Расплавы, 2021, № 4, стр. 365-375
Получение ультрапористого железа посредством электрохимического деаллоинга ферромарганца в расплавленной эквимольной смеси хлоридов натрия и калия
Д. А. Роженцев a, *, О. А. Тропин a, Д. С. Ренев b, Н. К. Ткачев a, В. И. Жучков b, О. В. Заякин b
a Институт высокотемпературной электрохимии УрО РАН
Екатеринбург, Россия
b Институт металлургии УрО РАН
Екатеринбург, Россия
* E-mail: d.a.rozhentsev@mail.ru
Поступила в редакцию 10.12.2020
После доработки 26.01.2021
Принята к публикации 01.02.2021
Аннотация
Исследовано влияние состава и времени анодного растворения на микроструктуру и морфологию ультрапористого железа путем электрохимического деаллоинга (селективного анодного растворения) сплавов железо–марганец в расплавленной эквимольной смеси NaCl–KCl. Установлена возможность электрохимического получения ультрапористого железа в режиме перколяции при температуре 700°C. Найдена область потенциалов селективного удаления марганца в указанной эквимольной смеси. Для образования характерной взаимно-непрерывной перколяционной структуры пор и лигаментов время выдержки при потенциале 0.1 В составляет один час. При деаллоинге ферромарганца с содержанием Mn 33 мас. % вытравливание марганца происходило практически до конца, и ультрапористое железо получалось более однородным по размеру пор и лигаментов.
ВВЕДЕНИЕ
Современный интерес к явлениям анодного растворения, контролируемым поверхностью, которые ярко проявляются в нанопористых материалах, связаны с их многообразным потенциальным применением и обусловлены относительной легкостью их изготовления с использованием простого процесса коррозии: химической или электрохимической. Нанопористые макроскопические тела, получаемые посредством деаллоинга (dealloying) или удаления одного из компонентов сплава, имеют строение сети “связок” (ligaments) с определенным характерным размером, который может варьироваться от нескольких нм до нескольких мкм [1–7]. Они могут быть изготовлены таким образом, что перед деаллоингом будущим изделиям можно придать нужную макроскопическую форму стандартными методами металлургии или металлообработки: литьем или прокаткой. Одним из перспективных способов получения нанопористых металлов является анодное растворение или деаллоинг менее благородных компонентов сплавов в перколяционном режиме [8]. Перколяционный деаллоинг подразумевает подбор таких параметров электрохимического растворения сплава, при которых твердому сплаву выгодно формировать максимально возможную поверхность при заданной температуре, разности потенциалов или кажущейся плотности тока, избавляясь от электроактивного компонента. Подобные процессы известны для многих сплавов и в потенциостатическом, и в гальваностатическом режиме [2–14].
Нанопористое железо и некоторые ферросплавы, содержащие марганец и другие электроактивные металлы, могут стать перспективными материалами в качестве саморассасывающихся имплантов для восстановления костной ткани после переломов [15]. Действительно, железо безвредно для человеческого организма, а показатели твердости нанопористых металлов вполне приемлемы для механических нагрузок на имплант. Нам известны лишь несколько работ, посвященных получению нанопористого железа деаллоингом в водных растворах. В работе [15] описан четырехэтапный способ получения нанопористого железа из сплавов Fe–Mn, Fe–Mn–Zn в водных растворах. Четыре этапа получения конечного материала включают в себя: насыщение поверхности цинком, первоначальный деаллоинг, отжиг и второй деаллоинг. Основным недостатком подобного метода является затраченное время на получение конечного продукта, которое может достигать нескольких дней.
Деаллоингу посвящено большое количество работ, выполненных в водных растворах, но практически полностью отсутствуют сведения о его проведении в жидкосолевых ионных средах при повышенных температурах. Между тем, такие электролиты способны обеспечить ускорение перколяционного процесса. В научном отношении солевые расплавы являются перспективными модельными системами для изучения влияния катионного и анионного состава среды, температуры и режима электролиза на размеры пор конечного продукта. Проведение анодного растворения в солевых расплавах способно избежать этапа дополнительного отжига сплавов и позволяет провести термическую обработку прямо во время электрохимического синтеза, что также представляет большой интерес.
