Теплоэнергетика, 2021, № 10, стр. 45-52
Технология комплексной очистки огнестойких масел
В. В. Мартынов a, *, Н. В. Аржиновская a, Н. М. Первушина a, В. А. Петрухин a, А. Б. Пономарёв b, С. К. Моисеев b
a Всероссийский теплотехнический институт
115280 Москва, Автозаводская ул., д. 14, Россия
b Институт элементоорганических соединений им. А.Н. Несмеянова РАН
В-334, 119991 Москва, Вавилова ул., д. 28, Россия
* E-mail: vvm@vti.ru
Поступила в редакцию 19.11.2020
После доработки 25.01.2021
Принята к публикации 17.02.2021
Аннотация
Огнестойкие турбинные масла на основе триарилфосфатов в процессе эксплуатации на электрических станциях в системах регулирования и смазки энергоблоков подвергаются гидролизу с образованием кислот и фенолов, что приводит к повышению кислотного числа (КЧ) и вызывает образование смолистых отложений на оборудовании. В данной работе исследован процесс снижения КЧ в отработанных огнестойких жидкостях Reolube OMTI на основе триксиленилфосфатов, имевших значения КЧ выше 1.5 мг KOH/г, с использованием гидроксильной формы анионита АВ-17-8чС. Показано, что при выдержке при температуре 70°С в течение 2 ч значение КЧ огнестойкой жидкости может быть понижено с 2.67 до 0.03 мг KOH/г. Уменьшение температуры ниже 60°С приводит к резкому снижению скорости нейтрализации кислот. Скорость нейтрализации кислот также резко падает по мере снижения КЧ огнестойкой жидкости и исчерпания обменной емкости анионита. В результате нейтрализация кислот в маслах с КЧ ниже 0.05 мг KOH/г с помощью ионообменной смолы становится невыгодной. Невозможно также полное исчерпание обменной емкости анионита. Осушка нейтрализованного масла в вакууме при 70°С и остаточном давлении 0.01 МПа позволяет получить масло с содержанием воды менее 0.03%.
Разработка и испытания огнестойких жидкостей для замены нефтяного турбинного масла были начаты во многих странах еще в 50-х годах прошлого века. Это было обусловлено переходом к применению в турбоагрегатах пара повышенных параметров, что увеличило опасность возникновения пожаров как на тепловых, так и на атомных электростанциях из-за самовозгорания нефтяного турбинного масла, что могло привести к значительным материальным потерям, а также к повышению опасности радиационного поражения персонала и загрязнения окружающей среды. Поэтому большие усилия были направлены на создание гидравлических жидкостей и смазочных масел, обладающих температурой самовоспламенения выше 650°С [1].
В результате проведенных исследований во Всесоюзном теплотехническом институте им. Ф.Э. Дзержинского (ВТИ) было разработано огнестойкое турбинное масло на основе сложных эфиров фосфорной кислоты, а в 1969 г. создан его улучшенный вариант, аналогичный минеральным турбинным маслам по эксплуатационным и токсикологическим характеристикам и превосходящий их по термоокислительной стабильности, деаэрирующим, антикоррозионным и смазывающим свойствам, а также по сроку службы (5–6 лет). Этот продукт получил название “масло ОМТИ” (огнестойкое масло Теплотехнического института).
ОГНЕСТОЙКОЕ МАСЛО ТЕПЛОТЕХНИЧЕСКОГО ИНСТИТУТА
По своему химическому составу масло ОМТИ представляет собой смесь ариловых эфиров фосфорной кислоты с преобладающим содержанием триксиленилфосфатов, обозначаемую обычно общей формулой триарилфосфатов (ArO)3P=O, где Ar – арильные группы (могут быть разными в одной молекуле). Качество масла ОМТИ определяется его составом [природой и соотношением групп Ar, образующих молекулы (ArO)3P=O)], которое, в свою очередь, зависит от состава используемой для получения масла ксиленольной фракции, представляющей собой жидкие продукты коксования каменных углей. В этой фракции должен преобладать (60–75% и более) 3,5-ксиленол (3,5-диметилфенол).
