Поверхность. Рентгеновские, синхротронные и нейтронные исследования, 2021, № 12, стр. 12-17
Нанопроволоки из меди как катализатор для окисления CO
Д. В. Панов a, В. Ю. Бычков b, Ю. П. Тюленин b, Д. Л. Загорский a, *, В. М. Каневский a, И. С. Волчков a
a ФНИЦ “Кристаллография и фотоника” РАН
119333 Москва, Россия
b ФИЦ химической физики им. Н.Н. Семенова РАН
119991 Москва, Россия
* E-mail: dzagorskiy@gmail.com
Поступила в редакцию 20.05.2021
После доработки 25.06.2021
Принята к публикации 30.06.2021
Аннотация
Показано, что медные пленки с расположенными на них медными нанопроволоками демонстрируют усиление каталитического эффекта при окислении окиси углерода. Проведено сравнение нанопроволок различных типов – цилиндрических, конических, массивов между двумя поверхностями. Выявлено, что наибольший эффект (возрастание степени окисления на 60–70%) достигается в случае цилиндрических нанопроволок. Эффект наблюдается при достаточно низких температурах 200–350°С. Исследования методом растровой электронной микроскопии выявили значительное утолщение нанопроволок после катализа за счет образования оксидов. В результате элементного анализа на их поверхности обнаружены кислород и углерод. Методом рентгенофазового анализа установлено образование оксидов двух типов при катализе. Также показано, что при длительном проведении катализа происходит деградация массива нанопроволок. Последующий стандартный процесс восстановления не приводит к возврату нанопроволок в исходную форму.
ВВЕДЕНИЕ
Работа посвящена изучению возможности применения одномерных наноструктур в каталитическом окислении окиси углерода. Окисление СО чрезвычайно важно – например, в доочистке автомобильных выхлопных газов. Для этой цели в настоящее время используют коммерческий катализатор Pt–Pd–Rh, который превращает CO в CO2 практически со 100%-ным выходом при температуре свыше 400°С [1–3]. Однако для широкого применения представляют интерес более дешевые катализаторы, способные работать при более низких температурах [4, 5].
Медьсодержащие системы демонстрируют каталитическую активность в различных гетерогенных реакциях, включая реакцию сдвига водяного газа [6, 7], окисление метанола до формальдегида [8] и окисление СО [9, 10]. В [11–13] массивы медных нанопроволок были получены методом гидротермального синтеза и применялись в катализе электрохимических реакций в жидкой фазе. Так, авторы [11, 12] показали эффективность использования медных нанопроволок в процессах электрокаталитического восстановления окиси и двуокиси углерода. В [13] их успешно применяли для каталитического гидролиза борогидрида натрия (для получения водорода).
Фундаментальные вопросы гетерогенного катализа на медных катализаторах изучали неоднократно [14–19]. Для достижения высокой каталитической активности обычно наносят медьсодержащий компонент на термостойкий носитель с большой площадью поверхности. Однако такие катализаторы имеют и некоторые недостатки, а именно высокое сопротивление газовому потоку и низкую скорость теплопереноса. Массивные металлические фольги, напротив, оказывают низкое сопротивление обтекающему потоку и отличаются большой скоростью теплопереноса, но, как правило, обладают низкой каталитической активностью из-за малой удельной поверхности. Поэтому представляет интерес разработка комбинированных структур, поверхность которых искусственно увеличена.
Одним из способов увеличения площади поверхности является выращивание на ней массива одномерных наноматериалов [20]. Такие материалы перспективны для применения в различных областях техники в качестве эмиттеров, элементов спинтроники, поверхностей для теплоотвода, датчиков и других устройств [21–24]. Их уникальные особенности – высокое отношение площади поверхности к объему в сочетании с электропроводностью и высокой кривизной острий нанопроволок – предполагают возможность применения таких структур в катализе.
Массивы нанопроволок могут быть получены методом матричного синтеза – заполнением медью пор в ростовой матрице с требуемыми параметрами поровой структуры [25–27]. Такого заполнения достигают путем электроосаждения металла из раствора его соли. Метод позволяет синтезировать множество идентичных нанопроволок контролируемой формы [28]. Настоящая работа посвящена исследованию возможностей создания структур на основе нанопроволок для каталитического окисления CO при наименьшей температуре. Задачей работы было получение каталитических пленок из меди с расположенными на них медными нанопроволоками, изучение каталитической активности полученных массивов геометрически различных нанопроволок и их изменений в ходе каталитического процесса.
