Теплоэнергетика, 2022, № 11, стр. 35-49
Исследование влияния напряжений, возникающих при модификации поверхности образцов стали 20Х13, на инкубационный период процесса каплеударной эрозии
А. Ф. Медников a, *, А. В. Рыженков a, Г. М. Бровка b, Г. В. Качалин a, А. Б. Тхабисимов a, О. С. Зилова a
a Национальный исследовательский университет “Московский энергетический институт”
111250 Москва, Красноказарменная ул., д. 14, Россия
b Белорусский национальный технический университет
220013 г. Минск, просп. Независимости, д. 65, Республика Беларусь
* E-mail: MednikovAlF@mpei.ru
Поступила в редакцию 29.04.2022
После доработки 21.05.2022
Принята к публикации 23.05.2022
- EDN: VCYMUQ
- DOI: 10.56304/S0040363622110054
Аннотация
В работе приведены результаты исследований напряжений, возникающих в образцах стали 20Х13 при реализации различных типов модификации поверхности и их комбинаций: борирования, ионного азотирования, ионно-плазменных покрытий Cr-CrC, импульсно-лазерной обработки. Исследование напряжений проводили по методике, основанной на измерении деформации (изгиба) образца. По профилям поверхности, измеренным до и после модификации, получены значения нормального изгиба, которые использовали для оценки изменения напряжений. В результате исследований установлено, что при импульсно-лазерной обработке по характеру нормального изгиба можно судить о наличии сжимающих напряжений в поверхностном слое. В случае нанесения покрытия Cr-CrC после импульсно-лазерной обработки изгиб поверхности уменьшается, что свидетельствует об уменьшении итогового уровня сжимающих напряжений. При комбинации типов модификации поверхности, включающей нанесение покрытия Cr-CrC с последующей импульсно-лазерной обработкой, с ростом толщины покрытия наблюдается переход от сжимающих к растягивающим напряжениям в поверхностном слое. Уменьшение глубины азотированного слоя приводит к снижению растягивающих напряжений. Формирование покрытий Cr-CrC разной толщины на стали 20Х13 ведет к образованию напряжений различного уровня. Объединение покрытий разной толщины на основе Cr-CrC с несколькими типами азотирования может приводить к снижению напряжений в этих комбинациях и эрозионной стойкости, превосходящей стойкость стеллита. Полученные зависимости удельной подведенной энергии, свидетельствующей об окончании инкубационного периода процесса эрозионного износа, от внутренних напряжений в поверхностном слое могут использоваться для прогнозирования эрозионной стойкости поверхности после модификации. Прогнозирование может осуществляться по измеренному уровню напряжений на этапе выбора способа защиты.
В настоящее время развитие турбостроительной отрасли нацелено на повышение эффективности работы турбоагрегатов благодаря росту начальных параметров рабочего тела, приводящему к увеличению эксплуатационных нагрузок на ответственные элементы проточной части турбины [1]. При этом возникает проблема обеспечения надежности высоконагруженных элементов оборудования, работающего в двухфазных средах [2]. Одной из актуальных до сих пор проблем является защита входных кромок рабочих лопаток последних ступеней паровых турбин, находящихся во влажно-паровом потоке, от эрозионного разрушения, возникающего вследствие высокоскоростного взаимодействия с ними капель жидкости [3–6].
На сегодняшний день используются различные способы пассивной защиты лопаток турбины от каплеударной эрозии: размещение на их поверхности наплавок, вставок и стеллитовых пластин, легирование, лазерное и диффузионное упрочнение, нанесение износостойких покрытий [7–13]. К сожалению, не все из них оказываются эффективны вследствие низкой стойкости к высокоэнергетическому капельному воздействию и невозможности проверки их результативности на этапе разработки.
В качестве материалов для эрозионно-стойких покрытий применяют нитриды, карбиды, карбонитриды тугоплавких химических элементов. Эффективны ионно-плазменные покрытия на основе Ti, TiAl, Cr [14, 15]. Полученные ранее авторами результаты экспериментальных исследований на образцах из титана и стали показали перспективность формирования на защищаемой поверхности многослойных ионно-плазменных покрытий на основе хрома-карбида хрома (Cr-CrC) [16–18]. Кинетические кривые эрозионного износа лопаток из стали 20Х13 c импульсно-лазерной обработкой их поверхности, приведенные в [19, 20], отражают положительную динамику эрозионной стойкости по сравнению с немодифицированной поверхностью.
Для создания упрочненного износостойкого поверхностного слоя несомненный интерес представляют результаты исследования процессов модификации на его глубину путем диффузионного одно- и многокомпонентного насыщения защищаемой поверхности металлами и неметаллами. В качестве возможного варианта диффузионного упрочнения поверхности лопаток для защиты от каплеударной эрозии были выбраны азотирование [21–26] и борирование [27]. Ранее проведенные авторами исследования эрозионной стойкости лопаточных сталей 12Х13, 20Х13, 15Х11МФ и ЭИ961 при их ионном азотировании показали их более высокую эффективность относительно литого стеллита (рис. 1) [28].
Рис. 1.
Зависимость относительной потери массы образца Δmот от относительного времени испытаний τот при скорости соударения 300 м/с и диаметре капель 800 мкм. 1, 2 − стеллит без покрытия и с азотированием; 3−6 − сталь 12Х13, 20Х13, 15Х11МФ, ЭИ961 с азотированием
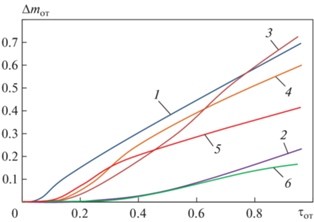
Задача создания эрозионно-стойких покрытий с заданным комплексом физических, механических, технологических и морфологических свойств многофакторна. Для ее решения необходимы экспериментальные и теоретические исследования комбинаторики типов модификации поверхностного слоя с одновременным формированием защитных покрытий с требуемыми характеристиками.
Для тестирования предлагаемых способов защиты используют зарекомендовавшие себя с хорошей стороны методы разрушающего контроля, реализуемые на специальных стендах и установках, моделирующих высокоскоростное каплеударное воздействие и позволяющих оценить стойкость одного способа защиты относительно другого [29–32]. Ввиду сложности натурного процесса износа трудно провести ранжирование характеристик выбранного типа модификации поверхности с выявлением наиболее эффективного сочетания свойств системы “способ защиты − основной материал” [33–35].
