Известия РАН. Теория и системы управления, 2022, № 1, стр. 95-104
О ПОСТРОЕНИИ ИНТЕЛЛЕКТУАЛЬНОЙ СИСТЕМЫ УПРАВЛЕНИЯ КИСЛОРОДНЫМ КОНВЕРТЕРОМ НА ОСНОВЕ КОМПЬЮТЕРНОГО ЗРЕНИЯ
В. Б. Трофимов *
ФГАОУ ВО “Национальный исследовательский технологический университет “МИСиС”
Москва, Россия
* E-mail: trofimov_vbt@mail.ru
Поступила в редакцию 06.04.2021
После доработки 09.06.2021
Принята к публикации 26.07.2021
- EDN: PZMQMT
- DOI: 10.31857/S0002338821060159
Аннотация
Предложена структура интеллектуальной системы управления конвертером, включающая подсистемы распознавания и оценивания выбросов газошлако-металлической эмульсии в режиме реального времени на основе компьютерного зрения по прямым признакам, подсистему прогнозирования выбросов по косвенным признакам, которые наиболее часто используются для мониторинга кислородно-конвертерного процесса. Разработаны процедуры прогнозирования и обнаружения выбросов на основе искусственных нейронных сетей и прецедентного подхода. Описаны морфологические признаки выбросов, а также факторы, влияющие на их возникновение.
Введение. Кислородно-конвертерный процесс представляет собой сложную совокупность тепловых, химических, аэро- и гидродинамических процессов, протекающих одновременно и совмещенных в пространстве. Выбросы (непрерывный перелив через край конвертера) вспенивающегося шлака, точнее газошлакометаллической эмульсии, содержащей пузырьки газов CO и CO2, оксиды металлов (шлак) и капли металла, образующейся на поверхности расплава во время продувки кислородом, – сложное явление, сопровождающее конвертерные процессы с момента их появления, зависящее от многих факторов. Выбросы вызывают потерю металла (обычно от 5 до 12%), нарушение кислородно-конвертерного процесса и загрязнение окружающей среды. Выбросы происходят неравномерно, что часто приводит к увеличению времени между плавками, остановкам для очистки (удаления остатков материала), ремонту охладительной системы.
Задача автоматического прогнозирования и оперативного обнаружения выбросов на основе компьютерного зрения и машинного обучения с целью их предотвращения, уменьшения эксплуатационных и экологических проблем до сих пор является актуальной.
На возникновение выброса вспененной эмульсии влияют: химический состав и показатели качества чугуна и лома (особенно содержание Si и Mn в чугуне); физико-химические свойства и количество шлака (увеличение окисленности шлака, основность шлака от 1.4 до 1.8); размер пузырьков газов CO и CO2, их выделение; скорость обезуглероживания; “присадка” большого количества железорудных материалов одной порцией; расстояние от поверхности металла до фурмы; интенсивность и программа расхода кислорода (существенное увеличение расхода кислорода с целью повышения производительности конвертера); вес каждого добавленного флюса; состояние футеровки конвертера (срок службы футеровки, количество плавок с момента последней замены); износ сопел фурмы (применение современных фурм не решает проблему выбросов). Причины выброса иногда имеют противоречивый характер. В середине продувки обычно наблюдаются два или три максимума интенсивности выбросов, совпадающие с наибольшими значениями скорости обезуглероживания и подъемом уровня ванны.
В [1] описан метод автоматического обнаружения выбросов по косвенным признакам на основе обработки акустического сигнала для оценки уровня шлака в конвертере (шум в процессе измерения рассматривается как “белый”, имеющий нормальный закон распределения) и на основе использования упрощенной модели (линейной регрессии), описывающей взаимосвязь между расходом отходящего газа, давлением и полученной оценкой уровня вспенивающегося шлака. Параметры этой модели определяются методом наименьших квадратов и обновляются в режиме реального времени. В качестве признака возможного выброса также рассматривается резкое изменение параметров модели из-за значительного изменения химических реакций в конвертере, т.е. из-за отклонения от нормального режима работы.
