Поверхность. Рентгеновские, синхротронные и нейтронные исследования, 2022, № 1, стр. 75-79
Механизмы усталостного разрушения ленточных аморфных металлических сплавов при испытаниях на растяжение и изгиб
В. А. Федоров a, *, Т. Н. Плужникова a, Д. Ю. Федотов a
a Тамбовский государственный университет им. Г.Р. Державина
392000 Тамбов, Россия
* E-mail: fedorov-tsu.tmb@inbox.ru
Поступила в редакцию 25.05.2021
После доработки 20.06.2021
Принята к публикации 30.06.2021
- EDN: GMUFIU
- DOI: 10.31857/S1028096022010046
Аннотация
Рассмотрены особенности усталостного разрушения ленточных образцов аморфных сплавов при испытаниях на растяжение и изгиб. Предложены механизмы разрушения, основанные на перераспределении избыточного свободного объема в образцах. Механизм роста усталостной трещины при испытаниях на растяжение следующий. После зарождения с торцевой поверхности образца на концентраторах нагрузки трещина формирует перед своей вершиной серию микропор за счет перераспределения избыточного свободного объема. После разрыва микропоры образуют на поверхности разрушения характерный полосчатый рельеф, наблюдаемый вплоть до зоны долома. Одновременно рост трещины сопровождается формированием “венозного узора” при переходе усталостной трещины из одной плоскости в другую. При испытаниях на изгиб исходно равномерно распределенный избыточный свободный объем мигрирует преимущественно в область растяжения. За счет упругого взаимодействия образуются скопления избыточного свободного объема в плоскостях, нормальных к поверхности растяжения. В этих плоскостях зарождаются трещины, поверхности которых испытывают касательный сдвиг относительно друг друга. Дальнейшие изгибные нагружения способствуют раскрытию трещины.
ВВЕДЕНИЕ
Усталостные испытания являются одним из видов исследований влияния циклических деформационных шумов и случайных процессов на целостность различных изделий из аморфных металлических сплавов. В отличие от кристаллических сплавов аморфные не обладают дальним порядком [1, 2]. Неупорядоченная структура и метастабильное состояние отвечают в металлических стеклах за необычные механизмы деформации [3, 4]. В настоящий момент имеется достаточно много данных о деформации кристаллических материалов. Сведений о деформации аморфных тел значительно меньше [5–7], так как аморфное состояние твердого тела – наименее изученная область современного структурного материаловедения. Аморфные сплавы обладают набором уникальных свойств [8–10], одним из таких свойств является способность к пластическому течению [11, 12]. Эта способность связана с металлическим характером межатомной связи, при которой легче идут процессы коллективных перемещений [13]. Пластическая деформация в аморфных сплавах может протекать гомогенно или негомогенно [14]. При гомогенном течении однородно нагруженный образец испытывает однородную деформацию. При негомогенной деформации пластическое течение локализовано в тонких дискретных полосах сдвига, а остальной объем твердого тела остается недеформированным [15]. Изучение смены механизмов пластического течения представляет собой сложную экспериментальную задачу. Сведения об условиях изменения характера пластического течения аморфных сплавов носят противоречивый характер. В [16] показано, что тип пластического течения, формирование его закономерностей определяются кинетикой необратимой структурной релаксации. В случае негомогенной деформации на поверхности деформированных растяжением, сжатием, изгибом или прокаткой образцов формируются ступени сдвига. Эти ступени соответствуют выходу на поверхность полос сдвига. Таким образом, аморфные сплавы обладают существенной локальной пластичностью при негомогенной деформации.
На проявление характеристик пластичности аморфных металлических сплавов могут влиять многие факторы, такие как состав материала, геометрия образца, химическая среда, температура, среднее напряжение, остаточное напряжение, состояние поверхности и т.д. Среди этих факторов стоит отметить геометрические параметры образцов, которые оказывают большое влияние на усталостное поведение металлических стекол [17, 18]. Большинство исследований усталостных свойств материалов проводят на объемных образцах металлических стекол [19–21].
Основной механизм усталостного разрушения объемных аморфных металлических сплавов до сих пор остается неясным. В общем случае возникновение усталостных трещин объясняют дефектами отливки и пористостью образцов, возникающей при литье сплава [22]. Исследований механизмов усталостного разрушения ленточных образцов аморфных сплавов практически нет.
Целью работы было выявление основных закономерностей усталостного разрушения ленточных образцов аморфного металлического сплава на основе Co при длительных циклических испытаниях на растяжение и изгиб.
