Поверхность. Рентгеновские, синхротронные и нейтронные исследования, 2022, № 1, стр. 63-74
Диффузионное взаимодействие силицидов молибдена со сплавом Э110
И. Б. Гнесин a, *, Б. А. Гнесин a, А. Н. Некрасов b, Д. В. Прохоров a, Н. И. Гнесина a, М. И. Карпов a, И. С. Желтякова a
a Институт физики твердого тела Российской академии наук
142432 Черноголовка, Россия
b Институт экспериментальной минералогии Российской академии наук РАН
142432 Черноголовка, Россия
* E-mail: ibgnesin@issp.ac.ru
Поступила в редакцию 15.03.2021
После доработки 08.05.2021
Принята к публикации 17.05.2021
- EDN: GVAAND
- DOI: 10.31857/S1028096022010058
Аннотация
Экспериментально исследована кинетика диффузионного взаимодействия заэвтектического сплава силицидов молибдена Mo5Si3 + MoSi2 с реакторным сплавом марки Э110 на основе циркония. Методами растровой электронной микроскопии и энергодисперсионного рентгеноспектрального микроанализа изучено структурное и фазовое состояние диффузионных пар, подвергнутых отжигам в вакууме при 1100, 1200 и 1300°C в течение 3, 6 и 9 ч. Во всем исследованном интервале температур и для всех выдержек на границе раздела сплавов силицидов молибдена и циркония в результате диффузионного взаимодействия образуются силициды циркония. Процесс переноса кремния является основным диффузионным процессом при взаимодействии сплава на основе циркония и силицидов молибдена. Признаков диффузии циркония в силициды молибдена не обнаружено, диффузия молибдена в цирконий значительно ограничена. Выявлены особенности структуры и химического состава образующихся в области диффузионного взаимодействия силицидных фаз. Проведен сравнительный анализ микроструктуры областей диффузионного взаимодействия силицидов Mo5Si3 и MoSi2 со сплавом циркония. Определены эффективные кинетические параметры процессов диффузионного взаимодействия при разных температурах, а также параметры температурной зависимости эффективной параболической константы роста слоя промежуточных фаз, возникающего при отжигах диффузионных пар.
ВВЕДЕНИЕ
Сплавы на основе циркония широко применяются в реакторостроении во всем мире. Они являются основным материалом, из которого изготавливают оболочки тепловыделяющих элементов (ТВЭЛ) и другие детали тепловыделяющих сборок (ТВС) ядерных энергетических установок (ЯЭУ), использующих легкую воду в качестве теплоносителя (ВВЭР, PWR, BWR, РБМК и т.д.). Они обладают высокой коррозионной стойкостью, достаточным уровнем механических свойств и, что очень важно, низким эффективным сечением захвата тепловых нейтронов [1]. На сегодняшний день в качестве оболочек ТВЭЛ в ЯЭУ используются сплавы циркония с оловом (Zircaloy 2, Zircaloy 4), ниобием (Э110, Э125, M5), сложнолегированные сплавы (ZIRLO, Э365) [2]. Их важным преимуществом также является высокая степень отработанности технологий их создания и эксплуатации. Однако серьезным недостатком сплавов циркония является их низкая стойкость при взаимодействии с водяным паром в условиях аварийных ситуаций на ЯЭУ, связанных с потерей теплоносителя [3]. При развитии подобной ситуации в активной зоне ЯЭУ происходит падение давления и интенсивный рост температуры за счет остаточного тепловыделения топлива. При достижении температуры около 900°C и выше выполненные из сплавов циркония оболочки ТВЭЛ вступают в экзотермическую реакцию с водяным паром, продуктами которой являются оксид циркония и газообразный водород. При дальнейшем росте температуры выделение тепла за счет пароциркониевой реакции значительно растет, растет и количество выделяющегося водорода. Развитие этого процесса может приводить к катастрофическим последствиям [4].
В связи с необходимостью повысить безопасность ЯЭУ усилиями МАГАТЭ была разработана концепция устойчивого к авариям топлива (accident tolerant fuel, ATF) [5]. Согласно этой концепции, решение задачи повышения уровня безопасности реакторов на легкой воде в краткосрочной перспективе достигается за счет создания защитных покрытий на существующие оболочки ТВЭЛ [6, 7]. Этот путь не потребует внесения серьезных изменений в существующие технологии конструирования и эксплуатации ЯЭУ.
Активные поиски материалов, способных защитить сплавы на основе циркония от пароциркониевой реакции, ведутся в последние годы по всему миру. Основными материалами, рассматриваемыми в качестве возможных покрытий, как правило, являются материалы, формирующие жаростойкие оксиды в процессе окисления. Это материалы, содержащие Cr, Al, Si [8]. В качестве материала защитных покрытий на оболочки ТВЭЛ рассматривают сплавы FeCrAl [9–11], MAX-фазы [12–14]. Изучали способность защитить сплавы циркония с помощью карбидных [15] и нитридных [16, 17] покрытий. Основным же материалом, рассматриваемым в качестве покрытия на оболочки ТВЭЛ, на сегодня является Cr [18–22].
Одной из важных проблем разработки покрытия на оболочки ТВЭЛ является диффузионное взаимодействие материала покрытия со сплавами циркония, которое может приводить к значительному снижению защитных свойств покрытия. Этот недостаток характерен для различных покрытий [23, 24], в том числе и для наиболее активно изучаемых покрытий на основе хрома [25, 26]. Поэтому продолжение работ по поиску новых материалов для защиты циркониевых сплавов от пароциркониевой реакции остается актуальным.
