Поверхность. Рентгеновские, синхротронные и нейтронные исследования, 2022, № 6, стр. 90-95
Влияние поверхностной пленки (третьего тела) на процесс трения и изнашивания углеродных волокнистых композитов
А. Г. Шпенев a, *, Т. И. Муравьева a, И. В. Шкалей a, П. О. Буковский a
a Институт проблем механики им. А.Ю. Ишлинского РАН
119526 Москва, Россия
* E-mail: kel-a-kris@list.ru
Поступила в редакцию 28.07.2021
После доработки 16.09.2021
Принята к публикации 30.09.2021
- EDN: GCPWVZ
- DOI: 10.31857/S1028096022060152
Аннотация
Изучался процесс трения углерод-углеродных волокнистых композитных материалов и исследовано образование пленки продуктов износа (третьего тела) на поверхности трения. Испытания композитов на трение и износ проводили в диапазоне температур и давлений, характерных для работы авиационных тормозных систем и других высоконагруженных фрикционных узлов. Поверхность трения материала и третье тело исследовались методами растровой электронной микроскопии, сканирующей зондовой микроскопии и Рáман-спектроскопии. Оценено влияние наличия пленки третьего тела и ее толщины на коэффициент трения и интенсивность изнашивания материала.
ВВЕДЕНИЕ
Композитные материалы на основе волокна углерод-углеродной матрицы находят широкое применение во фрикционных узлах, характеризуемых высокими нагрузками и температурами. Высокая прочность в сочетании с возможностью работать при температуре поверхности более 1500°С без потери фрикционных свойств делает углерод-углеродный композитный материал идеальным материалом для авиационных и высокоскоростных ж/д тормозных систем, сцеплений спецтехники и т.д. Математические основы трения и изнашивания композитных материалов развиты в меньшей степени, чем основы их прочности и трещиностойкости. Из основных работ в этой области можно отметить классические работы Хрущева [1] и Зум-Гара [2]. Из более современных – работы Дхарана с соавторами [3, 4] и работы группы Горячевой [5–8]. При трении на поверхности углерод-углеродного композитного материала образуется заметная пленка из продуктов износа (третье тело), которая может оказывать важное влияние на трение и износ материала. Подходы к описанию влияния третьего тела на трение можно условно разделить на два типа: моделирующие движение частиц износа в контакте на микроуровне (в основном численными методами) [9–12] и на подходы, опирающиеся на экспериментальные исследования [13, 14].
В данной работе процесс трения с образованием значительной пленки (третьего тела) будет представлен как два конкурирующих между собой процесса. Первый это, собственно, процесс изнашивания трущихся поверхностей, при котором частицы износа подпитывают пленку третьего тела, увеличивая ее толщину. При этом с увеличением своей толщины пленка все сильнее разделяет взаимодействующие поверхности, снижая интенсивность их изнашивания. При достижении толщины, при которой пленка полностью разделяет трущиеся тела, процесс изнашивания практически прекращается. Второй процесс заключается в выдавливании продуктов износа из пленки на границе области контакта. Этот процесс, напротив, уменьшает толщину пленки, увеличивая интенсивность изнашивания. В результате устанавливается некоторое равновесие, определяемое как параметрами контакта (контактными давлениями, скоростью скольжения, температурой), так и конфигурацией взаимодействующих образцов. Для оценки влияния этих процессов на износ углерод-углеродного композитного материала в работе используется линейное приближение влияния толщины пленки третьего тела на интенсивность изнашивания композита и на расход вещества пленки третьего тела через границу области контакта [15].
МАТЕРИАЛЫ И МЕТОДЫ
В работе исследован фрикционный волокнистый композит на основе углеродного волокна и углеродной матрицы АДФ-ОС, серийно производящийся ПАО “АК “Рубин” и применяющийся в качестве материала для изготовления авиационных тормозных дисков. При производстве композита используется термообработанное при температуре 2800°C (графитированное) волокно, собранное в разнонаправленные жгуты, лежащие параллельно поверхности трения. Матрица композита формируется путем многократной пропитки волокнистого каркаса полимерным составом с последующим обжигом до температуры пиролитического разложения полимера.
