Теплоэнергетика, 2023, № 2, стр. 32-36
Обеспечение вибрационной надежности рабочих лопаток при изготовлении паровых турбин
С. Ю. Григорьев a, Б. Е. Григорьев a, Д. А. Андрианов a, И. А. Соколов a, Ю. В. Ферафонтьев a, *
a АО “Силовые машины – ЗТЛ, ЛМЗ, Электросила, Энергомашэкспорт”
195009 Санкт-Петербург, ул. Ватутина, д. 3, Лит. А, Россия
* E-mail: Ferafontev_YV@power-m.ru
Поступила в редакцию 20.05.2022
После доработки 01.07.2022
Принята к публикации 28.08.2022
Аннотация
Коэффициент готовности энергетического блока во многом зависит от надежности рабочих лопаток последней ступени паровой турбины. В процессе эксплуатации рабочие лопатки подвергаются статическим и вибрационным нагрузкам от воздействия потоком пара, поэтому нередко получают повреждения, причиной которых являются усталостные напряжения. Особенно часто повреждаются относительно длинные рабочие лопатки последних ступеней паровых турбин. Аварийные остановы турбины, связанные с повреждениями лопаточного аппарата, составляют четверть их общего числа, а время аварийных простоев энергоблоков из-за поломок лопаток – более половины общего времени их нахождения в нерабочем состоянии. При изготовлении мощных паровых турбин особое внимание уделяется обеспечению вибрационной надежности рабочих лопаток последних ступеней. В статье описана технология обеспечения динамической вибрационной надежности рабочих лопаток последних ступеней паровых турбин ЛМЗ на стадии изготовления с помощью вибрационных испытаний на специальном стенде (Кэмпбелл-машине) в диапазоне частот вращения ротора, где наблюдаются резонансы третьей – десятой кратностей. Приведена Кэмпбелл-диаграмма рабочей лопатки последней ступени мощной паровой турбины с максимальными напряжениями в рабочей лопатке, возникающими при резонансах второй – шестой кратностей, а также результаты сравнения расчетного и экспериментального распределения относительных напряжений на входной и выходной кромках по длине лопатки при дисковых колебаниях четвертой кратности.
При эксплуатации паровой турбины может возникнуть опасный режим вибрации (резонанс лопаток), характеризующийся повышенной амплитудой колебаний рабочих лопаток при совпадении их собственных частот с частотами переменных аэродинамических сил, кратными частоте вращения ротора турбины. При резонансе возникают повышенные динамические напряжения в лопатке, которые приводят к образованию усталостной трещины и поломке лопатки. Избежать резкого увеличения динамических напряжений на резонансных частотах вращения ротора в процессе пуска турбины можно благодаря применению упруго-демпферной связи в конструкции рабочих лопаток, которая позволяет повысить демпфирование их колебаний. Рассматриваемые в данной статье рабочие лопатки имеют бандаж, а также специальную упруго-демпферную связь в промежуточном сечении по их высоте. Для подобной конструкции лопатки отстройке от резонанса подлежат только дисковые колебания (с узловыми диаметрами m, но без узловых окружностей), причем опасными считаются колебания при 2 ≤ m ≤ 6 [1].
Уменьшения возможности возникновения резонанса лопаток при номинальной частоте вращения ротора турбины можно добиться на стадии их изготовления с помощью вибрационной отстройки, изменяя при необходимости собственные частоты лопатки. Под вибрационной отстройкой комплекта рабочих лопаток понимается комплекс работ по обеспечению запасов между номинальной частотой вращения ротора и частотой, при которой возникают резонансные колебания лопаток c отстраиваемыми собственными формами.
На основании сопоставлений расчетных и экспериментальных частот колебаний лопаток, а также опыта эксплуатации были разработаны нормы на вибрационную отстройку лопаток паровых турбин. В соответствии с этими нормами отстройка выполняется только на комплектах лопаток, частоты которых ниже 310 Гц и на которых возможны резонансы с шестой и более низкими кратностями [1]. Вибрационная отстройка лопаток последних ступеней, изготавливаемых на Ленинградском металлическом заводе, производится при испытаниях в Кэмпбелл-машине (далее Установка).
На основании результатов испытаний в Установке можно оценить эффективность принятых конструктивных решений, а также качество изготовления и сборки комплекта рабочих лопаток. При испытаниях определяют частоты и формы колебаний рабочих лопаток, а также распределение напряжений по их высоте для различных форм колебаний.
Установка (рис. 1) представляет собой вакуумную камеру, в которой размещается специальный ротор с комплектом рабочих лопаток. Для возбуждения колебаний лопаток используют струю перегретого пара, которую подают внутрь вакуумной камеры на периферию лопаток через специальное сопло. На рабочих лопатках крепят тензорезисторы (рис. 2) и провода для вывода сигнала с вращающегося ротора на бесконтактное токосъемное устройство (БТУ) и далее на регистрирующую и анализирующую аппаратуру, разработанную в НПП “Мера”.
