Расплавы, 2021, № 3, стр. 243-252
Термодинамическая оценка фазовых превращений в системе Fe–Ni–Cr–Cu–Si–C
Ф. Р. Капсаламова a, *, С. А. Красиков b, **
a Национальный центр по комплексной переработке минерального сырья
Республики Казахстан
Алматы, Казахстан
b Институт металлургии Уральского отделения РАН
Екатеринбург, Россия
* E-mail: faridakapsalamova@gmail.com
** E-mail: sankr@mail.ru
Поступила в редакцию 11.12.2020
После доработки 06.01.2021
Принята к публикации 09.01.2021
Аннотация
Выполнен термодинамический анализ фазовых превращений в многокомпонентной системе Fe–Ni–Cr–Cu–Si–C, что представляет интерес для перспективной металлотермической технологии получения износостойкого сплава. Для оценки фазового состава и структуры сплава использован компьютерный расчет характерных политермических разрезов фазовой диаграммы системы с помощью программного комплекса Thermo-Calc (версия TCW5), основанный на численном моделировании равновесия фаз методом CALPHAD с использованием базы данных TTFe – Thermotech Fe-based Alloys Database, которая содержит сведения о химических элементах, и предназначена для расчета стабильных и метастабильных фаз в многокомпонентных сплавах. Фазовые превращения рассматривались при температурах от 300 до 1400°С и переменных содержаниях легирующих элементов Ni, Cr, Cu, Si, C с шагом 100°C. Рассчитаны политермические разрезы фазовой диаграммы системы Fe–Ni–Cr–Cu–Si–C и определены критические температуры фазовых превращений в сплаве и химические составы образующихся в них фаз (α, β, β2, γ, γ2, L). Результаты термодинамического моделирования показали, что по мере легирования сплава на основе железа усложняется его микроструктура и изменяется фазовый состав, что имеет место при газопламенной наплавке. Для изучения процесса затвердевания с целью получения количественной информации об этапах кристаллизации сплава, разделяющих их критических температурах, составе и количестве выделяющихся фаз выявлено влияние температуры. Характер температурной зависимости кристаллизации расплава показал переход при 950°С неравновесной кристаллизации расплава в стадию равновесной, что предполагает мелкозернистую структуру покрытия. Термодинамический анализ позволил прогнозировать феррито-мартенситную с включениями ледебурита структуру покрытия при металлотермической технологии получения износостойкого сплава. Построенные политермические разрезы показали, что полное растворение всех компонентов в жидкой фазе происходит при температуре ~1400°С.
ВВЕДЕНИЕ
Одним из условий успешного развития промышленности является создание новых материалов, обладающих уникальным комплексом свойств. Благодаря особенностям фазового и структурного состояния износостойкие сплавы, получаемые из самофлюсующихся наплавочных материалов, характеризуются высокой жаропрочностью, жаростойкостью, коррозионной стойкостью, многие имеют высокую твердость и износостойкость, что связано с наличием в структуре твердых упрочняющих фаз в виде карбидов, боридов, силицидов и т.д. [1–3]. К весьма перспективному самофлюсующемуся наплавочному материалу следует отнести сплав на основе железа, состав которого включает значительное количество никеля, хрома, меди, кремния, бора, углерода [4]. Введение данных элементов способствует хорошему раскислению основы сплава и контактирующей с ним поверхности изделия, что гарантирует формирование плотного однородного слоя с высокой адгезией. Материал отличается относительно невысокой температурой плавления, значение которой для железных сплавов в большинстве случаев не превышает 1100°С, что обусловлено образованием относительно легкоплавких эвтектических соединений [5].
Известный опыт получения наплавочных материалов, упрочняющих и восстанавливающих изношенные детали техники показал перспективность метода механохимического легирования (МХЛ), имеющего существенные технико-экономические преимущества, а также возможность регулирования состава, что позволяет повысить физико-механические свойства защитных покрытий [6, 7]. При этом в локальных микрообъемах твердого тела возникают внутренние напряжения, основными характеристиками релаксации которых являются выделение тепла, образование промежуточных жидких фаз с формированием новой поверхности, сопровождающееся возбуждением и ускорением химической реакции [8].
