Теплоэнергетика, 2022, № 12, стр. 64-72
Определение гидравлического сопротивления и объемных коэффициентов тепло- и массоотдачи при охлаждении оборотной воды в многоступенчатой вихревой камере
И. Н. Мадышев a, *, О. С. Дмитриева b, В. В. Харьков b, А. О. Маясова a
a Нижнекамский химико-технологический институт (филиал) “Казанский национальный исследовательский технологический университет”
423578 г. Нижнекамск, просп. Строителей, д. 47, Россия
b Казанский национальный исследовательский технологический университет
420015 г. Казань, ул. Карла Маркса, д. 68, Россия
* E-mail: ilnyr_91@mail.ru
Поступила в редакцию 01.04.2022
После доработки 12.05.2022
Принята к публикации 23.05.2022
- EDN: EDZZAW
- DOI: 10.56304/S0040363622110030
Аннотация
С целью улучшить тепловые характеристики испарительного охлаждения и снизить гидравлическое сопротивление разработана конструкция вихревой камеры с несколькими ступенями контакта фаз, отличительная особенность которых – зоны контакта закрученных течений жидкости и газа, находящиеся в кольцевом пространстве устройства. Экспериментальным путем исследован процесс охлаждения воды в многоступенчатой вихревой камере. Конструкция способна устойчиво работать в широком диапазоне нагрузок: как высоких, так и низких по жидкой и газовой фазам. При проектировании новых контактных устройств в технологических расчетах используется критерий энергоэффективности. Наиболее целесообразно проводить ее оценку по методу Меркеля и Кирпичева. Определены гидравлическое сопротивление вихревой камеры и ее тепловая мощность при различных режимах работы. Полученные значения гидравлического сопротивления в зависимости от плотности орошения в вихревой камере позволяют оценить энергоэффективность устройства и выбрать оптимальные режимы работы по критерию Кирпичева. Представлены выражения для расчетов коэффициентов тепло- и массоотдачи. Критериальное уравнение дает возможность определить, соответствует ли проектному значению эффективность предлагаемого устройства. Проведено сравнение разработанной вихревой камеры с оросителями известных типов по объемному коэффициенту массоотдачи. Многоступенчатая вихревая камера имеет повышенный коэффициент массоотдачи при соотношении массовых расходов газовой и жидкой фаз G/L > 0.5. Наиболее высокая охлаждающая способность вихревой камеры наблюдается при низких массовых плотностях орошения, т.е. небольших гидравлических нагрузках по жидкой фазе. Для повышения энергоэффективности используемых контактных устройств следует проводить процессы охлаждения оборотной воды при малых среднерасходных скоростях газа.
В связи с постоянно растущей потребностью в эффективных методах отвода тепла практически во всех отраслях промышленности необходима разработка новых конструкций градирен, принцип работы которых заключается в прямом контакте потоков воды с ненасыщенным воздухом. При проектировании или модернизации градирни основное внимание, как правило, уделяют повышению ее тепловых характеристик. На работу градирен влияет множество факторов: характеристики распыления, условия среды, свойства охлаждающей жидкости, модификация поверхности оросителя и пр. [1]. Стоит отметить, что именно от блока оросителя существенно зависят тепловые характеристики, так как в этом элементе происходит до 70% теплопередачи [2]. Обзор литературных источников о появившихся в последние годы конструкциях оросителей показал, что предприняты немалые усилия по повышению тепловых характеристик градирен и значительно меньшее внимание уделено снижению уноса жидкости из них [3, 4].
Процессы переноса тепла и массы при распылительном охлаждении очень сложны, поскольку они связаны с такими явлениями, как столкновение капель, образование пленок и зарождение пузырьков. Были проведены обширные экспериментальные и численные исследования механизма тепломассопереноса и влияния на него формы, шероховатости и других характеристик поверхности оросителей. Причем многие практические проблемы применения исследуемых блоков оросителей не были полностью решены из-за сложности протекающих в них процессов [5–8]. Поверхность, имеющая усовершенствованную структуру, может улучшить смачивание и растекаемость рабочей жидкости, сделать жидкую пленку тоньше, повысить характеристики теплопередачи при испарении. Однако зачастую предлагаемые конструкции обладают повышенным гидравлическим сопротивлением, сложны в изготовлении, при этом не всегда решены проблемы неравномерности распределения воды и воздуха по поперечному сечению градирни [9, 10].
