Поверхность. Рентгеновские, синхротронные и нейтронные исследования, 2022, № 11, стр. 20-28
Исследование остаточных напряжений в пленках CeхGd1 – хO2 – y, полученных методом магнетронного распыления
А. А. Соловьев a, *, С. В. Работкин a, А. В. Шипилова a, Д. А. Агарков b, И. Н. Бурмистров b, А. Н. Шмаков c
a Институт сильноточной электроники СО РАН (ИСЭ СО РАН)
634055 Томск, Россия
b Институт физики твердого тела им. Ю.А. Осипьяна РАН (ИФТТ РАН)
142432 Черноголовка, Московская область, Россия
c Институт ядерной физики им. Г.И. Будкера СО РАН (ИЯФ СО РАН)
630090 Новосибирск, Россия
* E-mail: andrewsol@mail.ru
Поступила в редакцию 10.03.2022
После доработки 15.05.2022
Принята к публикации 15.05.2022
- EDN: YFARHW
- DOI: 10.31857/S1028096022110243
Аннотация
Тонкие пленки оксида церия, допированного гадолинием (CeхGd1 –хO2 –y), были синтезированы на анодах твердооксидных топливных элементов методом реактивного дуального магнетронного распыления. Пленки толщиной 4 мкм наносили в различных режимах осаждения (переходном и оксидном), различающихся содержанием кислорода в вакуумной камере. Остаточные напряжений в пленках после осаждения и после термического отжига на воздухе определяли по кривизне анодных пластин. Получены зависимости между режимами осаждения, остаточными напряжениями и характеристиками топливных элементов с электролитом CeхGd1 –хO2 –y. Методом растровой электронной микроскопии исследована морфология поверхности и структура поперечного сечения пленок. Дополнительно структура пленок допированного гадолинием оксида церия была проанализирована методом рентгенофазового анализа с использованием источника синхротронного излучения в процессе нагрева до 1300°С. Показано, что при определенных режимах осаждения и отжига возможна трансформация сжимающих напряжений в растягивающие. Это уменьшает деформацию анодных пластин после нанесения электролита CeхGd1 –хO2 –y.
ВВЕДЕНИЕ
Оксид церия, допированный гадолинием (CeхGd1 –хO2 –y), в настоящее время интенсивно изучают для использования в качестве твердого электролита в твердооксидных топливных элементах (ТОТЭ). Основным преимуществом допированного оксида церия является в четыре–пять раз более высокая ионная проводимость в диапазоне температур 600–800°С по сравнению с диоксидом циркония, стабилизированным оксидом иттрия (YSZ) [1]. В этом материале проводимость обусловлена диффузией кислорода через кислородные вакансии, образующиеся в результате замены Ce4+ на Gd3+, и поэтому проводимость электролита зависит от концентрации Gd3+. Например, при 500°С максимальная проводимость у электролита состава Ce0.9Gd0.1O1.95 [2]. Однако недостатком допированного гадолинием оксида церия является его смешанная ионно-электронная проводимость в восстановительной атмосфере. Электронная проводимость начинает доминировать при высоких рабочих температурах (между 800 и 1000°С) [3]. По этой причине CeхGd1 –хO2 –y обычно используют в качестве электролита в диапазоне температур до 650°С для создания низкотемпературных ТОТЭ [4]. При более высоких температурах CeхGd1 –хO2 –y часто применяют в качестве барьерного слоя между электролитом YSZ и катодом ТОТЭ для предотвращения межфазной диффузии атомов [5].
Помимо проводимости электролита, от которой зависит удельная мощность, немаловажное значение для работы ТОТЭ имеет его механическая прочность. Особенно это касается топливных элементов анод-поддерживающей конструкции, в которой электролит имеет толщину менее 10 мкм [6]. Чтобы не допустить разрушения электролита при изготовлении и эксплуатации топливного элемента, важно избегать критических механических напряжений, превышающих напряжение разрушения керамики.
Планарные ТОТЭ анод-поддерживающей конструкции обычно изготавливают путем совместного спекания тонкого электролита и относительно толстого (толщиной 0.5–1 мм) анода при температуре 1400–1500°C [7]. Остаточные напряжения при комнатной температуре в топливных элементах, полученных совместным спеканием, в основном связаны с различием коэффициентов термического расширения слоев [8, 9]. Типичные значения остаточных сжимающих напряжений в электролите ТОТЭ анод-поддерживающей конструкции составляют 500–650 МПа при комнатной температуре [7, 10, 11]. Механизм и закономерности образования остаточных напряжений в топливных элементах, получаемых совместным спеканием слоев, изучены достаточно подробно. Однако сведений об уровне остаточных напряжений в тонких электролитах ТОТЭ, которые формируются на анодных подложках методом физического газофазного осаждения (магнетронное распыление, лазерная абляция), еще недостаточно.
