Поверхность. Рентгеновские, синхротронные и нейтронные исследования, 2021, № 2, стр. 73-77
Влияние поверхностного натяжения на диффузию углерода в наночастицу катализатора
С. В. Булярский a, *, Е. П. Кицюк b, **, А. В. Лакалин a, А. А. Павлов a, Р. М. Рязанов b
a Институт нанотехнологий микроэлектроники РАН
119991 Москва, Россия
b Научно-производственный комплекс “Технологический центр”
124498 Москва, Россия
* E-mail: bulyar2954@mail.ru
** E-mail: kitsyuk.e@gmail.com
Поступила в редакцию 11.04.2020
После доработки 25.06.2020
Принята к публикации 30.06.2020
Аннотация
В работе изучается синтез углеродных нанотрубок методом химического парофазного осаждения с использованием тонкопленочного катализатора на основе никеля. Проведено сопоставление распределений всех наночастиц катализатора по размерам с распределением частиц, из которых наблюдался рост углеродных нанотрубок. Установлено, что в данном режиме нанотрубки растут преимущественно из частиц размерами от 7 до 19 нм, из частиц других размеров нанотрубки практически не растут. Разработана термодинамическая модель растворимости углерода в наночастице никеля. Показано, что для каждого набора параметров процесса синтеза существует критический минимальный размер наночастицы катализатора, в которой углерод может раствориться.
ВВЕДЕНИЕ
Углеродные нанотрубки (УНТ) занимают важное место в наноэлектронике [1]. Они обладают многими уникальными свойствами, среди которых поглощение и испускание электромагнитного излучения. Это открывает перспективу создания приемно-передающих устройств на основе УНТ в широком диапазоне длин волн: от радиочастотного до оптического [2, 3]. Явление автоэлектронной эмиссии из УНТ [4] используется для создания холодных катодов, СВЧ-переключателей и катодов рентгеновских трубок. Для реализации указанных выше устройств необходимо выращивать вертикальные массивы углеродных нанотрубок длиной 1–4 мкм и диаметром не больше 30–40 нм. Причем, чем меньше диаметр нанотрубки, тем больше ее аспектное отношение и больше усиление электрического поля у конца нанотрубки, что ведет к увеличению плотности эмиссионных токов.
В настоящее время рост углеродных нанотрубок осуществляется методами химического парофазного осаждения (СVD) [1], в том числе в плазменном разряде (PECVD). В качестве катализатора для синтеза УНТ используют Fe, Co и Ni [5]. Механизмы роста достаточно хорошо изучены [6], в том числе с применением статистических методов [7]. Размер частиц катализатора четко коррелирует с диаметром, а, следовательно, и числом стенок УНТ. Для синтеза нанотрубок малого диаметра на планарной подложке необходимо формирование массива наночастиц катализатора требуемой морфологии. На синтез УНТ оказывают влияние различные технологические факторы формирования катализатора [1, 5]: толщина пленок катализатора [8], температура формирования наночастиц катализатора [9]. Отжиг в окислительной и восстановительной атмосфере перед ростом углеродных нанотрубок также сказывается на процессе их синтеза [1, 5]. Многочисленные исследования позволили сформировать последовательность технологических операций при росте УНТ методами CVD на тонкопленочных катализаторах: нанесение на подложку тонких пленок буферного и каталитического слоя, окисление их в кислородной среде, восстановление в среде водорода и/или аммиака.
Важной задачей является снижение температуры выращивания УНТ с целью приближения условия роста УНТ к условиям протекания технологических процессов при планарной технологии. Снижения этой температуры можно добиваться путем применения катализаторов, имеющих малое поверхностное натяжения, например, добавлением Ni [10], а также использованием биметалических (Co–Fe) и триметаллических (Ni–Co–Fe) катализаторов, нанесенных на различные подложки. В качестве подложки используются оксиды, которые обладают низкой поверхностной энергией [10, 11]. Ведутся работы по нанесению монометаллических пленок катализаторов на SiO2 [12], который также уменьшает поверхностную энергию [13].
Одним из направлений снижения температуры и улучшения условий роста является исследование влияния на поверхность катализатора окисляющей атмосферы [13]. Присутствие аммиака в составе газа носителя увеличивает размер частиц и ускоряет рост УНТ. Такое же влияние оказывает создание на поверхности медного катализатора (закиси меди) [14]. Имеется патент [15], в котором предлагается ускорять рост УНТ путем отжига образцов в кислородной среде в диапазоне температур от 200 до 400°С до проведения синтеза нанотрубок. Таким образом, подготовка поверхности катализатора перед ростом углеродных нанотрубок является важным технологическим этапом.