Таким образом, новые конструкции с учетом результатов предыдущих исследований, разработанные и лишенные указанных выше недостатков, могут иметь большой потенциал применения в современной промышленности.
Авторами статьи разработана оригинальная конструкция вихревой камеры, предназначенной для проведения процессов тепло- и массообмена в поле центробежных сил [11]. Конструктивная особенность ступеней вихревой камеры – зоны контакта закрученных течений жидкости и газа в кольцевом пространстве устройства. Это взаимодействие фаз достигается благодаря тому, что контактная ступень, установленная на основании вихревой ступени, имеет прорези, через которые газ проходит при относительно невысокой скорости и начинает закручиваться. При этом образуются два вихревых потока, направленных в противоположные стороны (рис. 1). Данная конструкция вихревой камеры позволяет отказаться от использования специальных закручивающих устройств – завихрителей, необходимых для создания закрученного газожидкостного потока в тепломассообменных аппаратах.
Рис. 1.
3D-модель с продольным разрезом (а) и принцип работы многоступенчатой вихревой камеры (б). 1 – корпус; 2 – вихревая контактная ступень; 3 – основание; 4 – прорези; 5 – отверстия для выхода воздуха. Треугольники: темные – потоки жидкости (воды); светлые – потоки газа (охлаждающего воздуха)
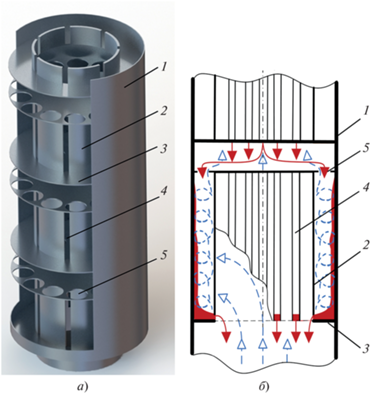
На рис. 1 представлена 3D-модель разработанной вихревой камеры, состоящей из трех контактных ступеней. Принцип работы предлагаемого аппарата заключается в том, что поток охлаждающего воздуха поступает снизу во внутреннюю часть нижней контактной ступени, которая установлена на основании вихревой камеры. Далее воздух, пройдя через прямоугольные прорези, разбивается на два разнонаправленных вихря. При этом в кольцевом зазоре между контактной ступенью и корпусом вихревой камеры образуется закрученное газожидкостное течение. Поток воды поступает на охлаждение в аппарат сверху через нижнюю часть прямоугольных прорезей вышележащей ступени и мгновенно разбивается восходящим потоком воздуха на отдельные струи и капли, после чего из-за центробежных сил поток отбрасывается к стенке корпуса вихревой камеры, где создается пленочное течение. Со стекающей по стенке аппарата пленки жидкости под действием закрученного потока воздуха срываются отдельные капли воды, формируя закрученное газожидкостное течение.
Спецификация контрольно-измерительных приборов
Параметр | Прибор | Диапазон значений | Погрешность |
---|---|---|---|
Средняя скорость воздуха в патрубке нагнетания, м/с | Термоанемометр TESTO 405i | 0.39–8.02 | ±(0.1 м/с + 5%) (0–2 м/с)* ±(0.3 м/с + 5%) (2–15 м/с) |
Температура охлаждающего воздуха, °С | Термогигрометр TESTO 605i | 23–25.7 | ±0.5°C |
Относительная влажность (ОВ) охлаждающего воздуха, % | 21.3–30.4 | ±3.0% (10–35% ОВ) |
|
Температура горячей воды, поступающей в вихревую камеру, °С | Терморегулятор ОВЕН 2ТРМ1 | 41.6–45 | ±0.5% |
Плотность орошения, м3/(м2 · ч) | Ротаметр LZB-VА10-15F | 16–75 | ±1.5% |
Дифференциальное давление, Па | Дифференциальный манометр TESTO 510i | 42–1072 | ±5.0% (0–100 Па) ±3.5% (100–1500 Па) |
Такое взаимодействие фаз наблюдается по всей высоте контактной ступени и характеризуется высокими коэффициентами тепло- и массоотдачи и значительной интенсивностью тепломассопередачи. На выходе из каждой контактной ступени установлен плоский диск с отверстиями, предназначенными для выхода воздуха. Благодаря такому конструктивному оформлению обеспечивается надежная сепарация воды и воздуха. Далее отсепарированный поток воздуха направляется в вышерасположенную контактную ступень аппарата, а охлажденная вода отводится из контактной ступени через прямоугольные прорези на ступень, находящуюся ниже.
