Поверхность. Рентгеновские, синхротронные и нейтронные исследования, 2021, № 11, стр. 45-50
Фазовые превращения и механические свойства двухкомпонентных титановых сплавов после термообработки в двухфазной области (α + интерметаллид) и кручения под высоким давлением
А. С. Горнакова a, *, Б. Б. Страумал a, b, **, Ю. И. Головин c, Н. С. Афоникова a, Т. С. Пирожкова c, А. И. Тюрин c
a Институт физики твердого тела имени Ю.А. Осипьяна РАН
142432 Черноголовка, Россия
b Черноголовский научный центр РАН
142432 Черноголовка, Россия
c Научно-исследовательский институт “Нанотехнологии и наноматериалы” ТГУ им. Г.Р. Державина
392000 Тамбов, Россия
* E-mail: alenahas@issp.ac.ru
** E-mail: straumal@issp.ac.ru
Поступила в редакцию 19.04.2021
После доработки 20.06.2021
Принята к публикации 25.06.2021
Аннотация
Были измерены нанотвердость (H) и модуль Юнга (E) для трех сплавов: Ti–2.5 мас. % Ni, Ti–2 мас. % Cr и Ti–2.2 мас. % Fe, предварительно отожженных в двухфазной области фазовой диаграммы (αTi + интерметаллид) и подвергнутых затем кручению под высоким давлением. Титановый сплав с добавлением никеля показал самые высокие значения H и E, они изменяются равномерно от центра к краю образца, и сплав после кручения под высоким давлением содержит две фазы: α и ω. Нанотвердость сплава Ti–2.5 мас. % Ni вдоль радиуса образца по поверхности меняется незначительно – от минимального 4.8 до максимального значения 5.2 ГПа, как и модуль Юнга (от 121 до 155 ГПа). Максимумы значений H и E приходятся на середину радиуса образца. Сплав Ti–2.2 мас. % Fe ведет себя по-другому: наличие в нем четырех фаз – α, β, ω и TiFe – приводит к сильному разбросу измеряемых значений H и E: от 4.4 до 2.0 ГПа и от 131 до 12 ГПа соответственно. Обработка диаграмм P–h позволила связать нанотвердость материала с его ползучестью.
ВВЕДЕНИЕ
Интерес к титану и его сплавам не уменьшается [1–6]. Благодаря удачному сочетанию механических и технологических характеристик эти материалы имеют широкий спектр применения [7, 8]. Наномеханические свойства материалов очень важны для анализа процессов трения и абразивного износа. Однако закономерности фазовых превращений в двухкомпонентных сплавах на основе α-титана, упрочненных частицами интерметаллических соединений, таких как TiFe, Ti2Ni, TiCr2, под воздействием сдвиговой деформации под высоким давлением в настоящее время изучены слабо и представляют большой интерес. Наличие в системе интерметаллидов, их свойства и структура обусловлены положением компонентов в периодической системе элементов, а также их атомными радиусами [9]. Атомы никеля, железа и хрома могут замещать атомы титана и образовывать с ним ограниченные твердые растворы. В работе [10] был подробно исследован интерметаллид TiFe, который занимает особое место среди гидридообразующих сплавов, так как он способен образовывать гидриды, характеризующиеся давлением диссоциации, близким к атмосферному при комнатной температуре. Интерметаллическое соединение TiFe обладает кубической структурой. Благодаря сильному упрочняющему действию железо используется в некоторых титановых сплавах как легирующая добавка обычно в количествах 0.5–1.5%, хотя известен сплав на основе β-фазы, содержащий 5% Fe [11]. Интерес к интерметаллидам в системе Ti−Ni вызван их многими полезными технологическими свойствами, такими как пластичность, деформируемость в широком интервале температур, высокая механическая прочность и эффект памяти формы [12]. В системе Ti−Ni существуют три интерметаллида: TiNi, Ti2Ni и TiNi3 [13]. Интерметаллид Ti2Ni образуется по перитектической реакции и имеет кубическую структуру. Упрочняющий эффект легирования титана никелем при комнатной температуре невелик [11]. По влиянию на полиморфное превращение титана хром относится к сильным β-стабилизаторам. Растворимость хрома в α-титане не превышает 0.5%. Хром обеспечивает в сплавах с титаном высокую прочность при хорошей пластичности и повышает эффективность упрочняющей термообработки [11]. Однако при повышенных температурах происходит эвтектоидный распад β-фазы, сопровождающийся выделением TiCr2 и вследствие этого потерей пластичности. При температурах ниже 1150°С TiCr2 имеет гранецентрированную кубическую решетку. Интерметаллид TiCr2 отличается высокой хрупкостью. Присутствие его в сплавах, даже в небольших количествах, резко снижает их пластичность. Целью работы было исследовать влияние кручения под высоким давлением и доли интерметаллида на фазовые превращения, нанотвердость и модуль Юнга в сплавах Ti–2.5 мас. % Ni, Ti–2 мас. % Cr и Ti–2.2 мас. % Fe.