Композит был испытан на модифицированном трибометре UMT-2 по схеме трения “кольцо–кольцо” в зеркальной паре трения. Были определены коэффициент трения и скорость изнашивания в диапазоне температур 300–1200°C и контактных давлений 0.5–1 МПа, имитирующих работу авиационного тормоза [16]. Для изучения поверхности композита с образовавшейся на ней в процессе трения пленкой третьего тела, была использована комплексная методика, включающая растровую электронную (РЭМ) и сканирующую зондовую микроскопии (СЗМ) [17, 18], а также Рáман-спектроскопию [19]. Электронно-микроскопические исследования проводили на приборе Quanta 650 (FEI, Нидерланды) с использованием детектора вторичных электронов. Для изучения пространственной геометрии поверхностей был использован микроскоп SmartSPMTM (AIST-NT, Россия) в режиме тейпинга. Рáмановские спектры комбинационного рассеяния света (КРС) на образцах углерод-углеродной матрицы композитного материала были получены на приборе inVia Qontor (Renishaw, Великобритания) с использованием возбуждающего зеленого лазера с длиной волны 532 нм. Спектры измеряли в диапазонах 900–1900 см–1 (спектр первого порядка) и 2500–3300 см–1 (спектр второго порядка). Для углеродных образцов были взяты пять 30-секундных накоплений с мощностью лазера 1.7 мВт. В работе используется 50-кратный объектив, при котором размер лазерного пятна на поверхности образца составлял 1 мкм. После этого пленка была удалена механической очисткой с растворителем, и поверхность без пленки была исследована аналогичными методами. Частицы износа, выделяющиеся при трении, были собраны, и получено их изображение методом РЭМ. Для оценки влияния третьего тела на изнашивание композита была использована модель линейного влияния геометрических параметров пленки третьего тела на поток частиц износа в зазоре контакта [15].
РЕЗУЛЬТАТЫ И ИХ ОБСУЖДЕНИЕ
На рис. 1 представлены результаты трибологических испытаний композита. На рис. 1а показан график зависимости коэффициента трения от времени в процессе испытания. Из графика следует, что в процессе приработки (и, следовательно, образования устойчивой пленки третьего тела на поверхности трения) коэффициент трения значительно снижается. При этом, как будет показано в дальнейшем, шероховатость поверхности композита растет (при изготовлении образцы проходят полировку, в процессе приработки на них образуется развитый рельеф). На рис. 1б представлен график зависимости коэффициента изнашивания от температуры и контактного давления. На рис. 2 представлен вид и рельеф поверхности трения углеродного композита, полученные методами РЭМ и СЗМ, с пленкой третьего тела и без нее. Продукты износа образуют на поверхности материала устойчивую пленку, практически целиком закрывающую поверхность.
Рис. 1.
Результаты трибологических испытаний композита: а – зависимость коэффициента трения и температуры от времени испытания при V = 2.5 м/с, P = 0.75 МПа; б – зависимость коэффициента изнашивания от температуры и контактного давления.
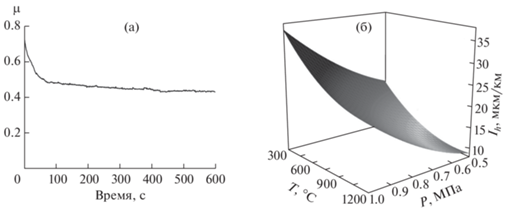
Рис. 2.
Поверхность трения углеродного композита: а – общий вид с пленкой третьего тела, РЭМ; б – общий вид с удаленной пленкой, РЭМ; в – рельеф поверхности с пленкой, СЗМ; г – рельеф поверхности с удаленной пленкой, СЗМ.