Бесконтактное токосъемное устройство состоит из вращающейся части, которая крепится на торец ротора Установки, и статорной части, которая закрепляется на основание Установки (рис. 3). Статорная часть БТУ крепится таким образом, чтобы имелась возможность перемещать ее в осевом направлении. Благодаря такому креплению обеспечиваются компенсация тепловых перемещений ротора и статора Установки и одинаковый воздушный зазор между вращающейся и неподвижной частями БТУ при испытаниях. При этом происходит передача электрической энергии на усилители сигнала, установленные во вращающейся части БТУ, и стабильного усиленного сигнала с тензорезисторов. Всего БТУ позволяет получить 128 сигналов с тензорезисторов.
Рис. 3.
Принципиальная схема размещения БТУ на роторе Установки. 1 – рабочая лопатка; 2 – тензорезистор; 3 – соединительные провода от тензорезистора к БТУ; 4 – ротор с диском; 5 – бесконтактное телеметрическое устройство; 6 – фланец для крепления роторной части БТУ к ротору; 7 – статорная часть антенного блока БТУ с приемником; 8 – роторная часть антенного блока БТУ с передатчиком; 9 – питающий кабель; 10 – кабель передачи данных; 11 – датчик частоты вращения ротора; 12 – блок обработки информации; 13 – соединительный кабель между блоком обработки информации и компьютером; 14 – компьютер
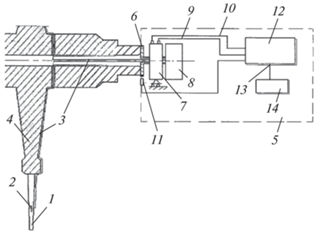
Тензорезисторы наклеивают в различных сечениях профильной части лопатки в соответствии с данными расчетов собственных форм колебаний лопаток в области входной и выходной кромок, где предполагается измерять наибольшие деформации материала лопатки при возникновении вибрации. Кроме того, тензорезисторы устанавливают и в наиболее напряженных зонах хвостовиков лопаток (рис. 4).
Рис. 4.
Схема тензооснастки рабочих лопаток на поверхности (а) и хвостовике (б) лопатки. Т – тензорезистор
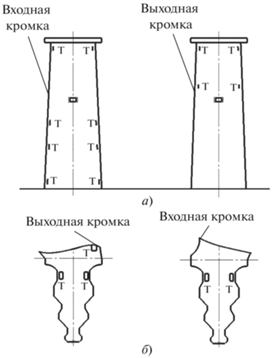
Испытания в Установке позволяют определить частотные характеристики комплекта лопаток при вращении ротора. Влияние центробежных сил на частоты и формы колебаний комплекта лопаток, а также на взаимодействие промежуточных лопаточных связей будет таким же, как и при эксплуатации.
На рис. 5 показана Кэмпбелл-диаграмма комплекта рабочих лопаток последней ступени турбины с бандажом и промежуточной лопаточной связью. Дисковые формы колебаний комплекта лопаток были зафиксированы при изменении частоты вращения ротора от 1600 до 3300 мин–1 с третьей – шестой кратностями колебаний k и низким уровнем напряжений. С наибольшими напряжениями в диапазоне частот, подлежащих отстройке в соответствии с нормами, были зарегистрированы резонансные колебания с четвертой кратностью, которые реализовывались в широком диапазоне изменения частоты вращения ротора 2230–2610 мин–1. Запас между номинальной частотой вращения ротора и резонансной частотой четвертой кратности составляет 13%. В соответствии с нормами запас должен быть не менее 6%. Резонансные колебания с третьей кратностью, соответствующие форме с тремя узловыми диаметрами, были зафиксированы при частоте вращения ротора 3200 мин–1 и выше. Так как частота вращения ротора при испытаниях, соответствующая максимальным напряжениям при резонансе с третьей кратностью, не была достигнута, то можно утверждать, что запас от резонанса с третьей кратностью составляет не менее 7% требуемого по нормам.
Рис. 5.
Зависимость частоты колебаний F комплекта лопаток последней ступени с бандажом и промежуточной лопаточной связью от частоты вращения ротора n
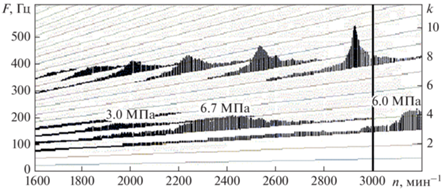
Широкие резонансные зоны третьей и четвертой кратностей свидетельствуют о значительном демпфирующем влиянии промежуточных лопаточных связей. На рис. 5 приведены также резонансные колебания кратностью выше шестой, которые, в соответствии с нормами, не подлежат вибрационной отстройке.