МЕТОДЫ
Двухкомпонентные титановые сплавы Ti–2.5 мас. % Ni, Ti–2 мас. % Cr и Ti–2.2 мас. % Fe были получены из титана марки ТИ-1 (иодидный титан 99.98%), хрома (99.99%), железа (99.97%) и никеля (99.95%). Сплавы были приготовлены в индукционной печи в атмосфере чистого аргона. Полученные слитки сплавов были структурно и химически однородными по всей длине и толщине. Из цилиндрических слитков сплавов диаметром 10 мм были нарезаны шайбы толщиной 0.7 мм. Затем образцы запаивали в кварцевые ампулы и отжигали в вакууме при остаточном давлении 4 × 10–4 Па. После отжига образцы закаливали в воде вместе с ампулой. Отжиг сплавов Ti–Ni и Ti–Cr проводился при температуре 600°С (2774 ч), а сплава Ti–Fe – при 470°С (673 ч). Полученные образцы подвергали кручению под высоким давлением (КВД) при комнатной температуре при 7 ГПа, скорости деформации 1 об./мин и 5 об. плунжера. После КВД толщина образцов составила 0.35 мм. Нанотвердость поверхности образцов измеряли на приборе TI-950 Triboindenter, оснащенном индентором Берковича. Измерения проводили в центре (R0), на середине радиуса (R1/2) и около края (R1) образцов, скорость нагружения была постоянной: dP/dt = 40 мН/с. Перед измерениями поверхность образцов полировали алмазной пастой с зернистостью 1 мкм. Численные значения нанотвердости (Н) и модуля Юнга (Е) исследованных образцов рассчитывали по методике Оливера–Фарра [14–16] на основе характерных диаграмм P–h (рис. 1), где Р – величина нагрузки, h – глубина отпечатка. Исследования проводили при комнатной температуре и постоянной максимальной нагрузке, прикладываемой к индентору: Рmax = 200 мН. Значения Н и Е получали путем усреднения результатов, полученных по 12 независимым экспериментам. Фазовый анализ образцов проводили с использованием рентгеновского дифрактометра Siemens D-500 (CuKα1-излучение). Параметры решетки рассчитывали с помощью программы PowderCell для Windows V.2.4.08.03.2000. Для определения химического состава образцов был использован растровый электронный микроскоп высокого разрешения Supra 50VP с системой микроанализа INCA Energy+, оснащенный приставкой для энергодисперсионного микроанализа Oxford Instruments.
РЕЗУЛЬТАТЫ И ИХ ОБСУЖДЕНИЕ
Фазовый состав образцов до и после КВД
Фазовый состав трех исследованных сплавов представлен в табл. 1. Основной объем материала приходится на фазу α-Ti. По сравнению с параметрами решетки α-фазы чистого титана в двухкомпонентных сплавах параметр решетки а меньше, а, следовательно, отношение с/а больше. Ячейка в ГПУ-решетке в двухкомпонентных сплавах “сжата”, т.е. титан обогащен вторым компонентом, поэтому период решетки уменьшился. Фазовый состав после отжига в трех исследованных сплавах отличается долей и типом структур интерметаллида.