В настоящее время на российских ТЭС и АЭС эксплуатируются огнестойкие масла зарубежного производства, которые, как и масло ОМТИ, являются жидкостями на основе триксиленилфосфатов и должны соответствовать нормативным документам [2, 3], регламентирующим требования к качеству огнестойких жидкостей для тепловых и атомных электростанций. Однако в последние годы качество поставляемых на российский рынок огнестойких масел значительно снизилось, что ставит под угрозу надежность и безопасность работы турбоагрегатов. Так, по статистическим данным [1], средний срок службы этих масел составляет 3.5 года вместо заявляемых производителем 6–7 лет.
С учетом высокой стоимости огнестойких турбинных масел вопрос повышения их эксплуатационного ресурса является крайне актуальным, поскольку позволит существенно повысить экономическую эффективность работы электрических станций.
Одним из важнейших нормируемых показателей огнестойких турбинных масел является кислотное число, показывающее количество кислот, содержащихся в масле. Значение КЧ определяется как количество миллиграммов гидроксида калия (KOH), необходимое для нейтрализации всех кислот, содержащихся в 1 г масла.
Присутствие кислот объясняется тем, что огнестойкие масла, представляющие собой смесь триарилфосфатов общей формулы (ArO)3P=O, в процессе эксплуатации постепенно подвергаются гидролизу под действием содержащейся в маслах воды в соответствии с реакцией
(1)
$\begin{gathered} {{\left( {{\text{ArO}}} \right)}_{3}}{\text{P = O}}\,\,{\text{ + }}\,\,{{{\text{H}}}_{2}}{\text{O}}\,\,\,\,\, \to \\ \to \,\,\,\,\,{{\left( {{\text{ArO}}} \right)}_{2}}{\text{P}}\left( { = {\kern 1pt} {\text{O}}} \right){\text{OH}}\,\,{\text{ + }}\,\,{\text{ArOH}}{\text{.}} \\ \end{gathered} $В реакции гидролиза принимает участие только одна из трех арилокси-групп (ArO), поскольку гидролиз с участием второй группы ArO, т.е. гидролиз диарилфосфатов, согласно реакции
(2)
$\begin{gathered} {{\left( {{\text{ArO}}} \right)}_{2}}{\text{P = OH}}\,\,{\text{ + }}\,\,{{{\text{H}}}_{2}}{\text{O}}\,\,\,\,\, \to \\ \to \,\,\,\,\,{\text{ArOP}}\left( { = {\kern 1pt} {\text{O}}} \right){{\left( {{\text{OH}}} \right)}_{2}}\,\,{\text{ + }}\,\,{\text{ArOH}} \\ \end{gathered} $протекает в значительно более жестких условиях, чем гидролиз с участием первой группы ArO. Кроме того, из-за низкой концентрации в масле диарилфосфатов (ArO)2P(=O)OH, образующихся на первой стадии гидролиза триарилфосфатов (ArO)3P=O в соответствии с (1), гидролиз согласно (2) должен протекать с очень малой скоростью. Поэтому реакцией гидролиза согласно реакции (2) можно пренебречь.
Поскольку реакции гидролиза катализируются кислотами, то по мере накопления в масле ОМТИ кислот (ArO)2P(=O)OH процесс гидролиза масла должен ускоряться, что подтверждается данными, получаемыми в процессе эксплуатации огнестойких масел [4]. Практический опыт свидетельствует о том, что ускоренное нарастание содержания кислот в масле начинается уже при значениях КЧ около 0.2 мг КОН/г [5].
