Поверхность. Рентгеновские, синхротронные и нейтронные исследования, 2020, № 6, стр. 61-67
Износ тонких покрытий различной твердости зондовыми методами
В. А. Лапицкая a, *, Т. А. Кузнецова a, С. А. Чижик a, Д. В. Соловей a, Б. Вархолинский b, А. Гилевич b, С. М. Айзикович c, Б. И. Митрин c, Л. И. Кренев c
a Институт тепло- и массообмена НАН Беларуси
220072 Минск, Республика Беларусь
b Кошалинский Технологический университет
75-453 Кошалин, Польша
c Донской государственный технический университет
1344000 Ростов-на-Дону, Россия
* E-mail: vasilinka.92@mail.ru
Поступила в редакцию 15.10.2019
После доработки 22.12.2019
Принята к публикации 24.12.2019
Аннотация
Методом атомно-силовой микроскопии выполнен износ и представлены результаты определения износостойкости покрытий Cu и SiO2, каждое толщиной 100 нм, и ZrN толщиной 3 мкм. Установлены зависимости удельного объемного износа от нормального механического напряжения в контакте зонда АСМ с поверхностью при износе.
ВВЕДЕНИЕ
Одним из направлений современной микрообработки поверхности является использование зондовых технологий механической литографии для создания наноструктур [1]. Метод применяется для создания одно-, двух- и даже трехмерных структур [2]. Кроме квантовых точек, нанопроволок, массивов периодических выступов и впадин возможно изготовление более сложных структур путем сочетания этапов нанесения фоторезиста, осаждения покрытий и наномеханический литографии [2]. Использование зондовых методов при создании полупроводниковых структур обеспечивает возможность появления новых базовых элементов наноэлектроники с размерами порядка десятков и единиц нанометров [3]. Возможность непосредственного воздействия на поверхность без необходимости использования масок и химических реагентов обеспечивает нанометровую точность контуров, исключает посторонние загрязнения поверхности [4]. АСМ как инструмент обработки поверхности позволяет реализовать нормальную нагрузку в диапазоне от нН до мН, что в сочетании с малым радиусом закругления острия зонда создает возможности для точного модифицирования поверхностей от мягких полимеров до твердых износостойких покрытий [5]. Возможность АСМ предварительно изучить морфологию поверхности, определить шероховатость, размер зерен, распределение различных фаз по контрастам латеральных сил или сил адгезии представляет полную информацию о микроконтакте с поверхностью, позволяет объяснить некоторые феномены микротрибологии и микромеханики [6–9]. Кроме формирования наноструктур износ поверхности методом АСМ с успехом применяется для тестирования материалов и тонких слоев [10, 11]. АСМ позволяет определить коэффициент трения между зондом и поверхностью покрытия, что позволяет успешнее выполнять операции контролируемого износа [11]. Помимо классического испытания на износ по схеме “шарик-диск” с использованием в качестве контртела шариков из Al2O3, WC, SiN (или других твердых материалов) диаметром 6–10 мм, направлением последних лет по определению износостойкости тонких покрытий на деталях малых размеров является использование АСМ с алмазным зондом [12–14]. Малый размер контакта в этом случае исключает деформацию подложки или образование механических напряжений на границе “покрытие–подложка” и разрушение покрытия вследствие его частичного отслаивания или растрескивания, а обеспечивает чисто абразивный механизм износа истираним нанометровых слоев [14]. Особенно актуален данный метод при испытании твердых тонких покрытий, нанесенных на подложку из более мягкого материала, а также при размерах деталей несколько миллиметров [15]. Точность визуализации результатов изнашивания АСМ позволяет оценивать удельный объемный износ до 10–16–10–17 м3/Н · м [16].
Необходимость использования для создания субмикро- и наноразмерных элементов структур различного назначения материалов с широким диапазоном механических свойств делает актуальным исследования по микрообработке АСМ тонких покрытий различной твердости, которые широко применяются в качестве поверхностей контактных площадок (например, медное), защитных слоев режущих инструментов (например, ZrN). Значения микротвердости покрытий Cu и ZrN различаются более чем в 50 раз [11, 17]. Среднее положение между ними по твердости занимает диоксид кремния (SiO2) и используется в микроэлектронике, различных датчиках. Контроль механических свойств и износостойкости таких покрытий обязателен наряду с их функциональными свойствами.
Цель данной работы – выполнение износа тонких покрытий ZrN, SiO2 и Cu с помощью атомно-силовой микроскопии, определение значений удельного объемного износа в зависимости от приложенной нормальной нагрузки при контроле изменения острия зонда и контактного давления.