Точную динамическую модель образования вспенивающегося шлака в конвертере (для оценки его уровня) аналитическим методом получить сложно или невозможно, проблема определения размера пузырьков газа, оценивания химического состава и измерения температуры расплава в режиме реального времени на всем интервале продувки не решена. Существующие методы позволяют оценить содержание углерода в расплаве и измерить его температуру только на завершающей стадии процесса (при этом контроль осуществляется дискретно в нескольких временных точках) и применяются для конвертеров большой емкости. При наличии помех, грубых выбросов в сигналах измерительной информации, при изменении базового режима работы объекта, при неточной информации о химическом составе лома гибридные или упрощенные модели требуют дополнительной настройки параметров. Для оценки этих параметров на основе экспериментов в работе [1] используют метод наименьших квадратов, предпосылки которого не выполняются для сложных нелинейных нестационарных динамических процессов. Для проверки таких упрощенных моделей применяют физическую модель конвертера (“холодную” модель объекта управления), но не рассматривают проблемы подобия [1].
На зависимость уровня вспенивающегося шлака в конвертере от акустических сигналов, вибрации конвертера, состава и температуры отходящего газа влияют изменяющиеся и не поддающиеся автоматическому контролю в режиме реального времени факторы, например физические свойства шлака, поэтому точность математических моделей, отражающих эту зависимость, существенно ограничена [2]. Обнаружение выброса по этим моделям определяется либо при пересечении определенного граничного уровня сигнала, либо в случае, когда измеренный параметр слишком сильно отклоняется от среднего значения.
Обнаружение выбросов с помощью видеокамер, просматривающих летку конвертера, может вызвать некоторые проблемы при обслуживании. В [2] представлена автоматическая система прямого обнаружения выбросов в режиме реального времени, основанная на методах обработки изображений, сделанных видеокамерой, которая просматривает горловину конвертера. В этой системе цветное изображение преобразуется в черно-белое, далее из полученного изображения удаляются помехи, искажающие распознаваемый выброс. Для ее настройки используются два параметра: значение порога для B-компоненты (в цветовой модели RGB) и максимальный размер исключаемых помех. Белые пиксели на изображении используются для обнаружения выбросов. Расстояние от видеокамеры до конвертера составляет около 10 м. Чтобы справиться с резкими изменениями интенсивности света во время плавки, вместо стандартной видеокамеры CCD была применена CMOS-видеокамера. Если произойдет сильное вспыхивание пламени, то это может замаскировать выброс и эта система перестанет идентифицировать его, поэтому необходимы дополнительные модули прогнозирования выбросов по косвенным признакам.
В [3] представлена автоматическая система обнаружения выбросов на основе одновременной цифровой обработки акустических сигналов от микрофона, установленного над конвертером, и изображения с видеокамеры, установленной в 27.5 м от горловины конвертера. Изображения горловины конвертера регистрируются со скоростью 10 кадров в секунду. Алгоритм обработки изображения [3]: извлечение “интересующей области” (ROI) из изображения, т.е. области, содержащей выброс; преобразование RGB-изображения в HSL; преобразование полученного изображения в черно-белое; применение метода Робертса для выделения контуров изображения; фильтрация мелких частиц (помех) на изображении; суммирование информативных участков изображения и вычисление нормированного значения “индекса обнаружения выбросов”. Если это значение выше порогового уровня, то возможен выброс. Данный алгоритм не позволяет автоматически распознать размер выброса (“сильный”, “слабый” или “средний”).
Если уровень звука L слишком высок, то уровень вспенивающегося шлака в конвертере низкий и вероятность возникновения выброса очень мала. На практике часто встречается ситуация когда уровень звука ниже порогового значения, а выброс не происходит, что приводит к большому количеству ложных сигнализаций. Искажение звукового сигнала шумами от внешних источников также является проблемой, поэтому звуковой акустический сигнал сам по себе не рассматривается как надежный признак для обнаружения выбросов [3].
