Поверхность. Рентгеновские, синхротронные и нейтронные исследования, 2022, № 11, стр. 57-62
Низкотемпературное комплексное модифицирование поверхности титановых сплавов
А. А. Николаев a, *, А. Ю. Назаров a, Э. Л. Варданян a, Р. Ш. Нагимов a, В. В. Денисов b
a Уфимский государственный авиационный технический университет
450000 Уфа, Республика, Башкортостан, Россия
b Институт сильноточной электроники СО РАН
634055 Томск, Россия
* E-mail: Nikolaev.aa@ugatu.su
Поступила в редакцию 28.02.2021
После доработки 01.04.2022
Принята к публикации 04.04.2022
- EDN: VVQHFU
- DOI: 10.31857/S1028096022110164
Аннотация
Приведены результаты исследования изменения микротвердости, химического состава в поверхностных слоях двухфазных титановых сплавов после комплексной модификации в плазме повышенной плотности. Комплексная модификация поверхности в едином вакуумном цикле включает следующие операции: ионную очистку поверхности и нагрев образца в аргоновой плазме, нанесение нитридообразующих элементов на поверхность и низкотемпературное (не более 550°С) азотирование в плазме повышенной плотности. Для определения влияния режимов комплексной модификации на характеристики поверхностных слоев были исследованы фазовый и элементный состав, микротвердость поверхностного слоя и шероховатость. Комплексная модификация поверхности привела к значительному, до двух раз, увеличению микротвердости модифицированного слоя. Изменение микротвердости связано с образованием твердого раствора внедрения, а также нитридов титана, содержащих дисперсные частицы нитридов интерметаллических соединений титана и алюминия.
ВВЕДЕНИЕ
В большинстве случаев контактного взаимодействия самой нагруженной частью детали являются ее поверхностные слои, которые испытывают наибольшие нагрузки и подвержены значительному износу [1]. Для устранения или снижения этих недостатков применяют различные методы упрочнения поверхности [2], в том числе электронно-лучевое [3, 4], плазменное электролитическое окисление [5], химико-термическую обработку [6–8], нанесение различных видов покрытий и комбинацию этих методов [9–12]. Среди перечисленных технологий наиболее эффективным и распространенным является метод нанесения из паровой фазы (PVD – physical vapor deposition) TiN [13], ZrN [14], CrN [15], CrAlN [16], TiAlN [17–19], алмазоподобных [20] и других твердых керамических покрытий [21–23]. Однако обычные твердые покрытия легко растрескиваются и разрушаются при высоких нагрузках, что ограничивает их применение в инженерных областях [24, 25]. Для улучшения характеристик однослойных покрытий были разработаны покрытия с многослойной структурой [26–28], которые способны эффективно блокировать распространение трещин и движение дислокаций за счет введения чередующихся систем. Однако, несмотря на все преимущества многослойных покрытий, в связи с увеличением нагрузок, температур, агрессивностью сред возникает проблема растрескивания и отслаивания покрытий. На сегодняшний день установлено, что эксплуатационные свойства поверхности зависят не только от параметров самого покрытия, но и от совокупности свойств покрытия–подложки. В [29, 30] было показано, что различие модулей упругости покрытия и подложки влияет на износостойкость, особенно при знакопеременных и ударных нагрузках. В свою очередь, разработка и создание новых объемных материалов – весьма дорогостоящий и длительный процесс. Поэтому разработка или совершенствование технологий модификации поверхности для обеспечения требуемых характеристик является актуальной задачей.
В связи с вышеописанными факторами целью работы было формирование контролируемого градиента физико-механических свойств в системе подложки за счет комплексной низкотемпературной модификации поверхности в плазме повышенной плотности.
МЕТОДИКА ИССЛЕДОВАНИЙ
Для экспериментальных исследований использовали двухфазный титановый сплав ВТ9 (Ti–88.1%, Al–6.7%, Mo–3.5%, Zr–1.7%). Комплексная модификация поверхности в едином вакуумном цикле включает следующие операции (рис. 1): ионную очистку поверхности и нагрев образца в аргоновой плазме, нанесение нитридообразующих элементов (нитридообразующего покрытия) на поверхность и низкотемпературное (не более 550°С) азотирование в плазме повышенной плотности.