ЭКСПЕРИМЕНТЫ И РЕЗУЛЬТАТЫ
Получение образцов и исследование их структуры
В работе исследованы наноструктуры трех типов. Схема их получения, разбитая на отдельные этапы, приведена на рис. 1. Во всех случаях процесс начинался с приготовления матрицы на основе полимерной пленки, облученной тяжелыми ионами (рис. 1, этап 1).
Рис. 1.
Этапы получения наноструктур трех типов и их схематическое изображение (слева – матрицы с цилиндрическими порами и полученные на их основе структуры с цилиндрическими нанопроволоками, справа – матрицы с коническими порами и структуры на их основе): исходная матрица – этап 1; травление (этапы 2, 3); металлизация тонким слоем меди (этапы 4, 5); металлизация толстым слоем меди (этапы 6, 7); рост конических нанопроволок и получение конических структур (этап 8); рост нанопроволок и получение структур цилиндрических нанопроволок (этапы 9, 10); рост “второго” медного слоя на поверхности мембраны и получение структур типа “сэндвич” (этапы 11, 12).
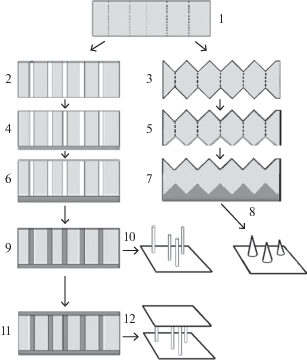
Матрицы. Дальнейшее проведение процесса было направлено либо на получение цилиндрических нанопроволок или структур типа “сэндвич” (этапы 2, 4, 6, 9, 10 и 11, 12), либо на получение конических нанопроволок (этапы 3, 5, 7, 8).
В первом случае облученную полимерную пленку травили в водном растворе щелочи для получения пор цилиндрической формы (рис. 1, этап 2). В ряде случаев брали готовые матрицы – трековые мембраны из полиэтилентерефталата (ПЭТФ) толщиной 12 и 23 мкм с диаметрами пор от 30 до 600 нм и с плотностями пор от 1 × 108 до 1.2 × 109 см–2 (производство ОИЯИ, г. Дубна). Во втором случае (для получения конусовидных структур) использовали облученный полимер (ПЭТФ) с плотностью треков 4 × 107 см–2 (ОИЯИ), в котором при специальном травлении латентных треков создавали поры конической формы (рис. 1, этап 3). Для этого использовали двунормальный раствор щелочи NaOH в водно-спиртовой смеси. Концентрация этилового спирта изменялась в пределах 25–75%. Известно, что, изменяя эту концентрацию, можно варьировать “конусность пор” [22]. Процесс травления “на конус” проводили при комнатной температуре.
Металлизацию поверхности матрицы осуществляли для создания проводящего контактного слоя. Этот же слой после получения наноструктур и удаления ростовой матрицы служил основанием для массива нанопроволок.
В обоих случаях на первой стадии металлизации на одну из поверхностей мембраны методом термического распыления на приборе ВУП-4 наносили тонкий контактный слой меди (рис. 1, этапы 4, 5). На второй стадии этот тонкий слой усиливали – на него наносили более толстый слой методом осаждения в гальванической ванне (рис. 1, этап 6). Использовали электролит следующего состава: CuSO4·5H2O – 200 г/л; H2SO4 – 16 г/л. В качестве источника применяли потенциостат-гальваностат Ellins P-2X. Осаждение проводили при потенциале 0.2–0.6 В.
Электроосаждение нанопроволок. В обоих случаях осуществляли гальваническое осаждение меди в поры металлизированной мембраны с использованием вышеописанного электролита на основе сульфата меди. Процесс проходил в гальванической ячейке при напряжении 0.4 В до полного заращивания пор матриц металлом, однако детали осаждения в трех случаях были различными.
Типы медных наноструктур. Как описано выше, были получены медные наноструктуры трех типов на медной подложке (рис. 1): цилиндрические нанопроволоки, конусовидные структуры (короткие нанопроволоки конической формы), структуры типа “сэндвич” (нанопроволоки, находящиеся между двух слоев-подложек).
Цилиндрические нанопроволоки (рис. 1, этап 10) были получены стандартным способом – гальваническим заполнением медью сквозных цилиндрических пор мембраны [25] (рис. 1, этап 9).