Целью данной работы было определение потенциалов и времени селективного анодного растворения при высокотемпературном электрохимическом деаллоинге сплавов железо-марганец двух различных составов в расплавленной эквимольной смеси хлоридов натрия и калия.
Основными идеями и вытекающими из них задачами исследования являлись: во-первых, использование ферросплава с заметным различием потенциала выделения второго компонента (марганец) и, во-вторых, использование хлоридных расплавов в качестве высокотемпературного электролита. По нашему мнению, такая постановка задачи должна привести к перколяционному режиму деаллоинга и образованию ультрапористых структур железа. Важнейшими параметрами, определяющими возможность такого рода процессов, являются потенциал селективного растворения, и время проведения высокотемпературного электролиза. Среда галогенидных расплавов щелочных металлов призвана значительно интенсифицировать процесс растворения за счет высокой температуры и широкого электрохимического окна, а также обеспечить дополнительную термообработку непосредственно во время изготовления пористого материала.
ЭКСПЕРИМЕНТАЛЬНАЯ ЧАСТЬ
Материалы и подготовка образцов
Для приготовления образцов Fe–Mn с содержанием марганца: 33 (образец 1) и 67 мас. % (образец 2) были использованы навески карбонильного железа (не менее 97% металлического железа) и электролитического марганца (не менее 99.8% металлического марганца). Подготовленную смесь взвешивали и сплавляли в печи Таммана при T = 1420°C в потоке аргона в алундовом тигле, чтобы уменьшить содержание кислорода в сплаве и минимизировать испарение марганца. После гомогенизации расплава в течение 30 мин, производили отбор расплавленного металла в кварцевые трубки диметром 5 мм, полученные стрежни охлаждали на воздухе. Затем, стержни подвергали механической резке на образцы длиной 25 мм и диаметром 4 мм. После этого определяли химическое содержание элементов в полученных образцах по всей длине. В табл. 1 приведены данные о среднем содержании марганца в образцах, состав которых оказался очень близок к заданному. С помощью рентгеновского фазового анализа кристаллическую структуру. Было найдено, что все изготовленные образцы имеют ГЦК решетку (рис. 1).
Таблица 1.
Химический состав образцов
Химический состав в мас. % | ||||||
---|---|---|---|---|---|---|
Элемент | Mn | Fe | О | Na | K | Cl |
Образец 1 | 33.13 | 66.87 | – | – | – | – |
Образец 2 | 67.05 | 32.95 | – | – | – | – |
Образец 1 после эксперимента: при 0.1 В в течение 30 мин | 7.07 | 87.5 | 4.14 | 0.93 | 0.36 | – |
Образец 1 после эксперимента: при 0.1 В в течение 1 ч | 2.82 | 91.6 | 4.96 | 0.41 | – | 0.21 |
Образец 1 после эксперимента: 0.1 В в течение 90 мин | 1.92 | 95.68 | 2.07 | 0.33 | – | – |
Образца 2 после эксперимента: 0.3 В в течение 30 мин | 44.15 | 41.87 | 13.98 | – | – | – |
Образец 2 после эксперимента: 0.35 В в течение 90 мин | 13.17 | 86.83 | – | – | – | – |
Перед экспериментами образцы шлифовали на наждачной бумаге разной зернистости до появления зеркального отражения. После шлифовки образцы приваривали к токоподводу из нержавеющей стали.
Подготовка исходных хлоридов щелочных металлов
В качестве солей-растворителей использовали эквимольную смесь хлоридов щелочных металлов NaCl–KCl (Tпл = 650°C). Ее получали из индивидуальных хлоридов щелочных металлов марки х. ч.: хлорид натрия (Tпл = 806°C), хлорид калия (Tпл = = 782°C).