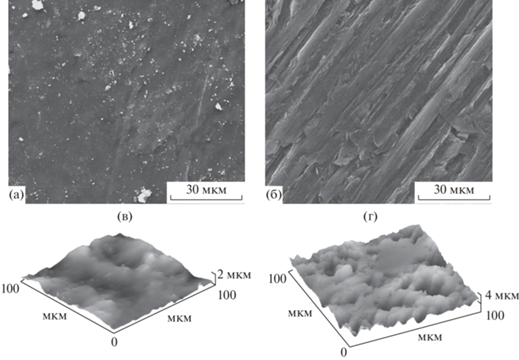
В процессе трения на поверхности композита образуется развитый рельеф, что является следствием его неоднородной структуры. Это позволяет существовать на поверхности материала достаточно толстой пленке продуктов износа без полного разделения трущихся поверхностей (что привело бы к прекращению износа). Наличие пленки третьего тела частично сглаживает шероховатость поверхности композита и уменьшает трение между поверхностями (последнее хорошо заметно на графике рис. 1а). На рис. 3 показаны продукты износа, собранные в процессе трения. Они состоят из отдельных частиц диаметром около 1 мкм (рис. 3а) и фрагментов пленки продуктов износа целиком (рис. 3б). Наличие последних является следствием высокой пластичности продуктов углерода при высоких давлениях и температурах, достигающихся в контакте, что в свою очередь, позволяет экспериментально оценить толщину пленки в установившемся режиме трения.
Рис. 3.
РЭМ-изображение продуктов износа углеродного композита: а – отдельные частицы; б – фрагмент пленки третьего тела целиком, в – край фрагмента пленки при высоком увеличении.
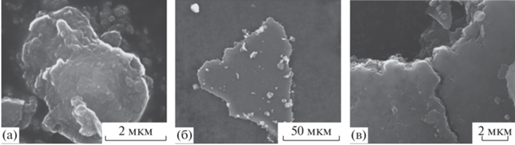
На рис. 4. представлены результаты Рáман-спектроскопии компонентов композита (волокна (кривая 1) и матрицы (кривая 2)) и пленки третьего тела (кривая 3). Во всех спектрах присутствуют полосы с максимумом в области 1350 и 1580 см–1 (D и G-полосы графита соответственно) и полосы фононных повторений в области 2400–3000 см–1. Полученные данные D и G-полос демонстрируют различия в их ширине и интенсивности. Из графиков следует, что интенсивность полосы D в 1.5 раза меньше полосы G и полная ширина полосы на половине высоты меньше 100 см–1 (кривая 1). Такой спектр характерен для хорошо закристаллизованного графита. В противоположном случае, когда интенсивность полосы D равна или больше интенсивности полосы G и полная ширина полосы на половине высоты больше 100 см–1 (кривая 2), тогда спектр характерен для наноструктурированных углеродных материалов. Кривая 3 значительно отличается от кривых 1 и 2, из чего можно сделать вывод о том, что вещество композита претерпевает значительную трансформацию при миграции в пленку третьего тела.