Структура типа “сэндвич” (рис. 1, этап 12) была получена “на базе” структуры с цилиндрическими порами путем “доращивания” нанопроволок. Осаждаемый металл “выходил” из пор полимера (происходил так называемый “перерост”). Продолжение гальванического процесса приводило к формированию сплошного медного слоя на “второй” (“верхней”) стороне матрицы (рис. 1, этап 11). Таким образом, обе поверхности матрицы были покрыты толстым слоем меди. После удаления ростовой матрицы структура представляла собой два медных слоя, между которыми находился массив параллельных нанопроволок (“сэндвич”). Данная структура вызывает интерес ввиду ее большей прочности и большей площади поверхности (по сравнению со структурой с цилиндрическими нанопроволоками).
Поскольку конические структуры (рис. 1, этап 8) получают в матрице с несквозными, а с конусными порами, в этом случае и металлизация, и заполнение пор происходят “с одной стороны” мембраны – “нижней” (рис. 1, этап 7). При получении конических нанопроволок ставили задачу уменьшения радиуса кривизны острия. Был подобран оптимальный состав электролита с добавлением блескообразователя ЦКН-74. В результате уменьшался размер кристаллитов меди, благодаря этому образовывались более острые “кончики” конусов-острий.
Время роста образцов подбирали экспериментально. Оно составляло 600 с для цилиндрической структуры, 500 с для конической структуры и 8000 с для структуры “сэндвич”. После получения образцов во всех случаях матрицу удаляли (вытравливание полимера в растворе щелочи).
Микроскопия. Электронно-микроскопическое исследование полученных образцов было проведено с помощью растрового электронного микроскопа (РЭМ) JEOL JCM-6000PLUS в режиме детектирования вторичных электронов при ускоряющем напряжении 15 кВ. Примеры РЭМ-изображений структур трех типов представлены на рис. 2: цилиндрические нанопроволоки диаметром 100 нм (рис. 2а), конические нанопроволоки в виде своеобразных пирамидок с диаметром основания 200 нм и высотой 300 нм (рис. 2б) и структура “сэндвич” с диаметром нанопроволок 300 нм (рис. 2в).
Изучение каталитической активности
Методика определения активности. Каталитическую активность оценивали путем измерения концентрации СО2 в газовой смеси после реакции. Схема проточной установки показана на рис. 3. Установка содержит трубчатый кварцевый реактор диаметром 6 мм, систему подачи и отвода газа, регулятор расхода газа, программируемую печь. Состав исходной газовой смеси СО(2%)–О2(5%)–Не. Скорость потока составляла 20 мл/мин. В реактор загружали образцы – медные пленки с медными нанопроволоками размером 16 × 5 мм. Затем часть газовой смеси отбирали с помощью петли для хроматографического анализа на хроматографе “Хроматек-2000” (рис. 3). Образцы ступенчато нагревали в интервале температур 200–450°С. Состав газа определяли через 5 мин после установления температуры.
Изучение активности образцов. На первом этапе было проведено сравнение активности образцов трех типов. Было обнаружено, что каталитический эффект проявился на всех типах структур. Структуры с коническими остриями дали увеличение каталитического эффекта в среднем на 20%, структуры “сэндвич” – на 40%. Наибольший эффект, до 70–80%, был получен на структурах с цилиндрическими нанопроволоками. Дальнейшие результаты представлены для этого типа каталитических подложек.
Для изучения влияния параметров структур были приготовлены образцы пяти типов. Первый (контрольный) – подложки из плоской медной фольги, остальные четыре – медные подложки с цилиндрическими нанопроволоками различных диаметров: образец 2 – диаметр 400 нм и длина 12 мкм, образец 3 – диаметр 30 нм и длина 12 мкм, образец 4 – диаметр 300 нм и длина 23 мкм, образец 5 – диаметр 100 нм и длина 12 мкм. На рис. 4 показаны зависимости концентрации СО2 от температуры для образцов пяти вышеперечисленных типов.
Рис. 4.
Образование СО2 при взаимодействии с потоком смеси СО(2%)–О2(5%)–Не (20 мл/мин) образцов меди (16 × 5 мм): 1 – обычная медная фольга; 2–5 – медные подложки с цилиндрическими нанопроволоками: диаметр 400 нм, длина 12 мкм (2); диаметр 30 нм, длина 12 мкм (3); диаметр 300 нм, длина 23 мкм (4); диаметр 100 нм, длина 12 мкм (5).
