Известия РАН. Теория и системы управления, 2022, № 5, стр. 102-117
КОНЦЕПЦИЯ УПРАВЛЕНИЯ ХАРАКТЕРИСТИКАМИ НАНОТРУБОК ПУТЕМ ОБРАБОТКИ ПРЕДШЕСТВЕННИКА КАТАЛИЗАТОРА ДЛЯ ИХ СИНТЕЗА
Е. А. Буракова a, *, Ю. В. Литовка a, В. А. Нестеров b, К. И. Сыпало c, А. Г. Ткачев a, Г. Ю. Юрков d
a ФГБОУ ВО “Тамбовский государственный технический университет”
Тамбов, Россия
b ФГБОУ ВО “Московский авиационный институт”
Москва, Россия
c ФГУП “ЦАГИ” им. Н.Е. Жуковского
Жуковский, Россия
d ФИЦ ХФ РАН
Москва, Россия
* E-mail: elenburakova@yandex.ru
Поступила в редакцию 26.01.2022
После доработки 10.03.2022
Принята к публикации 30.03.2022
- EDN: TRHFWS
- DOI: 10.31857/S0002338822050055
Аннотация
С целью реализации направленного синтеза углеродных наноструктур предлагается управление процессом их формирования осуществлять с помощью системы поддержки принятия решений. Для этого была разработана методология, основанная на новом методе управления параметрами синтезируемых наноструктур через реализацию пред- и посттермической обработки катализатора/его предшественника физическим воздействием. Реализация методологии позволила создать проблемно-ориентированную информационную систему сопровождения и поддержки принятия решений, гарантирующую без проведения экспериментов определение условий получения катализатора, которые способствуют синтезу наноструктур с заданными характеристиками. Использование данной системы в производстве наноструктур подтвердило надежность найденных условий формирования катализатора, обеспечивающих направленный синтез многослойных углеродных нанотрубок.
Введение. Последние десятилетия пристальное внимание ученых уделено нанотехнологиям, в частности получению и применению углеродных наноструктурных материалов. Одним из наиболее востребованных наноматериалов являются углеродные нанотрубки (УНТ). Несмотря на успешную реализацию промышленного производства УНТ, актуальной остается проблема реализации их направленного синтеза, так как для каждой области применения необходимы наноструктуры определенной морфологии [1]. Решение данной проблемы откроет новые производственные возможности для организаций, занятых в сфере нанотехнологий.
Анализ данного вопроса показал, что проблема реализации направленного синтеза (формирование УНТ с заданными характеристиками) вызвана отсутствием эффективного управления процессом синтеза наноструктур. Причинами этого являются отсутствие общепринятой теории формирования углеродных наноструктур [2, 3], функциональных связей между управляющими факторами (природа углеродсодержащего газа, состав катализатора, технологические режимы процесса получения катализатора и синтеза УНТ и др.) и характеристиками целевого продукта.
В наше время сложно представить современную производственную систему без использования информационных технологий и промышленное производство углеродных наноструктурных материалов не исключение. Оно тоже бесспорно нуждается в систематизации имеющейся информации и информационной поддержке на всех стадиях получения нанопродукта [4, 5]. Создание современной системы управления производственным процессом в отсутствие методологии невозможно – это долгий и сложный процесс, требующий больших затрат. Поэтому на данном этапе развития установление системных связей и закономерностей функционирования элементов технологической системы производства УНТ, поиск новых методов управления характеристиками наноструктур (без изменения состава катализатора и условий синтеза) представляются весьма актуальными, так как могут позволить решить проблему реализации направленного синтеза УНТ.
Цель работы – организация эффективного управления характеристиками УНТ с использованием системы поддержки принятия решений, обеспечивающей их направленный синтез.
1. Поиск метода управления. Известно, что среди существующих методов синтеза УНТ наиболее целесообразным для промышленного производства является метод газофазного химического осаждения (ГФХО) на поверхности катализатора. Несмотря на то, что данный метод принципиально прост, формирование наноструктур – это многофакторный и сложно контролируемый процесс [2, 6, 7]. Промышленное производство углеродных наноструктурных материалов методом ГФХО представляет собой сложную технологическую систему, в которой основными производственными процессами являются получение катализатора для синтеза УНТ и формирование наноструктур на его поверхности.
Эффективное функционирование (надежность, способность к адаптации и др.) данной технологической системы может быть реализовано через управление производственным процессом [8, 9]. Анализ научно-технических источников показал, что большинство работ, поверхностно затрагивающих вопросы управления параметрами УНТ, посвящены регулированию характеристик наноструктур через условия синтеза и состав катализатора [10–13]. Выявлено, что основные геометрические характеристики, такие, как внешний диаметр и длина УНТ, определяются соответственно размером частиц катализатора [14–16] и его активностью/эффективностью в процессе синтеза. Активность/эффективность катализатора оценивается по количеству нанопродукта, синтезированного на одном грамме катализатора (грамм нанопродукта/грамм катализатора, гС/гcat).
Поэтому в настоящее время при реализации лабораторного или промышленного производства УНТ в основном управление характеристиками синтезируемых наноструктур осуществляется путем изменения состава катализатора. Разрозненность, а иногда и противоречивость встречающейся информации о регулировании характеристик УНТ через состав и методы получения катализатора способствовали формированию в промышленном производстве углеродных наноструктур тенденции “один состав катализатора – один тип углеродных наноструктур”. Данный подход к управлению промышленным производством УНТ не всегда приемлем для производителя, так как препятствует расширению номенклатуры выпускаемой нанопродукции. При таком подходе в случае расширения ассортимента выпускаемой продукции от производителя требуются большие затраты на приобретение или разработку новых составов, методик получения катализатора, проведение длительных и трудоемких экспериментов по определению необходимых условий реализации синтеза наноструктур.