Одним из критериев оценки эрозионной стойкости того или иного способа упрочнения является длительность инкубационного периода процесса износа – периода, когда происходит накопление поврежденности без признаков разрушения защищаемой поверхности [36]. Особенно актуальным этот период становится для упрочнения поверхности в силу того, что после его окончания последующее разрушение происходит с максимальной скоростью износа. Это в большинстве случаев приводит к частичному или полному снижению износостойких свойств применяемой защиты [37, 38].
Целью настоящей работы являлась разработка методики предварительной оценки эрозионной стойкости перспективных типов модификации поверхности и их комбинаций, базирующейся на определении взаимосвязи напряжений в поверхностном слое и длительности инкубационного периода. При решении поставленной задачи использовали метод, основанный на определении напряжений путем измерения изгиба образцов стали 20Х13 после модификации.
Для рассмотрения были выбраны следующие типы модификации поверхности, а также их комбинации: борирование, ионное азотирование, ионно-плазменные покрытия на основе Cr-CrC, импульсно-лазерная обработка, ионное азотирование с ионно-плазменными покрытиями на основе Cr-CrC, ионно-плазменные покрытия на основе Cr-CrC с последующей импульсно-лазерной обработкой, импульсно-лазерная обработка с последующим нанесением ионно-плазменных покрытий на основе Cr-CrC.
ОПИСАНИЕ МЕТОДИКИ ПРОВЕДЕНИЯ ИССЛЕДОВАНИЙ
Для вычисления напряжений в покрытии σ применяется формула Стоуни [39–49]:
(1)
$\sigma = \frac{1}{6}\left( {\frac{1}{{{{R}_{{post}}}}} - \frac{1}{{{{R}_{{pre}}}}}} \right)\frac{E}{{\left( {1 - \nu } \right)}}\frac{{t_{s}^{2}}}{{{{t}_{f}}}},$Радиусы кривизны образца могут быть оценены по профилограммам, получаемым до и после нанесения покрытия.
Формула (1) может быть представлена в виде
(2)
$\sigma = \frac{{4\delta }}{{3{{l}^{2}}}}\frac{E}{{\left( {1 - \nu } \right)}}\frac{{t_{s}^{2}}}{{{{t}_{f}}}},$При этом должны выполняться следующие допущения:
вычитание из профиля после нанесения покрытия исходного (измеренного до нанесения покрытия) профиля поверхности;
аппроксимация получаемого профиля поверхности с помощью дуги окружности (рис. 2);
Рис. 2.
Схема определения радиуса кривизны образца R (а) после модификации с учетом исходного профиля поверхности (б)
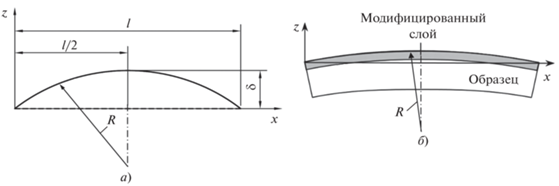
нормальный изгиб подложки δ намного меньше длины профиля l (см. рис. 2).
Таким образом, напряжения в покрытии будут прямо пропорциональны нормальному изгибу подложки.
В случае применения формулы (2) для оценки напряжений в поверхностном слое материала после упрочнения в качестве tf можно использовать толщину модифицированного слоя. Однако при лазерной обработке и комплексных вариантах модификации существуют проблемы корректного определения tf. Тем не менее, можно использовать нормальный изгиб, чтобы характеризовать изменение напряжений в поверхностном слое в процессе модификации.
В качестве основного материала при исследованиях использовали образцы из листовой лопаточной стали 20Х13 в виде пластин размером 6 × × 20 × 1 мм. В нижней части образца (рис. 3, а) было выполнено крепежное отверстие для его фиксации на державке во время эрозионных испытаний. Державку устанавливали и закрепляли на штанге гидроударного стенда. Измерение исходных профилей длиной 11 мм проводили на механическом профилометре Dektak 150 в соответствии со схемой (рис. 3, б).
Рис. 3.
Крепление образца в держателе для эрозионных испытаний (a) и схема измерения профилей поверхности (б)
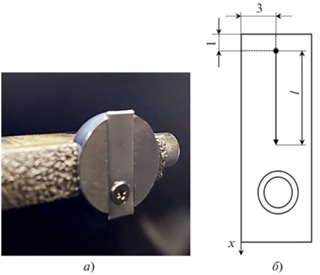
Первичные профили сглаживали (рис. 4) с использованием программного обеспечения профилометра путем исключения из них составляющей шероховатости и частично волнистости. После получения предварительных профилей поверхности выполняли модификацию поверхности образцов. Варианты модификации поверхности образцов стали 20Х13 и их обозначения приведены далее:
Борирование: |
тип I………………………………………Б(I) |
тип II……………………………………..Б(II) |
Азотирование: |
тип I………………………………………А(I) |
тип II……………………………………..А(II) |
тип III……………………………………А(III) |
Покрытие Cr-CrC: |
тип I………………………………………П(I) |
тип II……………………………………..П(II) |
тип III……………………………………П(III) |
Азотирование с П(I): |
тип I……………………………………..А(I) + П(I) |
тип II…………………………………….А(II) + П(I) |
тип III……………………………………А(III) + П(I) |
Азотирование с П(III): |
тип I……………………………………..А(I) + П(III) |
тип II……………………………………А(II) + П(III) |
тип III………………………….……….А(III) + П(III) |
Лазерная обработка…………………….……..Л |
Лазерная обработка с покрытием: |
П(I)………………………………….…..Л + П(I) |
П(II)……………………………………..Л + П(II) |
Покрытие с последующей лазерной обработкой: |
тип I……………………………………..П(I) + Л |
тип II…………………………………....П(II) + Л |
тип III…………………………………...П(III) + Л |
Рис. 4.
Характерный вид разделения первичного профиля (1) изогнутой поверхности на сглаженный профиль (2) для определения изгиба и профиль шероховатости (3)
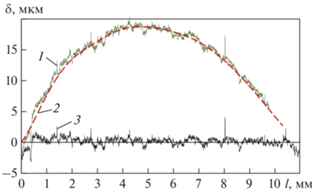
Борирование образцов стали 20Х13 выполняли в шахтной печи STC 35/50 с внешним обогревом в расплаве на основе тетрабората натрия, фтористых и хлористых солей натрия. Были проведены два технологических процесса, которые включали в себя подогрев и выдержку образцов при температуре 350°С в течение 2 ч, выдержку образцов в ванне борирования при температуре 880°С в течение 3 и 6 ч (I и II типы борирования) и закалку образцов в масле при подогреве до 90°С. Для определения влияния температур процесса борирования на свойства и микроструктуру лопаточных сталей требуются отдельные исследования. Высокая эрозионная стойкость борированных образцов обусловливает необходимость их изучения как перспективного способа противоэрозионной защиты. Такая модификация поверхности реальных изделий (рабочих лопаток паровых турбин), т.е. создание на них борированного слоя, может быть проведена только благодаря реализации других технологических процессов, в частности ионно-плазменных, для которых свойственны температуры, не влияющие на микроструктуру лопаточных сталей.