На рис. 6 показано расчетное распределение относительных напряжений σотн на входной и выходной кромках по длине лопатки Lотн при дисковых колебаниях четвертой кратности. При дисковой форме колебаний лопаток, соединенных замкнутыми на круг связями, напряжения на входной и выходной кромках имели разные знаки. При этом колебания лопаток носили аксиальный характер. Это можно объяснить тем, что тангенциальная составляющая амплитуды колебаний ограничивается жесткостью на растяжение промежуточных лопаточных связей и бандажа, а ограничения на осевую составляющую амплитуды колебаний из-за изгиба промежуточных лопаточных связей и бандажа значительно меньше.
Рис. 6.
Экспериментальное (1, 2) и расчетное (3, 4) распределение относительных напряжений на выходной (1, 3) и входной (2, 4) кромках по длине лопатки при дисковых колебаниях четвертой кратности
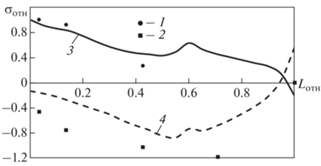
Данные на рис. 6 характеризуют приемлемое совпадение расчетного и экспериментального распределений динамических напряжений по перу лопатки. Как отмечалось ранее, для испытанного комплекта лопаток характерны широкие резонансные зоны. При этом замеряемые напряжения невелики, т.е. вся резонансная зона носит “пологий” характер, что позволяет только приблизительно оценить декремент колебаний по ширине резонансной зоны.
Расчет декремента колебаний δ четвертой кратности осуществляется по формуле [1]
Декремент колебаний для четвертой кратности может составлять δ = 0.129. При этом учитываются следующие виды демпфирования колебаний лопатки:
в материале лопаток;
в зоне контакта лопаток с диском;
в зоне контакта промежуточных лопаточных связей и бандажа.
Основной вклад в суммарное демпфирование вносит рассеяние энергии по контактным поверхностям промежуточных лопаточных связей, что объясняет резкое увеличение декрементов по мере снижения частоты вращения ротора. Полученное при испытаниях в Установке значение декремента колебаний не учитывает аэродемпфирование.
В Установке производятся испытания вновь спроектированных лопаток и тех лопаток, собственная частота которых находится ниже 310 Гц. Это обеспечивает надежную работу ступени турбины и отсутствие резонанса комплекта лопаток при номинальной частоте вращения ротора турбины.
Для ступеней с малым конструктивным демпфированием при эксплуатации возможно возникновение автоколебаний лопаток. Поэтому при отработке новых лопаток последних ступеней мощных паровых турбин наряду с испытаниями в Установке на ЛМЗ проводятся также испытания лопаток в модельных или натурных экспериментальных турбинах в различных эксплуатационных режимах. Окончательное заключение о вибрационной надежности лопаток получают на основании результатов станционных испытаний, выполняемых дискретно-фазовым методом (ДФМ) [2]. Контроль вибрационного состояния лопаток с помощью ДФМ осуществляется системой контроля вибрации лопаток, разработанной на ЛМЗ совместно с НПП “Мера”.
При ремонтах следует обратить внимание на отсутствие повреждений контактных поверхностей бандажных полок и поверхностей контакта промежуточных связей. Такие повреждения теоретически могут возникнуть из-за низкого уровня динамических напряжений в лопатках при начале проскальзывания по контактным поверхностям. В случае повреждения контактных поверхностей необходимо разработать технологию их упрочнения.
ВЫВОДЫ
1. Испытанная ступень турбины обладает удовлетворительными частотными характеристиками, достаточным конструкционным демпфированием и может быть допущена к эксплуатации.
2. В процессе испытаний были зафиксированы дисковые колебания в диапазоне 160–168 Гц, лежащие в настраиваемой зоне (не более 310 Гц).
3. Запас зоны резонансных колебаний четвертой кратности составил 13% номинальной частоты вращения ротора турбины, а зоны резонансных колебаний третьей кратности – не менее 7%.
4. При большом конструкционном демпфировании и кратностях не более шестой остановки на резонансных частотах вращения ротора в процессе пуска турбины практически безопасны. Кроме того, из-за значительного конструктивного демпфирования становится практически невозможным возникновение автоколебаний в процессе эксплуатации.
Список литературы
Боришанский К.Н. Колебания рабочих лопаток паровых турбин и меры борьбы с ними. Вопросы обеспечения вибрационной надежности лопаток турбин. Saarbrücken: Palmarium Academic Publishing, 2014.
Пат. РФ 2063519. Устройство для замера амплитуд колебаний рабочих лопаток турбомашины дискретно-фазовым методом / К.Н. Боришанский, Б.Е. Григорьев, С.Ю. Григорьев, А.Ю. Кондаков, А.В. Наумов, Ю.П. Тихомиров // Б.И. 1996. № 19.
Дополнительные материалы отсутствуют.
Инструменты
Теплоэнергетика