ОБСУЖДЕНИЕ РЕЗУЛЬТАТОВ
Количество вещества композита, расходуемого при изнашивании в единицу времени, может быть оценено в соответствии с линейной моделью третьего тела по формуле:
где QS – объем вещества композита, переходящий в зазор контакта в результате износа за единицу времени; V – скорость скольжения; S – площадь контакта; H – средняя толщина пленки третьего тела; Hmax – максимально возможная толщина пленки третьего тела, при достижении которой поверхности полностью разделяются и интенсивность изнашивания падает практически до нуля; CS – константа пропорциональности, зависящая от конкретного материала, контактного давления и температуры.При этом количество вещества, покидающего зазор контакта трущихся тел, может быть оценено по формуле:
где QW – объем вещества третьего тела, покидающего зазор контакта через его границу за единицу времени; L – периметр границы контакта; CW – константа пропорциональности, зависящая от конкретного материала, контактного давления и температуры.Соответственно, поделив (1) и (2) на SV и приравняв друг другу, получаем установившуюся безразмерную интенсивность изнашивания материала:
(3)
$\bar {u} = {{C}_{S}}\left( {{{H}_{{{\text{max}}}}} - H} \right) = {{{{C}_{W}}HL} \mathord{\left/ {\vphantom {{{{C}_{W}}HL} {S.}}} \right. \kern-0em} {S.}}$(4)
$\left\{ \begin{gathered} {{H}_{1}} = \frac{{{{C}_{S}}{{H}_{{{\text{max}}}}}}}{{\frac{{{{C}_{W}}{{L}_{1}}}}{{{{S}_{1}}}} + {{C}_{S}}}}, \hfill \\ {{u}_{1}} = \frac{{{{C}_{S}}{{H}_{{{\text{max}}}}}}}{{1 + \frac{{{{C}_{S}}{{S}_{1}}}}{{{{C}_{W}}{{L}_{1}}}}}}. \hfill \\ \end{gathered} \right.$При этом параметр Hmax определяется в основном рельефом поверхности композита, который, в свою очередь, определяется структурой материала и параметрами контакта на микроуровне. Отсюда следует, что эта величина будет мало меняться в зависимости от конфигурации контакта, но будет зависеть от контактных давлений и температур.
В нашем случае параметры $\bar {u},{{H}_{{{\text{max}}}}},H,L,S$ для температур и нагрузок (в среднем), характерных для работы авиационного тормоза (контактное давление 0.7 МПа, температура 750°C), можно оценить из следующих соображений.
Безразмерная интенсивность изнашивания составляет 17 мкм/км (рис. 1б), т.е. $\bar {u}$ = 17 × 10–9.
Максимальная толщина плeнки может быть оценена из шероховатости поверхности на микроуровне (рис. 2г), Hmax ≈ 9 мкм.
Толщину пленки в установившемся режиме изнашивания можно оценить, во-первых, как разность между максимальным перепадом шероховатости поверхности с пленкой и без нее (рис. 2в, 2г); во-вторых, через максимальный размер частиц износа, которые являются фрагментами пленки, выдавливаемой через границу контакта (рис. 3а); в-третьих, непосредственно из ее РЭМ-изображений (рис. 3в). Все методы дают сходный результат H ≈ 2.5 мкм.
Геометрический параметр L/S = 0.67 × 10–3 мкм–1. Отсюда, получаем CS = 2.43 × 10–9 мкм–1 и CW = = 12.69 × 10–6. На рис. 5 показаны графики зависимости толщины пленки третьего тела и интенсивности изнашивания от геометрического фактора контакта.
Рис. 5.
Зависимости толщины пленки третьего тела (а) и интенсивности изнашивания (б) от геометрического фактора контакта.
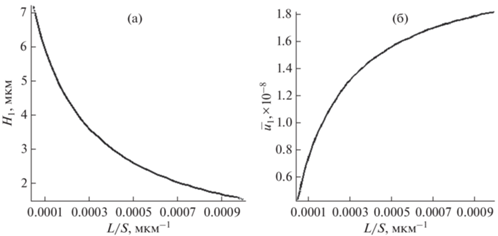
Анализируя графики можно сделать вывод, что при геометрическом факторе, характерном для полноразмерных авиационных тормозных дисков (L/S ≈ 10–4 мкм–1), толщина пленки значительно вырастет, приближаясь к максимально возможной, а интенсивность изнашивания будет примерно в три раза меньше, чем при испытаниях на трибометре в аналогичных условиях (L/S = = 0.67 × 10–3 мкм–1). Действительно, для тормозных дисков из АДФ-ОС характерен износ ≈1 мкм/торможение, что примерно соответствует 5 мкм/км. Большая толщина пленки вызывает уменьшение реального контакта между поверхностями композитов, что вызывает также уменьшение коэффициента трения (рис. 1а): коэффициент трения в начале испытаний до образования пленки достигает 0.7, а после – спадает до 0.4. При трении полноразмерных композитных дисков коэффициент трения еще меньше (0.25–0.35).