Возможность управления фазовым состоянием и структурой сплавов при металлотермических технологиях с использованием базы фазовых диаграмм металлических систем способствует развитию научных основ создания высококачественных металлических материалов [9]. В настоящее время для расчетного определения фазового состава большое распространение получил, так называемый, СALPHAD-метод. Он основан на том, что диаграмма состояния является отображением термодинамических свойств системы. Таким образом, если известны термодинамические свойства, то можно рассчитать диаграммы состояния многокомпонентных систем [10, 11]. К сожалению, сведения по диаграммам состояния многокомпонентных систем в литературе весьма ограничены.
Целью настоящей работы являлось термодинамическое моделирование фазовых превращений, протекающих при механическом легировании системы Fe–Ni–Cr–Cu–Si–C.
ЭКСПЕРИМЕНТАЛЬНАЯ ЧАСТЬ
Для анализа фазовых превращений проводили термодинамическое моделирование равновесного состояния системы (мас. %) 40Fe–31Ni–18Cr–5Cu–5Si–1C с применением программного комплекса Thermo-Calc, основанного на численном моделировании равновесия фаз CALPHAD-методом (база данных TTFe) при температурах от 300 до 1400°С и переменных содержаниях легирующих элементов c шагом 100°C.
РЕЗУЛЬТАТЫ И ИХ ОБСУЖДЕНИЕ
На рис. 1–5 представлены фрагменты политермических разрезов диаграммы состояния системы Fe–Ni–Cr–Cu–Si–C при температурах от 300 до 1400°С.
Рис. 1.
Политермический разрез диаграммы состояния системы Fe–Ni–Cr–Cu–Si–C при переменном содержании Ni.
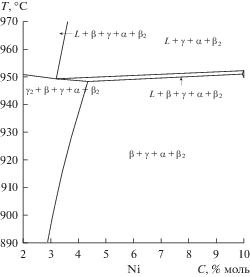
Рис. 2.
Политермический разрез диаграммы состояния системы Fe–Ni–Cr–Cu–Si–C при переменном содержании Cr.
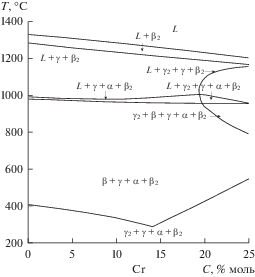
Рис. 3.
Политермический разрез диаграммы состояния системы Fe–Ni–Cr–Cu–Si–C при переменном содержании Cu.
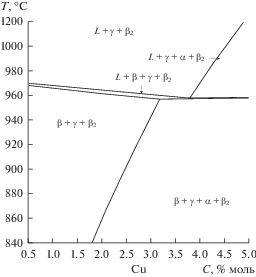
Рис. 4.
Политермический разрез диаграммы состояния системы Fe–Ni–Cr–Cu–Si–C при переменном содержании Si.
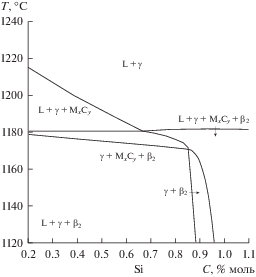
Рис. 5.
Политермический разрез диаграммы состояния системы Fe–Ni–Cr–Cu–Si–C при переменном содержании C.
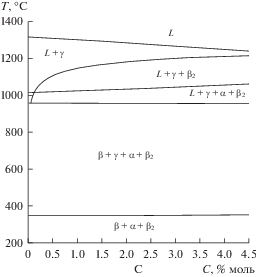
Из политермического разреза диаграммы состояния при переменном содержании Ni (рис. 1), вытекает, что начало плавления порошковой композиции начинается при температуре ~950°С и находится в пятифазной области (L + β + γ + α + β2). Данные по изменению относительных количеств и химических составов фаз в исследуемом сплаве в зависимости от температуры приведены в табл. 1. По результатам термодинамических расчетов Ni находится в α- и γ-фазах, которая существует до температуры примерно 970°С с последующим переходом в жидкую фазу.
Таблица 1.
