Поверхность. Рентгеновские, синхротронные и нейтронные исследования, 2022, № 11, стр. 78-84
Синтез керамики ZnO:Al методом шликерного литья
А. Ш. Асваров a, А. Х. Абдуев b, А. К. Ахмедов c, А. Э. Муслимов a, *, В. М. Каневский a
a Институт кристаллографии им. А.В. Шубникова ФНИЦ “Кристаллография и фотоника” РАН
119333 Москва, Россия
b Российский университет дружбы народов, Инженерная академия
115419 Москва, Россия
c Институт физики им. Х.И. Амирханова Дагестанского федерального исследовательского центра РАН
367015 Махачкала, Россия
* E-mail: amuslimov@mail.ru
Поступила в редакцию 12.02.2022
После доработки 20.04.2022
Принята к публикации 20.04.2022
- EDN: DCJKYM
- DOI: 10.31857/S1028096022110048
Аннотация
Исследован процесс синтеза керамики оксида цинка, легированного алюминием (ZnO:Al), из исходной смеси коммерческих порошков оксидов цинка и алюминия с низкой удельной поверхностью (не более 5 м2/г), заключающийся в предварительном формировании шликера и последующем высокотемпературном спекании в открытой атмосфере. Установлено, что пористость шликерной заготовки, плотность спеченной керамики и степень преимущественной укладки зерен в ней зависят как от длительности помола шликера, так и от его показателя кислотности. Продемонстрировано, что при оптимизации условий ликерного литья возможно получение проводящей керамики ZnO:Al с плотностью более 97% относительно стандартной плотности ZnO, что приемлемо при синтезе керамических мишеней, предназначенных для формирования терморегулирующих энергосберегающих покрытий.
ВВЕДЕНИЕ
Прозрачные проводящие слои на основе оксида цинка, легированного элементами III группы периодической таблицы (уровень легирования обычно находится в пределах 1–5 ат. %), получили широкое распространение в качестве функциональных слоев в многослойных энергосберегающих терморегулирующих покрытиях архитектурного стекла [1], прозрачных электродов различных оптоэлектронных устройств, в частности тонкопленочных солнечных преобразователей [2]. По ряду технологических и коммерческих соображений основным методом получения слоев на основе оксида цинка в многослойных энергосберегающих покрытиях в настоящее время является метод магнетронного реактивного распыления металлических трубчатых мишеней в окислительной атмосфере [3]. Однако сложность стабилизации рабочих режимов при реактивном распылении делает актуальным поиск относительно простых технологий замены металлических мишеней оксидными керамическими, обеспечивающими при их распылении в инертной атмосфере стабильность разряда, высокую скорость осаждения и приемлемые характеристики слоев [4].
Традиционным методом синтеза оксидных керамических мишеней является одноосное прессование порошковых смесей заданного состава и гранулометрии с последующим их спеканием в открытой атмосфере [5]. В настоящее время интенсивно развиваются и новые перспективные технологии получения мишеней, такие как горячее и холодное изостатические прессование, искровое плазменное спекание, обеспечивающие высокие характеристики синтезируемой керамики [6, 7]. Однако высокая стоимость оборудования делает актуальным поиск низкозатратных технологий синтеза. В первую очередь это касается мишеней, используемых в крупномасштабных производствах, таких как формирование терморегулирующих покрытий архитектурного стекла. В этом ключе одним из наиболее коммерчески привлекательных методов синтеза керамических мишеней представляется шликерное литье, которое позволяет получать достаточно плотные и однородные заготовки, в том числе сложной трубчатой формы, без применения высоких давлений [8–12].
В [9] на основании исследований зависимости плотности керамики ZnO:Al от соотношения вносимых в состав шликера органических компонентов (полиакриловой кислоты и полиэтиленгликоля), а также от величины pH шликера была проведена оптимизация процесса шликерного литья с целью достижения высокой плотности синтезируемой керамики.
При использовании в шликере на основе ZnO:Al в качестве дефлокулянта полиакрилата аммония и полиакриловой эмульсии в качестве связующего были получены плотные заготовки, после отжига которых в открытой атмосфере при температуре 1100°С была получена электропроводящая керамика, характеризующаяся отсутствием в своем составе нежелательной вторичной фазы шпинели ZnAl2O4 [10].
