Поверхность. Рентгеновские, синхротронные и нейтронные исследования, 2022, № 11, стр. 49-56
Формирование и рост зернограничных (αTi)-слоев и их твердость в сплавах Ti–Cr
А. С. Горнакова a, *, Н. С. Афоникова a, Е. Ю. Постнова a, А. Н. Некрасов b, Б. Б. Страумал a, **
a Федеральное государственное бюджетное учреждение науки
Институт физики твердого тела имени Ю.А. Осипьяна Российской академии наук
142432 Черноголовка, Россия
b Институт экспериментальной минералогии им. Д.С. Коржинского РАН
142432 Черноголовка, Россия
* E-mail: alenahas@issp.ac.ru
** E-mail: straumal@issp.ac.ru
Поступила в редакцию 12.04.2022
После доработки 11.05.2022
Принята к публикации 11.05.2022
- EDN: RJMODM
- DOI: 10.31857/S1028096022110103
Аннотация
Структура сплавов Ti–2 мас. % Cr, Ti–4 мас. % Cr и Ti–5.5 мас. % Cr, отожженных в условиях, соответствующих двухфазной области (α + β) фазовой диаграммы Ti–Cr, исследована с помощью растровой электронной микроскопии, рентгеноструктурного анализа и микроиндентирования. Целью работы было исследование образования и роста слоев фазы (αTi) на границах зерен (βTi)/(βTi). По результатам рентгеноструктурного анализа все образцы содержали после отжига фазы (αTi) и (βTi). Для каждого сплава были определены температуры, при которых на границах зерен формируются непрерывные слои фазы (αTi). Были измерены толщина и твердость этих слоев. Установлено, что чем выше содержание хрома, тем более твердыми являются как (αTi), так и (βTi). Твердость фазы (αTi) в сплаве Ti–5.5 мас. % Cr не зависит от температуры отжига, но твердость фазы (βTi) увеличивается с понижением температуры отжига.
ВВЕДЕНИЕ
Титановые сплавы имеют широкий спектр применения в различных областях промышленности [1–3]. Особое место среди них занимают двухфазные титановые сплавы [4, 5]. Варьирование их состава, а также термическая и механическая обработка позволяют управлять их свойствами, добиваясь заданных характеристик. Титановые сплавы с добавлением хрома до 10 мас. % относятся к β-титановым сплавам, которые привлекательны для биомедицинских приложений, поскольку для них характерен низкий модуль Юнга, близкий к значениям модуля Юнга натуральной кости [6–10].
Наличие в системе Ti–Cr двух фаз позволяет наблюдать такое явление, как зернограничное смачивание. Данное явление представляет собой процесс, когда при термической обработке граница зерен (оба зерна относятся к одной и той же фазе) заменяется слоем другой фазы, отличной от зерна. В результате вместо одной границы зерен, образуется две межфазные границы. Таким образом, явление зернограничного смачивания приводит к изменению физико-механических свойств материала. Впервые фазовые переходы между полным и неполным смачиванием в жидкостях были описаны в работе [11]. Было предсказано, что в любой двухфазной смеси жидкостей вблизи их критической точки краевые углы с любой третьей фазой должны стать равными нулю. Позднее [12, 13] был рассмотрен случай, когда капля жидкости растекается по поверхности. В зависимости от значения контактного угла могут возникнуть две ситуации. Если контактный угол равен нулю, то смачивание полное и капля растекается по поверхности. С другой стороны, если контактный угол находится в интервале от 0° до 180°, то капля не растекается (это – случай частичного или неполного смачивания). Переход смачивания – это поверхностный фазовый переход от частичного к полному смачиванию. Связь между явлением смачивания границ зерен в металлах и углом их разориентации подробно описана, например, для системы Fe–30 мас. % Mn–10 мас. % Cu [14]. Чем меньше угол разориентации границ зерен, тем больше границ остается несмоченными или сухими. Подробные обзоры по смачиванию границ зерен жидкой и твердой фазами в многокомпонентных сплавах представлены в работах [15–17]. Фазовое превращение смачивания границ зерен может быть, как первого, так и второго рода. Наличие таких фазовых превращений впервые наблюдали в системе Zn–Al [18], а затем – в системах Zn–Sn, Zn–In [19] и Zr–Nb [20]. Вторая (смачивающая) фаза может быть, как в жидком, так и в твердом состоянии. К настоящему времени опубликовано несколько работ по явлению смачивания границ зерен второй твердой фазой в бинарных титановых сплавах, в которых детально изучена микроструктура сплавов с различным содержанием второго компонента (медь, кобальт, железо), предварительно отожженных в условиях, соответствующих двухфазной области (α + β) фазовых диаграмм [21–24]. Показано, что вид второго компонента и его количество существенно влияют на явления смачивания границ зерен. Поэтому вопрос смачивания на границах зерен, а также механических свойств (например, твердости) фаз (αTi) и (βTi) в титановых сплавах по-прежнему остается актуальным. Целью настоящей работы было изучение смачивания границ зерен в отожженных сплавах Ti–Cr с закалкой из двухфазной области (α + β) фазовой диаграммы Ti–Cr, и измерение твердости фазы (βTi), а также зернограничных прослоек (αTi).