МЕТОДИКА ЭКСПЕРИМЕНТА
В качестве объекта исследования были выбраны тонкие покрытия с существенно различающейся микротвердостью – от мягких до износостойких покрытий (табл. 1) – покрытия Cu, SiO2 и ZrN. Значения модуля упругости (E) и микротвердости (H) определяли на наноинденторе Hysitron 750 Ubi (США) путем внедрения алмазного индентора Берковича с радиусом закругления 200 нм с непрерывной регистрацией деформационных кривых зависимости глубины внедрения от приложенной нагрузки. Калибровку радиуса острия выполняли внедрением в калибровочный образец плавленого кварца.
Таблица 1.
Микротвердость и модуль упругости покрытий Cu, SiO2 и ZrN
Покрытие | Толщина, мкм | Коэффициент Пуассона | Модуль упругости, ГПа | Микротвердость, ГПа |
---|---|---|---|---|
Cu | 0.1 | 0.35 | 110.0 | 0.5–1 |
SiO2 | 0.1 | 0.17 | 81.2 | 11 |
ZrN | 3 | 0.33 | 314.2 | 29 |
Магнетронное напыление меди (Cu) и диоксида кремния (SiO2) осуществлялось на установке Izolab (Изовак, Беларусь) на предварительно очищенные в изопропиловом спирте, промытые в дистиллированной воде и просушенные в струе горячего воздуха полированные кремниевые подложки диаметром 76 мм.
Напыление меди проводили с помощью водоохлаждаемого магнетрона при постоянном токе (DC, ∅ 100 мм) из медной мишени чистотой 99.997%, а диоксид кремния – с помощью водоохлаждаемого высокочастотного магнетрона (RF, ∅ 100 мм) из SiO2 мишени чистотой 99.99%. Перед проведением процесса в камере установки проводилась откачка вакуума с помощью безмаслянного форвакуумного и турбомолекулярного насосов до давления ≤1 × 10–3 Па, а также осуществлялся подогрев подложек до температуры 300°С для меди, а для диоксида кремния – до 150°С. Подложкодержатель вращался со скоростью 50 об./мин. По достижении заданного давления осуществлялась очистка ионами Ar поверхности подложек для удаления адсорбированных из атмосферы атомов при ускоряющем напряжении 1200 В. Затем проводился непосредственно процесс магнетронного напыления. Медь напыляли при установленной мощности 400 Вт и расходе рабочего газа (Ar) 60 см3/мин, а диоксид кремния – при установленной мощности 600 Вт и расходе смеси рабочих газов Ar 68 см3/мин и О2 2 см3/мин. В процессе напыления толщина слоев меди и диоксида кремния контролировалась кварцевым измерителем толщины и составила 100 нм при равномерности нанесения не хуже ±1%.
Покрытия ZrN были сформированы магнетронным методом на установке TINA 900M в плазме газового разряда аргона-азота на закаленных подложках из стали HS6-5-2 диаметром 32 мм, полированных до Ra = 0.02 мкм. Покрытие ZrN осаждали при мощности магнетрона 700 Вт, расходе азота 4 см3/мин.
Исследования износостойкости покрытий проводились на АСМ Dimension FastScan (Bruker, США) в режиме Contact Mode с использованием кантилеверов с алмазным острием на кремниевой консоли типа D300 (производство SCDprobes, Эстония) для покрытия ZrN с жесткостью консоли 73.7 Н/м и для покрытий SiO2 и Cu – c жесткостью консоли 48.1 Н/м. Дополнительно для износа Cu за пять проходов, а не за один, использовали стандартный кремниевый кантилевер типа NSC-11 (производство Micromash, Эстония) с начальным радиусом закругления острия 34.8 нм, с жесткостью консоли 7.4 Н/м. В процессе испытаний изменялась нормальная нагрузка на зонд, остальные параметры поддерживались постоянными: поле износа 1 × 1 мкм, пять циклов при каждой нагрузке, 128 × 128 точек, скорость 1.99 мкм/с. Исключение составило покрытие ZrN, для его износа понадобилось 40 циклов и скорость движения зонда 4.07 мкм/с. Движение зонда по поверхности – возвратно-поступательное. К алмазным зондам прикладывали нагрузку от 0.8 до 27 мкН, к кремниевому – от 0.5 до 5.8 мкН. Полученный результат износа визуализировали в режиме PeakForce Tapping QNM. Объем изношенного материала определяли согласно АСМ-профилю через след износа. Удельный объемный износ определяли по отношению объема изношенного материала к нагрузке и длине пути индентора [18].