Нитридообразующее покрытие наносили методом ионно-плазменного осаждения (arc-PVD) с двух катодов Ti и Al в среде аргона (30 и 60 мин) на установке ННВ 6.6–И1 (рис. 2) [31]. Расчетная толщина покрытия TiAl при 30 мин осаждения ~1.5 мкм, при 60 мин ~3 мкм [31]. Низкотемпературное комплексное модифицирование поверхности проводили в плазме повышенной плотности, формируемой при помощи плазмогенератора “ПИНК” [32, 33] в газовой смеси аргона и азота при температурах 500, 550°С в течение 1 ч. Поверхность образцов предварительно была очищена в ультразвуковой ванне, непосредственно перед осаждением покрытия образцы были подвергнуты ионной очистке и нагреву в среде аргона при напряжении смещения 800 В.
Методом энергодисперсионной рентгеновской спектроскопии был изучен химический состав модифицированных слоев образцов после обработки в растровом электронном микроскопе JEOL JSM-6490LV. Микротвердость измеряли методом Виккерса на поверхности образца и по глубине на поперечных шлифах на автоматическом твердомере EMCO–Test DuraScan 50. Измерения проводили не менее чем в пяти точках и 30 мкм по горизонтали при нагрузке 50 г с шагом 5 мкм по глубине до достижения значений микротвердости основы, что обеспечивало расстояние между отпечатками минимум 2.5 их диаметра.
Качественный фазовый состав модифицированного слоя определяли методом рентгенофазового анализа. Съемку проводили на дифрактометре Rigaku Ultima IV с в геометрии Брэгга–Брентано с шагом 0.02° в областях интенсивной рентгеновской дифракции и 0.1° в областях фона. Время накопления импульсов в одной точке составляло, соответственно, 10 и 5 с.
РЕЗУЛЬТАТЫ И ИХ ОБСУЖДЕНИЕ
Исследование влияния режимов комплексной модификации поверхностного слоя титанового сплава ВТ9 на микротвердость и глубину азотированного слоя показало, что режимы предварительного нанесения покрытия существенно влияют на характеристики азотированного слоя. На рис. 3 представлены графики распределения микротвердости по глубине поверхностного слоя титанового сплава ВТ9 в зависимости от режимов комплексной модификации (времени нанесения нитридообразующего покрытия, температуры азотирования). Микротвердость измеряли при выбранной нагрузке с целью определения интегральной твердости системы покрытие–подложка.
Рис. 3.
Распределение микротвердости по глубине модифицированного слоя после обработки при: а – 500; б – 550°С.
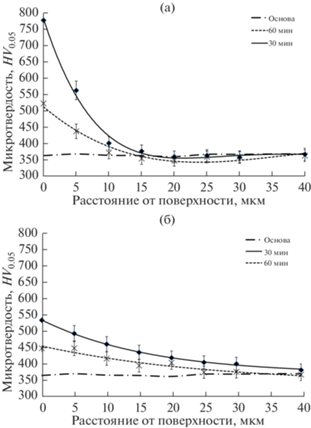
Анализ распределения микротвердости показал, что при всех режимах обработки наблюдается увеличение поверхностной микротвердости. Наибольшей поверхностной микротвердости и толщины упрочненного слоя достигают при меньшей толщине покрытия TiAl. Вероятно, такая зависимость определяется, во-первых, демпфирующими свойствами покрытия TiAl, во-вторых, снижением скорости диффузии азота сквозь покрытие большей толщины. Данное предположение объясняется тем, что в начальный момент азотирования в связи с высокой концентрацией азота на поверхности формируется сплошная нитридная пленка, затем происходит распад и распыление нитридов, массоперенос азота вглубь покрытия и материала основы. При меньшей толщине покрытия длина диффузии азота и алюминия из покрытия в материал меньше практически в два раза, поэтому массоперенос азота с поверхности происходит интенсивнее. В дальнейших исследованиях для подтверждения зависимости планируется провести эксперимент при 5 и 15 мин нанесения нитридообразующего покрытия. Сводная информация о степени упрочнения и глубине модифицированного слоя представлена в табл. 1.