Количественные параметры фазового состава сплава системы Fe–Ni–Cr–Cu–Si–C при температурах 300–1400°С
T, °C | Фаза | Qм, % масc | Содержание элементов, мас. % | |||||
---|---|---|---|---|---|---|---|---|
Fe | Ni | Cr | Cu | C | Si | |||
1400 | Liquid | 100 | 43.32 | 32.82 | 16.88 | 5.73 | 0.002 | 1.01 |
1300 | Liquid | 54.51 | 41.23 | 30.84 | 19.14 | 6.48 | 0.003 | 1.89 |
γ | 45.49 | 45.73 | 35.11 | 14.27 | 4.85 | 0.0001 | – | |
1200 | Liquid | 27.42 | 39.81 | 27.32 | 21.64 | 6.54 | 0.007 | 3.89 |
γ | 72.57 | 44.56 | 34.75 | 15.21 | 5.44 | 0.0002 | – | |
1000 | Liquid | 4.33 | 35.15 | 24.49 | 18.79 | 8.0 | 0.002 | 13.43 |
α | 7.37 | 35.18 | 24.69 | 21.54 | 18.57 | 0.0000003 | – | |
β2 | 1.95 | – | – | – | – | 29.95 | 70.04 | |
γ | 86.33 | 44.73 | 34.15 | 16.53 | 4.57 | 0.00001 | – | |
900 | β | 1.0 | – | – | – | – | 0.0003 | 99.96 |
α | 19.42 | 36.33 | 25.47 | 22.14 | 16.03 | 0.0000001 | – | |
β2 | 1.99 | – | – | – | – | 29.95 | 70.04 | |
γ | 77.57 | 45.76 | 35.18 | 15.82 | 3.22 | 0.000005 | – | |
800 | β | 1.0 | – | – | – | – | 0.015 | 99.98 |
α | 30.62 | 37.68 | 26.33 | 22.32 | 13.65 | 0.0000001 | – | |
β2 | 1.99 | – | – | – | – | 29.95 | 70.04 | |
γ | 66.37 | 46.72 | 36.42 | 14.67 | 2.16 | 0.00002 | – | |
700 | β | 1.0 | – | – | – | – | 0.00005 | 99.99 |
α | 42.79 | 39.21 | 27.29 | 22.08 | 11.42 | 0.00005 | – | |
β2 | 1.99 | – | – | – | – | 29.95 | 70.05 | |
γ | 54.21 | 47.54 | 37.92 | 13.16 | 1.37 | 0.00007 | – | |
600 | β | 1.0 | – | – | – | – | 0.00002 | 99.99 |
α | 56.35 | 40.85 | 28.44 | 21.29 | 9.4 | 0.00002 | – | |
β2 | 1.99 | – | – | – | – | 29.95 | 70.05 | |
γ | 40.64 | 48.04 | 39.85 | 11.29 | 0.82 | 0.00002 | – | |
500 | β | 1.0 | – | – | – | – | 0.006 | 99.99 |
α | 71.46 | 42.41 | 29.92 | 19.95 | 7.72 | 0.0005 | – | |
β2 | 2.0 | – | – | – | – | 29.95 | 70.05 | |
γ | 25.53 | 47.92 | 42.45 | 9.16 | 0.46 | 0.002 | – | |
400 | β | 1.0 | – | – | – | – | 0.06 | 99.99 |
α | 87.75 | 43.56 | 31.87 | 18.17 | 6.39 | 0.0007 | – | |
β2 | 2.0 | – | – | – | – | 29.95 | 70.05 | |
γ | 9.24 | 46.69 | 46.04 | 7.0 | 0.25 | 0.0009 | – | |
300 | β | 1.0 | – | – | – | – | 0.1 | – |
α | 97.0 | 43.86 | 33.23 | 17.09 | 5.8 | 0.2 | – | |
β2 | 2.0 | – | – | – | – | 29.95 | 70.05 |
Выше температуры 950°С (т.е., выше температуры эвтектоидного превращения) в зависимости от количественного соотношения компонентов имеются четырех- и пятифазные области с участием фаз α, β, β2, γ, γ2, L. Рассматриваемый сплав при температуре ~940–950°С попадает в пятифазную область, однако при увеличении содержания никеля можно увидеть исчезновение γ2-фазы (рис. 1).