Ионное азотирование образцов стали 20Х13 проводили в течение 2.5, 5.0 и 10.0 ч (I, II и III типы азотирования) с использованием опытно-промышленной установки “Гефест+” в НИУ МЭИ. Процесс ионного азотирования поверхности образцов включал в себя: предварительную подготовку поверхностей образцов (удаление загрязнений, обезжиривание поверхности и ее полировку), загрузку образцов в вакуумную камеру, откачку вакуумной камеры до высокого вакуума с предварительным нагревом до температуры 150°С, ионную очистку поверхности и ионное азотирование.
Нанесение покрытия Cr-CrC на образцы стали 20Х13 выполняли ионно-плазменным методом в течение различного времени (для получения покрытий I, II и III типов) также с использованием установки “Гефест+”. Для формирования покрытия использовали мишени-катоды из хрома (99.9%). Технологический процесс формирования покрытий включал в себя предварительную подготовку поверхностей образцов и загрузку их в камеру, откачку камеры до высокого вакуума с предварительным нагревом образцов, ионную очистку и формирование покрытия на поверхности образцов. Распыление хрома осуществляли в среде реакционного газа. Для формирования подслоев из карбида хрома (CrС) использовали метан высокой чистоты. При нанесении чистого хрома (в качестве адгезионного подслоя и промежуточных слоев) реакционный газ не подавали.
Формирование рельефа на поверхности образцов стали 20Х13 проводили с использованием лазерного комплекса FMark NS-FB-20 на базе инфракрасного иттербиевого волоконного лазера. Обработку поверхности экспериментальных образцов из стали 20Х13 выполняли лазерными импульсами частотой 50 кГц при скорости линейного перемещения луча 500 мм/с и мощности источника 20 Вт при продольном направлении бороздок и параллельном их расположении одна относительно другой.
После модификации проводили повторное измерение профилей поверхности в тех же областях и той же длины, что и для предварительных профилей, а также их сглаживание (аналогичное выполненному на предварительных профилях). После вычитания сглаженных предварительных профилей поверхности определяли нормальные изгибы δ и приведенные нормальные изгибы δ/l, зависящие от напряжений в поверхностном слое стали 20Х13, обусловленных выполненной модификацией.
После измерения профилей поверхности изготавливали поперечные металлографические шлифы для измерения толщины модифицированного поверхностного слоя. Исследование металлографических шлифов проводили на сканирующем электронном микроскопе TESCAN MIRA 3 LMU с катодом с полевой эмиссией в режиме обратноотраженных электронов. Помимо толщины поверхностного слоя на экспериментальных образцах дополнительно исследовали и анализировали их элементный состав с использованием спектрометра X-Max 50, установленного на электронный микроскоп MIRA 3 LMU. Микротвердость модифицированного слоя определяли с помощью твердомера DuraScan 20.
После измерения толщины рассчитывали напряжения по формуле (2) при Е = 218 ГПа и ν = = 0.27. Влияние температуры при модификации поверхности на значения модуля Юнга и коэффициент Пуассона не учитывали.
Помимо оценки напряжений в модифицированном слое проводили также эрозионные испытания образцов с различными вариантами модификации с применением гидроударного стенда “Эрозия-М” НИУ МЭИ, схема которого показана на рис. 5.
Гидроударный стенд – это испытательная установка роторного типа, работающая следующим образом. Два исследуемых образца крепятся на концах вращающейся в вакуумной камере штанги и пересекают вертикальный поток капель жидкости, выходящий из специального генератора капель. Испытания экспериментальных образцов на эрозионном стенде проводятся при заданных скоростях соударения капель жидкости Суд, м/с, с образцами. Схема соударения капель диаметром dк, м, с поверхностью исследуемых образцов, реализуемая в эрозионном стенде, показана на рис. 6.
После окончания эрозионных испытаний строили кривые эрозионного износа исследуемых образцов в виде зависимости потери массы Δm от времени экспонирования на стенде τ и рассчитывали длительность инкубационного периода τинк и удельную подведенную энергию Еинк, соответствующую его окончанию.
Для определения энергии Еинк по результатам, полученным на гидроударном стенде, сначала вычисляли кинетическую энергию одной капли Еi, Дж, по соотношению
где ${{G}_{{\text{к}}}} = {{v}_{{\text{к}}}}{{\rho }_{{\text{в}}}} = \frac{{\pi d_{{\text{к}}}^{3}}}{6}{{\rho }_{{\text{в}}}}$ – масса одной капли, кг; ${{v}_{{\text{к}}}}$ – объем капли, м3; ρв – плотность воды, кг/м3.Площадь эродированной поверхности Sэр рассчитывали по формуле
где lэр – средняя высота зоны эрозионного износа, м.Число капель Nк, ударившихся об образец за время экспонирования τ, вычисляли по формуле
где ${{K}_{{\text{c}}}} = \frac{{{{l}_{{{\text{эр}}}}}}}{{2\;{{d}_{{\text{к}}}}}}$ – коэффициент улавливания; lэр − средняя высота зоны эрозионного износа, м; b – число потоков капель; nуд = Суд/(π Ds) – частота соударения, с−1; Ds – диаметр крепления образцов на штанге, м.Таким образом, параметр, характеризующий энергию жидкости, подведенную к единице площади эродированной поверхности, Еж, Дж/м2, можно определить по формуле
Вычисленное по формуле (6) значение удельной энергии воздействия потока капель позволяет учитывать основные варьируемые в испытаниях параметры соударения и может использоваться в качестве единого параметра при построении зависимостей напряжений в поверхностном слое от условий каплеударного воздействия. Удельная подведенная энергия Еинк, соответствующая окончанию инкубационного периода, таким образом, составляет
(7)
${{E}_{{{\text{инк}}}}} = \frac{{{{\rho }_{{\text{в}}}}b}}{{24}}\frac{{{{d}_{{\text{к}}}}}}{{{{D}_{s}}}}C_{{{\text{уд}}}}^{3}{{\tau }_{{{\text{инк}}}}},$При проведении эрозионных испытаний модифицированной поверхности образца стали 20Х13 и стеллита диаметр капли составлял 800 мкм, скорость соударения 300 м/с.