МАТЕРИАЛЫ И МЕТОДЫ
В работе исследованы двухкомпонентные титановые сплавы, содержащие 2, 4 и 5.5 мас. % хрома (“по шихте”). Сплавы были изготовлены из титана марки ТИ-1 чистотой 99.98% и хрома чистотой 99.99% методом левитационной индукционной плавки в атмосфере чистого аргона. Компонентный состав всех образцов после выплавки был проверен с помощью рентгеновского микроанализа и составил (точные данные о составе по результатам РЭМ указаны в скобках): Ti–2 мас. % Cr (Ti–2.09 ± 0.06 мас. % Cr), Ti–4 мас. % Cr (Ti–3.81 ± 0.08 мас. % Cr) и Ti–5.5 мас. % Cr (Ti–5.58 ± 0.15 мас. % Cr).
Из полученных цилиндрических слитков диаметром 10.0 мм вырезали шайбы толщиной 2.0 мм. Затем каждый образец запаивали в кварцевую ампулу и отжигали в вакууме при остаточном давлении 4 × 10–4 Па. Отжиг проводили в условиях, соответствующих двухфазной области (α + β) диаграммы состояния титан-хром: при температурах 665°С (1032 ч), 690°С (840 ч), 730°С (768 ч), 770°С (1200 ч) и 810°С (720 ч).
После закалки в воде (вместе с ампулой) образцы последовательно шлифовали на шлифовальной бумаге из карбида кремния зернистостью от 220 до 2000 грит (размер зерна 68 и 10 мкм соответственно), после чего полировали с помощью алмазных паст зернистостью 6, 3 и 1 мкм. Структуру поликристаллических образцов исследовали с помощью оптического микроскопа Neophot-32 со встроенной камерой Canon Digital Rebel XT 10 Мпикс. Для компонентного анализа и получения изображений использовали растровые электронные микроскопы Tescan Vega TS5130 MM Oxford Instruments и Supra 50VP с системой микроанализа INCA Energy+, оснащенные энергодисперсионным спектрометром Oxford Instruments. Для фазового анализа образцов использовали рентгенограммы, полученные на рентгеновском дифрактометре Siemens D-500 с использованием излучения CuKα1. Измерения микротвердости проводили на приборе ПМТ-3 с индентором Виккерса. Микротвердость измеряли в объеме зерен (βTi) и в зернограничных слоях (αTi). Измерения микротвердости проводились при нагрузке Р = 20 г для образца, отожженного при 690°С, и при нагрузке Р = 50 г для всех остальных образцов. Выбор значения нагрузки зависел от толщины зернограничного слоя, поэтому при более низкой температуре отжига 690°С, когда слой более тонкий, нагрузка на индентор меньше, а также чтобы исключить влияние межфазных границ (βTi)/(αTi). Значения микротвердости усредняли по десяти независимым экспериментам для каждой фазы.