В процессе гидролиза по реакции (1) в масле происходит накопление диарилфосфатов (ArO)2P(=O)OH, которые представляют собой кислоты, по силе соизмеримые с фосфорной, а также фенолов ArOH. Полимеризация этих продуктов приводит к образованию смол и лаков, которые отлагаются на рабочих поверхностях оборудования. Таким образом, снижение КЧ огнестойких масел необходимо не только для формального доведения этой характеристики до значений ниже браковочных показателей, но и для продления эксплуатационного ресурса масла путем снижения скорости его гидролиза и, соответственно, замедления накопления в масле компонентов, приводящих к образованию смол и лаков. При этом следует особо подчеркнуть, что потеря огнестойкими турбинными маслами в процессе эксплуатации своих изначальных свойств является естественной и меры по продлению их эксплуатационного ресурса, применяемые на электрических станциях, могут лишь замедлить процесс деструкции масел, но не могут его полностью остановить.
Показатели качества образца Reolube OMTI, отобранного из системы смазки энергоблока и очищенного на стендовой установке ВТИ
Показатель качества | Требования СТО 70238424.27.100.053-2013 | Результаты испытаний Reolube OMTI | Методы испытаний | |
---|---|---|---|---|
до восста-новления | после восстановления | |||
Кислотное число, мг КОН/г | Не более 1.0 | 2.67 | 0.3 | МВИ 63-09 |
Коррозия на стальных пластинах, г/м2 | Не более 15 | 5.0 | 1.5 | МВИ 60-09 |
Массовая доля воды, % (по массе) | Отсутствует (не более 0.03) | 0.252 | 0.03 | ГОСТ 24614-81 |
Время, с: | ||||
деаэрации | Не более 540 | 60 | 60 | МВИ 61-09 |
деэмульсации | Не более 600 | 230 | 210 | ГОСТ 12068-66 |
Класс промышленной чистоты | Не более 9 | 11 | 9 | ГОСТ 17216-2001 |
Массовая доля, %: | ||||
растворенного шлама | Не более 0.1 | 0.01 | 0.008 | МВИ 77-09 |
механических примесей | Не более 0.01 | 0.006 | 0.004 | ГОСТ 6370-2018 |
Один из подходов к решению проблемы ускоренной деградации огнестойких масел – использование установок их комплексной очистки. Имеющиеся на данный момент маслоочистительные установки, ориентированные на снижение КЧ масел и удаление из них воды и механических примесей, являются однотипными и не имеют значительных конструктивных различий. В большинстве случаев эти установки представляют собой блок фильтрации и обезвоживания под вакуумом. В редких случаях они комплектуются дополнительным адсорбционным блоком, как правило, с использованием ионообменных смол. При этом известные на сегодняшний день технические решения продления срока службы огнестойких масел применимы только для систем регулирования паровых турбин и неприменимы для систем смазки. Эффективные технологии регенерации полностью отработанных масел на основе триарилфосфатов с полным восстановлением их свойств до уровня свежего товарного масла ранее отсутствовали вовсе. Соответствующая технология была разработана лишь недавно [6].
Определенный практический эффект достигается при использовании вакуумной маслоочистительной установки (МОУ) для восстановления качества огнестойких турбинных масел марки Reolube OMTI, в которой реализована технология ионного обмена для снижения кислотного числа в огнестойких жидкостях на основе эфиров фосфорной кислоты. Однако опыт применения подобных установок показал, что они неэффективны для очистки сильно загрязненных масел из систем смазки и могут использоваться только для жидкостей систем регулирования с характерной для них слабой степенью загрязнения.
ЛАБОРАТОРНЫЕ И СТЕНДОВЫЕ ИССЛЕДОВАНИЯ МЕТОДОВ ОЧИСТКИ REOLUBE OMTI
Специалистами ОАО “Всероссийский теплотехнический институт” в результате лабораторных и стендовых исследований методов очистки огнестойкого масла Reolube OMTI со значениями КЧ от 1.3 до 2.6 мг КОН/г и более были найдены технические решения, позволяющие снизить содержание кислот в масле до значений КЧ, соответствующих нормативным требованиям [2]. Причем, как показали стендовые испытания, эти решения оказались эффективными для снижения КЧ огнестойких масел, применяющихся не только в системе регулирования, но и в системе смазки.