Остаточные напряжения в пленках, наносимых методом магнетронного распыления, могут быть внутренними и термическими. Первые вызваны воздействием энергетических частиц (ионов, нейтральных атомов), а вторые – различным тепловым расширением пленки и подложки (если пленки наносят при повышенной температуре). Метод распыления основан на осаждении частиц с высокой кинетической энергией. Поэтому существенный вклад в развитие внутренних напряжений в тонких пленках вносят дефекты (межузельные атомы, вакансии, дислокации и другие дефекты), образующиеся в процессе осаждения [12]. Одним из важных механизмов развития напряжений в пленках, нанесенных с использованием высокоэнергетических частиц, является так называемый “атомный (ионный) наклеп” (atomic или ion peening) [13]. При соударении с растущей пленкой часть адсорбированных атомов может внедряться в ее поверхностный слой, в междоузлия кристаллической решетки. Это приводит к дисторсии кристаллической решетки, избыточному уплотнению пленки и возникновению сжимающих напряжений. Эффективным методом снижения остаточных напряжений является высокотемпературный отжиг [14]. Показано, что термическая обработка слоев YSZ и CeхGd1 –хO2 –y после магнетронного осаждения позволяет увеличить их ионную проводимость за счет улучшения кристалличности и плотности [15, 16].
В настоящей работе исследованы остаточные напряжения в слоях электролита CeхGd1 –хO2 –y толщиной 4 мкм после его осаждения методом реактивного магнетронного распыления и термического отжига на воздухе. Реактивное магнетронное распыление подразумевает распыление металлической мишени в присутствии реактивного газа (например, Ar + O2) [17]. Процесс может протекать в трех режимах: в металлическом, переходном и оксидном, в зависимости от концентрации кислорода в вакуумной камере [18]. В металлическом режиме преимущественно происходит распыление атомов металла ионами аргона, и скорость осаждения пленки наибольшая. В переходном режиме поверхность распыляемой мишени частично покрыта слоем оксида, количество которого меняется бесконтрольно. В этом режиме пленки напыляются с дефицитом кислорода. В оксидном режиме поверхность мишени почти полностью покрыта слоем оксида, в результате чего скорость осаждения пленки резко снижается. В этом режиме происходит напыление пленок с содержанием кислорода, близким к стехиометрическому. Для нанесения оксидных пленок на практике используют последние два режима. У каждого из них есть свои преимущества и недостатки в зависимости от конкретной задачи и требований к свойствам пленок. В работе проведено сравнение остаточных напряжений в пленках CeхGd1 –хO2 –y, полученных в переходном и оксидном режимах, с разной скоростью осаждения и различным содержанием кислорода.
ЭКСПЕРИМЕНТАЛЬНАЯ ЧАСТЬ
В качестве подложек использовали аноды NiO/YSZ размером 100 × 20 мм. Их вырезали лазером из анодных пластин размером 100 × 100 мм и толщиной 700 мкм производства фирмы Kceracell Co. (Южная Корея). Выбор данных анодов в качестве подложек был обусловлен их коммерческой доступностью. Напыление пленок CeхGd1 –хO2 –y проводили на модернизированной установке ННВ-6.6 методом дуального реактивного распыления металлических мишеней Ce0.9Gd0.1 размером 100 × 300 мм (чистота 99.9%) производства ООО “Гирмет” (Россия) [19]. Пленки толщиной около 4 мкм получали в смеси аргона и кислорода в оксидном и переходном режимах распыления. Расстояние от мишеней до подложки составляло около 90 мм. Вакуумную камеру откачивали диффузионным насосом до остаточного давления 0.01 Па. Затем образцы нагревали до температуры 450°C, которую поддерживали в процессе осаждения CeхGd1 –хO2 –y. Для повышения адгезии пленок непосредственно перед их осаждением проводили обработку подложек ионами Ar, генерируемыми ионным источником с анодным слоем. Давление в камере во время осаждения составляло 0.2 Па. Стабильность осаждения пленок в переходном режиме распыления обеспечивали следующим образом. Источник питания дуальных магнетронов APEL-M-12DU-symmetric (ООО “Прикладная электроника”, Россия) работал в импульсном режиме с частотой 50 кГц и поддерживал постоянной мощность разряда 3 кВт. Источник питания имел систему обратной связи с регулятором расхода кислорода и автоматически регулировал расход кислорода таким образом, чтобы поддерживать постоянным напряжение разряда, которое задавал оператор. Расход Ar поддерживали постоянным (40 мл/мин).