Возможным направлением научного поиска с целью создания жаростойкого покрытия на ТВЭЛ является создание покрытий на основе силицидов молибдена. Ранее силициды молибдена рассматривались в рамках концепции ATF как покрытия на перспективные молибденовые оболочки ТВЭЛ. При этом была установлена их повышенная стойкость к взаимодействию с паром в широком интервале температур [27]. Силициды молибдена продемонстрировали высокие показатели стойкости в парах воды, поэтому они могут рассматриваться в качестве перспективных материалов для создания покрытия на циркониевые оболочки ТВЭЛ устойчивого к авариям ядерного топлива.
Диффузионное взаимодействие циркония с простыми веществами изучалось ранее. Были получены данные о диффузионной подвижности кремния в цирконии [28, 29], а также молибдена в цирконии [30]. Однако, на сегодняшний день в научной литературе отсутствуют данные о характере диффузионного взаимодействия силицидов молибдена с цирконием или сплавами на его основе. Важность получения этих сведений для оценки возможности силицидных покрытий обеспечить защиту циркониевых сплавов трудно переоценить.
Получение данных о характере диффузионного взаимодействия силицидов молибдена с цирконием или сплавами на его основе является основной целью этой работы. Мы исследовали взаимодействие двухфазного силицидного сплава с реакторным сплавом Э110 на основе циркония, из которого изготавливаются оболочки ТВЭЛ большинства ЯЭУ российского производства.
МЕТОДИКА
Исследовали образцы, полученные путем диффузионного взаимодействия сплава силицидов Mo5Si3 + MoSi2 с реакторным сплавом марки Э110 на основе циркония.
Образцы силицидов были синтезированы в ИФТТ РАН из элементарных порошков молибдена и кремния. Был использован порошок молибдена “ПМ99,95” с чистотой 99.95 мас. % производства АО “ПОЛЕМА”, а также порошок кремния с чистотой 99.8 мас. % производства ООО “Платина”. Близкий к эвтектическому состав силицидного сплава был выбран на основании известных данных о стойкости Mo5Si3/MoSi2 к окислению, а также согласно ряду технологических свойств данных сплавов. Так как потери кремния при изготовлении силицидов были практически неизбежны, из исходных порошков была приготовлена смесь, близкая по составу к MoSi2, чтобы в результате синтеза получить эвтектическую смесь силицидов MoSi2 + Mo5Si3 или смесь первичных кристаллов MoSi2 с данной эвтектикой. Подобные сплавы характеризуются относительно низкими температурами плавления. Выделение заметных количеств первичных кристаллов фазы Mo5Si3 было бы нежелательным, так как это означало бы получение сплава с относительно высокой температурой ликвидус.
Порошки были тщательно смешаны и спрессованы при комнатной температуре при давлении прессования 25 МПа. Затем полученная прессовка была спечена при температуре T = = 1400°C в атмосфере аргона, после чего была подвергнута электронно-лучевому переплаву в охлаждаемой медной изложнице. Полученный слиток разрезали на пластины размером около 2 × 7 × 7 мм с плоскопараллельными гранями 7 × × 7 мм. Одну из плоскопараллельных граней подвергали шлифовке и полировке.
Образцы сплава марки Э110 (Zr–1 мас. % Nb) были получены из прутка диаметром 9.6 мм, изготовленного АО “Чепецкий механический завод” в соответствии с ТУ 95 241-89. Химический состав образцов соответствовал ТУ 95 166-98. Пруток разрезали на цилиндрические образцы высотой около 7 мм. Затем одна из плоских поверхностей полученных образцов подвергалась шлифовке и полировке.
Диффузионные пары для исследования приготовили методом диффузионной сварки образцов силицидов и циркония. Сварку осуществляли в модернизированной установке УДС-10 в вакууме (давление 10–3 Торр) при температуре 1000°C в течение одного часа, давление прессования составляло около 3 МПа. При подготовке процесса диффузионной сварки образцы циркония и силицидов сопрягались полированными поверхностями и помещались в установку. Для предотвращения взаимодействия образцов с графитовой оснасткой установки использовали прокладки из молибдена и термически расщепленного графита. После окончания высокотемпературной выдержки полученные таким образом образцы диффузионных пар охлаждались вместе с печью.
После получения, готовые диффузионные пары были подвергнуты отжигам различной продолжительности при различной температуре. Отжиги проводили в печи сопротивления с молибденовыми нагревателями и молибденовыми деталями тепловой зоны в вакууме, при давлении <5 × 10–5 Торр. Температура отжигов составляла 1100, 1200 и 1300°C, длительность – 3, 6 и 9 ч. Время выхода печи на температурный режим было около 12–15 мин и не учитывалось в общем времени выдержки. После отжигов образцы разрезали перпендикулярно плоскости контакта диффузионной пары и исследовали. Кроме того, для дополнительной оценки исходного состояния ряд образцов исследовали в состоянии сразу после получения диффузионной пары (без дополнительных диффузионных отжигов).
Резку образцов осуществляли с помощью электроэрозионного станка. Шлифовку и полировку образцов проводили путем абразивной обработки с последовательным уменьшением размера абразивных частиц. В качестве абразивов использовалась SiC-бумага с зернистостью от P120 до P2500, а также алмазные порошки от АСМ 10/7 до АСМ 1/0.