В ходе лабораторных экспериментов была продемонстрирована принципиальная возможность доведения технических характеристик эксплуатационного масла до нормативных значений. Очистка масла проводилась адсорбционным методом с использованием в качестве адсорбента ионообменной смолы – анионита АВ-17-8чС в гидроксильной (OH–) форме. В лабораторных условиях этот сильноосновный анионит показал способность эффективно снижать кислотное число эксплуатационного огнестойкого масла Reolube OMTI. Выбор сильноосновного анионита обусловлен тем, что из-за сильной загрязненности смол (отравления) рабочей жидкостью системы смазки, которые исследовались в работе, регенерация отработанных ионообменных смол была невозможна, а именно их более легкая регенерация (количество щелочи и воды значительно меньше) является главным преимуществом слабоосновных анионитов перед сильноосновными.
Стендовые испытания на экспериментальной базе ОАО ВТИ проводились на пилотной установке, схема которой представлена на рис. 1, в целях масштабирования лабораторной технологии и адаптации ее к условиям работы маслоочистительных установок.
Рис. 1.
Принципиальная технологическая схема пилотной установки. 1, 2 – фильтры грубой и тонкой очистки; 3 – адсорберы; 4 – вакуумный испаритель; 5 – электрообогреватель; 6 – пробоотборники; 7 – заливная горловина; 8 – маслобак
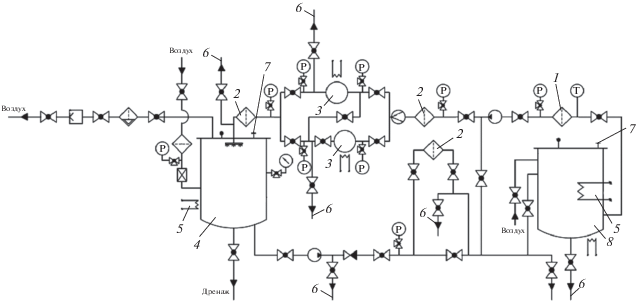
Технологическая схема пилотной установки включала механические фильтры грубой и тонкой очистки (до 1 мкм), два однотипных адсорбера, заполненных адсорбентом, которые могли включаться как поодиночке, так и одновременно (параллельно или последовательно), а также вакуумный испаритель для удаления влаги. Отдельные узлы установки обеспечивались независимым электрообогревом, необходимым контрольно-измерительным оборудованием и пробоотборниками.
В качестве адсорбента, так же как и в лабораторных экспериментах, в пилотной установке использовалась ионообменная смола анионит АВ-17-8чС в гидроксильной (OH–) форме. Испытания проводились на маслах с КЧ более 1.5 мг КОН/г, отобранных из системы смазки энергоблоков, и масле с КЧ 0.28 мг КОН/г из системы регулирования. Основными задачами испытаний были следующие:
установление предельной емкости адсорбента;
определение параметров, обеспечивающих оптимальную работу адсорбента;
определение показателей восстановленного масла.
Полученные в процессе испытаний результаты приведены в таблице.
Фильтрование эксплуатационного масла через фильтры стендовой установки в режиме циркуляции без пропускания его через адсорберы с ионообменной смолой позволило повысить класс промышленной чистоты (КПЧ) масла с 11 до 9, но не оказало влияния на значение КЧ. Определение КПЧ в исходных сильнозагрязненных маслах было затруднено из-за содержавшихся в них смолистых отложений, тогда как в очищенных маслах эти отложения наблюдались в меньшей степени, что свидетельствует об удалении продуктов деградации масла в процессе фильтрации.
