Теплоэнергетика, 2021, № 10, стр. 53-62
Оптимизация режимов работы установок ультрафильтрации
А. А. Пантелеев a, b, Ан. А. Пантелеев c, В. В. Бобинкин b, С. Е. Лысенко d, В. Б. Смирнов b, *
a Национальный исследовательский университет “Московский энергетический институт”
111250 Москва, Красноказарменная ул., д. 14, Россия
b Научно-производственная компания “Медиана-Фильтр”
119270 Москва, Лужнецкая наб., д. 2/4, стр. 17, Россия
c Московский физико-технический институт (Национальный исследовательский университет)
141701 Московская обл., г. Долгопрудный, Институтский пер., д. 9, Россия
d Всероссийский теплотехнический институт
115280 Москва, Автозаводская ул., д. 14, Россия
* E-mail: smirnov@mediana-filter.ru
Поступила в редакцию 20.01.2021
После доработки 11.02.2021
Принята к публикации 17.02.2021
Аннотация
Рассмотрены параметры, влияющие на эффективность очистки ультрафильтрационных мембран. Предложена простая гидравлическая модель режима обратной промывки. Полученные для расчета времени обратной промывки формулы позволили оптимизировать этот процесс. Представлены результаты исследования режимов работы установок ультрафильтрации. Для эффективного подбора режимов фильтрования, прямой и обратной промывок авторы предлагают применять лабораторные ультрафильтрационные модули и разработанную ими методику расчета. Проиллюстрированы гидравлическая модель режима обратной промывки и феноменологическая модель образования отложений внутри волокна. Приведены формулы для расчета времени обратной промывки, с помощью которых возможно оптимизировать этот процесс и снизить эксплуатационные затраты. Показано, что для анализа распределения отложений внутри волокна мембран могут быть использованы простые модели процесса фильтрования, одна из которых представлена в данной работе. Продемонстрировано, что при тупиковом режиме фильтрования значительная часть отложений собирается в центральной части волокна. Естественным способом борьбы с этими отложениями является организация тангенциального режима фильтрования. Предложено удобное для применения на практике математическое выражение для расчета индекса Ланжелье через измеряемые параметры качества воды. Индекс Ланжелье полезен для обоснования необходимости кислотных промывок или отсутствия такой необходимости. Показано, что при существенно нестабильной исходной воде использование перед установкой ультрафильтрации предварительного фильтрования на зернистой загрузке приводит к стабилизации качества и деаэрации обрабатываемой воды. Также показано, что при применении кислотных и щелочных очисток на основе комплексонсодержащих реагентов с периодичностью применения 2 раза в год можно существенно повысить стабильность работы ультрафильтрационной установки. Даны практические рекомендации для организации режима ультрафильтрации, которые были реализованы на водоподготовительной установке Новочеркасской ГРЭС.
Ультрафильтрация является оптимальным методом предварительной подготовки поверхностных вод для их очистки на установках обратного осмоса [1–5]. Она обеспечивает эффективное удаление из воды органических соединений с отсечкой 100–150 кДа, общей степенью очистки 25–60% и коллоидным индексом в фильтрате КИ15 = 1–3. При рейтинге фильтрации 20–50 нм возможно удалять из воды все взвешенные частицы и бо́льшую часть коллоидных частиц. Благодаря высокому качеству фильтрата установок ультрафильтрации (ультрафильтрационных установок – УФУ) обеспечиваются минимальные эксплуатационные затраты для установок обратного осмоса: снижаются степень загрязнения мембранного блока, перепады давления на нем и, соответственно, энергозатраты, уменьшаются расходы на реагенты для химической очистки. Существенно увеличивается срок службы обратноосмотических мембранных элементов. Пятилетний срок их эксплуатации в схемах с использованием УФУ в настоящее время является стандартом. Известны случаи, когда мембранные элементы в составе установок с непрерывным циклом производства служат уже более 10 лет. Такие результаты могут быть достигнуты при надежной и стабильной работе УФУ. Оптимизация режимов работы УФУ является важной и актуальной задачей.
ОСОБЕННОСТИ РАБОТЫ УСТАНОВОК УЛЬТРАФИЛЬТРАЦИИ
Принципиальная схема УФУ представлена на рис. 1. Характерными особенностями ее работы являются:
Рис. 1.
Принципиальная схема установки ультрафильтрации. 1, 2, 3 – насосы подачи исходной воды, воды при обратной промывке и раствора коагулянта; 4 – мембранный блок; 5–7 – насосы подачи растворов HCl, NaOH и NaOCl
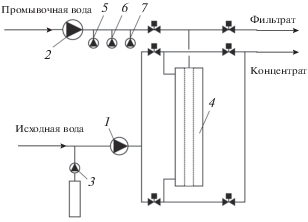
большое число переходных процессов, высокая нагрузка на запорно-регулирующую арматуру;
малая длительность фильтроцикла (20–60 мин в зависимости от качества исходной воды);
тангенциальный и тупиковый режимы фильтрования с рециркуляцией и без нее;
различные режимы промывок мембран: прямая, прямая водовоздушная, обратная;
химические очистки мембран: непродолжительная химическая очистка в сочетании с обратной и прямой промывками (CEB – Chemical Enhanced Backwash), продолжительная химическая очистка при сервисном обслуживании установки (CIP – Clean in Place);
сочетание режима фильтрования с коагуляцией;
низкая прочность фильтрующего материала, что вызывает необходимость проверки наличия механических повреждений;
длительность промывок сравнима с временем выхода насоса промывочной воды на рабочий режим;
большое количество рабочих операций (фильтрование, промывки, химические очистки, контроль повреждений фильтрующей мембраны).