Авторами [11] показано, что процесс спекания шликерной заготовки ZnO:Al, полученной с использованием субмикронных оксидных порошков, можно интенсифицировать путем введения в спекаемую систему малых добавок оксида кремния. Керамические мишени ZnO:Al с добавкой 0.05 мас. % SiO2 характеризовались высокой однородностью, ультранизкой пористостью (менее 0.2%) и малым удельным сопротивлением (менее 5 × 10–3 Ом · см).
Проведенные исследования показывают целесообразность и перспективность применения шликерных методов синтеза керамических мишеней на основе ZnO для формирования прозрачных электродов методом магнетронного распыления на постоянном токе. Однако стоит отметить, что в [8–10] в качестве исходных реагентов использовали ультрадисперсные порошки с высокой по данным, полученным методом Брунауэра–Эммета–Теллера, удельной поверхностью (10 м2/г и более).
В настоящей работе в качестве исходных реагентов для изготовления шликера брали коммерческие порошки оксидов цинка и алюминия с удельной поверхностью, не превышающей 5 м2/г. С использованием методов рентгеновской дифракции и электронной микроскопии исследовано влияние условий формирования шликера на структуру синтезированной керамики.
МАТЕРИАЛЫ И МЕТОДЫ
Исходная керамическая смесь включала в себя субмикронный порошок оксида цинка чистотой 99.95% и удельной поверхностью не более 5 м2/г (Grillo Zinkoxid GmbH, Германия) и микронный порошок оксида алюминия чистотой 99.9% (ЛенРеактив, Россия) в необходимом соотношении Zn : Al = 98 : 2. Морфология исходных порошков представлена на рис. 1. В качестве дефлокулянта была использована полиакриловая кислота со средней молекулярной массой 5000, в качестве связующего – полиэтиленгликоль массой 40 000.
Рис. 1.
РЭМ-изображения исходных порошков ZnO (а), Al2O3 (б) и внешний вид отшлифованного среза спеченного керамического образца ZnO:Al (в).
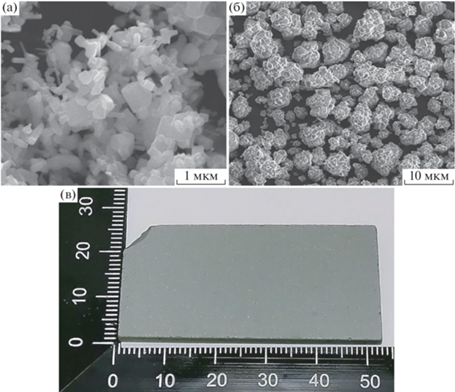
Шликеры требуемой вязкости формировали путем смешивания исходных смесей с водой в течение фиксированного времени в шаровой мельнице. Шликер включал 70% твердой фазы. Его вязкость контролировали вискозиметром ВЗ-246. Показатель кислотности pH варьировали путем внесения в состав шликера хлорида аммония. Шликер, прошедший помол в шаровой мельнице с мелющими телами из Al2O3, заливали в гипсовые формы. Были подготовлены четыре шликера, различающихся длительностью помола tобр и величиной pH.
После низкотемпературных этапов сушки и выгонки органических добавок измеряли открытую пористость образцов [12] и далее керамические заготовки подвергали двухчасовому высокотемпературному отжигу на воздухе при 1400°С. Скорость выхода на режим отжига составляла 100°С/ч.
Рентгенофазовый анализ проводили на шлифованных срезах спеченных образцов керамики (рис. 1в), параллельных плоскости основания литейной гипсовой формы, с использованием порошкового дифрактометра Shimadzu XRD-7000 с источником излучения CuKα (Япония). Морфологию спеченных образцов исследовали на свежеприготовленных сколах с использованием растрового электронного микроскопа (РЭМ) (Leo-1450, Карл Цейсс, Германия). Открытую пористость заготовок и плотность спеченных образцов измеряли методом гидростатического взвешивания с помощью аналитических весов Adventurer Analytical AX 124 (OHAUS, США).
РЕЗУЛЬТАТЫ И ИХ ОБСУЖДЕНИЕ
Для оценки влияния времени помола и величины pH шликера на характеристики керамики ZnO:Al были измерены коэффициент открытой пористости Коп шликерных заготовок после сушки, определяемый как отношение объема открытых пор к объему образца, а также относительная плотность спеченных образцов ρотн, определяемая как отношение измеренной плотности спеченного керамического образца к стандартной плотности ZnO (ρ0 = 5.61 г/см3). Результаты измерений приведены в табл. 1. Как видно из приведенных в таблице данных, уменьшение величины pH шликера и увеличение длительности его помола способствует снижению открытой пористости шликерных заготовок и, как следствие, нелинейному росту плотности спеченной керамики, что находится в согласии с литературными данными о механизмах спекания агломерированных дисперсных сред [9, 13]. Однако при увеличении длительности помола до 32 ч монотонный характер зависимости пористости заготовки от длительности помола нарушается – образец, полученный из шликера 4, характеризуется более высоким коэффициентом открытой пористости заготовки и, как следствие, низкой плотностью спеченной керамики.