Таблица 1.
Изменение физико-механических свойств в зависимости от режимов модификации
Тип обработки | Шероховатость, Ra | Поверхностная микротвердость, HV0.05 | Глубина слоя, мкм | Степень упрочнения, % |
---|---|---|---|---|
Без обработки | 0.083 | 370 | – | – |
TiAl 30 мин+ 500°C N2 | 0.215 | 777 | 13 | 110 |
TiAl 60 мин + 500°C N2 | 0.225 | 527 | 8 | 42 |
TiAl 30 мин + 550°C N2 | 0.228 | 534 | 35 | 44 |
TiAl 60 мин + 550°C N2 | 0.245 | 438 | 23 | 21 |
Также в скорость диффузии свой вклад вносят радиационные эффекты, возникающие при бомбардировке поверхности ионами аргона и азота, глубина распространения которых также ограничена и определяется в первую очередь энергетической составляющей, а также структурой и элементным составом материала. Бомбардировка ионами вводит множество точечных дефектов, дислокации в поверхностных слоях, формирование таких дефектов способствует повышению диффузии. В [6] было установлено, что энергия частиц при ионно-плазменном азотировании достаточна для создания дефектного слоя толщиной в несколько атомных слоев. Такой дефектный слой служит источником вакансий и дефектов внедрения. Даже если большинство этих дефектов будет уничтожено у поверхности, есть вероятность миграции вглубь материала, что в итоге приведет к увеличению коэффициента диффузии.
Анализ дифрактограмм (рис. 4) показал, что в ходе комплексной модификации на поверхности формируются нитриды титана и интерметаллидов системы титан–алюминий. Также смещение пиков α-титана в сторону меньших углов дифракции, их существенное уширение и снижение интенсивности свидетельствует о высокой степени дефектности в результате образования твердого раствора азота и алюминия в α-титане.
Рис. 4.
Дифрактограммы исходного образца (1) и образцов после обработки в различных режимах: при 500°С в течение 30 мин (2); 500°С, 60 мин (3); 550°С, 30 мин (4); 550°С, 60 мин (5).
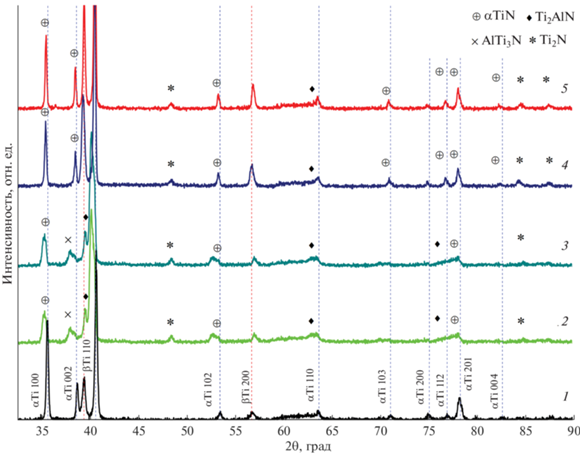
С увеличением толщины нитридообразующего покрытия характер пиков не изменяется, они отличаются только интенсивностью. В свою очередь, температура оказывает значительно влияние на фазовый состав. Комплексная модификация при температуре 500°С приводит к формированию нитридов интерметаллидов двух модификаций – AlTi3N и Ti2AlN (MAX-фаза) – и низкотемператрного нитрида титана Ti2N. В случае обработки при 550°С интенсивность и количество пиков Ti2N увеличивается, а нитридов интерметаллидов уменьшается. Данные результаты коррелируют с измерениями микротвердости. Так, при 500°С при одной толщине нитридообразующего покрытия поверхностная твердость была выше за счет наличия нитридов интерметаллидов.
Анализ микроструктуры (рис. 5) образцов при различной толщине нитридообразующего покрытия показал, что четкая граница раздела покрытие–подложка не визуализируется. Микроструктуры поверхностного слоя и объемного материала не различаются, рост зерна и выпадение дисперсных частиц по границам зерен не наблюдаются, что характерно для низкотемпературного азотирования титановых сплавов.
Рис. 5.