УСТАЛОСТНЫЕ ИСПЫТАНИЯ ЛЕНТОЧНЫХ АМОРФНЫХ МЕТАЛЛИЧЕСКИХ СПЛАВОВ НА РАСТЯЖЕНИЕ
Материалом для проведения исследования были выбраны ленты аморфных металлических сплавов АМАГ-186 (Сo85.5Fe2.27Si5.15Mn4.07B2Cr1), АМАГ-180 (Сo78.5Ni4.73Fe4Si7.25Mn1.88B2Cr1.5). Размер рабочей области образцов 20 × 3.5 × 0.02 мм.
Усталостные испытания образцов проводили на специально разработанной установке растягивающей нагрузкой, изменяющейся от некоторого минимального значения до максимального, с частотой 2 Гц. Зависимость изменения напряжения в образце от времени представляет собой периодическую функцию [23].
По результатам усталостных испытаний были построены зависимости разрушающей нагрузки σ от логарифма числа N циклов нагружения (кривые Веллера). На рис. 1 приведена зависимость для сплава АМАГ-186. При росте усталостных трещин выявлены области зарождения трещины, ее роста, переходная зона и зона долома [24].
Рис. 1.
Зависимость величины разрушающих напряжений σ от логарифма числа циклов N при усталостных испытаниях на растяжение образцов сплав АМАГ-186.
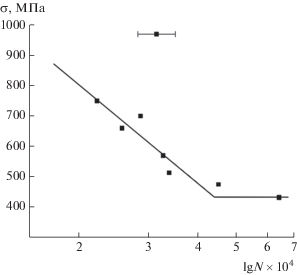
Проведены фрактографические исследования поверхности разрушения. В области зарождения трещины имеет место вязкое разрушение (рис. 2а) с образованием плотно расположенных микроутяжек. Характерное расстояние между утяжками ~0.5–1.5 мкм. Основная зона роста усталостной трещины развивается подобно сколу с образованием “венозного узора” (рис. 2б). Образование подобного узора наблюдали в [25] при разрушении объемного сплава на основе циркония. На поверхностях роста усталостной трещины наблюдаются характерные для такого вида разрушения ступени, соответствующие одноразовому скачкообразному подрастанию трещины (рис. 2в). Характерная величина такого “скачка” 0.2–0.5 мкм. В зоне долома трещина продвигается вязко, с образованием локализованных зон пластичности в местах остановки. Величина скачков ~5–8 мкм (рис. 2г).
Рис. 2.
Поверхность усталостного разрушения: а – поверхность в зоне зарождения трещины; б – формирование “венозного узора” на поверхности разрушения; в – характерные ступени роста усталостной трещины на поверхности разрушения; г – поверхность разрушения в зоне долома.
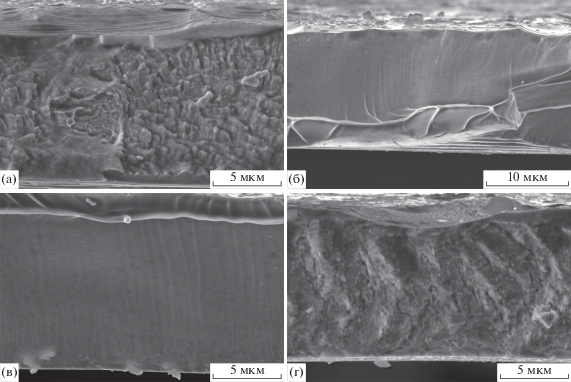
Представляется следующий механизм роста собственной усталостной трещины (рис. 3). После зарождения с торцевой поверхности образца на естественных концентраторах нагрузки трещина образует перед своей вершиной серию микропор за счет направленной миграции избыточного свободного объема [26] в область растягивающих напряжений. После слияния пор и разрыва перемычек на поверхности разрушения формируется рельеф (рис. 2в). Такой рельеф формируется вплоть до зоны долома. Формирование “венозного узора” обусловлено переходом усталостной трещины из одной плоскости в другую.
УСТАЛОСТНЫЕ ИСПЫТАНИЯ ОБРАЗЦОВ АМОРФНЫХ МЕТАЛЛИЧЕСКИХ СПЛАВОВ НА ИЗГИБ
Испытания на изгиб проводили на специально разработанном устройстве [23]. Частота нагружения образца составляла 12 Гц. Величину напряжений σ, возникающих в образце, оценивали по формуле (1):
где y – толщина образца; ρ – радиус кривизны изгиба образца, E – модуль Юнга материала образца. На рис. 4 приведена зависимость разрушающего напряжения σ от логарифма числа N циклов нагружения образцов сплава АМАГ-186.Рис. 4.