Так как зарождение и рост УНТ происходит непосредственно на частице катализатора, то управлять характеристиками наноструктур целесообразно не только через состав катализатора, но и через реализацию процесса его получения. Например, через различные методы воздействия на катализатор в процессе его формирования, в частности, химические – промотирование [17–20] и механические методы, направленные на увеличение удельной поверхности каталитической системы. Также известны случаи применения физических методов воздействия в процессе получения катализаторов для гидрирования [21], реакции дейтероводородного обмена [22] и других процессов [23]. Однако в отличие от первых двух методов воздействия, широко эксплуатируемых в процессе формирования катализаторов для синтеза УНТ, третий почти не используется. Следует отметить, что механические и физические методы воздействия на катализатор в отличие от промотирования не требуют изменения его состава и являются наиболее предпочтительными для производителя при расширении номенклатуры выпускаемой нанопродукции. В свою очередь механические методы воздействия на катализатор существенно уступают физическим по эффективности.
Ранее проведенные исследования процесса получения катализатора методом термического разложения неустойчивых соединений продемонстрировали влияние предтермической обработки предшественника катализатора (раствора исходных компонентов) физическим воздействием (электромагнитное, микроволновое излучение, ультразвук и др.) [24–26] и посттермической обработки катализатора [27–29] на его активность/эффективность в процессе ГФХО. Анализ полученных результатов показал, что благодаря обработке катализатора/его предшественника физическими воздействиями для одного состава катализатора можно добиться формирования металлоксидных каталитических систем с разными свойствами.
Использование в промышленном производстве УНТ данного подхода к процессу получения катализатора позволит, не меняя условия ГФХО и состав катализатора, расширить существующую на предприятии номенклатуру нанопродукции.
Из вышесказанного следует, что физическое воздействие на катализатор/его предшественник в процессе его формирования является новым методом управления характеристиками углеродных наноструктурных материалов.
Учитывая возможность управления характеристиками УНТ через реализацию процесса получения катализатора (через пред- и посттермическую обработку катализатора/его предшественника физическим воздействием), удалось представить структуру технологической системы производства УНТ методом ГФХО (рис. 1).
2. Методология создания системы управления. Так как синтез УНТ методом ГФХО довольно сложный многофакторный процесс, то организация гибкого управления характеристиками формируемого нанопродукта представляется возможной с использованием информационно-аналитической поддержки управленческих решений. Создание проблемно-ориентированной информационной системы сопровождения и поддержки принятия решений (СППР), позволяющей без проведения экспериментов определять состав катализатора и условия его обработки физическим воздействием, может способствовать реализации направленного синтеза УНТ.
С целью организации управления характеристиками УНТ через процесс получения катализатора была разработана методология, обеспечивающая эффективное функционирование производственной системы. В соответствии с предложенной методологией добиться формирования катализатора, обеспечивающего направленный синтез УНТ, можно классическим способом – через варьирование состава катализатора (“один состав катализатора – один тип углеродных наноструктур”) или с использованием нового метода управления. Структура предлагаемой в работе методологии создания системы управления представлена на рис. 2.
Реализация нового метода управления характеристиками наноструктур через процесс формирования катализатора с применением физических воздействий требует введения в классическую методику его получения дополнительных стадий. Таким образом, помимо стадий отбора навесок исходных компонентов, их растворения при t < 60°С, термообработки появляются стадии, выполняющие функцию управления (пред- и/или посттермическая обработка катализатора/его предшественника физическим воздействием). Модель процесса получения катализатора методом термического разложения с учетом дополнительных стадий рассмотрена на рис. 3.
Реализация методологии создания системы управления характеристиками УНТ (рис. 2) подразумевает установление критериев управления, факторов, оказывающих влияние на процесс формирования катализатора, а также связей между ними.
Так как процесс формирования катализатора синтеза УНТ с использованием дополнительных стадий является сложным малоизученным процессом, то его целесообразно представить в виде зависимости выходного вектора $\vec {Y}$ от входного $\vec {X}$, управляющего $\vec {U}$ и возмущающего $\vec {F}$ векторов. Формирование катализатора с учетом нового метода управления – это сложно контролируемый процесс, и на данном этапе развития его изучение возможно только с позиций системного анализа.
Так как в рамках работы управление характеристиками углеродных наноструктур осуществляется через реализацию процесса получения катализатора, а он является лишь частью производства УНТ, то его необходимо изучать в совокупности с процессом синтеза УНТ. В связи с чем для определения состава векторов, характеризующих процесс формирования катализатора, была проведена его двухуровневая декомпозиция (декомпозицию процесса ГФХО на поверхности катализатора не рассматриваем). Верхний уровень представляет собой блок, принимающий входной, управляющий и возмущающий векторы параметров и взаимодействующий с блоками нижнего уровня через векторы измерений $\overrightarrow {{{I}_{i}}} $ и координирующие или управляющие векторы $\overrightarrow {{{K}_{i}}} $. Декомпозиция позволила выявить несколько одновременно и взаимосвязано протекающих элементарных процессов. Схема производства УНТ методом ГФХО с декомпозицией процесса получения катализатора представлена на рис. 4.
В результате декомпозиции процесса получения катализатора был установлен состав не только входных, управляющих, возмущающих векторов верхнего уровня, но и векторов измерений, определяющих координирующие или управляющие векторы нижнего уровня. При этом векторы измерений $\overrightarrow {{{I}_{i}}} $ и координирующие или управляющие векторы $\overrightarrow {{{K}_{i}}} $ (рис. 4) имеют следующий вид:
Входной вектор $\vec {X}$ определяется составом катализатора как
где См – состав инертной матрицы; Са – состав активного компонента; Cп – состав промотора.Вектор возмущений $\vec {F}$, характеризующийся факторами, не поддающимися управлению, представляем в виде
Составляющими возмущающего вектора являются: ${{\Delta }}{{t}_{{{\text{о}}{\text{.c}}}}}$ – нестабильность температуры окружающей среды; ${{\Delta }}{{P}_{{{\text{о}}{\text{.c\;}}}}}$ – нестабильность атмосферного давления; ${{\Delta }}{{\vec {C}}_{{{\text{сырья\;}}}}}$ – нестабильность сырья (состава реактивов); ${{\Delta }}{{t}_{{{\text{печи}}}}}$ – градиент температуры в рабочей зоне печи; ${{\Delta }}\tau $ – отклонение от регламентных периодов обработки.