Полученные значения удельной подведенной энергии Еинк сопоставляли со значениями измеренных приведенных нормальных изгибов δ/l и рассчитанных напряжений, обусловленных соответствующими типами модификации поверхности.
РЕЗУЛЬТАТЫ ИССЛЕДОВАНИЙ
В результате анализа металлографических шлифов было выявлено, что на поверхности образцов стали 20Х13 с борированием сформировался двухфазный боридный слой (рис. 7), имеющий игольчатую структуру и состоящий из фаз FeB и Fe2B. Отмечено также наличие переходной зоны, в которой присутствуют зерна фазы Fe2B. Общая толщина борированного слоя после процесса длительностью 3 ч [Б(I)] составляет в среднем 52 мкм, после 6 ч [Б(II)] 100 мкм. Микротвердость борированного слоя составляет 1800–2200 HV в фазе FeB и 1500–1800 HV в фазе Fe2B.
Исследования азотированных образцов (рис. 8, a–в, ж–м) показали, что толщина слоя после азотирования в течение 2.5 ч [А(I)] составляет в среднем 24 мкм, после 5 ч [А(II)] 56 мкм, после 10 ч [А(III)] 104 мкм. В процессе ионно-плазменного азотирования происходило выделение нитридных включений (размером от 0.1 до 1.0 мкм) как внутри, так и по границам зерен. Микротвердость азотированного слоя при ионно-плазменном азотировании в течение 2.5 ч составляет в среднем 610 HV, при 5 ч 1120 HV, при 10 ч 1080 HV.
Рис. 7.
Характерный вид поверхностного слоя образцов стали 20Х13 с модификацией поверхности по типу Б(I) (а) и Б(II) (б)
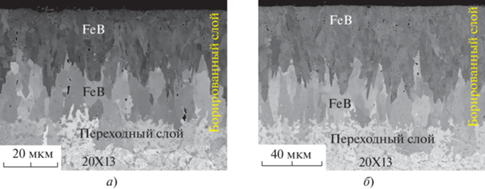
При исследовании образцов с покрытием Cr-CrC (см. рис. 8, г–м) было установлено, что покрытие типа П(I) средней толщиной 7.5 мкм − четыреххслойное, хромовые слои толщиной 0.8–1.0 мкм чередуются со слоями CrС толщиной 2.7–3.0 мкм. Покрытие типа П(II) средней толщиной 15 мкм состоит из аналогичных чередующихся восьми слоев хрома и карбида хрома. Покрытие типа П(III) средней толщиной 18 мкм – двухслойное, в нем располагается толстый нижний слой хрома толщиной 5–6 мкм. В пределах каждого слоя покрытия имеют волокнистую структуру. Микротвердость покрытия П(I) составляет в среднем 1760 HV, покрытия П(II) − 1920 HV и покрытия П(III) − 1840 HV.
Рис. 8.
Характерный вид поверхностного слоя образцов стали 20Х13 с различными типами модификации поверхности. а – А(I); б – А(II); в – А(III); г – П(I); д – П(II); е – П(III); ж – А(I) + П(I); з – А(II) + П(I); и – А(III) + П(I); к – А(I) + + П(III); л – А(II) + П(III); м − А(III) + П(III)
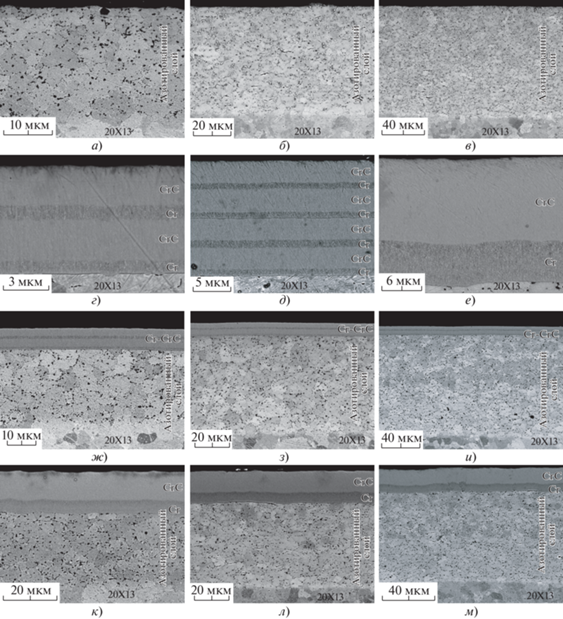
По результатам измерений, проведенных на изображениях поверхности и поперечного шлифа, геометрические параметры рельефа, сформированного после лазерной обработки экспериментальных образцов (рис. 9, a), имеют следующие средние значения: глубина впадины и высота выступа 15 мкм, ширина выступа 50 мкм, ширина впадины 50 мкм. Около поверхности также отмечается тонкий (примерно 5 мкм) поверхностный слой материала с измененным зерном. Общая толщина слоя материала, модифицированного при лазерной обработке, в среднем составляет 20 мкм.
Рис. 9.
Характерный вид поверхностного слоя образцов стали 20Х13 с различными типами модификации поверхности. а – Л; б – Л + П(I); в – Л + П(II); г − П(I) + Л; д − П(II) + Л; е − П(III) + Л
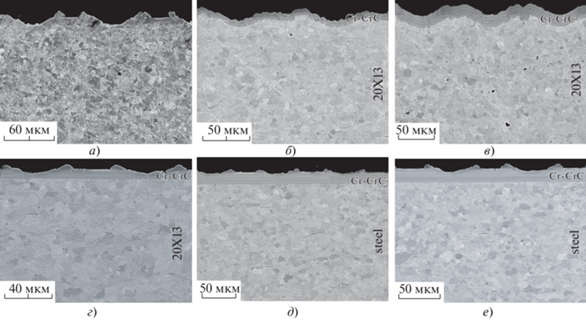
При нанесении покрытия Cr-CrC на рельеф, сформированный на поверхности при лазерной обработке, происходит лишь частичное сглаживание и заращивание дефектов поверхности (рис. 9, б–в). Микроструктура покрытия при формировании на рельефе аналогична микроструктуре на поверхности без него, но имеется большее количество дефектов на границе сталь 20Х13 − покрытие. Лазерная обработка поверхности стали 20Х13 с покрытием Cr-CrC приводит к снятию части покрытия и перенапылению его с образованием выступов (рис. 9, г–е).
