Приборы и техника эксперимента, 2021, № 6, стр. 114-119
ИЗМЕРЕНИЕ МГНОВЕННЫХ ЗНАЧЕНИЙ ТЕМПЕРАТУРЫ ГАЗОВ ГАЗОТУРБИННОГО ДВИГАТЕЛЯ С ИСПОЛЬЗОВАНИЕМ АКУСТИЧЕСКИХ МУЛЬТИВИБРАТОРОВ
А. В. Артюхов a, В. Г. Марков b, Ж. А. Сухинец c, А. И. Гулин d, *
a АО “Объединенная двигательная корпорация”
105118 Москва, просп. Буденного, 16, Россия
b Центральный институт авиационного моторостроения им. П.И. Баранова
111116 Москва, ул. Авиамоторная, 2, Россия
c Уфимский государственный авиационный технический университет
450025 Уфа, ул. К. Маркса, 12, Россия
d Уфимский государственный нефтяной технический университет
450062 Уфа, ул. Космонавтов, 1, Россия
* E-mail: gulin1940@gmail.com
Поступила в редакцию 24.03.2021
После доработки 16.05.2021
Принята к публикации 18.05.2021
Аннотация
Разработано дифференциальное устройство для измерения температуры в канале управления газотурбинного двигателя (г.т.д.), где неравномерность поля температур по радиусу и по окружности достигает 100–400 K и может меняться на переходных режимах со скоростью до 400 К/с. Устройство состоит из двух каналов измерения и блока обработки информации и обладает чувствительностью 8.5 Гц/К. Быстродействие устройства на три порядка превышает быстродействие термопар, что позволяет измерять истинную температуру газов г.т.д. Представлены функциональная схема устройства, описаны стенды для проведения испытаний, приведены результаты исследований, подтверждающие высокие метрологические характеристики устройства измерения.
ВВЕДЕНИЕ
Одним из основных параметров, определяющих прогресс в авиадвигателестроении [1], является температура газа перед турбиной, обеспечивающая энергетические и тяговые характеристики двигателя. Каждое новое поколение газотурбинного двигателя (г.т.д.), а всего их насчитывают пять, характеризуется ростом этой температуры на 100–200 К.
Камера сгорания – один из важнейших элементов г.т.д., совершенство которой в значительной мере определяет надежность и экономичность двигателя. Основное назначение камеры сгорания – преобразование химической энергии топлива в тепловую энергию. Коэффициент полезного действия и мощность г.т.д. возрастают с повышением температуры газа и давления в камере сгорания. В связи с этим основным назначением систем управления г.д.т. является обеспечение высокой точности поддержания заданной температуры на установившихся и переходных режимах [2] для получения требуемых характеристик и сохранения ресурса двигателя. Погрешности регулирования температуры газа на установившихся режимах не должны превышать 5–10 К, а на переходных режимах допустимая величина “заброса” температуры составляет 30–50 К за время не более 0.5–1 с. При этом скорость изменения температуры газа на переходных режимах может достигать 400 К/с. Неравномерность поля температур г.т.д. как перед турбиной, так и за ней по радиусу и по окружности [3] составляет 100–400 К и изменяется в зависимости от режима работы двигателя. Наблюдается также нерегулярность поля температур газа, т.е. в одной и той же точке измерения при неизменном режиме работы двигателя температура газа во времени изменяется по произвольному закону. Это объясняется непостоянной подачей топлива в г.т.д. и большой турбулентностью потока воздуха.
АКТУАЛЬНОСТЬ РАЗРАБОТКИ СРЕДСТВА ИЗМЕРЕНИЯ ТЕМПЕРАТУРЫ ГАЗА Г.Т.Д.