Как показывает практика, влияние первых двух составляющих возмущающего вектора на свойства катализатора несущественно, поэтому в технологическом регламенте обычно эти факторы не указываются.
Несмотря на то, что химические реактивы изготавливают в соответствии с ГОСТ, перед использованием в процессе получения катализатора необходимо проводить их аттестацию. Это вызвано тем, что несоблюдение условий хранения может привести к непригодности реактива. Аттестация реактивов – это важная предподготовка к производственному процессу, позволяющая на начальной стадии избежать формирования катализатора, который обеспечивает синтез нецелевого продукта. Применение в процессе получения катализатора синтеза УНТ разработанных в [30] методик аттестации реактивов позволяет нейтрализовать третью составляющую $\vec {F}.$ С учетом вышесказанного при дальнейшем изучении процесса получения катализатора факторами, характеризующими возмущающий вектор, можно пренебречь.
Так как добиться реализации направленного синтеза УНТ методом ГФХО можно через управление процессом формирования катализатора, основанное не только на варьировании состава катализатора, но и главным образом на его обработке физическими воздействиями, то в соответствии с рис. 3 управляющий вектор $\vec {U}$ характеризуется типом физического воздействия P, временем ${{\tau }_{{{\text{об\;}}}}}$, температурой $~{{t}_{{{\text{об\;}}}}}$ и удельной мощностью обработки катализатора и его предшественника ${{W}_{{{\text{об}}}}}{\text{.}}$ Тогда $\vec {U}$ представим как
Так как катализатор является полупродуктом, который в процессе ГФХО претерпевает изменения, то оценивать эффективность предлагаемого способа управления процессом его формирования целесообразно не по характеристикам полученного катализатора (удельная поверхность (Sуд, м2/г), насыпная плотность (ρ, кг/м3), изменение массы при прокаливании (Δmпрок, г) и др.), а по параметрам, идентифицирующим нанопродукт (рис. 4). В связи с этим выходной вектор процесса получения катализатора $\vec {Y}$ предложено характеризовать параметрами синтезируемых на нем наноструктур, а именно внешним (D, нм) и внутренним (d, нм) диаметрами, удельным выходом (γ, гС/гcat) и степенью дефектности (ID/G) синтезированных УНТ:
При этом степень дефектности УНТ определяется отношением интенсивностей мод, вызванных дефектом симметрии графенового слоя ID и колебаниями атомов углерода в плоскости графенового слоя IG.
Таким образом, упрощенно процесс получения катализатора для синтеза УНТ представляем в виде зависимости выходного $\vec {Y}$ вектора от входного $\vec {X}$, возмущающего $\vec {F}~$ и управляющего $~\vec {U}$ векторов:
На основе информации о составе выходного вектора с использованием метода свертки [31, 32] был сформулирован общий критерий оптимизации процесса получения катализатора, обеспечивающего направленный синтез УНТ, который в общем безразмерном виде запишем как
(2.1)
$M = {{\alpha }_{1}}{{\left( {\frac{{D - {{D}_{0}}}}{{{{D}_{0}}}}} \right)}^{2}} + {{\alpha }_{2}}{{\left( {\frac{{d - {{d}_{0}}}}{{{{d}_{0}}}}} \right)}^{2}} + {{\alpha }_{3}}{{\left( {\frac{{\gamma - {{\gamma }_{0}}}}{{{{\gamma }_{0}}}}} \right)}^{2}} + {{\alpha }_{4}}{{\left( {\frac{{{{I}_{{D/G}}} - {{I}_{{D/G}}}_{{_{0}}}}}{{{{I}_{{D/{{G}_{0}}}}}}}} \right)}^{{2~}}}.$Введение весовых коэффициентов α в (2.1) позволяет установить значимость параметров, характеризующих $\vec {Y}.$ В отсутствие информации о важности критериев значения α выбирают одинаковыми [33], в другом случае значения весовых коэффициентов определяет эксперт – лицо принимающее решение (ЛПР).
3. Постановка задачи. Идеальное совпадение полученных и заданных значений параметров, характеризующих нанопродукт, невозможно. Следовательно, задача управления производственной системой УНТ сводится к достижению их минимального отклонения от заданных значений. Получить решение данной задачи можно путем постановки и решения многокритериальной оптимизационной задачи. С учетом предлагаемой в работе методологии (рис. 2) решение задачи сводится к определению условий, обеспечивающих получение катализатора, способного формировать наноструктуры с характеристиками, значения которых наиболее близки к заданным.
На основе информации о составе $\vec {Y},\vec {X},\vec {U}$ постановка задачи оптимизации условий получения катализатора принимает следующий вид.
