Расплавы, 2021, № 3, стр. 315-322
Модифицирующая способность лигатуры Al–Zr
А. А. Филатов a, b, *, А. В. Суздальцев a, b, Ю. П. Зайков a, b
a Уральский федеральный университет
Екатеринбург, Россия
b Институт высокотемпературной электрохимии УрО РАН
Екатеринбург, Россия
* E-mail: fill.romantic@yandex.ru
Поступила в редакцию 17.01.2021
После доработки 25.01.2021
Принята к публикации 02.02.2021
Аннотация
В настоящей работе исследована возможность применения электролитически полученной лигатуры для измельчения зерна и улучшения свойств сплавов алюминия. Испытания проводили на примере промышленного сплава Al–Si–Fe, в который добавляли разное количество лигатуры Al–Zr с содержанием 10 мас. % циркония при температуре 900°С. Изучено влияние содержания циркония в алюминиевом сплаве и скорости охлаждения на его структуру и свойства. На основании результатов структурного анализа установлено, что добавка циркония в количестве 0.1 мас. % уменьшает средний размер зерна сплава в 4–5 раз, без изменения формы и структуры. Измерение твердости полученных сплавов показывает, что при добавлении циркония в высокочистый алюминий, твердость увеличивается в 1.5 раза при содержании циркония 0.4 мас. % и увеличивается с ростом содержания циркония. В то же время, добавление циркония в сплав АК6 не влияет на твердость по Бринеллю, что предположительно связано с более выраженным действием других легирующих элементов. Отсутствие интерметаллидных соединений в полученных образцах сплава, модифицированного лигатурой Al–Zr, содержащей интерметаллидные включения размером до 50 мкм, указывает на то, что исходную лигатуру Al–Zr можно разливать в слитки и охлаждать при любых условиях, исключая при этом операцию переплавки в миксере и прочие виды обработки.
ВВЕДЕНИЕ
В настоящее время существенно возрастает спрос на алюминиевые лигатуры, как наиболее подходящее сырье для производства многокомпонентных сплавов и композитов на основе алюминия [1, 2]. Наиболее востребованными в аэрокосмической отрасли и электротехнике являются алюминиевые сплавы с добавками циркония, поскольку его содержание в алюминии в пределах 0.2 мас. % существенно измельчает зерно [3], повышает прочность и термоустойчивость свойств при нагреве до 300°С [4]. Существующие технологии получения алюмо-циркониевых лигатур (лигатур Al–Zr) основаны на механическом смешении алюминия с цирконием или алюминотермическом восстановлении его соединений [5–7]. Производство лигатур обоими способами осложнено многостадийностью, высокой температурой процесса и расходом чистых исходных компонентов, а также отсутствием возможности контроля структуры и свойств целевого продукта.
Наиболее перспективным способом получения лигатур Al–Zr представляется совместное электролитическое разложение оксидов алюминия и циркония, растворенных в криолит-глиноземном расплаве. Данный способ позволяет организовать непрерывное производство лигатур в одну стадию, с использованием более дешевого исходного сырья, на базе действующих крупнотоннажных электролизеров, без существенных технологических изменений и соответствующих экономических издержек. Однако, несмотря на все попытки опытно-промышленных реализаций, способ не был внедрен в связи с высокой агрессивностью расплава при относительно высокой рабочей температуре – 960–1000°С. Устранить данный недостаток можно путем использования фторидного расплава с пониженной температурой плавления при сохранении высокой растворимости используемых оксидов [8]. Таким образом, для повышения технико-экономических показателей производства важными являются данные о растворимости и кинетике электровосстановления используемых оксидов, а также о влиянии параметров синтеза на структуру и свойства производимых сплавов.
Ранее нами был разработан метод получения лигатуры Al–Zr с содержанием циркония до 15 мас. % при извлечении циркония из оксида вплоть до 100% [4]. Интерес представляет дальнейшее практическое применение получаемых данным способом лигатур.
В данной работе по ранее отработанной методике была синтезирована партия лигаутры Al–Zr с содержанием циркония до 15 мас. %, и изучена модифицирующая способность лигатуры на примере алюминиевого сплава.