Таким образом, третье тело является одним из важнейших механизмов (наряду с термоупругой неустойчивостью [20]) действия масштабного фактора при трении высоконагруженных трибосопряжений из углерод-углеродного композитного материала.
ЗАКЛЮЧЕНИЕ
При трении углерод-углеродных композитных материалов на их поверхности образуется достаточно заметная и плотная пленка из частиц износа, которая значительно влияет на характеристики процесса трения.
Наличие этой пленки (за счет частичного разделения взаимодействующих поверхностей) уменьшает как коэффициент трения, так и интенсивность изнашивания.
Толщина этой пленки определяется геометрическими параметрами контактирующих поверхностей (в том числе), что может вызывать отличие результатов между испытаниями тестовых образцов и трением полноразмерных изделий.
Применение методик РЭМ, СЗМ и Рáман-спектроскопии в комплексе с трибологическими испытаниями позволяет оценить величину влияния третьего тела на трение и изнашивание углерод-углеродных композитных материалов.
Список литературы
Khruschov M.M. // Wear. 1974. V. 28. P. 69.
Zum-Gahr K.H. // International Conference on Wear of Materials, American Society of Material Engineering. 1985. P. 793.
Gun Y. Lee, Dharan C.K.H., Ritchie R.O. // Wear. 2002. V. 252. P. 322.
Yen B., Dharan C.K.H. // Wear. 1996. V. 195. P. 123.
Горячева И.Г., Торская Е.В. // Трение и износ. 1992. Т. 13. № 1. С. 185.
Shpenev A. // Advanced Materials. PHENMA 2017. Springer Proceedings in Physics. 2018. V. 207. P. 459.
Goryacheva I.G., Makhovskaya Y.Y. // Multiscale Solid Mechanics. Advanced Structured Materials. 2021. V. 141. https://doi.org/10.1007/978-3-030-54928-2_13
Shpenev A.G. // Materials Physics and Mechanics. 2020. V. 44. № 2. P. 229.
Zhang Y., Mollon G., Descartes S. // Tribology International. 2020. V. 145. P. 106188.
Renouf M., Cao H.-P., Nhu V.-H. // Tribology International. 2011. V. 44. P. 417.
Argatov I., Chai Y. // Wear. 2021. V. 466–467. P. 203562.
Donea V., Kesavana D., Krishna M., Chaisec T., Neliasc D. // Tribology International. 2017. V. 109. P. 1.
Majcherczak D., Dufrenoy P., Berthier Y., Nait-Abdelaziz M. // Wear. 2006. V. 261. P. 467.
Österlea W., Dörfel I., Prietzel C., Roocha H., Cristol-Bulthé A.-L., Degallaix G., Desplanques Y. // Wear. 2009. V. 267. P. 781.
Fillot N., Iordanoff I., Berthier Y. // Wear. 2007. V. 262. P. 949.
Буковский П.О., Морозов А.В., Кириченко А.Н. // Трение и износ. 2020. Т. 41. № 4. С. 448.
Shcherbakova O.O., Shpenev A.G., Zagorskiy D.L., Muravyeva T.I. // IOP Conference Series: Materials Science and Engineering. 2019. V. 699. P. 012032.
Shpenev A.G., Muravyeva T.I., Shkalei I.V., Kulakov V.V., Golubkov A.K. // Procedia Structural Integrity. 2020. V. 28. P. 1702.
Bokobza L., Bruneel J.-L., Couzi M. // Vibrational Spectroscopy. 2014. № 74. P. 57.
Shpenev A.G. // J. Friction and Wear. 2021. V. 42. № 1. P. 30.
Дополнительные материалы отсутствуют.
Инструменты
Поверхность. Рентгеновские, синхротронные и нейтронные исследования