При проектировании и выборе контактных устройств для охлаждения жидкости важной задачей является подбор рациональной конструкции аппарата, позволяющей проводить процессы тепло- и массообмена с высокой эффективностью и при использовании минимальных энергоресурсов [12]. С этой точки зрения энергетические затраты на процесс охлаждения оборотной воды в градирнях определяются суммарными потерями энергии на перекачивание воды и воздуха. Так, от давления жидкости перед форсунками зависят прежде всего гидравлические потери энергии в водоохладителях, а гидравлическое сопротивление проходу воздуха влияет на аэродинамическую мощность согласно уравнению
где G – массовый расход воздуха, кг/с; Δp – потери давления, Па; ρг – плотность воздуха, кг/м3.Разрабатываемые новые контактные устройства для взаимодействия газожидкостных фаз должны быть оценены с помощью критерия энергоэффективности, позволяющего определить тепловую мощность, приходящуюся на единицу затрачиваемой энергии. Один из таких показателей – критерий Кирпичева:
где Q – тепловая мощность, Вт.Количество тепла, переданного от воды к воздуху, можно определить по уравнению теплового баланса:
Таким образом, для определения показателя энергоэффективности разработанной вихревой камеры необходимы экспериментальные исследования, чтобы оценить гидравлическое сопротивление аппарата и его тепловую мощность при различных режимах работы.
Для проведения таких опытов была собрана установка, схема которой представлена на рис. 2. Корпус аппарата выполнен из прозрачного материала для визуализации потоков воды и воздуха на вихревых контактных ступенях. Крышка предназначена для замены исследуемых контактных устройств, имеющих различные геометрические размеры. Вода подается насосом из емкости в верхнюю часть аппарата. Воронка служит для сбора воды, стекающей частично из внутренней трубы и кольцевого пространства вихревой камеры, после контакта с воздухом. Регулировка расхода жидкости осуществляется запорной арматурой, установленной на линии подачи воды.
Рис. 2.
Схема экспериментальной установки с вихревыми контактными ступенями. 1 – корпус аппарата; 2 – вихревая контактная ступень; 3 – крышка; 4 – насос; 5 – емкость; 6 – воронка; 7 – фильтр жидкостной; 8 – запорная арматура; 9 – видеокамера; 10 – вентилятор. Датчики: φ1, 2 – относительной влажности; F1, 2 – расхода; p1, 2 – давления; T1–4 – температуры
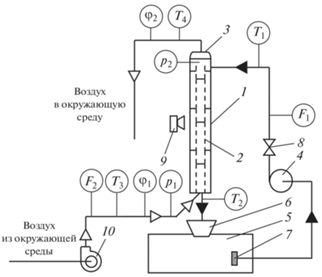
Исследуемый тепломассообменный аппарат состоит из трех вихревых контактных ступеней общей высотой 410 мм. Высота одной контактной ступени составляет 130 мм с учетом высоты сепарационной зоны 40 мм. Наружный диаметр корпуса 80 мм, размеры внутренней трубы – 50 × 1.8 мм. Для образования вихревых потоков на каждой ступени равномерно по всей высоте контактной зоны выполнены 88 отверстий (по 11 в каждом ряду) диаметром 5 мм. Размеры проходных сечений для воздуха на вихревой ступени рассчитываются с учетом равнопроточности, т.е. при отсутствии локальных расширений и сужений газового потока.
В процессе проведения экспериментальных исследований возможно попадание твердых дисперсных частиц вследствие загрязнений рабочих поверхностей оборудования. Чтобы исключить их из потока воды, устанавливают жидкостной фильтр. Подача воздуха в установку осуществляется вентилятором. После взаимодействия с жидкостью на вихревых контактных ступенях воздух направляется в окружающую среду. Поскольку корпус аппарата изготовлен из прозрачного материала, структуру потоков воды и воздуха, а также степень их взаимодействия можно оценить с помощью видеокамеры (см. рис. 2).
Стоит отметить, что для изменения производительности центробежного вентилятора использовался частотный преобразователь Mitsubishi FR E-700, с помощью которого средняя скорость воздуха в патрубке нагнетания изменялась в пределах от 0.39 до 8.02 м/с.