Сильное хаотическое пламя, имеющее область насыщенного цвета, близкую к белому, – актуальная проблема для цифровой обработки изображений. Сильное пламя при низком уровне пены в конвертере часто распознается в этой системой [3] как выброс, что приводит к ложному срабатыванию.
В автоматизированной оптоакустической системе обнаружения выбросов [4] используются три микрофона, чтобы выдерживать высокие уровни звукового давления, обрабатываются акустические сигналы, оценивается уровень звука, используется видеокамера CCD, просматривающая горловину конвертера и зону пламени, обрабатываются изображения по специальным алгоритмам обнаружения и оценки выбросов.
1. Постановка задачи. Управление кислородно-конвертерным процессом осуществляется оператором, который должен найти компромисс между высотой шлака (обеспечивающей высокое качество металла) и уменьшением (предотвращением) выбросов. Основной способ ведения продувки заключается в ступенчатом изменении положения фурмы и изменении расхода кислорода с помощью систем автоматического регулирования (САР) по утвержденным шаблонам (схеме продувки) для каждой марки стали. Корректировка программных управляющих воздействий осуществляется оператором на основе данных о химическом составе отходящих газов (по показаниям газоанализаторов) и визуального наблюдения за горловиной конвертера. На металлургических заводах разработаны способы борьбы с выбросами путем изменения режима продувки, шлакового режима. Оператор оценивает возможность выбросов по шкале от “1” до “3”, где “1” означает то, что выброса не будет, “2” – возможен “слабый” (“небольшой”, “легкий”) или “средний” выброс, “3” – возможен “сильный” выброс. Эта оценка является субъективной, часто проводится в условиях стресса, в агрессивных производственных условиях (высокие температуры, объемные потоки запыленных газов, быстро меняющиеся металлургические операции). Визуальное наблюдение опытным оператором через видеокамеру, контролирующую внутреннюю часть конвертера, обеспечивает предсказание выброса примерно за 30 с до его появления. Регистрация выбросов выполняется операторами вручную, и поэтому они не всегда могут быть “надежно” учтены (присутствует человеческий фактор). Обычно из 100% плавок 15% плавок с выбросами, из них: 7% – с “сильными” выбросами, 5% – со “средними” выбросами и 3% – с “небольшими” выбросами. Продолжительность ремонтных работ по очистке конвертера от шлака может составлять 20 мин. Сокращение издержек от выбросов является важной задачей (потери от одного выброса могут достигать более 0.5 млн руб.).
Применение вибрационного метода для оценки уровня вспенивающегося шлака не обеспечивает высокую точность, точность этой оценки во многом зависит от выбора измеряемых частот вибрации, которые меняются в зависимости от условий кислородно-конвертерного процесса.
Автоматическая система обнаружения выбросов (диагностирования состояния конвертерного процесса) должна быть точной, работать в режиме реального времени, прогнозировать выбросы в условиях колебания качества сырья и ассортимента продукции (заданных марок стали), быть интегрирована в систему аварийной сигнализации цеха. Система должна идентифицировать аномалии за время не менее чем сумма времени ответной реакции оператора-дистрибуторщика (от 5 до 10 с) и постоянной времени исполнительного механизма, регулирующего ход технологического процесса.
2. Схема интеллектуальной системы управления конвертером. Создание современных интеллектуальных технологий, систем обработки больших объемов данных, машинного обучения и искусственного интеллекта является актуальным направлением в науке и производстве [5–8].
В предлагаемой системе (рис. 1) осуществляется прогнозирование, распознавание и оценивание выбросов, формируются аварийные сигналы, выполняется сбор, отображение и хранение технологических данных, прецедентов в базе знаний с возможностью их использования в смежных системах. Система позволяет оператору наблюдать за процессами в конвертере с помощью видеокамер (ВК) и принимать окончательное решение о наличии выбросов, корректировать программы управления конвертером.
