Радиотехника и электроника, 2019, T. 64, № 8, стр. 811-818
Исследование и разработка состава LTCC-керамики для создания приборов СВЧ-диапазона
Д. А. Вайман 1, *, В. С. Данилов 1
1 Новосибирский государственный технический университет
630073 Новосибирск, просп. Карла Маркса, 20, Российская Федерация
* E-mail: dima-1nsk@mail.ru
Поступила в редакцию 20.04.2018
После доработки 03.02.2019
Принята к публикации 12.02.2019
Аннотация
Представлены результаты теоретических исследований и экспериментальных работ по разработке технологии изготовления LTCC-керамики для создания приборов СВЧ-диапазона, а также результаты расчета и приготовления двух керамических шликеров c разными типами стекол для изготовления “сырых” керамических LTCC-листов. Подтверждено экспериментально, что разработанный состав технологической связки по свойствам идентичен керамике “Ferro A6M”. Показано, что такие стеклообразующие компоненты, как BaO, PbO, позволяют добиться увеличения диэлектрической проницаемости и снижения тангенса угла диэлектрических потерь всего материала в целом. Проведено сравнение основных характеристик полученного материала и LTCC-керамики “Ferro A6M”.
1. ПОСТАНОВКА ЗАДАЧИ
Для решения задач по миниатюризации устройств радиоэлектронной аппаратуры используют LTCC-керамику (Low temperature co-fired ceramic – низкотемпературная совместно обжигаемая керамика). Высокий интерес разработчиков и производителей СВЧ-приборов к данному материалу вызван многими его преимуществами по сравнению с традиционными решениями.
Существующий способ – нанесение проводников на полированные керамические подложки и установка навесных компонентов – уже не в состоянии обеспечить современные требования миниатюризации и интеграции устройств. К тому же во многих случаях приходится применять дополнительные соединения и перемычки, что негативно сказывается, не только на свойствах СВЧ-устройств, но и на технологичности их изготовления. Другой традиционный способ – технология HTCC-керамики (High temperature co-fired ceramic – высокотемпературная совместно обжигаемая керамика), позволяющий создавать многослойные структуры с проводящими слоями и переходными металлизационными отверстиями. Но из-за высокой температуры спекания (1500…1850°С) данная технология ограничена в выборе материала проводящих слоев. Как правило, в качестве основного компонента проводников используют молибден и вольфрам с высоким удельным сопротивлением, что неблагоприятно влияет на характеристики готовых СВЧ-устройств. Также высокие требования к среде обжига и большая, более 18…22%, геометрическая усадка накладывают серьезные технологические ограничения.
LTCC-керамика обладает следующими преимуществами [1–5]. Низкая температура спекания (750…1000°С) позволяет использовать для создания проводников низкоомные металлизационные пасты на основе серебра, золота и т.д. (по сравнению с HTCC-технологией).
1. Возможность создания трехмерных структур до 80 и более рабочих слоев. LTCC системы позволяют создавать полости, отверстия, использовать встроенные пассивные компоненты.
2. Геометрическая усадка керамики, в большинстве систем материалов LTCC представленных на рынке, в процессе спекания не превышает 10–15%, что позволяет значительно увеличить точность изготовления устройств.
3. Механическая устойчивость и сохранение стабильных линейных размеров обеспечиваются малым коэффициентом теплового расширения, значение которого близко ко многим известным полупроводниковым материалам, что позволяет устанавливать полупроводниковые кристаллы непосредственно на основание керамической платы.
4. Низкие диэлектрические потери, стабильные в широком диапазоне частот. Для разных типов систем диэлектрическая проницаемость (ε) LTCC-керамики варьируется от 6 до 12, а тангенс угла диэлектрических потерь (tg δ) от 0.006 до 0.0001 в СВЧ-диапазоне.
5. В отличие от HTCC-керамики не требуется создания специальных сред для обжига при использовании металлизационных паст на основе серебра, золота, а технологический цикл короче и менее энергоемкий, что делает технологию LTCC-керамики более экономически выгодной.
Производство изделий из данного материала осуществляется по технологии литья тонких керамических пленок (в среднем от 50 до 200 мкм [6]. В целом, изготовление изделий из низкотемпературной совместно обжигаемой керамики можно разделить на две составляющие (рис. 1): первая (п. 1–4) – создание керамических “сырых листов” и вторая часть (п. 5–12) – формирование из них трехмерных интегральных систем [6–9].