Дано: D0, d0, ${{\gamma }_{0}},~{{I}_{{D/{{G}_{0}}}}}.$
Найти:
при которыхОграничения:
(3.3)
$\begin{gathered} C = \overline {1,{{N}_{C}}} ;\quad P = \overline {0,{{N}_{P}}} ;\quad {{\tau }_{{{\text{об}}}}} \in \left[ {{{\tau }_{{{\text{oб\;min}}}}};{{\tau }_{{{\text{об}}~{\text{max}}}}}} \right];\quad {{t}_{{{\text{об}}}}} \in \left[ {{{t}_{{{\text{oб\;min}}}}};{{t}_{{{\text{об\;max}}}}}} \right]; \\ {{W}_{{{\text{об}}}}} \in \left[ {{{W}_{{{\text{oб\;min}}}}};{{W}_{{{\text{об\;max}}}}}} \right], \\ \end{gathered} $Так как управление характеристиками синтезируемых УНТ предложено осуществлять с помощью нового метода, то применение аналитических и экспериментально-аналитических математических моделей для описания этих сложных совмещенных процессов невозможно. На данном этапе из-за их малой изученности целесообразно использовать регрессионную математическую модель, полученную на основе экспериментальных данных.
Для решения оптимизационной задачи необходимо установить функциональные зависимости D, d, ID/G, γ с составом катализатора, типом и условиями физического воздействия на него и его предшественник. При этом состав катализатора и тип физического воздействия являются дискретными величинами, а параметры синтезированных УНТ, характеризующие $\vec {Y}$, определяются условиями физического воздействия непрерывно. В связи с этим целесообразно регрессионные зависимости представить в следующем виде:
(3.4)
$\vec {Y}\left( {C,~P,~{{\tau }_{{{\text{об}}~}}},{{t}_{{{\text{об}}~}}},{{W}_{{{\text{об\;}}}}}} \right) = \left\{ \begin{gathered} D = {{f}_{1}}\left( {{{\tau }_{{{\text{об}}~}}},{{t}_{{{\text{об}}~}}},{{W}_{{{\text{об\;}}}}}} \right),\quad ~d = {{f}_{2}}\left( {{{\tau }_{{{\text{об}}~}}},{{t}_{{{\text{об}}~}}},{{W}_{{{\text{об\;}}}}}} \right), \hfill \\ {{\gamma }} = {{f}_{3}}\left( {{{\tau }_{{{\text{об}}~}}},{{t}_{{{\text{об}}~}}},{{W}_{{{\text{об\;}}}}}} \right),~\quad {{I}_{{D/G}}} = {{f}_{4}}\left( {{{\tau }_{{{\text{об}}~}}},{{t}_{{{\text{об}}~}}},{{W}_{{{\text{об\;}}}}}} \right)\quad {\text{при}}\quad C = 1,\quad P = 1; \hfill \\ D = {{f}_{5}}\left( {{{\tau }_{{{\text{об}}~}}},{{t}_{{{\text{об}}~}}},{{W}_{{{\text{об\;}}}}}} \right),\quad ~d = {{f}_{6}}\left( {{{\tau }_{{{\text{об}}~}}},{{t}_{{{\text{об}}~}}},{{W}_{{{\text{об\;}}}}}} \right), \hfill \\ {{\gamma }} = {{f}_{7}}\left( {{{\tau }_{{{\text{об}}~}}},{{t}_{{{\text{об}}~}}},{{W}_{{{\text{об\;}}}}}} \right),~\quad {{I}_{{D/G}}} = {{f}_{8}}\left( {{{\tau }_{{{\text{об}}~}}},{{t}_{{{\text{об}}~}}},{{W}_{{{\text{об\;}}}}}} \right)~\quad {\text{при}}\quad ~C = 1,\quad P = 2; \hfill \\ ...; \hfill \\ ...\;. \hfill \\ \end{gathered} \right.$Необходимо найти такие варьируемые параметры (3.1), при которых критерий оптимальности (3.2) принимает минимальное значение при выполнении условий (3.3) и (3.4).
4. Решение оптимизационной задачи. Для определения функциональных зависимостей был проведен комплекс экспериментальных исследований, направленных на получение новых знаний о влиянии обработки катализатора физическим воздействием на параметры УНТ, синтезируемых при одинаковых условиях [24, 25, 34]. Анализ управляющих факторов в проведенных экспериментах позволил установить диапазоны их изменения. В частности, тип катализатора C, физического воздействия Р и природа углеродсодержащего газа приняты за дискретные величины, а диапазон изменения значений непрерывных величин ограничен Wоб $ \in $ [0; 2.86 × 104]; ${{\tau }_{{{\text{об}}}}} \in $ ∈ [5; 7200]; ${{t}_{{{\text{об}}}}} \in $ [350; 750].
В работе были исследованы несколько типов катализатора: С = 1 – Ni/0.16MgO; С = 2 – Ni/0.3MgO; С = 3 – Ni/0.5MgO; C = 4 – Fe–0.7Co/2.1Al2O3; C = 5 – Fe–Co/2.1Al2O3; C = 6 – Fe–0.7Co–0.11Мо/2.1Al2O3; С = 7 – Co–0.1Mo/0.36Al2O3–1.14MgO; С = 8 – Co–0.015Mo/0.8Al2O3. А также изучены следующие типы физического воздействия на исследуемые катализаторы: Р = 0 – отсутствие обработки; Р = 1 – предтермическая обработка ультразвуком; Р = 2 – предтермическая обработка микроволновым излучением; Р = 3 – предтермическая обработка электромагнитным полем; Р = 4 – посттермическая обработка высокими температурами.
Обработка с использованием программных продуктов Maple14, TableCurve 2D v5.01 и TableCurve 3D v4.0. данных, полученных в ходе экспериментов, позволила установить характер функциональных зависимостей и определить вид математической модели. Фрагмент модели для трех типов катализатора и способов воздействия представлен ниже:
Такой подход к выявлению математических зависимостей параметров, характеризующих $\overrightarrow {Y,~} $ от управляющих факторов реализует принцип открытости и позволяет вносить в модель информацию о новых способах воздействия на новые составы катализаторов.
Так как оптимизационная задача является классической задачей поиска минимума функции многих переменных с ограничениями, то определение непрерывных величин τоб, Wоб, tоб осуществлялось универсальным градиентным методом при переборе дискретных переменных С, Р с помощью алгоритмического языка Python. Проведенные расчеты показали, что градиентные методы не гарантируют нахождение адекватных решений, так как локальные минимумы целевой функции могут наблюдаться на границах. Примеры подобных расчетов приведены на рис. 5.