Эксперименты проводились в рабочих средах воздух – вода. Вода подавалась на периферийную зону верхней контактной ступени, откуда через прямоугольные прорези стекала во внутреннюю часть цилиндрической трубы. Для измерения и контроля параметров в ходе эксперимента использовались приборы, характеристики которых приведены в таблице. Фактическое местоположение применявшихся контрольно-измерительных приборов указано на схеме экспериментальной установки (см. рис. 2).
На графике, представленном на рис. 3, видно, что с увеличением плотности орошения наблюдается рост гидравлического сопротивления в вихревой камере. При этом стоит отметить, что предлагаемое устройство надежно работает при высоких гидравлических нагрузках по жидкой фазе. Так, плотность орошения в ходе экспериментальных исследований достигала 75 м3/(м2 · ч).
Рис. 3.
Потери давления ΔpH многоступенчатой вихревой камеры, отнесенные к единице высоты устройства, в зависимости от среднерасходной скорости Wср газа (воздуха) и объемной плотности орошения qV. qV, м3/(м2 · ч): 1 – 16; 2 – 20.6; 3 – 28.4; 4 – 60; 5 – 75
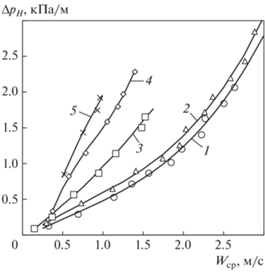
Видно, что с увеличением плотности орошения предельная скорость газа, при которой наступает захлебывание в вихревой камере, снижается. Например, при объемной плотности орошения 16 м3/(м2 · ч) среднерасходная скорость захлебывания составляет 2.63 м/с, а при 28.4 м3/(м2 · ч) – 1.5 м/с (см. рис. 3). Это означает, что новая вихревая камера может устойчиво работать в широком диапазоне удельных нагрузок – соотношение расходов жидкой и газовой фаз может достигать L/G = 37.6.
При проектировании аппаратов охлаждения оборотной воды важной задачей является вычисление объемных коэффициентов тепло- и массоотдачи, зная которые, можно оценить количество тепла, переданного от воды к воздуху. Вследствие сложности определения поверхности контакта воды с воздухом, значения объемных коэффициентов тепло- и массоотдачи находят по эмпирическим формулам, полученным на основе опыта эксплуатации промышленных аппаратов или экспериментальных исследований охлаждения оборотной воды. Объемные коэффициенты тепло- и массоотдачи зависят от типа и конструкции аппарата, а также от массовых расходов воды и воздуха.
Цель исследований – определить значения объемных коэффициентов тепло- и массоотдачи в разработанной вихревой камере и получить критериальную зависимость, позволяющую проводить проектную оценку эффективности предлагаемого аппарата.
На основе метода единиц переноса, широко используемого для расчета высоты рабочей части тепло- и массообменных аппаратов, выведено уравнение для объемного коэффициента массоотдачи, кг/(м3 · с):
(2)
${{\beta }_{{Vx}}} = \frac{{L{{c}_{{\text{ж}}}}}}{V}\frac{{{{t}_{{{\text{ж}}{\text{.н}}}}} - {{t}_{{{\text{ж}}{\text{.к}}}}}}}{{\Delta {{h}_{{{\text{ср}}}}}}},$Объемные коэффициенты теплоотдачи можно вычислить, исходя из аналогии Льюиса:
Так как для воздуха ${{\left( {\frac{{{\text{S}}{{{\text{c}}}_{{\text{г}}}}}}{{{{{\Pr }}_{{\text{г}}}}}}} \right)}^{{0.5}}} \approx 1$, то объемный коэффициент теплоотдачи можно найти по выражению
В общем виде объемный коэффициент массоотдачи описывается формулой [13]:
где A – эмпирический коэффициент, характеризующий охлаждающую способность блока оросителя градирни (определяет совершенство используемых контактных устройств); q – массовая плотность орошения, кг/(м2 · с); n – показатель степени, отражающий зависимость объемного коэффициента массоотдачи от изменения удельного расхода воздуха.Для многих используемых в промышленной теплоэнергетике контактных элементов константы A и n определены. Результаты эксплуатации и экспериментальных исследований некоторых типов оросителей обобщены в работе [14].