ЭКСПЕРИМЕНТ
Приготовление расплавов
Для получения лигатур использовали расплав KF–NaF–AlF3; исходные компоненты расплавов (соли KF⋅HF, NaF, AlF3 и NH4F квалификации х. ч., производство ОАО “Вектон”) были максимально очищены от примесных элементов и влаги по ранее описанной методике [9]. Чистый KF получали путем термического разложения KF·HF нагреванием соли в течение 12 ч до температуры 900°С, что позволило попутно удалить оксидные примеси взаимодействием с образующимся HF. Удаление оксидных примесей из AlF3 производили путем его выдержки в смеси с избыточным количеством NH4F в течение 6–8 ч при 450–500°C. Смесь NaF–AlF3 и KF–AlF3 получали простым сплавлением компонентов в присутствии NH4F для более полной очистки. Для этого получали эквимольные смеси KF–AlF3 и NaF–AlF3, которые затем корректировали до расплава с заданным мольным соотношением CR = ([NaF] + [KF])/[AlF3] добавками KF и NaF.
Для удаления электроположительных (по отношению к алюминию) примесей расплавы подвергали потенциостатическому электролизу в течение 2-х часов при потенциале графитового катода 0.2 В относительно потенциала алюминиевого электрода [10].
Синтез лигатур
Исходную лигатуру Al–Zr получали электролизом расплава KF–NaF–AlF3 с периодической подгрузкой ZrO2 при температуре 800°С в электролизерах на силу тока от 10 до 100 А [11]. Подгрузку ZrO2 осуществляли в соответствии с растворимостью оксида в исследуемом расплаве [12]. Синтез лигатуры проводили в графитовом контейнере на воздухе при постоянном перемешивании алюминия со скоростью 100 об./мин [13]. Перемешивание алюминия осуществляли при помощи графитовой мешалки, которая дополнительно являлась токоподводом к алюминиевому катоду, расположенному на дне контейнера. Анодом служил графитовый цилиндр. Катодную плотность тока в процессе электролиза поддерживали равной 0.5 А/см2 на основании результатов поляризационных измерений в используемом расплаве [14, 15]. Электролиз периодически приостанавливали для извлечения лигатуры Al–Zr из электролизера. Часть (примерно половину) лигатуры извлекали металлическим тиглем и сливали в стальную изложницу. Параллельно в электролит загружали аналогичную массу чистого алюминия и продолжали электролиз.
Модификация сплава AK6
Модификацию сплава лигатурой осуществляли в высокотемпературной камерной электропечи ПВК-1.4 25 по известным методикам [16, 17]. Слиток сплава АК6 загружали в печь в графитовом тигле. Печь нагревали до 900°С, после чего убирали шлак с поверхности сплава, и добавляли расчетное количество лигатуры Al–Zr. Тигель со сплавом выдерживали в печи 10 минут при температуре 900°С, после чего сплав перемешивали графитовой мешалкой, извлекали тигель из печи, и выливали сплав в графитовую изложницу.
Анализ результатов
Для определения структуры полученных лигатур и сплавов изготавливали шлифы при помощи режущего и шлифовального оборудования (Struers, Дания). Для изучения микроструктуры и оценки размера зерна, полученные образцы были протравлены в 10% водном растворе плавиковой кислоты, с продолжительностью травления от 10 с до 1 мин, при необходимости проводили осветление поверхности шлифа в концентрированной азотной кислоте. Структурные исследования проводили на сканирующем электронном микроскопе Quanta-200 с приставкой EDAX и оптическом микроскопе Neophot-21. Объемную долю фаз и размер структурных составляющих определяли по стандартным методикам количественного анализа с помощью компьютерных программ в металловедческом комплексе Siams-700. Макроструктуру изучали на бинокулярном микроскопе Микромед MC2 Zoom 2CR. Твердость образцов определяли по Бринеллю в соответствии с ГОСТ 9012-59 на твердомере ТШ-2м при нагрузке 2500 H с диаметром шарика 5 мм. Элементный и фазовый состав полученных лигатур и сплавов определяли атомно-эмиссионным методом с индуктивно-связанной плазмой, а также рентгенофазовым анализом с использованием спектрометра iCAP 6300 Duo (Thermo scientific, США) и дифрактометра Rigaku D/MAX-2200VL/PC (Rigaku, Япония).
РЕЗУЛЬТАТЫ И ОБСУЖДЕНИЕ
Всего в процессе электролизных испытаний было получено более 50 образцов высоколегированных сплавов с содержанием циркония до 15 мас. %, а также проведена серия экспериментов на укрупненном полупромышленном электролизере при варьировании параметров синтеза. Чтобы исключить влияние прочих примесных элементов, для данного эксперимента была изготовлена лигатура Al–Zr с использованием высокочистого алюминия марки АВЧ в качестве основы. Согласно результатам химического анализа, полученная лигатура содержит 10 мас % Zr. Типичная микрофотография полученной лигатуры с содержанием циркония 10 мас. % представлена на рис. 1.
