Поверхность. Рентгеновские, синхротронные и нейтронные исследования, 2021, № 10, стр. 89-96
Микроструктура, фазовый состав, субструктура и остаточные напряжения в алюминиевом сплаве АК5М7 после его электроискровой обработки
И. Х. Хасан a, *, Н. А. Панькин b, **
a Ministry of Science and Technology
Baghdad, Iraq
b Институт физики и химии, Национальный исследовательский
Мордовский государственный университет им. Н.П. Огарева
430005 Саранск, Россия
* E-mail: srorismael@gmail.com
** E-mail: panjkinna@yandex.ru
Поступила в редакцию 17.01.2021
После доработки 12.03.2021
Принята к публикации 22.03.2021
Аннотация
Представлены результаты исследования микроструктуры, фазового состава, параметров субструктуры и остаточных напряжений поверхностного слоя сплава марки АК5М7 после его электроискровой обработки (ЭИО) с использованием медно-фосфорного электрода. Основным изменяющимся параметром являлась энергия ЭИО. Исследуемый материал представляет собой многофазную систему. Основными являются фазы: алюминия, Al2Cu и Cu3Al. Увеличение энергии электроискровой обработки сопровождается ростом долей Al2Cu и Cu3Al, величины микродеформаций и остаточных напряжений, а также уменьшением размеров субблоков. Для фазы алюминия остаточные напряжения носят растягивающий характер, а для Al2Cu – сжимающий. Анализ интенсивностей дифракционных линий указывает на возможность текстуры в обрабатываемом слое. Повышение энергии электроискровой обработки приводит к хаотическому распределению ориентации зерен формируемых кристаллографических фаз. Полученные результаты объясняются неравновесными процессами в приповерхностном слое при высоких механических и термических воздействиях, сопровождающихся микрометаллургическими процессами.
ВВЕДЕНИЕ
В ходе эксплуатации приборов/агрегатов детали, входящие в их состав, подвергаются различным видам воздействий: термо- и мехациклическим, трибологическим и т.д. При длительной работе в них возникают (в большинстве случаев) разнообразные микро- или макроразрушения, которые в дальнейшем могут привести к выходу из строя данной детали. В большинстве случаев это требует полной замены испорченного компонента прибора на аналогичный. Иногда возможно восстановить разрушенную поверхность изделия различными физико-химическими способами. Среди них можно назвать следующие: электроконтактная приварка ленты, напыление покрытий газотермическими, газодинамическими и газоплазменными методами, электроискровое легирование и т.д. К одному из перспективных методов относится электроискровая обработка/легирование (ЭИО) поверхностного слоя [1]. В ее основе лежит разрушение материала анода и его перенос через газовую среду на обрабатываемое изделие (катод). При этом температура в межэлектродном пространстве (искровом канале) находится в интервале от 5000 до 10 000°С. Не смотря на относительную простоту реализации метода ЭИО и множество литературных данных (например, [2–8]) по его исследованию, остаются вопросы о физических и химических процессах, протекающих при формировании структуры и свойств материала, модифицированного электроискровой обработкой.
Целью настоящей работы являлось исследование алюминиевого сплава АК5М7 после его электроискровой обработки медным электродом с фосфором. При этом решались следующие задачи: выявление фазового состава модифицированного слоя; расчет параметров субструктуры из уширения дифракционных линий и определение величины остаточных напряжений.
МЕТОДИКА ЭКСПЕРИМЕНТА
Электроискровая обработка образцов алюминиевого сплава АК5М7 проводилась на установке ALIER-31 в ручном режиме. Исходные образцы имели форму параллелепипеда с размерами 20 × × 20 × 5 мм. Состав сплава по данным рентгенофлуоресцентного анализа, проведенного на спектрометре ARL PERFORM'X 4200, был следующий, в ат. %: Al – 88, Si – 5 и Cu – 7. При ЭИО в качестве анода использовали проволочные электроды из сплава меди с фосфором марки МФ9. Доля фосфора составляла порядка 8 ат. %.
Для исследования микроструктуры использовали растровый электронный JEOL JSM-6480LV и оптический МЕТАМ РВ-21 микроскопы.
Рентгенографические исследования проводили с помощью рентгеновского дифрактометра “Empyrean PANalytical” (излучение CuKα). Обработку исходных рентгенограмм (определение фазового состава и параметров дифракционных линий) осуществляли в программном комплексе High Score Plus. Используя его, можно работать с базой рентгенографических данных порошковых материалов PDF-2.