При температуре 25°С масло с КЧ 1.73 мг КОН/г, проходя через ионообменную смолу даже при небольшой скорости подачи (12 л/ч), нейтрализовывалось лишь в незначительной степени (до КЧ = 1.56 мг КОН/г). Очевидной причиной этого была высокая вязкость масла при столь низкой температуре, которая затрудняла диффузию и тем самым препятствовала эффективному контакту содержащихся в масле кислот с поверхностью ионообменной смолы (рис. 2).
Рис. 2.
Изменение КЧ масла при прохождении через ионообменную смолу при различных температурах. Температура масла, °С: 1 – 25; 2 – 45; 3 – 60
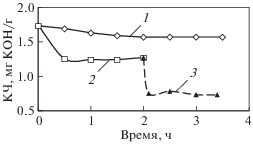
При более высокой температуре (45°С) и скорости подачи масла 5 л/ч ионообменная смола более активно нейтрализовывала содержащиеся в нем кислоты, но и в этих условиях эффективность нейтрализации была невысокой (КЧ снизилось лишь до 1.24 мг КОН/г). Это свидетельствует о том, что и при данной температуре скорость нейтрализации кислот остается слишком низкой. Повышение температуры до 60°С немедленно привело к снижению КЧ масла на выходе из адсорбера до 0.75 мг КОН/г, хотя скорость потока масла при этом была увеличена до 120 л/ч.
Циркуляция 132 л (150 кг) масла с КЧ 0.48 мг КОН/г, приготовленного смешением 120 л масла с КЧ 0.28 мг КОН/г из системы автоматического регулирования энергоблока и 12 л масла с КЧ 2.67 мг КОН/г из системы смазки, ч-ерез адсорбер, содержавший 3.5 кг анионита АВ‑17-8чС, в течение 2 ч при температуре 70°С привела к снижению КЧ до 0.028 мг КОН/г. Это значение не изменилось при пропускании масла через ионообменную смолу в течение последующих 7 ч при тех же условиях, хотя обменная емкость анионита при этом не была исчерпана. Данный результат указывает на резкое снижение скорости нейтрализации кислот даже в благоприятных для этого процесса температурных условиях вследствие значительного снижения концентрации кислот в масле. Этот факт свидетельствует об экономической нецелесообразности нейтрализации кислотных примесей в огнестойких маслах с помощью ионообменных маслоочистительных установок для масел со значениями КЧ менее 0.05 мг КОН/г.
Вывод о снижении скорости нейтрализации кислот по мере уменьшения их концентрации в масле подтверждается результатами эксперимента с использованием двух адсорберов, каждый из которых содержал по 6 кг ионообменной смолы. В этом эксперименте было использовано 120 л (136 кг) масла с КЧ 2.67 мг КОН/г. Масло, нагретое до 70°С, циркулировало со скоростью 450 л/ч сначала только через первый адсорбер. Через 1 ч поток масла был направлен на циркуляцию через оба адсорбера, соединенных последовательно.
Прохождение масла через первый адсорбер сопровождалось на начальном этапе резким снижением КЧ масла, однако с течением времени оно сильно замедлилось и через 1 ч КЧ составило 0.43 мг КОН/г. Графически динамика снижения КЧ масла отражена на рис. 3.
Рис. 3.
Изменение КЧ масла в зависимости от времени при циркуляции через один (1), а затем через два адсорбера (2)
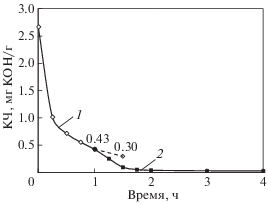
Судя по графику, с течением времени следовало ожидать снижения КЧ масла после его циркуляции только через первый адсорбер до предельного значения около 0.30 мг КОН/г, т.е. 6.0 кг данного анионита способны нейтрализовать (2.67 – 0.30) × 136 : 57 = 5.65 экв. кислоты, что соответствует динамической объемной емкости анионита 0.94 экв/кг. После подключения второго адсорбера закономерность снижения КЧ масла осталась той же: быстрое снижение КЧ на начальном этапе с последующим замедлением. Замедление темпа нейтрализации масла может объясняться как снижением концентрации в нем кислоты, так и меньшей доступностью для масла остающихся активных центров анионита по мере исчерпания им емкости в процессе нейтрализации. Пропускание масла только через первый адсорбер в течение первых 30 мин привело к снижению КЧ на 1.95 мг КОН/г, в то время как в течение первых 30 мин после подключения второго адсорбера КЧ снизилось на 0.33 мг КОН/г. Этот результат также свидетельствует о том, что снижение скорости нейтрализации масла при малом значении КЧ обусловлено не уменьшением обменной емкости анионита, а слишком низкой концентрацией кислоты в очищаемом масле.