В то же время, растворимость углерода в наночастице катализатора исследована пока недостаточно. Оказывается, что нанотрубки растут не из каждой наночастицы катализатора. Чаще всего рост происходит из наночастиц среднего для данного распределения размера. При этом понятие “средний размер” зависит от условий формирования наночастиц катализатора, в том числе толщины слоя катализатора, который наносится на буферный слой, самого буферного слоя, температур отжига как в окислительной, так и восстановительной атмосферах. При толщине пленки катализатора порядка 2 нм и температуре восстановления 500°С, средний размер определяют наночастицы с диаметром 4–18 нм практически для любого времени отжига. При этом из частиц размером менее, чем 7 нм, нанотрубки не растут, а при диаметре большем, чем 20 нм, растут с много меньшей вероятностью.
Целью настоящей работы является разработка и проверка термодинамической модели растворимости углерода в наночастицах катализатора, которая бы учитывала влияние энергии поверхности частицы определенного размера и температуру синтеза углеродных нанотрубок на растворение атомов примеси.
ЭКСПЕРИМЕНТАЛЬНАЯ ЧАСТЬ
Синтез углеродных нанотрубок проводился на установке “Nanofab 800 Agile”, разработанной на основе серии “Plasmа Lab System 100” фирмы “Oxford Instruments”. В качестве подложки использовался окисленный монокристаллический кремний. На эту подложку методом электронно-лучевого напыления были нанесены пленки титана и никеля толщиной 10 и 2 нм соответственно. Синтез углеродных нанотрубок проводился в три стадии: окисление при температуре 280°С в течение 10 мин, восстановление в потоке аммиака при температуре 500°С в течение 1 мин и рост при этой же температуре в потоке аргона, ацетилена и аммиака в течении 30 с. Результаты синтеза анализировались с помощью растрового электронного микроскопа (РЭМ) FEI Helios NanoLab 650i. Прибор способен получать изображения с разрешением не хуже 0.7 нм при ускоряющем напряжении не более 1 кВ. На рис. 1 показано РЭМ-изображение приповерхностной области образца после синтеза. Как следует из рис. 1, рост нанотрубок происходит преимущественно из наночастиц среднего размера среди данного распределения. Для того, чтобы убедиться в существовании этой закономерности, были построены диаграмма распределения наночастиц по размеру, а также диаграмма распределения растущих из них нанотрубок по диаметру, которые представлены на рис. 2.
Рис. 2.
Распределение наночастиц и УНТ по диаметрам. Точечный график – распределение размеров наночастиц никеля после окислительного (T = 280°С, 10 мин) и восстановительного (T = 500°С, 1 мин) отжигов; гистограмма – распределение диаметров углеродных нанотрубок, которые выросли из данных наночастиц.
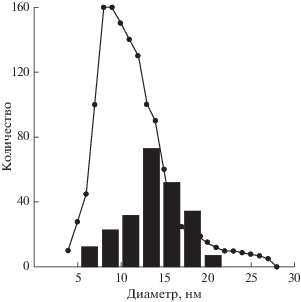
РЕЗУЛЬТАТЫ И ИХ ОБСУЖДЕНИЕ
Как будет показано ниже, учитывать поверхность кристаллов больших размеров нет необходимости, так как вклад поверхности в этом случае невелик. Однако поверхностные эффекты становятся заметными для наноразмерных кристаллов, в том числе для наночастиц катализаторов.
Для решения задачи воспользуемся методом минимизации свободной энергии Гиббса, разработанным в [16, 17]. Рассмотрим систему из наноразмерной частицы катализатора, находящегося в равновесии с углеродом, который высвободился из углеводородов в результате каталитических процессов на поверхности катализатора. Объем системы ограничен объемом, в котором происходит выращивание углеродных нанотрубок. В такой системе нет обмена частиц с внешней средой, но есть обмен энергией, поэтому к ней можно применить метод поиска минимума свободной энергии.
Будем считать, что в первом приближении в этой системе есть только два сорта атомов (С и Ni), и рассчитаем растворимость углерода в катализаторе. При этом используются следующие обозначения: ${{N}^{{{\text{Ni}}}}}$ – число мест, на которых могут размещаться атомы, из которых состоит наночастица катализатора, $N_{{\text{С}}}^{{{\text{Ni}}}}$ – число атомов углерода, которые растворены в катализаторе, $N_{{{\text{Ni}}}}^{{{\text{Ni}}}}$ – число атомов никеля в наночастице катализатора, $N_{{{\text{Ni}}}}^{g},$ $N_{{\text{C}}}^{g}$ – число атомов сорта Ni и C, которые находятся во внешней фазе.