База знаний содержит:
изображения “слабых”, “средних” и “сильных” выбросов, на которых часть вспененного шлака капает или выливается через край конвертера, которые обычно можно увидеть в середине плавки, представляющих собой желтые или оранжевые объекты, расположенные вертикально прямо над защитным экраном (и их почти никогда не бывает над горловиной конвертера), наблюдаемые на нескольких последующих видеокадрах с ВК1 и ВК2;
изображения “слабых”, “средних” и “сильных” выбросов с ВК3 и ВК4, расположенных под корпусом конвертера;
изображения пламени, которые могут принимать любую форму и размер, но обычно это большие желтые или оранжевые узоры, возникающие в середине плавки, пламя может появиться внезапно и исчезнуть, а может быть видно некоторое время на всем изображении и, следовательно, над горловиной конвертера тоже;
изображения без выбросов, характеризующие “ровный” ход (“нормальное” состояние) процесса, представляющие собой горизонтальные желтые или оранжевые полоски, расположенные над устьем конвертера, они часто наблюдаются в начале и в конце плавки.
Для прогнозирования выбросов выполняются следующие операции:
проверка технологических данных на достоверность, фильтрация;
оценивание признаков в подсистеме № 1: CO, СО/СО2, СО/(СО+СО2), CO2, N2, Ar конвертерного отходящего газа;
ввод признаков в подсистему прогнозирования, т.е. в нейросетевой прогнозатор, представляющий собой многослойный персептрон с шестью входными элементами, 13 нейронами в промежуточном слое и одним выходным нейроном, функция активации нейронов – униполярная логистическая;
принятие решения о возможности возникновения выброса по правилу: если выход нейросетевого прогнозатора (искусственной нейронной сети – ИНС) ${{Y}_{{{\text{ИНС}}}}}(t) > 0.9$, то возможен выброс эмульсии, если ${{Y}_{{{\text{ИНС}}}}}(t) < 0.1$ и уровень звукового сигнала L выше порогового значения, то выброс не предвидится.
Обнаружение выбросов выполняется на основе обработки изображений с цифровых ВК. ВК1 и ВК2 направлены на зазор между нижней частью юбки газоотводящего тракта и горловиной конвертера (верхней частью защитного экрана).
Для распознавания выбросов выполняются следующие операции:
получение видеосигнала с ВК1 и ВК2;
разбиение каждого видеосигнала на последовательность непересекающихся видеокадров (цифровых изображений);
представление i-го цифрового изображения в цветовой модели RGB (получение 24-разрядного рисунка);
преобразование полученного цветного изображения в изображение с нулевым контрастом (изображение в градации серого) выполняется по формуле, которая отражает цветовое восприятие человека:
минимаксное нормирование (индекс “Н”) изображения осуществляется по формуле
бинаризация (индекс “Б”) изображения (“0” – черный цвет пикселя, “1” – белый) осуществляется по правилу
оценивание информативного признака в подсистеме № 2 путем суммирования бинарных кодов цвета пикселей в соответствии с выражениями:
по строкам: $X_{1}^{{}}(i) = \sum\limits_{m = 1}^M {S_{{1,m}}^{{\text{Б}}}(i)} ,$ …, $X_{N}^{{}}(i) = \sum\limits_{m = 1}^M {S_{{N,m}}^{{\text{Б}}}(i)} ;$
по столбцам: $X_{{N + 1}}^{{}}(i) = \sum\limits_{n = 1}^N {S_{{n,1}}^{{\text{Б}}}(i)} ,$ …, $X_{{N + M}}^{{}}(i) = \sum\limits_{n = 1}^N {S_{{n,M}}^{{\text{Б}}}(i)} ;$
оценивание принадлежности текущего изображения к одному из возможных состояний процесса осуществляется путем подачи на входы нейросетевых классификаторов выделенного информативного признака. На входные элементы первого классификатора подается признак, полученный по изображению с ВК1, а на входы второго – с ВК2. Математическое описание нейросетевых классификаторов (многослойного персептрона) имеет следующий вид:
Следующая операция – принятие решения о состоянии процесса по правилам:
если {${{Y}_{1}}(i) > 0.7$ и ${{Y}_{2}}(i) < 0.1$ и ${{Y}_{3}}(i) < 0.1$ и ${{Y}_{4}}(i) < 0.1$}, то выбросы отсутствуют, наблюдается “нормальное” состояние процесса;
если {${{Y}_{1}}(i) < 0.1$ и ${{Y}_{2}}(i) > 0.7$ и ${{Y}_{3}}(i) < 0.1$ и ${{Y}_{4}}(i) < 0.1$}, то наблюдается пламя;
если {${{Y}_{1}}(i) < 0.1$ и ${{Y}_{2}}(i) < 0.1$ и ${{Y}_{3}}(i) > 0.7$ и ${{Y}_{4}}(i) < 0.1$}, то появились “сильные” выбросы;
если {${{Y}_{1}}(i) < 0.1$ и ${{Y}_{2}}(i) < 0.1$ и ${{Y}_{3}}(i) < 0.1$ и ${{Y}_{4}}(i) > 0.7$}, то возникли “слабые” или “средние” выбросы.