Таблица 1.
Данные измерений открытой пористости заготовок Коп и относительной плотности спеченных керамик ρотн в зависимости от показателя кислотности pH и длительности помола шликера
Номер шликера | pH | tобр, ч | Коп | ρотн |
---|---|---|---|---|
1 | 10.0 | 8 | 0.149 ± 0.003 | 0.942 ± 0.003 |
2 | 9.0 | 8 | 0.142 ± 0.003 | 0.948 ± 0.003 |
3 | 9.0 | 16 | 0.138 ± 0.003 | 0.971 ± 0.003 |
4 | 9.5 | 32 | 0.166 ± 0.003 | 0.945 ± 0.003 |
На рис. 2 приведены РЭМ-изображения сколов спеченных керамик. Можно видеть, что замкнутые поры, расположенные как внутри зерен, так и на их границах, присутствуют во всех спеченных образцах. Количество и размер пор в образцах керамики коррелируют с данными об их относительной плотности ρотн (табл. 1). Наименьшее количество пор и их минимальный размер наблюдаются в керамике с относительной плотностью ρотн = 0.971, полученной из шликера 3. В образцах керамики, полученных из шликеров с более высоким значением pH и/или меньшим временем помола (шликеры 1 и 2), увеличивается как число пор, так и их средний размер. В то же время в образце керамики, полученной из шликера 4 и имеющей максимальную исходную пористость заготовки, а также относительную плотность после спекания, близкую к плотности образцов 1 и 2, концентрация пор ниже, однако они большего размера и расположены преимущественно на границах зерен.
Рис. 2.
РЭМ-изображения сколов спеченных керамических образцов ZnO:Al, синтезированных с использованием различных шликеров: а – шликер 1; б – шликер 2; в – шликер 3; г – шликер 4.
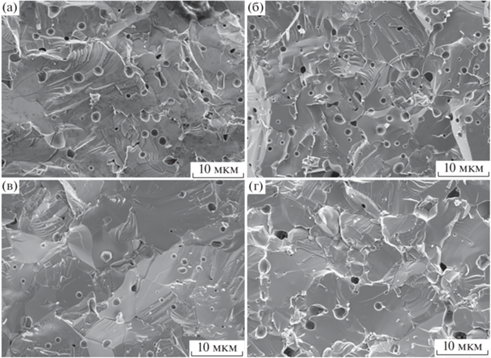
Ранее в [14] было показано, что согласно модели роста зерен, в ходе уплотнения на промежуточной стадии спекания исходная пористость заготовки влияет на распределение пор по размерам в спеченном образце – спекание более пористой заготовки приводит к формированию в конечной керамике более крупных пор, однако их концентрация при этом снижается.
Отсутствие на представленных РЭМ-изображениях композиционного контраста может свидетельствовать об отсутствии локализованной самостоятельной примесной фазы в керамике, т.е. примесь алюминия растворяется в кристаллической решетке ZnO в ходе высокотемпературного отжига [10]. О растворении примеси алюминия в ZnO также свидетельствует тот факт, что в результате отжига шликерных заготовок на воздухе цвет всех керамических образцов изменяется от белого до однородного серо-зеленого (рис. 1в), а их удельная электропроводность после отжига больше 104 См/м, что приемлемо при их использовании в качестве мишени для магнетронного распыления на постоянном токе.
Исследование спеченных образцов методом рентгеновской дифракции показало (рис. 3), что в керамических образцах, приготовленных из шликеров 1, 2 и 3, присутствует единственная фаза – ZnO со структурой вюрцита (карточка PDF № 00-036-1451), а в образце, полученном из шликера 4, наряду с рефлексами ZnO обнаруживаются незначительные рефлексы, которые можно отнести к фазе шпинели ZnAl2O4 (карточка PDF № 98-000-9559). Можно предположить, что длительная обработка шликера в шаровой мельнице приводит к увеличению содержания Al2O3 за счет частичного намола материала мелющих тел. Такой намол может привести к тому, что содержание примеси в системе заметно превысит значение предельной растворимости Al в ZnO. Согласно [15] предельная растворимость Al в ZnO не превышает 3 моль. %.