Таблица 1.
Параметры решеток, фазы и их содержание в сплавах после термообработки в области αTi + интерметаллид
Сплав | Область фазовой диаграммы | αTi | TiMe | ||
---|---|---|---|---|---|
объемная доля, % | а, с, нм | объемная доля, % | а, нм | ||
Ti–2.5 мас. % Ni | αTi + Ti2Ni | 96 | 0.2944, 0.4688 | 4 | 1.1318 |
Ti–2 мас. % Cr | αTi + TiCr2 | 98 | 0.2950, 0.4689 | 2 | 0.6933 |
Ti–2.2 мас. % Fe | αTi + TiFe | 97 | 0.2950, 0.4687 | 3 | 0.2978 |
Чистый Ti | – | – | 0.2955, 0.4686 | – | – |
В табл. 2 представлены данные об объемной доле каждой фазы и параметры решеток этих фаз после отжига и КВД, полученные со всей поверхности образцов. Все три образца отличаются фазовым составом. В титановом сплаве с никелем присутствуют только две фазы: α и ω. В сплаве с хромом был найден еще и интерметаллид. Легирование титана железом в сочетании с КВД приводит к образованию четырех фаз: α, β, ω и TiFe. Возможно, большая доля интерметаллида в сплаве после отжига приводит к более равномерному распределению материала, а, следовательно, и к близким значениям нанотвердости и модуля Юнга после КВД в центре и на краю образца.
Таблица 2.
Параметры решеток, фазы и их содержание в сплавах после термообработки и кручения под высоким давлением
Сплав | αTi | βTi | ωTi | TiMe | ||||
---|---|---|---|---|---|---|---|---|
объемная доля, % | а, с, нм | объемная доля, % | а, нм | объемная доля, % | а, с, нм | объемная доля, % | а, нм | |
Ti–2.5 мас. % Ni | 37 | 0.2951, 0.4688 | – | – | 63 | 0.4625, 0.2812 | – | – |
Ti–2 мас. % Cr | 43 | 0.2950, 0.4690 | – | – | 55 | 0.4628, 0.2813 | 2 (TiCr2) | 0.6943 |
Ti–2.2 мас. % Fe | 8 | 0.2950, 0.4690 | 16 | 0.3255 | 76 | 0.4626, 0.2814 | ≥2 (TiFe) | 0.2979 |
Чистый Ti | – | 0.2959, 0.4690 | – | – | – | 0.4627, 0.2830 | – | – |
Нанотвердость сплавов
Для сплава Ti–Ni значения нанотвердости Н изменялись слабо – от 4.8 ± 0.1 в центре до 5.0 ± ± 0.1 ГПа на краю образца (рис. 2), значения модуля Юнга изменялись от 148 до 121 ГПа. Для сплавов Ti–Fe и Ti–Cr разброс значений нанотвердости и модуля Юнга был более широким. Рассмотрим более подробно три области измерения образцов: при R0, R1/2 и R1 для каждого сплава. Значения нанотвердости в центральной части образцов сплавов с никелем и железом различаются на 1.3 ± 0.2 ГПа. Поскольку известно, что центральная область образца меньше всего подвергается деформации, можно предположить, что изначально сплав Ti–Ni был более твердым, чем Ti–Fe. На середине радиуса разброс значений нанотвердости у трех сплавов самый низкий по образцу – 0.8 ГПа. Эта область подвергается более интенсивной деформации, которая “выравнивает” нанотвердость образцов. На краю образцов наблюдается самый сильный разброс значений нанотвердости – 2.9 ГПа. Обычно центральная часть образца и ее край не используются для проведения дальнейших исследований, но все же хотелось бы понять, какие причины могут привести к такому разбросу значений. Первое предположение: размер канавки под плунжером 0.3 мм, а толщина исходного образца варьировалась от 0.6 до 0.7 мм. Возможно, вариации толщины исходных образцов, влияющие на степень сдвиговой деформации, сыграли отрицательную роль и привели к разбросу значений на краях. Второе предположение: это недостаточно качественная подготовка поверхности образцов перед измерениями, которая привела к разбросу данных. Обе эти причины возможны, но, так как КВД и подготовка поверхности проводились однообразно, ошибка должна быть одинаковой при измерениях. Есть другое более существенное предположение, которое не проверялось в настоящей работе, – это фазовый состав образцов в трех областях и микроструктурные составляющие, такие как размер или доля фаз или размер частиц фаз или доля межфазных границ и “выделение” частиц интерметаллида на границах зерен. Эти предположения открывают возможности дальнейших, более подробных исследований.