Механические напряжения в зоне контакта зонда АСМ с поверхностью покрытий (контактное давление) определяли с помощью web-калькулятора контактных напряжений AMES (Advanced Mechanical Engeneering Solutions) [19, 20], задавая значения радиуса закругления зонда, модуля упругости покрытий и зонда.
РЕЗУЛЬТАТЫ И ИХ ОБСУЖДЕНИЕ
Покрытие Cu, как самое мягкое, служило для отработки методики износа АСМ с алмазным зондом. При износе применялась нагрузка на зонд 0.8 и 2 мкН. Радиус закругления зонда составлял 45.5 нм. Однако уже при нагрузке 0.8 мкН произошло полное “соскабливание” покрытия меди с подложки (рис. 1). Удельный объемный износ при этом составил 1.10 × 10–10 м3/Н · м. Контактное давление при нагрузках 0.8 и 2 мкН составило 15.6 и 21.2 ГПа соответственно. При нагрузке 2 мкН за пять циклов алмазный зонд износил медное покрытие и на 30 нм кремниевую подложку.
Рис. 1.
Результат износа медного покрытия толщиной 100 нм алмазным зондом за один цикл (проход): а – АСМ-изображение (4 × 7 мкм); б – профиль износа при нагрузках 0.8 и 2 мкН.
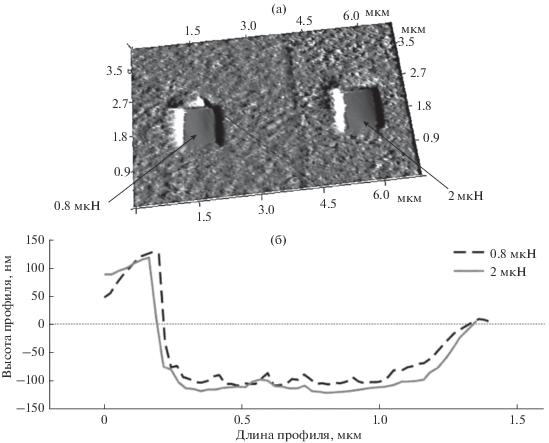
С использованием кремниевого зонда удалось выполнить износ постепенно за несколько проходов (рис. 2). При нагрузках 0.48 и 0.97 мкН после пяти циклов износ выявить не удалось, так как какие-либо следы на поверхности отсутствовали. Первый след при нагрузке 1.9 мкН равнялся глубине 20 нм. Данная глубина показывает особое состояние поверхностного слоя толщиной около 20 нм, для разрушения которого нужно затратить больше энергии, чем для остального покрытия. При последующем росте нагрузки до 5.8 мкН глубина следа износа увеличивалась незначительно и находилась приблизительно на уровне 40 нм. Удельный объемный износ при этом составил 7.8 × 10–12 –2.0 × 10–11 м3/(Н · м).
Рис. 2.
АСМ-изображение поверхности медного покрытия толщиной 100 нм после износа кремниевым зондом за пять циклов на поле 3 × 3 мкм: а – при нагрузке 1.9 мкН; б – при нагрузке 4.6 мкН; в – профили сечения поверхности износа при различных нагрузках от 1.9 до 5.8 мкН.
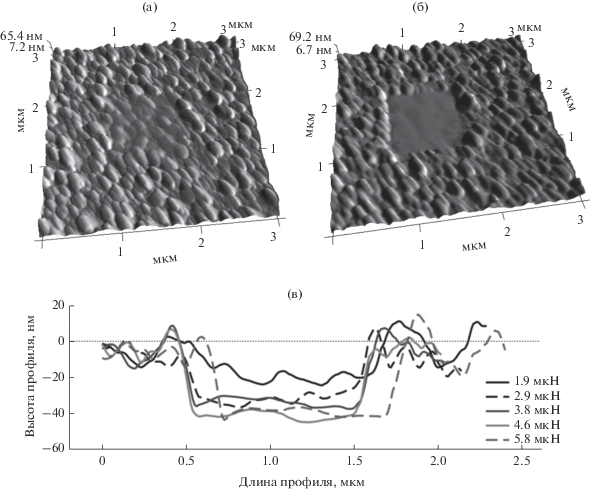
Зависимость глубины износа от приложенной нагрузки для медного покрытия представлена на рис. 3.
Рис. 3.
Зависимости глубины износа (а) и удельного объемного износа и нормального механического напряжения (б) для покрытия Cu от нормальной нагрузки.
