Теплоэнергетика, 2022, № 11, стр. 50-56
Комплексная алюмоводная технология получения водорода
Э. П. Волков a, Е. И. Школьников a, *
a Объединенный институт высоких температур РАН
125412 Москва, Ижорская ул., д. 13, стр. 2, Россия
* E-mail: 1shkolnikov@mail.ru
Поступила в редакцию 01.02.2022
После доработки 23.03.2022
Принята к публикации 28.05.2022
- EDN: ZIXZGK
- DOI: 10.56304/S0040363622110108
Аннотация
В настоящей работе изложены особенности гидротермального окисления дисперсного алюминия и обосновывается перспективность его использования для массового производства “безуглеродного” водорода. В процессе гидротермального окисления алюминий взаимодействует с водой или паром. При этом образуются водород без примеси углерода или его соединений и тепловая энергия. Твердым продуктом окисления алюминия является гидроксид алюминия. В статье описывается комплексная малоотходная алюмоводная технология с использованием одного расходуемого агента – электроэнергии. Технология подразумевает восстановление до металла полученного гидроксида алюминия в рамках одного производства. Регенерированный в процессе электролиза алюминий снова возвращается в цикл для восстановления водорода из воды в реакции гидротермального окисления. Если при электролизе алюминия применять разработанные относительно недавно инертные аноды, а также использовать электроэнергию, вырабатываемую на ГЭС или АЭС, то в технологии будет отсутствовать углеродный след. Разобраны массово-энергетические характеристики и состав продуктов каждого из основных процессов комплексной алюмоводной технологии, а именно: восстановления алюминия из Al2O3 электролизом для возвращения его в цикл производства водорода; гидротермального окисления алюминия с получением на выходе пароводородной смеси и конденсированной смеси воды и бемита; выделения оксида алюминия Al2O3 из бемита AlOOH; получения чистого водорода из пароводородной смеси, а также воды для повторного использования; компримирования водорода. Серьезное внимание уделено потенциальной возможности утилизации тепловой энергии пароводородной смеси для компримирования водорода. Вследствие получения при реализации технологии гидротермального окисления алюминия большого количества низкопотенциального тепла возможно использовать термосорбционный компрессор для сжатия водорода до рабочих параметров (40–90 МПа). Это позволяет более чем на порядок уменьшить эксплуатационные расходы на сжатие водорода по сравнению с традиционными механическими компрессорами и одновременно повысить эффективность гидротермального окисления алюминия.
В настоящее время в большинстве экономически развитых стран активно реализуются программы внедрения в экономику водородных энергетических технологий. При этом одной из наиболее актуальных задач является организация экономически эффективного массового производства высококачественного, химически чистого водорода, которое не сопровождалось бы массированным выбросом в атмосферу парниковых газов. С этой точки зрения весьма перспективной оказывается технология гидротермального окисления алюминия (ГТОА). Первый продукт этой технологии – газообразный, состоящий из водорода и водяного пара. Второй продукт – конденсированный, состоит из бемита и воды.
В процессе гидротермального окисления алюминий взаимодействует с водой или паром, в результате образуется водород без примеси углерода или его соединений. При этом из реактора ГТОА выделяются пароводородная смесь и конденсированный продукт, состоящий из бемита AlOOH и воды, а также тепловая энергия. Продуктом окисления алюминия в зависимости от температуры процесса может быть не бемит, а оксид алюминия Al2O3. Оксид алюминия можно выделить из бемита также путем кальцинирования. Полученный оксид алюминия восстанавливается до металла в процессе электролиза. Алюминий снова возвращается в цикл для восстановления водорода из воды в реакции гидротермального окисления (рис. 1). Такая технология получения водорода по основным рабочим веществам, участвующим в процессе, называется алюмоводной.
Рис. 1.
Схема производства “безуглеродного” водорода на основе реакции гидротермального окисления алюминия
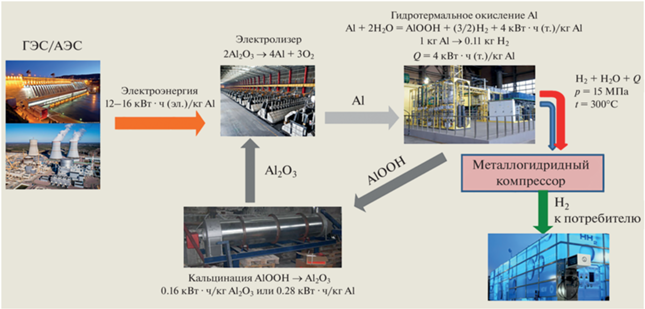
При электролитическом производстве алюминия может использоваться традиционная технология Hall-Heroult (далее Холл-Эру) с применением углеродных анодов. В этом случае наблюдается выделение углекислого газа, образующегося при взаимодействии кислорода и углеродного анода, что не позволяет считать технологию Холл-Эру экологически чистой. В связи с этим в мире интенсивно разрабатываются и внедряются технологии электролиза алюминия с использованием инертных анодов [1, 2], которые не взаимодействуют с кислородом. В процессе электролиза с использованием таких анодов выделяется кислород, а не углекислый газ. Если при этом для электролиза использовать электроэнергию, вырабатываемую на ГЭС или АЭС, то при получении водорода выделение парниковых газов будет исключено.