Исходные смеси хлоридов щелочных металлов готовили следующим образом: индивидуальные хлориды щелочных металлов сушили под вакуумом в специальных кварцевых ячейках при температуре 573 K в течение 3 ч. После вакуумной сушки соль расплавляли, для этого температуру поднимали выше температуры плавления индивидуальной соли на 50–100 К. Расплавы сливали в чистые тигли из углерода. Соли хранили в сухом инертном боксе в атмосфере азота. Для приготовления эквимолярных смесей брали навески индивидуальных хлоридов щелочных металлов, очищенных и переплавленных вышеупомянутым образом: 0.5NaCl–0.5KCl (мол. %). Навески помещали в кварцевую ячейку и сплавляли при нагреве выше температуре плавления на 50–100 K. После проведения данных процедур расплав сливали в чистые углеродные тигли. Полученную эквимольную смесь хранили в сухом инертном боксе в атмосфере азота.
Электрохимическая ячейка и проведение эксперимента
Электрохимические эксперименты проводили в силитовой печи сопротивления, в трехэлектродной ячейке, состоящей из круглодонной кварцевой колбы в атмосфере аргона, дополнительно очищенном от влаги. Особое внимание было уделено выбору материалов, устойчивых в агрессивной среде расплавленных солей при высоких температурах. В электрохимической ячейке использовали кварцевую круглодонную колбу в качестве контейнера для расплавленной соли, молибденовый электрод в виде проволоки диаметром 4 мм в качестве катода, платиновую проволоку диаметром 2 мм в качестве электрода сравнения. Анодом в данной ячейке являлся образец из предварительно подготовленного сплава Fe–Mn, приваренный к токоподводу из нержавеющей стали диаметром 4 мм. Схема электрохимической ячейки приведена на рис. 2.
Рис. 2.
Схема экспериментальной ячейки: 1 – молибденовый катод, 2 – токоподвод из нержавеющей стали, 3 – платиновый электрод сравнения, 4 – вакуумные пробки, 5 – алундовые чехлы, 6 – газовый подвод, 7 – образец из сплава ферромарганца, 8 – хлоридный расплав, 9 – кварцевая круглодонная ячейка.
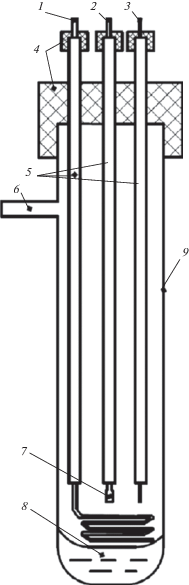
Эксперименты проводили при температуре 700°C в атмосфере аргона. Сначала в кварцевую круглодонную колбу загружали примерно 30 г предварительно подготовленной и измельченной смеси хлоридов. Расплавление смеси проводили под вакуумом. После расплавления и гомогенизации смеси в течение 30 мин, в расплав погружали электроды и заполняли электрохимическую ячейку очищенным и высушенным аргоном.
Определение интервала потенциостатического деаллоинга: циклическая вольтамперометрия
Первоначально снимались циклические вольтамперные кривые с помощью потенциостата BioLogic SP-50 для определения характерных параметров (потенциала коррозии), необходимых для выбора режима электролиза (рис. 3). Из рисунка видно, что интервал выделения марганца 0.05–0.2 В. Пик 0.15 В. Интервал выделения железа 0.6–0.8 В, пик– 0.65 В. Разница около 500 мВ позволяет сделать вывод о том, что процесс выделения марганца возможен. После определения подходящего потенциала проводилось анодное растворение сплава Fe–Mn при потенциалах 0.1, 0.15, 0.3 и 0.35 В. После проведения экспериментов и охлаждения ячейки до комнатной температуры полученные образцы аккуратно отрезались алмазным диском от токоподвода и промывались в ультразвуковой ванне в дистиллированной воде (6 мин), а затем в ацетоне (3 мин).