Микроструктуру полученных образцов исследовали с помощью растрового электронного микроскопа Tescan VEGA II XMU. Анализ химического состава структурных составляющих был произведен методом рентгеноспектрального микроанализа с использованием энергодисперсионного спектрометра INCA Energy 450 с полупроводниковым Si(Li) детектором INCA X-sight. Все приведенные в работе иллюстрации микроструктуры получены с использованием сигнала от отраженных электронов.
Анализ кинетики диффузионного взаимодействия осуществляли по данным зависимости общей толщины слоя силицидов циркония, образующегося на границе раздела Э110 и силицидов молибдена, от температурно-временны́х параметров термообработки.
Толщину слоя определяли по изображениям микроструктуры, проводя от 17 до 27 измерений толщины для каждого образца. Толщину измеряли на случайных участках микроструктуры. Для каждого образца определяли среднюю общую толщину образовавшегося слоя силицидов циркония, а также стандартное отклонение результатов ее измерения от среднего значения. Для всех образцов был определен коэффициент вариации толщины силицидного слоя, представляющий отношение стандартного отклонения к среднему значению измеряемой величины. Для анализа изображений микроструктуры, а также для проведения измерений размеров структурных составляющих использовали программу ImageJ [31].
Эффективную параболическую константу роста kэф для каждой температуры определяли двумя методами.
Метод 1. Для каждой длительности выдержки при данной температуре рассчитывалась величина
(1)
${{k}_{{{\text{эф}}}}} = {{{{x}^{2}}} \mathord{\left/ {\vphantom {{{{x}^{2}}} {2t,}}} \right. \kern-0em} {2t,}}$Метод 2. Эффективная параболическая константа для данной температуры определялась согласно соотношению:
(2)
${{k}_{{{\text{эф}}}}} = {{{{a}^{2}}} \mathord{\left/ {\vphantom {{{{a}^{2}}} {2,}}} \right. \kern-0em} {2,}}$По полученным данным строили зависимость натурального логарифма kэф от величины, обратной температуре. По линейной аппроксимации этой зависимости определяли параметры уравнения Аррениуса:
где k0 – предэкспоненциальный множитель, E – энергия активации роста, R – универсальная газовая постоянная, T – температура.РЕЗУЛЬТАТЫ И ИХ ОБСУЖДЕНИЕ
Микроструктура и состав
Общий вид диффузионных пар, характерный для всех полученных образцов, представлен на рис. 1а. Как видно из рисунка, каждый образец состоял из трех основных областей:
Рис. 1.
Общий вид приготовленной диффузионной пары (Mo5Si3 + MoSi2)–Э110 (а); структура слоя силицидов молибдена: Mo5Si3 – светлая фаза, MoSi2 – темная (б).
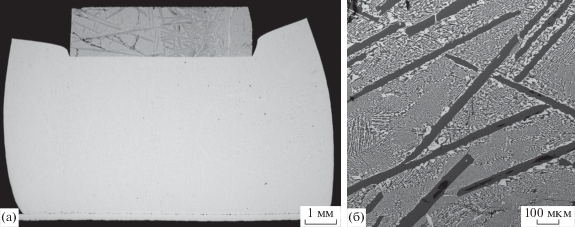
1) расположенный вверху слой силицидов молибдена;
2) занимающий основную, среднюю часть образца слой циркония;
3) тонкий слой молибдена, расположенный внизу.
Слой молибдена представлял технологическую подложку, использованную при изготовлении образца. Основное внимание при исследовании было обращено на изменения структуры вблизи границы раздела слоя силицидов молибдена со слоем циркония, происходящие при отжигах.
Во всех исследованных случаях структура слоя силицидов молибдена была образована эвтектическими колониями (Mo5Si3 + MoSi2) с включением избыточных кристаллов фазы MoSi2 (рис. 1б). Выделение первичных кристаллов фазы Mo5Si3 не было зафиксировано ни в одном случае.
Следует отметить, что почти для всех исследованных образцов характерна зональная ликвация в слое силицидов молибдена, т.е. неоднородность распределения первичных кристаллов фазы MoSi2 по объему. Присутствие подобных неоднородностей химического и фазового состава силицидного слитка может быть связано с особенностями электронно-лучевой плавки, а также с высокой температурой плавления силицидов молибдена. При этом, наблюдаемые изменения объемной доли первичных кристаллов MoSi2 соответствуют изменению среднего содержания кремния в объеме сплава в пределах всего нескольких единиц атомных процентов. Таким образом, можно заключить, что примененная технология получения силицидов молибдена позволила успешно получить образцы сплавов силицидов молибдена необходимого состава. Однако, наблюдаемая (пусть и небольшая) неоднородность распределения кремния в объеме слоя силицидов молибдена приводит и к неоднородности его распределения и по плоскости диффузионного взаимодействия с цирконием. Влияние этой неоднородности на параметры диффузионного взаимодействия будет обсуждено ниже.
Структура зоны диффузионного взаимодействия циркония и силицидов молибдена всех исследованных образцов представлена на рис. 2.
Рис. 2.
Структура границы раздела диффузионных пар после отжигов при различной температуре: а – 1100°C 3 ч, б – 1100°C 6 ч, в – 1100°C 9 ч; г – 1200°C 3 ч, д – 1200°C 6 ч, е – 1200°C 9 ч; ж – 1300°C 3 ч, з – 1300°C 6 ч, и – 1300°C 9 ч.