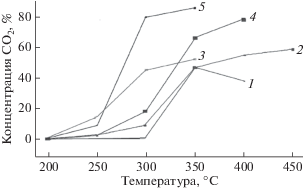
Анализ результатов свидетельствует о том, что во всех случаях концентрация СО2 в образцах с нанопроволоками после катализа превышает величины, зафиксированные для простой фольги в тех же условиях. Сравнение образцов 2 и 4 показывает, что при близких диаметрах нанопроволок каталитическая активность возрастает с увеличением их длины от 12 до 23 мкм. Сравнение образцов 2, 3 и 5 с нанопроволоками одинаковой длины (12 мкм), но разного диаметра (400, 30 и 100 нм соответственно) свидетельствует о том, что при максимальной толщине проволок (400 нм) образец имеет самую низкую каталитическую активность. Самую высокую активность при температуре 250°С имел образец 3 с проволоками диаметром 30 нм, а при температурах 300–350°С гораздо более активным был образец 5 (диаметр 100 нм). Активность практически не менялась в течение первого часа, но в последующие 30–60 мин она значительно падала.
Исследования поверхности
Микроскопия. Методом РЭМ на этом этапе была изучена модификация поверхности при проведении каталитических реакций. На рис. 5 представлены РЭМ-изображения поверхностей – исходных, после катализа и после восстановления. Видно, что после реакции катализа (рис. 5б) нанопроволоки с исходным диаметром около 300 нм в целом сохраняют свою форму и структуру, но их диаметр сильно увеличивается до 600–800 нм. Очевидно, они покрываются слоем оксида.
Рис. 5.
РЭМ-изображение цилиндрических нанопроволок (указан исходный диаметр): а – исходные (100 нм); б – после реакции катализа (300 нм); в – восстановленные водородом после катализа (100 нм).
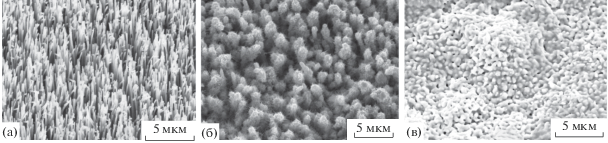
Так как утолщение нанопроволок в ходе катализа вызывается окислением меди, представляло интерес проверить, не приведет ли химическое восстановление оксидов меди к обратному эффекту. С этой целью окисленный образец после катализа восстановили в потоке водорода при нагреве до 300°С. Восстановление проводили в термовесах Setaram SETSYS Evolution в режиме линейного повышения температуры, и при температуре 300°С происходило резкое уменьшение массы, т.е. восстановление оксида меди с выделением воды. Анализ поверхности (рис. 5в) показывает, что после восстановления в водороде образец не возвращается в исходное состояние, а формируется хаотическая микропористая поверхность с видимыми остаточными структурами с нанопроволоками.
Элементный анализ поверхности. Одновременно с микроскопией поверхности был проведен энергодисперсионный рентгеноспектральный микроанализ. Результаты анализа поверхности образцов в трех состояниях приведены в табл. 1. Видно, что в процессе катализа на поверхности заметно увеличивается концентрация углерода и кислорода. Кислород удаляется с поверхности в процессе восстановления. Очевидно, что обнаруженное изменение формы нанопроволок на поверхности (утолщение) происходит за счет образования оксида на поверхности медной подложки. Отметим, что при восстановлении кислород удаляется с поверхности, однако углерод остается.
Таблица 1.
Состав образцов, ат. %
Элемент | Исходный | После катализа | Восстановленный |
---|---|---|---|
C | 4.03 | 8.73 | 21.80 |
O | 2.29 | 66.55 | 3.71 |
Cu | 93.68 | 24.72 | 74.50 |
Рентгенофазовый анализ. Исследования проводили с помощью рентгеновского дифрактометра X’pert pro PANalytical (излучение CuKα, λ = 1.54 нм) при ускоряющем напряжении 40 кВ и токе 40 мА. Полученная дифрактограмма образца с нанопроволоками диаметром 100 нм до и после катализа представлена на рис. 6. На обеих дифрактограммах видны четкие линии меди. Анализ полученной дифрактограммы также показывает, что в процессе катализа на поверхности меди образуются два оксида – CuO и Cu2O. Эти данные коррелируют с результатами элементного анализа. Отметим, что образование оксидов на поверхности медьсодержащих нанопроволок при нагреве или при длительном выдерживании на воздухе отмечено в [23].
ЗАКЛЮЧЕНИЕ
В работе продемонстрировано, что использование пленок с массивом медных нанопроволок значительно усиливает каталитический эффект при окислении окиси углерода. Изучены образцы разных конфигураций и показано, что наибольший эффект дают традиционно используемые нанопроволоки цилиндрической формы. При катализе происходит изменение поверхности – образование оксида и гемиоксида меди, а также осаждение на поверхность нанопроволок углерода. Установлено, что изменения после катализа являются необратимыми – восстановление не приводит к исходной структуре.