Цикл производства водорода по комплексной алюмоводной технологии состоит из следующих процессов:
восстановление алюминия из Al2O3 путем электролиза и возвращение его в цикл производства водорода;
гидротермальное окисление алюминия, дающее на выходе пароводородную газовую смесь и конденсированную смесь воды и бемита AlOOH;
кальцинация оксида алюминия Al2O3 из бемита;
выделение чистого водорода путем конденсации из пароводородной смеси воды и ее сепарация для повторного использования;
компримирование водорода до давления 90 МПа;
утилизация тепловой энергии пароводородной смеси.
ВОССТАНОВЛЕНИЕ АЛЮМИНИЯ ИЗ Al2O3
Расход электроэнергии E на получение алюминия из глинозема с помощью электролиза (в процессе Холл-Эру) оценивается в диапазоне от 12 до 16 кВт · ч/кг Al. По информации, предоставленной авторам дирекцией ОК “Русал”, которая в настоящее время является единственной в мире компанией, имеющей опыт промышленного производства алюминия с использованием инертных анодов, затраты на производство инертных анодов больше, чем затраты на производство углеродных, расход электроэнергии на электролиз с использованием инертных анодов также несколько выше, чем в процессе Холл-Эру. Однако ресурс инертных анодов существенно выше, чем ресурс их угольных аналогов. В целом суммарные затраты электроэнергии и текущие расходы при эксплуатации для обоих видов анодов оказываются примерно одинаковыми. Ввиду отсутствия детальной информации о технико-экономических характеристиках электролиза с инертными анодами в концептуальных расчетах далее будет использоваться среднее значение расхода электроэнергии при электролизе E = 14 кВт · ч/кг Al. В ходе окисления 1 кг алюминия водой по стехиометрии выделяется 0.11 кг водорода. Время работы установки в течение года составляет 8760 ч.
Далее рассматриваются основные параметры процесса получения водорода при гидротермальном окислении алюминия на примере сравнительно крупной (концептуальной) установки производительностью 72 т водорода в год. В этом случае секундный массовый расход алюминия ġAl можно определить по выражению
где ${{P}_{{{{{\text{H}}}_{2}}}}}$ – производительность установки, кг H2/год; s – стехиометрический массовый выход водорода, кг Н2/кг Al; τ – период работы установки в году, ч/год.Для используемых значений приведенных параметров установки секундный массовый расход алюминия будет равен 0.02 кг Al/c. При удельном расходе электроэнергии 14 кВт · ч/кг Al секундный расход соответствует мощности установки
(2)
$W = E{{\dot {g}}_{{{\text{Al}}}}} \times 3600 = 0.02\; \times \;14\; \times \;3600 = 1008\;{\text{кВт}}{\text{.}}$Массово-энергетический баланс электролизера в расчете на 1 кг водорода при его производительности по алюминию 20 г/с приведен на рис. 2.
В зависимости от соотношения расходов воды и алюминия можно получить большой спектр продуктов реакции в широком диапазоне температуры в реакторе ГТОА. В рассматриваемом случае, когда это соотношение равно 6:1 [3], начальная температура реагентов составляет 300 К и давление в реакторе 15 МПа, процесс происходит с образованием бемита по формуле
(3)
${\text{Al}} + 2{{{\text{H}}}_{2}}{\text{O}} \to \operatorname{AlOOH} \,\, + 1.5{{{\text{H}}}_{2}}.$Расход алюминия в этой реакции, согласно (1), равен 0.02 кг/с, воды − 0.122 кг/с. Данный расход воды является избыточным по сравнению со стехиометрическим соотношением для реакции (3). Результирующая температура реакции составляет 598.4 К. Это значение, как и остальные результаты по состояниям рабочих тел и составам продуктов реакции (табл. 1‒7), получены с помощью программы расчета термодинамического равновесия в многокомпонентной гетерогенной системе с использованием свойств индивидуальных веществ из базы данных ИВТАНТЕРМО [4].