Зависимость величины разрушающих напряжений σ от логарифма числа циклов N при усталостных испытаниях на изгиб образцов сплав АМАГ-186.
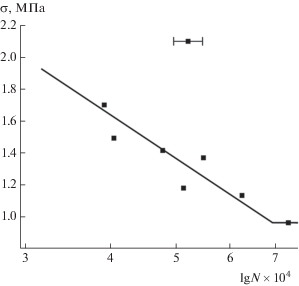
Проведены фрактографические исследования поверхности разрушения и берегов роста трещины. На поверхности разрушения выявлены три зоны (рис. 5): 1 – зона образования трещины, поверхность разрушения гладкая, без видимых следов пластичности; 2 – зона усталостного роста, связанная с образованием деформационного рельефа с характерным размером блоков структуры ~0.5–1 мкм; 3 – зона долома с развитием грубых пластических сдвигов. Трещина зарождается со стороны поверхности с растягивающими напряжениями. По характеру формирования деформационного рельефа и разрушения можно предположить образование интрузий и экструзий. На рис. 6 видно, что трещина образуется вдоль экструзии. Ветвления трещин и сдвигов при испытаниях на изгиб не наблюдали. “Венозного узора” на берегах трещины также нет. Это подтверждает, что зарождение трещины происходит сколом.
Рис. 5.
Поверхность роста усталостной трещины при испытаниях на изгиб: 1 – зона зарождения трещины; 2 – зона усталостного роста; 3 – зона долома.
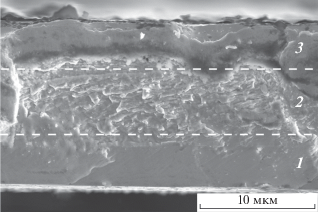
Рис. 6.
Фрагмент зарождения усталостной трещины при испытаниях на изгиб. Трещина формируется сколом вдоль экструзии.
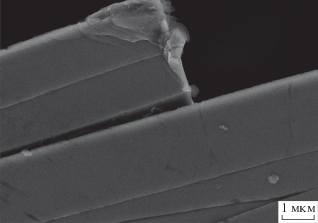
В ненагруженном образце избыточный свободный объем равномерно распределен (рис. 7а). При циклически повторяющихся изгибах происходит перераспределение избыточного свободного объема. Он мигрирует преимущественно в область растяжения (рис. 7б). За счет упругого взаимодействия образуются скопления свободного объема в плоскостях, нормальных к поверхности растяжения (рис. 7в) (наподобие образования полигональных стенок). В этих плоскостях зарождаются трещины, поверхности которых испытывают касательный сдвиг относительно друг друга (рис. 7г). Изгибные нагружения способствуют раскрытию трещины (рис. 7д). Образование подобных трещин и сдвигов наблюдали экспериментально (рис. 6).
Рис. 7.
Механизм зарождения трещин на поверхности образца при усталостных испытаниях на изгиб: а – исходное состояние; б – перераспределение свободного объема в область растягивающих напряжений; в – формирование плоских скоплений свободного объема; г – формирование экструзий и интрузий; д – раскрытие трещины.

ЗАКЛЮЧЕНИЕ
Таким образом, механизм роста усталостной трещины в аморфных сплавах при испытаниях на растяжение основан на направленном перераспределении избыточного свободного объема в области растягивающих напряжений.
После зарождения с торцевой поверхности образца на концентраторах нагрузки трещина формирует перед своей вершиной серию микропор за счет перераспределения избыточного свободного объема, которые после разрыва формируют на поверхности разрушения характерный рельеф. Одновременно рост трещины сопровождается формированием “венозного узора” при переходе усталостной трещины из одной плоскости в другую.
Предложен и подтвержден экспериментально механизм зарождения трещины, в основе которого лежит процесс возникновения экструзий и интрузий. Образование микротрещин обусловлено перераспределением избыточного свободного объема в образце, что приводит к образованию плоских скоплений – источников зарождения трещины при сдвиге одних слоев сплава относительно других.