Микроструктура образцов после комплексной обработки при 500°С в течение: а – 30; б – 60 мин.
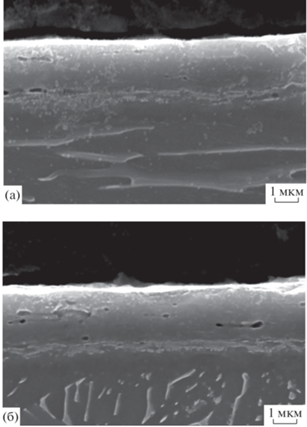
Дальнейшее исследование поверхности образца, подвергнутого комплексной обработке, проводили методом энергодисперсионной рентгеновской спектроскопии (табл. 2). Наряду с исходными элементами (Ti, Al, Zr, Mo) в обычном количестве на глубине до 5 мкм от поверхности был обнаружен градиент содержания Al от 11 до 6.7%. Градиент концентрации алюминия присутствовал на поверхности всех образцов после комплексной обработки и зависел только от глубины. Следует отметить, что технические возможности использованного прибора не позволяли детектировать азот, углерод и кислород. В легированном слое Al может присутствовать в твердом растворе, находиться в свободном состоянии, быть составной частью частиц других фаз (интерметаллических соединений с титаном и их нитридов), которые были обнаружены при рентгенофазовом анализе. В виду того, что обработка происходила при предплавильных для Al температурах (500–550°С), можно ожидать, что Al будет присутствовать на дефектах решетки (дислокациях), а также на внутрифазных и межфазных границах. Для детального исследования механизмов образования нитридных, интерметаллидных фаз, МАХ-фаз и микронапряжений в поверхностном слое в процессе комплексной ионно-плазменной обработки в дальнейшем планируется провести исследования с помощью синхротронного излучения в рамках совместного проекта с ИСЭ СО РАН, г. Томск.
Таблица 2.
Изменение химического состава по глубине модифицированного слоя (мас. %)
Спектр | N | Al | Ti | Zr | Mo | Итог |
---|---|---|---|---|---|---|
TiAl 30 мин | ||||||
2(1) | 0.00 | 9.31 | 84.19 | 3.03 | 3.46 | 100.00 |
2(2) | 0.00 | 8.66 | 84.76 | 2.89 | 3.68 | 100.00 |
2(3) | 0.00 | 8.06 | 85.71 | 3.06 | 3.18 | 100.00 |
2(4) | 0.00 | 7.64 | 85.46 | 3.56 | 3.34 | 100.00 |
2(5) | 0.00 | 7.55 | 86.87 | 2.99 | 2.59 | 100.00 |
2(6) | 0.00 | 7.14 | 86.41 | 3.29 | 3.16 | 100.00 |
2(7) | 0.00 | 6.94 | 88.09 | 2.67 | 2.30 | 100.00 |
2(8) | 0.00 | 6.93 | 85.79 | 3.77 | 3.51 | 100.00 |
2(9) | 0.00 | 6.45 | 87.42 | 2.87 | 3.26 | 100.00 |
2(10) | 0.00 | 6.74 | 87.15 | 2.81 | 3.31 | 100.00 |
TiAl 60 мин | ||||||
2(1) | 0.00 | 9.48 | 85.35 | 2.93 | 2.24 | 100.00 |
2(2) | 0.00 | 7.95 | 86.02 | 3.35 | 2.68 | 100.00 |
2(3) | 0.00 | 7.08 | 87.49 | 2.96 | 2.47 | 100.00 |
2(4) | 0.00 | 6.66 | 86.75 | 3.34 | 3.25 | 100.00 |
2(5) | 0.00 | 6.78 | 87.50 | 2.96 | 2.76 | 100.00 |
2(6) | 0.00 | 6.76 | 87.18 | 3.32 | 2.74 | 100.00 |
2(7) | 0.00 | 6.42 | 88.21 | 2.74 | 2.63 | 100.00 |
2(8) | 0.00 | 6.29 | 88.12 | 3.05 | 2.54 | 100.00 |
2(9) | 0.00 | 6.21 | 87.20 | 2.85 | 3.74 | 100.00 |
ЗАКЛЮЧЕНИЕ
В результате нанесения покрытия титана–алюминия и последующего азотирования на поверхности формируются нитридные фазы титана и интерметаллидов системы титан–алюминий. Увеличение длительности напыления нитридообразующего покрытия приводит к снижению глубины азотированного слоя и поверхностной микротвердости. Низкотемпературная ионно-плазменная обработка в сильноточном разряде не увеличивает значительно шероховатость поверхности, что позволяет использовать данную обработку как предварительную для повышения адгезионной прочности и трещиностойкости защитного покрытия и в качестве финишной операции.