В подсистеме оценивания признаков № 3 осуществляется: разбиение каждого видеосигнала с ВК3 и ВК4 на последовательность непересекающихся видеокадров, представление цифрового изображения в цветовой модели RGB, преобразование полученного цветного изображения в изображение с нулевым контрастом, минимаксное нормирование изображения, бинаризация изображения.
В подсистеме оценивания выбросов выполняется суммирование бинарных кодов цвета белых и черных пикселей изображения. Соотношение между белыми пикселями выбросов эмульсии и черными пикселям фона изображения используется для оперативного оценивания эффективности обнаружения выбросов, их прогнозирования, а также для оценивания размеров выбросов, которые не удалось устранить на ранней стадии. Это соотношение усредняется за период выборки 2 с и сохраняется в базе знаний.
Подсистема управления программным движением конвертера построена на основе подхода, представленного в работе [6], использующего CBR-концепцию [7]. Прецедент включает: описание проблемной ситуации (химический состав чугуна, его температура и вес, вид лома и его вес, номер и состояние фурмы, футеровки, заданная марка стали, вид ферромарганца, флюса, тип угля, химический состав извести, сворачивание шлака, выбросы, переливы шлака); описание совокупности управляющих воздействий (расход кислорода и его программная траектория, положение фурмы и ее программная траектория, время начала и окончания плавки, количество чугуна, залитого в конвертер, количество лома, извести, ферромарганца, флюса, угля, поданного в конвертер, длительность нагрева лома); описание результата применения решения (химический состав полученной стали, ее температура, параметры отходящих технологических газов, марка стали).
3. Применение интеллектуальной системы управления конвертером. Для исследования системы управления (рис. 1) были использованы натурные данные, полученные в кислородно-конвертерном цехе № 1 АО “ЕВРАЗ Объединенного Западно-Сибирского металлургического комбината”, производительность конвертера составляет 170 т/ч. При нормальном режиме работы объекта продувка ведется сверху через 5-сопловую фурму с расходом кислорода от 350 до 450 м3/мин. Положение фурмы в течение первых 3–4 мин продувки поддерживается на высоте от 2 до 2.6 м от уровня жидкого металла, после чего продувка ведется при высоте фурмы от 1 до 1.5 м. На плавках с присадкой на 8–14-й мин продувки углеродосодержащих материалов продувка ведется при высоте фурмы от 1.4 до 1.6 м.
При “сворачивании” шлака (основная причина – недостаток окислов железа в шлаке) разрешается кратковременный подъем фурмы на 1.5–1.8 м относительно рабочего положения. При появлении “выносов” металла разрешается кратковременный подъем фурмы до 2–3 м, производится присадка плавикошпатового концентрата порциями до 150 кг. При “выбросах” вспененной эмульсии допускается кратковременное снижение расхода кислорода до 250–300 м3/мин, при одновременном снижении положения фурмы на 100–300 мм, и присадка извести в количестве до 1 т. Выбросы возникают в периоды жидкофазного шлака, а выносы – при его сворачивании. При необходимости продувка прекращается и производится скачивание шлака.