Оценку остаточных напряжений проводили по значениям параметров кристаллической решетки, для которых разные плоскости отражения параллельны поверхности образца [9, 10]. В этом случае величину макронапряжений σ можно рассчитать по формуле:
где K1, K2 – рентгеновские упругие константы для направлений h1k1l1 и h2k2l2, которые соответствуют периодам а1 и а2 кристаллической решетки. Значения K = (μ/Е)hkl, где μ, Е – коэффициент Пуассона и модуль Юнга для заданного кристаллографического направления (hkl) соответственно, определяли с помощью программы IsoDEC [11]. Исходными данными для нее являлись монокристальные константы упругой податливости Sij исследуемых фаз. Их значения для кристаллографических фаз, выявленных в ходе настоящего исследования можно найти в источниках [12, 13].Для кубического кристалла параметр кристаллической решетки a можно рассчитать через межплоскостное расстояние d в направлении (hkl) по формуле:
В случае тетрагональной и гексагональных фаз можно использовать приведенные значения x = = с/a периодов а и с кристаллической решетки [10]:
Параметры субструктуры (микродеформации ε и размер субблоков D) определялись из результатов полнопрофильного анализа рентгенограмм методом Ритвельда [14].
РЕЗУЛЬТАТЫ И ОБСУЖДЕНИЕ.
На рис. 1 представлены фотографии поверхности образцов после их электроискровой обработки. Они получены методами оптической и растровой электронной микроскопии (РЭМ). Их анализ свидетельствует о наличии сильно неоднородного по микроструктуре поверхностного слоя с возможным образованием покрытия. Согласно результатам исследований РЭМ, поверхности образцов после электроискровой обработки имеют большую шероховатость. Данные факты определяются процессами при ЭИО. В частности, ЭИО сопровождается высокими механическими и термическими воздействиями на обрабатываемые участки поверхности образца [1, 3]. Вследствие этого могут возникать локальные давления до нескольких МПа при температуре в месте контакта ~104°С, которая существенно превышает соответствующие температуры кипения основных материалов подложки (алюминий) и электрода (медь). Такое термомеханическое воздействие приводит к образованию пластических течений и деформаций в обрабатываемом и близлежащих участках образца, а также переносу вещества в виде больших жидких капель. Хотя не исключается отрыв от медно-фосфорного электрода твердых частиц. Высокие значения коэффициента теплопроводности основных компонентов рассматриваемой системы (~390 Вт/(м · К) для меди и ~210 Вт/(м · К) для алюминия) способствуют большой скорости теплоотвода от места электроискровой обработки. Данный факт приводит к появлению градиента температур между обрабатываемой поверхностью и нижележащими слоями. При этом в слое толщиной порядка нескольких микрометров, температура быстро убывает до соответствующих температур фазовых переходов и превращений материалов электрода и подложки. Вследствие этого интенсифицируются микрометаллургические процессы с турбулентным движением перемешивающихся масс. Данный факт способствует образованию неравновесных структур с малым размером зерна, высокой гетерогенностью по составу, структуре, высокими макронапряжениями и т.д.
Рис. 1.
Микроструктура поверхности сплава АК5М7 после его электроискровой обработки по данным электронной и оптической (вкладка) микроскопий.
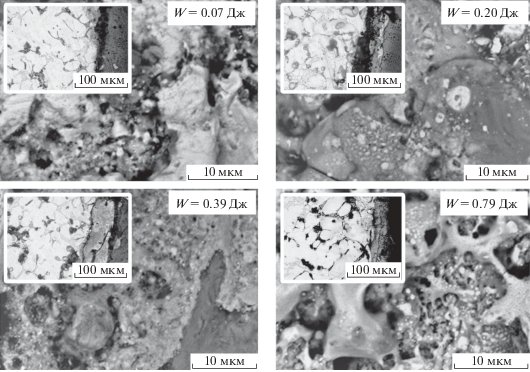
Повышение энергии электроискровой обработки W сопровождается ростом джоулева тепла, что способствует увеличению масс контактирующих материалов (подложки и электрода), переходящих в парообразное состояние. При этом преимущественно испаряется материал обрабатываемого сплава – алюминий, что обусловлено различиями в температурах кипения меди и алюминия. Об этом свидетельствуют значения изменения массы образца Δm после электроискровой обработки, представленные на рис. 2. Она принимает отрицательные значения при различных энергиях ЭИО и увеличивается по мере роста W. Данный факт говорит об эрозии поверхностного слоя вследствие электроискровой обработки. Об интенсификации процесса испарения с ростом W свидетельствуют значения изменения массы Δm (рис. 2). Подобный результат наблюдался также при обработке сплава АК5М7 электродом из чистой меди [2]. Отрицательные значения прироста массы характерны для процесса электроискровой обработки с использованием электродов другого элементного состава [15]. Такое поведение связано с различием вкладов в массоперенос двух основных конкурирующих процессов: увеличения массы катода из-за полярного переноса вещества и разрушения электроискрового покрытия за счет накопления в нем дефектов, а также образования хрупких оксидов и нитридов металлов подложки и электрода [16]. На начальном этапе происходит преимущественный перенос вещества с анода на катод, а затем более интенсивно теряется масса покрытия в результате его разрушения.