Таблица 1.
Состав продуктов реакции
Вещество | Доля | ||
---|---|---|---|
мольная | массовая | объемная | |
Водяной пар | 0.7166 | 0.6494 | 0.8215 |
AlOOH | 0.1038 | 0.3131 | − |
H2 | 0.1557 | 0.0158 | 0.1785 |
H2O | 0.0239 | 0.0217 | − |
Таблица 2.
Состав газообразного и конденсированного продуктов
Вещество | Доля | ||
---|---|---|---|
мольная | массовая | объемная | |
Газообразный продукт | |||
Водяной пар | 0.8215 | 0.9763 | 0.8215 |
H2 | 0.1785 | 0.0237 | 0.1785 |
Конденсированный продукт | |||
AlOOH | 0.8125 | 0.9352 | ‒ |
H2O | 0.1875 | 0.0648 | ‒ |
Таблица 3.
Состав конденсированной фазы
Вещество | Доля | ||
---|---|---|---|
мольная | массовая | объемная | |
AlOOH | 0.8125 | 0.9352 | ‒ |
H2O | 0 | 0 | ‒ |
Водяной пар | 0.1875 | 0.0648 | 1.0 |
Таблица 4.
Восстановление оксида алюминия γ-Al2O3
Вещество | Доля | ||
---|---|---|---|
мольная | массовая | объемная | |
γ-Al2O3 | 0.5003 | 0.85 | − |
Водяной пар | 0.4997 | 0.15 | 1.0 |
Таблица 5.
Состав охлажденной пароводородной смеси при 290 К
Вещество | Доля | ||
---|---|---|---|
мольная | массовая | объемная | |
Водяной пар | 4.285 × 10‒5 | 5.092 × 10‒5 | 2.401 × 10‒4 |
H2 | 0.1785 | 0.02373 | 0.9999 |
H2O | 0.8215 | 0.9762 | ‒ |
Таблица 6.
Состав товарного водорода при 290 К и 6 МПа
Вещество | Доля | ||
---|---|---|---|
мольная | массовая | объемная | |
Водяной пар | 2.401 × 10‒4 | 0.002141 | 2.401 × 10‒4 |
H2 | 0.9998 | 0.9979 | 0.9999 |
Таблица 7.
Предварительные характеристики ТСКВ и механического компрессора
Параметр | Компрессор | |
---|---|---|
ТСКВ | механический | |
Объемный расход водорода, м3/ч | 90.7 | 90.7 |
(при нормальных условиях) | ||
Давление, МПа: | ||
на входе в компрессор | 6 | 6 |
на выходе из компрессора | 100 | 100 |
Количество ступеней | Не менее 2 | 3 |
Масса металлогидрида, кг | Не менее 360 | ‒ |
Общая масса, кг | Не более 800 | Не более 5760 |
Объем системы, м3 | 0.2 | 9.6 |
Требуемая тепловая мощность, кВт | 67* | ‒ |
Электрическая мощность, кВт | 1 | 20 |
Как уже отмечалось ранее, на выходе реактора ГТОА образуются два продукта (рис. 3), составы которых приведены в табл. 1‒3. Первый – газообразный, состоящий из водорода и водяного пара. Его массовая доля в общем расходе согласно проведенным расчетам составляет 0.6494 + 0.0158 = = 0.6652. Второй продукт – конденсированный, состоит из бемита и воды, его массовая доля в общем расходе 0.3131 + 0.0217 = 0.3348. В газообразном продукте массовая доля водяного пара равна 0.6494/(0.6494 + 0.0158) = 0.9760, а в конденсированном массовая доля бемита составляет 0.3131/(0.3131 + 0.0217) = 0.9350.
ВОССТАНОВЛЕНИЕ ОКСИДА АЛЮМИНИЯ ИЗ КОНДЕНСИРОВАННОЙ ФАЗЫ
В рассматриваемом случае из реактора выходит 0.04755 кг/с конденсированной смеси (см. рис. 3), состоящей из бемита с небольшим содержанием воды при температуре 598.4 К под давлением 15 МПа. Процесс получения из этой смеси оксида алюминия $\gamma {\text{ - A}}{{{\text{l}}}_{2}}{{{\text{O}}}_{3}}$ включает в себя несколько простых термодинамических подпроцессов:
приведение давления к 0.1 МПа и снижение температуры до 507.1 К (рис. 4), в результате получается смесь бемита и водяного пара (конденсированная фаза), состав которой представлен в табл. 3;
сепарация пара (расход пара 0.00308 кг/с), остается только бемит с расходом 0.04447 кг/с при температуре 507.1 К;
изотермический подвод тепла (26.51 кВт), в результате бемит разлагается на оксид алюминия γ‑Al2O3 и водяной пар (см. табл. 4);
сепарация пара (расход пара 0.00667 кг/с), в остатке только оксид алюминия γ-Al2O3 с расходом 0.0378 кг/с при температуре 507.1 К.