РЕЗУЛЬТАТЫ И ОБСУЖДЕНИЕ
Структура и фазовый состав исходных сплавов
На рис. 1 представлены РЭМ-изображения литых сплавов Ti–2 мас. % Cr (а), Ti–4 мас. % Cr (b) и Ti–5.5 мас. % Cr (c), сделанные в режиме обратно-рассеянных электронов. Вследствие того, что фазовый контраст в литых сплавах слабый, что легко объяснимо равномерным распределением хрома в титане после литья, в качестве примера мы отметили пунктирными линиями границы зерен в сплаве Ti–2 мас. %Cr (рис 1а). Видно, что сплав является поликристаллом с крупными зернами, на границах зерен нет выделений второй фазы (αTi). Исследуемые сплавы содержат две фазы (рис. 2), доля (βTi)-фазы увеличивается с увеличением концентрации хрома в сплаве (табл. 1), а параметры решетки фаз (αTi) и (βTi) меняются незначительно.
Структура и фазовый состав отожженных сплавов
Серия РЭМ-изображений на рис. 3 демонстрирует зависимость структуры трех исследованных сплавов от температуры отжига. Образцы состоят из зерен (βTi)-фазы и колоний (αTi)-фазы внутри этих зерен. При повышении температуры эти колонии разрушаются и образуют прослойки (αTi) фазы на границах зерен (βTi)/(βTi). Видно, что первые границы зерен (βTi)/(βTi) полностью покрытые (αTi)-фазой, появляются в трех изученных сплавах при разных температурах отжига.
Рис. 3.
РЭМ-изображения отожженных сплавов Ti–2 мас. % Cr (а–д), Ti–4 мас. % Cr (е–к) и Ti–5.5 мас. % Cr (л–п).
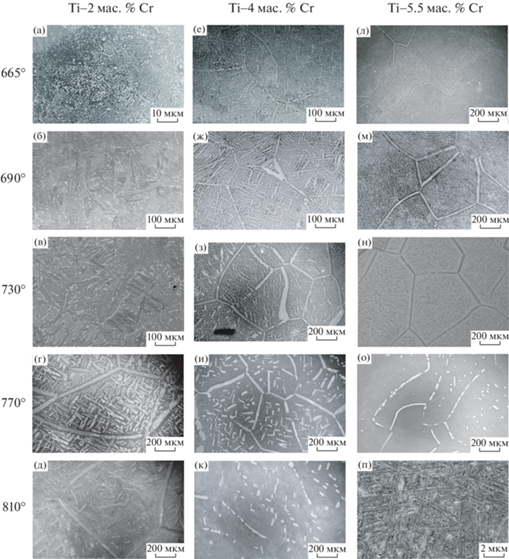
В табл. 2 представлены результаты рентгеноструктурного анализа для трех отожженных сплавов при трех различных температурах. Заметные изменения можно наблюдать только в параметре решетки a кубической (βTi)-фазы, в которой значения a изменяются от минимального значения 0.3220 нм до максимального 0.3231 нм. Доля (βTi)-фазы в образцах увеличивается с увеличением содержания хрома, в соответствии с фазовой диаграммой. Образец сплава Ti–5.5 мас. % Cr, отожженный при 810°С, сильно текстурирован, имеет игольчатую форму, a линии (αTi)-фазы на рентгенограмме сильно размыты при больших углах отражения. Все это свидетельствует о том, что (αTi)-фаза является (α'Ti)-мартенситом. Таким образом, условия отжига этого образца соответствовали не двухфазной области (α + β) фазовой диаграммы, а однофазной (β). При закалке в образце сплава Ti–5.5 мас. % Cr образовался мартенсит, и зернограничного смачивания в нем не происходило. В дальнейшей работе этот образец не рассматривали.
Таблица 2.