При исследовании напряжений в поверхностном слое стали 20Х13, обусловленных модификацией для всех рассмотренных образцов, были измерены профили поверхности до и после модификации. Характерный вид сглаженных профилей поверхности образцов с различными вариантами модификации образцов стали 20Х13 после вычитания исходных профилей показан на рис. 10. Полученные по профилям значения приведенных нормальных изгибов δ/l, вызванных модификацией и зависящих от напряжений, для различных вариантов модификации поверхности образцов стали 20Х13 показаны на рис. 11.
Рис. 10.
Характерный вид сглаженных профилей поверхности образцов стали 20Х13 при борировании и азотировании (а) и покрытии Cr-Cr-C и лазерной обработке (б) после вычитания исходных профилей. 1 − Б(I); 2 − Б(II); 3 − А(I); 4 − А(II); 5 − А(III); 6 − А(I) + П(I); 7 − А(II) + П(I); 8 − А(III) + П(I); 9 − А(I) + П(III); 10 − А(II) + П(III); 11 − А(III) + П(III); 12 − П(I); 13 − П(II); 14 − П(III); 15 − Л; 16 – Л + П (I); 17 – Л + П(II); 18 − П(I) + Л; 19 − П(II) + Л; 20 − П(III) + Л
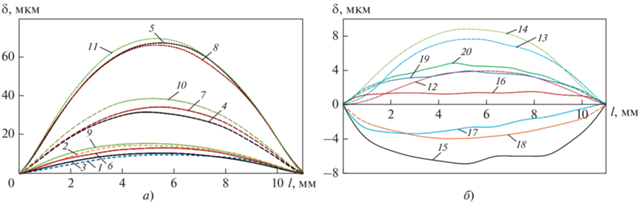
Рис. 11.
Приведенный нормальный изгиб при борировании и азотировании (а) и покрытии Cr-Cr-C и лазерной обработке (б) поверхности стали 20Х13
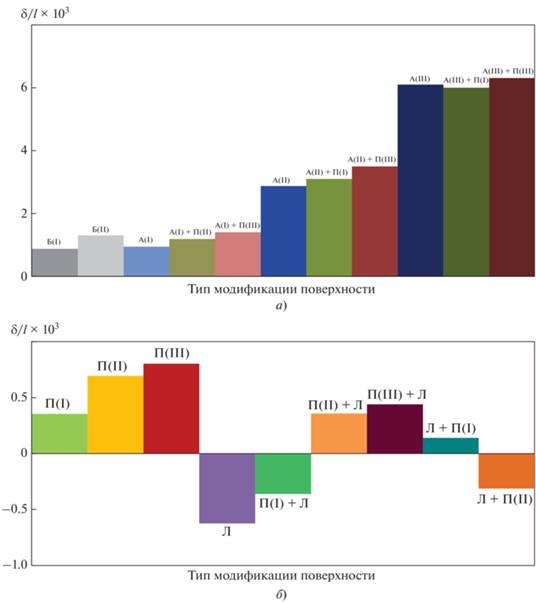
Приведенный нормальный изгиб после борирования, азотирования, нанесения покрытия Cr-CrC (см. рис. 10, a, 11) – положительный, увеличивается при росте толщины слоя. Вследствие азотирования изгиб увеличивается в большей степени, нежели при этом возрастает толщина азотированного слоя, что свидетельствует о повышении напряжений при увеличении длительности азотирования. Образцы с азотированием обладают наибольшими внутренними напряжениями, образующимися в поверхностном слое в результате модификации поверхности, из всех рассмотренных вариантов.
Рассчитанные по формуле (2) напряжения, обусловленные модификацией образцов, показаны на рис. 12. Напряжения в слое после азотирования в течение 5 ч в 1.4 раза выше, чем при длительности процесса 2.5 ч, различие в напряжениях при 5 и 10 ч азотирования незначительное (около 9%). Для азотирования типа I напряжения составляют 1.4 ГПа, для азотирования типа II − 1.9 ГПа, для азотирования типа III − 2.1 ГПа.
Изгиб после борирования и нанесения покрытия увеличивается в меньшей степени, нежели при этом возрастает толщина борированного слоя или толщина покрытия Cr-CrC, что свидетельствует об уменьшении напряжений при увеличении длительности борирования или формирования покрытия данного типа. Оценка напряжений показывает, что напряжения в борированном слое при 3 ч борирования в 1.3 раза выше, чем при 6 ч. Напряжения при 3 ч борирования (тип I) составляет 0.61 ГПа, при 6 ч (тип II) − 0.47 ГПа.
Напряжения в покрытии Cr-CrC при увеличении толщины покрытия уменьшаются, но незначительно. Для толщины покрытия Cr-CrC 7.5−18.0 мкм средние напряжения составляют 1.6–1.7 ГПа.
В случае азотирования с последующим нанесением покрытия вклад в общий изгиб, обусловленный данной комбинацией модификаций поверхности, тем больше, чем меньше толщина азотированного слоя и больше толщина покрытия (см. рис. 10, a, 11). В случае азотирования типа I (2.5 ч) с покрытием типа III Cr-CrC толщины азотированного слоя и покрытия сопоставимы, при этом напряжения наименьшие в комбинации азотирование с покрытием.
При формировании рельефа путем лазерной обработки наблюдается отрицательный нормальный изгиб образцов (см. рис. 10, б, 11).
При нанесении покрытия Cr-CrC на поверхность после лазерной обработки происходит уменьшение изгиба (см. рис. 10, б, 11) по сравнению с изгибом образцов после лазерной обработки и по сравнению с изгибом образцов после нанесения покрытия, что обусловлено разнонаправленным действием на изгиб поверхности комбинируемых типов модификации: лазерного воздействия (отрицательный изгиб) и нанесения покрытия (положительный изгиб). Таким образом, при применении данной комбинации модификаций можно уменьшить итоговые напряжения.
Лазерная обработка, проводимая после нанесения покрытия Cr-CrC, также приводит к меньшему итоговому изгибу образцов (см. рис. 10, б, 11) по сравнению с изгибом стали 20Х13 без покрытия после лазерной обработки из-за разнонаправленного действия на изгиб комбинируемых типов модификации поверхности: нанесения покрытия (положительный изгиб) и лазерного воздействия (отрицательный изгиб). С ростом толщины покрытия наблюдается переход от отрицательного изгиба к положительному. При комбинации модификации поверхности, включающей нанесение покрытия Cr-CrC с последующей или предварительной лазерной обработкой, можно достичь требуемого знака и уровня напряжений путем выбора соответствующей толщины покрытия.