После устойчивого зажигания плавки (появления устойчивого факела над горловиной), но не позднее, чем через 1 мин после начала продувки, юбку опускают, далее химический состав отходящих газов (рис. 2, а, 3, а, 4, а) подается в подсистему оценивания признаков № 1. По этим признакам в режиме реального времени формируется прогноз возникновения выбросов (рис. 2, б, 3, б, 4, б).
Рис. 2.
Натурные данные (после 100-й с продувки) по ситуации № 1: а – химический состав конвертерного газа, б – выход нейросетевого прогнозатора (прогноз выброса)
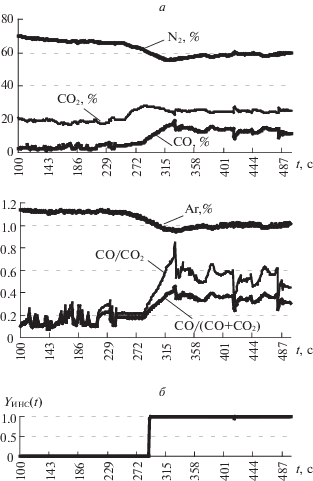
Искусственная нейронная сеть для прогнозирования выбросов была обучена по алгоритму обратного распространения ошибки с использованием натурных данных (прецедентов), характеризующих разные технологические ситуации. Среднеквадратическое отклонение сети на обучающем наборе данных составило 0.03 ед. Сеть прошла испытания на верификационном наборе данных и прогнозирует возможность возникновения выброса (рис. 2, б, 3, б, 4, б).
Параметры состава отходящих газов имеют наибольшую связь с процессами, протекающими в конвертере. Химический состав отходящего газа оценивается каждую секунду, что приводит к значительному сокращению времени на изменение этих процессов.
Искусственная нейронная сеть для распознавания выбросов была обучена по алгоритму обратного распространения ошибки с использованием цифровых изображений (рис. 5, M = 310, N = 254). Среднеквадратическое отклонение сети на обучающем наборе данных составляет 0.01 ед., а на верификационном – 0.08 ед. (при $\delta (i) = 0.5$, K = 284). Сеть распознает изображения, характеризующие разные состояния кислородно-конвертерного процесса.
Рис. 3.
Натурные данные (после 100-й с продувки) по ситуации № 2: а – химический состав конвертерного газа, б – выход нейросетевого прогнозатора (прогноз выброса)
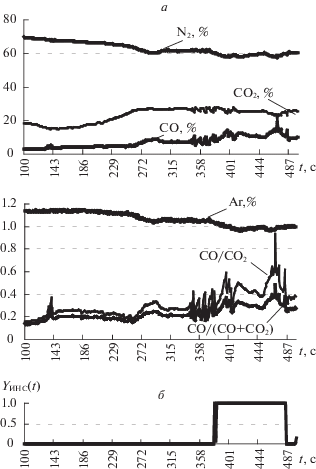
Рис. 4.
Натурные данные (после 100-й с продувки) по ситуации № 3: а – химический состав конвертерного газа, б – выход нейросетевого прогнозатора (прогноз выброса)
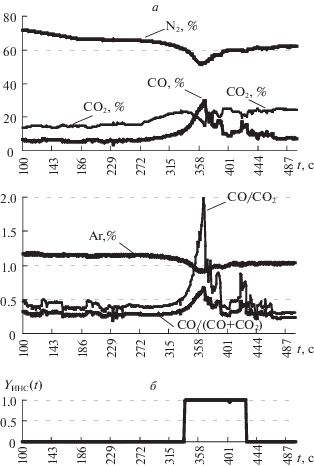
Рис. 5.