После нанесения пленок часть образцов подвергалась отжигу в печи Nabertherm (Германия) при температуре 1200°С. Отжиг проводили в течение 2 ч в воздушной атмосфере. Скорость нагрева 3 град/мин, а охлаждение происходило с естественной скоростью.
Остаточные напряжения σf в пленках после нанесения и после отжига определяли посредством измерения кривизны подложки по формуле Стоуни [20]:
Радиус изгиба, входящий в формулу Стоуни, рассчитывали по формуле:
где R1 – радиус изгиба исходной пластины до нанесения пленки, R2 – радиус изгиба пластины после нанесения пленки или после отжига. Радиус изгиба пластины вычисляли по формуле: R = (l 2 + + 4h2)/8h, где l – длина, h – высота (рис. 1).Для изучения микроструктуры пленок использовали растровые электронные микроскопы (РЭМ) Quanta 200 3D (FEI Company, США) и Supra 50VP (ZEISS, Германия). С целью проверки катионного соотношения пленки были проанализированы методом энергодисперсионной рентгеновской спектроскопии. Анализ проводили не менее чем в пяти точках для каждого образца.
Рентгенофазовый анализ (РФА) пленок CeхGd1 –хO2 –y проводили на канале № 6 источника синхротронного излучения накопителя электронов ВЭПП-3 в Институте ядерной физики (Новосибирск). В процессе исследования методом РФА с использованием синхротронного излучения образец нагревали от 30 до 1300°C со скоростью 15 град/мин и охлаждали со скоростью 50 град/мин. Рабочая длина волны синхротронного излучения 0.172 нм. Полученные дифрактограммы пересчитывали на соответствующие углы для λ = 0.1541 нм (излучение CuKα) для сравнения результатов с базой данных PDF 4+.
Для исследования характеристики ТОТЭ с электролитом CeхGd1 –хO2 –y из образцов размером 100 × 20 мм лазером вырезали диски диаметром 20 мм. Катод La0.6Sr0.4CoO3 (LSC) (Kceracell Co., Южная Корея) площадью 10 × 10 мм наносили на электролит методом трафаретной печати и спекали во время запуска и испытания топливного элемента. Вольт-амперные характеристики ТОТЭ измеряли при 700°С при постоянной подаче сухого водорода (30 мл/мин) к аноду и воздуха (300 мл/мин) к катоду. Для токосъема с электродов использовали сетки из серебра и проволоку из платины.
РЕЗУЛЬТАТЫ И ИХ ОБСУЖДЕНИЕ
Пленки CeхGd1 –хO2 –y были получены в трех различных режимах осаждения, различающихся содержанием кислорода в вакуумной камере и, соответственно, скоростью осаждения (табл. 1). На рис. 2 показаны зависимости скорости осаждения пленок Vн и напряжения разряда Ud от расхода кислорода ${{Q}_{{{{{\text{O}}}_{2}}}}}$. Зависимость Vн = f(${{Q}_{{{{{\text{O}}}_{2}}}}}$) имеет типичный для магнетронного распыления вид [23] – резкое падение скорости осаждения в переходном режиме распыления и небольшое изменение скорости осаждения в оксидном (“отравленном” режиме). На границе металлического и переходного режима Vн ≈ 40 нм/мин, но из-за большого дефицита кислорода пленки имеют низкую прозрачность в видимом диапазоне длин волн и черный оттенок. На границе переходного и оксидного режимов Vн снижается до 7–8 нм/мин, но полученные пленки прозрачные, что говорит об их составе, близком к стехиометрическому. Зависимость Ud = f(${{Q}_{{{{{\text{O}}}_{2}}}}}$) носит немонотонный характер, который определяется свойствами конкретного материала, в частности, коэффициентом ионно-электронной эмиссии. В переходном режиме распыления напряжение разряда при увеличении расхода кислорода сначала снижается от 400 до 313 В, а затем начинает увеличиваться и достигает 500 В в оксидном режиме. В настоящей работе пленки CeхGd1 –хO2 –y были получены при Ud = 345, 353 и 500 В. Пленку на образец 1О наносили в оксидном режиме со скоростью осаждения 8 нм/мин. Образцы 2П и 3П были получены в переходном режиме со скоростью осаждения 11 и 17 нм/мин. Образец 4П был получен в тех же условиях, что и образец 2П.