Параметры решеток (αTi) и (βTi) фаз и их объемная доля в отожженных сплавах
Концентрация хрома, мас. % | T, °C | Параметры решетки α-фазы, нм |
Параметр решетки β-фазы, нм |
Объемная доля β-фазы, % |
---|---|---|---|---|
2 | 665 | a = 0.2949; c = 0.4690 | a = 0.3229 | 8 |
730 | a = 0.2950; c = 0.4686 | a = 0.3226 | 1 | |
810 | a = 0.2949; c = 0.4685 | a = 0.3225 | 3 | |
4 | 665 | a = 0.2950; c = 0.4688 | a = 0.3230 | 14 |
730 | a = 0.2950; c = 0.4686 | a = 0.3222 | 8 | |
810 | a = 0.2950; c = 0.4686 | a = 0.3225 | 16 | |
5.5 | 665 | a = 0.2949; c = 0.4689 | a = 0.3231 | 24 |
730 | a = 0.2951; c = 0.4689 | a = 0.3220 | 18 | |
810 | a = 0.2950; c = 0.4686 | a = 0.3226 | 3 |
Для проверки компонентного состава в зерне и зернограничном слое (αTi)-фазы был проведен химический анализ поперек границы (βTi)/(βTi) в образце сплава Ti–5.5 мас. % Cr, отожженного при 730°C. (рис. 4а). Результат (рис. 4б) показал, что зернограничный слой (αTi)-фазы содержит около 0.3 мас. % хрома. На рис. 4в представлены температурные зависимости средней толщины зернограничного слоя 2Δ в трех исследованных сплавах. Для сплава Ti–4 мас. % Cr средняя толщина зернограничной прослойки (αTi)-фазы увеличивается с увеличением температуры отжига примерно втрое. В сплавах Ti–2 мас. % Cr и Ti–5.5 мас. % Cr значения 2Δ уменьшаются по мере приближения к линии транзуса (т.е. границы β и α + β областей на фазовой диаграмме). На рис. 4г видно небольшое увеличение среднего размера зерна с ростом температуры отжига во всех образцах.
Рис. 4.
РЭМ-изображения сплава Ti–5.5 мас. % Cr, отожженного при 730°C (а). Темно-серые области соответствуют (αTi)-фазе, светло-серые области соответствуют (βTi). Точками 1–7 обозначены области образца, в которых была определена концентрации титана и хрома (б). Температурные зависимости толщины зернограничного слоя 2Δ (в) и среднего размера зерен (г) в сплавах Ti–2 мас. % Cr, Ti–4 мас. % Cr и Ti–5.5 мас. % Cr.
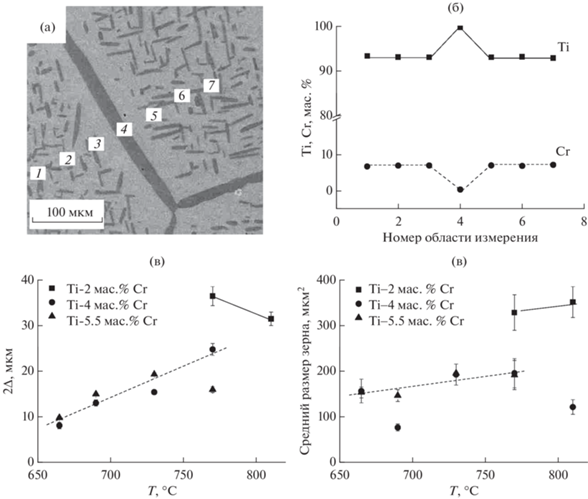
Микротвердость отожженных сплавов
В работе была измерена микротвердость зернограничных прослоек (αTi)-фазы (они выглядят темно-серыми на рис. 4а) и зерен (βTi) (рис. 4а светло-серые области). На рис. 5 показаны результаты этих измерений.
Рис. 5.
Значения микротвердости фаз (αTi) и (βTi): а) в сплавах Ti–2 мас. % Cr (треугольники), Ti–4 мас. % Cr (круги) и Ti–5.5 мас. % Cr (квадраты), отожженных при 770°С (1200 ч); б) В сплаве Ti–5.5 мас. % Cr, отожженном при: 690°С (840 ч) (черные символы), 730°С (768 ч) (темно-серые символы) и 770°С (1200 ч) (светло-серым).