Основная часть циркония в полученных лигатурах представлена фазами интерметаллидных соединений переменного состава, что согласуется с диаграммой плавкости [18]. В связи с наличием фаз интерметаллидных соединений, размер которых достигает 50 мкм, и неоднородным распределением циркония в объеме сплава, возникает вопрос о модифицирующей способности полученных лигатур для модификации промышленных сплавов на основе алюминия.
Рис. 2.
Сравнение макроструктуры сплава АК6 без добавки циркония и с содержанием циркония 0.1 мас. %.
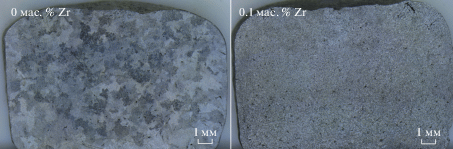
Для более детального изучения модифицирующей способности лигатуры, а также поведения интерметаллидных соединений в процессе модификации, была проведена серия экспериментов по модифицированию алюминиевого сплава АК6. Химический состав исходного сплава АК6 представлен в табл. 1.
Таблица 1.
Состав исследуемого сплава АК6
Fe | Si | Mn | Ni | Ti | Al | Cu | Mg | Zn | Остальное |
---|---|---|---|---|---|---|---|---|---|
0.7 | 0.7–1.2 | 0.4–0.8 | 0.1 | 0.1 | 93.3–96.7 | 1.8–2.6 | 0.4–0.8 | 0.3 | Всего 0.1 |
При изучении макроструктуры полученных сплавов было установлено, что добавка циркония уже в количестве 0.1 мас. % существенно измельчает зерно (рис. 2), что согласуется с известными представлениями о влиянии циркония на макроструктуру алюминиевых сплавов [16–20]. Более детальный расчет среднего размера зерна при помощи программы Siams-700 показывает среднее уменьшение размера зерна в 4–5 раз, дальнейшее увеличение содержания циркония уже не оказывает влияния на средний размер зерен.
При изучении микроструктуры и расчете среднего размера зерна в программе Siams-700 было установлено, что добавка циркония снижает средний размер зерен, но не влияет на микроструктуру сплава (рис. 3). Отмечено также отсутствие фаз интерметаллидных соединений в полученном сплаве. Дополнительно было установлено, что добавка циркония в чистый алюминий повышает его твердость по Бринелю на 15–20 ед., но не влияет на твердость при наличии других легирующих элементов.
Отсутствие фаз интерметаллидных соединений циркония в модифицированных образцах сплава АК6, полученных при разной скорости кристаллизации, указывает на то, что электролитически получаемая лигатура Al–Zr не требует дополнительной термической или ультразвуковой обработки с целью уменьшения размеров фаз интерметаллидных соединений.
ВЫВОДЫ
В данной работе была изучена модифицирующая способность лигатуры Al–Zr с содержанием 10 мас. % циркония, полученной электролизом расплава KF–NaF–AlF3 на электролизере с токовой нагрузкой до 100 А. Проверку модифицирующей способности лигатуры выполняли на примере легирования и модифицирования сплава АК6 добавками циркония 0.1, 0.3, и 0.5 мас. %.
На основании результатов микроструктурного анализа установлено, что добавка циркония в количестве 0.1 мас. % уменьшает средний размер зерна сплава в 4–5 раз. Измерение твердости полученных сплавов показывает, что при добавлении циркония в высокочистый алюминий, твердость увеличивается в 1.5 раза при содержании циркония 0.4 мас. % и увеличивается с ростом содержания циркония. В то же время, добавление циркония в сплав АК6 не влияет на твердость по Бринеллю, что предположительно связано с более выраженным действием других легирующих элементов.
Исследование выполнено при финансовой поддержке РФФИ в рамках научного проекта № 19-33-90 144.
Список литературы
Inoue A. Amorphous, nanoquasicrystalline and nanocrystalline alloys in Al-based systems // Progress in Materials Science. 1998. 43. P. 365–520.
Меньшикова С.Г., Ширинкина И.Г., Бродова И.Г., Бражкин В.В. Структура сплава Al90Y10 при кристаллизации под давлением // Расплавы. 2019. № 1. С. 18–23.
Напалков В.И., Махов С.В. Легирование и модифицирование алюминия и магния. МИСиС: М. 2002. 375 с.