Вторая часть данной технологии успешно внедрена на многих предприятиях России. Однако производство отечественных “сырых” керамических листов практически отсутствует, поэтому для разработки и производства многих приборов используют сырье американских фирм “DuPont” и “Ferro” [5, 10].
Цель данной работы – проанализировать физические и электрические характеристики основных компонентов стекол, выпускаемых отечественной промышленностью и разработать собственный состав LTCC-керамики для создания приборов СВЧ-диапазона.
2. ПОДБОР СТЕКЛА
Качество керамической пленки: пластичность, прочность, однородность, способность ламинироваться, совместимость для трафаретной печати и т.д., определяется тщательно подобранными компонентами и технологическими режимами приготовления шликера и литья керамической пленки. Чтобы придать “сухим” компонентам свойства жидкости, добавляют технологическую связку. В данном случае под “сухими” компонентами понимается порошки керамического глинозема, стекла и прочих порошковых дополнительных добавок. Ключевым компонентом, способствующим снижению температуры спекания и оказывающий большое влияние на диэлектрические характеристики является стекло [2, 6, 7, 11].
Материалы для введения стеклообразующих оксидов по химическому признаку подразделяют на три группы:
1) материалы для введения кислотных оксидов (SiO2, B2O3, А12О3, TiO2, ZrO2, P2O5 и др.);
2) материалы для введения оксидов щелочноземельных металлов (CaO, MgO, BaO, SrO и др.);
3) материалы для введения щелочных оксидов (Na2O, K2O, Li2O) [12].
Авторы работы [13] провели анализ стеклокомпонентов, используемых для создания LTCC-керамики компаний “DuPont” и “Ferro”. На образцах необожженных пленок керамики проведено исследование микроструктуры. Результаты рентгенофазового и элементного анализа показали, что исходные материалы представляют собой порошки оксида алюминия и стекол различных составов: стеклокомпоненты пленки “DuPont 951” представлены оксидами группы PbO–CaO–SiO2–Al2O3–Na2O–K2O, а пленки фирмы "Ferro L8" – бессвинцовым стеклом BaO–TiO2–SiO2–Al2O3–CaO. Также было выявлено, что в процессе обжига для образца “DuPont 951” происходят процессы спекания и кристаллизации анортита CaO–Al2O3–2SiO2, а для “Ferro L8” – процессы спекания и одновременной кристаллизации цельзиана Ba–Al2O3–2SiO2 и волластонита CaO–SiO2. Отметим, что присутствие в составе данных стекол большого содержания тяжелых оксидов BaO, PbO позволяет существенно увеличить показатель диэлектрической проницаемости и снизить тангенс угла диэлектрических потерь [14–16]. Снижению тангенса угла диэлектрических потерь также способствует содержание оксида алюминия Al2O3. Присутствие оксидов щелочных металлов с наличием ионов Na или K увеличивает удельное электрическое сопротивление. К увеличению диэлектрических потерь приводят такие компоненты как Fe2O3, Cr2O3, V2O5 и NiO. Влияние различных компонентов стекла на физические и диэлектрические характеристики представлено в табл. 1 [12, 14–19].
Таблица 1.
Влияние различных компонентов стекла на физические и диэлектрические характеристики
Свойства и характеристики | Оксиды силикатных стекол | ||||||||||
---|---|---|---|---|---|---|---|---|---|---|---|
SiO2 | K2O | Na2O | CaO | MgO | BaO | PbO | Al2O3 | B2O3 | P2O3 | TiO2 | |
Тпл | + | – | – | – | ± | – | – | + | – | + | – |
η | + | – | – | – | ± | – | – | + | – | ± | – |
Механические свойства | + | + | – | + | – | – | – | + | + | + | + |
Химическая стойкость | + | – | – | + | – | – | – | + | + | + | + |
ТКЛР | – | + | + | + | + | + | + | – | – | + | – |
ε | – | + | + | + | ± | + | + | + | – | – | – |
tg δ | – | – | + | ± | – | – | – | – | – | – | + |
В данной работе рассмотрены марки стекол электровакуумной группы, так как они используются при производстве многих электронных приборов. Для изготовления данных стекол используют химически чистые материалы и компоненты, они обладают хорошей химической стойкостью и высокими показателями диэлектрических характеристик. В табл. 2 представлены основные выпускаемые российскими производителями марки стекол и их состав в соответствии с ОСТ 11 027.010-75 [20].
Таблица 2.