РЕЗУЛЬТАТЫ И ОБСУЖДЕНИЕ
На рис. 4 приведен рентгеноспектральный микроанализ (РЭМ) изображения поверхности образца ферромарганца, подвергнутого анодному растворению при 0.1 В в течение 30 мин при 700°С. Видно, что в данном случае пористая структура не успевает сформироваться. Морфология поверхности свидетельствует о вытравливании марганца с образованием рельефа, в котором плотность пор слишком мала.
Рис. 4.
Изображения РЭМ образца 1 (33 мас. % Mn), подвергнутому электрохимическому деаллоингу в расплаве NaCl–KCl при температуре 700°С, электродный потенциал – 0.1 В, время выдержки – 30 мин, увеличение ×10 000 и ×20 000.
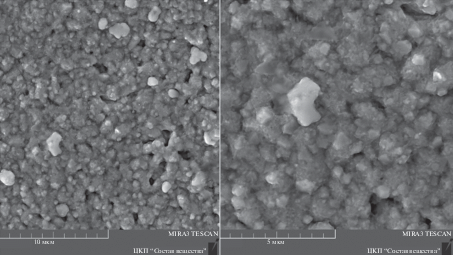
Химический состав, определенный после эксперимента, свидетельствует об удаление марганца до 7 мас. % (табл. 1). В совокупности можно сделать вывод о том, что марганец за 30 мин удалился с поверхности, а деаллоинг не прошел в режиме перколяции.
На рис. 5 приведены РЭМ изображения поверхности образца ферромарганца, подвергнутого анодному растворению при 0.1 В в течение 1 ч при 700°С. Видно, что в данном случае пористая структура успевает сформироваться. Размер пор и лигаментов (связок) примерно одинаков и составляет величину микронного масштаба. В табл. 1 приведен химический состав после эксперимента, видно, что марганец удалился до 2.82% с образованием перколяционной структуры образца.
Рис. 5.
Изображения РЭМ образца 1 (33 мас. % Mn), подвергнутого электрохимическому деаллоингу в расплаве NaCl–KCl при температуре 700°С, электродный потенциал – 0.1 В, время выдержки – 60 мин, увеличение ×2000 и ×10 000.

Если руководствоваться характерными размерами пор и лигаментов, то рассуждения показывают, что 1 см3 такого материала заключает в себе площадь порядка 100 см2 поверхности. Если размер 1 поры или лигамента порядка 1 мкм, то площадь его поверхности составляет величину порядка 10–7 см2, объем поры соответствует 10–12 см3, а число пор в 1 см3 – 1011. Следовательно, площадь поверхности, заключенной в кубическом сантиметре такого материала будет составлять величину порядка 104 см2, т.е. порядка 1 м2.
На рис. 6 приведены РЭМ изображения поверхности образца ферромарганца, подвергнутого анодному растворению при 0.1 В в течение 90 мин при 700°С. Видно, что за это время характерный размер связок увеличивается до нескольких мкм. В табл. 1 приведен химический состав после эксперимента, видно, что марганец удалился до 2.82%, но перколяционная структура после 90 мин проведения эксперимента начинает зарастать, происходит коалесценция металлической фазы.
Рис. 6.
Изображения РЭМ образца 1 (33 мас. % Mn), подвергнутого электрохимическому деаллоингу в расплаве NaCl–KCl при температуре 700°С, электродный потенциал – 0.1 В, время выдержки – 90 мин, увеличение ×1000 и ×10 000.