Рис. 3.
Дифрактограммы спеченных керамических образцов, синтезированных с использованием различных шликеров. Нумерация кривых соответствует нумерации шликеров; незначительные рефлексы, отмеченные знаком ◆ на дифрактограмме 4, относятся к фазе шпинели ZnAl2O4.
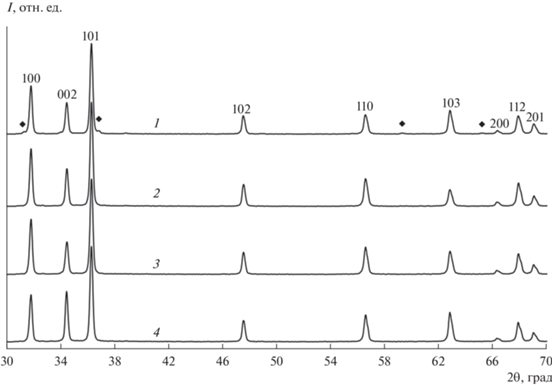
На представленных дифрактограммах видно, что также меняется интенсивность рефлекса 002 по сравнению с соседними рефлексами 100 и 101 при переходе от одного образца к другому. Так как дифрактограммы всех образцов снимали с поверхности, параллельной плоскости основания литейной гипсовой формы, по отклонению соотношения I100/I002 от стандартного значения можно судить о формирующейся на этапе заливки текстуры в шликере [16]. Согласно данным, представленным в табл. 2, при высоком значении показателя кислотности (шликер 1) соотношение I100/I002 = 0.907 значительно меньше стандартного значения 1.295. При снижении кислотности шликера это соотношение становится больше стандартного значения. В то же время с увеличением времени помола шликера степень отклонения соотношения I100/I002 от стандартного уменьшается. Данное явление можно объяснить влиянием показателя кислотности шликера на преимущественную укладку микрочастиц ZnO, имеющих анизотропную форму (рис. 1а). В случае высокого pH при заливке шликера микрочастицы ZnO укладываются так, что ось с кристаллитов преимущественно направлена перпендикулярно плоскости основания литейной формы. При снижении pH проявляется преимущественная ориентация оси с в плоскости, параллельной основанию литейной формы. В свою очередь, с увеличением времени помола анизотропия формы микрочастиц ZnO должна уменьшаться, и влияние показателя кислотности на преимущественную укладку должно снижаться.
Таблица 2.
Данные измерений спеченных керамических образцов методом рентгеновской дифракции
№ шликера | hkl | I, имп. | I100/I002* | 2θ, град | Параметры решетки, нм | с/а** |
---|---|---|---|---|---|---|
1 | 100 | 764 | 0.907 | 31.741 | a = 0.3252 ± 0.0002 | 1.6029 |
002 | 842 | 34.375 | c = 0.5213 ± 0.0002 | |||
2 | 100 | 955 | 1.718 | 31.745 | a = 0.3252 ± 0.0002 | 1.6015 |
002 | 556 | 34.410 | с = 0.5208 ± 0.0002 | |||
3 | 100 | 1011 | 1.511 | 31.743 | a = 0.3252 ± 0.0002 | 1.6018 |
002 | 669 | 34.402 | с = 0.5209 ± 0.0002 | |||
4 | 100 | 833 | 1.520 | 31.746 | a = 0.3252 ± 0.0002 | 1.6024 |
002 | 548 | 34.391 | с = 0.5211 ± 0.0002 |
В табл. 2 также представлены данные об угловом положении рефлексов 100 и 002 и вычисленные значения параметров a и c гексагональной кристаллической решетки ZnO и их отношение c/a. Сравнивая между собой отношения I100/I002 и c/a в зависимости от характеристик шликера, можно сделать вывод, что наблюдаемые вариации значений c/a и их отклонения от табличного значения (PDF № 00-036-1451), по-видимому, обусловлены в первую очередь анизотропной укладкой микрочастиц ZnO в исходных шликерных заготовках и связанным с этим различием влияния сжимающих макронапряжений, возникающих в ходе спекания, на параметр c.