Рис. 2.
Зависимость нанотвердости сплавов Ti–2.5 мас. % Ni (квадраты), Ti–2.2 мас.% Fe (треугольники) и Ti–2 мас. % Cr (кружки), предварительно отожженных и подвергнутых кручению под высоким давлением, от области измерения вдоль поверхности образца: в центре (R0), на середине радиуса (R1/2) и на крае (R1).
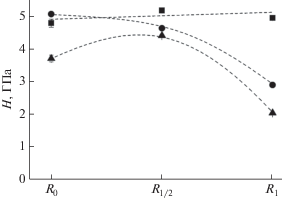
Модуль Юнга сплавов
Рассмотрим измеренные значения модуля Юнга (Е) (рис. 3). Видно, что в центральной части образцов различие в значениях Е сплавов меньше 20 ГПа, в то время как на краях разброс более 100 ГПа. Можно сделать предположение, что разброс обусловлен тем, что модуль упругости является более чувствительной характеристикой, и наличие мелких неровностей на поверхности, границах зерен может внести свои коррективы в механизмы пластичности. Но однообразность подготовки образцов исключает данное предположение. Сочетание α- и ω-фаз дает самые высокие значения нанотвердости и модуля Юнга, и, что немаловажно, равномерное распределение этих значений от центра к краю образца в сплаве Ti–Ni. В литературе подобный разброс значений H и E не обсуждался [17–20], поэтому полученные данные представляют несомненный интерес.
Рис. 3.
Зависимость модуля Юнга для сплавов Ti–2.5 мас. % Ni (квадраты), Ti–2.2 мас. % Fe (треугольники) и Ti–2 мас. % Cr (кружки) от области измерения вдоль поверхности образца: в центре (R0), на середине радиуса (R1/2) и на крае (R1). Образцы были предварительно отожжены и подвергнуты кручению под высоким давлением.
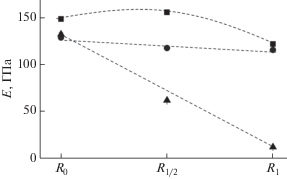
Особенности диаграмм P–h
На записанных во время эксперимента диаграммах P–h (рис. 1) было отмечено сильное отличие на участках Δhcr, которые отвечают за приращение глубины отпечатка при ползучести. Рассчитав значения Δhcr из рис. 1, мы построили зависимость приращения глубины отпечатка (Δhcr) при ползучести от нанотвердости для исследованных сплавов после КВД (рис. 4). Полученная зависимость демонстрирует, как неравномерно перемешиваются компоненты в образцах при КВД. Сплав с никелем имеет одинаковые значения Δhcr вдоль всего образца, в то время как для сплавов с хромом и железом значения Δhcr очень сильно различаются. Другая особенность заключалась в том, что для сплава с хромом при одном и том же значении Δhcr наблюдались разные значения нанотвердости. Такое поведение может быть обусловлено неоднородностью самого образца, т.е. индентор попадал либо на границу зерен, либо на межфазную границу, либо в другую фазу.
ЗАКЛЮЧЕНИЕ
Были измерены нанотвердость и модуль Юнга для сплавов Ti–2.5 мас. % Ni, Ti–2 мас. % Cr и Ti–2.2 мас. % Fe, предварительно отожженных в двухфазной области (αTi + интерметаллид) и подвергнутых кручению под высоким давлением. Сплав Ti–2.5 мас. % Ni с большим содержанием фазы интерметаллида показал более высокие значения нанотвердости и модуля Юнга после КВД. Наноиндентирование является подходящим инструментом для изучения микронеоднородностей структуры и состава, возникающих при КВД.