Таблица 1.
Параметры осаждения, остаточные напряжения в пленках CeхGd1 –хO2 –y и характеристики ТОТЭ с электролитом CeхGd1 –хO2 –y
Образец | Ud, В | Vн, нм/мин | tf, мкм | σf0, МПа | σf1, МПа | НРЦ, мВ | Рmax, мВт/см2 |
---|---|---|---|---|---|---|---|
1О | 500 | 8 | 4.15 | –2411 | –1347 | 666 | 92 |
2П | 345 | 11 | 4 | –2270 | –4896 | 636 | 97 |
3П | 353 | 17 | 4.2 | –2062 | –42 430 | 538 | 66 |
4П | 345 | 11 | 4 | –1790 | +2016* | 693 | 126 |
Примечание: * отжиг проводился под нагрузкой 600 г., О – оксидный режим распыления, П – переходный режим распыления, Ud – напряжение разряда, Vн – скорость нанесения пленки, tf – толщина пленки, σf0 и σf1 – остаточные напряжения после нанесения пленки и ее отжига при температуре 1200°С соответственно, НРЦ – напряжение разомкнутой цепи ТОТЭ, Рmax – максимальная удельная мощность ТОТЭ с отожженным при 1200°С электролитом при температуре 700°С.
Рис. 2.
Зависимости скорости осаждения пленок CeхGd1 –хO2 –yVн и напряжения разряда Ud от расхода кислорода при реактивном магнетронном распылении.
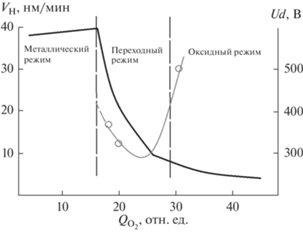
Из табл. 1 видно, что все пленки CeхGd1 –хO2 –y после осаждения обладают достаточно высокими сжимающими остаточными напряжениями (более –2000 МПа). Чем ниже расход кислорода в камере при осаждении пленки, т.е. чем больше дефицит кислорода в полученной пленке, тем ниже амплитуды остаточных напряжений.
Ожидалось, что после высокотемпературного отжига остаточные напряжения в пленках CeхGd1 –хO2 –y уменьшатся. Такое явление наблюдалось в пленках YSZ толщиной 250 нм, полученных методом высокочастотного распыления [24], где нагрев до 450°С и последующее охлаждение до комнатной температуры приводили к трансформации сжимающих напряжений –500 МПа в растягивающие напряжения +550 МПа. Это может быть вызвано диффузией межузельных атомов в стандартные узлы решетки, которая уменьшает деформации решетки. Однако в случае пленок CeхGd1 –хO2 –y отжиг при температуре 1200°С привел к уменьшению остаточных напряжений до –1347 МПа только в образце 1О, полученном в оксидном режиме осаждения. У образцов, полученных в переходном режиме распыления (2П и 3П), остаточные напряжения увеличились до ‒4896 и –42430 МПа соответственно. Таким образом, наличие дефицита кислорода в осажденной пленке приводит к увеличению остаточных напряжений в ней после отжига и, как следствие, встраиванию дополнительного кислорода в кристаллическую решетку. Чем больше дефицит кислорода в исходной пленке, тем выше амплитуды остаточных напряжений после термообработки.
Для примера на рис. 3 приведены фото образца 3П до и после отжига пленки, показывающие влияние остаточных напряжений на изгиб подложки. Интересно, что, несмотря на очень большие механические напряжения в пленке образца 3П, приведшие к сильной деформации подложки, пленка не имеет видимых повреждений (трещин или отслаивания) и демонстрирует отличную адгезию к подложке (рис. 4).
Рис. 3.
Фото исходной подложки NiO/YSZ образца 3П (а), после нанесения пленки CeхGd1 – хO2 –y (б), после отжига при температуре 1200°С (в).
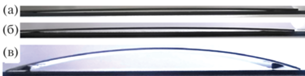
Для того чтобы избежать чрезмерного изгиба образцов во время их отжига, был применен отжиг под статической нагрузкой. Этот подход часто применяется при спекании многослойной керамики [25, 26]. Для этого образец 4П во время отжига помещали между двумя плоскими пластинами из оксида алюминия массой 600 г и размером 120 × 120 × 20 мм. Отжиг под нагрузкой привел к тому, что изгиб образца 4П после отжига был меньше, чем исходной подложки. Это означает трансформацию в процессе отжига сжимающих напряжений в растягивающие величиной +2016 МПа.