Политермический разрез при переменном содержании Cr, представленный на рис. 2, показывает температуру полного растворения всех компонентов в жидкой фазе, которая составляет ~1300°С. При 1000°С существует точка эвтектики, являющаяся шестифазной (L + γ + β + α + γ2 + β2). Также из рис. 2 видно, что примерно до температуры 800°С хром находится в α-фазе с последующим переходом в γ2-фазу при температуре близкой к 1000°С, вследствие высокой температуры плавления, которая составляет 1856.9°С [12].
На рис. 3 показан политермический разрез диаграммы состояния системы Fe–Ni–Cr–Cu–Si–C при переменном содержании Cu. Как известно из литературных данных, медь способствует повышению жидкотекучести расплава при формировании наплавки [13]. Из диаграммы можно заметить, что жидкая фаза появляется ближе к температуре 970°С, и как видно, Cu выделяется в жидкую фазу первым из-за низкой температуры плавления среди легирующих элементов [13]. Фаза β2 образуется при относительно низких температурах и она устойчива почти до температуры 1300°С.
Данные политермического разреза диаграммы состояния при переменном содержании Si (рис. 4) показывают появление фазы MxCy, что указывает на возможность формирования структуры износостойкого покрытия вследствие присутствия карбидообразующих легирующих элементов [14].
Из политермического разреза на рис. 5 можно увидеть, что углерод присутствует в β-фазе в интервале температур примерно от 200 до 980°С. Также в этом интервале температур видим образование карбидов других элементов.
Таким образом, при рассмотрении политермических разрезов удалось изучить фазовый состав разрабатываемого наплавочного материала Fe–Ni–Cr–Cu–Si–Cu и показать, что система достаточно полно расплавляется при температуре >1400°С, что может иметь место при газопламенной наплавке самофлюсующего порошка, полученного механохимическим легированием, в котором происходит локальное выделение тепла. Это способствует ускорению диффузии реагентов и образованию вязко-пластичного состояния с появлением промежуточных жидких продуктов [15, 16].
Предположения о фазовых превращений из политермических разрезов подтвердились в результатах расчета при помощи программного комплекса Thermo-Calc количественной информации по фазовому составу при темепературах от 300 до 1400°С, приведенной в табл. 1.
Кроме массовых количеств фаз (QM) расчеты позволяют определить и их состав. Представленный фазовый массив системы позволяет планировать эксперимент для получения износостойкого покрытия с регламентируемыми свойствами [11].
Для изучения процесса затвердевания сплава с целью получения количественной информации об этапах кристаллизации сплава, разделяющих их критических температурах, составе и количестве выделяющихся фаз была построена кривая формирования твердой фазы с помощью програмного продукта Thermo-Calc, которая представлена на рис. 6. Эта информация позволяет установить температуры ликвидуса и солидуса сплава, выявить характер распределения фаз на разных этапах кристаллизации, рассчитать количество выделеляющейся твердой фазы, что необходимо для изучения тепловых процессов и анализа формирования усадочных дефектов.
Анализ построенной кривой кристаллизации для сплава на базе системы Fe–Ni–Cr–Cu–Si–C показывает, что в температурном интервале 2 образуется двухвазная область (L + β2) с избытком жидкой фазы. При кристаллизации из жидкой фазы в интервале температур для областей 3–6, предполагается, что образуются кристаллы феррита с последующим протеканием перитектической реакции. Т.е., кристаллы феррита взаимодействуют с жидкой фазой, и формируются кристаллы аустенита, которые существуют до температуры 738°С и при дальнейшем охлаждении с переходом в феррито-мартенситную структуру.
Также из рис. 6 видно, что до темепературы примерно 950°С осуществляется неравновесная кристаллизация расплава, а после кристаллизация переходит в стадию равновесной – область 8, что предполагает мелкозернистую структуру покрытия.
Таким образом, термодинамическое моделирование фазовых превращений системы Fe–Ni–Cr–Cu–Si–C позволяет прогнозировать, что структура получаемого покрытия при использовании метода газопламенной наплавки, может быть феррито-мартенситной с частичными включениями ледебурита.