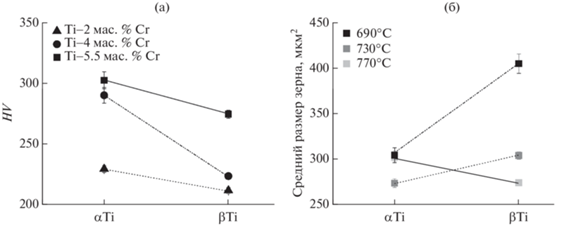
Значения микротвердости фаз (αTi) и (βTi) для трех исследованных сплавов, отожженных при одной и той же температуре 770°С (1200 ч), показали, что увеличение содержания хрома в (αTi) и (βTi) твердых растворах приводит к увеличению микротвердости (αTi) и (βTi) фаз (рис. 5а). Согласно фазовой диаграмме Ti–Cr, при одной и той же температуре отжига изменяется доля фаз в сплавах, а состав фаз должен оставаться неизменным. Хотя условия отжига и закалки сплавов были одинаковы, закалка, скорее всего, оказывает основное влияние на компонентный состав фаз, т.е. долю хрома в каждой фазе в каждом сплаве, структуру и морфологию, а значит, и на микротвердость фаз.
Если рассматривать сплав Ti–5.5 мас. % Cr (рис. 5б), отожженный при разных температурах, то мы видим, что значения микротвердости (αTi)-фазы изменяются от 270 до 300 HV, а для (βTi)-фазы они находятся в пределах от 270 до 400 HV. Микротвердость обеих фаз увеличивается с повышением температуры отжига. Предел растворимости хрома в (αTi) изменяется с ростом температуры очень незначительно, поэтому мало изменяется и микротвердость. При этом состав (βTi)-фазы существенно меняется. При температуре отжига 690°С (черные квадраты на рис. 5б) содержание хрома в твердом растворе (βTi,Cr) составляет ~9 мас. %, при 730°С оно равно ~7 мас. % (темно-серые квадраты), а при 770°С составляет ~5 мас. % (светло-серые квадраты). Таким образом, с помощью отжига в условиях, соответствующих двухфазной области (αTi + βTi), и с добавлением большего количества хрома, можно повысить общую твердость материала за счет твердого раствора (βTi,Cr).
Морфологию взаимного расположения фаз анализировали по серии РЭМ-изображений, приведенных на рис. 3. В качестве примера на рис. 6а стрелкой (GBW) показана граница зерен (βTi)/(βTi), полностью смоченная прослойкой фазы (αTi). Другой стрелкой (GBNW) показана граница зерен (βTi)/(βTi), не полностью (частично) смоченная прослойкой фазы (αTi). На рис. 6б для трех исследованных сплавов показаны температурные зависимости доли границ зерен (βTi)/ (βTi), полностью смоченных прослойкой фазы (αTi).
Рис. 6.
(а) РЭМ-изображение сплава Ti–5.5 мас. % Cr, отожженного при температуре 690°C. Темно-серые области соответствуют (αTi)-фазе, а светло-серые области соответствуют (βTi)-фазе. Стрелкой и символом GBW показана граница зерен (βTi)/(βTi), полностью смоченная прослойкой фазы (αTi). Другой стрелкой и символом GBNW показана граница зерен (βTi)/(βTi), неполностью (частично) смоченная прослойкой фазы (αTi). (б) Температурная зависимость доли границ зерен (βTi)/(βTi), полностью смоченных прослойкой фазы (αTi) в сплавах Ti–2 мас. % Cr (квадраты), Ti–4 мас. % Cr (кружки) и Ti–5.5 мас. % Cr (треугольники).