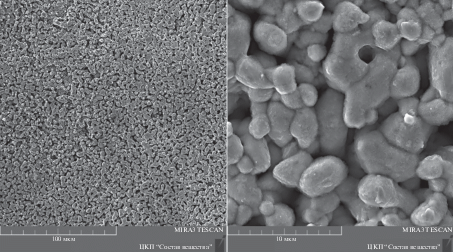
На рис. 7 приведены РЭМ изображения поверхности образца ферромаргнаца (33 мас. % Mn), подвергнутого анодному растворению при 0.15 В в течение 45 мин при 700°С. Видно, что за это время начинает возникать пористая структура на поверхности. Характерный размер пор при увеличении содержания марганца уменьшился и составляет до 300 нм.
Рис. 7.
Изображения РЭМ образца 2 (67 мас. % Mn), подвергнутого электрохимическому деаллоингу в расплаве NaCl–KCl при температуре 700°С, электродный потенциал – 0.15 В, время выдержки – 45 мин, увеличение ×10 000 и ×40 000.
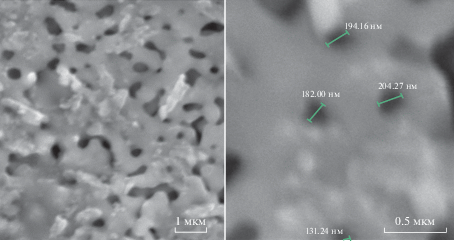
На рис. 8 приведены РЭМ изображения поверхности образца ферромаргнаца, подвергнутого анодному растворению при 0.3 В в течение 30 мин при 700°С. Видно, что за это время перколяционная структура лишь начинает формироваться, при этом размер связок достигает порядка 1 мкм. В табл. 1 приведен химический состав образца после эксперимента, видно, что марганец удалился до 44 мас. %.
Рис. 8.
Изображения РЭМ образца 2 (67 мас. % Mn), подвергнутого электрохимическому деаллоингу в расплаве NaCl–KCl при температуре 700°С, электродный потенциал – 0.3 В, время выдержки – 30 мин, увеличение ×5000 и ×50 000.
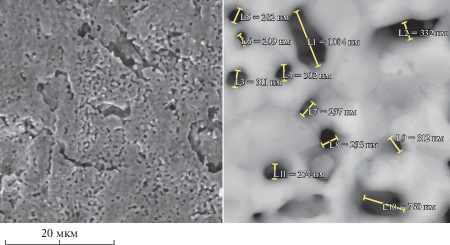
На рис. 9 приведены РЭМ изображения поверхности образца ферромарганца (67 мас. % Mn), подвергнутого анодному растворению при 0.35 В в течение 90 мин при 700°С. Видно, что за это время перколяционная структура сформировалась, при этом размер пор и связок примерно одинаковый и достигает порядка 700 нм. Коалесценция как в образцах с 33% марганца не происходит. В табл. 1 приведен химический состав после эксперимента, видно, что марганец удалился до 13 мас. %.
Рис. 9.
Изображения РЭМ образца 2 (67 мас. % Mn), подвергнутого электрохимическому деаллоингу в расплаве NaCl–KCl при температуре 700°С, электродный потенциал – 0.35 В, время выдержки – 90 мин, увеличение ×5000 и ×40 000.
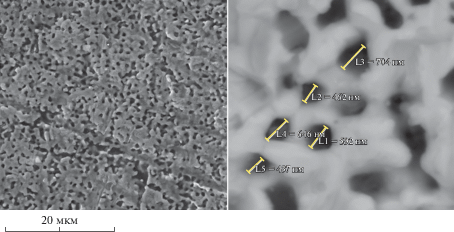
Таким образом, продолжительность процесса, которое необходимо для получения равномерной пористой структуры, приблизительно 1 ч, при меньшем времени порядка 30 мин перколяция не происходит, пористая структура не равномерна. В результате применения высоких температур время получения пористой структуры заметно ниже, чем в случае водных растворах [15], однако размер пор получается в 3–4 раза больше. В качестве перспективы можно отметить понижение температуры деаллоинга за счет использования низкоплавких эвтектик галогенидов щелочных металлов. Также интересно рассмотреть различные составы, в том числе с включением третьего компонента.