Эти особенности делают технологию ультрафильтрации одной из самых сложных среди применяемых в водоподготовительных системах. Обеспечение оптимальных режимов работы УФУ является залогом надежности, технологической и экономической эффективности. В России более половины промышленных УФУ размещено на ТЭС. Почти во всех этих установках используются ультрафильтрационные модули с волокнами на основе полиэфирсульфона.
МЕХАНИЧЕСКОЕ УДАЛЕНИЕ ЗАГРЯЗНЕНИЙ С ПОВЕРХНОСТИ МЕМБРАННЫХ ЭЛЕМЕНТОВ
В процессе работы на поверхности мембраны и внутри ее пор формируются отложения (рис. 2). Для удаления поверхностных отложений используется прямая промывка, эффективность которой обеспечивается значительным градиентом скоростей промывочной воды или турбулентным режимом. Мерой турбулентности принято считать число Рейнольдса ${\text{Re}} = ~{{\rho {v}d} \mathord{\left/ {\vphantom {{\rho {v}d} \mu }} \right. \kern-0em} \mu }$ (здесь v – средняя скорость потока воды; d – гидравлический диаметр; ρ, $\mu $ – плотность и динамический коэффициент вязкости воды).
Скорость потока воды при прямой промывке vп.п рассчитывают по формуле
(1)
${{{v}}_{{{\text{п}}{\text{.п}}}}} = {{{{Q}_{{{\text{п}}{\text{.п}}}}}} \mathord{\left/ {\vphantom {{{{Q}_{{{\text{п}}{\text{.п}}}}}} S}} \right. \kern-0em} S},$Информацию о числе волокон мембранного модуля можно запросить у его производителя, посчитать на спиле корпуса мембраны или рассчитать по формуле
где Sф – площадь фильтрующей поверхности; lв – рабочая длина волокна.Выражение для расчета площади поперечного сечения волокон выглядит следующим образом:
При оптимизации режима прямой промывки необходимо использовать ее продолжительность τп.п и расход промывочной воды. Полное время прямой промывки Тп.п вычисляют по формуле
Для удаления загрязнений из пор проводится обратная промывка. Форма зависимости расхода промывочной воды Qо.п от продолжительности процесса (рис. 3) обусловлена особенностью работы насоса с частотно-регулируемым приводом, которому требуется время на разгон для достижения номинальной производительности и торможение при отключении.
Рис. 3.
Зависимость расхода воды от времени при обратной промывке. τн 1 – время достижения номинального расхода воды на промывку; τн 2 – время снижения расхода воды до прекращения промывки; τо.п – продолжительность обратной промывки при номинальном расходе воды
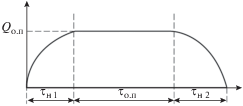
Расход воды при обратной промывке определяется по формуле
где Jо.п – удельный расход воды при обратной промывке.Удельный расход преобразуется в линейную скорость vо.п по выражению
(3)
${{{v}}_{{{\text{о}}{\text{.п}}}}} = {{\theta }_{{J{v}}}}{{J}_{{{\text{о}}{\text{.п}}}}}{\text{,}}$При часто рекомендуемом удельном расходе обратной промывки Jо.п = 250 дм3/(м2 · ч) линейная скорость составляет vо.п ≈ 70 мкм/с. Скорость воды в порах волокна vп определяется соотношением vп = vо.п/ε (здесь ε – пористость мембраны, обычно ε = 0.3–0.4) и равна примерно 200 мкм/с. Это означает, что время прохождения воды через стенку волокна (по поре) толщиной δ ≈ 200 мкм составляет примерно 1 с, а через плотный фильтрующий слой – около 0.1 с.
Для выделенного цилиндрического объема в волокне характерно выражение
(4)
${\text{d}}{{Q}_{{{\text{вх}}{\text{.в }}}}} = \pi {{d}_{{\text{в}}}}{{{v}}_{{{\text{о}}{\text{.п}}}}}{\text{d}}z{\text{,}}$Расход воды, выходящей из канала волокна, Qвых.в является дифференциальной разностью между расходами воды с торцов цилиндра
(5)
$\begin{gathered} {\text{d}}{{Q}_{{{\text{вых}}{\text{.в}}}}} = Q\left( {z + {\text{d}}z} \right) - Q\left( z \right) = {\text{0}}{\text{.25}}\pi d_{{\text{в}}}^{{\text{2}}} \times \\ \times \,\,\left[ {{{{v}}_{{\text{в}}}}\left( {z + {\text{d}}z} \right) - {{{v}}_{{\text{в}}}}\left( z \right)} \right] \approx {\text{0}}{\text{.25}}\pi d_{{\text{в}}}^{{\text{2}}}\frac{{{\text{d}}{{{v}}_{{\text{в}}}}}}{{{\text{d}}z}}~{\text{d}}z. \\ \end{gathered} $После приравнивания выражений (4) и (5) можно получить
(6)
$\frac{{{\text{d}}{{{v}}_{{\text{в}}}}}}{{{\text{d}}z}} = {{{\text{4}}{{{v}}_{{{\text{о}}{\text{.п}}}}}} \mathord{\left/ {\vphantom {{{\text{4}}{{{v}}_{{{\text{о}}{\text{.п}}}}}} {{{d}_{{\text{в}}}}}}} \right. \kern-0em} {{{d}_{{\text{в}}}}}}.$Интегрирование (6) при условии vв (0) = 0 дает выражение
(7)
${{{v}}_{{\text{в}}}}\left( z \right) = {{{\text{4}}{{{v}}_{{{\text{о}}{\text{.п}}}}}z} \mathord{\left/ {\vphantom {{{\text{4}}{{{v}}_{{{\text{о}}{\text{.п}}}}}z} {{{d}_{{\text{в}}}}}}} \right. \kern-0em} {{{d}_{{\text{в}}}}}}.$Формула для расчета времени вытеснения воды из волокна τв выглядит следующим образом:
(8)
${{\tau }_{{\text{в}}}} \approx ~\int\limits_{{{d}_{{\text{в}}}}}^{{{l}_{{\text{в}}}}} {{{{\text{d}}z} \mathord{\left/ {\vphantom {{{\text{d}}z} {{{{v}}_{{\text{в}}}}}}} \right. \kern-0em} {{{{v}}_{{\text{в}}}}}}\left( z \right)} = \frac{{{{d}_{{\text{в}}}}}}{{{\text{4}}{{{v}}_{{{\text{о}}{\text{.п}}}}}}}{\text{ln}}\left( {{{{{l}_{{\text{в}}}}} \mathord{\left/ {\vphantom {{{{l}_{{\text{в}}}}} {{{d}_{{\text{в}}}}}}} \right. \kern-0em} {{{d}_{{\text{в}}}}}}} \right).$Для практического применения можно использовать формулу
(9)
${{\tau }_{{\text{в}}}} \approx {{{{d}_{{\text{в}}}}{\text{ln}}\left( {{{{{l}_{{\text{в}}}}} \mathord{\left/ {\vphantom {{{{l}_{{\text{в}}}}} {{{d}_{{\text{в}}}}}}} \right. \kern-0em} {{{d}_{{\text{в}}}}}}} \right)} \mathord{\left/ {\vphantom {{{{d}_{{\text{в}}}}{\text{ln}}\left( {{{{{l}_{{\text{в}}}}} \mathord{\left/ {\vphantom {{{{l}_{{\text{в}}}}} {{{d}_{{\text{в}}}}}}} \right. \kern-0em} {{{d}_{{\text{в}}}}}}} \right)} {\left( {{\text{4}}{{\theta }_{{J{v}}}}{{J}_{{{\text{о}}{\text{.п}}}}}} \right)}}} \right. \kern-0em} {\left( {{\text{4}}{{\theta }_{{J{v}}}}{{J}_{{{\text{о}}{\text{.п}}}}}} \right)}}.$При dв = 0.9 мм, lв = 1.5 м скорость потока воды на выходе из торца мембранного модуля составляет ${{{v}}_{{\text{в}}}} = {{{\text{4}}{{{v}}_{{{\text{о}}{\text{.п}}}}}{{l}_{{\text{в}}}}} \mathord{\left/ {\vphantom {{{\text{4}}{{{v}}_{{{\text{о}}{\text{.п}}}}}{{l}_{{\text{в}}}}} {{{d}_{{\text{в}}}}}}} \right. \kern-0em} {{{d}_{{\text{в}}}}}} \approx {\text{6}}{\text{.7}} \times {\text{1}}{{{\text{0}}}^{{\text{3}}}}{{{v}}_{{{\text{о}}{\text{.п}}}}}$ и при vо.п = = 70 мкм/с равна vв ≈ 0.47 м/с, необходимое время вытеснения воды τв ≈ 24 с.
Полное время обратной промывки То.п определяется суммой
(10)
$\begin{gathered} {{Т}_{{{\text{о}}{\text{.п}}}}} = {{\tau }_{{\text{п}}}} + {{{{\tau }}}_{{\text{в}}}}~ + {{\tau }_{{{\text{п}}{\text{.оч}}}}} + {{\tau }_{{{\text{н}}\,\,{\text{1}}}}} + {{\tau }_{{{\text{н}}\,\,{\text{2}}}}} = \\ = {{\tau }_{{{\text{о}}{\text{.п}}}}} + {{\tau }_{{{\text{н}}\,\,{\text{1}}}}} + {{\tau }_{{{\text{н}}\,\,{\text{2}}}}}{\text{,}} \\ \end{gathered} $Для промышленных установок большой производительности (более 50 м3/ч) требуется значительное время для разгона насосных агрегатов τн 1, τн 2 = 10–20 с. Эффективность процесса удаления загрязнений из поры зависит от многих параметров. Наиболее существенное влияние на нее оказывает удельный расход воды при обратной промывке Jо.п (или vо.п). Длительность промывки не может компенсировать уменьшение расхода Qо.п (или Jо.п), значение которого зависит от вида загрязнений и перепада трансмембранного давления Δртм. При экспериментальных исследованиях было установлено, что τп.оч < 4 с.
С увеличением Δртм растет и необходимое значение Jо.п для осуществления эффективной очистки. Соотношение между ними должно определяться в ходе пусконаладочных работ либо длительных опытно-промышленных испытаний. При наличии технических возможностей (необходимые параметры насосной станции обратной промывки) изменения могут вноситься в процессе промышленной эксплуатации. Корректное определение значений Qо.п и То.п способствует долгосрочной эксплуатации ультрафильтрационных мембранных модулей.
ОПРЕДЕЛЕНИЕ ПАРАМЕТРОВ ПРОМЫВКИ С ПОМОЩЬЮ ЛАБОРАТОРНОЙ УСТАНОВКИ
На промышленных объектах параметры, при которых производится промывка, подбирают при пусконаладочных работах или устанавливают их по проектным данным. Возможно определять их на пилотной установке с мембранным модулем, однако на промышленных объектах это дорогостоящее оборудование отсутствует, а стоимость услуг сторонних организаций высока. Более доступная установка для этих целей – лабораторный ультрафильтрационный модуль (ЛУМ) с прозрачной внешней трубкой, который подключается к источнику исходной воды и позволяет моделировать различные режимы работы (рис. 4). Техническими параметрами ЛУМ являются материал, проницаемость и геометрическая форма волокон, их число в мембране и длина. Динамику загрязнения волокна можно исследовать с помощью набора ЛУМ, имеющих мембраны с волокнами различной длины. Для классификации лабораторных модулей можно ввести обозначение [lв]/[Sф] (здесь [lв] – целая часть длины волокна lв, см; [Sф] – целая часть до десятков площади фильтрующей поверхности, см2). Например, в модуле ЛУМ-80/250 lв = 0.8 м, Nв = 11, dв = 0.9 мм.