Использование ионообменной смолы АВ-17-8чС в гидроксильной (OH–) форме для нейтрализации кислот (ArO)2P(=O)OH, содержащихся в эксплуатационном масле, приводит к удалению их из масла, поскольку анион кислоты связывается со смолой, а катион нейтрализуется с образованием воды, которая впоследствии удаляется на стадии осушки.
Стендовые испытания показали, что удаление воды до уровня 0.06% (по массе) и ниже может быть эффективно осуществлено при циркуляции через вакуумную емкость масла, предварительно пропущенного через адсорберы. Осушка масла проводилась при температуре 70°С и остаточном давлении в вакуумной емкости около 0.01 МПа. На рис. 4 графически изображен процесс осушки масла с КЧ 0.16 мг КОН/г.
Таким образом, апробированная на пилотной установке технология нейтрализации огнестойкого масла Reolube OMTI показала наибольшую эффективность при поддержании температуры около 70°С. При этой температуре обеспечиваются довольно высокие скорости процессов снижения КЧ и осушки масла. Повышение температуры более 80°С является нецелесообразным, так как в этих условиях начинаются процессы деструкции адсорбента. При термическом разрушении анионита АВ-17-8чС может происходить выделение метанола и триметиламина. Взаимодействие триметиламина с диарилфосфатами (ArO)2P(=O)OH, являющимися продуктами разложения масла, должно приводить к нейтрализации этих кислот вследствие образования диарилфосфатов триметиламмония и снижению кислотного числа. Однако дальнейшая циркуляция масла через ионообменную смолу приведет, как и в случае самой кислоты (ArO)2P(=O)OH, к обмену диарилфосфат-аниона образовавшейся соли с анионитом (т.е. к связыванию его с ионообменной смолой) и к повторному высвобождению триметиламина из соли. Поскольку и метанол, и триметиламин являются низкокипящими веществами, они должны удаляться на стадии вакуумной осушки масла, не оказывая, таким образом, влияния на КЧ. Это было подтверждено экспериментальными данными: значения КЧ масла до и после вакуумной осушки были одинаковыми. Таким образом, термическая деструкция анионита ведет лишь к снижению его обменной емкости.
Воспроизводимость параметров работы анионита АВ-17-8чС в процессе нейтрализации отработанного масла была показана в ходе как лабораторных, так и стендовых испытаний. При использовании конкретной партии адсорбента в одинаковых условиях для снижения КЧ как в различных порциях одной и той же партии отработанного масла, так и в разных партиях масла результаты экспериментов были сходными.