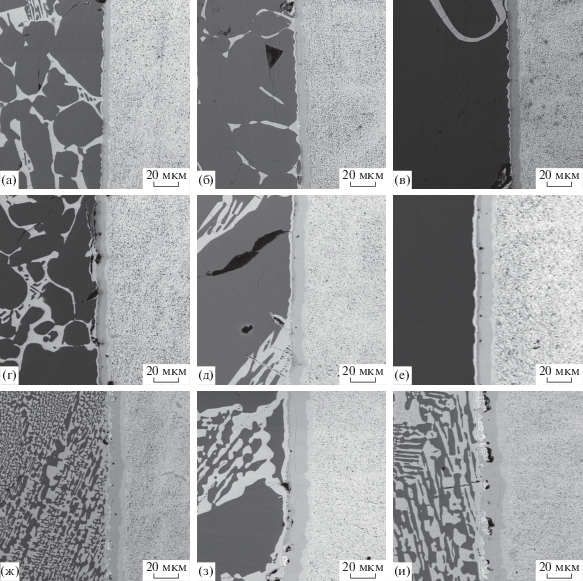
Экспериментальные данные о химическом составе фаз, образующихся в результате взаимодействия, показали, что во всех случаях основным процессом диффузионного переноса являлся перенос кремния из силицидов молибдена в сплав циркония, сопровождающийся образованием слоев силицидов циркония различного состава.
Условно можно разделить образующуюся зону диффузионного взаимодействия на три области, по мере продвижения от циркония к силицидам молибдена (рис. 3):
Рис. 3.
Микроструктура (а) и распределение компонентов по фазам (б) для образца после отжига при 1200°C в течение 6 ч. Измерение концентрации компонентов проводились вдоль линии 1–2.
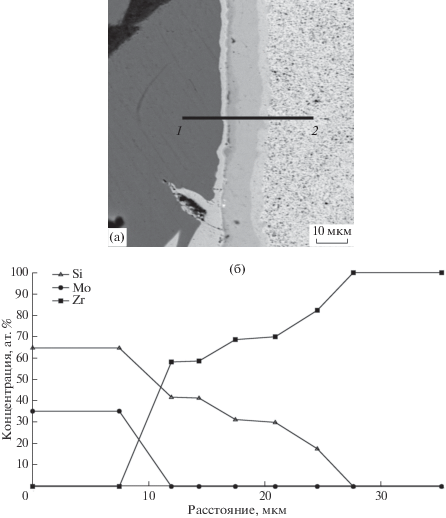
1) область, прилегающая к цирконию,
2) промежуточная область,
3) область, прилегающая к силицидам молибдена.
Наибольшей по толщине является промежуточная область, которая всегда образована фазой Zr2Si. Слой этой фазы характерен для всех исследованных образцов. Оценка химического состава этого слоя для всех исследованных образцов показала содержание кремния на уровне 30–31 ат. %, что несколько ниже, чем стехиометрическое. Следует также отметить, что заметная толщина данного слоя позволяла оценить изменение химического состава данной фазы в зависимости от удаления от силицидов молибдена. В рамках настоящей работы подобного изменения не было обнаружено: в пределах точности используемой методики, состав данной фазы не зависел от расположения области анализа.
Также практически всегда обнаруживали слой силицида циркония Zr3Si, образующего область, прилегающую к цирконию. Образец после отжига при 1100°C в течение 3 ч является единственным, где эта фаза выделяется не в виде сплошного слоя заметной толщины, а отдельными, не всегда сомкнутыми областями. На всех остальных исследованных образцах этот слой присутствует в полной мере. Следует отметить, что в данной работе измеренное содержание кремния в фазе Zr3Si всегда отклонялось от стехиометрического и составляло около 20 ат. %, что фактически соответствует соединению Zr4Si. Однако неопределенность области существования фазы Zr3Si, а также отклонения ее химического состава в сторону более обогащенных цирконием составов считаются известными [32]. Поэтому в данной работе эта фаза обозначается как Zr3Si, несмотря на ее фактический химический состав. При этом существуют другие современные экспериментальные оценки уровня содержания кремния в этом силициде. Например, в работе [33] авторы изучали диффузионное взаимодействие содержащей кремний MAX-фазы титана со сплавом на основе циркония. Авторы отмечают присутствие фазы Zr3Si в исследуемых образцах. Данные о концентрации кремния в ней, полученные авторами, совпадают с полученными нами и составляют также около 20 ат. %.
Что касается третьей области зоны диффузионного взаимодействия, области, прилегающей к силицидам молибдена, то ее строение на том или ином участке образца зависит от структуры силицидов молибдена на этом участке. Так, в случае выхода на поверхность диффузионного контакта с цирконием силицида MoSi2 между ним и силицидами циркония возникает тонкая (1–2 мкм) прослойка силицида Mo5Si3 (рис. 3, 4а). Далее формируется слой силицида циркония, содержание кремния в котором составляет около 42 ат. %. Согласно анализу имеющихся данных, это, вероятнее всего, фаза Zr3Si2. В ряде случаев в пределах этой фазы находятся отдельные области силицида циркония с содержанием кремния около 46 ат. %. Предполагается, что это фаза Zr5Si4.
Рис. 4.
Микроструктура границы раздела вблизи фазы MoSi2 (а) и эвтектики Mo5Si3 + MoSi2 (б). Образцы после отжига в течение 9 ч при температуре 1200°C (а) и 1300°C (б). Области анализа химического состава указаны точками, результаты анализа представлены в табл. 1.