Свободная энергия такой системы запишется в виде [1, 17]:
(1)
$\begin{gathered} G = {{G}^{g}}\left( {N_{{{\text{Ni}}}}^{g},N_{{\text{C}}}^{g}} \right) + g_{{\text{C}}}^{{{\text{Ni}}}}N_{{\text{C}}}^{{{\text{Ni}}}} + \\ + \,\,\left( {g_{{{\text{Ni}}}}^{{{\text{Ni}}}}N_{{{\text{Ni}}}}^{{{\text{Ni}}}} - {{G}^{S}}\left( {N_{{{\text{Ni}}}}^{{{\text{Ni}}}}} \right)} \right) - kT\ln \frac{{{{N}^{{{\text{Ni}}}}}{\kern 1pt} !}}{{N_{{\text{C}}}^{{{\text{Ni}}}}{\kern 1pt} !N_{{{\text{Ni}}}}^{{{\text{Ni}}}}{\kern 1pt} !}}. \\ \end{gathered} $Здесь ${{G}^{g}}\left( {N_{{{\text{Ni}}}}^{g},N_{{\text{C}}}^{g}} \right)$ – свободная энергия внешней фазы, $g_{{\text{C}}}^{{{\text{Ni}}}}$ – свободная энергия растворимости атомов углерода в наночастице катализатора, $g_{{{\text{Ni}}}}^{{{\text{Ni}}}}$ – свободная энергия, выделяющаяся при переходе атомов Ni из внешней фазы в катализатор, ${{G}^{S}}$ – свободная энергия поверхности катализатора, величина которой зависит от размеров наночастицы катализатора, а, следовательно, от $N_{{{\text{Ni}}}}^{{{\text{Ni}}}},$ k – постоянная Больцмана, T – абсолютная температура. Последнее слагаемое в (1) является конфигурационной энтропией кристалла.
При минимизации свободной энергии необходимо учитывать законы сохранения (уравнения связи) для количества частиц никеля NNi и углерода NC, а также общего числа атомов в наночастице катализатора NNi:
(2)
$\begin{gathered} {{\varphi }_{{\text{С}}}} \equiv {{N}_{{\text{С}}}} - N_{{\text{С}}}^{{{\text{Ni}}}} - N_{{\text{C}}}^{g} = 0, \\ {{\varphi }_{{{\text{Ni}}}}} \equiv {{N}_{{{\text{Ni}}}}} - N_{{{\text{Ni}}}}^{{{\text{Ni}}}} - N_{{{\text{Ni}}}}^{g} = 0, \\ {{\varphi }^{{{\text{Ni}}}}} \equiv {{N}^{{{\text{Ni}}}}} - N_{{\text{C}}}^{{{\text{Ni}}}} - N_{{{\text{Ni}}}}^{{{\text{Ni}}}} = 0. \\ \end{gathered} $Минимум свободной энергии (1) с дополнительными условиями (2) можно найти методом Лагранжа. Термодинамическое равновесие кристалла соответствует минимуму функционала:
(3)
$\Psi = G + {{\lambda }_{{\text{С}}}}{{\varphi }_{{\text{С}}}} + {{\lambda }_{{{\text{Ni}}}}}{{\varphi }_{{{\text{Ni}}}}} + {{\lambda }^{{{\text{Ni}}}}}{{\varphi }^{{{\text{Ni}}}}}.$(4)
$\left\{ \begin{gathered} {{\mu }_{{\text{С}}}} - {{\lambda }_{{\text{C}}}} = 0, \hfill \\ {{\mu }_{{{\text{Ni}}}}} - {{\lambda }_{{{\text{Ni}}}}} = 0, \hfill \\ g_{{\text{C}}}^{{{\text{Ni}}}} + kT\ln N_{{\text{C}}}^{{{\text{Ni}}}} - {{\lambda }_{{\text{C}}}} - {{\lambda }^{{{\text{Ni}}}}} = 0, \hfill \\ g_{{{\text{Ni}}}}^{{{\text{Ni}}}} + kT\ln N_{{{\text{Ni}}}}^{{{\text{Ni}}}} - {{\lambda }_{{{\text{Ni}}}}} - {{\lambda }^{{{\text{Ni}}}}} - \frac{{\partial {{G}^{S}}}}{{\partial N_{B}^{B}}} = 0, \hfill \\ \end{gathered} \right.$(5)
${{\mu }_{{\text{C}}}} = \frac{{\partial {{G}^{g}}}}{{\partial N_{{\text{C}}}^{g}}},\,\,\,\,{{\mu }_{{{\text{Ni}}}}} = \frac{{\partial {{G}^{g}}}}{{\partial N_{{{\text{Ni}}}}^{g}}}.$Решая систему уравнений (4) с учетом определений химических потенциалов (5), получаем растворимость углерода в наночастице никеля:
(6)