Повышение энергии ЭИО приводит к росту зоны, подвергающейся значительным термомеханическим воздействиям. При этом происходит интенсивное перемешивание компонентов подложки и электрода, сопровождающееся ростом площади контакта материалов подложки и электрода. Данный факт способствует интенсификации образования интерметаллических соединений системы “медь–алюминий”. При этом интенсивнее происходит перенос на подложку материала медно-фосфорного электрода, что подтверждается результатами рентгенофазового исследования, представленными на рис. 3. Анализ дифрактограмм от сплава АК5М7 в исходном состоянии и после его электроискровой обработки указывает на многофазность в рассматриваемых системах. Отмечается после ЭИО присутствие в поверхностном слое следующих основных фаз: Al, Si, Al2Cu и Cu3Al (при W ≥ 0.29 Дж). Фазовый набор Al, Si, Al2Cu характерен и для исходного сплава АК5М7. Возможно также существование кристаллографических фаз системы Cu–Al–P. Их объемное содержание, скорее всего, меньше предела обнаружения рентгенографического метода. В табл. 1 представлены доли основных фаз присутствующих в поверхностном слое алюминиевого сплава АК5М7 до и после его ЭИО. Они вычислены из анализа интегральных интенсивностей.
Рис. 3.
Участки рентгеновской дифракционной картины от поверхностного слоя сплава АК5М7 после его электроискровой обработки (линии фаз: + – Si, ▼ – Al2Cu, * – Al, △ – Cu3Al). На вкладке (вверху справа) увеличенный участок дифрактограммы для энергии ЭИО W = 0.79 Дж.
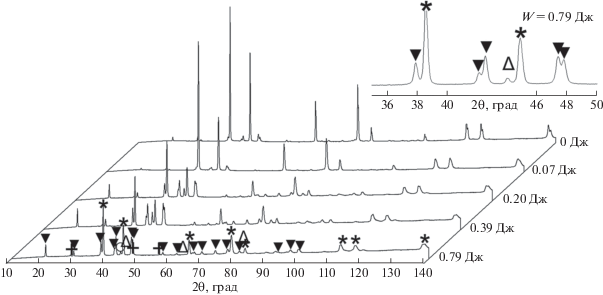
Таблица 1.
Фазовый состав поверхности сплава АК5М7 после его электроискровой обработки
W, Дж | Доля фаз, об. % | |||
---|---|---|---|---|
Al | Al2Cu | Si | Cu3Al | |
АК5М7 | 94 | 2 | 4 | – |
0.07 | 94 | 3 | 2 | – |
0.20 | 70 | 22 | 5 | 1 |
0.39 | 65 | 25 | 5 | 3 |
0.79 | 59 | 28 | 5 | 5 |
Увеличение доли фаз Al2Cu и Cu3Al с повышением энергии электроискровой обработки свидетельствует об интенсификации процессов массопереноса в рассматриваемой системе. Преимущественное испарение алюминия, отмеченное выше, также вносит определенный вклад в значения содержания интерметаллических соединений в обрабатываемом объеме. Образование интерметаллических соединений системы Cu–Al происходит преимущественно за счет объемной диффузии в жидкофазных материалах [17, 18]. В этом случае возможно формирование структуры, состоящей из чередующихся слоев различного фазового состава. Их порядок и состав будет определяться диаграммой состояния системы Cu–Al:
Исходя из роста интенсивности фазы Cu3Al в поверхностном слое при увеличении энергии W, можно говорить о формировании на поверхности сплава электроискрового покрытия. Хотя анализ микроструктуры (рис. 1) не дает на это однозначного ответа. Увеличение доли меди сопровождается ростом числа центров кристаллизации (у меди более высокая температура плавления) с формированием мелкодисперсной структуры. Вследствие этого получается структура с большими деформациями и высокой плотностью дислокаций в кристаллических решетках формирующихся фаз. На это указывают значения уширения дифракционных линий, которое обусловлены параметрами субструктуры: микродеформациями ε и малостью размеров субблоков D. На рис. 4 представлены зависимости D и ε от энергии электроискровой обработки W для трех основных фаз: Al, Al2Cu и Cu3Al. Можно отметить, что увеличение W сопровождается ростом величины микродеформаций и уменьшением размеров субблоков. Для других кристаллографических фаз, обнаруженных в ходе настоящего исследования, определение параметров субструктуры крайне затруднительно. Это обусловлено малой интенсивностью отдельных рефлексов данных фаз, а также их взаимным перекрытием с другими дифракционными линиями. Данный факт приводит к большой ошибке в определении значений D и ε.
