32 × 103 Дж/м2. Следует отметить, что указанные величины вполне удовлетворяют требованиям к конструкционным материалам такого назначения.
Рис. 4.
Примеры зависимостей прогибов композитных образцов от нагрузки: а – изготовленных в режиме первого этапа, б – изготовленных в режиме третьего этапа.
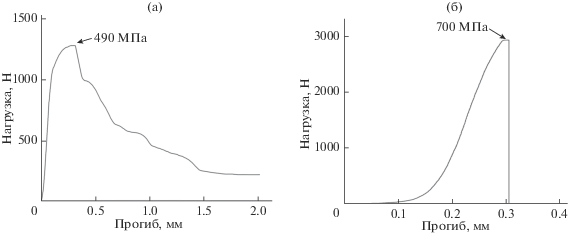
Рис. 5.
Образцы после испытаний на трехточечный изгиб: а – продольное сечение образца, полученного в режиме второго этапа (сплошной стрелкой показано направление приложения нагрузки, а пунктирной – направление распространения макротрещины); б – поверхность разрушения; 1 – волокно, 2 – слой II исходного сплава ниобия, 3 – слой III исходного порошка ниобия.
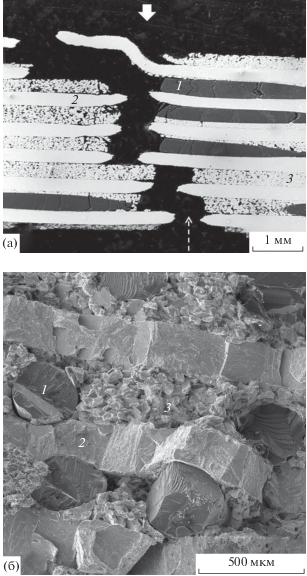
Разрабатываемый композитный материал планируется применять в широком диапазоне температур. И проблема трещиностойкости (в особенности при низких температурах) для него является одной из наиболее важных. Макроскопические характеристики нехрупкого поведения материала под нагрузкой (деформационные кривые и величины эффективной поверхностной энергии разрушения) дополняются топологий поверхностей разрушения, показанной на рис. 5. На продольном сечении образца (рис. 5а) после разрушения наблюдаются множественные микроразрушения: дробление волокон (1) с расслоениями и сдвигами по границам волокно–матрица; пластическая деформация с “шейкообразованием” слоя достаточно пластичного твердого раствора ниобия (2); разрушение неоднородной структуры ниобия по границам зерен в слое с образованием микротрещин вблизи зоны продвижения макротрещины (3), причем микротрещины тормозятся на границах раздела слоев. Поверхность разрушения (рис. 5б), образовавшаяся после прохождения макротрещины, подтверждает описанный характер микроразрушений. Эти виды микроразрушений, не лежащих в плоскости распространения макротрещины, приводят к увеличению энергии неупругого рассеяния в процессе разрушения композита, то есть к увеличению его трещиностойкости.
ЗАКЛЮЧЕНИЕ
Разработана иерархически организованная слоисто-волокнистая композитная структура. Твердофазным методом диффузионной сварки впервые получены образцы слоисто-волокнистого композита с матрицей из высокотемпературного материала на основе ниобия, однонаправленно армированного волокнами монокристаллического сапфира.
Методом Степанова из расплава оксида алюминия изготовлены армирующие волокна. В результате испытаний волокон впервые получены зависимости их прочности от длины. Прочность полученных волокон отвечает мировому уровню.
Установлено образование твердых растворов и возникновение интерметаллидов системы Nb–Al в процессе формирования структуры композитов, повышающих их механические свойства.
Проведены испытания на прочность, определена эффективная поверхностная энергия разрушения композитов, установлена их корреляция с режимами изготовления. Полученные значения прочности и поверхностной энергии удовлетворяют требованиям для материалов такого рода.
Методом растровой электронной микроскопии исследована структура композитов, методом рентгеноспектрального микроанализа определен элементный состав данной структуры. Получены фрактограммы поверхностей разрушения, проведен топографический анализ различных видов множественных микроразрушений, обеспечивающих повышение сопротивления разрушению.