В результате испытаний образцов из стали 20Х13 с азотированием и покрытием Cr-CrC были получены кривые эрозионного износа (рис. 13), по которым определяли длительности инкубационного периода, использовавшиеся для последующего расчета Еинк. Для сравнения на рис. 13 также приведены кривые эрозионного износа стали 20Х13 без модификации и литого стеллита.
Рис. 13.
Кривые эрозионного износа стали 20Х13 при азотировании (а) и азотировании с покрытием (б) и стеллита. 1 − сталь 20Х13; 2 – стеллит; 3 – А(I); 4 – А(II); 5 – А(III); 6 – А(I) + П(I); 7 – А(II) + П(I); 8 – П(I)
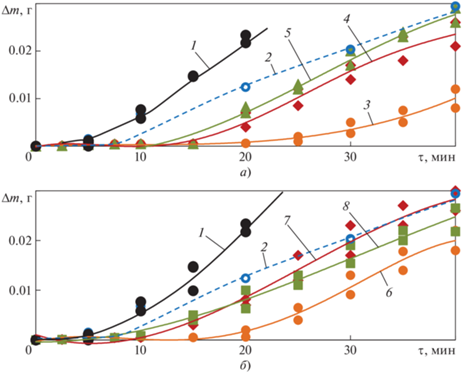
Рассчитанные по формуле (7) значения удельной подведенной энергии Еинк, Дж/мм2, приведены далее:
Сталь 20Х13……………………….............………..230 |
Стеллит………………………………..............…….322 |
Сталь 20Х13 после модификации: |
А(I)…………………………………....................830 |
А(II)………………………………..............…....460 |
А(III)………………………………...................440 |
А(I) + П(I)…………………..............…………600 |
А(II) + П(I)……………………..............……..370 |
П(I)…………………………..............……….....310 |
Значения Еинк сопоставляли с рассчитанными напряжениями в поверхностном слое, возникающими вследствие модификации. Изменение Еинк в зависимости от напряжений для наиболее перспективных типов модификации (стали 20Х13 с азотированием и/или с покрытием Cr-CrC) показано на рис. 14.
Рис 14.
Зависимость удельной энергии Еинк от внутренних напряжений σ в поверхностном слое образцов стали 20Х13 при различных типах модификации
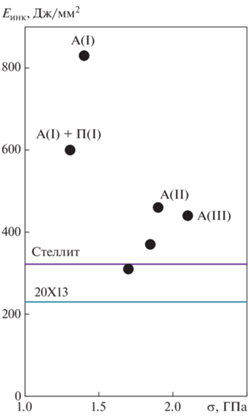
Для рассмотренных вариантов модификации поверхности стали 20Х13 увеличению напряжений соответствует снижение удельной подведенной энергии Еинк, т.е. ухудшение эрозионной стойкости. Наибольшей Еинк соответствует азотирование типа I со средней толщиной азотированного слоя 24 мкм. Увеличение толщины азотированного слоя (в рамках рассмотренного диапазона толщин) приводит к увеличению напряжений и уменьшению энергии Еинк. Нанесение на азотированную поверхность стали 20Х13 покрытия Cr-CrC также, как правило, приводит к снижению Еинк при увеличении напряжений.
ВЫВОДЫ
1. Максимальные значения приведенного нормального изгиба, обусловленные лазерной обработкой, наблюдаются при формировании рельефа на образцах стали 20Х13 с покрытием Cr-CrC толщиной 7.5 мкм, минимальные – на образцах без покрытия. При этом характер изгиба свидетельствует о наличии сжимающих напряжений в поверхностном слое. Нанесение покрытия Cr-CrC на поверхность после лазерной обработки уменьшает итоговый уровень напряжений. При комбинации типов модификации поверхности, включающей нанесение покрытия Cr-CrC и последующую лазерную обработку, с ростом толщины покрытия наблюдается переход от сжимающих к растягивающим напряжениям в поверхностном слое. С использованием данной комбинации типов модификации поверхности можно достигать требуемого знака и уровня напряжений в поверхностном слое путем выбора соответствующей толщины покрытия. Тем не менее, рассмотренные комбинации лазерной обработки и нанесения покрытия не позволяют получить большую, по сравнению со стеллитом, эрозионную стойкость на этапе инкубационного периода.
2. Борирование приводит к повышению стойкости к каплеударному воздействию на этапе до начала разрушения. Характер нормального изгиба свидетельствует о том, что в случае борирования поверхности массивных изделий типа турбинных лопаток поверхностный слой будет находиться в сжатом состоянии по сравнению с материалом основы.
3. Реализация процесса азотирования приводит к увеличению эрозионной стойкости в 1.5–2.0 раза на этапе инкубационного периода по сравнению со стеллитом. Уменьшение глубины азотированного слоя вызывает снижение возникающих напряжений, оптимальной глубиной азотирования является средняя глубина 24 мкм.
4. Формирование покрытий Cr-CrC разной толщины на стали 20Х13 приводит к образованию напряжений различного уровня. Проведенные измерения свидетельствуют о сжатом состоянии покрытия при нанесении его на поверхность массивных изделий, к которым можно отнести рабочие лопатки последних ступеней паровых турбин.
5. Объединение покрытия Cr-CrC разной толщины с несколькими типами азотирования приводит к снижению напряжений в этих комбинациях, но при этом к меньшей эрозионной стойкости, превосходящей, тем не менее, стойкость стеллита.
6. Зависимости удельной подведенной энергии от внутренних напряжений в поверхностном слое могут использоваться для прогнозирования эрозионной стойкости при модификации по измеренному уровню напряжений на этапе выбора способа защиты.
Список литературы
Leyzerovich A.S. Steam turbines for modern fossil-fuel power plants. Lilburn: Fairmont Press, 2008.
Рыженков В.А., Лебедева А.И., Медников А.Ф. Современное состояние и способы решения проблемы эрозионного износа лопаток влажно-паровых ступеней турбин // Теплоэнергетика. 2011. № 9. С. 8−13.