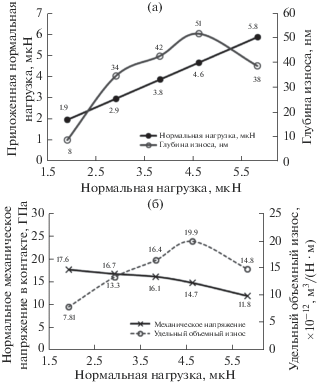
Для износа покрытия SiO2 (рис. 4) использовался алмазный зонд с жесткостью консоли 48.1 Н/м и радиусом закругления 45.5 нм. При износе применялась нагрузка на зонд от 0.8 до 8 мкН. При нагрузке 0.8 мкН удельный объемный износ покрытия SiO2 составил 0.79 × 10–12 м3/(Н · м). Завышение глубины левого края на следе износа (рис. 4) объясняется некоторым замедлением зонда при изменении направления возвратно-поступательного движения. С увеличением нагрузки удельный объемный износ SiO2 увеличивается по экспоненциальной зависимости (рис. 5). Очень малые значения глубины износа (0.8–1.1 нм) при нагрузках 0.8 и 2 мкН также могут объясняться необходимостью затратить дополнительную энергию на разрушение поверхности, но в отличие от Cu, у SiO2 толщина поверхностного слоя составляет не 20, а 1.1 нм. Для полного износа покрытия SiO2 толщиной 100 нм до подложки понадобилась нагрузка на зонд 8 мкН. При этом удельный объемный износ составил 10.42 × 10–12 м3/(Н · м). Контактное давление при нагрузке на зонд 8 мкН составило 16.56 ГПа (рис. 5).
Рис. 4.
Результат износа покрытия SiO2 толщиной 100 нм: а – АСМ-изображение (2 × 3.5 мкм); б – профили сечения поверхности износа при нагрузках 0.8 и 2 мкН; в – профили сечения поверхности износа при нагрузках 4 и 8 мкН.
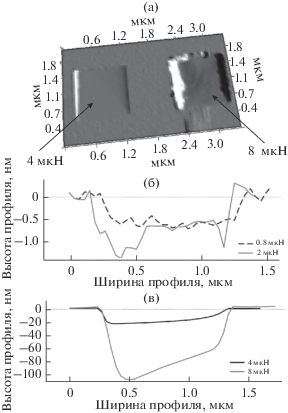
Рис. 5.
Зависимости глубины износа (а) и удельного объемного износа и нормального механического напряжения (б) при износе для покрытия SiO2 от нормальной нагрузки.
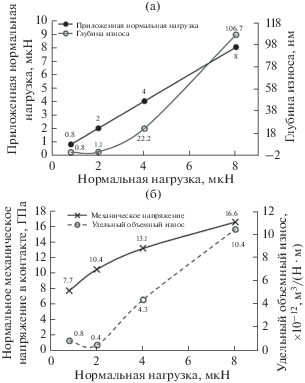
Износ покрытия ZrN при нагрузке на зонд от 0.8 до 8 мкН и 5 циклах прохода зонда результатов, выявляемых АСМ не дал. Существенное влияние на износ оказывает высокая микротвердость покрытия в отличие от покрытия Cu и SiO2. Поэтому для износа покрытия ZrN нагрузку устанавливали от 8.98 до 26.8 мкН, а количество циклов увеличили до 40. При этом постоянными оставались следующие параметры: поле 1 мкм2, скорость движения зонда 4.07 мкм/с. Жесткость консоли и радиус кривизны зонда составили 73.67 Н/м и 31.0 нм соответственно.
Результаты проведения износа на покрытии ZrN приведены на рис. 6. Установлено, что с ростом нагрузки удельный объемный износ уменьшается (рис. 7). Так, при нагрузке 8.98 мкН удельный объемный износ составил 6.19 × 10–14 м3/(Н · м), а при нагрузке 26.94 мкН – 4.79 × 10–14 м3/(Н · м). При этом глубина износа незначительно росла. Данный результат связан с износом не только покрытия, но и алмазного зонда, т.к. после проведенных испытаний на износ на покрытии ZrN радиус закругления острия зонда увеличился до 40.2 нм.
ЗАКЛЮЧЕНИЕ
Методом атомно-силовой микроскопии с использованием алмазного зонда выполнен износ и определена износостойкость покрытий Cu, SiO2 и ZrN. Установлены зависимости удельного объемного износа от нагрузки на зонд.