Рис. 4.
Зависимость размера субблоков D (а) и величины микродеформаций ε (б) от энергии электроискровой обработки W (◻ – Al, ▽ – Al2Cu, ⚪ – Cu3Al).
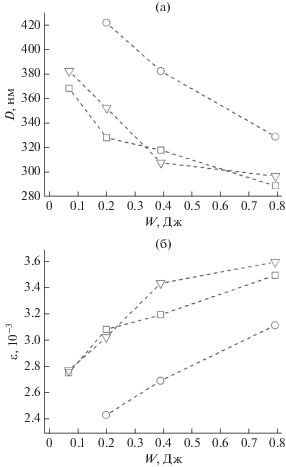
Наблюдаемые изменения положений дифракционных линий относительно порошкового материала (данные базы PDF-2) обусловлены, прежде всего, наличием внутренних сжимающих и растягивающих напряжений. На рис. 5 представлены зависимости остаточных напряжений σ для фаз алюминия и интерметаллического соединения Al2Cu поверхностного слоя сплава АК5М7 от энергии W электроискровой обработки. Данные результаты получены усреднением по глубине порядка 15–17 мкм (определяется проникновением рентгеновского излучения в соответствующий материал для рассматриваемых брегговских углов [14]). Можно отметить, что для алюминия остаточные напряжения носят (в основном) растягивающий характер. Макронапряжения в интерметаллическом соединении Al2Cu для всего исследуемого диапазона энергий ЭИО носят сжимающий характер. Для кремния Si дифракционные линии находятся в области малых брегговских углов и имеют небольшую интенсивность. Вследствие этого оценка величины макронапряжений для него крайне затруднительна из-за большой ошибки в определении параметров дифракционных линий.
Рис. 5.
Зависимость остаточных напряжений в алюминии (◻) и интерметаллическом соединении Al2Cu (▽) от энергии электроискровой обработки.
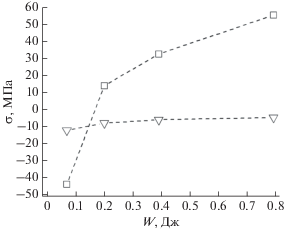
Среди причин возникновения остаточных напряжений можно назвать большой градиент температур по толщине модифицированного слоя, обусловленного процессами, происходящими при ЭИО (говорилось выше по тексту). В данном случае, появление макронапряжений связано с температурной зависимостью линейного коэффициента теплового расширения (КТР). Как было указано выше, рассматриваемая система состоит из многих фаз, различающихся значениями КТР. Вследствие этого на границе фаз будут присутствовать термические напряжения, обусловленные различиями КТР контактирующих материалов. Кроме того, возможен также вклад различия элементного и фазового составов по глубине модифицированного ЭИО слоя (в настоящей статье данные исследования не проводились).
Изменение размеров зерен/субблоков и доли фаз Al2Cu и Cu3Al по мере роста W, как отмечалось выше, сопровождается ростом площади межфазных и межзеренных границ. Вышеуказанный факт приводит к изменению остаточных напряжений (наблюдается их рост). На это указывает достаточно хорошая корреляция между зависимостями σ(W) и D(W) для различных фаз. Средний коэффициент корреляции составляет порядка 0.98.
Образование интерметаллического соединения сопровождается также изменениями в удельном объеме/плотности. Данный факт также способствует возникновению макронапряжений в исследуемых материалах.