Используемые в настоящее время термопары имеют большую инерционность и не позволяют измерить истинную температуру газа в двигателе. Поэтому вместо локальной температуры измеряют лишь приближенно среднемассовую, осредненную температуру. Обычно устанавливают от 8 до 24 и более экранированных термопар, позволяющих измерять температуру с погрешностью не более ±2 K. Экранирование термопар ухудшает их динамические свойства, т.е. увеличивает постоянную времени, которая находится в пределах 0.5–8 с. Для ее компенсации вводят последовательное корректирующее устройство по составляющим, пропорциональным изменению э.д.с. термопары и ее производной. При этом компенсация, близкая к оптимальной, обеспечивается только при устойчивых режимах работы двигателя на автопилоте. На других же режимах будет или недокомпенсация, или перекомпенсация.
В работе [4] рассмотрен оптический метод спектрального контроля процессов в камерах сгорания г.т.д. Разработанная лабораторная установка позволяет контролировать параметры горения как косвенно, так и в режиме реального времени, не нарушая первичный поток горения. Метод основан на регистрации излучения, испускаемого в узких спектральных диапазонах видимого излучения, от молекул, присутствующих в продуктах сгорания в газообразном несмешанном топливном пламени. Излучение от радикалов C2 и CH используется для установления корреляции с температурой пламени и коэффициентом эквивалентности топлива/воздуха. Измерения проводились на специально разработанном испытательном стенде с пропановой горелкой с температурой более 1400 К. Дальнейшее развитие этого метода позволит проводить исследовательские работы по двигателям на стационарных стендах.
Можно констатировать, что в настоящее время нет прямых быстродействующих методов измерения температуры газов г.т.д., позволяющих создавать системы управления параметрами работы двигателя вблизи их функциональных, прочностных и температурных ограничений [5, 6] с предотвращением выхода за пределы допустимых значений за десятые доли секунды. Необходимо отметить, что превышение температуры лопаток г.т.д. выше предельных на 5 K приводит к перерасходу топлива и уменьшению ресурса двигателя примерно на 7–10%. Таким образом, работы по исследованию и созданию систем для динамических измерений температуры газов г.т.д. являются весьма актуальными.
ДИФФЕРЕНЦИАЛЬНОЕ УСТРОЙСТВО ИЗМЕРЕНИЯ ТЕМПЕРАТУРЫ
Струйные системы измерения температуры более перспективны [7], так как обладают высоким быстродействием, на три-четыре порядка выше термопреобразователей, нечувствительностью к электромагнитным и радиационным полям, простой конструкцией и высокой надежностью.
Рассмотрим работу дифференциального устройства измерения температуры [8, 9] газового потока (рис. 1). Два струйных генератора СГ1 и СГ2 устанавливают на посадочное место термопар и помещают в газовый поток, абсолютную температуру T которого измеряют. В струйных генераторах, являющихся акустическими мультивибраторами, расположенными в одном корпусе, но относящихся к двум каналам измерения 1 и 2, возбуждаются акустические колебания прямоугольной формы с частотами ${{f}_{{A1}}}$ и ${{f}_{{A2}}}$. С помощью пьезоэлементов ПЭ они преобразуются в электрические полигармонические колебания $n{{f}_{1}}$ и $n{{f}_{2}}$, поступающие на входы адаптивных селекторов АС. ПЭ вместо прямоугольных импульсов воспроизводят, в соответствии с преобразованием Фурье, спектр синусоидальных частот электрических напряжений. В АС осуществляется отбор первых гармоник ${{f}_{1}}$ и ${{f}_{2}}$, пропорциональных измеряемой температуре T газового потока каждым СГ.
Рис. 1.
Дифференциальное устройство измерения температуры газового потока. СГ – струйный генератор; ПЭ – пьезоэлемент; АС – адаптивный селектор; ВЧ – вычитатель частот; ДЧ – делитель частоты.