Список литературы
Гордон Е., Карабулин А., Матюшенко В., Ростовщикова Т. // Теоретическая и экспериментальная химия. 2016. Т. 52. № 2. С. 74.
Rostovshchikova T.N. Smirnov V.V., Kozhevin V.M., Yavsin D.A., Zabelin M.A., Yassievich I.N., Gurevich S.A. // Appl. Catalysis. A. 2005. V. 296. P. 70.
Gordon E.B., Karabulin A.V., Matyushenko V.I. // Gold Bull. 2015. V. 52. № 2. P. 119.
Thomas Ch.L. Catalytic Processes and Proven Catalysts. N.Y.–London: Academic Press, 1970. 386 p.
Козлов Д., Трофименко Ю., Дубова В. // Катализ в промышленности. 2006. № 6. С. 19.
Lin J.H., Guliants V. // ChemCatChem. 2011. B. 3. S. 1426.
Caldas P.C.P., Gallo J.M.R., Lopez-Castillo A. // ACS Catal. 2017. V. 7. P. 2419.
Wachs I.E., Madix R.J. // J. Catal. 1978.V. 53. P. 208.
Szanyi J., Goodman D.W. // Cat. Lett. 1993. V. 21. P. 165.
Jernigan G.G., Somorjai G.A. // J. Catal. 1994. V. 147. P. 567.
Zhang H., Zhang Y., Li Y., Ahn S., Palmore G.T.R. // Nanoscale. 2019. V. 11. P. 25.
Wang Y., Zhu Y., Niu C. // J. Phys. Chem. Solids. 2020. V. 144. P. 109507.
Hashimi A., Nohan M., Chin S., Khiew P., Zakaria S. // Nanomaterials. 2020. V. 10. P. 6.
Bychkov V.Y., Tulenin Y.P., Gorenberg Ya. // Reac. Kinet. Mech. Cat. 2020. V. 129. P. 57.
Domagala M.E., Campbell C.T. // Cat. Lett. 1991. V. 9. P. 65.
Xu F., Mudiyanselage K., Baber A., Soldemo M. // J. Phys. Chem. 2014. V. 118. P. 15902.
Eren B., Lichtenstein L., Wu C.H., Bluhm H. // J. Phys. Chem. 2015. V. 119. P. 14669.
Bikaljevic D., Rameshan R., Köpfle N., Götsch T., Mühlegger E., Schlögl R., Penner S., Memmel N., Klötzer B. // Appl. Catal. A. 2019. V. 572. P. 151.
Svintsitskiy D.A., Kardash T.Y., Stonkus O.A., Slavinskaya E.M., Stadnichenko A.I., Koscheev S., Chupakhin A.P., Boronin A.I. // J. Phys. Chem. 2013. V. 117. P. 14588.
Елисеев А., Лукашин А. Функциональные наноматериалы. М.: Физматлит, 2010. 456 с.
Анищик В.М. Наноматериалы и нанотехнологии. Минск: Изд-во БГУ, 2008. 375 с.
Oleinikov V., Zagorski D., Bedin S., Volosnikov A. // Rad. Meas. 2008. V. 43. P. 635.
Kozhina E.P., Bedin S.A., Nechaeva N.L., Podoynitsyn S.N., Tarakanov V.P., Andreev S.N., Grigoriev Y.V., Naumov A.V. // Appl. Sci. 2021. V. 11. № 4. P. 1375.
Кожина Е.П., Андреев С.Н., Тараканов В.П., Бедин С.А., Долуденко И.М., Наумов А.В. // Изв. РАН. Сер. физ. 2020. Т. 84. № 12. С. 1725.
Martin C.R. // Science. 1994. V. 23. № 266. P. 1961.
Chakarvarti S.K., Vetter J. // Nucl. Instrum. Methods Phys. Res. 1991. V. 62. Iss. 1. P. 109.
Vetter J., Spohr R. // Nucl. Instrum. Methods Phys. Res. 1993. V. 79. Iss. 1–4. P. 691.
Жигалина О.М., Долуденко И.М., Хмеленин Д.Н., Загорский Д.Л., Бедин С.А., Иванов И.М. // Кристаллография. 2018. Т. 63. № 3. С. 463.
Дополнительные материалы отсутствуют.
Инструменты
Поверхность. Рентгеновские, синхротронные и нейтронные исследования