Следует отметить, что при термодинамическом моделировании не учитываются кинетические факторы, учитывающие взаимодействие межфазных границ, конечные скорости реакций и диффузионный транспорт реагирующих атомов, а также теплоперенос между частицами реагентов и теплопотери в окружающую среду. В связи с этим, результаты термодинамического моделирования нужно рассматривать лишь как некоторое приближение к реальному состоянию многокомпонентной системы при реакционном механическом легировании.
ЗАКЛЮЧЕНИЕ
С использованием программного продукта Thermo-Calc рассчитаны фазовые диаграммы системы Fe–Ni–Cr–Cu–Si–C в интервале температур 300–1400°С, выявлены возможные фазовые превращения при механохимическом легировании в данной композиции. Представленный фазовый комплекс системы позволяет планирование эксперимента для получения износостойкого покрытия с регламентируемыми свойствами в зависимости от цели исследования. Выявленные стабильные и метастабильные композиции могут являться объектом исследования для получения перспективного наплавочного материала с заданными свойствами на основе многокомпонентной системы, что является основой современного материаловедения.
Работа выполнена в рамках Государственного задания ИМЕТ УрО РАН.
Список литературы
Xu L., Ma S., Fu H. // Front. Mater. 2020. 7. P. 1–2. https://doi.org/10.3389/fmats.2020.00059
Marques F.P., Bozzi A.C., Scandian C., Tschiptschin A.P. Microabrasion of three experimental cobalt-chromium alloys: Wear rates and wear mechanisms // Wear. 2017. 390–391. P. 176–183.
Криворогова А.С., Ильиных Н.И., Ильиных С.А., Гельчинский Б.Р. // Расплавы. 2020. № 1. С. 87–97. https://doi.org/10.31857/S0235010620010053
Al-Joubori A.A., Suryanarayana C. Synthesis of austenitic stainless steel powder alloys by mechanical alloying // J. Materials Science. 2017. 52. P. 11919–11932.
Easo P. George, Dierk Raabe, Robert O. Ritchie. High-entropy alloys // Nature Reviews Materials. 2019. 4. P. 515–534.
Болдырев В.В. Фундаментальные основы механической активации, механосинтеза и механохимических технологий. Новосибирск: Издательство СО РАН, 2009.
Jogindra N.S., Sasikumar C. // J. Mater. Process. Tech. 2019. 263. P. 285–295. https://doi.org/10.1016/j.jmatprotec.2018.08.027
Suryanarayana C. // Research. 2019. https://doi.org/10.34133/2019/4219812
Gorsse S., Senkov O.N. // Entropy. 2018. 20. № 12. P. 899. https://doi.org/10.3390/e20120899
Shah M.S., Ullah N., Ullah B., Shehzad Khan M., Usman T. Thermodynamic analysis and calculations of Fe–Co alloy by modeling and simulation using thermo-calc software // J. Heterocyclics. 2018. 1. P. 35–38.
Mao H., Chen H.-L., Chen Q. TCHEA1: A Thermodynamic Database Not Limited for “High Entropy” Alloys // Journal of Phase Equilibria and Diffusion. 2017. 38. P. 353–368.
Самойлова О.В., Трофимов Е.А., Гераскин В.И. Изучение процеcса образования карбидов хрома из компонентов расплава системы Cu–Cr–C // Вестник ЮУрГУ. Сер. “Металлургия”. 2017. 17. № 3. С. 13–20.
Jain D., Isheim D., Hunter A.H., Seidman D.N. // Metallurgical and Materials Transactions A. 2016. 47. № 3872. P. 3860–3872. https://doi.org/10.1007/s11661-016-3569-5
Pawar S., Jha A.K., Mukhopadhyay G. // International J. Refractory Metals and Hard Materials. 2019. 78. P. 288–295. https://doi.org/10.1016/j.ijrmhm.2018.10.014
Dreizin E.L., Schoenitz M. Mechanochemically prepared reactive and energetic materials: a review // J. Materials Science. 2017. 52. P. 11789–11809.
Azabou M., Ibn Gharsallah H., Escoda L., Suñol J.J., Kolsi A.W., Khitouni M. Mechanochemical reactions in nanocrystalline Cu–Fe system induced by mechanical alloying in air atmosphere // Powder Technology. 2012. 224. P. 338–344.
Дополнительные материалы отсутствуют.