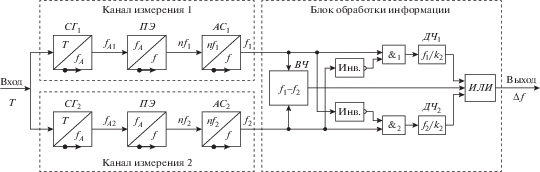
В блоке обработки информации с выхода вычитателя частот ВЧ, реализующего дифференциальный принцип измерения, разница частот $\Delta f = {{f}_{1}} - {{f}_{2}}$, также пропорциональная температуре газового потока, через элемент ИЛИ поступает на выход устройства. Дифференциальное включение повышает быстродействие устройства [10] в два с лишним раза за счет сокращения переходного процесса установления измеряемой разницы частот. При выходе из строя одного из каналов измерения, например первого, схема И запирается нулевым потенциалом с выхода АС2, и через инвертор НЕ открывается схема И второго канала, пропуская частоту ${{f}_{2}}$ после ее деления в ${{k}_{2}}$ раз делителем частоты ДЧ через элемент ИЛИ на выход устройства в виде $\Delta f$. Аналогичным образом работает схема при выходе из строя второго канала измерения. Коэффициенты деления k1 и k2 ДЧ выбирают таким образом, чтобы частоты на их выходах были равны разности частот $\Delta f$, т.е.
ПРИНЦИП РАБОТЫ СТРУЙНОГО ГЕНЕРАТОРА
Струйный генератор представляет собой миниатюрную звуковую или ультразвуковую замкнутую автоколебательную нелинейную систему [11], являющуюся акустическим мультивибратором, выходной сигнал которой частотой ${{f}_{А}}$ имеет прямоугольную форму. Частота ${{f}_{А}}$ связана с измеряемой абсолютной температурой Т выражением
где b – коэффициент, зависящий от конструктивных параметров СГ.Струйно-акустический датчик, внешний вид которого представлен на рис. 2а, снабжен входным устройством 1 (рис. 2б) и резонатором 2, который через звуковод 3 сообщается с пьезоэлементом 4. Газ, протекающий через СГ, сбрасывается через выхлопной жиклер 5 и канал 6, соединенный со штуцером 7, в область пониженного давления. Разница давлений на входе и выходе, необходимая для нормальной работы СГ, должна различаться не менее чем вдвое.
Рис. 2.
Внешний вид (а) и схема (б) струйно-акустического датчика температуры и пневматическая схема струйного генератора (в). 1 – входное устройство, 2 – резонатор, 3 – звуковод, 4 – пьезоэлемент, 5 – выхлопной жиклер, 6 – канал, 7 – штуцер, 8 – сопло питания, 9 – рабочая камера, 10 – первый канал обратной связи, 11 – второй канал обратной связи, 12 – первый выходной канал, 13 – второй выходной канал.
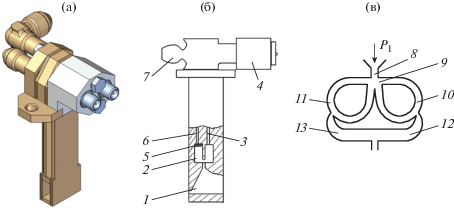
Процесс возникновения автоколебаний в СГ (рис. 2в) происходит следующим образом. Поток, вытекающий из сопла питания 8, первоначально (вследствие имеющейся естественной несимметрии конструкции) отклоняется к одной из боковых стенок рабочей камеры 9, при этом повышается давление на входе, например, в канале обратной связи 10. Взаимодействие основного потока, вытекающего из сопла питания 8, с управляющим потоком из канала обратной связи 10 приводит к вытеснению основного потока к противоположной стенке. В результате в каналах обратной связи 10, 11 и в выходных каналах 12, 13 создаются колебания давлений с частотой, определяемой временными задержками развития процессов в рабочей камере 9 и каналах обратной связи 10, 11.
Следует отметить, что для частот 3000–36 000 Гц, соответствующих рассматриваемому температурному диапазону 293–2000 К, СГ имеет конструктивные размеры, позволяющие его устанавливать на те же посадочные места, что и термопары.
Выбор начальной частоты генерации важен с точки зрения получения необходимой разрешающей способности струйно-акустического датчика температуры. Производная частоты от температуры может быть определена как:
Согласно приведенной формуле, увеличение начальной частоты положительно сказывается на чувствительности датчика. Частота колебаний при нормальной температуре (Т = 293 К) и давлении среды Р = 1.01 бар для аналогичных генераторов составляет порядка 5 кГц. При выборе такого значения номинальной частоты руководствовались, с одной стороны, возможностью иметь высокую чувствительность генератора по температуре, а с другой – ограничениями, возникающими при передаче колебаний давления по специальному каналу к пьезопреобразователю.