Производительность ЛУМ Qу вычисляют по формуле
где– удельная производительность; I(τ) – проницаемость мембраны; τ – время.
При снижении проницаемости мембраны производительность установки поддерживается примерно постоянной путем увеличения перепада трансмембранного давления. Удельная производительность – проектный показатель, значение которого принимается равным 60 дм3/(м2 · ч). Настройка Δртм(τ) осуществляется регулировочным вентилем, измерение расхода воды – весовым методом, Δртм измеряется с помощью датчиков давления.
Фильтрование воды на промышленных установках происходит в соответствии со стандартным алгоритмом в течение заданного времени τф, после чего выполняются обратная промывка мембран и их химическая очистка. При этом должно быть выполнено условие $\Delta {{p}_{{{\text{тм}}}}}\left( {{{\tau }_{{\text{ф}}}}} \right) < \Delta p_{{{\text{тм}}}}^{{\text{к}}}$ (здесь $\Delta p_{{{\text{тм}}}}^{{\text{к}}}$ – критическое значение перепада трансмембранного давления, которое выбирается на основе рекомендаций производителя мембран). При достижении этого значения проводится продолжительная химическая очистка.
Цель исследований, осуществляемых на ЛУМ, – определение оптимальных параметров при работе установки вблизи максимально допустимого загрязнения, т.е. вблизи $\Delta p_{{{\text{тм}}}}^{{\text{к}}}.$ Для этого фиксируется начальный перепад давления $\Delta p_{{{\text{тм}}}}^{{\text{0}}},$ который должен совпадать с перепадом давления на промышленной установке при проектном значении Qу. Далее производится фильтрование до достижения $\Delta p_{{{\text{тм}}}}^{{\text{к}}}.$ В процессе фильтрования при $\Delta {{p}_{{{\text{тм}}}}}\left( \tau \right) < \Delta p_{{{\text{тм}}}}^{{\text{к}}}$ фактическое значение Qу может быть и больше рассчитанного по формуле (11) на 20–50%. Такое отклонение допустимо и связано с трудностью контроля условия ${{Q}_{{{\text{у}}~}}} \approx {\text{const}}{\text{.}}$
Прямая промывка выполняется с расходом промывочной воды ${{\bar {Q}}_{{{\text{п}}{\text{.п}}}}},$ при котором загрязнения заведомо удаляются с поверхности мембраны и перепад давления на ней $\Delta p_{{{\text{тм}}}}^{{{\text{п}}{\text{.п}}}}$ не изменяется. Для определения оптимального значения Qп.п и скорости потока воды vп.п его расход при обратной промывке начинают уменьшать от ${{\bar {Q}}_{{{\text{п}}{\text{.п}}}}}$ до тех пор, пока значение $\Delta p_{{{\text{тм}}}}^{{{\text{п}}{\text{.п}}}}$ не начнет увеличиваться.
На примере Новочеркасской ГРЭС было установлено, что при vп.п = 0.7–0.8 м/с более 80% отложений удаляется с поверхности мембраны за время 3lв/vп.п. Оптимальное время было экспериментально определено как ${{T}_{{{\text{п}}{\text{.п}}}}} \approx {{{\text{10}}{{l}_{{\text{в}}}}} \mathord{\left/ {\vphantom {{{\text{10}}{{l}_{{\text{в}}}}} {{{{v}}_{{{\text{п}}{\text{.п}}}}}}}} \right. \kern-0em} {{{{v}}_{{{\text{п}}{\text{.п}}}}}}}.$ С помощью ЛУМ можно проверять эффективность и других очисток на действующих установках ультрафильтрации прежде, чем менять настройки промышленной УФУ.
ХИМИЧЕСКАЯ ОЧИСТКА МЕМБРАННЫХ МОДУЛЕЙ
Большая площадь поверхности, низкая линейная скорость фильтрования (14–20 мкм/с), малый размер пор (0.02–0.05 мкм) обеспечивают высокое качество очистки воды при ультрафильтрации. Обратной стороной этого является подверженность мембраны сильному загрязнению. Прямая и обратная промывки не обеспечивают полного удаления загрязнений. Кроме того, доля неудаленных загрязнений растет от промывки к промывке. Поэтому на практике применяют химические очистки мембран, которые осуществляются регулярно во время механических промывок (в поток воды добавляют реагенты) и периодически (с прекращением работы установки). Для обеспечения минимальных затрат используют базовые химические реагенты (щелочь, соляную кислоту, гипохлорит натрия).
Кислотные промывки предназначены для удаления из мембран отложений, состоящих из солей жесткости. При ультрафильтрации солевой состав воды не изменяется, поэтому не следует ожидать заметных отложений солей жесткости. Однако при предварительной обработке, подогреве и коагуляции воды изменяются ее температура и рН. Как правило, рН сдвигается в кислую сторону и не провоцирует отложение солей жесткости. Кислотные промывки реализуются с применением соляной кислоты и являются самыми неудобными из химических очисток, особенно CEB по рекомендации производителей мембранных модулей и оборудования (1–2 раза в день).