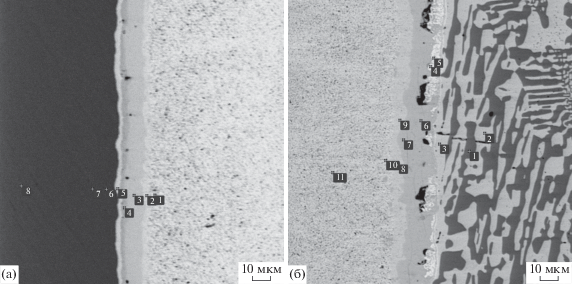
В случае выхода на поверхность раздела силицида Mo5Si3, либо мелкодисперсной эвтектической смеси Mo5Si3 + MoSi2 указанные выше силициды циркония с содержанием кремния 40 ат. % и более, не образуются (рис. 4б). Взамен указанных силицидов в структуре, помимо слоев Zr2Si и Zr3Si, наблюдается фаза, характеризующаяся соотношением атомных концентраций молибдена и циркония RMo = CMo/(CMo+ CZr) = 54–60%, а также признаками присутствия кремния в количестве 4–7 ат. % (табл. 1). Точный анализ химического состава данной фазы был затруднен вследствие малых размеров ее кристаллитов (1–2 мкм). Следует отметить, что эта фаза встречается в малых количествах во всех исследованных образцах. Однако даже после наиболее длительных и наиболее высокотемпературных термообработок, которые применяли в настоящей работе, данная фаза не образовала протяженного слоя (даже на локальных участках), несмотря на то, что ее количество выросло. Увеличение ее объемной доли в слое диффузионного взаимодействия приводило к ее росту в виде отдельных кластеров, а не в виде слоев (рис. 4б).
Таблица 1.
Результаты исследований химического состава в областях, обозначенных на рис. 4
Рис. 4а | Рис. 4б | ||||||||
---|---|---|---|---|---|---|---|---|---|
номер точки на рисунке | концентрация, ат. % | фаза | номер точки на рисунке | концентрация, ат. % | фаза | ||||
Si | Zr | Mo | Si | Zr | Mo | ||||
1 | – | 100.0 | – | Zr | 1 | 64.9 | – | 35.1 | MoSi2 |
2 | 22.4 | 77.6 | – | Zr3Si | 2 | 36.1 | – | 63.9 | Mo5Si3 |
3 | 31.0 | 69.0 | – | Zr2Si | 3 | 35.6 | – | 64.4 | Mo5Si3 |
4 | 43.4 | 56.6 | – | Zr3Si2 | 4 | 3.6 | 37.8 | 58.6 | Mo3Zr2Six |
5 | 36.9 | – | 63.1 | Mo5Si3 | 5 | 6.9 | 41.6 | 51.4 | Mo3Zr2Six |
6 | 64.5 | – | 35.5 | MoSi2 | 6 | 30.7 | 69.3 | – | Zr2Si |
7 | 65.0 | – | 35.0 | MoSi2 | 7 | 30.9 | 69.1 | – | Zr2Si |
8 | 64.7 | – | 35.3 | MoSi2 | 8 | 19.5 | 80.5 | – | Zr3Si |
– | – | – | – | – | 9 | 19.9 | 80.1 | – | Zr3Si |
– | – | – | – | – | 10 | – | 100.0 | – | Zr |
– | – | – | – | – | 11 | – | 100.0 | – | Zr |
В литературе имеются данные о возможности образования в системе Mo–Zr–Si тройного соединения на базе фазы Лавеса Mo2Zr [34]. При этом указывается, что кремний в таком случае замещает именно цирконий, а не молибден. Это означает, что параметр RMo, составляющий 66.7% для Mo2Zr, при введении кремния лишь вырастает, достигая уровня более 70%. Однако, обнаруженная фаза имеет, как уже указывалось выше, значение параметра RMo в интервале 54–60%, что говорит, скорее, против гипотезы о возникновении обнаруженной фазы на базе фазы Mo2Zr. Для более надежного определения состава обнаруженной фазы, а также ее кристаллической структуры, необходимы дальнейшие исследования.
Обобщая сказанное выше, можно заключить, что полученные экспериментальные данные свидетельствует о процессе переноса кремния как об основном диффузионном процессе, протекающем при взаимодействии сплава марки Э110 на основе циркония с силицидами молибдена. Перенос циркония в силициды молибдена зафиксирован не был. Определенные свидетельства слабого переноса молибдена в цирконий были обнаружены, однако этот процесс практически не оказывает влияния на общее диффузионное взаимодействие изучаемых материалов в рассмотренных температурно-временны́х рамках.
Кинетика взаимодействия
Особенности кинетики взаимодействия силицидов молибдена и сплава Э110 на основе циркония изучались путем определения единой эффективной константы параболического роста области диффузионного взаимодействия. В табл. 2 приведены экспериментально определенные значения общей толщины области диффузионного взаимодействия (суммарной толщины всех слоев силицидов циркония) для исследованных образцов, а также некоторые статистические параметры, характеризующие проведенные измерения.
Таблица 2.