Для того чтобы выяснить влияние режимов осаждения на морфологию поверхности и структуру пленок CeхGd1 –хO2 –y, было проведено их исследование после отжига при 1200°С методом РЭМ (рис. 5). Обнаружено, что морфология поверхности и структура поперечного сечения пленок после отжига практически не зависит от режима их осаждения. Поверхность пленок имеет зернистую структуру с размером зерен 1–2 мкм. Каждое зерно состоит из субзерен диаметром около 300 нм. На поперечном сечении пленок видны закрытые поры размером 20–60 нм. Они могли образоваться в результате рекристаллизации пленки во время ее отжига в местах границ зерен и пустот, которые сформировались в процессе роста пленки.
Рис. 5.
РЭМ-изображения поверхности (а, в, д) и скола (б, г, е) пленок CeхGd1 –хO2 –y, полученных в режимах 1О (а, б), 2П (в, г) и 3П (д, е) и подвергшихся отжигу при температуре 1200°С.
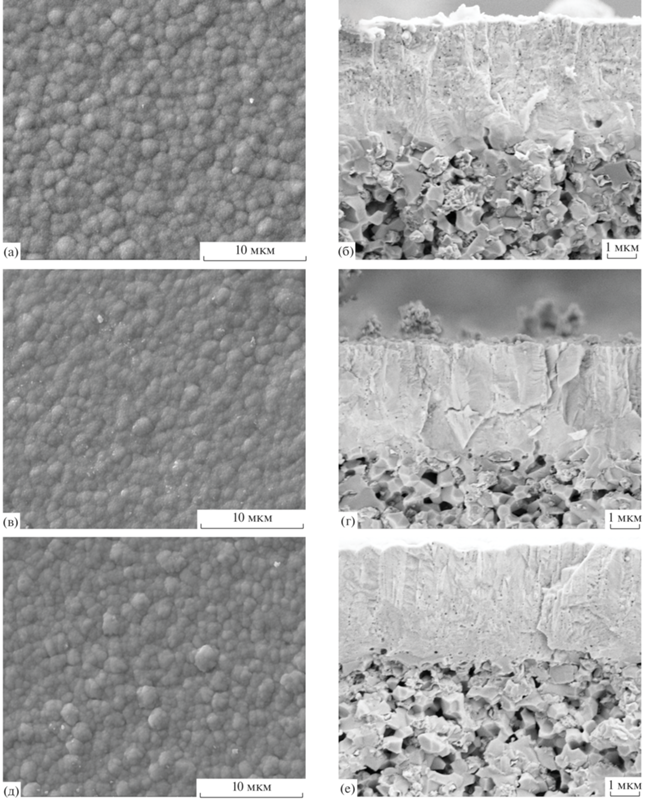
На рис. 6 показаны морфология поверхности и микроструктура скола пленки на образце 4П после отжига под нагрузкой. Видно, что отжиг под нагрузкой, сопровождающийся трансформацией сжимающих напряжений в растягивающие, не приводит к разрушению или появлению трещин в пленке, которая имеет плотную и однородную структуру.
Рис. 6.
РЭМ-изображения поверхности (а) и скола (б) пленки CeхGd1 –хO2 –y, полученной в режиме 4П и подвергшейся отжигу при температуре 1200°С под статической нагрузкой.
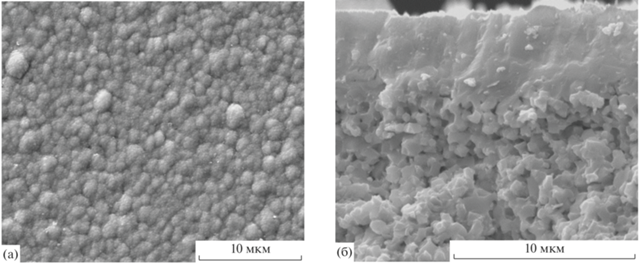
Поскольку основным назначением пленок CeхGd1 –хO2 –y является использование в качестве электролита ТОТЭ, было проведено сравнение вольт-амперных характеристик топливных элементов, изготовленных из образцов 1О, 2П, 3П и 4П. Результаты измерения вольт-амперных характеристик ТОТЭ при рабочей температуре 700°С представлены в табл. 1.
Напряжение разомкнутой цепи ТОТЭ с электролитом CeхGd1 –хO2 –y обычно меньше теоретически возможного (1.08–1.1 В) и находятся в диапазоне 0.7–0.8 В вследствие электронной проводимости, которая появляется в оксиде церия в восстановительной атмосфере. Например, напряжение разомкнутой цепи ТОТЭ с тонкопленочным электролитом CeхGd1 –хO2 –y, полученным в [27] методом сильноточного магнетронного распыления на аналогичных анодах, составляло 0.77–0.8 В при рабочих температурах 600–750°С.