Работы по оптимизации режимов эксплуатации установки ультрафильтрации проводили на Новочеркасской ГРЭС, на которой вода на нужды химического цеха поступает из водоотводного канала. Она используется для прямоточного охлаждения, и в течение бо́льшей части года ее температура составляет 20–30°С. Химический состав воды подвержен существенным колебаниям: общее солесодержание ОСС ≈ 350–750 мг/дм3, рН ≈ 7.5–8.4, щелочность Щ ≈ 2.2–4.2 мг-экв/дм3, жесткость Ж ≈ 4.5–9.2 мг-экв/дм3, концентрация кальция СCa ≈ 2.2 ммоль/дм3. Доля кальция в солях жесткости равна 60–67%. Средние значения показателей составляют: температура 25°С, ОСС = = 600 мг/дм3, рН = 7.9, Щ = 2.6 мг-экв/дм3, Ж = = 5.8 мг-экв/дм3.
Для оценки возможности образования карбонатных отложений используется индекс стабильности Ланжелье (LSI – Langelier Saturation Index) [6]
где рНи, рНр – измеренное и расчетное значение рН.При отрицательном значении LSI вода считается стабильной и карбонатные отложения не образуются.
Значение рНр вычисляют по формуле
где $A = {{\left( {{\text{lg}}{\kern 1pt} {\kern 1pt} {\text{ОСС}} - {\text{1}}} \right)} \mathord{\left/ {\vphantom {{\left( {{\text{lg}}{\kern 1pt} {\kern 1pt} {\text{ОСС}} - {\text{1}}} \right)} {{\text{10}}}}} \right. \kern-0em} {{\text{10}}}}{\text{;}}$ B = 34.55 – 13.12 lg (t + 273); С = lg CСа – 0.4; D = lg Щ; t – температура.Формула (13) основана на стандартах США, ОСС при расчете по ней и концентрацию Са по СаСО3 получают в мг/дм3.
Формулу (13) можно преобразовать в выражение, принятое в производственной практике водоподготовки:
(14)
$\begin{gathered} {\text{p}}{{{\text{H}}}_{{\text{р}}}} = {\text{8}}{\text{.2}} + {\text{0}}{\text{.1}}~{\text{l}}\,{\text{gOCC}} - {\text{lg}}\,{{С}_{{{\text{Са}}}}} - {\text{lg}}\,{\text{Щ}} - \\ - \,\,{\text{13}}{\text{.12lg}}\left( {{\text{1 + }}\frac{t}{{{\text{273}}}}} \right)~{\text{,}} \\ \end{gathered} $С учетом $\frac{t}{{273}}\,\,{\text{ < < }}\,\,1$ для линейного разложения $13.12\lg \left( {1 + \frac{t}{{273}}} \right) \approx ~ 0.02t$ и формула (14) упрощается:
(15)
${\text{p}}{{{\text{H}}}_{{\text{р}}}} = {\text{8}}{\text{.2}} + {\text{0}}{\text{.1}}~{\kern 1pt} {\kern 1pt} {\text{lg}}\,{\text{ОСС}} - {\text{lg}}\left( {{{С}_{{{\text{Са}}}}} \times {\text{Щ}}} \right) - {\text{0}}{\text{.02}}t.$Среднее значение индекса Ланжелье, рассчитанное по показателям качества воды на Новочеркасской ГРЭС, составило 0.32 и приблизилось к пороговому значению 0.5, при котором начинаются образование отложений солей жесткости и их осаждение на поверхности ультрафильтрационной мембраны. Для того чтобы уменьшить значение LSI, следовало снизить концентрацию кальция в воде. С этой целью после подогрева воду фильтровали через крупнодисперсную фильтрующую загрузку, находящуюся в контактных емкостях. При этом осаждалась нестабильная составляющая солей жесткости, снижалась более чем на 0.7 ммоль/дм3 концентрация кальция, уменьшалась щелочность. Это привело к снижению значения индекса Ланжелье на 0.3. Применение коагулянта способствовало также снижению рН на 0.2 и дополнительному уменьшению щелочности. Значение индекса Ланжелье становилось близким к нулю, вследствие чего интенсивность процессов отложения солей жесткости на поверхности мембран УФУ существенно уменьшалась. Благодаря этому стало возможным отказаться от кислотных СЕВ.
Эффективность такой технологии подтверждается стабильной многолетней работой УФУ на Новочеркасской ГРЭС. При этом длительность рабочего фильтроцикла была больше, чем его длительность с применением СЕВ без фильтрования воды через фильтрующую загрузку. Срок службы мембранных элементов существенно превысил расчетные 7 лет.
Щелочные промывки являются неотъемлемой частью работы УФУ. Они позволяют удалять из мембраны органические отложения, которые не удаляются при обратных промывках. Использование щелочи также является обязательным при проведении CIP.
Для очистки установок обратного осмоса используют кислотные и щелочные растворы на базе комплексонов. Их применение для УФУ ограничено высокой стоимостью и довольно большим количеством реагента на единицу площади обрабатываемой поверхности. На Новочеркасской ГРЭС в конце 2006–начале 2007 г. были введены в эксплуатацию три УФУ с мембранными модулями Dizzer 5000. В течение 2014–2016 гг. на двух из этих установок были проведены исследования эффективности применения реагентов, содержащих комплексонаты, для очистки мембран. Установки, на которых применяли такие реагенты, эксплуатируются до сих пор без замены мембранных модулей, а на третьей была произведена их замена.