Данные экспериментов по охлаждению оборотной воды в вихревой камере позволяют оценить изменение влагосодержания насыщенного воздуха на входе в аппарат и на выходе из него. Среднюю разность энтальпий можно найти методом численного интегрирования выражения
где h" – энтальпия насыщенного воздуха, Дж/кг; hi – энтальпия воздуха, Дж/кг.Энтальпию насыщенного воздуха, кДж/кг, вычисляли по уравнению
где x" – влагосодержание насыщенного воздуха, кг/кг.Энтальпию воздуха для каждого поперечного сечения вихревой камеры, в котором температура воды равна tж, определяли по выражению
Подставляя значения средней разности энтальпий в уравнение (2), можно определить объемные коэффициенты массоотдачи при различных плотностях орошения. На основе обработки опытных данных получено выражение для расчета объемного коэффициента массоотдачи при охлаждении оборотной воды в исследуемой вихревой камере:
Уравнение (3) позволяет вычислить объемный коэффициент массоотдачи с точностью, достаточной для инженерных расчетов. Так, например, средняя относительная погрешность полученного уравнения составила не более 4.42% при массовых плотностях орошения от 4.4 до 12 кг/(м2 · с).
На графике, представленном на рис. 4, видно, что увеличение среднерасходной скорости воздуха приводит к повышению значений объемных коэффициентов массоотдачи в вихревой камере. При этом интенсивность их роста, определяемая как тангенс угла наклона линии, составляет 2.625. Кроме того, установлено, что массовая плотность орошения q в исследуемом диапазоне величин практически не влияет на коэффициенты массоотдачи, так как изменения значений находятся в допускаемой погрешности контрольно-измерительных приборов.
Рис. 4.
Зависимость объемного коэффициента массоотдачи от среднерасходной скорости воздуха и массовой плотности орошения. q, кг/(м2 · с): 1 – 4.4; 2 – 5.67; 3 – 6.63; 4 – 7.84; 5 – 12; точки – эксперимент; сплошная линия – расчет по уравнению (3)
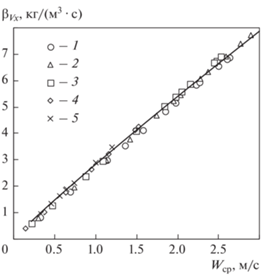
На рис. 5 показана зависимость объемных коэффициентов массоотдачи устройств различных типов, широко используемых в промышленности, от массовых расходов воздуха и воды (экспериментальные данные). Расчеты проводились для градирни с площадью орошения 100 м2, массовый расход воды составлял 896 т/ч, а для воздуха изменялся от 59.2 до 2219.2 т/ч.
Рис. 5.
Зависимость объемного коэффициента массоотдачи от соотношения массовых расходов воздуха и воды для различных контактных элементов градирен. 1 – пленочный асбестоцементный ороситель (A = = 0.479; n = 0.66); 2 – ороситель из призмы ПР50 (A = = 1.05; n = 0.36); 3 – сетчатая насадка [15] [по уравнению ${{\beta }_{{Vx}}} = 1.04q_{{}}^{{1.04}}{{\left( {G{\text{/}}L} \right)}^{{0.79}}}$]; 4 – струйно-пленочный ороситель [16] (A = 1.66; n = 0.8); 5 – ороситель из решетчатых элементов ПР50 [17] (A = 1.41; n = 0.54); 6 – предлагаемая многоступенчатая вихревая камера (A = 2.15; n = 0.93)
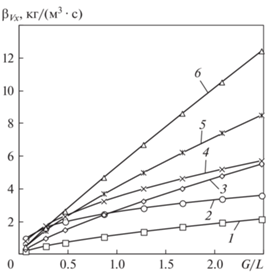
Стоит отметить, что при невысоких соотношениях удельных нагрузок G/L (до 0.26) наибольшие значения объемных коэффициентов массоотдачи наблюдаются у оросителя из призмы ПР-50 (кривая 2). При значениях G/L > 0.5 наибольшие значения коэффициентов массоотдачи наблюдаются у разработанной вихревой камеры, что объясняется высокой интенсивностью процессов тепло- и массообмена, протекающих в кольцевом пространстве аппарата.
На рис. 6 видно, что значения объемных коэффициентов теплоотдачи прямо пропорциональны объемным коэффициентам массоотдачи. Стоит отметить, что при среднерасходной скорости воздуха равной 2.89 м/с и плотности орошения 5.67 кг/(м2 · с) значение объемного коэффициента теплоотдачи в вихревой камере может достигать 8063 Вт/(м3 · K).
Рис. 6.