Рис. 5.
Зависимость критерия оптимизации от: a – времени, с; б – времени и температуры обработки, мин
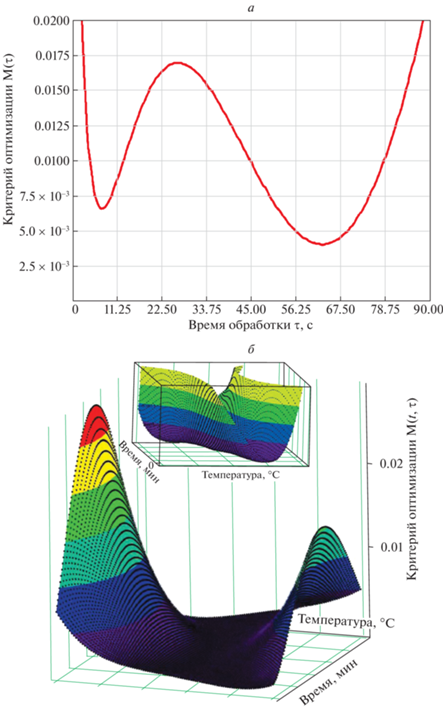
Также данный метод оказался неподходящим при работе напрямую с дискретными величинами и функциями, имеющими разрывы. Замена его безградиентным методом сканирования (сравнение значений целевой функции осуществляли в узлах сетки значений аргументов) [35, 36] позволила унифицировать расчетный алгоритм, оперировать дискретными величинами, производить расчет для функций, имеющих разрывы. При этом вид целевой функции упрощается за счет перехода от возведения в квадрат разности заданных и полученных фактически значений параметров синтезированных УНТ к модулям. Это привело к повышению точности и скорости нахождения решения. При условии, что входящие в состав выходного вектора значения параметров нормированы в диапазоне [0, 1], выражение (3.2) принимает вид
(4.1)
$~ + \,{{\alpha }_{\gamma }}\left| {\gamma \left( {C,~P,{{\tau }_{{{\text{об\;}}}}},{{t}_{{{\text{об\;}}}}},{{W}_{{{\text{об\;}}}}}} \right) - {{\gamma }_{0}}} \right| + {{\alpha }_{{{{I}_{{D/G}}}}}}\left| {{{I}_{{D/G}}}\left( {C,~P,{{\tau }_{{{\text{об\;}}}}},{{t}_{{{\text{об\;}}}}},~{{W}_{{{\text{об\;}}}}}} \right) - {{I}_{{D/G0}}}} \right| \to {\mathbf{min}}.$Согласно выбранному методу, решение оптимизационной задачи находили итерационным методом сканирования непрерывных функций с переменным шагом hm. С учетом имеющихся ограничений
(4.2)
$~{{\tau }_{i}} = {{\tau }_{{об}}}_{{{\text{min}}}} + i \cdot {{h}_{m}};\quad {{t}_{j}} = {{t}_{{{\text{обmin}}}}} + j \cdot {{h}_{m}};\quad {{W}_{k}} = {{W}_{{{\text{обmin}}}}} + k \cdot {{h}_{m}};\quad {{h}_{1}} = {\text{ }}1{\text{/}}z,$(4.3)
$ + \,{{\alpha }_{\gamma }}\left| {{{\gamma }_{{c,p}}}\left( {{{\tau }_{i}},~{{t}_{j}},{{W}_{k}}} \right) - {{\gamma }_{0}}~} \right| + {{\alpha }_{{{{I}_{{\frac{D}{G}}}}}}}\left| {{{I}_{{{{{\frac{D}{G}}}_{{c,p}}}}}}\left( {{{\tau }_{i}},~{{t}_{j}},{{W}_{k}}} \right) - {{I}_{{{{{\frac{D}{G}}}_{0}}}}}} \right|,$Здесь ɛ – погрешность расчета, hm – шаг на m-й итерации; m – номер итерации, $~\tau _{i}^{*}$, $t_{j}^{*},~W_{k}^{*}$ – значения времени, температуры и удельной мощности обработки физическим воздействием, при которых целевая функция принимает минимальное значение.
В случае, когда условие (4.4) не выполнялось, для непрерывных величин уменьшали область поиска и уточняли решения в соответствии с уравнениями
(4.5)
$\left\{ \begin{gathered} {{\tau }_{{{\text{об\;min}}}}} = \tau _{i}^{*} - \left( {\frac{{{{h}_{m}}}}{2}} \right);\quad i \ne 0\quad {\text{или}}\quad i \ne z{{,}_{{\text{\;}}}} \hfill \\ {{\tau }_{{{\text{об\;min}}}}} = \tau _{i}^{*} - {{h}_{m}};\quad i = z, \hfill \\ {{t}_{{{\text{об\;min}}}}} = t_{j}^{*} - \left( {\frac{{{{h}_{m}}}}{2}} \right);\quad j \ne 0~\quad {\text{или}}\quad j \ne z, \hfill \\ {{t}_{{{\text{об\;min}}}}} = t_{j}^{*} - {{h}_{m}};\quad j = z, \hfill \\ {{W}_{{{\text{об\;min}}}}} = W_{k}^{*} - \left( {\frac{{{{h}_{m}}}}{2}} \right);\quad k \ne 0~\quad {\text{или}}\quad k \ne z, \hfill \\ {{W}_{{{\text{об\;min}}}}} = W_{k}^{*} - {{h}_{m}};\quad k = z. \hfill \\ \end{gathered} \right.$Для новой области определяли новое значение шага по формуле
Расчет повторяли до тех пор, пока не выполнится условие (4.4), найденные значения $\tau _{i}^{*},~t_{j}^{*},W_{k}^{*},~C,~P$ принимали за решение оптимизационной задачи.