Список литературы
Inoue A., Takeuchi A. // Acta Mater. 2011. V. 59. P. 2243.https://doi.org/10.1016/j.actamat.2010.11.027
Johnson W.L. // MRS Bull. 1999. V. 24. P. 42.https://doi.org/10.1557/S0883769400053252
Schuh C.A., Hufnagel T.C., Ramamurty U. // Acta Mater. 2007. V. 55. P. 4067.https://doi.org/10.1016/j.actamat.2007.01.052
Trexler M.M., Thadhani N.N. // Prog. Mater. Sci. 2010. V. 55. P. 759.https://doi.org/10.1016/j.pmatsci.2010.04.002
Алехин В.П., Хоник В.А. Структура и физические закономерности деформации аморфных сплавов. М.: Металлургия, 1992. 248 с.
Судзуки К., Фудзимори Х., Хасимото К. Аморфные металлы. М.: Металлургия, 1987. 328 с.
Глезер А.М., Молотилов Б.В. Структура и механические свойства аморфных сплавов. М.: Металлургия, 1992. 208 с.
Аморфные металлические сплавы / Ред. Люборский Ф.Е. М.: Металлургия, 1987. 584 с.
Манохин А.И., Митин Б.С., Васильев В.А., Ревякин А.В. Аморфные сплавы. М.: Металлургия, 1984. 160 с.
Металлические стекла / Ред. Гилман Дж.Дж. и др. М.: Металлургия, 1984. 264 с.
Nair B., Priyadarshini G. // Mater. Sci. 2016. V. 3. № 3. P. 1022.https://doi.org/10.3934/matersci.2016.3.1022
Suryanarayana C., Inoue A. Bulk Metallic Glasses. USA: Taylor and Francis Group, 2011. 548 p.
Глезер А.М., Пермякова И.Е. Нанокристаллы, закаленные из расплава. М.: Физматлит, 2012. 360 с.
Немошкаленко В.В., Романова А.В., Ильинский А.Г. Аморфные металлические сплавы. Киев: Наук. думка, 1987. 248 с.
Глезер А.М., Плотникова М.Р., Сундеев Р.В., Шурыгина Н.А. // Изв. РАН. Сер. физ. 2013. Т. 77. № 11. С. 1687.https://doi.org/10.7868/S0367676513110173
Кобелев Н.П., Колыванов Е.Л., Хоник В.А. // Физика твердого тела. 2005. Т. 47. № 3. С. 395.https://doi.org/10.1134/1.1884696
Greer J.R., De Hosson J.T.M. // Prog. Mater. Sci. 2011. V. 56. P. 654.https://doi.org/10.1016/j.pmatsci.2011.01.005
Jang D., Gross C.T., Greer J.R. // Int. J. Plast. 2011. V. 27. P. 858.https://doi.org/10.1016/j.ijplas.2010.09.010
Li D.-F., Yang Y.-L., Shen Y., Xu J. // J. Mater. Sci. Tech. 2021. V. 89. P. 1.https://doi.org/10.1016/j.jmst.2021.02.015
Wang Z., Wang C., Zhao Y.-L., Kai J.-J., Liu C.-T., Hsueh C.-H. // Surf. Coat. Tech. 2021. V. 410. P. 126927.https://doi.org/10.1016/j.surfcoat.2021.126927
Sha Z., Lin W., Poh L.H., Xing G., Liu Z., Wang T. // Appl. Mech. Rev. 2020. V. 72. P. 050801.https://doi.org/10.1115/1.4048056
Xianqi L., Lichao Y., Liu P., Chengqi S., Bingchen W., Yujie W. // Int. J. Fatigue. 2021. V. 143. P. 106004.https://doi.org/10.1016/j.ijfatigue.2020.106004
Федотов Д.Ю., Федоров В.А., Яковлев А.В., Плужникова Т.Н., Березнер А.Д. // Вестн. Тамб. ун-та. Сер. Естеств. и тех. науки. 2016. Т. 21. № 3. С. 1396.https://doi.org/10.20310/1810-0198-2016-21-3-1396-1399
Федотов Д.Ю., Федоров В.А., Яковлев А.В., Плужникова Т.Н., Шлыкова А.А. // Вестн. Тамб. ун-та. Сер. Естеств. и тех. науки. 2017. Т. 22. № 5. С. 1109.https://doi.org/10.20310/1810-0198-2017-22-5-1109-1114
Zhu Y., Fu J., Zheng C., Ji Z. // Opt. Laser Tech. 2015. V. 75. P. 157.https://doi.org/10.1016/j.optlaseng.2020.106052
Spaepen F. // Acta Metall. 1977. V. 25. P. 407.https://doi.org/10.1016/0001-6160(77)90232-2
Дополнительные материалы отсутствуют.
Инструменты
Поверхность. Рентгеновские, синхротронные и нейтронные исследования