Значения отношений интенсивностей I(hkl) рефлекса с индексами (hkl) к суммарной интенсивности IΣ всех дифракционных максимумов рассматриваемой фазы представлены на рис. 6. Приведены данные лишь для трех самых сильных линий (на них приходится более 95% всей интенсивности). Можно отметить, что для алюминия значение отношения интенсивности рефлекса (111) к суммарной интенсивности рассматриваемой фазы (I(111)/IΣ изменяются от 0.65 до 0.52 по мере повышения W) несколько выше соответствующих данных для порошкового материала (0.44, согласно данным PDF-2). Данный факт свидетельствует о возможности наличия преимущественной ориентации роста зерен алюминия в направлении (111). Особенно это касается модификации поверхности с малыми энергиями W. Стоит отметить, что в настоящей работе не проводились текстурные исследования путем построения соответствующих полюсных фигур. Повышение энергии электроискровой обработки W сопровождается формированием хаотической ориентацией зерен: отношения I(hkl)/IΣ приближаются к соответствующим данным порошкового материала. Для интерметаллического соединения наблюдается более сложное поведение интенсивностей рефлексов для различных кристаллографических направлений. При этом тенденция к устранению преимущественного направления при кристаллизации с ростом W такая же, как и для алюминиевой фазы.
Рис. 6.
Зависимость отношения интенсивности рефлекса I(hkl) в направлении (hkl) к суммарной интенсивности всех рефлексов данной фазы IΣ для алюминия: ◻ – (111), ▽ – (200), ⚪ – (220).
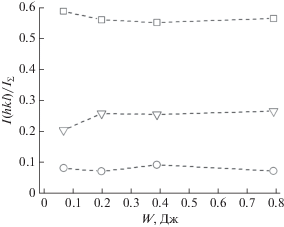
Появление той или иной преимущественной ориентации в покрытиях качественно позволяет объяснить энергетическая модель, предложенная в работе [19] и развитая авторами публикаций [20, 21]. В рамках модели, наличие текстуры соответствующего направления (hkl) связано с соотношением между поверхностной Shkl и деформационной Uhkl энергиями. Значения Shkl могут быть оценены из энергии сублимации LS и числа разорванных связей Nhkl на атом в направлении (hkl) по формуле:
где Z – координационное число, NA – постоянная Авогадро; Ahkl – площадь поверхности, приходящаяся на атом. При этом LS не зависит от кристаллографического направления. Вследствие этого Nhkl – единственный фактор, определяющий значение поверхностной энергии.Энергия деформации Uhkl, обусловленная напряжениями, возникающими в процессе формирования покрытия, может быть оценена из соотношения:
Таким образом, при малых энергиях электроискровой обработки, в нашем случае (рис. 4), величина микродеформаций минимальна, а размер субблоков максимален. Следовательно, значение Nhkl минимально. А так как наблюдается квадратичная зависимость энергии деформации от ε, то она преобладает над поверхностной. Согласно [21], данная ситуация способствует для кубической фазы (алюминия) формированию преимущественной ориентации в направлении (111), что и наблюдалось при W = 0.07 Дж. Уменьшение размера субзерен приводит к росту числа разорванных связей и, естественно, Shkl. Как следствие, постепенно поверхностная энергия будет сравниваться с деформационной. Данный факт будет способствовать хаотической ориентации зерен. В случае преобладания поверхностной энергии будет формироваться (для кубического кристалла) преимущественная ориентация в направлении (200) [21].
ЗАКЛЮЧЕНИЕ
По результатам настоящей статьи можно сделать следующие выводы:
1. Рентгенографическим методом обнаружено присутствие в модифицированном слое следующих фаз: Al, Si, Al2Cu, и Cu3Al. Рост энергии электроискровой обработки сопровождается ростом доли интерметаллических фаз Al2Cu и Cu3Al.
2. Уширение дифракционных линий обнаруженных фаз обусловлено параметрами субструктуры. Отмечается, что увеличение энергии обработки сопровождается ростом величин микродеформаций и размеров субблоков.
3. Остаточные напряжения в алюминии носят растягивающий характер, а в интерметаллическом соединении Al2Cu – сжимающий. Увеличение энергии обработки приводит к росту их значений. Их появление обусловлено градиентом температур при электроискровой обработке, многофазностью рассматриваемых систем и изменениями в удельном объеме.