Из табл. 1 видно, что в случае образцов 1О, 2П и 3П напряжение разомкнутой цепи и максимальная плотность мощности зависят от режима осаждения электролита CeхGd1 –хO2 –y и коррелируют со значениями остаточных напряжений. Для всех исследуемых топливных элементов напряжение разомкнутой цепи было менее 0.7 В. Это говорит о неидеальной газонепроницаемости электролита, т.е. наличии в нем дефектов, которые не попали на РЭМ-изображения или образовались в процессе нагрева топливных элементов до рабочей температуры. Наименьшее напряжение разомкнутой цепи (0.53 В) и максимальную плотность мощности (66 мВт/см2) продемонстрировал образец 3П, который характеризуется наибольшими остаточными напряжениями после отжига. В то же время образец 4П с растягивающими остаточными напряжениями в электролите (при комнатной температуре) продемонстрировал наибольшее напряжение разомкнутой цепи (0.69 В) и максимальную плотность мощности (126 мВт/см2). Это говорит о том, что отжиг под нагрузкой не только трансформирует сжимающие напряжения в растягивающие, но и улучшает характеристики электролита CeхGd1 –хO2 –y. В [28] показано, что механические растягивающие напряжения увеличивают ионную проводимость оксида циркония, стабилизированного 8 мол. % иттрия за счет увеличения подвижности ионов кислорода. Предполагается, что механические напряжения вызывают градиент потенциальной энергии соседних кислородных центров, особенно вокруг ионов иттрия, что, вероятно, способствует миграции ионов кислорода. Поэтому эффект влияния механических напряжений на проводимость электролита требует дальнейшего более детального изучения, поскольку дает возможность улучшения характеристик ТОТЭ.
Для получения точной структуры пленок CeхGd1 –хO2 –y после осаждения и отжига был применен метод РФА с использованием синхротронного излучения. Высокая интенсивность и коллимация синхротронного излучения позволяют проводить исследования с высоким разрешением. На канале № 6 источника синхротронного излучения накопителя электронов ВЭПП-3 в ИЯФ СО РАН была исследована пленка CeхGd1 –хO2 –y, полученная в оксидном режиме распыления (образец 1О) и не подверженная термообработке.
Анализ дифрактограмм (рис. 7) показал, что параметр элементарной ячейки пленки CexGd1 –xO2 –y после осаждения превышает значения, приведенные в базе данных ICDD PDF-2 даже для степени допирования 0.3, что говорит о несовершенстве структуры пленки, малых значениях области когерентного рассеяния (ОКР) 25–28 нм и большой концентрации дефектов. В диапазоне углов 2θ = 44°–60° были зафиксированы рефлексы оксида церия 220, 311 и 222. Для сравнения на рис. 7 показаны положения рефлексов Ce0.9Gd0.1O2 (PDF Card 04-002-6160). Сравнение с положением рефлексов оксида церия, допированного 10 ат. % гадолиния, проводили вследствие того, что распыляемая мишень содержала 10 ат. % Gd. Кроме того, энергодисперсионная рентгеновская спектроскопия (рис. 8) показала 11.4 ат. % Gd в пленке, что близко к составу распыляемой мишени. Сдвиг рефлексов оксида церия в область меньших углов на дифрактограммах исходной пленки по сравнению со стандартными значениями, по-видимому, связан с остаточными сжимающими напряжениями в пленке, образующимися в процессе ее роста.
Рис. 7.
Дифрактограммы in situ пленки CeхGd1 –хO2 –y, полученной в режиме 1О при нагреве/охлаждении на воздухе (пунктирными линиями показаны положения рефлексов Ce0.9Gd0.1O2 при комнатной температуре, PDF Card 04-002-6160).
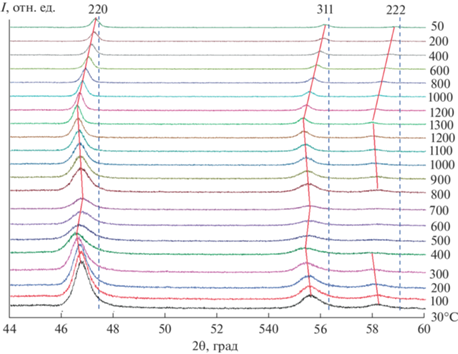
Рис. 8.