МАСЛООЧИСТИТЕЛЬНАЯ УСТАНОВКА
Окисление самогó масла под влиянием температуры выражено в очень незначительной степени. Это весьма стабильное по отношению к окислению вещество (точнее, смесь веществ). Основной процесс деструкции масла – гидролиз. Окислению же подвергаются продукты гидролиза – фенолы (ксиленолы). Именно фенолы и продукты их окисления обусловливают цвет эксплуатируемого масла, его запах и наличие смолообразных отложений на внутренних поверхностях оборудования. Скорость образования фенолов в процессе эксплуатации можно оценить по времени эксплуатации масла и по содержанию в масле кислот (по значению КЧ) и/или ксиленолов (по значению фенольного числа). В масле с КЧ 2.0 мг КОН/г содержание кислот составляет примерно 1% (по массе). Эти кислоты накапливаются в масле в процессе его эксплуатации. При этом скорость их накопления с течением времени возрастает (в том числе и из-за нагрева масла при контакте с подшипниками), поскольку гидролиз масла катализируется кислотами, образующимися в процессе самого гидролиза. При более высокой температуре (например, при 70°С) процесс гидролиза, естественно, будет протекать интенсивнее. Известно, что повышение температуры на каждые 10°С способствует увеличению скорости химической реакции в 2–4 раза. Следовательно, повышение температуры с 45–47 до 70°С при работе маслоочистительной установки (далее – МОУ) приводит к увеличению скорости гидролиза масла в 6–20 раз. Если предположить, что с учетом повышенного содержания влаги в МОУ скорость гидролиза возрастает в 100 раз (хотя в условиях значительного снижения концентрации кислоты в масле, находящемся в МОУ, скорость гидролиза масла должна, наоборот, резко снизиться), то, приняв, что масло в МОУ находится не более 10 ч, можно считать, что даже при самых неблагоприятных допущениях разложение масла в процессе восстановления в МОУ при температуре 70°С эквивалентно его разложению в условиях эксплуатации при 45–47°С в течение 10 × × 100 : 24 = 42 сут. И это в предположении, что восстановленное масло с низким КЧ в дальнейшем будет гидролизоваться с такой же скоростью, что и находящееся в эксплуатации масло с высоким КЧ, что, конечно, не так. Поэтому в реальности при повышенной (70°С) температуре в МОУ последующий срок эксплуатации восстановленного масла может сократиться от силы на несколько суток.
Необходимо также иметь в виду тот факт, что в процессе снижения КЧ из масла удаляются только кислоты; все остальные продукты разложения в масле остаются11. Поэтому следует ожидать, что срок дальнейшей эксплуатации восстановленного масла будет менее продолжительным, чем срок эксплуатации свежего масла. По нашей оценке, применение описанной технологии очистки на начальном этапе после установления роста кислотного числа позволит увеличить срок службы огнестойкого масла как минимум в 1.5 раза по сравнению с обычно заявляемым производителем масла сроком 5–7 лет.
О положительной стендовой апробации технологии комплексной очистки огнестойких масел свидетельствуют следующие результаты: снижение кислотного числа до уровня 0.03–0.04 мг КОН/г; уменьшение содержания влаги до значения менее 0.03%; повышение класса промышленной чистоты с 11-го до 9-го.
Успешно проведенные испытания образцов сильно загрязненного масла из систем смазки и регулирования турбин позволили создать максимально автоматизированную мобильную установку комплексной очистки масла (рис. 5). Суть разработанной технологии заключается в трехступенчатой очистке эксплуатационной огнестойкой жидкости от различных примесей методами ионообменной адсорбции, вакуумной осушки и тонкой механической фильтрации. Проведение процесса при температуре 70–75°С обеспечивает его высокую скорость и использование полного ресурса ионообменной смолы. Показатели качества восстановленного огнестойкого масла при этом соответствовали нормативным требованиям для масел, находящихся в эксплуатации.
Рис. 5.
Схема маслоочистительной установки. А1, А2 – адсорберы; МБ1 – маслобак; МБ2-1, МБ2-2 – маслобаки вакуумные; МВ – модуль вакуумной осушки; МФ – модуль фильтрации
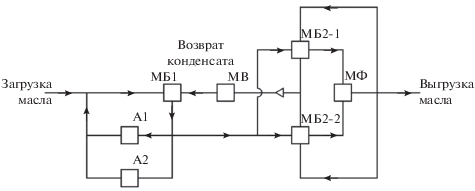
Загрузка масла в установку осуществляется шестеренным насосом в маслобак МБ1, где оно нагревается до заданной температуры посредством установленного в баке теплообменника. Процесс адсорбции производится путем пропускания масла через один из двух адсорберов, заполненных разовыми картриджами с ионообменным материалом. Масло после адсорбции подается в один из двух вакуумных баков (МБ2-1 или МБ2-2), где проводится параллельная вакуумная осушка двух отдельных партий масла. Поддержание температуры масла, подвергаемого вакуумной сушке, осуществляется теплообменными аппаратами, установленными в вакуумных баках. Поток водяного пара направляется на модуль вакуумной осушки, где конденсат отделяется и накапливается для периодического возврата в контур адсорбции, включающий в себя маслобак МБ1 и адсорберы, непосредственно в маслобак МБ1.