Марки стекол и их состав в соответствии с ОСТ 11 027.010-75
Марка стекла | ТКЛР, 10–6/°С | Химический состав стекол, % | |||||||||
---|---|---|---|---|---|---|---|---|---|---|---|
SiO2 | B2O3 | Al2O3 | MgO | CaO | BaO | PbO | Na2O | K2O | другие окислы, % | ||
С48-1 | 4.8 | 66.5 | 23.0 | 3.0 | – | – | – | – | 3.7 | 3.8 | – |
С48-2 | 4.8 | 66.3 | 20.9 | 3.5 | – | – | – | – | 3.0 | 5.0 | 0.2 (Li2O) |
С48-3 | 4.8 | 54.0 | – | 18.5 | – | – | – | – | – | – | 13.5 (CaO); 6.0 (InO); 9.0 (BaO) |
С49-1 | 4.9 | 67.5 | 20.3 | 3.5 | – | – | – | – | 8.7 | – | – |
С52-1 | 5.2 | 68.7 | 19.0 | 3.5 | – | – | – | – | 4.4 | 4.4 | – |
С78-5 | 7.8 | 2.2 | 57.8 | 8.8 | 0.5 | 3.5 | 19.0 | – | – | 8.2 | – |
С82-1 | 8.2 | 71.0 | – | 3.0 | – | 13.0 | – | – | 11.7 | 1.3 | – |
С87-1 | 8.7 | 55.0 | – | 2.0 | – | – | – | 30.0 | 3.8 | 9.2 | – |
С89-1 | 8.9 | 71.0 | – | 0.9 | 8.5 | 5.5 | 2.0 | – | 16.1 | 1.0 | – |
С90-1 | 9.0 | 69.0 | – | 0.7 | 3.5 | 5.5 | – | – | 12.8 | 4.0 | – |
С93-1 | 9.3 | 55.0 | – | 2.0 | – | – | – | 30.0 | 3.8 | 9.2 | – |
С93-2 | 9.3 | 67.5 | – | 5.0 | – | – | 12.0 | – | 7.0 | 7.0 | 0.9 (F2); 0.4 (Li2O) |
С94-1 | 9.4 | 59.8 | – | 3.6 | 2.5 | 5.5 | 2.3 | 10.5 | 5.5 | 9.0 | 0.8 (F2); 0.5 (Li2O) |
С95-2 | 9.5 | 68.5 | 2.8 | 4.0 | – | 7.0 | – | – | 10.0 | 7.7 | – |
Стекла марок С87-1, С93-1 и С94-1 по химическому составу являются схожими со стеклами, используемыми в LTCC-керамики фирм “Ferro L8” и “DuPont 951”. Они содержат тяжелые оксиды BaO, PbO, которые способствуют увеличению показателя диэлектрической проницаемости и снижению тангенса угла диэлектрических потерь. Однако данные стекла обладают большим показателем температурного коэффициента линейного расширения, что может негативно сказаться на характеристиках конечного продукта. Наиболее сбалансированным по химическому составу и физическим свойствам является стекло марки С48-3. В отличие от предыдущих марок оно содержит меньше тяжелых окислов, но наличие Al2O3 также способствует увеличению диэлектрических характеристик. К тому же стекло С48-3 имеет низкий показатель ТКЛР: 4.8 × 10–6/°С, сопоставимый с ТКЛР многих распространенных полупроводников.
3. МЕТОДИКА ЭКСПЕРИМЕНТА
Для проведения эксперимента были приготовлены образцы двух составов LTCC-керамики с использованием марок стекол С95-2 (рецепт 1) и С48-3 (рецепт 2). Выбор стекла марки С95-2 обусловлен его широким применением в радиоэлектронной промышленности и доступностью в приобретении. Недостатками данного стекла является высокий показатель ТКЛР и большое содержание оксида натрия, который негативно сказывается на показателе тангенса угла диэлектрических потерь, но в то же время позволяет снизить температуру плавления. Стекло марки С48-3 имеет низкий показатель температурного коэффициента линейного расширения, сопоставимый с многими полупроводниками. Также наличие в их составе оксидов Al2O3 и BaO способствует улучшению механических и диэлектрических свойств. Для того чтобы данные стекла можно было использовать для приготовления шликера, их измельчали на планетарной мельнице АПФ-3 при частоте вращения барабана 40 об/мин в течение 30 мин. Для более высокой эффективности измельчения специальная емкость была заполнена на 1/3 ацетоном ЧДА ГОСТ 2603-79. В качестве мелющих тел были использованы циркониевые шары диаметром 10 мм. Затем полученный порошок стекла сушили при температуре 90°С в течение 24 ч. Средний размер частиц стекла по результатам замеров методом седиментации и центрифугирования с рентгеновским детектором BI-XDC составил 1.1 мкм, соотношение размера частиц 1 : 5, что является оптимальным показателем для “сухих” компонентов в технологии литья тонких керамических пленок. В качестве керамического порошка был использован Almatis CT1200 SG, измеренный средний размер частиц 0.9 мкм, соотношение размера частиц 1 : 3. Наиболее подробно подбор компонентов, расчет технологической связки и режимы приготовления шликера представлены в работе [21]. Количественный состав экспериментальных рецептов 1 и 2 приготовления шликеров LTCC-керамики одинаков и отличаются только типом используемых стекол – С95-2 и С48-3 соответственно (табл. 3).