К преимуществам струйно-акустических генераторов с резонаторами перед генераторами других типов следует отнести:
– высокую чувствительность при Т = 293 К и f = 5 кГц: df/dT = 8.5 Гц/K;
– малую инерционность, так как каналы имеют интенсивный проток газа;
– меньшую вероятность засорения (нет длинных и узких каналов);
– простую конфигурацию проточной части, т.е. технологичность в изготовлении.
Сложность процессов, происходящих при течении газа в каналах СГ, и отсутствие аналитического описания газодинамических и пневмоакустических явлений привели к тому, что в настоящее время зависимость частоты f от таких параметров, как геометрические размеры и форма проточной части, полное давление в потоке, а также степень расширения газа в сопле питания, необходимо исследовать экспериментально, путем снятия статических и динамических характеристик для конкретного типа СГ:
Здесь k – показатель адиабаты (для воздуха k = 1.4); R – газовая постоянная (для воздуха R = = 287.14 Дж/(кг · К)); l1 – характерные размеры проточной части; λ1 – безразмерная скорость внутреннего потока, однозначно связанная с отношением давлений J = Pвх/Pвых, где Pвх – полное давление на входе СГ, а Pвых– статическое давление на выходе.Исследования различных СГ показали, что частота $f$ колебаний в них, при прочих неизменных условиях, пропорциональна скорости распространения возмущений в газе, заполняющем рабочую полость и каналы обратной связи, т.е.:
где Т – абсолютная температура газа на входе в СГ; λ – длина волны акустических колебаний СГ, равная суммарной длине каналов обратной связи 10, 11 датчика на рис. 2в.Типовая переходная характеристика СГ при скачкообразном изменении температуры представлена на рис. 3. Она состоит из двух участков. Первый – характеризуется отработкой выходного сигнала на величину ${{a}_{1}}$ за время ${{t}_{1}}$, которое равно времени прохождения газа по каналам генератора. Поскольку скорость W потока газа в генераторе больше 10 м/с, а длина L резонансных каналов менее 0.02 м, то ${{t}_{1}}$ = L/W < 0.002 с. Величина ${{a}_{1}}$ определяется [12] процессами теплообмена во внутренних полостях СГ.
Второй участок характеристики определяется прогревом стенок датчика. При скачкообразном изменении температуры газа до значения Тг изменение температуры стенки Тст датчика по времени равно
где Tст0 – температура стенки в начальный момент времени; t – время от момента скачка температуры газа; t0 – постоянная времени прогрева стенок датчика.ЭКСПЕРИМЕНТ
Схема измерения температуры газа в камере сгорания г.т.д. представлена на рис. 4.
Зависимости установившихся значений выходных частот от температуры газов г.т.д. в обоих каналах устройства измерения приведены на рис. 5.
Рис. 5.
Зависимости установившихся значений выходных частот от температуры газов г.т.д. в обоих каналах устройства измерения.
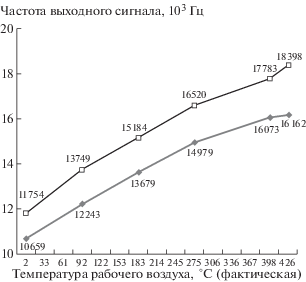
На рис. 6 представлена динамическая характеристика, полученная при скачке температуры на 300°С, на которой видны выбросы температуры, связанные с турбулентностью подаваемого горячего воздуха в тепловую камеру.
Выбросы температуры в основном составляют ±10 К, а некоторые – до 40 K и связаны с турбулентностью подаваемого воздуха.
На рис. 7 представлены динамические характеристики термопары (штриховая линия) и струйно-акустического датчика (сплошная линия), полученные при испытаниях реального г.д.т. Выбросы температуры в основном составляют ±10 K, а некоторые – до 40 K и связаны как с турбулентностью газов, так и с неравномерностью процессов горения топлива.
Рис. 7.