Осушенное масло подается из маслобака МБ2-1 (или МБ2-2) вторым шестеренным насосом на фильтры тонкой очистки модуля фильтрации МФ, в состав которого также включен теплообменник с принудительным воздушным охлаждением, обеспечивающим снижение температуры до необходимых значений. Масло, прошедшее основные технологические процессы и достигшее в результате требуемых характеристик, выгружается из установки.
Разработанные маслоочистительные установки целесообразно использовать в первоначальный период эксплуатации огнестойкого масла. При этом диапазон кислотного числа, в пределах которого рекомендуется использовать установку, определяется, прежде всего, требованиями к эксплуатационным маслам. При очистке масел с таким кислотным числом гарантированно достигаются нормативные показатели [2].
ВЫВОДЫ
1. Разработанная технология показала наибольшую эффективность при поддержании температуры процессов нейтрализации кислотных примесей и осушки масла в пределах 70–75°С.
2. Основное влияние на снижение кислотного числа оказывают температура и концентрация кислот в масле.
3. При испытаниях восстановленного масла были достигнуты снижение его кислотного числа до 0.03 мг КОН/г, уменьшение содержания влаги до значений менее 0.03%, повышение класса промышленной чистоты с 11-го до 9-го.
4. Маслоочистительные установки на основе технологии комплексной очистки целесообразно использовать в первоначальный период эксплуатации огнестойкого масла. При этом диапазон кислотного числа, при котором рекомендуется использовать установку, определяется, прежде всего, требованиями к эксплуатационным маслам.
5. Применение данной технологии позволит увеличить срок службы огнестойкого масла как минимум в 1.5 раза по сравнению с обычно заявляемым производителем масла сроком 5–7 лет.
Список литературы
Вайнштейн А.Г. Российские огнестойкие турбинные масла: создание, освоение производства и 45-летний опыт эксплуатации в энергетическом оборудовании ТЭС и АЭС // Новое в российской энергетике. 2011. № 6. С. 30–39.
СТО 70238424.27.100.053-2013. Энергетические масла и маслохозяйства электрических станций и сетей. Организация эксплуатации и технического обслуживания. Нормы и требования. 2-е изд. М.: НП ИНВЭЛ, 2013.
РД ЭО1.1.2.05.0444-2016. Требования к эксплуатации, организации и проведению испытаний трансформаторных и турбинных масел на атомных станциях (с изм. 1-3). М.: АО “Концерн Росэнергоатом”, 2016.
Огнестойкие турбинные масла / К.И. Иванов, Г.Д. Вилянская, Ю.Д. Зильбер, М.З. Хейфец, М.С. Фрагин, И.Д. Гадаскина; под ред. К.И. Иванова. М.: Химия, 1974.
Галимова Л.А. Применение синтетических огнестойких масел в маслосистемах турбинного оборудования АЭС // Теплоэнергетика. 2017. № 10. С. 87–91. https://doi.org/10.1134/S0040363617100022
Пат. РФ № 2736715. Способ регенерации использованного смазочного масла / В.В. Мартынов, Н.В. Аржиновская, В.А. Петрухин, С.К. Моисеев, И.А. Черепанов. 19.11.2020.
Дополнительные материалы отсутствуют.
Инструменты
Теплоэнергетика