Таблица 3.
Количественный состав экспериментальных рецептов 1 и 2
Компоненты | Наименование | Вес, г |
---|---|---|
Мелющие тела цилиндрической формы (∅8 мм) | Al2O3 93% | 765.0 |
Глинозем | Almatis CT 1200 SG | 284.0 |
Стекло | С95-2/С48-3 | 394.0 |
Прочие добавки | – | 32.0 |
Система растворителей | Толуол 99.5% | 102.0 |
Этанол 99.8% | 215.0 | |
Связующее | Поливинилбутираль | 66.7 |
Пластификатор | Бутилбензилфталат | 50.1 |
Диспергатор | Рыбий жир Menhaden Fishoil Defloc Z3 | 7.4 |
Для приготовления шликеров использовали валковую мельницу “KEKO BL-3”. Литье керамической пленки производили на установке “KEKO CAM-M3520H”. Резка на листы 8 × 8' произведена на установке “KEKO SC-25MNC”. Для проверки качества совместного спекания LTCC керамики на листы наносили серебросодержащую пасту “Ferro CN33-498”, которая предназначена для LTCC-керамики “Ferro A6M”. Рисунок наносили вручную с помощью сетки-трафарета. После каждого этапа нанесения металлизации листы керамики сушили обдувом воздуха при температуре 90°С на установке “KEKO SD-3”, затем формировали стеки, т.е. производили операцию совмещения листов керамики между собой. Для того чтобы точно совместить все слои между собой, на каждом листе еще на этапе формирования отверстий были сформированы специальные реперные метки. Далее произвели ламинирование стека. На данном этапе важно было сохранить топологию стека неизменной, потому что велик риск искажения отверстий и полостей во время изостатического прессования. Чтобы избежать этого, на стек сверху положили специальную силиконовую прокладку. Прессование осуществляли в изостатическом прессе “KEKO ILS-66” при следующих условиях: температура жидкости 60°С, время нагрева стека 5 мин, прессование осуществлялось в течение 15 минут при давлении в 20 МПа. Затем стек разрезали на заготовки с помощью установки резки “сырой” керамики “KEKO CM-15” (подробнее см. в работе [11]).
Спекание LTCC-керамики произведено без пригруза в печи “Nabertherm HT276” за один этап в две стадии по режиму, рекомендованному фирмой “Ferro” для LTCC-керамики марки “A6M” (рис. 2).
Первая стадия – нагрев до 450°С и выдержка в течение двух часов, что необходимо для эффективного процесса удаления всех органических компонентов, которые придавали “сырым” листам керамики форму и эластичность. На второй стадии происходит собственно спекание керамики: нагрев до 850°С с выдержкой 10 мин.
4. ОБСУЖДЕНИЕ РЕЗУЛЬТАТОВ
Полученные “сырые” листы LTCC-керамики (рис. 3а) обладают механическими свойствами, аналогичными керамическому материалу “Ferro A6M” (рис. 3б). Процесс формирования стека и ламинирование производится без видимых деформаций отверстий и полостей деталей.
Рис. 3.
“Сырые” листы LTCC-керамики, полученные в данной работе по рецепту 1 (а), и листы марки “Ferro A6M” (б).