Максимальные значения удельного объемного износа при использовании алмазного зонда составили 1.10 × 10–10 м3/(Н · м) для Cu (полный срыв пленки), 10.42 × 10–12 м3/(Н · м) для SiO2 и 6.19 × 10–14 м3/(Н · м) для ZrN. При использовании кремниевого зонда и абразивном изнашивании удельный объемный износ Cu составил 2.0 × 10–11 м3/(Н · м). Значения удельного объемного износа в определяющей степени зависят от нормального механического напряжения в контакте, в величине которого учитывается увеличение радиуса зонда при износе твердых материалов. Для изнашивания Cu и образования следов износа нормальное механическое напряжение составило: 11.8–17.6 ГПа; SiO2 – 13.1–16.6 ГПа; ZrN – 109.4–134.4 ГПа. Кроме того, свойства покрытий неоднородны по толщине. Заниженные значения удельного объемного износа при малых нагрузках для Cu и SiO2 объясняются особым состоянием поверхностного слоя, для разрушения которого требуется больше энергии, чем для нижележащих слоев. У покрытия Cu этот слой имеет толщину 20 нм, у SiO2 – 1 нм. Убывающая зависимость удельного объемного износа от контактного давления для ZrN объясняется неоднородностью свойств по толщине покрытия, при этом на поверхности находится более мягкий слой толщиной около 6 нм, образованный оксидами Zr.
Список литературы
Geng Y., Brousseau E. B., Zhao X. et al. // Precision Engineering. 2018. V. 51. P. 536.
Yan Y., GengY., Hu Z. // International Journal of Machine Tools & Manufacture. 2015. V. 99. P. 1.
Борисов В.И., Кувшинова Н.А., Курочка С.П. и др. // Физика и техника полупроводников. 2017. Т. 51. Вып. 1. С. 1534.
Temiryazev A. // Diam. Relat. Mater. 2014. V. 48. P. 60.
Кузнецова Т.А., Вархолински Б., Зубарь Т.И. и др. // Трение и износ. 2017. Т. 38. № 6. P. 503.
Kuznetsova T.A., Chizhik S.A., Khudoley A.L. // Journal of Surface Investigation: X-Ray, Synchrotron and Neutron Techniques. 2014. T. 8. № 6. P. 1275.
Ulyanova T.M., Titova L.V., Medichenko S.V. et al. // Crystallography Reports. 2006. V. 51. Suppl. 1. P. S144. https://doi.org/10.1134/S1063774506070212
Углов В.В., Анищик В.М., Кулешов А.К. и др. // Перспективные материалы.2003. № 6. P. 5.
Andreyev M., Markova L., Kuznetsova T., Ani-shchik V.M. // Vacuum. 2005. V. 78. № 2–4. P. 451.
Погоцкая И.В., Кузнецова Т.А., Чижик С.А. // Механика машин, механизмов и материалов. 2011. № 3 (16). С. 43–48.
Тарендь М.В., Кузнецова Т.А., Чижик С.А. // Методологические аспекты сканирующей зондовой микроскопии Сб. док. X межд. конф. Гл. ред. Чижик С.А. 2012. С. 164.
Вархолински Б., Гилевич А., Куприн А.C. и др. // Трение и износ. 2019. Т. 40. № 2. С. 209.
Kuznetsova T.A., Andreev M.A., Markova L.V., Chekan V.A. // Journal of Friction and Wear. 2001. V. 22. № 4. P. 423.
Kuznetsova T., Zubar T., Chizhik S. et al. // J. Materials Engineering and Performance 2016. V. 25. Iss. 12. P. 5450. https://doi.org/10.1007/s11665-016-2390-z
Витязь П.А., Комаров А.И., Комарова В.И., Кузнецова Т.А. // Трение и износ. 2011. Т. 32. № 4. С. 313.
Кузнецова Т.А., Андреев М.А., Маркова Л.В., Чижик С.А. // Трение и износ. 2007. Т. 28. № 3. С. 276.
Kuznetsova T.A. et al. // IOP Conf. Series: Materials Science and Engineering. 2018. V. 443. P. 012 017.
Кузнецова Т.А., Андреев М.А., Маркова Л.В. // Трение и износ. 2005. Т. 26. № 5. С. 521.
http://www.amesweb.info/HertzianContact/HertzianContact.aspx.
Budynas R.G. Shigley’s Mechanical Engineering Design / 10-th Edition. McGraw-Hill, 2014. 1105 p.
Дополнительные материалы отсутствуют.
Инструменты
Поверхность. Рентгеновские, синхротронные и нейтронные исследования