Таким образом, решение оптимизационной задачи безградиентным методом сводится к сканированию непрерывных функций с переменным шагом для нахождения таких комбинаций ${{\tau }_{{{\text{об}}}}},{{t}_{{{\text{об}}}}},~{{W}_{{{\text{об}}}}},~$ при которых значение целевой функции управления характеристиками УНТ через обработку катализатора физическим воздействием (4.1) примет минимальное значение.
На базе предложенной методологии создания системы управления характеристиками УНТ была разработана СППР, состоящая из блоков поддержки принятия решения (на базе Borland Delphi 7) и сопровождения производства катализатора (на базе SupaSoft 1.10). Блок сопровождения позволяет систематизировать и хранить информацию о количествах, физико-химических характеристиках исходного сырья и катализатора на всех стадиях производства, а также параметрах синтезированных наноструктур.
В основе блока поддержки принятия решения лежит модуль поиска минимума целевой функции, который перебирает все возможные варианты соотношений “Тип катализатора” – “Тип воздействия” – “Тип газа” и для каждого варианта из базы данных определяет набор зависимостей D = fD (…); d = fd (…); γ = fγ (…); D/G = fD/G (…) в виде аппроксимирующих функций от τоб, tоб и Wоб. Блок поддержки принятия решения, взаимодействуя с ЛПР через пользовательский интерфейс, по заданным характеристикам УНТ определяет оптимальное сочетание состава катализатора, типа физического воздействия и режимов его обработки, позволяющее получать каталитическую систему, которая обеспечивает реализацию направленного синтеза наноструктур.
Апробация созданной СППР позволила без проведения экспериментов определить состав и условия реализации процесса получения катализатора, обеспечивающего синтез многослойных УНТ диаметром 20 нм и ID/G не более 1.0 (активность/эффективность катализатора должна быть не менее 12.0 гС/гcat). Вид рабочего окна модуля рекомендаций с найденными вариантами условий формирования катализатора, прогнозирующими синтез наноструктур с характеристиками, близкими к заданным, приведен на рис. 6.
Согласно найденным условиям (первый вариант является оптимальным), формирование УНТ с заданными характеристиками может обеспечить Ni/MgO-катализатор, полученный с использованием предтермической обработки его предшественника ультразвуком в течение 10 с (удельная мощность воздействия 2.86 × 104 Вт/см3). Реализация предложенных информационной системой оптимальных условий приготовления катализатора позволила сформировать Ni/MgO-каталитическую систему, способную в процессе ГФХО (углеродсодержащее сырье – пропан-бутановая смесь) синтезировать многослойные нанотрубки диаметром 10–30 нм, ID/G = 0.7 (активность/эффективность катализатора при этом составила ~17.4 гС/гcat).
Использование катализатора (второй вариант, предложенный СППР, рис. 6), сформированного в результате предтермической обработки его предшественника магнитным воздействием в течение 30 с, в процессе ГФХО приводит к синтезу УНТ диаметром 10–40 нм и степенью дефектности – 0.96. Несмотря на то, что данный катализатор способствует образованию УНТ с характеристиками, близкими к заданным, наиболее приемлемым для производителя будет предыдущий вариант, так как обеспечивает формирование наиболее активной/эффективной его формы (высокий γ, гС/гcat).
Реализация в лаборатории методики получения Co-Mo/Al2O3-MgO-катализатора, согласно выработанным рекомендациям СППР, способствует формированию каталитической системы, обеспечивающей синтез УНТ диаметром 8–15 нм, что соответствует прогнозируемым системой параметрам наноструктур (D0= 9 нм). Результаты тестирования катализаторов, приготовленных согласно рекомендациям созданной СППР, частично представлены в таблице.
Таблица.
Результаты тестирования СППР
Параметры наноструктур от заказчика | Результат расчета | Фактические параметры наноструктур | Морфология синтези-рованных УНТ | |
---|---|---|---|---|
Состав и условия получения катализатора | Ожидаемые характеристики наноструктур | |||
D0 = 20 нм; ID/G0 = 1.0; γ0 = 12.0 гС/гcat | Ni/MgO, предтермическая обработка ультразвуковым воздействием в течение 10 с | D = 22 нм; ID/G = 0.92; γ = 18.2 гС/гcat | D = 10–30 нм; ID/G = 0.7; γ = 17.4 гС/гcat | Рис. 7, a |
Ni/MgO, предтермическая обработка магнитным воздействием в течение 30 с | D = 25 нм; γ = 13.3 гС/гcat; ID/G = 0.98 | D = 10–40 нм; γ =14.3 гС/гcat; ID/G = 0.96 | Рис. 7, б | |
D0 = 9.0 нм; d0 = 5.0 нм; γ0 = 11 гС/гcat, D/G0 = 1.2 | Co-Mo/Al2O3-MgO, посттермическая обработка прокаливанием в течение часа при 600°С | D = 9.5 нм, d = 6.7 нм, γ = 15.1 гС/гcatID/G = 1.0 | D = 8–15 нм, d = 5.0–8 нм, γ = 13.5 гС/гcatID/G = 1.05 | Рис. 7, в |
Морфология наноструктур, синтезированных на рассмотренных в таблице катализаторах, приведена на рис. 7.
Рис. 7.
Морфология наноструктур, синтезированных на катализаторе обработанном: a – ультразвуком; б – магнитным полем; в – прокаливанием
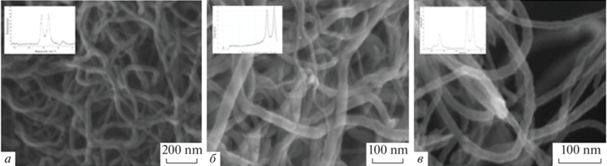
Синтез на поверхности катализатора, приготовленного с учетом рекомендаций СППР (состав, условиях формирования), наноструктур с характеристиками, значения которых близки к заданным, подтверждает эффективность разработанной информационной системы.