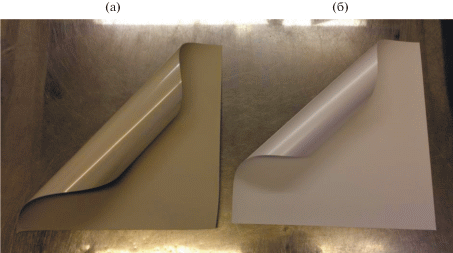
Для того чтобы сравнить свойства полученных керамических материалов с LTCC керамикой “Ferro A6M”, произведен термографический анализ с использованием прибора синхронного термического анализа “NETZSCH STA 449 F3 Jupiter” и получены диаграммы “сырых” листов керамики (рис. 4, 5). На графиках представлены кривые изменения массы от температуры (термогравиметрия (ТГ)) и выделение энергии от температуры (дифференциальная сканирующая калориметрия (ДСК)). Результаты анализа керамики “Ferro A6M” представлены на рис. 4, а образцов, полученных по рецепту 1 и рецепту 2, – на рис. 5а и 5б соответственно.
Рис. 5.
Дифференциальный термический анализ образцов LTCC-керамики, полученных по рецепту 1 (а) и по рецепту 2 (б).
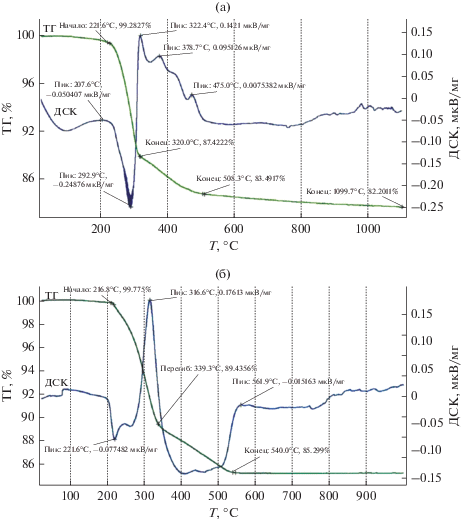
Как видно из рисунков, графики изменения массы от температуры нагрева на образце “Ferro A6M” и образце, полученному по рецепту 2, идентичны и практически не отличаются, за исключением участка температур 340…500°С. Это является основанием полагать, что состав органических компонентов у всех образцов LTCC-керамики идентичен и небольшие различия связаны с разным составом стекла. Наличие в образце рецепта 1 большого содержания оксида натрия в составе стекла С95-2 способствует снижению температуры плавления, что и является причиной отличий на графиках. Внешний вид деталей образцов рецептов 1 и 2 до и после спекания представлен на рис. 6.
Рис. 6.
Образцы деталей из LTCC-керамики по рецепту 1 (а, б) и 2 (в, г) до спекания (a, в) и после спекания (б, г).
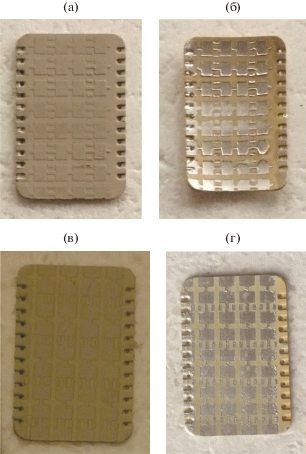
Как видим, на образцах рецепта 2 отсутствуют расслоения и деформации при совместном спекании деталей, состоящих из пяти слоев керамики, на каждый из которых был нанесен слой металлизации с идентичной конфигурацией. Применение стекла с более низким показателем ТКЛР в составе LTCC-керамики позволило добиться лучшей совместимости с металлизационной пастой “Ferro CN33-498”. Сравнительные результаты измерений физических и диэлектрических характеристик представлены в табл. 4.
Таблица 4.
Результаты измерений физических и диэлектрических характеристик разработанных материалов в сравнении с LTCC-керамикой “Ferro A6M”
Характеристики | “Ferro A6M” | Рецепт 1 | Рецепт 2 |
---|---|---|---|
Кажущаяся плотность, г/см3 | 2.47 | 2.31 | 2.37 |
Предел прочности при статическом изгибе, МПа | 183 | 150 | 167 |
КТЛР, 10-6/ºС | 6.8 | 8.1 | 6.1 |
λ, Вт/м К | 2.20 | 1.79 | 1.86 |
ε | 6.1 | 5.7 | 6.7 |
tgδ (при 1 МГц) | 2.2 × 10–4 | 64 × 10–4 | 8.2 × 10–4 |
ρ, Ом см | 8.1 × 1012 | 5.1 × 1012 | 7.2 × 1012 |
Усадка в плоскости XY , % | 14.4 | 8.5 | 12.5 |
Большой коэффициент температурного линейного расширения образцов “Рецепт 1” связан с применением стекла С95-2, у которого данный показатель равен 9.5 × 10–6/°С. Предел прочности при статическом изгибе, теплопроводность, диэлектрическая проницаемость, удельное электрическое сопротивление полученных образцов отличаются от показателей LTCC-керамики “Ferro A6M” в среднем не более чем на 16%. Существенно отличаются значения геометрической усадки образцов. Образцы рецептов 1 и 2 имеют значительно меньшую геометрическую усадку по сравнению с зарубежной керамикой, что связано с особенностями процесса приготовления шликера и обжига.