Зависимость объемного коэффициента теплоотдачи от среднерасходной скорости воздуха при различных массовых плотностях орошения. q, кг/(м2 · с): 1 – 4.4; 2 – 5.67; 3 – 6.63; 4 – 7.84; 5 – 12
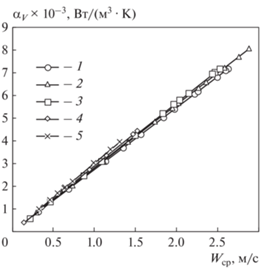
Далее был определен безразмерный критерий Меркеля, который характеризует охлаждающую способность контактных элементов градирни, по уравнению [18]:
(4)
$Me = \frac{{{{\beta }_{{Vx}}}H}}{q} = \frac{{\Delta t{{c}_{{\text{ж}}}}}}{{K\Delta {{H}_{{{\text{ср}}}}}}} \approx AH{{\left( {\frac{G}{L}} \right)}^{n}},$Из (4) следует, что критерий Меркеля прямо пропорционален объемному коэффициенту массоотдачи.
Наиболее высокая охлаждающая способность вихревой камеры наблюдается при низких массовых плотностях орошения (рис. 7), т.е. небольших гидравлических нагрузках по жидкой фазе. Стоит отметить, что из-за центробежных сил, действующих в кольцевом зазоре вихревой камеры, практически полностью отсутствуют застойные зоны и обеспечивается интенсивное перемешивание газожидкостных фаз в поперечном сечении аппарата.
Рис. 7.
Зависимость числа Меркеля от среднерасходной скорости газа в вихревой камере при различных массовых плотностях орошения. q, кг/(м2 · с): 1 – 4.4; 2 – 5.67; 3 – 6.63; 4 – 7.84; 5 – 12
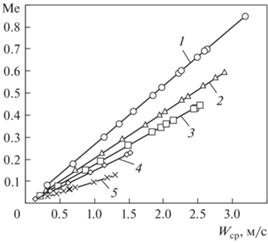
Из рис. 8 следует, что для повышения энергоэффективности χ используемых контактных элементов процессы охлаждения оборотной воды нужно проводить при невысоких среднерасходных скоростях газа. Так, при средней скорости газа в вихревой камере 0.46 м/с и плотности орошения 43.5 м3/(м2 · ч) показатель энергоэффективности составил 1683.5 Вт/Вт.
Рис. 8.
Изменение критерия Кирпичева (1) в зависимости от среднерасходной скорости воздуха при различных объемных плотностях орошения. qV, м3/(м2 · ч): 1 – 16; 2 – 24.1; 3 – 28.4; 4 – 43.5; 5 – 75
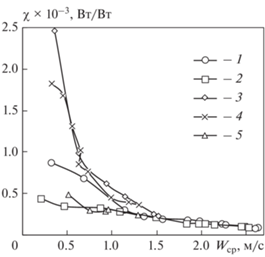
ВЫВОДЫ
1. Проектную оценку эффективности предлагаемого устройства можно провести, используя полученное критериальное уравнение для определения объемных коэффициентов массоотдачи для многоступенчатой вихревой камеры.
2. Найденные значения гидравлического сопротивления при различных плотностях орошения в вихревой камере позволяют оценить энергоэффективность устройства и выбрать наиболее эффективные режимы работы согласно критерию Кирпичева.
3. Проведенные экспериментальные исследования подтверждают возможности достижения высоких значений объемных коэффициентов тепло- и массоотдачи в вихревой камере благодаря интенсивному перемешиванию газовой и жидкой фаз в поперечном сечении аппарата.
4. Полученные значения критерия Меркеля, характеризующие охлаждающую способность жидкости в многоступенчатой вихревой камере, соответствуют таковым для перспективных контактных устройств, предназначенных для реализации процессов тепло- и массообмена.
5. Разработанная вихревая камера может быть использована для охлаждения оборотной воды в условиях высоких нагрузок как по жидкой, так и по газовой фазе с сохранением относительно высокой эффективности охлаждения.