Список литературы
Asl M.S., Delbari S.A., Azadbeh M. et al. // J. Mater. Res. Technol. 2020. V. 9. P. 10647. https://doi.org/10.1016/j.jmrt.2020.07.066
Moshokoa N., Raganya L., Obadele B.A., Machaka R., Makhatha M.E. // Int. J. Adv. Manufact. Technol. 2020. V. 111 P. 1237. https://doi.org/10.1007/s00170-020-06208-7
Verestiuc L., Spataru M.-C., Baltatu M.S. et al. // J. Mechan. Behavior Biomed. Mater. 2021. V. 113. P. 104 198. https://doi.org/10.1016/j.jmbbm.2020.104198
Deng G., Bhattacharjee T., Chong Y. et al. // J. Alloys Compd. 2020. V. 822. P. 153604. https://doi.org/10.1016/j.jallcom.2019.153604
Chong Y., Deng G., Shibata A., Tsuji N. // Adv. Eng. Mater. 2019. V. 21. P. 1 900 607. https://doi.org/10.1002/ADEM.201900607
Kao Y.L., Tu G.C., Huang C.A., Liu T.T. // Mater. Sci. Eng. A. 2005. V. 398. P. 93.https://doi.org/10.1016/j.msea.2005.03.004
Veiga C., Davim J.P., Loureiro A.J.R. // Rev. Adv. Mater. Sci. 2012. V. 32. P. 133.
Lütjering G. Williams J.C. Titanium. 2nd ed. Berlin: Springer, 2007.
https://bigenc.ru/chemistry/text/2014495 (Большая российская энциклопедия).
Задорожный М.Ю. Механосинтез и водородсорбционные свойства сплавов на основе нанокристаллического интерметаллического соединения TiFe: Автореферат дис. … канд. т. н.: 05.16.09. Москва: МИСиС, 2013. 24 с.
https://www.libmetal.ru/titan/titan%203.htm (Справочник по цветным металлам).
Куликова Т.М., Моисеев Г.К., Ильиных Н.И. // Известия Челябинского науч. центра. 2001. Вып. 1. С. 41.
Murray J.L. // Bull. Alloy Phase Diagr. 1981. V. 2(3). P. 320.
Oliver W.C., Pharr G.M. // J. Mater. Res. 2004. V. 19(1). P. 3. https://doi.org/10.1557/jmr.2004.19.1.3
Golovin Yu.I., Tyurin A.I., Aslanyan E.G., Pirozhkova T.S., Vasyukov V.M. // Phys. Solid State. 2017. V. 59. № 9. P. 1803. https://doi.org/10.1134/S1063783417090104
Golovin Yu.I., Tyurin A.I., Iunin Yu.L. // Dokl. Phys. 2003. V. 48. № 9. P. 505. https://doi.org/10.1134/1.1616061
Deng G., Bhattacharjee T., Chong Y. et al. // J. Alloys Compd. 2020. V. 82. P. 153604. https://doi.org/10.1016/j.jallcom.2019.153604
Nie M., Wang C.T., Qu M. et al. // J. Mater. Sci. 2014. V. 49. P. 2824. https://doi.org/10.1007/s10853-013-7988-z
Gornakova A.S., Straumal A.B., Khodos I.I., Gnesin I.B., Mazilkin A.A., Afonikova N.S., Straumal B.B. // J. Appl. Phys. 2019. V. 125. P. 082522. https://doi.org/10.1063/1.5053937
Straumal B.B., Korneva A., Kilmametov A.R., Litynska-Dobrzynska L., Gornakova A.S., Chulist R., Karpov M.I., Zieba P. // Materials. 2019. V. 12. P. 426. https://doi.org/10.3390/ma12030426
Дополнительные материалы отсутствуют.
Инструменты
Поверхность. Рентгеновские, синхротронные и нейтронные исследования