Элементный анализ пленки CeхGd1 –хO2 –y (образец 1О) методом энергодисперсионной рентгеновской спектроскопии (в таблице приведено содержание Ce и Gd без учета кислорода и атомов серебра, наносимых перед проведением РЭМ).
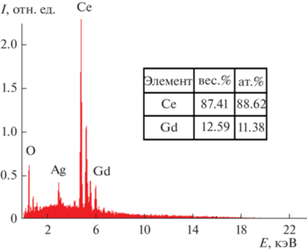
В процессе нагрева до 400°С рефлексы оксида церия сдвигаются влево вследствие теплового расширения кристаллической решетки. Однако в диапазоне температур 400–700°С они немного смещаются вправо, демонстрируя сжатие решетки. Такое поведение рефлексов обычно связывают с упорядочением структуры материала или изменением его химического состава. При температуре ~800°C возобновляется смещение рефлексов влево, свидетельствующее о дальнейшем тепловом расширении. После нагрева до 1300°C и охлаждения до комнатной температуры параметр решетки a пленки CeхGd1 –хO2 – y становится меньше исходного значения и составляет 0.54312 нм. Размеры ОКР вырастают примерно вдвое, до ~49–51 нм. Приближение рефлексов оксида церия на дифрактограммах к стандартным значениям после нагрева и охлаждения говорит об уменьшении остаточных напряжений в пленке, что согласуется с результатами измерения изгиба образцов.
В [16] также наблюдалось увеличение размера ОКР от 18 до 26 нм после отжига при 900°C пленки CeхGd1 –хO2 –y, полученной методом реактивного высокочастотного магнетронного распыления мишени состава 90 ат. % Ce и 10 ат. % Gd. После отжига при температуре 900–1100°C в течение 2 ч дифракционные рефлексы оксида церия смещались в сторону больших углов 2θ, отражая уменьшение параметра решетки.
ЗАКЛЮЧЕНИЕ
Исследовано влияние режимов осаждения и высокотемпературного отжига в воздушной атмосфере на остаточные напряжения в пленках оксида церия, допированного гадолинием, полученных методом реактивного дуального магнетронного распыления. Установлено, что после осаждения в пленках CeхGd1 –хO2 –y присутствуют остаточные сжимающие напряжения более 2000 МПа. Их величина зависит от дефицита кислорода в пленке таким образом, что наименьшие напряжения наблюдаются в пленках с наибольшим дефицитом кислорода. Отжиг при температуре 1200°С в воздушной атмосфере приводит к снижению остаточных напряжений в пленках, осажденных в оксидном режиме и увеличению в 2–20 раз в пленках, осажденных в переходном режиме. Однако было показано, что проблема остаточных напряжений успешно решается отжигом пленок под статической нагрузкой, в результате которого происходит трансформация сжимающих напряжений в растягивающие. Поэтому с практической точки зрения лучше осаждать пленки CeхGd1 –хO2 –y в переходном режиме распыления, в котором скорость осаждения значительно превышает значения, наблюдаемые в оксидном режиме, а затем проводить отжиг под статической нагрузкой.
Список литературы
Mogensen M., Sammes N.M., Tompset G.A. // Solid State Ion. 2000. V. 129. № 1–4. P. 63. https://www.doi.org/10.1016/S0167-2738(99)00318-5
Steele B.C.H. // Solid State Ion. 2000. V. 129. № 1–4. P. 95. https://www.doi.org/10.1016/S0167-2738(99)00319-7
Rupp J.L.M., Infortuna A., Gauckler L.J. // J. Am. Ceram. Soc. 2007. V. 90. № 6. P. 1792. https://www.doi.org/10.1111/j.1551-2916.2007.01531.x
Park H.C., Virkar A.V. // J. Power Sources. 2009. V. 186. P. 133. https://www.doi.org/10.1016/j.jpowsour.2008.09.080
Cho S., Kim Y., Kim J., Manthiram A., Wang H. // Electrochim. Acta. 2011. V. 56. № 16. P. 5472. https://www.doi.org/10.1016/j.electacta.2011.03.039