При малых концентрациях второго компонента (2 мас. % Cr) первые границы зерен (βTi)/(βTi), полностью смоченные прослойкой фазы (αTi), появляются при приближении температуры отжига к линии транзуса, а их доля скачкообразно изменяется от 0 до 80%. В двух других сплавах доля границ зерен (βTi)/(βTi), полностью смоченных прослойками фазы (αTi), наоборот, понижается с увеличением температуры. Стопроцентного смачивания границ зерен (βTi)/(βTi) прослойками фазы (αTi) (как в работах [21–24]) зафиксировать не удалось. Вероятно, это связано со сложной морфологией фаз в титановых сплавах. В литом состоянии зерна фазы (βTi) содержат колонии ламелей (αTi)-фазы [4], а температурная обработка сплава приводит к коагуляции ламелей и их росту. Кроме того, изоляция на границах зерен, т.е. образование прослоек (αTi)-фазы по границам зерен, происходит скачком, и измерить толщину зернограничного слоя (αTi) становится возможным только тогда, когда он делается заметным в растровом микроскопе. Возможно, что максимум смачивания в 80% связан со спектром разориентации границ зерен, от малоугловых до большеугловых границ. Так, в статье [14] подробно рассмотрено явление смачивания границ зерен в сплаве Fe–30% Mn–10% Cu и показано, что оно связано с разориентацией зерен, как это было показано и на индивидуальных границах зерен в системе Zn–Al [18]. К сожалению, из-за мартенситных превращений в титане очень сложно оценить даже методом дифракции обратного рассеяния электронов разориентацию зерен в поликристаллических титановых сплавах. В статье [25] был разработан метод определения ориентации высокотемпературной β-фазы по измеренным данным обратного рассеяния электронов для низкотемпературной α-фазы в сплаве Ti–6Al–4V. Следовательно, по доле полностью смоченных границ зерен можно косвенно оценить долю мало- и большеугловых границ зерен (границы зерен с разориентацией от 15° до 50° будут смачиваться в первую очередь) и оценить твердость материала зная состав сплава.
ВЫВОДЫ
Исследованы структура и морфология титановых сплавов Ti–2 мас. % Cr, Ti–4 мас. % Cr и Ti–5.5 мас. % Cr, отожженных в условиях, соответствующих двухфазной области (α + β) фазовой диаграммы Ti–Cr. Определен средний размер зерен для каждого отожженного образца и установлено, что самые крупные зерна в сплаве с 2 мас. % Cr имеют величину ~350 мкм. Измерена толщина слоев фазы (αTi) на границах зерен (βTi)/(βTi), при повышении температуры отжига на ~100°С она увеличивается втрое. Для каждого сплава при всех температурах отжига определяли долю границ зерен (βTi)/(βTi), полностью покрытых (смоченных) прослойками фазы (αTi). Максимальное значение доли полностью смоченных границ зерен (βTi)/(βTi) составляет 80%. Значение твердости по Викерсу фазы (αTi) не зависит от температуры отжига, но чем ниже температура отжига, тем выше значение твердости фазы (βTi). Установлено, что чем больше доля второго компонента в сплаве, тем тверже фазы (αTi) и (βTi).
Список литературы
Zwicker U. Titanium and Titanium Alloys. Berlin: Springer, 1974. 717 p.
Lütjering G., Williams J.C. Titanium. 2nd Edn. Berlin: Springer, 2007. 435 p.
Veiga C., Davim J.P., Loureiro A.J.R. // Rev. Adv. Mater. Sci. 2012. V. 32. P. 133.