Список литературы
Гудимова Е.Ю. Структурно-фазовые состояния, формируемые путем импульсного электронно-пучкового легирования танталом поверхностных слоев никелида титана, и физико-механические свойства слоевых композитов (TiNi–Ta)/TiNi: Дис. … канд. физ.-мат. наук: 01.04.07. Томск: ИФПМ СО РАН, 2015. 225 с.
Прокопец А.Д., Бажи П.М., Константинов А.С., Чижико А.П., Столин П.А. // Неорган. материалы. 2021. Т. 57. № 9. С. 986. https://doi.org/10.31857/S0002337X2109013X
Konovalov S.V., Ivanov Y.F., Zaguliaev D.V., Yakupov D.F., Ustinov A.M., Kosinov D.A. // J. Surf. Invest.: X-ray, Synchrotron Neutron Tech. 2021. V. 15. № 1. P. 183. https://doi.org/10.1134/S1027451021010262
Ivanov Y.F., Gromov V.Е., Konovalov S.V., Zagulyaev D.V., Petrikova Е.А., Semin А.P. // Успехи физики металлов. 2018. Т. 19. № 2. С. 195. https://doi.org/10.15407/ufm.19.02.195
Aliofkhazraei M., Macdonald D.D., Matykina E., Parfenov E.V., Egorkin V.S., Curran J.A., Troughton S.C., Sinebryukhov S.L., Gnedenkov S.V., Lampke T., Simchen F., Nabavi H.F // Appl. Surf. Sci. Adv. 2021. V. 5. P. 100121. https://doi.org/10.1016/j.apsadv.2021.100121
Берлин Е.В., Коваль Н.Н., Сейдман Л.А. Плазменная химико-термическая обработка поверхности стальных деталей. М.: Техносфера, 2012. 464 с.
Budilov V.V., Ramazanov K.N., Zolotov I.V., Khusainov Y.G., Vardanyan E.L. // J. Phys.: Conf. Ser. 2017. V. 830. № 1. P. 012094. https://doi.org/10.1088/1742-6596/830/1/012094
Agzamov R.D., Tagirov A.F., Nikolaev A.A., Ramazanov K.N // J. Phys.: Conf Ser. 2019. V. 1393. № 1. P. 012066. https://doi.org/10.1088/1742-6596/1393/1/012066
Vardanyan E.L., Ramazanov K.N., Nagimov R.S., Nazarov A.Y. // Surf. Coat. Technol. 2020. V. 389. P. 125657. https://doi.org/10.1016/j.surfcoat.2020.125657
Devyatkov V.N., Ivanov Y.F., Krysina O.V., Koval N.N., Petrikova E.A., Shugurov V.V. // Vacuum. 2017. V. 143. P. 464. https://doi.org/10.1016/j.vacuum.2017.04.016
Krysina O.V., Koval N.N., Kovalsky S.S., Shugurov V.V., Lopatin I.V., Prokopenko N.A., Petrikova E.A. // Vacuum. 2021. V. 187. P. 110123. https://doi.org/10.1016/j.vacuum.2021.110123
Koval N.N., Ivanov Y.F. // Russ. Phys. J. 2019. V. 62. № 7. P. 1161. https://doi.org/10.1007/s11182-019-01831-8
Grigoriev S.N., Volosova M.A., Migranov M.S., Minin I.V., Shekhtman S.R., Suhova N.A., Gurin V.D. Pivkin P.M. // Proc. SPIE. 2021. V. 11867. P. 31. https://doi.org/10.1117/12.2602166
Kuznetsova T., Lapitskaya V., Khabarava A., Chizhik S., Warcholinski B., Gilewicz A. // Appl. Surf. Sci. 2020. V. 522. P. 146508. https://doi.org/10.1016/j.apsusc.2020.146508
Vereschaka A., Tabakov V., Grigoriev S., Sitnikov N., Milovich F., Andreev N., Bublikov J. // Wear. 2019. V. 438. P. 203069. https://doi.org/10.1016/j.wear.2019.203069
Калиниченко А.И., Перепелкин С.С., Стрельницкий В.Е. // Вестн. рос. ун-тов. Математика. 2016. Т. 21. № 3. С. 1038.