Толщина образующегося слоя силицидов циркония в исследованных образцах
Температура, °С | Выдержка, ч | Общая толщина слоя, мкм | Стандартное отклонение, мкм | Объем выборки, шт. | Коэффициент вариативности, % |
---|---|---|---|---|---|
1100 | 3 | 4.7 | 0.7 | 27 | 15.2 |
6 | 6.6 | 0.6 | 18 | 9.8 | |
9 | 7.8 | 0.7 | 18 | 9.5 | |
1200 | 3 | 9.0 | 0.8 | 22 | 9.2 |
6 | 12.2 | 1.0 | 18 | 8.1 | |
9 | 14.4 | 1.2 | 17 | 8.5 | |
1300 | 3 | 15.4 | 1.1 | 27 | 7.4 |
6 | 21.4 | 1.1 | 17 | 5.2 | |
9 | 24.1 | 1.0 | 23 | 4.1 |
Приведенные в табл. 2 данные позволяют определить некоторые общие закономерности взаимодействия сплава Э110 с двухфазным силицидным сплавом. Так, стандартное отклонение при измерении средней толщины области взаимодействия находится практически на одном и том же уровне для всех исследованных образцов и составляет всего около 1 мкм. Учитывая рост абсолютного значения средней толщины слоя взаимодействия при росте температуры и времени выдержки образцов, очевидно, что коэффициент вариативности толщины слоя взаимодействия падает с ростом толщины слоя взаимодействия. Это достаточно важный факт, позволяющий сделать вывод о том, что, несмотря на определенную неоднородность химического состава силицидов молибдена, используемых в данной работе, описание общей кинетики процессов их диффузионного взаимодействия с цирконием может быть осуществлено единой константой параболического роста. Разница в механизмах взаимодействия с цирконием силицида Mo5Si3 и силицида MoSi2 была достаточной для того, чтобы проявились некоторые структурные отличия, которые были отмечены выше. Однако общее влияние этих различий не привело к значительному колебанию толщины зоны общего диффузионного взаимодействия. Более того, с ростом времени и температуры термообработки общая неопределенность средней толщины слоев силицидов практически не выросла. А величина относительной неопределенности в определении этого параметра, напротив, снизилась в три раза. Это говорит о том, что в рассмотренных в работе температурно-временны́х рамках даже двухфазные сплавы силицидов молибдена можно рассматривать как достаточно однородный источник кремния с точки зрения процессов диффузионного взаимодействия со сплавами на основе циркония.
Зависимость толщины зоны диффузионного взаимодействия от корня квадратного из времени для различных температур отжига приведена на рис. 5а. Очевидно, что полученные данные хорошо соответствуют параболическому закону, что подтверждает диффузионную природу исследуемого процесса.
Рис. 5.
Зависимость общей толщины слоя всех силицидов циркония от корня квадратного из времени (а) и зависимость натурального логарифма kэф от 1/T (б).
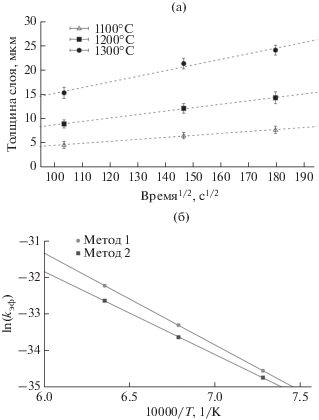
На рис. 5б представлена зависимость рассчитанных двумя методами констант параболического роста от температуры термообработки образцов. В обоих случаях, полученные результаты позволяют констатировать, что зависимость константы параболического роста исследуемых фаз от температуры хорошо соответствует уравнению Аррениуса. Расчет параметров этого уравнения на основе полученных экспериментальных данных для случая определения методом нахождения среднего арифметического констант для данной температуры приводит к следующему выражению:
(4)
${{k}_{{{\text{эф}}}}} = 8.75 \times {{10}^{{ - 8}}}{\text{exp}}({{ - 208{\kern 1pt} {\kern 1pt} 800} \mathord{\left/ {\vphantom {{ - 208{\kern 1pt} {\kern 1pt} 800} {RT}}} \right. \kern-0em} {RT}}).$(5)
${{k}_{{{\text{эф}}}}} = 1.23 \times {{10}^{{ - 8}}}{\text{exp}}({{ - 188{\kern 1pt} {\kern 1pt} 600} \mathord{\left/ {\vphantom {{ - 188{\kern 1pt} {\kern 1pt} 600} {RT}}} \right. \kern-0em} {RT}}).$Верификация полученных зависимостей путем расчета толщины образующегося слоя силицидов циркония для разных температурно-временны́х параметров термообработки и сравнение полученных значений с экспериментально определенными приведены на рис. 6. Из приведенных данных видно, что в обоих случаях расчетные толщины слоев близки как друг к другу, так и к экспериментальным значениям. Но при расчете константы параболического роста путем определения среднего арифметического для данной температуры расчетные данные толщины слоев лучше совпадают с экспериментальными во всем диапазоне времен выдержки и температур. Поэтому в настоящей работе мы склонны считать данные, полученные первым методом, более надежными.
Рис. 6.
Сравнение экспериментальных данных по толщине слоя силицидов циркония с полученными методами 1 и 2.
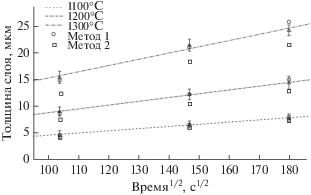
Следует также отметить, что образование тонких слоев силицидов циркония на этапе диффузионной сварки фиксировалось нами. Толщины подобных слоев находились на уровне, примерно соответствующем стандартному отклонению определения толщины, указанному ранее, и составляли 0.5–1 мкм. Введение поправки на подобную величину не вносило заметных изменений в результаты верификации получаемых данных по кинетике роста, что не удивительно в виду малой величины этих поправок.
В таблице 3 приведены результаты исследования кинетики взаимодействия циркония и кремния, полученные в различных работах, включая настоящую. Для удобства сопоставления по данным каждой работы был произведен расчет толщины образующихся слоев силицидов циркония за единое время выдержки – 9 часов :
(6)
${{x}_{9}} = {{x}_{t}}{{({9 \mathord{\left/ {\vphantom {9 t}} \right. \kern-0em} t})}^{{{1 \mathord{\left/ {\vphantom {1 2}} \right. \kern-0em} 2}}}},$Таблица 3.