Chrapoński J., Szkliniarz W. // Mater. Charact. 2001. V. 46. P. 149. https://www.doi.org/10.1016/S1044-5803(01)00117-6
Salihu S.A., Suleiman I.Y. // IOSR J. Appl. Phys. 2019. V. 11. P. 35. https://www.doi.org/10.9790/4861-1102013539
Shinohara Yu., Ishigaki T., Inamura T., Kanetaka H., Miyazaki Sh., Hosoda H. // Mater. Sci. Forum. 2010. V. 654–656. P. 2122. https://www.doi.org/10.4028/www.scientific.net/ MSF.654-656.2122
Kusano Y., Inamura T., Hosoda H., Wakashima K., Miyazaki S. // Adv. Mat. Res. 2010. V. 89–91. P. 307. https://www.doi.org/10.4028/www.scientific.net/ AMR.89-91.307
Kiryukhantsev-Korneev F.V., Sheveiko A.N., Komarov V.A., Blanter M.S., Skryleva E.A., Shirmanov N.A., Levashov E.A., Shtansky D.V. // Russ. J. Non-Ferr. Met. 2011. V. 52. P. 311. https://www.doi.org/10.3103/S1067821211030138
Murayama Y., Sasaki Sh., Kimura H., Chiba A. // Mater. Sci. Forum. 2010. V. 638–642. P. 635. https://www.doi.org/10.4028/www.scientific.net/ MSF.638-642.635
Nakai M., Niinomi M., Hieda J., Shibata T. // ISIJ Internat. 2012. V. 52. P. 1655. https://www.doi.org/10.2355/isijinternational.52.1655
Cahn J.W. // J. Chem. Phys. 1977. V. 66. P. 3667. https://www.doi.org/10.1063/1.434402
Bonn D., Ross D. // Rep. Prog. Phys. 2001. V. 64. P. 1085. https://www.doi.org/10.1088/0034-4885/64/9/202
Bonn D., Ross D., Bertrand E., Ragil K., Shahidzadeh N., Broseta D., Meunier J. // Physica A. 2002. V. 306. P. 279. https://www.doi.org/10.1016/S0378-4371(02)00505-8
Takashima M., Wynblatt P. Adams B.L. // Interface Sci. 2000. V. 8. P. 351. https://www.doi.org/10.1023/A:1008727728076
Straumal B.B., Korneva A., Lopez G.A., Kuzmin A., Rabkin E., Gerstein G., Straumal A.B., Gornakova A.S. // Materials. 2021. V. 14. P. 7506. https://www.doi.org/10.3390/ma14247506
Straumal B.B., Korneva A., Kuzmin A., Lopez G.A., Rabkin E., Straumal A.B., Gerstein G., Gornakova A.S. // Metals. 2021. V. 11. P. 1881. https://www.doi.org/0.3390/met11111881
Straumal B., Rabkin E., Lopez G.A., Korneva A., Kuzmin A., Gornakova A., Straumal A., Baretzky B. // Crystals. 2021. V. 11. P. 1540. https://www.doi.org/10.3390/cryst11121540
Straumal B.B., Gornakova A.S., Kogtenkova O.A., Protasova S.G., Sursaeva VG, Baretzky B. // Phys. Rev. B. 2008. V. 78. P. 054202. https://www.doi.org/10.1103/PhysRevB.78.054202
Gornakova A.S., Straumal B.B., Tsurekawa S., Chang L.-S., Nekrasov A.N. // Rev. Adv. Mater. Sci. 2009. V. 21. P. 18.
Straumal B.B., Gornakova A.S., Kucheev Y.O., Baretzky B., Nekrasov A.N. // J. Mater. Eng. Perform. 2012. V. 21. P. 721. https://www.doi.org/10.1007/s11665-012-0158
Gornakova A.S., Prokofiev S.I., Straumal B.B., Kolesnikova K.I. // Russ. J. Non-Ferr. Met. 2016. V. 57. P. 703. https://www.doi.org/10.3103/S1067821216070099
Straumal B.B., Gornakova A.S., Prokofjev S.I., Afonikova N.S., Baretzky B., Nekrasov A.N., Kolesnikova K.I. // J. Mater. Eng. Perform. 2014. V. 23. P. 1580. https://www.doi.org/10.1007/s11665-013-0789-3
Gornakova A.S., Straumal B.B., Nekrasov A.N., Kilmametov A., Afonikova N.S. // J. Mater. Eng. Perform. 2018. V. 27. P. 4989. https://www.doi.org/10.1007/s11665-018-3300-3
Gornakova A.S., Prokofiev S.I., Kolesnikova K.I., Straumal B.B. // Russ. J. Non-Ferr. Met. 2016. V. 57. P. 229. https://www.doi.org/10.3103/S106782121603007X
Glavicic M.G., Kobryn P.A., Bieler T.R., Semiatin S.L. // Mater. Sci. Eng. A. 2003. V. 346. P. 50. https://www.doi.org/10.1016/S0921-5093(02)00535-X
Дополнительные материалы отсутствуют.
Инструменты
Поверхность. Рентгеновские, синхротронные и нейтронные исследования