Полученные результаты характеризуют не только представленный композитный материал, но носят и достаточно общий характер. Данные могут быть применены в качестве экспериментальной основы для механико-математического моделирования поведения подобных структур в процессе их формирования и под нагрузкой, а также дальнейших исследований с целью улучшения характеристик полученного композита и разработки новых слоисто-волокнистых композитных материалов.
Список литературы
Келли А. // Наука – производству. 2007. № 2. С. 8.
Милейко С.Т. // Наука – производству. 2007. № 2. С. 12.
Карпов M.И., Внуков В.И., Строганова Т.С., Прохоров Д.В., Желтякова И.С., Гнесин Б.А., Кийко В.М., Светлов И.Л. // Изв. РАН. Сер. физ. 2019. Т. 83. № 9. С. 1353. https://doi.org/10.1134/S0367676519100156
Алексеев А.Г., Бовкун А.Г., Болгар А.С. Свойства, получение и применение тугоплавких соединений / Ред. Косолапова Т.Я. М.: Металлургия, 1986. 928 с.
Mileiko S.T., Novokhatskaya N.I. // J. Mater. Eng. and Perform. 2015. V. 24. № 7. P. 2836. https://doi.org/10.1007/s11665-014-1305-0
Кийко В.М., Коржов В.П. // Поверхность. Рентген., синхротр. и нейтрон. исслед. 2019. № 5. С. 62. https://doi.org/10.1134/S0207352819050081
Korzhov V.P., Kiiko V.M. // J. Int. Sci. Publ.: Mater. Methods Technol. 2018. V. 12. P. 343.
Kiiko V.M., Korzhov V.P. // J. Int. Sci. Publ.: Mater. Methods Technol. 2017. V. 11. P. 28.
Кийко В.М., Коржов В.П. // Поверхность. Рентген., синхротр. и нейтрон. исслед. 2017. № 11. С. 42. https://doi.org/107868/S0207352817110051
Коржов В.П., Кийко В.М. // Изв. РАН. Сер. физ. 2017. Т. 81. № 11. С. 1513. https://doi.org/107868/S036767651711014X
Korzhov V.P., Kiiko V.M. // Sci. Proc. Sci. Tech. Union Mech. Eng. 2016. V. 3. Iss. 189. P. 14. https://doi.org/10.1007/978-3-319-62870-7_14
Korzhov V.P., Kiiko V.M. // J. Int. Sci. Publ.: Mater. Methods Technol. 2016. V. 10. P. 83.
Cook J., Gordon J.E. // Proc. Royal Society. 1964. V. 282. Iss. 8. P. 508.
Милейко С.Т. // Изв. РАН. Сер. физ. 1999. Т. 63. № 9. С. 1866.
Милейко С.Т. // Композиты и наноструктуры. 2015. Т. 7. № 7. С. 191.
Коржов В.П., Кийко В.М. // Актуальные проблемы прочности. Т. 1. Витебск: Издательство Витебского государственного технологическго университета, 2018. С. 359.
Светлов И.Л. // Материаловедение. 2010. № 9. С. 29.
Светлов И.Л. // Материаловедение. 2010. № 10. С. 18.
Kurlov V.N., Stryukov D.O., Shikunova I.A. // J. Phys.: Conf. Ser. 2016. V. 673. P. 012017.
Коржов В.П., Кийко В.М. // Деформация и разрушение материалов. 2015. № 6. С. 11.
Kelly A. // Proc. Royal Society. 1970. V. 319. P. 95.
Коржов В.П., Кийко В.М., Прохоров Д.В. // Перспективные материалы и технологии. Т. 1. Витебск: Издательство Витебского государственного технологического университета, 2017. С. 360.
Kiiko V.M., Mileiko S.T. // Composites Science and Technology. 1999. V. 59. Iss. 13. P. 1977.
Рудицин М.Н., Артемов П.Я., Любошиц М.И. Справочное пособие по сопротивлению материалов. Минск: Вышэйшая школа, 1970. 632 с.
Кийко В.М. // LVIII Международная конференция Актуальные проблемы прочности. Пермь. 2017. С. 194.
Кийко В.М, Коржов В.П. // Поверхность. Рентген., синхротр. и нейтрон. исслед. 2019. № 5. С. 62. https://doi.org/10.1134/S0207352819050081
Дополнительные материалы отсутствуют.
Инструменты
Поверхность. Рентгеновские, синхротронные и нейтронные исследования