В испытаниях были использованы кислотный раствор MF-CRO-220 и щелочной раствор MF-CRO-218 производства НПК “Медиана-Фильтр”, разработанные специально для установок ультрафильтрации в целях снижения затрат при проведении CIP. В результате исследований было установлено, что применение этих реагентов снижает $\Delta {{p}_{{{\text{тм}}}}}$ на 10–20% в зависимости от степени загрязнения мембраны. Эффективность очисток с помощью комплексонов довольно высока. Значение усредненного по времени перепада трансмембранного давления $\Delta {{\hat {p}}_{{{\text{тм}}}}}\left( \tau \right),$ который обеспечивает необходимую производительность установки, определяется по выражению
(16)
$\Delta {{\hat {p}}_{{{\text{тм}}}}} = \frac{{\text{1}}}{{\hat {T}}}\int\limits_{{{{{\tau }}}_{{\text{р}}}}}^{{{{{\tau }}}_{{\text{р}}}} + \hat {T}} {\Delta {{p}_{{{\text{тм}}}}}\left( \tau \right){\text{d}}\tau } {\text{,}}$Применять реагенты следует после проведения базовой щелочной или кислотной очистки. Использование реагентов увеличивает время между последовательными CIP-очистками в среднем на 15%. Следует ожидать, что в целом увеличится срок службы мембранных модулей благодаря уменьшению суммарного времени воздействия на мембрану агрессивных очищающих растворов.
Применение реагентов на основе комплексонов для CIP-очистки УФУ позволяет значительно снизить перепад трансмембранного давления, уменьшить естественную деградацию мембраны в течение эксплуатации. При их использовании можно восстановить рабочие характеристики мембранных модулей, если не помогают стандартные CIP-очистки. Рекомендуется производить CIP-очистки с применением реагентов на базе комплексонов 2 раза в год. Частота выполнения очисток будет ограничиваться стоимостью реагентов.
Были проведены промышленные испытания щелочного раствора, содержащего детергент MF-CRO-326 для очистки мембранных элементов от нефтепродуктов. Содержание нефтепродуктов в воде, поступающей на УФУ, было незначительным (0.1 мг/дм3). Применение реагента MF-CRO-326 привело к снижению $\Delta {{\hat {p}}_{{{\text{тм}}}}}$ на 4%. Это значение находится в пределах погрешности измерения и расчета $\Delta {{\hat {p}}_{{{\text{тм}}}}}.$ Таким образом, надежный положительный эффект не был зарегистрирован, что связано с низким содержанием нефтепродуктов в исходной воде. Применение реагента MF-CRO-326 возможно на установках ультрафильтрации, где в исходной воде содержится значительное количество нефтепродуктов, либо для очистки установки, которая подвергалась воздействию залповых выбросов нефтепродуктов.
РАБОЧИЙ РЕЖИМ ФИЛЬТРОВАНИЯ
Расход фильтрата Qф в ультрафильтрационной установке описывается уравнением
(17)
${{Q}_{{\text{ф}}}} = {{N}_{{\text{в}}}}\int {\frac{{\partial {{J}_{{\text{ф}}}}}}{{\partial p}}} \left( {z{\text{,}}{{\tau }_{{\text{ф}}}}} \right)\Delta {{p}_{{{\text{тм}}}}}\left( {{{\tau }_{{\text{ф}}}}} \right){\text{d}}{{S}_{{\text{ф}}}}{\text{,}}$В этой формуле учитывается зависимость проницаемости мембраны $I\left( {z{\text{,}}{{\tau }_{{\text{ф}}}}} \right) = \frac{{\partial {{J}_{{\text{ф}}}}}}{{\partial p}}$ от неоднородности загрязнения и времени, которая в процессе фильтрования уменьшается. Для обеспечения постоянной производительности УФУ увеличивают трансмембранное давление согласно выражению
(18)
${{Q}_{{\text{ф}}}} = {{S}_{{\text{ф}}}}I\left( {{{\tau }_{{\text{ф}}}}} \right)\Delta {{p}_{{{\text{тм}}}}}\left( {{{\tau }_{{\text{ф}}}}} \right).$Технология ультрафильтрации предусматривает тупиковый и тангенциальный режимы фильтрования (рис. 5). Тангенциальный режим предполагает фильтрование со сбросом части исходной воды (см. рис. 5, в) и без него (см. рис. 5, б). В первом случае
Рис. 5.
Режимы фильтрования: тупиковый (а), тангенциальный без сброса концентрата (б) и со сбросом концентрата (в). Qвх, Qк, Qр – расход воды на входе в установку, концентрата и рециркуляции; 2 – насос рециркуляции; остальные обозначения см. рис. 1
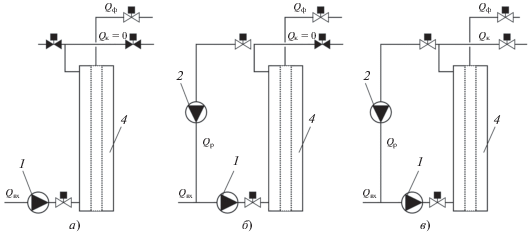
Во втором случае Qк = 0.
Тангенциальная скорость u(z), т.е. линейная скорость потока воды над мембраной, определяется выражением
(20)
$u\left( z \right) = {{\tilde {Q}\left( z \right)} \mathord{\left/ {\vphantom {{\tilde {Q}\left( z \right)} S}} \right. \kern-0em} S}{\text{,}}$(21)
$\tilde {Q}\left( z \right) = \left( {{\text{1}} - {z \mathord{\left/ {\vphantom {z {{{l}_{{\text{в}}}}}}} \right. \kern-0em} {{{l}_{{\text{в}}}}}}} \right){{Q}_{{\text{ф}}}} + {{Q}_{{\text{к}}}} + {{Q}_{{\text{р}}}}$– расход воды над мембраной в точке с координатой z.