В случае, когда предложенный СППР оптимальный вариант не устраивает ЛПР (не выгоден для производителя в данный момент), оно может рассмотреть другие найденные варианты реализации процесса получения катализатора, позволяющие синтезировать УНТ с характеристиками, близкими к заданным. При этом нет необходимости делать новый расчет, так как блок поддержки принятия решения (модуль рекомендаций) все найденные варианты сортирует по возрастанию значения целевой функции (рис. 6). Алгоритм поддержки принятия решений, реализованный с использованием созданной СППР в производстве УНТ, представлен на рис. 8.
Таким образом, блок поддержки принятия решений (модуль рекомендаций) является базовым элементом системы управления характеристиками УНТ. Его основная задача – упростить принятие решений ЛПР относительно условий формирования каталитической системы, обеспечивающей направленный синтез УНТ. Это становится возможным за счет интеграции информации от всех структурных элементов технологической системы производства наноструктур.
Разработанная методология создания системы управления характеристиками УНТ позволила создать СППР, которая дает возможность ЛПР, зная требования заказчика к наноструктурам, в сжатые сроки определить условия формирования катализатора, обеспечивающего синтез целевого нанопродукта. Применение СППР в производстве УНТ (ООО “НаноТехЦентр”, г. Тамбов) снижает нагрузку на ЛПР. Информация, полученная от данной информационной системы, была использована при проектировании опытно-промышленного участка производства Co–Mo/Al2O3–MgO-катализатора производительностью до 245 кг/год для АО “ЗАВКОМ” (г. Тамбов).
Заключение. Проведенные исследования производства УНТ методом ГФХО позволили разработать методологию, отличающуюся новым методом управления характеристиками синтезируемых УНТ. Метод заключается в пред- и/или посттермической обработке катализатора/его предшественника физическим воздействием на стадии его формирования. Полученная в результате экспериментального исследования информация создала предпосылки для реализации направленного синтеза наноструктур и расширения их номенклатуры без изменения условий синтеза. На базе данной методологии была создана СППР при производстве катализатора, позволяющая организовать эффективное управление параметрами УНТ в процессе их синтеза.
Список литературы
Kim K.J., Huh M.-Y., Kim W.-S., Song J.-H., Lee H.S., Kim J.-Y., Lee S.-R., Seo W.S., Yang S.-M., Park Y.S. The Effect of Carbon Nanotube Diameter on the Electrical, Thermal, and Mechanical Properties of Polymer Composites // Carbon Letters. 2018. V. 26. P. 95–101.
Рухов А.В. Основные процессы синтеза углеродных нанотрубок методом газофазного химического осаждения // Изв. вузов. Химия и хим. технология. 2013. Т. 56. № 9. С. 117–121.
Раков Э.Г. Нанотрубки и фуллерены. М.: Логос, 2006. 376 с.
Cheng Yi., Chen K., Sun H., Zhang Y, Tao F. Data and Knowledge Mining with Big Data Towards Smart Production // J. Industrial Information Integration. 2018. V. 9. P. 1–13.
Guo Yu., Wang N., Xu Z., Wu K. The Internet of Things-Based Decision Support System for Information Processing in Intelligent Manufacturing Using Data Mining Technology // Mechanical Systems and Signal Processing. 2020. V. 142 (3).
Abbaslou R., Soltan J., Dalai A. The Effects of Carbon Concentration in the Precursor Gas on the Quality and Quantity of Carbon Nanotubes Synthesized by CVD Method // Applied Catalysis A: General. 2010. V. 372 (2). P. 147–152.
Буянов Р.А., Чесноков В.В. О процессах, происходящих в металлических частицах при каталитическом разложении на них углеводородов по механизму карбидного цикла // Химия в интересах устойчивого развития. 2005. Т. 13. С. 37–40.
Дмитриев А.К., Мальцев П.А. Основы теории построения и контроля сложных систем. Л.: Энергоатомиздат, 1988. 192 с.
Гришко А.К., Юрков Н.К., Кочегаров И.И. Методология управления качеством сложных систем // Тр. Междунар. симпоз. “Надежность и качество”. Пенза, 2014. № 2. С. 377–379.
Мищенко С.В., Ткачев А.Г. Углеродные наноматериалы. Производство, свойства, применение. М.: Машиностроение, 2008. 320 с.
Kumar M., Ando Y. Chemical Vapor Deposition of Carbon Nanotubes: A Review on Growth Mechanism and Mass Production // J. Nanoscience and Nanotechnology. 2010. V. 10(6). P. 3739–3758.
Кульметьева В.Б., Мальцев И.А. Влияние условий каталитического пиролиза паров этанола на характеристики углеродных нанотрубок // Современные проблемы науки и образования. 2014. № 6. С. 123–123.
Magrez A., Seo J.W., Smajda R., Mionic M., Forro L. Catalytic CVD Synthesis of Carbon Nanotubes: Towards High Yield and Low Temperature Growth // Materials. 2010. V. 3 (11). P. 4871–4891.
Fiawoo M., Bonnot A., Amara H., Bichara C., Thibault-Pénisson J., Loiseau A. Evidence of Correlation Between Catalyst Particles and the Single-Wall Carbon Nanotube Diameter: A First Step Towards Chirality Control // Physical Review Letters. 2012. V. 108 (19).
Chen S.Y., Miao H.Y., Lue J.T., Ouyang M.S. Fabrication and Field Emission Property Studies of Multiwall Carbon Nanotubes // J. Physics D Applied Physics. 2003. V. 37 (2). P. 273–279.