Мощность доступного для утилизации тепла, содержащегося в паре температурой 507.1 К, давлением 0.1 МПа и суммарным расходом 0.00975 кг при его охлаждении до 290 К при 6 МПа, составляет 287.6 кВт.
ПОЛУЧЕНИЕ ЧИСТОГО ВОДОРОДА
Чистый водород получается путем конденсации водяного пара из пароводородной смеси при ее охлаждении до 300 К (рис. 5). При этом расход пароводородной смеси, состав которой при температуре 290 К и давлении 15 МПа приведен в табл. 5, равен 0.09445 кг/с.
После удаления воды (расход 0.0922 кг/с) остается товарный водород (в расчете на давление 6 МПа) с расходом 0.00225 кг/с (см. табл. 6).
КОМПРИМИРОВАНИЕ ВОДОРОДА
Одним из существенных недостатков водорода в качестве энергоносителя является его низкая плотность. Поэтому в большинстве приложений требуется компримирование водорода (до давления 5‒100 МПа в зависимости от конкретного направления использования). Для сжатия водорода традиционно используются механические компрессоры.
Применяемые в настоящее время в промышленности механические компрессоры водорода (поршневые, мембранные) имеют ряд недостатков: сложная конструкция, недостаточная надежность, высокая стоимость обслуживания, вероятность утечки водорода и загрязнения водорода маслом, сильный шум и вибрация при работе.
По данным NREL [5], стоимость компримирования составляет до 70% общей стоимости доставки, хранения и выдачи (compression, storage and dispensing ‒ CSD) водорода как при транспортировании водорода по трубе, так и при распределенном его производстве на месте. При этом практические затраты электроэнергии на сжатие на существующих пилотных водородных заправочных станциях, например Linde Engineering, составляют 1.3‒4.0 кВт ⋅ ч/кг при давлении до 90.0 МПа [6, 7].
Альтернатива механическим компрессорам ‒ термосорбционный компрессор водорода (ТСКВ) или металлогидридный компрессор [8, 9], принцип действия которого основан на обратимом взаимодействии металлов или сплавов с водородом. Такой компрессор представляет собой систему компримирования, включающую в себя модули с металлогидридом, устройства для их нагрева и охлаждения, распределительные газопроводы с запорно-регулирующей арматурой, систему контроля и управления. Основным преимуществом данной системы является использование низкопотенциального тепла вместо электроэнергии, что существенно удешевляет процесс сжатия водорода. Кроме того, следует отметить возможность создания высокого давления нагнетания (свыше 100 МПа), масштабируемость, модульность конструкции, простоту при ремонте и обслуживании, высокую чистоту компримированного водорода. К тому же в ТСКВ нет движущихся частей, что упрощает конструкцию, повышает ее надежность и обеспечивает снижение шума и вибрации.
Использование металлогидридного компрессора в сочетании с гидротермальной установкой окисления алюминия представляется весьма эффективным, так как последняя может служить источником низкопотенциального тепла. Авторы рассчитали предварительные характеристики ТСКВ (см. табл. 7), сопряженного с установкой гидротермального окисления алюминия производительностью 72 т Н2/год (пилотная установка) на давление 100 МПа с использованием данных, приведенных в [8]. Источником тепла для сжатия водорода является низкопотенциальная энергия, образующаяся в результате окисления алюминия водой, при утилизации которой повышается эффективность процесса производства водорода.
Стоимость механического компрессора оценивается в 80 тыс. дол., ТСКВ – 145 тыс. дол. при производительности установки 70 т/год. При этом электрическая мощность механического компрессора составляет 20 кВт, ТСКВ – 1 кВт.
Затраты на компримирование водорода с помощью ТСКВ и механического компрессора аналогичной производительности в зависимости от цены на электроэнергию приведены в табл. 8.
Таблица 8.
Стоимость компримирования водорода с помощью ТСКВ и механического компрессора
Цена на электроэнергию, дол/(кВт · ч) | Стоимость компримирования, дол/кг Н2 | |
---|---|---|
механическим компрессором | ТСКВ | |
0.10 | 0.229 | 0.011 |
0.03 | 0.069 | 0.003 |
0.01 | 0.023 | 0.001 |
Как следует из этой таблицы, стоимость компримирования с помощью традиционного компрессора более чем на порядок выше, чем посредством ТСКВ, и в обоих случаях имеет сопоставимую чувствительность к изменению цены на электроэнергию.