Список литературы
Application status and prospect of spray cooling in electronics and energy conversion industries / H. Chen, X.H. Ruan, Y.-H. Peng, Y.-L. Wang, C.-K. Yu // Sustainable Energy Technol. Assess. 2022. V. 52. Part B. P. 102181. https://doi.org/10.1016/j.seta.2022.102181
Williamson N., Behnia M., Armfield S. Comparison of a 2D axisymmetric CFD model of a natural draft wet cooling tower and a 1D model // Int. J. Heat Mass Transfer. 2008. V. 51. Is. 9–10. P. 2227–2236. https://doi.org/10.1016/j.ijheatmasstransfer.2007.11.008
Thermal performance and emissions analysis of a new cooling tower prototype / J. Ruiz, P. Navarro, M. Hernández, M. Lucas, A.S. Kaiser // Appl. Therm. Eng. 2022. V. 206. P. 118065. https://doi.org/10.1016/j.applthermaleng.2022.118065
Study on thermal performance of new finned heat exchange tube bundles in cooling tower / R. Zhao, S. Bu, X. Zhao, L. Zhang, W. Xu, Z. Yu, J. Fang, Y. Ji, Y. Hu, B. Bao // Int. J. Therm. Sci. 2021. V. 168. P. 107064. https://doi.org/10.1016/j.ijthermalsci.2021.107064
Liang G., Mudawar I. Review of spray cooling – Part 1: Single-phase and nucleate boiling regimes, and critical heat flux // Int. J. Heat Mass Transfer. 2017. V. 115. Part A. P. 1174–1205. https://doi.org/10.1016/j.ijheatmasstransfer.2017.06.029
Breitenbach J., Roisman I.-V., Tropea C. From drop impact physics to spray cooling models: A critical review // Exp. Fluids. 2018. V. 59. P. 55. https://doi.org/10.1007/s00348-018-2514-3
Experimental study of the falling film evaporative cooling on horizontal tubes plates / J. Lu, Z. Liu, X. Xu, J. Liu // Int. J. Refrig. 2022. V. 138. P. 108–117. https://doi.org/10.1016/j.ijrefrig.2022.03.013
The role of enhancement techniques on heat and mass transfer characteristics of shell and tube spray evaporator: a detailed review / A.M. Abed, M.A. Alghoul, M.H. Yazdi, A.N. Al-Shamani, K. Sopian // Appl. Therm. Eng. 2015. V. 75. P. 923–940. https://doi.org/10.1016/j.applthermaleng.2014.10.020
Experimental investigation of fill pack impact on thermal-hydraulic performance of evaporative cooling tower / A.V. Dmitriev, I.N. Madyshev, V.V. Kharkov, O.S. Dmitrieva, V.E. Zinurov // Therm. Sci. Eng. Prog. 2021. V. 22. P. 100835. https://doi.org/10.1016/j.tsep.2020.100835
Мадышев И.Н., Харьков В.В., Николаев А.Н. Интенсификация тепломассообменных процессов в испарительных градирнях. Казань: Изд-во КНИТУ, 2022.
Заявка на изобретение РФ № 2022103039. Контактное устройство для тепломассообменного аппарата / И.Н. Мадышев, В.В. Харьков, А.В. Дмитриев. Заявитель КНИТУ. Заявл. 08.02.2022.
Ma K., Liu M., Zhang J. Online optimization method of cooling water system based on the heat transfer model for cooling tower // Energy. 2021. V. 231. P. 120896. https://doi.org/10.1016/j.energy.2021.120896
Пономаренко В.С., Арефьев Ю.И. Градирни промышленных и энергетических предприятий. М.: Энергоатомиздат, 1998.
Лаптев А.Г., Ведьгаева И.А. Устройство и расчет промышленных градирен. Казань: КГЭУ, 2004.
Лаптев А.Г., Данилов В.А., Вишнякова И.В. Определение эффективности охлаждения оборотной воды в градирне // Теплоэнергетика. 2004. № 8. С. 61–65.
Dmitrieva O.S., Madyshev I.N., Dmitriev A.V. Determination of the heat and mass transfer efficiency at the contact stage of a jet-film facility // J. Eng. Phys. Thermophys. 2017. V. 90. Is. 3. P. 651–656. https://doi.org/10.1007/s10891-017-1612-z
Бергман Д. Испарительные градирни: современные конструкции и преимущества реконструкции // Энергетик. 2000. Спец. вып. С. 15–21.
Kloppers J., Kröger D. A critical investigation into the heat and mass transfer analysis of counterflow wet-cooling towers // Int. J. Heat Mass Transfer. 2005. V. 48. Is. 3–4. P. 765–777. https://doi.org/10.1016/j.ijheatmasstransfer.2004.09.004
Дополнительные материалы отсутствуют.
Инструменты
Теплоэнергетика