Suzdaltsev A.V., Pershin P.S., Filatov A.A., Nikolaev A.Yu., Zaikov Yu.P. Review—Synthesis of aluminum master alloys in oxide-fluoride melts: A Review // J. Electrochemical Society. 2020. 167. № 10. P. 102503.
Баранов В.Н., Лопатина Е.С., Дроздова Т.Н., Сидельников С.Б., Гильманшина Т.Р., Трифоненков Л.П. Исследование влияния параметров литья на структуру сплава системы Al‒Zr // Литейное производство. 2011. № 11. С. 16–18.
Першин П.С., Филатов А.А., Суздальцев А.В., Зайков Ю.П. Алюмотермическое получение сплавов Al–Zr в расплаве KF–AlF3 // Расплавы. 2016. № 5. С. 413–421.
Красиков С.А., Агафонов С.Н., Ченцов В.П., Жилина Е.М. Влияние фазообразования на характер межфазных взаимодействий при алюмотермическом восстановлении циркония из его диоксида // Расплавы. 2015. № 2. С. 60–64.
Дедюхин А.Е., Аписаров А.П., Ткачева О.Ю., Редькин A.A., Зайков Ю.П., Фролов А.В., Гусев А.О. Растворимость Al2O3 в расплавленной системе KF–NaF–AlF3 // Расплавы. 2009. № 2. С. 23–28.
Nikolaev A.Yu., Suzdaltsev A.V., Polyakov P.V., Zaikov Yu.P. Cathode process at the electrolysis of KF–AlF3–Al2O3 melts and suspensions // J. Electrochemical Society. 2017. 164. № 8. H5315–H5321.
Суздальцев А.В., Храмов А.П., Зайков Ю.П. Углеродный электрод для электрохимических исследований в криолит-глиноземных расплавах при 700–960°С // Электрохимия. 2012. 48. С. 1251–1263.
Filatov A.A., Pershin P.S., Suzdaltsev A.V., Nikolaev A.Yu., Zaikov Yu.P. Synthesis of Al–Zr master alloys via the electrolysis of KF–NaF–AlF3–ZrO2 melts // J. Electrochemical Society. 2018. 165. № 2. E28–E34.
Pershin P.S., Kataev A.A., Filatov A.A., Suzdaltsev A.V., Zaikov Yu.P., Synthesis of Al-Zr alloys via ZrO2 aluminum-thermal reduction in KF–AlF3-based melts // Met. and Mat. Trans. B. 2017. 48. P. 1962–1969.
Суздальцев А.В., Филатов А.А., Николаев А.Ю., Панкратов А.А., Молчанова Н.Г., Зайков Ю.П. Извлечение скандия и циркония из их оксидов при электролизе оксидно-фторидных расплавов // Расплавы. 2018. № 1. С. 5–13.
Филатов А.А., Першин П.С., Николаев А.Ю., Суздальцев А.В. Получение сплавов и лигатур Al–Zr при электролизе расплавов KF–NaF–AlF3–ZrO2 // Цветные металлы. 2017. № 11. С. 27–31.
Nikolaev A.Yu., Suzdaltsev A.V., Zaikov Yu.P. Cathode process in the KF–AlF3–Al2O3 melts // J. Electrochemical Society. 2019. 166. № 15. D784–D791.
Brodova I.G., Stolyarov V.V., Manukhin A.B., Yablonskikh T.I., Bashlykov D.V., Soshnikova E.P., Zolotova N.A. Formation of ultrafine structure in a rapidly solidified Al–Zr alloy under the effect of severe plastic deformation // Physics of Metals and Metallography. 2001. 91. P. 494–499.
Ткачева О.Ю., Бродова И.Г., Архипов П.А., Зайков Ю.П. Влияние условий кристаллизации на структуру и модифицирующую способность Al–Sc-сплавов // Известия вузов. Цветная металлургия. 2016. № 6. С. 55–64.
Лякишев Н.П. Диаграммы состояния двойных металлических систем: Справочник в 3 т. М.: Машиностроение, 1996.
Birbilis N., Buchheit R.G. Electrochemical characteristics of intermetallic phases in aluminum alloys—an experimental survey and discussion // J. Electrochemical Society. 2005. 152. № 4. B140–B151.
Brodova I.G., Bashlykov D.V., Manukhin A.B., Stolyarov V.V., Soshnikova E.P. Formation of nanostructure in rapidly solidified Al–Zr alloy by severe plastic deformation // Scripta Materialia. 2001. 44. P. 1761–1764.
Дополнительные материалы отсутствуют.