Ahmad M., Casey M., Sürken M. Experimental assessment of droplet impact erosion resistance of steam turbine blade materials // Wear. 2009. V. 267. No. 9–10. P. 1605–1618. https://doi.org/10.1016/j.wear.2009.06.012
Hesketh J.A., Walker P.J. Effects of wetness in steam turbines // Proc. Inst. Mech. Eng. C: J. Mech. Eng. Sci. 2005. V. 219. No. 12. P. 1301–1314. https://doi.org/10.1243/095440605X32110
Ahmad M., Schatz M., Casey M.V. Experimental investigation of droplet size influence on low pressure steam turbine blade erosion // Wear. 2013. V. 303. No. 1–2. P. 83–86. https://doi.org/10.1016/j.wear.2013.03.013
Development of a water droplet erosion model for large steam turbine blades / B.E. Lee, K.J. Riu, S.H. Shin, S.B. Kwon // KSME Int. J. 2003. V. 17. No. 1. P. 114–121. https://doi.org/10.1007/BF02984292
HVOF sprayed coatings of nano-agglomerated tungsten-carbide/cobalt powders for water droplet erosion application / M.S. Mahdipoor, F. Tarasi, C. Moreau, A. Dolatabadi, M. Medraj // Wear. 2015. V. 330–331. P. 338–347. https://doi.org/10.1016/j.wear.2015.02.034
Mann B.S., Arya V. HVOF coating and surface treatment for enhancing droplet erosion resistance of steam turbine blades // Wear. 2003. V. 254. No. 7–8. P. 652–667. https://doi.org/10.1016/S0043-1648(03)00253-9
Mann B.S., Arya V., Pant B.K. Cavitation erosion behavior of HPDL-treated TWAScoated Ti6Al4V alloy and its similarity with water droplet erosion // J. Mater. Eng. Perform. 2012. V. 21. No. 6. P. 849–853. https://doi.org/10.1007/s11665-011-9949-5
Liu Z. Microstructure and cavitation erosion behavior of sputtered NiCrAlTi coatings with and without N incorporations // J. Mat. Sci. Technol. 2020. V. 54. P. 211−222. https://doi.org/10.1016/j.jmst.2020.02.072
Hu H.X., Zheng Y.G., Liu C.B. Predicting the preferential sites to liquid droplet erosion of the bellows assemblies by CFD // Nucl. Eng. Des. 2011. V. 241. No. 6. P. 2295−2306. https://doi.org/10.1016/j.nucengdes.2011.03.045
Di J. Experimental investigation on effect of surface strengthening process and roughness on water droplet erosion behavior in turbomachinery // Trib. Int. 2021. V. 153. Art. No. 106647. https://doi.org/10.1016/j.triboint.2020.106647
The effect of initial surface roughness on water droplet erosion behavior / H.S. Kirols, D. Kevorkov, A. Uihlein, M. Medraj // Wear. 2015. V. 342–343. P. 198−209. https://doi.org/10.1016/j.wear.2015.08.019
Исследование эффективности применения ионно-вакуумных покрытий для защиты от коррозионного и эрозионного повреждения рабочих лопаток паровых турбин / В.И. Ногин, В.А. Рыженков, А.И. Лебедева, С.И. Погорелов // Энергосбережение и водоподготовка. 1999. № 1. С. 30−36.
State-of-the art, problems and methods to improve erosion resistance of materials used for manufacturing of turbines / G.V. Kachalin, A.F. Mednikov, A.B. Tkhabisimov, E.A. Zhukova // Res. J. Pharmaceut., Biol. Chem. Sci. 2016. V. 7. P. 955−963.
Study of the wear resistance of ion-plasma coatings based on titanium and aluminium and obtained by magnetron sputtering // G.V. Kachalin, A.F. Mednikov, A.B. Tkhabisimov, S.V. Sidorov // J. Phys: Conf. Ser. 2017. V. 857. No. 1. art. No. 012016. https://doi.org/10.1088/1742-6596/857/1/012016
Studies of the Cr-CrN coating characteristics formed by means of the magnetron sputtering method from bulk target / G.V. Kachalin, A.F. Mednikov, A.B. Tkhabisimov, S.V. Sidorov // J. Phys.: Conf. Ser. 2017. V. 872. No. 1. art. No. 012040. https://doi.org/10.1088/1742-6596/872/1/012040
The results of water droplet erosion tests of ion-plasma coatings formed on titanium Ti-6Al-4V alloy samples manufactured by using 3D-printing and traditional technological process / A.F. Mednikov, A.B. Tkhabisimov, O.S. Zilova, A.A. Burmistrov, S.V. Sidorov // IOP Conf. Ser.: Mater. Sci. Eng. 2019. V. 537. art. No. 022066. https://doi.org/10.1088/1757-899X/537/2/022066
Медников А.Ф., Тхабисимов А.Б., Качалин Г.В. Результаты эрозионных испытаний образцов из стали 20Х13 с защитным покрытием и упорядоченным рельефом // Естественные и технические науки. 2020. № 10 (148). С. 133−137.
Mednikov A.F., Tkhabisimov A.B., Kachalin G.V. Results of steel 20Kh13 samples with combined hardened-structured surface erosion tests // J. Phys.: Conf. Ser. 2020. V. 1683. art. No. 032025. https://doi.org/10.1088/1742-6596/1683/3/032025
Water droplet erosion behaviour of gas nitrided Ti6Al4V / M.S. Mahdipoor, D. Kevorkov, P. Jedrzejowski, M. Medraj // Surface and Coatings Technology. 2016. V. 292. No. 25. P. 78−89. https://doi.org/10.1016/j.surfcoat.2016.03.032
Microstructure and cavitation erosion behavior of sputtered NiCrAlTi coatings with and without N incorporations / Z. Liu, S. Zhu, M. Shen, Y. Jia, W. Wang, F. Wang // J. Mater. Sci. Technol. 2020. V. 54. No. 1. P. 211−222.
Plasma nitriding of Ti6Al4V alloy for improved water erosion resistance / D. Batory, W. Szymanski, M. Panjan, O. Zabeida, J.E. Klemberg-Sapieha // Wear. 2017. V. 374–375. P. 120−127.
Yang Q., Zhao L.R., Patnaik P. Erosion performance, corrosion characteristics and hydrophobicity of nanolayered and multilayered metal nitride coatings // Surface and Coatings Technology. 2019. V. 375. P. 763−772. https://doi.org/10.1016/j.surfcoat.2019.07.074
Ultrasonic cavitation erosion of gas nitrided Ti–6Al–4V alloys / I. Mitelea, E. Dimian, I. Bordeaşu, C. Crăciunescu // Ultrasonics Sonochem. 2014. V. 21. Is. 4. P. 1544−1548. https://doi.org/10.1016/j.ultsonch.2014.01.005
Cavitation erosion resistance and wear mechanisms of active screen low temperature plasma nitrided AISI 410 martensitic stainless steel / L.A. Espitia, H. Dong, X.‑Y. Li, C.E. Pinedo, A.P. Tschiptschin // Wear. 2015. V. 332. P. 1070−1079.