В формуле (21) множитель ${z \mathord{\left/ {\vphantom {z {{{l}_{{\text{в}}}}}}} \right. \kern-0em} {{{l}_{{\text{в}}}}}}$ учитывает уменьшение расхода воды вследствие отбора фильтрата. Это предполагает, что удельная производительность мембраны постоянна, что не всегда обосновано из-за ее неоднородного загрязнения. При граничных условиях $\tilde {Q}\left( {\text{0}} \right) = {{Q}_{{{\text{вх}}}}}{\text{,}}$ $u\left( {\text{0}} \right) = {{u}_{{{\text{вх}}}}}{\text{,}}$ $\tilde {Q}\left( {{{l}_{{\text{в}}}}} \right) = {{Q}_{{\text{р}}}} + {{Q}_{{\text{к}}}}{\text{,}}$ $u\left( {{{l}_{{\text{в}}}}} \right) = {{u}_{{{\text{вых}}}}}$ расходы рециркуляции и сбрасываемого концентрата составляют ${{Q}_{{\text{р}}}} = {{\xi }_{{\text{р}}}}{{Q}_{{\text{ф}}}}{\text{,}}$ ${{Q}_{{\text{к}}}} = {{\xi }_{{\text{к}}}}{{Q}_{{\text{ф}}}}$ (здесь ${{\xi }_{{\text{р}}}}$ – коэффициент рециркуляции; ${{\xi }_{{\text{к}}}}$ – коэффициент сброса концентрата).
Расчет скоростей удобно выполнить через базовую проектную удельную производительность Jф и площадь фильтрующей поверхности мембранного элемента Sф:
(22)
${{u}_{{{\text{вх}}}}} = {{\theta }_{{J{v}}}}{{J}_{{\text{ф}}}}\left( {{\text{1}} + {{\xi }_{{\text{р}}}} + {{\xi }_{{\text{к}}}}} \right)\frac{{{\text{4}}{{l}_{{\text{в}}}}}}{{{{d}_{{\text{в}}}}}}{\text{;}}$(23)
$u\left( z \right) = \frac{{{\text{4}}{{l}_{{\text{в}}}}}}{{{{d}_{{\text{в}}}}}}{{\theta }_{{J{v}}}}{{J}_{{\text{ф}}}}\left( {{\text{1}} - \frac{z}{{{{l}_{{\text{в}}}}}} + {{\xi }_{{\text{р}}}} + {{\xi }_{{\text{к}}}}} \right).$Данная модель позволяет описать и режим тупикового фильтрования. При $\tilde {Q}\left( {\text{0}} \right) = {{Q}_{{{\text{вх}}}}} = {{Q}_{{\text{ф}}}}{\text{,}}$ $\tilde {Q}\left( {{{l}_{{\text{в}}}}} \right) = {\text{0,}}$ $u\left( {{{l}_{{\text{в}}}}} \right) = {{u}_{{{\text{вх}}}}}{\text{,}}$ $u\left( {{{l}_{{\text{в}}}}} \right) = {\text{0}}$ этот режим не является чисто тупиковым, так как значение продольной компоненты довольно велико
(24)
$u{\text{(}}z{\text{)}} = {{u}_{{{\text{вх}}}}}\left( {{\text{1}} - \frac{z}{{{{l}_{{\text{в}}}}}}} \right).$При удельном расходе фильтрата Jф ≈ ≈ 60 дм3/(м2 · ч) линейная скорость потока воды на входе в УФУ uвх ≈ 0.1 м/с является существенной. На значительной части волокна этот поток приводит к взрыхлению легких прилегающих к поверхности веществ, препятствуя снижению удельной производительности мембраны. При этом происходит унос загрязнений и повышение их концентрации в следующих по ходу движения потока областях. Очевидно, это приводит к неравномерному загрязнению поверхности мембраны. Динамику образования отложений в волокне можно отобразить выражением
(25)
$\frac{{\text{d}}}{{{\text{d}}t}}\rho \left( z \right) = \alpha - \beta \rho \left( z \right)u\left( z \right) + ~\theta \int\limits_{\text{0}}^z {\rho \left( {z{\kern 1pt} '} \right)u\left( {z{\kern 1pt} '} \right){\text{d}}z{\kern 1pt} '} {\text{,}}$Значение α пропорционально концентрации взвешенных частиц. Второй член в уравнении (25) описывает унос отложений, третий – их поступление вследствие уноса из других областей. С учетом (24) для качественного описания процессов интеграл в уравнении (25) можно аппроксимировать в первом приближении
(26)
$\begin{gathered} \frac{{\text{d}}}{{{\text{d}}t}}\rho \left( z \right) = \alpha - \beta {{u}_{{{\text{вх}}}}}\rho \left( z \right){{\left( {{{l}_{{\text{в}}}} - z} \right)} \mathord{\left/ {\vphantom {{\left( {{{l}_{{\text{в}}}} - z} \right)} {{{l}_{{\text{в}}}}}}} \right. \kern-0em} {{{l}_{{\text{в}}}}}} + \\ + \,\,{{u}_{{{\text{вх}}}}}\rho \left( z \right)\left( {\gamma z - \delta {{z}^{{\text{2}}}}~} \right){\text{,}} \\ \end{gathered} $При начальном условии ρ(z, 0) = 0 решение уравнения (26) выглядит следующим образом:
(27)
$\rho \left( {z{\text{,}}\,\,{{\tau }_{{\text{ф}}}}} \right) = \frac{\alpha }{{\omega \left( z \right)}}\left[ {{{{\text{e}}}^{{{{\omega }}\left( z \right){{{{\tau }}}_{{\text{ф}}}}}}} - {\text{1}}} \right]{\text{,}}$На первоначальном этапе фильтрования ω(z) << 1 и происходит простое линейное однородное отложение загрязнений на поверхности волокна, после которого начинается нелинейный режим в динамике отложений (рис. 6). Он сопровождается образованием неоднородности с максимумом ${{z}_{{{\text{max}}}}} = {{\left( {{\beta \mathord{\left/ {\vphantom {\beta {{{l}_{{\text{в}}}}}}} \right. \kern-0em} {{{l}_{{\text{в}}}}}} + \gamma } \right)} \mathord{\left/ {\vphantom {{\left( {{\beta \mathord{\left/ {\vphantom {\beta {{{l}_{{\text{в}}}}}}} \right. \kern-0em} {{{l}_{{\text{в}}}}}} + \gamma } \right)} {\left( {{\text{2}}\delta } \right)}}} \right. \kern-0em} {\left( {{\text{2}}\delta } \right)}}{\text{.}}$ Фильтрование на взвешенном слое осадка дополнительно увеличивает неоднородность отложений. При этом снижается эффективность фильтрования, происходит быстрый рост перепада трансмембранного давления, увеличивается вероятность разрыва волокон, что ограничивает применение технологии ультрафильтрации при увеличении концентрации взвешенных и коллоидных частиц.