Vardanyan E., Ramazanov K., Yagafarov I., Budilov V., Agzamov R. // J. Phys.: Conf. Ser. 2017. V. 830. № 1. P. 012113. https://doi.org/10.1088/1742-6596/830/1/012113
Budilov V., Vardanyan E., Ramazanov K. // J. Phys.: Conf. Ser. 2015. V. 652. № 1. P. 012053. https://doi.org/10.1088/1742-6596/652/1/012053
Ratayski U., Motylenko M., Ershova A., Šíma M., Jílek M., Rafaja D. // Surf. Coat. Technol. 2018. V. 344. P. 322. https://doi.org/10.1016/j.surfcoat.2018.03.031
Emlin D.R., Plotnikov S.A., Gavrilov N.V., Trachtenberg I.S., Khatmullin I.G. // Изв. вузов. Физика. 2012. Т. 55. № 12-2. С. 66.
Antonov M., Afshari H., Baronins J., Adoberg E., Raadik T., Hussainova I. // Tribology Int. 2018. V. 118. P. 500. https://doi.org/10.1016/j.triboint.2017.05.035
Krella A. // Coatings. 2020. V. 10. № 10. P. 921. https://doi.org/10.3390/coatings10100921
Tillmann W., Fehr A., Stangier D., Dildrop M. // Results Phys. 2019. V. 12. P. 2206. https://doi.org/10.1016/j.rinp.2019.02.048
Zhang H., Li Z., He W., Ma C., Liao B., Li Y. // J. Alloys Compd. 2019. V. 809. P. 151816. https://doi.org/10.1016/j.jallcom.2019.151816
Колубаев А.В., Белый А.В., Буяновский И.А., Колубаев Е.А., Кукареко В.А., Сизова О.В., Хрущов М.М. // Изв. вузов. 2019. Т. 62. № 8. С. 52.
Белов Д.С., Сергевнин В.С., Блинков И.В., Смирнов Н.И., Черногор А.В. // Трение и износ. 2021. Т. 42. № 2. С. 136.
Верещака А.А., Табаков В.П. // Упрочняющие технологии и покрытия. 2021. Т. 17. № 7. С. 332.
Погребняк А.Д., Кравченко Я.О., Бондар О.В., Жоллыбеков Б., Купчишин А.И. // Физикохимия поверхности и защита материалов. 2018. Т. 54. № 2. С. 152.
Huang X., Etsion I., Shao T. // Wear. 2015. V. 338. P. 54. https://doi.org/10.1016/j.wear.2015.05.016
Łępicka M., Grądzka-Dahlke M., Pieniak D., Pasierbiewicz K., Niewczas A. // Wear. 2017. V. 382. P. 62. https://doi.org/10.1016/j.wear.2017.04.017
Варданян Э.Л. Композиционные покрытия на основе интерметаллидов системы Ti–Al и технологии их нанесения из плазмы вакуумно-дугового разряда: Дис. … канд. тех. наук: 05.16.06. М.: МАТИ, 2015.
Ковальский С.С., Денисов В.В., Коваль Н.Н., Лопатин И.В. // Изв. вузов. Физика. 2015. Т. 58. № 9-2. С. 166.
Denisov V.V., Denisova Y.A., Vardanyan E.L., Ostroverkhov E.V., Leonov A.A., Savchuk M.V. // Russ. Phys. J. 2021. V. 64. № 1. P. 145. https://doi.org/10.1007/s11182-021-02310-9
Дополнительные материалы отсутствуют.
Инструменты
Поверхность. Рентгеновские, синхротронные и нейтронные исследования