Cheung C.L., Hafner J.H., Lieber C.M. Carbon Nanotube Atomic Force Microscopy Tips: Direct Growth by Chemical Vapor Deposition and Application to High-Resolution imaging // Proc. of the National Academy of Sciences. 2000. V. 97 (8). P. 3809–3813.
Chesnokov V.V., Zaikovskii V.I., Chichkan A.S., Buyanov R.A. The Role of Molybdenum in Fe–Mo–Al2O3 Catalyst for Synthesis of Multiwalled Carbon Nanotubes From Butadiene-1,3 // Applied Catalysis A: General. 2009. V. 363 (1). P. 86–92.
Wang G., Wang J., Wang H., Bai J. Preparation and Evaluation of Molybdenum Modified Fe/MgO Catalysts for the Production of Single-Walled Carbon Nanotubes and Hydrogen-Rich Gas by Ethanol Decomposition // J. Environmental Chemical Engineering. 2014. V. 2 (3). P. 1588–1595.
Awadallah A.E., Aboul-Enein A., Azab M., Abdel-Monem Y.K. Influence of Mo or Cu Doping in Fe/MgO Catalyst for Synthesis Of Single-Walled Carbon Nanotubes by Catalytic Chemical Vapor Deposition of Methane // Fullerenes, Nanotubes and Carbon Nanostructures. 2017. V. 25 (4). P. 256–264.
Gu B., Zhou Ch., He Sh., Moldovan S., Chernavskii P.A., Ordomsky V.V., Khodakov A.Y. et al. Size and Promoter Effects on Iron Nanoparticles Confined in Carbon Nanotubes and Their Catalytic Performance in Light Olefin Synthesis From Syngas // Catalysis Today. 2019. V. 357. P. 203–213.
Сульман М. Г. Влияние ультразвука на каталитические процессы // Успехи химии. 2000. Т. 69. № 2. С. 178–191.
Шелимов Б.Н. Нетрадиционные методы активации оксидных катализаторов с нанесенными ионами переходных металлов // Российский химический журнал. 2000. Т.44. № 1. С. 57–70.
Azarhoosh M., Halladj R., Askari S., Aghaeinejad-Meybodi A. Performance Analysis of Ultrasound-Assisted Synthesized Nano-Hierarchical SAPO-34 Catalyst in the Methanol-to-lights-olefins Process via Artificial Intelligence Methods // Ultrasonics Sonochemistry. 2019. V. 58.
Burakova E.A., Galunin E.V., Rukhov A.V., Memetov N.R., Tkachev A.G. Effect of Ultrasound on a Mixed Oxide-Based Catalyst in the Synthesis of Carbon Nanostructured Materials // Research on Chemical Intermediates. 2016. V. 42 (9). P. 7045–7055.
Burakova E.A., Dyachkova T.P., Rukhov A.V., Tugolukov E.N., Galunin E.V., Tkachev A.G., Basheer A.A., Imran Al. Novel and Economic Method of Carbon Nanotubes Synthesis on a Nickel Magnesium Oxide Catalyst Using Microwave Radiation // J. of Molecular Liquids. 2018. V. 253. P. 340–346.
Каримов О.Х., Даминев Р.Р., Касьянова Л.З., Каримов Э.Х. Применение СВЧ-излучения при приготовлении металлоксидных катализаторов // Фундаментальные исследования. 2013. № 4. С. 801–805.
Liu W.W., Adam T., Azizan A., Chai S.P., Mohamed A.R., Hashim U. A Study on the Effect of Calcination Temperature on the Graphitization of Carbon Nanotubes Synthesized by the Decomposition of Methane // Advanced Materials Research. 2014. V. 832. P. 56–61.
Akbarzadeh O., Zabidi N.A.M., Hamizi N.A., Wahab Y.A., Merican Z.M.A., Yehya W.A., Akhter S., Shalauddin M., Rasouli E., Johan M.R. Effect of pH, Acid and Thermal Treatment Conditions on Co/CNT Catalyst Performance in Fischer-Tropsch Reaction // Symmetry. 2019. V. 11 (1). P. 50–69.
Pourkhalil M. Effect Calcination Temperature and Calcination Time on the Catalytic Activity of Multi-Walled Carbon Nanotube for Low Temperature Selective Catalytic Reduction // J. Applied Researches in Chemistry. 2017. V. 11 (1). P. 67–77.
Dyachkova T., Besperstova G., Burakova E., Rukhov A., Tugolukov E. Peculiarities of Obtaining a Catalyst for the Synthesis of Nanostructured Carbon Materials via Thermal Decomposition // AIP Conference Proceedings. 2017. V. 1899 (1).
Ногин В.Д. Линейная свертка в многокритериальной оптимизации // Искусственный интеллект и принятие решений. 2014. № 4. С. 73–82.
Новикова Н.М., Поспелова И.И., Зенюков А.И. Метод сверток в многокритериальных задачах с неопределенностью // Изв. РАН. ТиСУ. 2017. № 5. С. 27–45.
Машунин К.Ю., Машунин Ю.К. Векторная оптимизация с равнозначными и приоритетными критериями // Изв. РАН. ТиСУ. 2017. № 6. С. 80–99.
Буракова Е.А., Бесперстова Г.С., Неверова М.А., Ткачев А.Г., Чапаксов Н.А., Рухов А.В. Влияние термообработки на свойства катализатора синтеза углеродных нанотрубок // Вестн. Воронежск. гос. ун-та инженерных технологий. 2020. Т. 82. № 1 (83). С. 237–246.
Карпушкин С.В. Теория принятия проектных решений. Учеб. пособие. Тамбов: ТГТУ, 2015. 86 с.
Бояринов А.И., Кафаров В.В. Методы оптимизации в химической технологии. М.: Химия, 1975. 576 с.
Дополнительные материалы отсутствуют.
Инструменты
Известия РАН. Теория и системы управления