Рис. 6.
Зависимость плотности отложений внутри волокна от z/lв при uвх = 0.1 м/с, α = 0.1, β = 0.2, γ = 0.2, δ = 0.5. τ, с: 1 – 10; 2 – 100; 3 – 200; 4 – 300; 5 – 400; 6 – 500
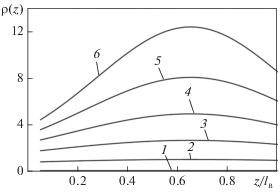
Решение этой проблемы – применение тангенциального режима фильтрования при ${{\xi }_{{\text{р}}}} \ne {\text{0,}}$ что позволяет оставлять загрязняющие вещества во взвешенном слое и снижать количество отложений на мембране. Использование тангенциального режима обеспечивает на выходе из волокна скорость $u\left( {{{l}_{{\text{в}}}}} \right) = \frac{{{\text{4}}{{l}_{{\text{в}}}}}}{{{{d}_{{\text{в}}}}}}{{\theta }_{{J{v}}}}{{J}_{{\text{ф}}}}{{\xi }_{{\text{р}}}},$ которая при достаточном значении ${{\xi }_{{\text{р}}}}$ предотвращает образование неоднородностей внутри волокна и способствует стабильному режиму фильтрования. Проводимые на пилотных установках исследования показали, что вплоть до концентраций взвешенных частиц 200 мг/дм3 коэффициент рециркуляции должен составлять ${{\xi }_{{\text{р}}}}$ = 0.5–0.7. Эти режимы работы УФУ были реализованы на Новочеркасской ГРЭС при концентрации взвешенных частиц 15–180 мг/дм3. Для высоких значений (более 30 мг/дм3) средний перепад трансмембранного давления в тангенциальном режиме при ${{\xi }_{{\text{р}}}}$ = 0.5 ниже, чем в тупиковом. В тангенциальном режиме эксплуатации УФУ увеличивается продолжительность фильтрования τф, уменьшается число химических промывок, снижается вероятность разрывов волокон. Срок службы ультрафильтрационных мембранных элементов на Новочеркасской ГРЭС оказался больше, чем на водоподготовительных установках других ТЭС с использованием технологии ультрафильтрации в тупиковом режиме.
ВЫВОДЫ
1. Для эффективного подбора режимов фильтрования, прямой и обратной промывок могут применяться лабораторные ультрафильтрационные модули.
2. При оптимизации кислотных промывок рекомендуется рассчитывать индекс стабильности карбоната кальция (индекс Ланжелье).
3. Для снижения интенсивности отложений в установке ультрафильтрации при существенно нестабильной исходной воде может быть использовано предварительное фильтрование воды через зернистую загрузку.
4. Оптимизация режимов работы ультрафильтрационных установок и предварительная обработка воды во многих случаях позволяют отказаться от непродолжительных кислотных очисток и ограничиться продолжительными кислотными очистками, что существенно упрощает эксплуатацию установки.
5. Качество работы ультрафильтрационных установок может быть повышено благодаря применению продолжительных кислотных и щелочных очисток на основе комплексонов с периодичностью применения 2 раза в год.
6. При тупиковом режиме фильтрования значительная часть отложений собирается в центральной части волокна. Естественным способом борьбы с этими отложениями является организация тангенциального режима фильтрования.
7. При нестабильном качестве исходной воды и повышенном содержании взвешенных и коллоидных частиц (более 30 мг/дм3) эффективным режимом является тангенциальное фильтрование, которое применяется при очистке стоков.
Список литературы
Технологии мембранного разделения в промышленной водоподготовке / А.А. Пантелеев, Б.Е. Рябчиков, О.В. Хоружий, С.Л. Громов, А.Р. Сидоров. М.: ДеЛи плюс, 2012.
Ho Jia Shin, Ma Zhun. Inline coagulation-ultrafiltration as the pretreatment for reverse osmosis brine treatment and recovery // Desalination. 2015. V. 365. P. 242–249.
Guillem Gilabert Oriol. Optimization of ultrafiltration membrane cleaning processes. Pretreatment for reverse osmosis in seawater desalination plants. Tarragona: Universitat i virgili, 2013. https://www.researchgate.net/publication/268514675_Optimization_of_ultra-filtration_membrane_cleaning_processes_Pretreatment_for_reverse_osmosis_in_seawater_desalination_plants
Pearce G.K. The case for UF/MF pretreatment to RO in seawater applications // Desalination. 2007. V. 203. № 1–3. P. 286–295.
Wolf P.H., Siverns S, Monti S. UF membranes for RO desalination pretreatment // Desalination. 2005. V. 182. № 1–3. P. 293–300.
Langelier W.F. The analytical control of anti-corrosion water treatment // J. American Water Works Association. 1936. V. 28. № 10. P. 1500–1521.
Дополнительные материалы отсутствуют.
Инструменты
Теплоэнергетика