ЗАКЛЮЧЕНИЕ
1. Показана возможность электрохимического получения ультрапористого железа в режиме перколяции в эквимиольной смеси NaCl–KCl при температуре рекристализационного отжига сталей T = 700°С.
2. Были измерены циклические вольтамперограммы, найдена область потенциалов селективного удаления марганца, интервал выделения составил 0.05–0.2 В; с максимумом на 0.15 В.
3. Найдено, что время выдержки при потенциале 0.1 В составляет около часа для образования характерной взаимно непрерывной перколяционной структуры пор и лигаментов. Более длительная выдержка приводила к коалесценции металлической фазы железа.
4. Установлено, что при деаллоинге Fe–Mn с содержанием Mn 33 мас. % вытравливание менее благородного металла происходило практически до конца, и ультрапористое железо получалось более равномерным по размеру пор и лигаментов.
Таким образом, сплавы железа и марганца в пропорции 2 : 1 являются перспективными для получения ультрапористого железа с размерами пор микронного размера, а применение жидкосолевого электролита позволяет уменьшить время электрохимического деаллоинга и параллельно провести термообработку.
Исследование выполнено при финансовой поддержке РФФИ в рамках научного проекта № 20-33-90 224.
Список литературы
Stenner C., Shao L.-H., Mameka N., Weissmüller J. // Adv. Funct. Mater. 2016. 26. № 28. P. 5174–5181. https://doi.org/10.1002/adfm.201600938
Sun S., Chen X., Badwe N., Sieradzki K. // Nat. Mater. 2015. 14. № 9. P. 894–898. https://doi.org/10.1038/nmat4335
Ian M., Alain K., Jonah E. // Materials Research Society. 2018. 43. № 1. P. 27–34. https://doi.org/10.1557/mrs.2017.301
Zhang J., Li C.M. // Chem. Soc. Rev. 2012. 41. № 21. P. 7016–7031. https://doi.org/10.1039/c2cs35210a
Sieradzki K., Dimitrov N., Movrin D., McCall C., Vasiljevic N., Erlebacher J. // J. Electrochem. Soc. 2002. 149. № 8. P. 370–377. https://doi.org/10.1149/1.1492288
Введенский А.В. Термодинамика и кинетика селективного растворения бинарных твердых растворов: дис. д-ра хим. наук. Воронеж. 1994.
Озеряная И.Н. Особенности коррозии металлов в расплавленных галогенидах и карбонатах. Высокотемпературная коррозия и методы защиты от нее. Наука, 1973.
Weissmüller J., Sieradzki K. // MRS Bulletin. 2018. 43. № 1. P. 14–19. https://doi.org/10.1557/mrs.2017.299
Masataka H., Mamoru M. // Materials Transactions. 2009. 50. № 3. P. 431–435. https://doi.org/10.2320/matertrans.MBW200825
Masataka H., Hiromi N., Toshiyuki F., Masaki T. // J. Phys. Chem. 2010. 114. № 2. P. 868–873. https://doi.org/10.1021/jp909479m
Wenjing L., Houyi M., Lihui H., Yi D. // Phys. Chem. 2011. 13. № 2. P. 5565–5568. https://doi.org/10.1039/c0cp02178d
Shan S., Jurgen M., Jorg W. // J. Electrochimica Acta. 2018. 285. P. 60–69. https://doi.org/10.1016/j.electacta.2018.07.081
Junling X., Yan W., Zhonghua Z. // J. Phys. Chem. 2012. 116. № 9. P. 5689–5699. https://doi.org/10.1021/jp210488t
Маршаков И.К. Анодное растворение и селективная коррозия сплавов. Изд-во Воронеж. гос. ун-та, 1988.
Heiden M., Johnson D., Stanciu L. // Acta Mater. 2016. 103. P. 115–127. https://doi.org/10.1016/j.actamat.2015.10.002
Дополнительные материалы отсутствуют.