$\begin{gathered} N_{{\text{C}}}^{{{\text{Ni}}}} = N_{{{\text{Ni}}}}^{{{\text{Ni}}}}\exp \left\{ { - \frac{{\left( {g_{{\text{C}}}^{{{\text{Ni}}}} + {{\mu }_{{{\text{Ni}}}}} - {{\mu }_{{\text{C}}}}} \right)}}{{kT}}} \right\} \times \\ \times \,\,\exp \left\{ { - \left( {\frac{{\partial {{G}^{S}}\left( {N_{{{\text{Ni}}}}^{{{\text{Ni}}}}} \right)}}{{\partial N_{{{\text{Ni}}}}^{{{\text{Ni}}}}}}} \right)\frac{1}{{kT}}} \right\}, \\ \end{gathered} $(7)
$N_{{\text{C}}}^{{{\text{Ni}}}} = N_{{{\text{C0}}}}^{{{\text{Ni}}}}\exp \left\{ { - \left( {\frac{{\partial {{G}^{S}}\left( {N_{{{\text{Ni}}}}^{{{\text{Ni}}}}} \right)}}{{\partial N_{{{\text{Ni}}}}^{{{\text{Ni}}}}}}} \right)\frac{1}{{kT}}} \right\}.$Таким образом, на количество растворенного в наночастице никеля углерода оказывает влияние поверхностная энергия. Ниже будет показано, что это влияние тем сильнее, чем меньше размеры кристалла.
Поверхностную энергию сферического кристалла можно представить в виде:
где $N_{{{\text{Ni}}}}^{S}$ – количество атомов никеля на поверхности наночастицы, $\Delta H_{{{\text{Ni}}}}^{S}$ – изменение энергии атома никеля при его переходе на поверхность.Из простых геометрических соображений, считая, что наночастица катализатора сферическая, можно получить следующее выражение:
(9)
$S = 4\pi {{R}^{2}} = {{a}^{2}}{{(4\pi )}^{{{1 \mathord{\left/ {\vphantom {1 3}} \right. \kern-0em} 3}}}}{{\left( {3N_{{{\text{Ni}}}}^{{{\text{Ni}}}}} \right)}^{{{2 \mathord{\left/ {\vphantom {2 3}} \right. \kern-0em} 3}}}},$Используя формулы (8) и (9), получаем выражение для поверхностной энергии:
(10)
${{G}^{S}} = \sigma S = {{a}^{2}}\sigma {{\left( {3N_{{{\text{Ni}}}}^{{{\text{Ni}}}}} \right)}^{{{2 \mathord{\left/ {\vphantom {2 3}} \right. \kern-0em} 3}}}}{{(4\pi )}^{{{1 \mathord{\left/ {\vphantom {1 3}} \right. \kern-0em} 3}}}},$Из (10) с учетом выражения для радиуса наночастицы, получаем:
(11)
$\frac{{\partial {{G}^{S}}}}{{\partial N_{{{\text{Ni}}}}^{{{\text{Ni}}}}}} = \frac{{2{{a}^{3}}\sigma }}{R}.$Тогда с учетом (11), выражение (7) для количества растворенных в наночастице катализатора атомов углерода принимает вид:
(12)
$N_{{\text{C}}}^{{{\text{Ni}}}} = N_{{{\text{C}}0}}^{{{\text{Ni}}}}\exp \left\{ { - \frac{{2{{a}^{3}}\sigma }}{R}\frac{1}{{kT}}} \right\}.$Чем меньше радиус наночастицы катализатора, тем меньше атомов углерода в ней растворяется. Критический радиус наночастицы катализатора, при котором растворится один атом углерода, равен:
(13)
${{R}_{{\min }}} = \frac{{2{{a}^{3}}\sigma }}{{kT\ln \left( {N_{{{\text{C}}0}}^{{{\text{Ni}}}}} \right)}}.$Наночастицы катализатора меньшего размера в данных условиях растворить углерод не могут, поэтому из таких частиц нанотрубки не растут. Коэффициент поверхностного натяжения расплавленного никеля равен 2.3 × 10–3 Дж/м2 при температуре 1450°С. При таком коэффициенте поверхностного натяжения радиус минимальной наночастицы составляет порядка 10 нм. При более низких температурах коэффициент поверхностного натяжения растет и критический радиус наночастицы еще больше. Как следует из литературных данных [1], рост более тонких трубок наблюдается при повышении температуры синтеза.