Если подвести итоги, то следует отметить, что при производстве водорода на основе реакции гидротермального окисления алюминия за водородом остается 51% теплоты сгорания алюминия. Из выделяющегося тепла (49%) большую часть (94%) уносит пароводородная смесь. Использование 23% тепла пароводородной смеси в металлогидридном термосорбционном компрессоре для сжатия водорода до 90 МПа и утилизация оставшегося тепла пароводородной смеси могут повысить эффективность гидротермального окисления алюминия до 70%.
Комплексная алюмоводная технология позволяет создать в течение короткого срока промышленные установки по производству водорода, так как установки по электролизу алюминия существуют в промышленном масштабе, а установка по гидротермальному окислению алюминия для получения водорода – достаточно простое и надежное устройство, которое можно сравнительно просто масштабировать.
ВЫВОДЫ
1. Представленная технология получения водорода с помощью окисления алюминия является технологией малоотходной, позволяющей производить “безуглеродный” водород по замкнутому циклу с использованием одного расходуемого агента – электроэнергии.
2. В условиях получения при реализации указанной технологии большого количества остаточного низкопотенциального тепла имеется возможность использовать термосорбционный компрессор для сжатия водорода до рабочих параметров (40–90 МПа). Это позволяет более чем на порядок уменьшить эксплуатационные расходы на сжатие водорода по сравнению с традиционными механическими компрессорами и повысить эффективность процесса гидротермального окисления алюминия на 20–25%.
3. Технико-экономические характеристики и конкурентоспособность технологии будут рассмотрены в последующих публикациях авторов.
Список литературы
РУСАЛ начал испытания электролизера с инертными анодами нового поколения // Аргументы и факты. 10.06.2020 [Красноярск]. https://krsk.aif. ru/money/rusal_nachal_ispytaniya_elektrolizera_s_ inertnymi_anodami_novogo_pokoleniya (Дата обращения 24.05.2021.)
Padamata S.K., Yasinskiy A.S., Polyakov P.V. Progress of inert anodes in aluminium industry: Review // J. Sib. Fed. Univ., Chem. 2018. V. 11. Is. 1. P. 18‒30. https://doi.org/10.17516/1998-2836-0055
Экспериментальная когенерационная энергетическая установка на основе гидротермального окисления алюминия / М.С. Власкин, Е.И. Школьников, А.В. Берш, А.З. Жук, А.В. Лисицын, А.И. Сороковиков, Ю.В. Панкина // Изв. РАН. Энергетика. 2011. № 6. С. 31‒45. https://www.elibrary.ru/item. asp?id=17055893.
Белов Г.В., Иориш В.С., Юнгман В.С. Моделирование равновесных состояний термодинамических систем с использованием ИВТАНТЕРМО для Windows // ТВТ. 2000. Т. 38. № 2. С. 191‒196.
Hydrogen station compression, storage, and dispensing technical status and costs /G. Parks, R. Boyd, J. Cornish, R. Remick // Independent Peer Review Team NREL Technical Monitor: Neil Popovich NREL. Technical Report NREL/BK-6A10-58564. May 2014.
Penev M., Zuboy J., Hunter Ch. Economic analysis of a high-pressure urban pipeline concept (HyLine) for delivering hydrogen to retail fueling stations // Transp. Res. Part D: Transp. Environ. 2019. V. 77. P. 92‒105. https://doi.org/10.1016/j.trd.2019.10.005
Linde Hydrogen FuelTech – Driving the Future of Mobility. Linde Engineering. https://www.linde-engineering. com/en/plant-components/hydrogen-fueling-technologies/index.html (Дата обращения 24.05.2021.)
Metal hydride hydrogen compressors: Current developments & early markets / E. Stamatakis, E. Zoulias, G. Tzamalis, Z. Massina, V. Analytis, Ch. Christodoulou, A. Stubos // Renewable Energy. 2018. V. 127. P. 850‒862. https://doi.org/10.1016/j.renene.2018.04.073
Metal hydride hydrogen storage and purification technologies/ D.V. Blinov, V.I. Borzenko, A.V. Bezdudny, A.N. Kazakov // J. Phys.: Conf. Ser. 2021. V. 2039 P. 012005. https://doi.org/10.1088/1742-6596/2039/1/012005
Дополнительные материалы отсутствуют.
Инструменты
Теплоэнергетика