Графики динамических характеристик термопары (штриховая линия) и струйно-акустического датчика (сплошная линия).

Увеличенный фрагмент графика изменения температуры в камере сгорания г.д.т., представленный на рис. 8, демонстрирует высокое быстродействие дифференциального устройства измерения температуры газового потока.
В работе [13] представлены результаты испытаний спектральной системы измерения температуры газового потока на брэгговских решетках внутри камеры сгорания г.д.т. Результаты показывают, что быстродействие предлагаемой системы измерений находится на уровне пирометрических. Спектральная система основана на методе многоволновой пирометрии сажи в видимом оптическом диапазоне и содержит мультиспектральный сенсорный датчик на кристалле, который позволяет измерять температуру в диапазоне от 1083 до 1393 К с погрешностью 3%.
ВЫВОДЫ
Испытания, проведенные на стенде-имитаторе газотурбинного двигателя, подтвердили высокие быстродействие и точность измерения температуры газового потока г.т.д. разработанного дифференциального устройства. Устройство может быть использовано для исследования теплообменных процессов в камерах сгорания как вновь создаваемых г.т.д., так и уже используемых, но с различными видами топлива, а также для выявления предпомпажных явлений.
Испытания, проведенные на г.т.д., выявили возможность управления его работой на переходных режимах в реальном времени.
Температура использования струйно-акустического датчика ограничена материалом, из которого он изготовлен.
В отличие от устройств на основе оптических методов, имеющих такой недостаток, как закопчение, разработанное устройство позволит создавать автоматические системы взлета и посадки летательных аппаратов.
Список литературы
https://www.elektro-expo.ru/ru/articles/2016/gazoturbinnye-ustanovki-dlya-proizvodstva-elektroenergii/
http://avia.pro/blog/regulirovanie-temperatury-gaza-v-gtd
Сухинец Ж.А., Гулин А.И., Галиев А.Л. // Cб. трудов IV Международной научно-практической конференции “Актуальные проблемы науки и образования в современном вузе” / Под ред. А.Л. Галиева. (Стерлитамак, 23–25 мая 2019 г.) Уфа: Башкирский государственный университет, 2019. С. 544–553.
Mekhgrengin M.V., Guriev V.I., Meshkovskii I.K., Smirnov D.S., Sukhinets A.V. / /IEEE East-West Design & Test Symposium (EWDTS) 2018. P. 876. https://doi.org/10.1109/EWDTS.2018.8524839
Юнаков Л.П. Основы теории авиационных газотурбинных двигателей: учебное пособие / Под ред. Л.П. Юнакова. СПб.: Балт. гос. техн. ун-т, 2013.
Иноземцев А.А. Основы конструирования авиационных двигателей энергетических установок: учебник. Т. 1 / Под ред. А.А. Иноземцева, М.А. Нихамкина, В.Л. Сандрацкого. М.: Машиностроение, 2008.
Сухинец Ж.А., Галиев А.Л., Гулин А.И. // Авиакосмическое приборостроение. 2015. № 10. С. 4.
Сухинец Ж.А., Гатчина Ю.А., Гулин А.И. // Датчики и системы. 2017. № 4. С. 31.
Гатчин Ю.А., Сухинец Ж.А., Гулин А.И. Патент № 2626232 РФ // Бюл. № 21. Опубл. 24.07.2017.
Гулин А.И. // Авиакосмическое приборостроение. 2012. № 9. С. 10.
Залманзон Л.А. Теория элементов пневмоники. М.: Наука, 1969.
Sukhinets Zh.A., Sukhinets A.V., Gulin A.I. // 2017 IEEE East-West Design & Test Symposium (EWDTS). 2017. P. 1. doi 10,1109 / EWDTS.2017.8110088
Mekhgrengin M.V., Meshkovskii I.K., Tashkinov V.A., Guriev V.I., Sukhinets A.V., Smirnov D.S. // Measurement. 2019. V. 139. P. 355. https://doi.org/10.1016/j.measurement.2019.02.084
Дополнительные материалы отсутствуют.
Инструменты
Приборы и техника эксперимента