* * *
Таким образом, найдено, что улучшение показателей диэлектрической проницаемости и тангенса угла диэлектрических потерь оказывают влияние элементы BaO, PbO. Данные оксиды, также содержатся в LTCC-керамик “Ferro L8” и “DuPont 951” [13]. В ходе экспериментов, проведенных в рамках данной работы определено, что наиболее оптимальным по составу и свойствам является марка стекла С48-3. Оно обладает низким показателем ТКЛР: 4.8 × 10–6/°С и содержит в своем составе 9% BaO и 18.5% Al2O3, которые способствуют улучшению диэлектрических характеристик LTCC-керамики. Образцы с применением данного стекла обладают характеристиками, сопоставимыми и даже по некоторым параметрам превосходящие американскую LTCC-керамику “Ferro А6M”.
Применение в составе LTCC-керамики стекла марки С95-2 позволило экспериментально убедиться, что большой показатель ТКЛР негативно сказывается на качестве конечного продукта и способствует деформациям и расслоениям во время обжига. Большое содержание в составе стекла Na2O способствует увеличению тангенса угла диэлектрических потерь на образцах LTCC-керамики.
Список литературы
Максимов А. // Электроника НТБ. 2011. № 3. С. 56.
Кондратюк Р. // Наноиндустрия. 2011. № 2. С. 26.
Чигиринский С. // Технологии. 2009. № 11. С. 130.
Симин А.В., Холодняк Д.В., Вендик И.Б. // Компоненты и технологии. 2005. № 5. С. 190.
Черных В., Чигиринский С. // Технологии. 2012. № 4. С. 176.
Mistler R.E., Twiname R.E. // Tape casting theory and practice. Westerville: American ceramic society, 2000.
Zhou J. // J. Advanced Ceramics. 2012. № 1. P. 89.
Imanaka Y. Multilayered Low Temperature Co-fired Ceramics (LTCC) Technology. Kawasaki: Fujitsu Laboratories, Ltd, 2005.
King A.G. Ceramic technology and processing. N.-Y.: William Andrew Publ., 2002.
Непочатов Ю., Кумачева С., Швецова Ю., Дитц А. // Совр. электроника. 2014. № 4. С. 12.
Вайман Д.А., Красный И.Б., Данилов В.С., Кумачева С.А. // Доклады АН ВШ РФ. 2017. № 1. С. 31. https://doi.org/10.17212/1727-2769-2017-1-31-45
Жигальский А.А. Технология материалов электронной техники: учебное пособие. Томск: ТУСУР, 2006.
Пашков Д.А., Тютюнькова Д.О., Погребенков В.М. // XII Междунар. конф. студентов и молодых ученых: “Перспективы развития фундаментальных наук”. Томск, 2015. С. 484.
Федотов А.К., Анищик В.М., Тиванов М.С. Физическое материаловедение: учебное пособие. Ч. 3. Материалы энергетики и энергосбережения. Минск: Высшая школа, 2015.
Справочник химика. Т. 5. Сырье и продукты промышленности неорганических веществ, процессы и аппараты, коррозия, гальванотехника, химические источники тока / Под ред. Никольского Б.П. М.: Химия, 1968.
Машиностроение: энциклопедический справочник. Т. 4. Материалы машиностроения / Под ред. Чудакова Е.А., Одинга И.А. М.: Машгиз, 1947.
Нанотехнологии в электронике / Под ред. Чаплыгина Ю.А. М.: Техносфера, 2013. Вып. 2.
Евстропьев К.С., Торопов Н.А. Химия кремния и физическая химия силикатов. М.: Промстройиздат, 1950.
Куколев Г.В. Химия кремния и физическая химия силикатов. М.: Высш. школа, 1966.
Стекло электровакуумное. Марки: ОСТ 11 027.010-75. Взамен НПО.027.600, 1975.
Вайман Д.А., Данилов В.С. // Доклады АН ВШ РФ. 2018. № 1. С. 69.
Дополнительные материалы отсутствуют.
Инструменты
Радиотехника и электроника