Толщина образующегося слоя силицидов циркония в различных работах по исследованию диффузии Si в Zr
Анализ приведенных данных позволяет утверждать, что диффузия кремния в цирконий наименее активно протекает при взаимодействии с цирконием именно силицидов молибдена. Само по себе это является положительным фактором для перспективных силицидных покрытий на ТВЭЛ.
Причем интересным результатом является и то, насколько наличие кремния в силицидах молибдена подавило диффузию самого молибдена. Полученные в настоящей работе результаты согласуются с данными о подвижности молибдена и кремния в силицидах молибдена, полученными в работе [35]. Ее авторами установлено, что во всех промежуточных фазах системы Mo–Si диффузия кремния идет значительно активнее диффузии молибдена. Авторы связывают этот факт с различным количеством точечных дефектов в подрешетках кремния и молибдена. Эти результаты и выводы согласуются с наблюдаемой нами картиной, когда при взаимодействии силицидов молибдена с цирконием основным продуктом являются именно силициды циркония, а не фазы, содержащие цирконий и молибден.
ЗАКЛЮЧЕНИЕ
Полученные в настоящей работе результаты позволяют сделать следующие выводы:
При диффузионном взаимодействии силицидов молибдена со сплавом на основе циркония Э110 при температурах 1100–1300°C и временах порядка нескольких часов основным процессом переноса вещества является диффузионный перенос кремния из силицидов молибдена в сплав циркония. Перенос циркония в силициды молибдена практически не зафиксирован. Перенос молибдена в цирконий весьма ограничен.
Кинетика роста слоев силицидов циркония хорошо описывается параболическим законом для всех исследуемых образцов. Этот процесс сопровождается формированием на границе силицидов молибдена и сплава циркония слоев силицидов циркония различной стехиометрии.
Значительных колебаний толщины образующегося слоя силицидов циркония в зависимости от фазового состава силицидов молибдена не обнаружено. Коэффициент вариации при измерении толщины слоев силицидов циркония падает с ростом температуры и времени диффузионного взаимодействия, что говорит о допустимости изучения кинетики диффузионного взаимодействия методами, выбранными в данной работе.
Определены кинетические параметры диффузионного взаимодействия силицидов молибдена и сплава Э110. Зависимость константы параболического роста от температуры определяется уравнением kэф = 8.75 × 10–8 exp(–208 800/RT).
Список литературы
Разработка, производство эксплуатация тепловыделяющих элементов энергетических реакторов / Под ред. Решетникова Ф.Г. Москва: Энергоатомиздат, 1995. В 2-х кн. 320 + 336 с.
Tang C., Stueber, M., Seifert H., Steinbrueck M. // Corrosion Reviews. 2017. V. 35. № 3. P. 141.https://doi.org/10.1515/corrrev-2017-0010
Cheng T., Keiser J.R., Brady M.P., Terrani K.A., Pint B.A. // J. Nucl. Mater. 2012. V. 427. I. 1–3. P. 396. https://doi.org/10.1016/j.jnucmat.2012.05.007
The Fukushima Daiichi Accident. Vienna. IAEA, 2015. 1254 p.
Accident Tolerant Fuel Concepts for Light Water Reactors. Vienna. IAEA-TECDOC-1797, 2016. 384 p.
Zinkle S.J., Terrani K.A., Gehin J.C., Ott L.J., Snead L.L. // J. Nucl. Mater. 2014. V. 448. № 1–3. P. 374.https://doi.org/10.1016/j.jnucmat.2013.12.005
Savchenko A.M., Ivanov V.B., Novikov V.V., Skupov M.V., Kulakov G.V., Orlov V.K., Uferov O.I., Konovalov Y.V. // Conf. TopFuel Annual Meeting. American Nuclear Society. Zurich, Switzerland. 2015. Sep. 13–17.
Terrani K.A. // J. Nucl. Mater. 2018. V. 501. P. 13.https://doi.org/10.1016/j.jnucmat.2017.12.043
Maier B., Yeom H., Johnson G., Dabney T., Walters J., Romero J., Shah H., Xu P., Sridharan K. // JOM. 2018. V. 70. P. 198.https://doi.org/10.1007/s11837-017-2643-9
Gigax J.G., Kennas M., Kim H., Maier B.R., Yeom H., Johnson G.O., Sridharan K., Shao L. // J. Nucl. Mater. 2019. V. 519. P. 57.https://doi.org/10.1016/j.jnucmat.2019.03.004
Dabney T., Johnson G., Yeom H., Maier B., Walters J., Sridharan K. // Nuclear Materials and Energy. 2019. V. 21. P. 100715.https://doi.org/10.1016/j.nme.2019.100715
Maier B.R., Garcia-Diaz B.L., Hauch B., Olson L.C., Sindelar R.L., Sridharan K. // J. Nucl. Mater. 2015. V. 466. P. 712.https://doi.org/10.1016/j.jnucmat.2015.06.028
Yeom H., Hauch B., Cao G., Garcia-Diaz B., Martinez-Rodriguez M., Colon-Mercado H., Olson L., Sridharan K. // Thin Solid Films. 2016. V. 615. P. 202.https://doi.org/10.1016/j.tsf.2016.07.024
Imtyazuddin M., Mir A.H., Tunes M.A., Vishnyakov V.M. // J. Nucl. Mater. 2019. V. 526. 151742.https://doi.org/10.1016/j.jnucmat.2019.151742
Usui T., Sawada A., Amaya M., Suzuki A., Chikada T., Terai T. // J. Nucl. Sci. Technol. 2015. V. 52. № 10. P. 1318.https://doi.org/10.1080/00223131.2015.1020901
Alat E., Motta A.T., Comstock R.J., Partezana J.M., Wolfe D.E. // J. Nucl. Mater. 2016. V. 478. P. 236.https://doi.org/10.1016/j.jnucmat.2016.05.021
Tunes M.A., Felipe C. da Silva, Camara O., Schön C.G., Sagás J.C., Fontana L.C., Donnelly S.E., Greaves G., Edmondson P.D. // J. Nucl. Mater. 2018. V. 512. P. 239.https://doi.org/10.1016/j.jnucmat.2018.10.013
Kashkarov E.B., Sidelev D.V., Rombaeva M., Syrtanov M.S., Bleykher G.A. // Surface and Coatings Technology. 2020. V. 389. P. 125618.https://doi.org/10.1016/j.surfcoat.2020.125618
Карпюк Л.А., Краснобаев Н.Н., Маслов А.А., Новиков В.В., Орлов В.К., Титов А.О., Кузнецов В.И., Рыкунов Д.В. // Вопросы атомной науки и техники. Серия: Материаловедение и новые материалы. 2020. Т. 106. № 5. С. 4.