ЗАКЛЮЧЕНИЕ
Исследован процесс получения проводящей керамики ZnO:Al (2 ат. %) методом шликерного литья в гипсовые формы с последующим высокотемпературным отжигом в открытой атмосфере. Изучение связи технологических параметров шликера с финальной микроструктурой спеченной керамики выявило влияние показателя кислотности шликера на преимущественную укладку частиц ZnO анизотропной формы при заливке шликера в форму. Время помола шликера снижает такое влияние и увеличивает плотность шликерной заготовки. Продемонстрировано, что при pH 9 и времени помола 16 ч в результате двухчасового отжига при 1400°С формируется проводящая керамика ZnO:Al (2 ат. %) плотностью около 5.45 г/см3 (ρотн > 97%). Такая плотность достаточна для мишеней, используемых при магнетронном осаждении функциональных слоев энергосберегающих покрытий и прозрачных электродов тонкопленочных преобразователей солнечной энергии в промышленных масштабах. Принимая во внимание известные преимущества шликерного метода формования керамики, можно заключить, что полученные результаты делают актуальным проведение дальнейших работ по оптимизации процесса получения высокоплотных проводящих керамических мишеней на основе ZnO.
Список литературы
Sun K., Tang X., Yang Ch., Jin D. // Ceram. Int. 2018. V. 44. P. 19597. https://doi.org/10.1016/j.ceramint.2018.07.207
Pietruszka R., Witkowski B.S., Ozga M., Gwozdz K., Placzek-Popko E., Godlewski M. // Beilstein J. Nanotechnol. 2021. V. 12. P. 766. https://doi.org/10.3762/bjnano.12.60
Linss V. // Surf. Coat. Technol. 2016. V. 290. P. 43. https://doi.org/10.1016/j.surfcoat.2015.09.051
Bingel A., Füchsel K., Kaiser N., Tünnermann A. // Adv. Opt. Techn. 2014. V. 3. P. 103. https://doi.org/10.1515/aot-2013-0044
Abduev A.K., Asvarov A.S., Akhmedov A.K., Zobov M.E., Kramynin S.P. // Tech. Phys. Lett. 2015. V. 41. P. 124. https://doi.org/10.1134/S1063785015020029
Liu H., Gao M., Yang B., Chen H., Zhang H., Zhang H. // Ceram. Int. 2020. V. 46. P. 6311. https://doi.org/10.1016/j.ceramint.2019.11.103
Akhmedov A.K., Abduev A.K., Asvarov A.S., Muslimov A.E., Kanevsky V.M. // Tech. Phys. Lett. 2019. V. 45. P. 773. https://doi.org/10.1134/S1063785019080030
Sun Y.H., Xiong W.H., L Ch.H.i, Yuan L. // J. Am. Ceram. Soc. 2009. V. 92. P. 2168. https://doi.org/10.1111/j.1551-2916.2009.03178.x
Sun Y.-H., Xiong W.-H., Li Ch.-H. // Trans. Nonferrous Met. Soc. Chin. 2010. V. 20. P. 624. https://doi.org/10.1016/S1003-6326(09)60189-8
Wu M.-W., Liu D.-S., Sua Y.-H. // J. Eur. Ceram. Soc. 2012. V. 32. P. 3265. https://doi.org/10.1016/j.jeurceramsoc.2012.04.030
Xu J.-W., Yang Z.-P., Wang H., Yang L., Yuan Ch. // J. Mater. Sci.: Mater. Electron. 2015. V. 26. P. 3819. https://doi.org/10.1007/s10854-015-2908-4
Nakanishi K. // Handbook of Sol-Gel Science and Technology / Ed. Klein L., Aparicio M., Jitianu A. Cham: Springer, 2016. https://doi.org/10.1007/978-3-319-19454-7_38-1
O'Donnell R.G., Yousuff M., Palamara J. // J. Aust. Ceram. Soc. 2012. V. 48. P. 133.
Occhionero M.A., Halloran J.W. // Materials Science Research / Ed. Kuczynski G.C., Miller A.E., Sargent G.A. Boston: Springer, 1984. Vol. 16. P. 89. https://doi.org/10.1007/978-1-4613-2761-5_7(1984)
Zhang Y., Wang W., Tan R., Yang Y., Zhang X., Cui P., Song W. // Int. J. Appl. Ceram. Technol. 2012. V. 9. P. 374. https://doi.org/10.1111/j.1744-7402.2011.02666.x
Li J., Da N., Jiang M., Hun K., Kwang K., Shim B. // Ceram. Int. 2007. V. 33. P. 107. https://doi.org/10.1016/j.ceramint.2005.08.005
Дополнительные материалы отсутствуют.
Инструменты
Поверхность. Рентгеновские, синхротронные и нейтронные исследования