Цифровые изображения и их информативный признак: а – выбросы отсутствуют, наблюдается “нормальное” состояние процесса, б – пламя, в – “сильный” выброс, г – “слабый” выброс
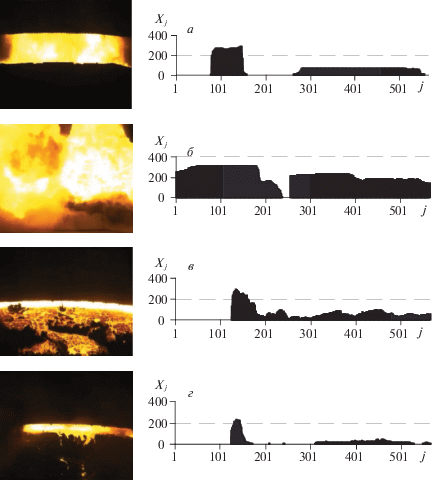
Цвет, размер и положение распознаваемых огненных образов на цифровых изображениях рассматриваются как отличительные признаки, которые искусственная нейронная сеть использует для идентификации состояния конвертера, для обнаружения выбросов. Если искусственная нейронная сеть распознает выброс на 8–10 изображениях подряд в течение 3 с, то это верный признак появления выброса, так как он обычно наблюдается длительное время.
Сохранение изображений и технологических данных (прецедентов) в базе знаний позволяет выполнить ретроспективный поиск причин возникновения выбросов.
Заключение. Обеспечение рентабельного производства, повышение качества выпускаемой продукции, минимизация негативного воздействия процесса на окружающую среду, уменьшение повреждений конвертера и риска для здоровья и безопасности операторов-технологов, а также уменьшение аварий невозможно без использования современных интеллектуальных систем управления.
Предлагаемая система отличается от других тем, что предупреждает оператора-технолога в режиме реального времени о возможности возникновения выброса (в среднем за 25 с до его появления) на основе искусственных нейронных сетей по признакам {CO, СО/СО2, СО/(СО+СО2), CO2, N2, Ar} конвертерного газа. Если выброс произошел, то система распознает его в течение 3–5 с после его возникновения, автоматически классифицирует его на “сильные” или “слабые/средние” выбросы, а также применяет прецедентный подход для управления конвертером.
Интеллектуальные системы управления на основе распознавания образов в автоматическом режиме позволяют уменьшить длительность продувки металла кислородом на 1–1.3 мин, увеличить производительность конвертера на 1–2%, уменьшить количество выбросов на 50–95%.
Список литературы
Evestedt M., Medvedev A. Model-based Slopping Warning in the LD Steel Converter Process // J. of Process Control. 2009. № 19 (6). P. 1000–1010.
Kattenbelt C., Spelbos E., Mink P., Roffel B. Detection of Slopping in Basic Oxygen Steelmaking Using a Camera Viewing the Converter Mouth // Steel Research Int. 2008. № 11 (79). P. 821–825.
Batista L.G., Salarolli P.F., Menezes R.P., Ayres L.M., Pereira R.P., Cuadros M.A., Furtado H.S. Slopping Detection System for LD Converters Using Sound Signal Digital and Image Processing // 13th IEEE Intern. Conf. on Industry Applications. Sao Paulo. 2019. P. 1137–1142.
Odenthal H.-J., Schluter J., Uebber N. Recent SMS Siemag Developments in BOF Steelmaking // 7th European Oxygen Steelmaking Conf. Trinec. 2014. 12 p.
Vassilyev S.N., Novikov D.A., Bakhtadze N.N. Intelligent Control of Industrial Processes // 7th IFAC Conf. on Manufacturing Modelling, Management, and Control. St. Petersburg. 2013. P. 49–57.
Trofimov V.B. An Approach to Intelligent Control of Complex Industrial Processes: An Example of Ferrous Metal Industry // Automation and Remote Control. 2020. V. 81. № 10. P. 1856–1864.
Aamodt A., Plaza E. Case-Based Reasoning: Foundational Issues, Methodological Variations, and System Approaches // AI Communications. IOS Press. 1994. V. 7. № 1. P. 39–59.
Temkin I., Klebanov D., Deryabin S., Konov I. Predictive Analytics in Mining. Dispatch System Is the Core Element of Creating Intelligent Digital Mine // Communications in Computer and Information Science. 2020. V. 1201. P. 365–374.
Дополнительные материалы отсутствуют.
Инструменты
Известия РАН. Теория и системы управления