Kim H.-G., Kim I.-H., Jung Y.-I., Park D.-J., Park J.-Y., Koo Y.-H. // J. Nucl. Mater. 2015. V. 465. P. 531.https://doi.org/10.1016/j.jnucmat.2015.06.030
Park J.-H., Kim H.-G., Park J.-Y., Jung Y.-I., Park D.-J., Koo Y.-H. // Surface and Coatings Technology. 2015. V. 280. P. 256.https://doi.org/10.1016/j.surfcoat.2015.09.022
Bischoff J., Delafoy C., Vauglin C., Barberis P., Roubeyrie C., Perche D., Duthoo D., Schuster F., Brachet J.-C., Schweitzer E.W., Nimishakavi K. // Nuclear Engineering and Technology. 2018. V. 50. I. 2. P. 223. https://doi.org/10.1016/j.net.2017.12.004
Yeom H., Maier B., Johnson G., Dabney T., Walters J., Sridharan K. // J. Nucl. Mater. 2018. V. 507. P. 306.https://doi.org/10.1016/j.jnucmat.2018.05.014
Ougier M., Michau A., Lomello F., Schuster F., Maskrot H., Schlegel M.L. // J. Nucl. Mater. 2020. V. 528. P. 151855.https://doi.org/10.1016/j.jnucmat.2019.151855
Brachet J.-C., Rouesne E., Ribis J., Guilbert T., Urvoy S., Nony G., Toffolon-Masclet C Le, Saux M., Chaabane N., Palancher H., David A., Bischoff J., Augereau J., Pouillier E.// Corrosion Science. 2020. V. 167. P. 108537.https://doi.org/10.1016/j.corsci.2020.108537
Kashkarov E.B., Sidelev D.V., Syrtanov M.S., Tang C., Steinbrück M. // Corrosion Science. 2020. V. 175. P. 108883.https://doi.org/10.1016/j.corsci.2020.108883
Wood E.S., Parker S.S., Nelson A.T. // Molybdenum Disilicide Oxidation Kinetics in High Temperature Steam. United States. Affiliation: Los Alamos National Laboratory, January 2016. Report number: LA-UR-15-26776. https://doi.org/10.2172/1323383
Bertolino N., Anselmi-Tamburini U., Maglia F., Spinolo G., Munir Z.A. // J. Alloys Compd. 1999. V. 288. P. 238.https://doi.org/10.1016/S0925-8388(99)00077-8
Roy S., Paul A. // Materials Chemistry and Physics. 2014. V. 143. I. 3. P. 1309. https://doi.org/10.1016/j.matchemphys.2013.11.039
A. Paz y Puente), Dickson J., Keiser D.D., Sohn Y.H. // International J. Refractory Metas. and Hard Materials. 2014. V. 43. P. 317.https://doi.org/10.1016/j.ijrmhm.2013.12.017
Schindelin J., Arganda-Carreras I., Frise E., Kaynig V., Longair M., Pietzsch T., Preibisch S., Rueden C., Saalfeld S., Schmid B., Tinevez J.-Y., White D.J., Hartenstein V., Eliceiri K., Tomancak P., Cardona A. // Nature Methods. 2012. V. 9. P. 676.https://doi.org/10.1038/nmeth.2019
Okamoto H. // Bulletin of Alloy Phase Diagrams. 1990. V. 11. № 5. P. 513.https://doi.org/10.1007/BF02898272
Tallman D.J., Yang J., Pan L., Anasori B., Barsoum M.W. // J. Nucl. Mater. 2015. V. 460. P. 122.https://doi.org/10.1016/j.jnucmat.2015.02.006
Blažina Ž., Trojko R., Ban. Z. // J. Less Common Metals. 1984. V. 97. P. 91.https://doi.org/10.1016/0022-5088(84)90012-2
Prasad S., Paul. A. // Intermetallics. 2011. V. 19. I. 8. P. 1191. https://doi.org/10.1016/j.intermet.2011.03.027
Дополнительные материалы отсутствуют.
Инструменты
Поверхность. Рентгеновские, синхротронные и нейтронные исследования