Kalinina E.G., Pikalova E.Y. // Russ. Chem. Rev. 2021. V. 90. № 6. P. 703. https://www.doi.org/10.1070/RCR4966
Yakabe H., Baba Y., Sakurai T., Yoshitaka Y. // J. Power Sources. 2004. V. 135. № 1–2. P. 9. https://www.doi.org/10.1016/j.jpowsour.2003.11.04
Atkinson A. // Solid State Ion. 1997. V. 95. № 3–4. P. 249. https://www.doi.org/10.1016/s0167-2738(96)00588-7
Montross C.S., Yokokawa H., Dokiya M. // Br. Ceram. Trans. 2002. V. 101. № 3. P. 85. https://www.doi.org/10.1179/096797802225003956
Sun B., Rudkin R.A., Atkinson A. // Fuel Cells. 2009. V. 9. № 6. P. 805. https://www.doi.org/10.1002/fuce.200800133
Fischer W., Malzbender J., Blass G., Steinbrech R.W. // J. Power Sources. 2005. V. 150. P. 73. https://www.doi.org/10.1016/j.jpowsour.2005.02.014
Shugurov A.R., Panin A.V. // Tech. Phys. 2020. V. 65. P. 1881. https://www.doi.org/10.1134/S1063784220120257
D’Heurle F.M., Harper J.M. // Thin Solid Films. 1989. V. 171. № 1. P. 81. https://doi.org/10.1016/0040-6090(89)90035-7
Stenzel O., Wilbrandt S., Kaiser N., Vinnichenko M., Munnik F., Kolitsch A., Chuvilin A., Kaiser U., Ebert J., Jakobs S. // Thin Solid Films. 2009. V. 517. № 21. P. 6058. https://www.doi.org/10.1016/j.tsf.2009.05.009
Bae J., Chang I., Kang S., Hong S., Cha S.W., Kim Y.B. // J. Nanosci. Nanotechnol. 2014. V. 14. № 12. P. 9294. https://www.doi.org/10.1166/jnn.2014.10121
Wu W., Liu Z., Zhao Z., Zhang X., Ou D., Tu B., Cui D., Cheng M. // Chin. J. Catal. 2014. V. 35. № 8. P. 1376. https://www.doi.org/10.1016/s1872-2067(14)60137-6
Musil J., Baroch P., Vlček J., Nam K.H., Han J.G. // Thin Solid Films. 2005. V. 475. № 1–2. P. 208. https://www.doi.org/10.1016/j.tsf.2004.07.041
Berg S., Nyberg T., Kubart T., Modelling of Reactive Sputtering Processes, in Reactive Sputter Deposition / Ed. Depla D., Mahieu S. Springer, 2008.
Solovyev A., Ionov I., Lauk A., Linnik S., Shipilova A., Smolyanskiy E. // J. Electrochem. En. Conv. Stor. 2018. V. 15. № 4. P. 044501. https://www.doi.org/10.1115/1.4039705
Janssen G.C.A.M., Abdalla M.M., van Keulen F., Pujada B.R., van Venrooy B. // Thin Solid Films. 2009. V. 517. № 6. P. 1858. https://www.doi.org/10.1016/j.tsf.2008.07.014
Pihlatie M., Kaiser A., Mogensen M. // J. Eur. Ceram. Soc. 2009. V. 29. № 9. P. 1657. https://www.doi.org/10.1016/j.jeurceramsoc.2008
Giraud S., Canel J. // J. Eur. Ceram. Soc. 2008. V. 28. № 1. P. 77. https://www.doi.org/10.1016/j.jeurceramsoc.2007.05.009
Fernandes S.L., Albano L.G.S., Affonço L.J., da Silva J.H.D., Longo E., Graeff C.F. de O. // Front. Chem. 2019. V. 7. P. 50. https://www.doi.org/10.3389/fchem.2019.00050
Quinn D.J., Wardle B., Spearing S.M. // J. Mater. Res. 2008. V. 23. № 03. P. 609. https://www.doi.org/10.1557/jmr.2008.0077
Atkinson A., Selçuk A. // Acta Mater. 1999. V. 47. № 3. P. 867. https://www.doi.org/10.1016/s1359-6454(98)00412-1
Jia L., Lu Z., Miao J., Liu Z., Li G., Su W. // J. Alloys Compd. 2006. V. 414. № 1–2. P. 152. https://www.doi.org/10.1016/j.jallcom.2005.03.119
Solovyev A.A., Rabotkin S.V., Shipilova A.V., Ionov I.V. // Int. J. Electrochem. Sci. 2019. V. 14. P. 575. https://www.doi.org/10.20964/2019.01.03
Araki W., Imai Y., Adachi T. // J. Eur. Ceram. Soc. 2009. V. 29. P. 2275. https://www.doi.org/10.1016/j.jeurceramsoc.2009.01.014
Дополнительные материалы отсутствуют.
Инструменты
Поверхность. Рентгеновские, синхротронные и нейтронные исследования