Результаты исследований эрозионной стойкости лопаточной стали 15Х11МФ с различными диффузионными покрытиями / С.Ю. Капустин, А.В. Аникеев, Г.В. Качалин, А.Б. Тхабисимов, А.Ф. Медников, А.А. Красуля // Сб. трудов III науч.-техн. конф. студентов “Энергетика. Технологии будущего”. Москва, 20−22 мая 2020 г. С. 54−58.
Влияние параметров упрочнения поверхности на эрозионную стойкость лопаточных сталей / А.В. Рыженков, А.Ф. Медников, А.Б. Тхабисимов, Г.В. Качалин // XVII Междунар. науч.-техн. конф. “Быстрозакаленные материалы и покрытия”. Москва, 2020. С. 238−243.
Mann B., Arya V. An experimental study to corelate water jet impingement erosion resistance and properties of metallic materials and coatings // Wear. 2002. V. 253. P. 650−666. https://doi.org/10.1016/S0043-1648(02)00118-7
Erosion of wind turbine blade coatings – design and analysis of jet-based laboratory equipment for performance evaluation / S. Zhang, K. Dam-Johansen, S. Nørkjær, P.L. Bernad, S. Kiil // Prog. Org. Coating. 2015. V. 78. P. 103−115. https://doi.org/10.1016/j.porgcoat.2014.09.016
Surface topography parameters as a correlation factor for liquid droplet erosion test facilities / E. Tobin, O. Rohr, D. Raps, W. Willemse, P. Norman, T. Young // Wear. 2015. V. 328. P. 318–328. https://doi.org/10.1016/j.wear.2015.02.054
Erosion of polymer-particle composite coatings by liquid water jets / B. Briscoe, M. Pickles, K. Julian, M. Adams // Wear. 1997. V. 203. P. 88−97. https://doi.org/10.1016/S0043-1648(96)07379-6
Chidambaram P.K., Kim H.-D. A numerical study on the water droplet erosion of blade surfaces // Comput Fluid. 2018. V. 164. P. 125−129. https://doi.org/10.1016/j.compfluid.2017.11.004
Khan J.R., Wang T. Three-dimensional modeling for wet compression in a single stage compressor including liquid particle erosion analysis // J. Eng Gas Turbines Power. 2011. V. 133. Art. № 012001. https://doi.org/10.1115/1.4001828
Energy based approach for understanding water droplet erosion / H. Kirols, M. Mahdipoor, D. Kevorkov, A. Uihlein, M. Medraj // Mater. Des. 2016. V. 104. P. 76−86. https://doi.org/10.1016/j.matdes.2016.04.089
Селезнев Л.И., Рыженков В.А., Медников А.Ф. Феноменология эрозионного износа материала конструкционных сталей и сплавов жидкими частицами // Теплоэнергетика. 2010. № 9. С. 12−16.
Mann B.S. Water droplet erosion behavior of high-power diode laser treated 17Cr4Ni PH stainless steel // J. Mater. Eng. Perform. 2014. V. 23. No. 5. P. 1861–1869. https://doi.org/10.1007/s11665-014-0927-6
Mechanisms of damage initiation in a titanium alloy subjected to water droplet impact during ultra-high pressure plain waterjet erosion / L. Huang, J. Folkes, P. Kinnell, P.H. Shipway // J. Mater. Process. Technol. 2012. V. 212. No. 9. P. 1906–1915. https://doi.org/10.1016/j.jmatprotec.2012.04.013
Stoney G. The tension of metallic films deposited by electrolysis // Proc. of the Royal Society of London. Series A, Containing Papers of a Mathematical and Physical Character. L.: Royal Society, 1909. P. 172−175.
Handbook of silicon based MEMS materials and technologies / V. Lindroos, M. Tilli, A. Lehto, T. Motooka. Burlington: Elsevier, 2010. https://doi.org/10.1016/C2009-0-19030-X
Методика измерения механических напряжений в тонких пленках на пластине с помощью оптического профилометра / Н.А. Дюжев, А.А. Дедкова, Е.Э. Гусев, А.В. Новак // Изв. вузов. Электроника. 2016. № 4. С. 367−372.
Internal stresses in Mo/Y multilayer mirrors / D.S. Kvashennikov, Y.A. Vainer, S.Y. Zuev, V.N. Polkovnikov // Surface. X-ray, Synchrotron and Neutron Res. 2019. V. 3. P. 14−18. https://doi.org/10.1134/S1027451019020113
Петрова А.П., Мухаметов Р.Р., Ахмадиева К.Р. Внутренние напряжения в отвержденных полиэфирных связующих для ПКМ // Труды ВИАМ. 2019. № 5 (77). С. 12−21.
Internal stresses in polymer film coatings obtained by plasma deposition / M.P. Danilaev, E. Bogogslov, Yu.E. Polsky, I. Yanilkin // Phys. Chem. Matеr. Proc. 2018. V. 3. P. 21−26. https://doi.org/10.1134/S2075113319030079
Зависимость механических напряжений в пленках нитрида кремния от режимов плазмохимического осаждения / А.В. Новак, В.Р. Новак, А.А. Дедкова, Е.Э. Гусев // Изв. вузов. Электроника. 2017. Т. 22. № 2. С. 138−146.
Асташенкова О.Н., Корляков А.В. Механизмы формирования механических напряжений в пленках карбида кремния и нитрида алюминия, полученных магнетронным методом // Современная наука: исследования, идеи, результаты, технологии. 2014. № 2 (15). С. 57−61.
Ayvazyan G.E. On the determination of internal stresses in the film substrate system // Proc. of the NAS RA and SEUA. Ser. TN. 2000. V. 53. No. 1. P. 63−67.
Obtaining a superhard nanocomposite film by coaxial plasma deposition / H. Naragino, M. Egiza, A. Tominaga, T. Yoshitake // Laboratory and Production. 2019. V. 6. No. 2. P. 156−160.
Гибридное просветляющее покрытие с алмазоподобным слоем / И.С. Гайнутдинов, М.Х. Азаматов, А.В. Михайлов, А.Н. Галиев, И.З. Нуруллин, С.Н. Шушарин // Оптический журн. 2015. Т. 82. № 1. P. 70−73.
Дополнительные материалы отсутствуют.
Инструменты
Теплоэнергетика