Однако поверхностное натяжение существенно меньше в оксидах. Поэтому на синтез нанотрубок может оказывать влияние наличие атомов кислорода на поверхности катализатора или использование буферного слоя на основе оксида. С другой стороны, если наночастица состоит только из оксида никеля NiO, то рост нанотрубок невозможен. Во-первых, температура плавления оксида никеля составляет 1955°С, поэтому его наночастица при температурах синтеза находится в твердом состоянии (без жидкого слоя на поверхности), а поверхностная энергия твердой фазы в несколько раз превышает поверхностную энергию расплава, поэтому углерод в малых наночастицах оксида не растворяется. Во-вторых, коэффициент диффузии углерода в твердом теле на несколько порядков меньше, чем в расплаве, что затрудняет поступление углерода к месту роста нанотрубки и замедляет ее рост. Таким образом, использование предваряющих синтез технологических приемов, а именно режимов окисления и восстановления катализатора, является важным этапом при синтезе нанотрубок.
ЗАКЛЮЧЕНИЕ
Как следует из полученных экспериментальных результатов, рост углеродных нанотрубок в выбранных условиях с большей вероятностью проходит из наночастиц катализатора среднего для данного распределения размера (7–19 нм). Мы считаем, что это связано с влиянием поверхностного натяжения на растворимость углерода в наночастице. При температуре 500°С приведенные выше размеры никелевых наночастиц являются оптимальными для роста углеродных нанотрубок, что доказывается совпадением распределения размеров наночастиц с диаметром УНТ, синтезируемых на данном катализаторе.
Список литературы
Булярский С.В. Углеродные нанотрубки: технология, управление свойствами, применение. Ульяновск: Стрежень, 2011. 432 с.
Rutherglen C., Burke P. // Nano Lett. 2007. V. 7. № 11. P. 3296.https://doi.org/10.1021/nl0714839
Jensen K., Weldon J., Garcia H., Zettl A. // Nano Lett. 2007. V. 7. № 11. P. 3508.https://doi.org/10.1021/nl0721113
Chernozatonskii L.A., Gulyaev Y.V., Kosakovskaja Z.J. et al. // Chem. Phys. Lett. 1995. V. 233. P. 63.https://doi.org/10.1016/0009-2614(94)01418-U
Булярский C.В., Басаев А.С. // ЖЭТФ. 2009. Т. 134. № 4. С. 788.
Krasnikov D.V., Kuznetsov V.L., Romanenko A.I., Shmakov A.N. // Carbon. 2018. V. 139. P. 105.https://doi.org/10.1016/j.carbon.2018.06.033
Mengqi Fan, Su Wu, Chi Xu. // Appl. Phys. A. 2018. V. 124. P. 790.https://doi.org/10.1007/s00339-018-1916-7
Lee M.W., Haniff M.A., Sh.M., Teh A.Sh., Bien D.C.S., Chen S.K. // J. Experimental Nanoscience. 2015. V. 10. № 16. P. 1232.https://doi.org/10.1080/17458080.2014.994679
Zhang K., Lin X., Xu W., Miao Y., Hu K., Zhang Y. // Optoelectronics Letters. 2011. V. 7. № 2. P. 85.https://doi.org/10.1007/s11801-011-0169-x
Zhang H., Cao G., Wang Z., Yang Y., Gu Z. // Carbon. 2008. V. 46. P. 822.https://doi.org/10.1016/j.carbon.2008.02.015
Lucia K.N., Norberto S.G., Antoninho V. et al. // J. Mater Sci. 2007. V. 42. P. 914.https://doi.org/10.1007/s10853-006-0009-8
Terrado E., Tacchini I., Benito A.M. // Carbon. 2009. V. 47. P. 1989.https://doi.org/10.1016/j.carbon.2009.03.045
Булярский С.В. // ЖТФ. 2011. Т. 81. С. 64.
Vanhaecke E., Huang F., Yu Y., RønningM., Holmen A., Chen D. // Top. Catal. 2011. V. 54. P. 986.https://doi.org/10.1007/s11244-011-9720-z
Liu L., Fan S.-S. US Pat. 2004/0109815A1, 2004.
Bulyarskiy S.V., Oleynikov V.P. // Phys. Stat. Sol. 1987. V. 141. P. K7. https://doi.org/10.1002/pssb.2221410137
Булярский С.В., Фистуль В.И. Термодинамика и кинетика взаимодействующих дефектов в полупроводниках. М.: Наука, 1997. 352 с.
Дополнительные материалы отсутствуют.
Инструменты
Поверхность. Рентгеновские, синхротронные и нейтронные исследования