4. При малых энергиях обработки для алюминиевой фазы отмечается преимущественная ориентация в направлении (111). Повышение энергии электроискровой обработки приводит к хаотическому распределению ориентации зерен кристаллографических фаз алюминия и интерметаллического соединения Al2Cu. Для рассматриваемых кристаллографических направлений появление той или иной текстуры объясняется соотношениями между поверхностной и деформационной энергиями.
Результаты настоящей статьи могут быть использованы при оптимизации процесса электроискровой обработки алюминиевых сплавов и совершенствованию теорий модификации поверхности и создания покрытий различного назначения.
Список литературы
Величко С.А., Сенин П.В., Чумаков П.В. Повышение долговечности поршневых гидроцилиндров с применением электроискровой технологии. Саранск: Изд-во Мордов. ун-та, 2016. 108 с.
Фомин Н.Е., Хасан И.Х., Кяшкин В.М. // Вестник Донского государственного технического университета. 2019. Т. 19. № 2. С. 138. https://doi.org/10.23947/1992-5980-2019-19-2-138-142
Игнатьков Д.А. // Электронная обработка материалов. 2001. № 4. С. 9.
Бурумкулов Ф.Х., Лялякин В.П., Пушкин И.А., Фролов С.Н. // Механизация и электрификация сельского хозяйства. 2001. № 4. С. 23.
Смагин С.И., Власенко В.Д., Мулин Ю.И. // Вычислительные технологии. 2009. Т. 14. № 3. С. 79.
Верхотуров А.Д., Иванов В.И., Коневцов Л.А. // Труды ГОСНИТИ. 2011. Т. 107. № 2. С. 131.
Vlasenko V.D., Kolisova M.V. // Contemporary Engineering Sciences. 2016. V. 9. № 6. P. 249. https://doi.org/10.12988/ces.2016.611
Юрченко Е.В., Иванов В.И. // Труды ГОСНИТИ. 2014. Т. 117. С. 251.
Бецофен С.Я., Петров Л.М., Ильин А.А. // Поверхность. Рентген., синхротр. и нейтрон. исслед. 2004. № 1. С. 39.
Бецофен С.Я., Ашмарин А.А., Лозован А.А., Рябенко Б.В., Луценко А.Н., Мамонов А.М., Молостов Д.Е. // Поверхность. Рентген., синхротр. и нейтрон. исслед. 2016. № 7. С. 33. https://doi.org/10.7868/S0207352816070052
Gnaupel-Herold T. // J. Appl. Cryst. 2012. V. 45. P. 573. https://doi.org/10.1107/S0021889812014252
Wang S., Fan C. // Metals. 2019. V. 9. P. 1037. https://doi.org/10.3390/met9101037
Liu H., Papadimitriou I., Lin F.X., Lorca J.L. // Acta Materialia. 2019. V. 167. P. 121. https://doi.org/10.1016/j.actamat.2019.01.024
Уманский Я.С. Рентгенография металлов. М.: Металлургия, 1967. 235 с.
Пячин С.А., Аблесимов Н.Е., Ягодзинский Д.Л. // Электронная обработка материалов. 2003. № 1. С. 19.
Парканский Н.Я., Кац М.С., Гольдинер М.Г., Гитлевич А.Е. // Электронная обработка материалов. 1982. № 3. С. 20.
Dolgopolov N., Rodin A., Simanov A., Contar’ I. // Materials Letters. 2008. V. 62. P. 4477. https://doi.org/10.3103/S1067821209020114
Гореславец Н.Н., Родин А.О. // Физика металлов и металловедение. 2017. Т. 118. № 11. С. 1183. https://doi.org/10.7868/S0015323017100060
Pelleg J., Zevin L.Z., Lungo S., Croitoru N. // Thin Solid Films. 1991. V. 197. P. 117. https://doi.org/10.1016/0040-6090(91)90225-M
Rauschenbach B., Gerlach J.W. // Cryst. Res. Technol. 2000. V. 35. № 6–7. P. 675. https://doi.org/10.1002/1521-4079(200007)35:6/ 7<675: :AID-CRAT675>3.0.CO;2-7
Zhao J.P., Wang X., Chen Z.Y. // J. Phys. D. 1997. V. 30. P. 5.
Афанасьев В.К., Горшенин А.В., Старостина М.А., Дегтярева И.В., Первакова Е.В. // Металлургия машиностроения. 2010. № 3. С. 30.
Дополнительные материалы отсутствуют.
Инструменты
Поверхность. Рентгеновские, синхротронные и нейтронные исследования